外圆磨床常见故障排除
外圆磨床常见故障排除

调整间隙
进刀太快,光磨时间不够
进刀要慢而均匀,光磨至没有火花为止
砂轮与工件接触面积大,磨削压 力大。
把砂轮端面修成内凹,使工作面尽量狭小,同时先 把砂轮退出一段距离后再吃刀,然后逐渐摇进 砂轮,磨出整个端面
工件顶得过紧或过松
调节尾架顶尖压力
砂轮主轴中心与工作台运动方向 不平行
调整砂轮架的位置
与椭圆度原因1和5相同
降 可点
,利 许锋 允得 不修 备轮 设砂 如把 。長 削以 磨量 上给
扒动 棒跳 承向 轴径 轴生 主产 轮, 砂大
架
3),o7/|\W恤w M轮杲网W, wio使伴 心后‘舊( 1可令阴W;段关在 平」先集 堆卯J,煤 沁(2砂心
高
择
砂
砂轮修得过细,或金刚石顶角已 磨钝。砂轮修正不锋利。
合理选择修正用量或翻身金刚石, 或得金刚石磨修 尖。
外圆磨常见故障排除
1
工件有螺旋形痕迹
深 肖 磨 细 过 得 修 高
度。 硬大 轮过 砂&
大 过 量 给
量 给
®, 磨 轮 砂
砂
O刚在平 金石不
需 装
台
产 台, 作起 工浮
作 工
或
2
工件表面有烧伤现象
度
修 轮 砂
量
砂
或 大 过 量 给
或 量 △口 纟
3
工件表面出现直波形振痕
圆角 件多 工有
量
W则 件规 工床
4
中心孔形状不正确,或内有污后, 铁销等,
根据具体情况重新修正中心孔,或把中心孔檫净
中心孔或顶尖因润滑不良而磨损
注意润滑,如有磨损,需重新修正中心孔或修磨顶 尖
数控外圆磨床常见缺陷及其解决方法

数控外圆磨床常见缺陷及其解决方法
一、外圆磨床在磨削时工件容易弯曲
welcome
解析原因:
1.在外圆磨削时磨削量太大;
2.在外圆磨床磨削时,切削液供给不充分;
预防措施:
1.适当的减少外圆磨床的背吃刀量;
2.保证切削液供给充足;
二、轴肩旁外圆尺寸较大
welcome
解析原因:
1.数控外圆磨床换向工作台停留时间太短;
2.外圆磨床砂轮磨损、砂轮外角变圆。
预防措施:
1.延长外圆磨床工作台换向的停留时间。
2.要及时修正数控外圆磨床的砂轮,保证工件磨削的精度。
三、工件两端尺寸较大呈鞍型
welcome
解析原因:
1.数控外圆磨床的砂轮余越出工件端面太少;
2.外圆磨床工作台停留时间太短;
3.磨细长轴时,顶尖顶的太紧;
4.外圆磨床的中心架水平撑块压力太大;
预防措施:
1.正确调整外圆磨床工作台上换向撞块位置,使外圆磨床砂轮越出端面为1/3-1/2的砂轮宽度。
2.正切调整外圆磨床工作台停留时间;
3.调整外圆磨床顶尖压力。
4.正确调整外圆磨床中心架水平撑块位置。
磨床故障及排除方法
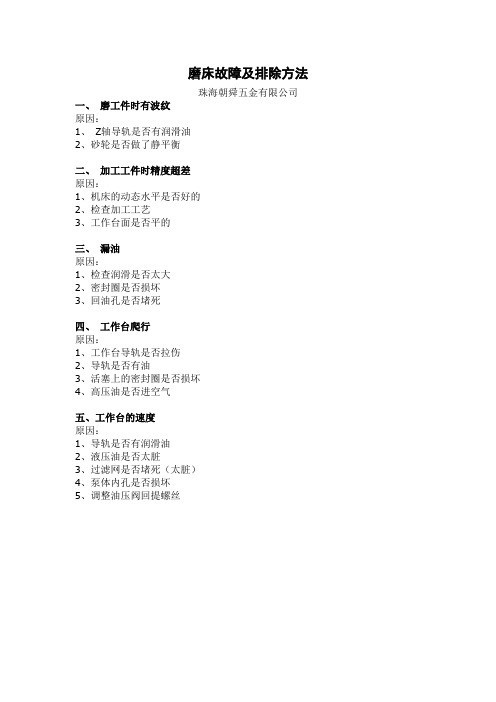
磨床故障及排除方法
珠海朝舜五金有限公司一、磨工件时有波纹
原因:
1、Z轴导轨是否有润滑油
2、砂轮是否做了静平衡
二、加工工件时精度超差
原因:
1、机床的动态水平是否好的
2、检查加工工艺
3、工作台面是否平的
三、漏油
原因:
1、检查润滑是否太大
2、密封圈是否损坏
3、回油孔是否堵死
四、工作台爬行
原因:
1、工作台导轨是否拉伤
2、导轨是否有油
3、活塞上的密封圈是否损坏
4、高压油是否进空气
五、工作台的速度
原因:
1、导轨是否有润滑油
2、液压油是否太脏
3、过滤网是否堵死(太脏)
4、泵体内孔是否损坏
5、调整油压阀回提螺丝。
外圆磨削质量缺陷原因分析与排除措施

外圆磨削质量缺陷原因分析与排除措施摘要:在外圆磨削加工过程中,在工件表面经常会产生各种各样的表面缺陷,常见的如表面存在波纹、表面划伤、烧伤、鱼鳞状痕迹等。
为了保证磨削的质量,不仅要保证磨床有较高的加工精度,还要保证砂轮有较好的磨削性能。
我们从检查的角度对外圆磨削这些质量缺陷,进行分析并给出相应的解决措施。
关键词:外圆磨削质量缺陷原因分析1.表面波纹缺陷在磨削加工的过程中,工件表面或多或少的都会留下一些加工波纹,表面的波纹是磨削加工过程中最常见的缺陷,形成表面波纹的原因是由于磨削过程中,磨床存在机械的振动,使砂轮在磨削工件时,与工件表面的接触力不能保证时刻一致,从而在工件的表面会留下不同的加工痕迹,由于振动的随机性,因此会产生不同的波纹。
常见的有直线的条纹、多边形波纹、鱼鳞斑纹和斜纹、螺纹线等。
(1)直线条纹产生原因及排除措施直线条纹的产生主要原因是由于磨削系统中存在的各种振动:①、由于砂轮的不平衡,在转动过程中产生的振动。
排除的方法:主要是在使用的过程中,保证砂轮的平衡质量,砂轮使用一段时间后,要对砂轮重新进行平衡性调整。
②、由于砂轮自身的硬度不均匀,在磨削的过程中引起振动。
排除方法:检查砂轮表面的硬度是否满足工艺的要求,如果硬度过高要更换硬度较软些的砂轮。
③、砂轮的修整量过大,或者是修整量不够。
排除的方法:对砂轮要进行合理的修整,修整量过大或不足同样会对工件的表面产生影响,根据要加工的工件进行合理的修整。
④、电机的振动引起的加工过程中砂轮的振动。
排除方法:电机要固定平衡,或者采用相应的隔振装置,如通过弹性零件吸收振动,消除电机的振动对磨削加工的影响。
⑤、砂轮的主轴与轴承这间的间隙过大,使砂轮在旋转时产生径向的跳动。
排除的方法:检查砂轮主轴与轴承间的间隙,按要求正确调整间隙。
(2)多边形波纹产生的原因及排除措施①、由于工件细长,在磨削过程中,工件由于刚性不足,产生振动。
排除的方法:在工件中间增加支撑架,提高支承的刚性,同时稍微降低进给量和进给速度。
外圆磨床简单加工问题及解决方法
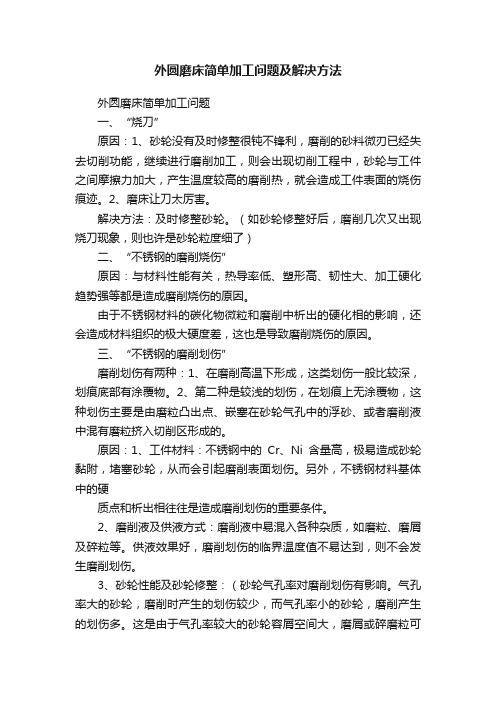
外圆磨床简单加工问题及解决方法外圆磨床简单加工问题一、“烧刀”原因:1、砂轮没有及时修整很钝不锋利,磨削的砂料微刃已经失去切削功能,继续进行磨削加工,则会出现切削工程中,砂轮与工件之间摩擦力加大,产生温度较高的磨削热,就会造成工件表面的烧伤痕迹。
2、磨床让刀太厉害。
解决方法:及时修整砂轮。
(如砂轮修整好后,磨削几次又出现烧刀现象,则也许是砂轮粒度细了)二、“不锈钢的磨削烧伤”原因:与材料性能有关,热导率低、塑形高、韧性大、加工硬化趋势强等都是造成磨削烧伤的原因。
由于不锈钢材料的碳化物微粒和磨削中析出的硬化相的影响,还会造成材料组织的极大硬度差,这也是导致磨削烧伤的原因。
三、“不锈钢的磨削划伤”磨削划伤有两种:1、在磨削高温下形成,这类划伤一般比较深,划痕底部有涂覆物。
2、第二种是较浅的划伤,在划痕上无涂覆物,这种划伤主要是由磨粒凸出点、嵌塞在砂轮气孔中的浮砂、或者磨削液中混有磨粒挤入切削区形成的。
原因:1、工件材料:不锈钢中的Cr、Ni含量高,极易造成砂轮黏附,堵塞砂轮,从而会引起磨削表面划伤。
另外,不锈钢材料基体中的硬质点和析出相往往是造成磨削划伤的重要条件。
2、磨削液及供液方式:磨削液中易混入各种杂质,如磨粒、磨屑及碎粒等。
供液效果好,磨削划伤的临界温度值不易达到,则不会发生磨削划伤。
3、砂轮性能及砂轮修整:(砂轮气孔率对磨削划伤有影响。
气孔率大的砂轮,磨削时产生的划伤较少,而气孔率小的砂轮,磨削产生的划伤多。
这是由于气孔率较大的砂轮容屑空间大,磨屑或碎磨粒可挤进砂轮较大的孔穴中而不划伤工件加工表面)(砂轮修整状态对磨削划伤也有一定影响。
粗修整时在初始磨削时容易出现磨削划伤,但很快会减少,精修整时,初始获得高质量表面,经一段时间磨削,由于砂轮磨损和堵塞,将很快出现磨削划伤)4、磨削加工量(砂轮速度、径向进给量)减少或消除磨削划伤的途径:1、安装二次过滤系统;目的是为了避免在循环使用的磨削液中混入碎磨粒、磨屑和其他杂物,这是减少和消除磨削划伤的有效措施。
M1432A型万能外圆磨床故障的排除
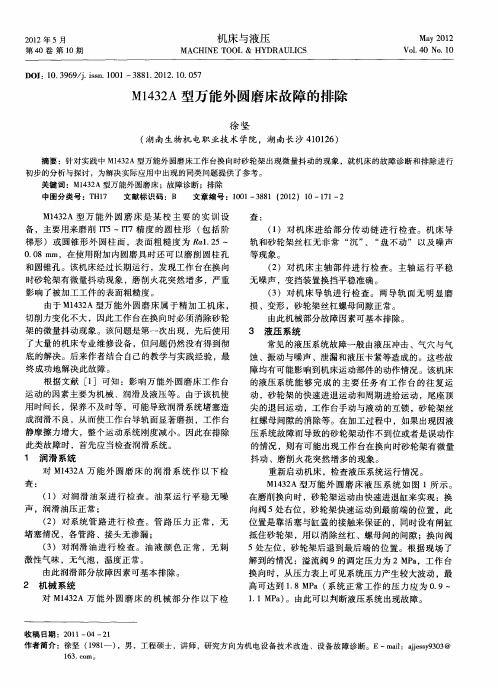
将会通过丝杠螺母使砂轮架产生微量抖动。 从分析结果来看 ,要想解决砂轮架在工作台换 向
时 出的现微量抖动 问题 ,关键就是减缓换 向过程 中主 油路 的油液对快速进退缸 的冲击 。首先 调整溢流 阀 9 的调定压力为 10M a . P ,同时在换 向阀 5的 回油路上 加装一个溢流阀起双向背压缓 冲作用 。 上 电使系统运行 ,故 障完全排 除。
床 与 液 压 ,0 83 ( )3 3 . 2 0 ,6 8 :7— 8
【】 4 李义梅. 如何用 G K90 S - T数控车床 系统加 工椭圆零件 8
[ ] 中国科技信 息 ,0 8 6 : 6 . J. 2 0 ( )5 9— 0
【 】 国经. 5 吴 数控机床故障诊断与维修 [ . M]北京 : 电子工业
【】 2 徐坚, 易竞. 基于 Y 44 T53液压系统故障的分析与探讨
[ ] 机床与液压 ,0 0 3 ( 2 :1 J. 2 1 ,8 1 ) 17—18 8 . 1 ,9 【】 3 徐坚 , 良冲. 于 C 64 数 控车 床故 障 的分 析 与探 廉 基 K 10
讨 [ ] 制造技术与机床 ,0 9 8 :2 —12 J. 20 ( ) 1 1 2 .
出版 社 , 0 4 2o.
( )对机床 进 给部分 传动 链进 行 检查 。机 床导 1
轨和砂轮架丝杠 无非常 “ ” “ 沉 、 盘不 动” 以及噪声 等现象 。
( )对 机床 主轴 部件 进行 检查 。主轴运 行 平稳 2 无噪声 ,变挡装置换挡平稳准确 。 ( )对 机床 导轨 进行 检查 。两 导轨 面无 明显磨 3 损 、变形 ,砂轮架丝杠螺母 间隙正常。 由此机械部分故障 因素可基本排除。
外圆磨床液压系统常见故障分析
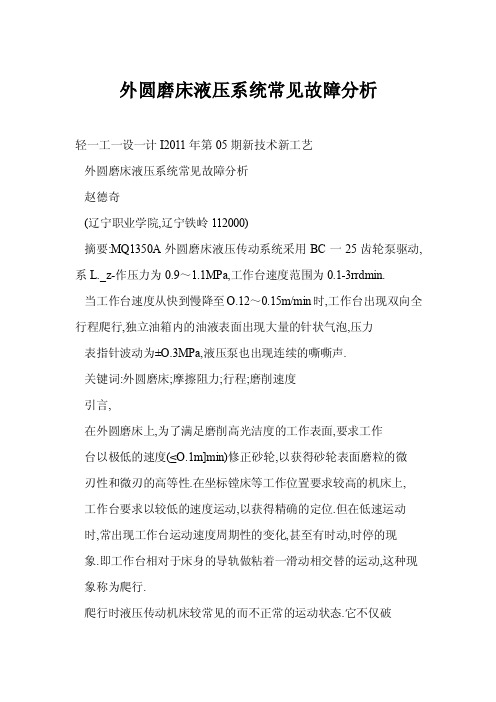
外圆磨床液压系统常见故障分析轻一工一设一计I2011年第05期新技术新工艺外圆磨床液压系统常见故障分析赵德奇(辽宁职业学院,辽宁铁岭112000)摘要:MQ1350A外圆磨床液压传动系统采用BC一25齿轮泵驱动,系L._z-作压力为0.9~1.1MPa,工作台速度范围为0.1-3rrdmin.当工作台速度从快到慢降至O.12~0.15m/min时,工作台出现双向全行程爬行,独立油箱内的油液表面出现大量的针状气泡,压力表指针波动为±O.3MPa,液压泵也出现连续的嘶嘶声.关键词:外圆磨床;摩擦阻力;行程;磨削速度引言,在外圆磨床上,为了满足磨削高光洁度的工作表面,要求工作台以极低的速度(≤O.1m]min)修正砂轮,以获得砂轮表面磨粒的微刃性和微刃的高等性.在坐标镗床等工作位置要求较高的机床上,工作台要求以较低的速度运动,以获得精确的定位.但在低速运动时,常出现工作台运动速度周期性的变化,甚至有时动,时停的现象.即工作台相对于床身的导轨做粘着一滑动相交替的运动,这种现象称为爬行.爬行时液压传动机床较常见的而不正常的运动状态.它不仅破坏液压系统工作的稳定性和精确定位,还使被加工表面质量恶化, 降低机床和道具的使用寿命,甚至被迫停机检修而影响生产.MQ1350A外圆磨床液压传动系采用Bc一25齿轮泵驱动,系统工作压力为0.9~I.1MPa,工作台速度范围为0.1-3m/rain.当工作台速度从快到慢降至0.12~0.15m/min时,工作台出现双向全行程爬行,独立油箱内的油液表面出现大量的针状气泡,压力表指针波动为--:0.3MPa,液压泵也出现连续的嘶嘶声.液压传动是以液压油(本机床采用20#液压油)作为工作介质,液体具有可压缩性,在受压后液体的容积缩小,密度增大,但在低压系统中可忽略不计,即认为液体是不可压缩的.若空气进入液压系统后,一部分溶解于压力油中,另一部分形成气泡浮游于压力油里. 由于空气的压缩性很大,使传动系统由”刚体”变成了”弹性体”;且工作台液压缸位于所有液压元件的最高处,空气极易积聚在这里. 因此,直接影响到工作台运动的平稳性.…值得注意的是:空气进人液压系统后会使油液变成乳化状,而外圆磨床磨削工件时是采用乳化液冷却的,若油水混合搅拌后也成乳化状,如何区别它们呢?方法有三:(1)观察.停泵1~2小时,如乳化状消失,即是空气进入液压系统.若仍然成乳化状,是冷却液混入油液中.(2)听.空气侵入液压系统后必然会发出嘶嘶声,且比较刺耳.而冷却液混入液压系统后发出的噪声较低沉.(3)若空气进入液压系统,手触及液压泵出油管时有”触电”的感觉(即高频振荡的缘故),而冷却液混入液压系统一般无此感觉.处理方法:(1)在制造和修配零件时,严格控制几何形状偏差和配合间隙.(2)紧固个接合面螺钉,各管道连接螺帽及管接头.(3)更换损坏或失效的密封件.(4)所有回油管道的出口插入油面以下.(5)补充油箱油液,使油位不低于油标线.(6)清洗滤油器(网).(7)试车时,先打开放气阀,后启动液压泵,使压力油互通液压缸左,右腔,然后置开停阀于”开”的位置,并操纵节流阀,使工作台由慢至快,由短行程至全行程往复运动5分钟,以排除液压系统中的空气(当转入正常磨削工作时应关闭放气阀).结果:液面针状气泡消失,压力表波动值减少.但双向全行程的爬行变成不规则的间断爬行.从现象判断是节流阀引起的,因为当工作台低速运动时,节流阀的通流面积较小,油中杂质及污物极易积聚在这里,液流速度,高引起发热,将油析出沥青等杂质粘附于节流口处,致使通过节流阀的流量减小;接着,因节流口压差增大,将杂质从口上冲走,使通过节流口的又流量增加.如此反复,致使工作台出现间歇性的跳跃.处理方法:(1)用6o℃的什锦锉仔细清除节流口粘附的杂质. (2)更换清洁的油液,防止油液污染.结果:工作台速度在≥0.5m/min,运动平稳.另有一台同型号的旧机床,工作台运动至液压缸行程两端出现局部爬行.对这种现象一般是因摩擦阻力发生变化而引起.当液压缸左腔进入液压油时,因液体缸刚体与工作台固联,工作台向左运38动.它之所以运动,必须克服作用在活塞上的总负载p(包括切削力在液压缸轴向的分力和法相分力;导轨的摩擦阻力;工作机构在启动时的惯性力;活塞与缸体内孔0型密封圈及液压缸两端支架中活塞杆与型密封圈的摩擦阻力;液压缸的背压力等).因磨削力较小,粗磨与精磨的磨削力变化亦较小工作台在低速运动时,惯性力变化很小;当工作台速度调定后,液压缸的背压基本不变,因此下面仅分析,的变化对爬行的影响.拆卸液压缸检查发现:(1)0型密封圈沟槽底径与活塞外圆同轴度约0.2mm(要求≤0.1mm),致使0型密封圈在圆周上的压缩量不等.密封圈压的过紧.(2)活塞与活塞杆同轴度约为0.1/100mm(要求≤O.4/1000mm).(3)由于使用年久,且经常磨削短工件,液压缸的缸体中间部分磨损较多,呈”腰鼓形”.活塞杆两端局部弯曲.装配质量不良,当用手拉退活塞杆移动时,行程终点处阻力较大,说明活塞与缸体孑L,活塞杆与两端支座三则同轴度差.(6)液压缸的上侧母线与导轨不平衡.处理方法:(1)以活塞外圆为基准,修整沟槽底径对外圆的同轴度要求.(2)更换新的0型密封圈,矫正活塞与活塞杆的同轴度要求.(3)镗磨缸体孔至要求.(4)组装时调整两支座与活塞的同轴度及适当放松密封圈的端盖螺钉.(5)重新以平导轨为基准修刮液压缸的安装底面(全长为0.1ram)以V型导轨为基准调整液压缸的侧母线至要求(0.1mm).结果:液压缸的行程两端的爬行消除.但当工作台负载(O.6O吨)移动时,仍有爬行现象.这说明导轨润滑不良,即工作台导轨与床身导轨接触不均匀,润滑油品质不好等.该机床采用静力润滑,它虽具有油膜刚性好,动,静摩擦系数接近,不易产生爬行等优点.但经检查发现油液污染严重,污物堵塞了润滑油调节器的节流口,润滑油几乎中断.同时,工作台导轨与床身导轨接触不均匀,特别是油腔封油边接触较差,因而润滑压力建立不起来,承载能力差.处理方法:(1)刮修导轨,使两者接触面I>75%,且均匀.(2)更换10#液压油.(3)清洗润滑油调节器.结果:在磨削速度范围内(0.4~lm/mm)运动平稳,但当工作台速度在0.2~0.3ndmm范围内时出现区域性爬行.该机床工作台与床身导轨均采用铸铁材料.实验表明,其摩擦系数虽运动速度的增加而下降,这种摩擦系数的降落特性对不同的油品是不一样的.一般说,当油的粘度较小,油膜强度较低,载荷大,速度低时,油膜容易被破坏.为了获得低速时速度平稳,可适当提高油的粘度(更换粘度较大的油液).但该机床润滑系统与主运动系统合用一油箱,且用同一液压泵供油,因此,工作油液的粘度不能太大.处理方法:更换20#精密机床导轨油.结果:工作台速度t>0.03m/min,运动平稳.参考文献【1]章红甲.金属且学机床液压传动『M].南京:江苏科学技术出版社,1984.[2】李壮云,葛宜远.液压元件与系统fM1.北京:机械工业出版社,2000. 【3】盛敬超.液压流体力学rM1.北京:机械工业出版社,1980.。
外圆磨床的维修
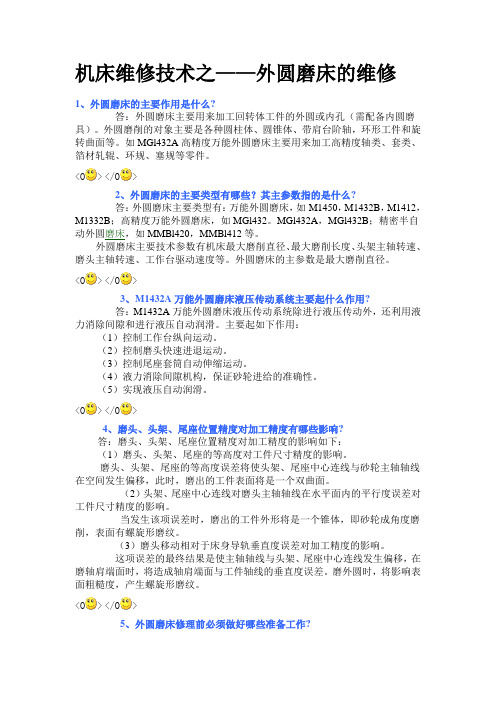
机床维修技术之——外圆磨床的维修1、外圆磨床的主要作用是什么?答:外圆磨床主要用来加工回转体工件的外圆或内孔(需配备内圆磨具)。
外圆磨削的对象主要是各种圆柱体、圆锥体、带肩台阶轴,环形工件和旋转曲面等。
如MGl432A高精度万能外圆磨床主要用来加工高精度轴类、套类、箔材轧辊、环规、塞规等零件。
<O></O>2、外圆磨床的主要类型有哪些?其主参数指的是什么?答:外圆磨床主要类型有:万能外圆磨床,如M1450,M1432B,M1412,M1332B;高精度万能外圆磨床,如MGl432。
MGl432A,MGl432B;精密半自动外圆磨床,如MMBl420,MMBl412等。
外圆磨床主要技术参数有机床最大磨削直径、最大磨削长度、头架主轴转速、磨头主轴转速、工作台驱动速度等。
外圆磨床的主参数是最大磨削直径。
<O></O>3、M1432A万能外圆磨床液压传动系统主要起什么作用?答:M1432A万能外圆磨床液压传动系统除进行液压传动外,还利用液力消除间隙和进行液压自动润滑。
主要起如下作用:(1)控制工作台纵向运动。
(2)控制磨头快速进退运动。
(3)控制尾座套筒自动伸缩运动。
(4)液力消除间隙机构,保证砂轮进给的准确性。
(5)实现液压自动润滑。
<O></O>4、磨头、头架、尾座位置精度对加工精度有哪些影响?答:磨头、头架、尾座位置精度对加工精度的影响如下:(1)磨头、头架、尾座的等高度对工件尺寸精度的影响。
磨头、头架、尾座的等高度误差将使头架、尾座中心连线与砂轮主轴轴线在空间发生偏移,此时,磨出的工件表面将是一个双曲面。
(2)头架、尾座中心连线对磨头主轴轴线在水平面内的平行度误差对工件尺寸精度的影响。
当发生该项误差时,磨出的工件外形将是一个锥体,即砂轮成角度磨削,表面有螺旋形磨纹。
(3)磨头移动相对于床身导轨垂直度误差对加工精度的影响。
这项误差的最终结果是使主轴轴线与头架、尾座中心连线发生偏移,在磨轴肩端面时,将造成轴肩端面与工件轴线的垂直度误差。
- 1、下载文档前请自行甄别文档内容的完整性,平台不提供额外的编辑、内容补充、找答案等附加服务。
- 2、"仅部分预览"的文档,不可在线预览部分如存在完整性等问题,可反馈申请退款(可完整预览的文档不适用该条件!)。
- 3、如文档侵犯您的权益,请联系客服反馈,我们会尽快为您处理(人工客服工作时间:9:00-18:30)。
矿产资源开发利用方案编写内容要求及审查大纲
矿产资源开发利用方案编写内容要求及《矿产资源开发利用方案》审查大纲一、概述
㈠矿区位置、隶属关系和企业性质。
如为改扩建矿山, 应说明矿山现状、
特点及存在的主要问题。
㈡编制依据
(1简述项目前期工作进展情况及与有关方面对项目的意向性协议情况。
(2 列出开发利用方案编制所依据的主要基础性资料的名称。
如经储量管理部门认定的矿区地质勘探报告、选矿试验报告、加工利用试验报告、工程地质初评资料、矿区水文资料和供水资料等。
对改、扩建矿山应有生产实际资料, 如矿山总平面现状图、矿床开拓系统图、采场现状图和主要采选设备清单等。
二、矿产品需求现状和预测
㈠该矿产在国内需求情况和市场供应情况
1、矿产品现状及加工利用趋向。
2、国内近、远期的需求量及主要销向预测。
㈡产品价格分析
1、国内矿产品价格现状。
2、矿产品价格稳定性及变化趋势。
三、矿产资源概况
㈠矿区总体概况
1、矿区总体规划情况。
2、矿区矿产资源概况。
3、该设计与矿区总体开发的关系。
㈡该设计项目的资源概况
1、矿床地质及构造特征。
2、矿床开采技术条件及水文地质条件。