钙处理工艺对低碳冷镦钢洁净度的影响
SWRCH22A冷镦钢的冶炼工艺实践

N . tema igPa t h c n lgc l rc se f o tlp e e t n .c n etr n — on o 2 Se l kn ln.T et h oo ia o e sso tmea rt ame t o v r d p it e p h r ee c nrl Fwht lgrf ig rtcin c niu u at g rv nigf m ozeco gn ,a d o to ,L i s e nn ,p oe t o t o sc s n ,p e e t o n zl lg ig n e a i o n i n r S n w r tde n mpo e n c l e dn te. L w c ro n o i c n c l e dn O o ee s id a d i rv d o od h a ig se 1 0 ab n a d lw s io od h a ig u l se l rd c d b h mp o e e h oo yh dtes p r r yo ihp ry, r o t W t te o u e ytei rv d tc n lg a h u ei i fhg ui wi rd w h l t a p ot t e i O ol
S C 2 A 冷 镦 钢 的 冶 炼 工 艺 实 践 WR H 2
陈ቤተ መጻሕፍቲ ባይዱ
摘
宏 曾
立 喻黄海 许 东利 侯
( 第二炼钢 厂 )
成
一
要 第二炼钢厂采用 B F L —c o — F c工艺生产 S C 2 A冷镦钢 ,通 过对铁水 预处 理、转炉 冶炼 终点 WR H 2
控制、L F炉造 白渣精炼和钙处理 、连铸保护浇注和防止水 口堵塞等工艺进行研究和技术改进 ,使低碳、低 硅铝镇静冷镦钢具有较高的洁净度 ,盘条 T O]含量为( 2~ 3 ×1 ~,钢材 的冷镦性能 良好 。 [ 1 2) 0 关键 词 S C 2 A 冷镦 钢 终点控制 WR H 2 L F炉精 炼 水口堵塞
ml08al钢种冶炼工艺路线确定 (1)

ML08Al钢种冶炼工艺路线确定专业:冶金技术(通用方向)班级:2010级冶金技术2班姓名:学号:一、钢种用途及性能分析ML08Al属低碳冷镦钢,是生产4.8级以下标准件及各类复杂外形非标零件的主要钢种,产品具有成分稳定、有害元素低、钢质纯净度高、尺寸精度高、表面缺陷少、冷镦开裂率低,冷镦钢成型用钢,冷镦是在室温下采用一次或多次冲击加载,广泛用于生产螺钉,销订,螺母等标准件.冷镦工艺可节省原料,降成本,而且通过冷作硬化提高工作的抗拉强度,改善性能,冷镦用钢必须其有良好的冷顶锻性能,钢中S和P等杂质含量减少,对刚才的表面质量要求严格,经常采用优质碳钢,若钢的含碳钢大于0.25%,应进行球化退火热处理,以改善钢的冷镦性能.。
冷镦性能是冷镦钢的重要性能之一。
冷镦钢应具备的主要性能是,具有良好的冷成形性;对于冷镦钢变形要具有尽可能小的阻力和可能高的变形能力。
为此,一般要求冷镦钢的屈强比为0.5~0.65,断面收缩率大于50%。
此外,为避免在冷镦时表面开裂,要求钢材表面质量良好,同时钢材的表面脱碳要尽可能小,采用冷镦工艺制造紧固件,不但效率高、质量好,而且用料省、成本低。
但是冷镦工艺对原材料的质量要求较高。
可用于交通、机械和运输等行业应用,适用于生产各种4.8级以下的标准和非标件等优点,通常使用时不需要热处理. 如制造铆钉、垫圈等。
(一)、力学性能要求1.屈服强度σs及变形抗力尺可能的小,这样可使单位变形力相应减小,以延长模具寿命。
2.钢材的冷变形性能要好,即材料应有较好的塑性,较低的硬度,能在较大的变形程度下不致引起产品开裂。
3.钢材的加工硬化敏感性可能的低,这样不致使冷镦变形过程中的变形力太大。
(二)、化学成份要求1.碳(C)碳是影响钢材冷塑性变形的最主要元素。
含碳量越高,钢的强度越高,而塑性越低。
实践证明,含碳量每提高0.1%,其屈服强度σs约提高27.4Mpa;抗拉强度σb提高58.8~78.4Mpa;而伸长率δ则降低4.3%,断面收缩率ψ降低7.3%。
钙处理低合金高强钢连铸过程中塞棒侵蚀机理及其改进

图 1 塞 棒 及 塞 棒 表 面 、截 面 取 样 位 置 示 意 图 Fig. 1 Schematic diagram of the corroded stopper rod,and sampling positions
先 将 样 品 表 面 的 凝 钢 层 打 磨 干 净 ,用 树 脂 冷 镶磨平后喷金,采 用 Carl Zeiss公 司 E V 0 1 8 型扫 描 电 镜 —能 谱 仪 (scanning electron microscope energy dispersive spectrometer,简称 S E M -E D S )
1 试验研究方法和钢种成分
宁钢炼钢厂生产的低合金高强钢主要钢种包 括汽车大梁钢(5 1()L ) 、汽 车 结 构 钢 (QStE420T M ) 和汽车车轮钢(S P F H 590),规 范 成 分 要 求 如 表 1 所 示 。冶炼工艺流程为:铁水预处理—22U t转炉 —L F 精炼一R H 处理—连铸 。转炉吹炼后, L F 精 炼造 渣 ,以 保 证 钢 液 较 低 的 氧 、硫 含 量 ;R H 处理 结 束 后 喂 入 硅 钙 线 ,钙 处 理 结 束 后 经 过 软 吹 、静 置 ,然后进行连铸。从 表 1 可以看出,钢中碳和硅 含量 较 低 ,锰 、铝含量较高,钢中的平均钙质量分 数在(>.003 % 左右 。
RH前后钙处理对高钛高强钢夹杂物的影响
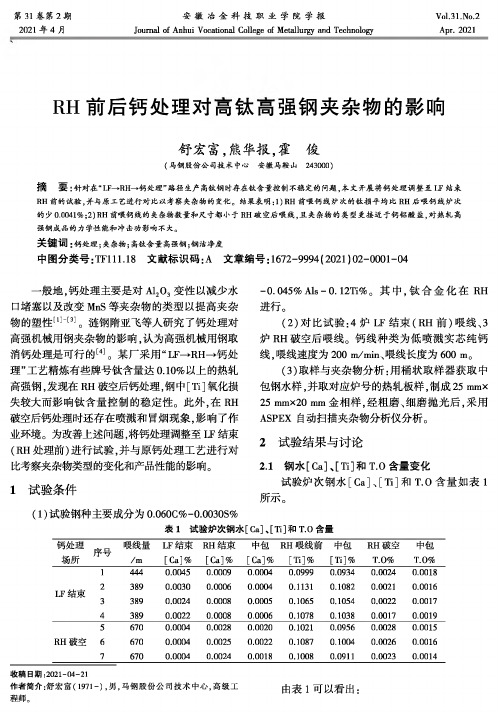
面积率、最大夹杂物的尺寸和大于20 Jim的夹杂 的夹杂物的数量较LF喂线工艺多,尺寸也较大。
物数量均小于RH喂线工艺。 这是因为经过LF白渣精炼脱硫和弱搅拌,钢
2.3夹杂物类型及其成分 试验炉次的夹杂物主要类型为Ti析出物、CaO
水的洁净度已经较高,喂线后,钢中大多数A12O3
-Al2O3,CaS-MnS,Al2O3和MnS,各类夹杂物所占
0.0022 0.0004
0.0008 0.0028
0.0006 0.0020
0.1078 0.1021
0.1038 0.0956
0.0004 0.0025 0.0022 0.1087 0.1004
0.0004 0.0024 0.0018 0.1008 0.0911
RH破空 T.0% 0.0024 0.0021 0.0022 0.0017 0.0028 0.0026 0.0023
1试验条件
2试验结果与讨论
2.1钢水[Ca]、[Ti]和T.0含量变化 试验炉次钢水[Ca]、[ Ti ]和T. 0含量如表1
所示。
(1)试验钢种主要成分为0.060C%-0.0030S%
钙处理 序号
场所 1 2
LF结束 3 4 5
RH破空 6 7
喂线量 /m 444 389 389 389 670 670 670
15.0
1.3
由表3可以看出:在LF结束喂线钙处理工艺 的热轧板中的Ti析出物比例为70.5%、CaS-MnS
总第92期
舒宏富,熊华报,霍俊:RH前后钙处理对高钛高强钢夹杂物的影响
•3•
类夹杂物比例为23.6%;而RH破空后钙处理工艺 的热轧板中的两类夹杂物比例分别为36.4%和56. 5%。由此说明,在RH前钙处理的热轧板中Ti析
钢水钙处理的若干理论问题

钢水钙处理的若干理论问题1. 概述钙处理是20世纪70年代发展起来的一种钢水精炼手段。
其主要目的包括:○1深度降低钢中[O]、[S]等有害元素含量;○2改变夹杂物组成形态,避免浇铸铝镇静钢发生水口堵塞并改善钢材力学性能 [1]。
历史上,曾经有过向钢包内直接加入钙合金、向钢液内喷吹钙合金等方法,但由于处理效果不稳定或成本过高等原因已渐被淘汰,现在应用的是钢包喂钙线方法。
它是将钙合金(Ca 、Ca-Si 、Ca-Fe 等)用钢皮包裹制成包芯线,通过喂丝机的导引管将其以很高的速度插入钢液。
喂丝过程中同时伴随惰性气体搅拌,以增加Ca 蒸汽泡在钢液中的停留时间和良好的混合[2]。
这种方法在全世界的钢铁企业中得到了广泛应用并取得了极大成功。
钢包喂钙线的主要处理效果有:1)降低钢液中的[S],减少硫化物夹杂含量,最终形成CaS 而分散到钢中,在轧制时不会变形。
2)钢液中的氧化物夹杂不形成串簇状而转变为均匀分散的含Ca 氧化物夹杂,从而减少夹杂物尺寸,改善钢液洁净度。
3)在Al 镇静钢中加入Ca ,易把Al 2O 3夹杂变成液态钙铝酸盐,便于它聚合长大上浮,从而防止水口堵塞。
[3]2. 钙处理的脱硫与脱氧2.1钙处理脱氧的热力学条件及处理效果钙与氧的亲和力大于铝、锰、铁与氧的亲和力,在它们形成的氧化物中CaO 是最稳定的。
向钢包内喂入钙线能使钢液中氧活度降低到稳定的狭小范围内,从而能够有效的控制钢中氧含量。
据陶启兆等人研究发现,喂线前控制[%O]≤80×10-6,喂入金属钙线后,平均脱氧率为31.1%,最高脱氧率可达60%[4]。
钙在钢液中脱氧时其反应为:)(][][CaO O Ca =+.................................(1) 65.725655lg -=TK CaO 脱氧后的钢中[Ca]与[O]的溶解度都不高,欲降低钢液中[O]的活度需通过增加[Ca]或降低CaO 来达到。
简析钙处理对管坯钢中夹杂物的影响

条件 下 ,保 持 冶炼及 连铸工 艺参数 基本 稳定 ,分 别 在 V D真 空 处 理 前 或 V D真 空 处 理 后 向 钢 液 喂 入 C — i 芯线 ( aS 包 主要参 数见 表 1。C — i 芯线 的 喂 ) as 包 人 量为 07k/,喂人 速度 约 1 0mmi。采 用 的 两 . g t 5 / n 种试 验方 案 的工艺 流程 如下 。 试 验方案 1 :电弧炉 ( 转炉 ) 炼一 L 初 F精 炼一 喂 C — i 芯线一 VD真 空处理 静 吹一连 铸 。 aS 包 试验方案 2 :电弧 炉 ( 炉 ) 炼 一 L 转 初 F精炼 一 V D真空处 理一 喂 c — i a S 包芯线 静 吹一 连铸 。
Ab t a t s r c :El b r t d i h a e sh w t e i c u i n n t e se l o b — o ln r o to l d b a g n a o a e n t ep p ri o h n l so si h t e rt e r li g a ec n r le y P n a g f u Gr u e g u S e la d Va a i m o , L d o p Ch n d t e n n d u C . t .Co a a i e y a a z e r h e u t f t a c u t e t n mp r tv l n l y d a e t e r s l o wo c l i m r a me t s p o e s s f rd n t rz to fA1O n S i c u i n n t e a u n u k le 0 r t e o u e r li g r c s e o e a u ia i n o , a d Mn n l so s i h l mi i m. il d 3 C M0 se lf rt b —o ln . B s d o h n l s sr s h, i i o c u e h tn i e f h a d t r c s e sc p b e o u l e a u i i g a e n t e a a y i e u t sc n l d d t a et ro e s i wo p o e s s i a a l f l d n t rz n h t f y b t x d n u f e i h t e , a d t u ,o l y me n fi c e s n h fe t e c n e to a c u i h o h o i e a d s l d n t e s e l n h s i n y b a so n r a i g t e e f c i o t n fc l i m n t e v se l a h u p s f u l e a u i a i n b t t e ,c n t e p r o eo l d n t rz to e me . f
不同精炼工艺对管线钢洁净度的影响
㈣
[参考文献]
一一一~一
一
埘姚Ⅶ”
一
蛾一
一
棚一
一州~ 一Ⅲ瑚一蝴一
论一 一钒一 一~~删 ㈣嬲猫一一一
[13张彩军,蔡开科,袁伟霞。等.管线钢的性能要求与炼钢生产 特点[J].炼钢,2002。18(5)。40—46.
[2]潘秀兰.钢洁净度的评定和控制(一)[J].鞍钢技术,2004.
(1):57-61.
管线钢的要求。 RH的脱氢能力较强,可使钢中的氢质量分
数降到2×lo叫以下。本次实验中2种流程都采 用了RH真空精炼,所生产的管线钢氢质量分数 都不大于2×10一,都达到较高的洁净度。但LF —RH生产的第l炉钢的硼(H)是2×10一,高于 第3炉、第4炉,有2个方面原因:一是所取试样 可能存在偏差,正好H富集;二是实验过程中保 护不好,造成测H试样被污染,以至叫(H)偏高。 因而从硼(H)来分析2种工艺,其差别不大。
图3大型央杂物照片
对大型夹杂物拍照后用SEM—EDX观察其形 貌和分析成分。图4是典型的大型夹杂物的扫描 电镜照片,其化学成分见表3。从图4中可以看 出,大部分夹杂物粒径都大于150弘m,且多是不 规则形状。从表3可以看出,纯Al:O。和纯Si(): 夹杂各有1个,Al:()3一Si()2二元夹杂物有3个, 其它的大型夹杂物都是j=元及多元复合夹杂物, 而且w(A12 03)和w(Si()2)比较高。有些夹杂物 含有NazO等成分,可能来自于结晶器保护渣,验 证了这些夹杂物是外来夹杂物。
2.5/_tm以下的夹杂物所占比例为86.86%,2.5 ~5肚m的夹杂物所占比例为11.68%,5~10 gm 的夹杂物所占比例为1.46%,>10“m的夹杂物 在所观察的视场范围内没有发现;RH—LF工艺 中O~2.5 btm的夹杂物所占比例为83.87%,2.5 ~5弘m的夹杂物所占比例为13.71%,5~10肛m 的夹杂物所占比例为2.42%,>10 p.m的夹杂物 数量很少,在观察的夹杂物中所占比例几乎可忽 略不计。根据管线钢夹杂物控制目标要求,要尽 量减少夹杂物数量,减小夹杂物尺寸。比较2种 工艺,LF—RH工艺下夹杂物数目更少,尺寸更 小,因而该工艺更符合高质量管线钢的质量要求。 2.3大型夹杂物研究结果
钙处理对含0.048%-0.065%S中碳结构钢中硫化物的影响
adq at o s p i .4 % ~O05 Sm dl-l o t l( . n Uy f u hd i 008 u l en .6 % ei cE ns e 04 l t m b e 6—05 C .3—09Mn .1 . C , . 。08 7 . 4 。02 ~02 r 4 O0 00 Mo a ens de yacro b maenl o t y t s t so e a te  ̄g n unt o . 3— .4 )hs e ui b abnt ef c br o .l r us hw dt th nt adqat b t d u u i a a r l e l e h l h i f y
关键 词 中碳结构钢 钙处理 硫化物
E e to — e t e to u p i e I cu in n 0. 4 % ~0. 6 f c f Ca Tr a m n n S l h d n l so s i 0 8 0 5% S M e i m. r o t u t r te d u Ca b n S r cu e S e l
本实验 从不 同 的加 入 c . 线方式 和不 同 a C/ 的角度考虑 , a S 研究 了钙处理对含硫 中碳结构 钢中夹杂物形态 的影响。
1 实验 方法
7 - Crn 其它炉次随炉缓冷至室温, 18 ̄/i; a 冷却速率
为 2 . o/ i 个炉次所取试样 的分析结果见 74 Crn a 。6 表1 。 冶炼完后 的小钢锭 , 5 下保温 3 i 在11 o 0C 0mn 后锻造成 西 5m 1 m的钢棒 , 压缩 比为 1:。 11 2 实验结果与分析 2 1 试样中夹杂物的形态与成分 . 用扫描电镜对锻压后试样中的夹杂物进行观
维普资讯
- 1、下载文档前请自行甄别文档内容的完整性,平台不提供额外的编辑、内容补充、找答案等附加服务。
- 2、"仅部分预览"的文档,不可在线预览部分如存在完整性等问题,可反馈申请退款(可完整预览的文档不适用该条件!)。
- 3、如文档侵犯您的权益,请联系客服反馈,我们会尽快为您处理(人工客服工作时间:9:00-18:30)。
118 2007年炉外精炼年会论文集 2007年7月 Ladle Refining 2007 Annual Meeting Proceedings July.2007
钙处理工艺对低碳冷镦钢洁净度的影响 高振波1) 梁海庆1) 吴 坚1) 胡义贵1) 李 颂1) 杜松林1, 2) 1) 马钢第三钢轧总厂,安徽 马鞍山,243000 2) 北京科技大学冶金与生态工程学院,北京100083 摘 要 本文对钙处理工艺过程中夹杂物变性处理需要的钙含量以及硫化钙的生成条件进行了热力学计算,确定了LF处理后硫含量需控制的上限和钙处理后钙含量所需的下限;并对温度和喂钙线量对钙的收得率的影响、钙处理后弱吹氩时间对钢中钙和铝的损失进行了试验摸索。以理论计算和试验结果为基础,优化钙处理工艺,保证LF处理后钢液含硫不大于0.007%,按每炉钢喂钙线100~200m、喂钙线后弱吹氩15~30分钟,最终提高低碳冷镦钢夹杂物合格率达到92%。 关键词 冷镦钢;钙处理;弱吹氩;洁净度;夹杂物
冷镦钢主要用于制造紧固件产品,客户对冷镦钢的使用性能和加工性能要求很高,这样要求冷镦钢具有较好的内部质量,夹杂物大小、分布、数量、种类均较好。作为衡量钢材质量的一个重要指标—夹杂物等级,通过电镜扫描、能谱分析等手段,根据冷镦钢夹杂物评级标准,检测到马钢第三钢轧总厂(以下简称三钢轧)冷镦钢夹杂物合格率83%, B类和DS类夹杂物超标较多。实践证明,钙处理是控制夹杂物的重要环节。本文通过理论计算和试验并结合生产实践,提出了钙处理工艺优化的方向,并付诸实践,有效提高了低碳冷镦钢洁净度。
1工况条件简介 1.1 工艺路线 铁水预处理—50t复吹转炉—吹氩合金微调站—70t LF炉—六机六流140mm方坯连铸机—高速线材轧机 LF工序配备双管喂线机; 140mm方坯连铸机浇注方式为“外装式浸入水口+保护渣”。 1.2 钢种内控成份 冷镦钢成分请见表1
表1 马钢冷镦钢内控成分/% Table 1 controlled component of cold heading steel/%
wt/% C Si Mn S P Al ≤0.10 ≤0.08 0.20~0.5 ≤0.015 ≤0.030 0.020~0.040
1.3 检测方法 (1)使用瑞士ARL-4460型光谱仪快速分析钢中C、Si、Mn、P、S、Al等元素; (2)通过电镜扫描观察夹杂物形态,能谱分析夹杂物组成; (3)采用小样电解分析夹杂物总量; (4)采用TOS针状全氧取样器取样,检验全氧、氮。 2 试验结果及分析 钙处理主要目是使高熔点的Al2O3变性为低熔点的铝酸钙,再经过一段时间弱吹氩,降低非 金属夹杂物含量,从而改善钢液的可浇性,提高钢液的洁净度。 由于钙的沸点低(约1487℃)、蒸气压大、在钢中溶解度低,向钢包钢液内喂钙线进行钙处理过程钢液沸腾非常严重,这必然导致钢液的二次氧化,因此,怎样既能达到钙处理的目的,又能使二次氧化程度降到最小,以及喂过钙线后弱吹氩时间的掌握成为钙处理技术的关键。 2.1 钙处理前钢中硫含量对钙处理效果的影响 在钢包和中间包取样,通过电镜扫描和能谱分析,结果在钢包样里发现了少量硫化钙,在中间包样发现了更多硫化钙夹杂,请见图1和图2 。 July.2007 2007年炉外精炼年会论文集 • 119 • 图1 硫化钙和钙铝酸盐的复相夹杂 Fig.1 compound impurity of sulfuric calcium and alu-minate calcium
图2 A点能谱能谱分析 Fig.2 spectrum analysis of point A
根据热力学反应: [Ca]+[S]=(CaS) (1) ⊿G0=-530651.00+121.81T J/mol Kp=a(CaS)/(a[Ca]*a(S)) 可以计算出钢中含[Al]s:0.02%~0.04%时,在不同温度下硫与钙平衡点,热力学计算结果显示于图3。
0.0000.0050.0100.0150.0200.0250.0300.035
102030405060708090Ca(PPM)
S(%)1590℃
1550℃
图3 不同温度下硫化钙生成条件 Fig.3 the condition of produced sulfuric calcium in dif-ferent temperature.
从图3得知在钢包温度下(约1600℃),钢中硫含量≤0.010%,很难生成硫化钙,实际生产中我们有10%以上炉次硫含量超过了0.010%,钙含量一般在40~60ppm,所以在钢包取样也发现了少量的硫化钙。由于反应(1)受温度影响非常大,温度低更有利于该反应向正方向进行,在中间包温度(约1550℃)下,只要钢液含硫≥0.005%就有可能生成生硫化钙夹杂,这也正是我们所看到的中间包样比钢包样硫化钙夹杂更多的原因所在。以三钢轧目前工艺条件,无法避免随着温度的降低而生成硫化钙夹杂,但是尽量降
低钙处理前钢液中硫含量和保持较低的钙含量有利于减少硫化钙夹杂的生成。从图3我们可以看到若钢液到中间包后含钙30ppm以下,满足钢液中硫含量≤0.007%,基本上不会生成硫化钙。 2.2钙含量对钙处理效果影响 钙在钢液中的溶解度很小,随着温度的提高溶解度会有所提高,向钢包内喂钙线进行钙处理,温度对钙收得率有怎样的影响?为此我们进行了试验设计,把温度和喂线量做为变量,按设计要求进行试验,共测得有效数据24个,试验结果列于图4和图5,从中上我们可以看到,随着喂钙线温度的提高,钙收得率提高,随着喂线量的增加,钙收得率降低。
钙收得率%(平均值)
1655℃1600℃28262422201816141210600m300m100m
温度喂线量
图4 主效应图(平均值) Fig.4 Main Effects Plot (data means)
温度喂线量
600300100252015105
1655160025
2015105
温度16001655
喂线量600100300
钙收得率%(
平
均值)钙收得率%(平均值)
图5交互作用图(平均值) Fig.5Interaction Plot (data means)
我们也做了更低喂线量(≤80m/炉)的试验,结果发现钙含量过低(<12ppm),浇注过程有水口堵塞、堵死现象。 关于钢中含钙多少才能起到变形夹杂物的作用,各种资料介绍并不统一,计算如下反应:
[Ca]+7/6[Al]+11/4[O]=1/12·12CaO·7Al2O3(s) (2)
⊿G0= -1347130.68 + 357.78TJ/mol Kp=(a(12(aO*Al2O3))1/12/(a[Ca]* a[Al]7/6*a[O]11/4) 结果表明,钢中含[Al]s:0.02%~0.04%时,钙含量超过16ppm就能满足夹杂物变性条件,试验结果表明,喂钙线量100m/炉时,钢中钙含量 • 120 • 2007年炉外精炼年会论文集 2007年 7月 在20~38ppm,能满足钙处理的要求,考虑到钢液中[Al]s等的波动,所以每炉钢喂钙线范围100~200m(相当于钙加入量0.01%~0.02%)。 2.3 弱吹氩时间的影响 钢液中非金属夹杂物上浮需要一定的时间,通过吹氩搅拌,增加夹杂物之间的碰撞,能够使固态夹杂物聚集,液态夹杂物集合为大颗粒夹杂物,根据斯托克斯(Stokes)公式,夹杂物上浮速度与夹杂物半径的平方成正比,夹杂物的聚合大大提高价杂物去除速率。通常生产较高品质的钢,比如冷镦钢,都会适当延长喂钙线后的弱吹氩时间,从下图我们可以看到,弱吹氩25分钟内钢液中最容易氧化的钙和铝元素几乎没有变化,另外我们对不同弱吹氩时间钢液中钙含量和铝含量做方差分析,证明弱吹氩5分钟和25分钟的两组数据没有区别。
不同弱吹时间钢中[Ca]对比
0.00000.00100.00200.00300.00400.00500.00600.00700.00800.0090
№1№4№7№10№13№16№19炉次
[Ca]%Ca%(弱吹5分钟)Ca%(弱吹25分钟)
图6不同弱吹时间钢中[Ca]对比 Fig.6 compared with content calcium in different soft blowing time
不同弱吹时间钢中[Al]对比00.010.020.030.040.050.060.07
№1№4№7№10№13№16№19炉次
[Al]%Als%(弱吹5分钟)Als%(弱吹25分钟)
图7不同弱吹时间钢中[Al]对比 Fig.7 compared with content aluminum in different soft blowing time.
图6和图7表明,在三钢轧条件下,钢包喂钙线后弱吹氩时间25分钟以内钢液二次氧化程度非常小,这样我们完全可以在不增加设备投入的前提下,适当延长弱吹氩时间,促进更多的较小非金属夹杂物的上浮。取洋检测结果表明,弱吹氩25分钟比弱吹5分钟夹杂物总量降低约5ppm。 2.4 取样分析结果对比 我们在钙处理工艺优化前后各取4个炉号48个线材样对比分析。优化后线材取样夹杂物不合格4个,合格率92%;压限3个,良好率85%。优化前线材取样夹杂物不合格8个,即合格率83%;压限4个,良好率75%。 取样检测结果列于表2和表3,可以看到B类夹杂物大大降低,而DS类夹杂物并没有减少,这可能与中间包和结晶器卷渣有关,仅仅通过对钙处理工艺的改进和优化是不能实现DS类夹杂减少的。
表2 钙处理工艺优化后线材夹杂物检验结果(个数) Table 2 inspect result of impurity in wire rod after optimum (number)
样本数 不合格数 A B C D DS 细系 粗系 细系 粗系 细系 粗系 细系 粗系
48 4 0 0 0 1 0 0 0 0 3
压限数 A B C D DS 细系 粗系 细系 粗系 细系 粗系 细系 粗系
3 0 0 0 0 0 0 0 0 3
表3 钙处理工艺优化前线材夹杂物检验结果(个数) Table 3 inspect result of impurity in wire rod before optimum (number)
样本数 不合格数 A B C D DS 细系 粗系 细系 粗系 细系 粗系 细系 粗系
48 8 1 0 2 2 0 0 0 0 3
压限数 A B C D DS 细系 粗系 细系 粗系 细系 粗系 细系 粗系
5 0 0 1 1 0 0 0 0 3