外圆磨床常见故障排除(严选内容)
球磨机的常见故障及解决办法(表格)

电动机带减速机启动后,发生振动
(1)联轴节的两轮间隙太小,不能够补偿电动机在启动时,由自身磁力中心所引起的窜动量。
(2)减速机、电机及传动轴的传动联轴器没有保持很高的同轴性,致使两轴不同心。
(3)联轴节的连接螺栓没有对称的拧紧,并且紧固力大小不一样。
(4)轴承外圈没有固定好。
解决方法:按规定的对轮间隙调好,使两轴同心。以同等力矩对称紧固连轴节的连接螺栓。转子不平衡时,将球磨机转子抽出另行找出平衡点。
减速机带动磨机时发生巨大振动
(1)球磨机与减速机的平衡轴,轴心不在一直线上,磨机安装衬板时,没有进行二次灌浆,或二次灌浆后的地脚螺栓没有紧固好,用卷扬机转动磨筒体,致使磨筒体一端位移,两轴心不在一直线上,使减速机带动磨机后而产生振动。解决方法:要重新进行调整,使球磨机磨机轴心与减速机轴心在同一平面轴心线上。
球磨机常见故障及解决办法
故障现象
原因分析及解决办法
运行时出现有规则很大的敲打声音
部分衬板螺栓没有拧紧,球磨机旋转时衬板敲击磨筒体。根据声音判断衬板部位,找出松动螺栓,另行紧固。
球磨机及电机轴承温度升高,超过70℃
(1)检查各部位润滑点,润滑油牌号与说明书是否一致。
(2)检查润滑油及润滑脂是否有效。
(3)检查润滑管路是否堵塞,或是润滑油没有直接注入润滑点,油量不足引起发热。
(2)大型球磨机体积大,重量重,使地基下沉;发生了位移。解决方法:在基础旁设监测沉降点,进行观测,发现有下沉时,及时进行调整。
减速机运转声音异常
减速机正常运转的声音应是均匀平稳的。如齿轮发生轻微的敲击声或嘶哑的磨擦声音,而运转中无明显变化,可以继续观察,查清原因,球磨机停机进行处理,如声音越来越大,应立即停止球磨机进行检查。同时,若球磨机减速机的平衡轮与中间轮没有按规定的啮合齿标高安装,会造成球磨机高速轴小齿轮带动一侧的中间轴大齿轮,而球磨机中间轴的小齿轮带动平衡轮,球磨机平衡轮又转过来带动另一侧的中间轴,使球磨机减速机没有形成两侧均衡转动,所以,球磨机减速机的平衡轮与中间轮一定要按照规定的啮合齿标安装。
外圆磨床常见故障排除

调整压力
头架和尾座中心不重合
修正使其重合
6
工件有鼓型
工件刚性差,磨削时产生弹性弯曲变型
减小工件的弹性变化;(1)减小磨削深度(2)及时修正砂轮(3)工件很长时,适当使用中心架。
中心架调整不适当
正确调整支撑肯支承块对工件的压力。
7
工件两端尺寸过大或过小
砂轮超出工件端面台小或过大
工作有不平衡重量时,由于离心力作用,会在重的那边磨去较多金属,使工件有椭圆度。
事先加以平衡
砂轮主轴轴承间隙过大。
调整主轴轴承间隙
用卡盘装夹磨削外圆时,头架主轴径向跳动过大
调整头架主轴轴承间隙
5
工件有锥度
工作台未调整好,工件旋转轴线与工作台运动方向不平行
仔细找正工作台
工件和机床的弹性变型发生变化
应在砂轮锋利的情况下仔细找正工作台,每个工件在精磨时,砂轮的锋利程度,磨削用量和光磨次数应与找正工作台时的情况基本一致,否则需要不均匀走到加以消除,
外圆磨床常见故障排除
外圆磨常见故障排除
1
工件有螺旋形痕迹
砂轮硬度高,修得过细,磨削深度过大。
合理选择砂轮硬度和修正用量,适当减小磨削深度
纵向进给量过大
适当降低进给量
砂轮磨损,母线不直
修正砂轮
金刚石在修正器中未夹紧或金刚石在刀杆未焊牢,修出砂轮凹凸不平。
把金刚石装夹牢固,如金刚石有松动,需重新焊接
冷却液太少或太淡
适当减小磨削深度和纵向进给量,或增大工件转速
冷却液不充足
加大冷却液
3
工件表面出现直波形振痕
工件圆周速速过大,工件中心孔有多角.
适当降低工件转速,修正中心孔
外圆磨床常见故障排除
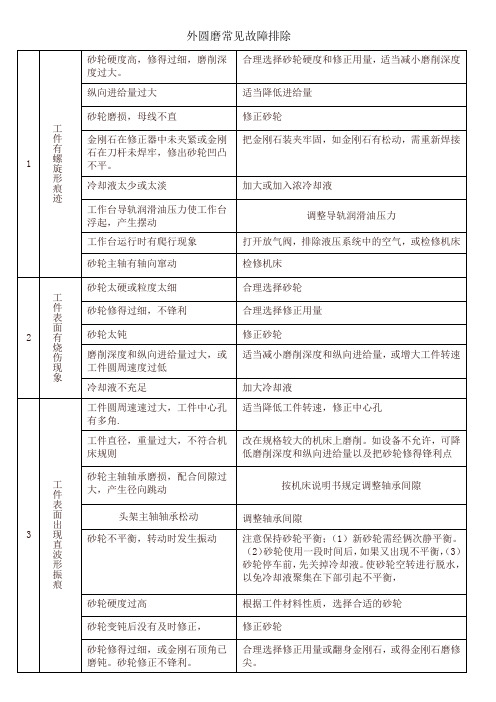
仔细找正工件基准面
10
阶台端面内部凸起
吃刀过大,退刀过块
吃刀时纵向摇动工作台要慢而且均匀,光磨时间要充分
冷却液不充分
加大冷却液
砂轮主轴有轴向窜动
机床检修
头架主轴轴承间隙大
调整间隙
用卡盘磨削端面时,头架主轴轴承窜动大。
调整间隙
进刀太快,光磨时间不够
进刀要慢而均匀,光磨至没有火花为止
冷却液不充足
加大冷却液
3
工件表面出现直波形振痕
工件圆周速速过大,工件中心孔有多角.
适当降低工件转速,修正中心孔
工件直径,重量过大,不符合机床规则
改在规格较大的机床上磨削。如设备不允许,可降低磨削深度和纵向进给量以及把砂轮修得锋利点
砂轮主轴轴承磨损,配合间隙过大,产生径向跳动
按机床说明书规定调整轴承间隙
顶尖在主轴和尾架内贴合不紧,发生摇晃。
卸下顶尖,檫净后重新装上,
砂轮过钝
修正砂轮
冷却液不充分或供应不及时
保证充足的冷却液
工作刚性差而毛坯形状误差又大,磨削时因余量不均而引起磨削深度变化,使工件弹性变型发生相应变化,磨削后部分部分保留毛坯形状误差,
磨削深度不能太大。并应随着余量减小而逐步减小,最后多次几次光磨行程,
调整换向撞块位置,使砂轮超出工件端面1/3-1/2个砂轮宽度
工作台换向时停留时间太长或太短
调整时间
8
阶台旁外圆尺寸大
工作台换向时停留时间太短
延长停留时间
砂轮磨损,靠阶台旁外角变或母线不直
修正砂轮
9
阶台轴各外圆表面不同轴
磨削用量过大或光磨时间不够
精磨时减小磨削深度,多做光磨
M1432A型万能外圆磨床故障的排除
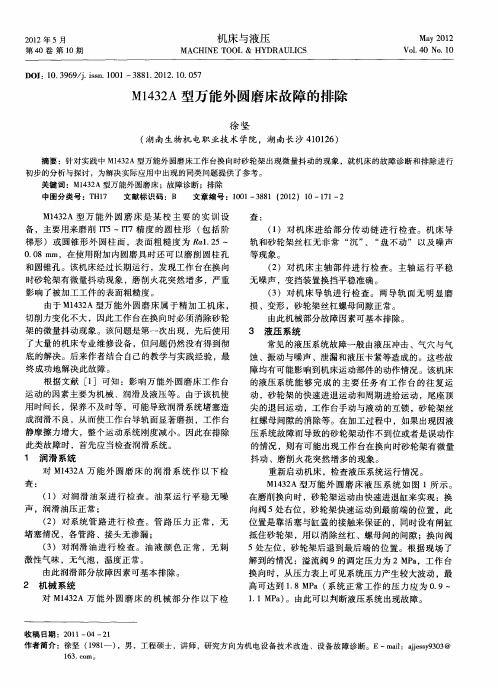
将会通过丝杠螺母使砂轮架产生微量抖动。 从分析结果来看 ,要想解决砂轮架在工作台换 向
时 出的现微量抖动 问题 ,关键就是减缓换 向过程 中主 油路 的油液对快速进退缸 的冲击 。首先 调整溢流 阀 9 的调定压力为 10M a . P ,同时在换 向阀 5的 回油路上 加装一个溢流阀起双向背压缓 冲作用 。 上 电使系统运行 ,故 障完全排 除。
床 与 液 压 ,0 83 ( )3 3 . 2 0 ,6 8 :7— 8
【】 4 李义梅. 如何用 G K90 S - T数控车床 系统加 工椭圆零件 8
[ ] 中国科技信 息 ,0 8 6 : 6 . J. 2 0 ( )5 9— 0
【 】 国经. 5 吴 数控机床故障诊断与维修 [ . M]北京 : 电子工业
【】 2 徐坚, 易竞. 基于 Y 44 T53液压系统故障的分析与探讨
[ ] 机床与液压 ,0 0 3 ( 2 :1 J. 2 1 ,8 1 ) 17—18 8 . 1 ,9 【】 3 徐坚 , 良冲. 于 C 64 数 控车 床故 障 的分 析 与探 廉 基 K 10
讨 [ ] 制造技术与机床 ,0 9 8 :2 —12 J. 20 ( ) 1 1 2 .
出版 社 , 0 4 2o.
( )对机床 进 给部分 传动 链进 行 检查 。机 床导 1
轨和砂轮架丝杠 无非常 “ ” “ 沉 、 盘不 动” 以及噪声 等现象 。
( )对 机床 主轴 部件 进行 检查 。主轴运 行 平稳 2 无噪声 ,变挡装置换挡平稳准确 。 ( )对 机床 导轨 进行 检查 。两 导轨 面无 明显磨 3 损 、变形 ,砂轮架丝杠螺母 间隙正常。 由此机械部分故障 因素可基本排除。
磨床常见故障分析与排除

磨床常见故障分析与排除—济南金鑫
1磨削工件的表面突然拉毛的痕迹
磨削工件的表面突然拉毛的痕迹主要由于粗粒砂轮磨粒脱落后夹在砂轮和工件之间形成的。
(1)粗磨时遗留下来的痕迹在精磨时未磨掉,
适当放大精磨余量。
(2)磨削液中有磨粒存在。
清楚砂轮罩壳内
的磨削,过滤或更换磨削液。
(3)材料韧性太大。
根据工件材料韧性的特
点,选择铬钢玉系列砂轮。
(4)粗粒度砂轮在刚修正好时,其磨粒易于
脱落。
降低工作台速度,尽量使砂轮修
整的细一些,并以较低的纵向速度进行
粗加工,或者改用粒度较细的砂轮。
(5)砂轮太软。
一般情况是材料硬,砂轮软;
材料软,砂轮硬。
但材料过软,亦应选
用较软的砂轮。
(6)砂轮未修整好,有突起的磨粒,重新修
整砂轮。
更多济南机械加工信息。
外圆磨床液压系统常见故障分析
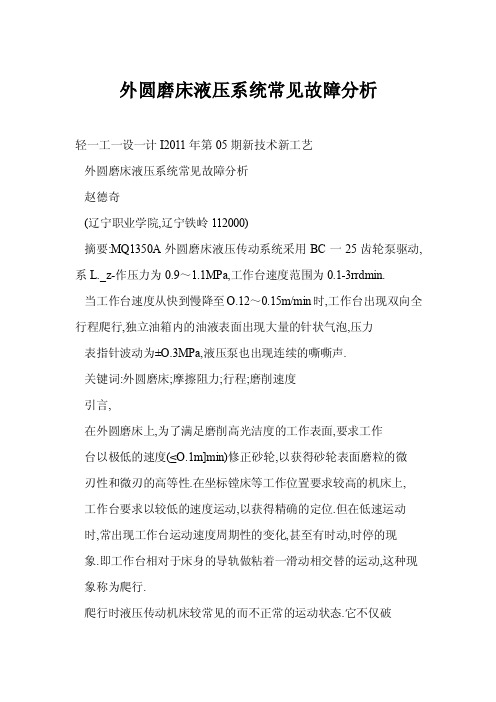
外圆磨床液压系统常见故障分析轻一工一设一计I2011年第05期新技术新工艺外圆磨床液压系统常见故障分析赵德奇(辽宁职业学院,辽宁铁岭112000)摘要:MQ1350A外圆磨床液压传动系统采用BC一25齿轮泵驱动,系L._z-作压力为0.9~1.1MPa,工作台速度范围为0.1-3rrdmin.当工作台速度从快到慢降至O.12~0.15m/min时,工作台出现双向全行程爬行,独立油箱内的油液表面出现大量的针状气泡,压力表指针波动为±O.3MPa,液压泵也出现连续的嘶嘶声.关键词:外圆磨床;摩擦阻力;行程;磨削速度引言,在外圆磨床上,为了满足磨削高光洁度的工作表面,要求工作台以极低的速度(≤O.1m]min)修正砂轮,以获得砂轮表面磨粒的微刃性和微刃的高等性.在坐标镗床等工作位置要求较高的机床上,工作台要求以较低的速度运动,以获得精确的定位.但在低速运动时,常出现工作台运动速度周期性的变化,甚至有时动,时停的现象.即工作台相对于床身的导轨做粘着一滑动相交替的运动,这种现象称为爬行.爬行时液压传动机床较常见的而不正常的运动状态.它不仅破坏液压系统工作的稳定性和精确定位,还使被加工表面质量恶化, 降低机床和道具的使用寿命,甚至被迫停机检修而影响生产.MQ1350A外圆磨床液压传动系采用Bc一25齿轮泵驱动,系统工作压力为0.9~I.1MPa,工作台速度范围为0.1-3m/rain.当工作台速度从快到慢降至0.12~0.15m/min时,工作台出现双向全行程爬行,独立油箱内的油液表面出现大量的针状气泡,压力表指针波动为--:0.3MPa,液压泵也出现连续的嘶嘶声.液压传动是以液压油(本机床采用20#液压油)作为工作介质,液体具有可压缩性,在受压后液体的容积缩小,密度增大,但在低压系统中可忽略不计,即认为液体是不可压缩的.若空气进入液压系统后,一部分溶解于压力油中,另一部分形成气泡浮游于压力油里. 由于空气的压缩性很大,使传动系统由”刚体”变成了”弹性体”;且工作台液压缸位于所有液压元件的最高处,空气极易积聚在这里. 因此,直接影响到工作台运动的平稳性.…值得注意的是:空气进人液压系统后会使油液变成乳化状,而外圆磨床磨削工件时是采用乳化液冷却的,若油水混合搅拌后也成乳化状,如何区别它们呢?方法有三:(1)观察.停泵1~2小时,如乳化状消失,即是空气进入液压系统.若仍然成乳化状,是冷却液混入油液中.(2)听.空气侵入液压系统后必然会发出嘶嘶声,且比较刺耳.而冷却液混入液压系统后发出的噪声较低沉.(3)若空气进入液压系统,手触及液压泵出油管时有”触电”的感觉(即高频振荡的缘故),而冷却液混入液压系统一般无此感觉.处理方法:(1)在制造和修配零件时,严格控制几何形状偏差和配合间隙.(2)紧固个接合面螺钉,各管道连接螺帽及管接头.(3)更换损坏或失效的密封件.(4)所有回油管道的出口插入油面以下.(5)补充油箱油液,使油位不低于油标线.(6)清洗滤油器(网).(7)试车时,先打开放气阀,后启动液压泵,使压力油互通液压缸左,右腔,然后置开停阀于”开”的位置,并操纵节流阀,使工作台由慢至快,由短行程至全行程往复运动5分钟,以排除液压系统中的空气(当转入正常磨削工作时应关闭放气阀).结果:液面针状气泡消失,压力表波动值减少.但双向全行程的爬行变成不规则的间断爬行.从现象判断是节流阀引起的,因为当工作台低速运动时,节流阀的通流面积较小,油中杂质及污物极易积聚在这里,液流速度,高引起发热,将油析出沥青等杂质粘附于节流口处,致使通过节流阀的流量减小;接着,因节流口压差增大,将杂质从口上冲走,使通过节流口的又流量增加.如此反复,致使工作台出现间歇性的跳跃.处理方法:(1)用6o℃的什锦锉仔细清除节流口粘附的杂质. (2)更换清洁的油液,防止油液污染.结果:工作台速度在≥0.5m/min,运动平稳.另有一台同型号的旧机床,工作台运动至液压缸行程两端出现局部爬行.对这种现象一般是因摩擦阻力发生变化而引起.当液压缸左腔进入液压油时,因液体缸刚体与工作台固联,工作台向左运38动.它之所以运动,必须克服作用在活塞上的总负载p(包括切削力在液压缸轴向的分力和法相分力;导轨的摩擦阻力;工作机构在启动时的惯性力;活塞与缸体内孔0型密封圈及液压缸两端支架中活塞杆与型密封圈的摩擦阻力;液压缸的背压力等).因磨削力较小,粗磨与精磨的磨削力变化亦较小工作台在低速运动时,惯性力变化很小;当工作台速度调定后,液压缸的背压基本不变,因此下面仅分析,的变化对爬行的影响.拆卸液压缸检查发现:(1)0型密封圈沟槽底径与活塞外圆同轴度约0.2mm(要求≤0.1mm),致使0型密封圈在圆周上的压缩量不等.密封圈压的过紧.(2)活塞与活塞杆同轴度约为0.1/100mm(要求≤O.4/1000mm).(3)由于使用年久,且经常磨削短工件,液压缸的缸体中间部分磨损较多,呈”腰鼓形”.活塞杆两端局部弯曲.装配质量不良,当用手拉退活塞杆移动时,行程终点处阻力较大,说明活塞与缸体孑L,活塞杆与两端支座三则同轴度差.(6)液压缸的上侧母线与导轨不平衡.处理方法:(1)以活塞外圆为基准,修整沟槽底径对外圆的同轴度要求.(2)更换新的0型密封圈,矫正活塞与活塞杆的同轴度要求.(3)镗磨缸体孔至要求.(4)组装时调整两支座与活塞的同轴度及适当放松密封圈的端盖螺钉.(5)重新以平导轨为基准修刮液压缸的安装底面(全长为0.1ram)以V型导轨为基准调整液压缸的侧母线至要求(0.1mm).结果:液压缸的行程两端的爬行消除.但当工作台负载(O.6O吨)移动时,仍有爬行现象.这说明导轨润滑不良,即工作台导轨与床身导轨接触不均匀,润滑油品质不好等.该机床采用静力润滑,它虽具有油膜刚性好,动,静摩擦系数接近,不易产生爬行等优点.但经检查发现油液污染严重,污物堵塞了润滑油调节器的节流口,润滑油几乎中断.同时,工作台导轨与床身导轨接触不均匀,特别是油腔封油边接触较差,因而润滑压力建立不起来,承载能力差.处理方法:(1)刮修导轨,使两者接触面I>75%,且均匀.(2)更换10#液压油.(3)清洗润滑油调节器.结果:在磨削速度范围内(0.4~lm/mm)运动平稳,但当工作台速度在0.2~0.3ndmm范围内时出现区域性爬行.该机床工作台与床身导轨均采用铸铁材料.实验表明,其摩擦系数虽运动速度的增加而下降,这种摩擦系数的降落特性对不同的油品是不一样的.一般说,当油的粘度较小,油膜强度较低,载荷大,速度低时,油膜容易被破坏.为了获得低速时速度平稳,可适当提高油的粘度(更换粘度较大的油液).但该机床润滑系统与主运动系统合用一油箱,且用同一液压泵供油,因此,工作油液的粘度不能太大.处理方法:更换20#精密机床导轨油.结果:工作台速度t>0.03m/min,运动平稳.参考文献【1]章红甲.金属且学机床液压传动『M].南京:江苏科学技术出版社,1984.[2】李壮云,葛宜远.液压元件与系统fM1.北京:机械工业出版社,2000. 【3】盛敬超.液压流体力学rM1.北京:机械工业出版社,1980.。
机床维修M1432

M1432B型万能外圆磨床一般故障的分析和排除磨床发生故障可归纳为如下四种情况:第一种情况:磨削加工件本身精度低,误差大;由于撞击、拉毛或其他外伤所致,使工件表面产生印痕。
第二种情况为磨床本身制造精度误差大第三种情况为磨床的零件磨损,机构配合松动或间隙过大以及零件损坏等第四种情况为液压系统的故障对于第一种情况,可在加工前对工件进行严格的检查,不符合精度要求的、或外伤所致表面质量未达到要求的工件,予以退回或退修。
下面分析和讨论其他几种情况:1、圆度超差1)磨床头架主轴轴承的磨损,磨削是,使主轴的径向圆跳动圆跳动超差。
可调整轴承游隙或更换新轴承。
2)尾座套筒磨损,配合间隙增大,磨削时在磨削力的作用下,使顶尖位移,工件回转使造成不理想的圆形。
可修复或更换尾座套筒。
2、圆柱度超差1)头架主轴中心与尾座套筒中心不等高或套筒中心在水平面内偏斜。
由于尾座经常沿上工作台表面移动而磨损所致。
可修复或更换尾座,使其与头架主轴中心线等高和同轴。
2)纵向导轨的不均匀磨损,而造成工作台直线度超差。
可修复导轨面,重新校整导轨的精度。
3、磨削时工件表面出现有规律性的直波纹(呈多角状)1)砂轮主轴与轴承、砂轮法兰盘相配合的轴颈磨损,使径向圆跳动和全跳动超差是,可修复或调换主轴。
2)砂轮主轴轴承的磨损,配合间隙过大,使砂轮回转不平衡时,将使磨削产生振动,可调整或更换轴承。
3)砂轮主轴的电动机轴承磨损后,磨削时电动机产生振动,可调换轴承。
4、磨削时工件表面产生有规律的螺旋波纹1)工作台低速爬行,可消除进入液压系统中的空气,疏通滤油器,稳定液压系统中的油压,以及修整导轨表面使其减少摩擦。
2)砂轮主轴的轴向窜动可调整轴承的轴向游隙或更换轴承。
3)砂轮主轴轴心线与工作台导轨不平行可修复导轨使其达到达到精度要求。
5、磨削时工件表面产生无规律的波纹或振痕1)所选砂轮硬度、顆粒不恰当,可选择合适的砂轮。
2)砂轮修整不正确、不及时,可及时地、正确地修整砂轮。
外圆磨床的维修
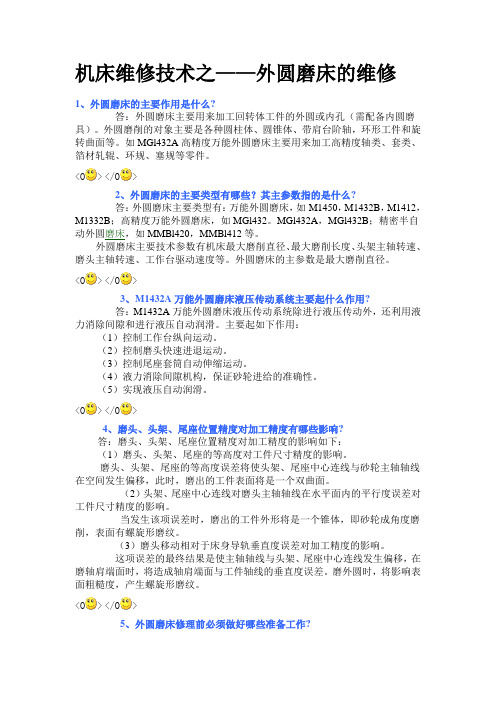
机床维修技术之——外圆磨床的维修1、外圆磨床的主要作用是什么?答:外圆磨床主要用来加工回转体工件的外圆或内孔(需配备内圆磨具)。
外圆磨削的对象主要是各种圆柱体、圆锥体、带肩台阶轴,环形工件和旋转曲面等。
如MGl432A高精度万能外圆磨床主要用来加工高精度轴类、套类、箔材轧辊、环规、塞规等零件。
<O></O>2、外圆磨床的主要类型有哪些?其主参数指的是什么?答:外圆磨床主要类型有:万能外圆磨床,如M1450,M1432B,M1412,M1332B;高精度万能外圆磨床,如MGl432。
MGl432A,MGl432B;精密半自动外圆磨床,如MMBl420,MMBl412等。
外圆磨床主要技术参数有机床最大磨削直径、最大磨削长度、头架主轴转速、磨头主轴转速、工作台驱动速度等。
外圆磨床的主参数是最大磨削直径。
<O></O>3、M1432A万能外圆磨床液压传动系统主要起什么作用?答:M1432A万能外圆磨床液压传动系统除进行液压传动外,还利用液力消除间隙和进行液压自动润滑。
主要起如下作用:(1)控制工作台纵向运动。
(2)控制磨头快速进退运动。
(3)控制尾座套筒自动伸缩运动。
(4)液力消除间隙机构,保证砂轮进给的准确性。
(5)实现液压自动润滑。
<O></O>4、磨头、头架、尾座位置精度对加工精度有哪些影响?答:磨头、头架、尾座位置精度对加工精度的影响如下:(1)磨头、头架、尾座的等高度对工件尺寸精度的影响。
磨头、头架、尾座的等高度误差将使头架、尾座中心连线与砂轮主轴轴线在空间发生偏移,此时,磨出的工件表面将是一个双曲面。
(2)头架、尾座中心连线对磨头主轴轴线在水平面内的平行度误差对工件尺寸精度的影响。
当发生该项误差时,磨出的工件外形将是一个锥体,即砂轮成角度磨削,表面有螺旋形磨纹。
(3)磨头移动相对于床身导轨垂直度误差对加工精度的影响。
这项误差的最终结果是使主轴轴线与头架、尾座中心连线发生偏移,在磨轴肩端面时,将造成轴肩端面与工件轴线的垂直度误差。
- 1、下载文档前请自行甄别文档内容的完整性,平台不提供额外的编辑、内容补充、找答案等附加服务。
- 2、"仅部分预览"的文档,不可在线预览部分如存在完整性等问题,可反馈申请退款(可完整预览的文档不适用该条件!)。
- 3、如文档侵犯您的权益,请联系客服反馈,我们会尽快为您处理(人工客服工作时间:9:00-18:30)。
外圆磨常见故障排除
1工
件
有
螺
旋
形
痕
迹
砂轮硬度高,修得过细,磨削深
度过大。
合理选择砂轮硬度和修正用量,适当减小磨削深度纵向进给量过大适当降低进给量
砂轮磨损,母线不直修正砂轮
金刚石在修正器中未夹紧或金刚
石在刀杆未焊牢,修出砂轮凹凸
不平。
把金刚石装夹牢固,如金刚石有松动,需重新焊接冷却液太少或太淡加大或加入浓冷却液
工作台导轨润滑油压力使工作台
浮起,产生摆动
调整导轨润滑油压力工作台运行时有爬行现象打开放气阀,排除液压系统中的空气,或检修机床砂轮主轴有轴向窜动检修机床
2工
件
表
面
有
烧
伤
现
象
砂轮太硬或粒度太细合理选择砂轮
砂轮修得过细,不锋利合理选择修正用量
砂轮太钝修正砂轮
磨削深度和纵向进给量过大,或
工件圆周速度过低
适当减小磨削深度和纵向进给量,或增大工件转速冷却液不充足加大冷却液
3工
件
表
面
出
现
直
波
形
振
痕
工件圆周速速过大,工件中心孔
有多角.
适当降低工件转速,修正中心孔
工件直径,重量过大,不符合机
床规则
改在规格较大的机床上磨削。
如设备不允许,可降
低磨削深度和纵向进给量以及把砂轮修得锋利点砂轮主轴轴承磨损,配合间隙过
大,产生径向跳动按机床说明书规定调整轴承间隙
头架主轴轴承松动调整轴承间隙
砂轮不平衡,转动时发生振动注意保持砂轮平衡;(1)新砂轮需经俩次静平衡。
(2)砂轮使用一段时间后,如果又出现不平衡,(3)
砂轮停车前,先关掉冷却液。
使砂轮空转进行脱水,
以免冷却液聚集在下部引起不平衡,
砂轮硬度过高根据工件材料性质,选择合适的砂轮
砂轮变钝后没有及时修正,修正砂轮
砂轮修得过细,或金刚石顶角已磨钝。
砂轮修正不锋利。
合理选择修正用量或翻身金刚石,或得金刚石磨修尖。
4工
件
有
椭
圆
度
中心孔形状不正确,或内有污后,
铁销等,
根据具体情况重新修正中心孔,或把中心孔檫净
中心孔或顶尖因润滑不良而磨损注意润滑,如有磨损,需重新修正中心孔或修磨顶
尖
工件顶得过紧或放松重新调节尾架顶尖压力
顶尖在主轴和尾架内贴合不紧,
发生摇晃。
卸下顶尖,檫净后重新装上,
砂轮过钝修正砂轮
冷却液不充分或供应不及时保证充足的冷却液
工作刚性差而毛坯形状误差又
大,磨削时因余量不均而引
起磨削深度变化,使工件弹
性变型发生相应变化,磨削
后部分部分保留毛坯形状误
差,
磨削深度不能太大。
并应随着余量减小而逐步减
小,最后多次几次光磨行程,
工作有不平衡重量时,由于离心
力作用,会在重的那边磨去
较多金属,使工件有椭圆度。
事先加以平衡
砂轮主轴轴承间隙过大。
调整主轴轴承间隙
用卡盘装夹磨削外圆时,头架主
轴径向跳动过大
调整头架主轴轴承间隙
5工
件
有
锥
度
工作台未调整好,工件旋转轴线
与工作台运动方向不平行
仔细找正工作台
工件和机床的弹性变型发生变化应在砂轮锋利的情况下仔细找正工作台,每个工件
在精磨时,砂轮的锋利程度,磨削用量和光磨
次数应与找正工作台时的情况基本一致,否则
需要不均匀走到加以消除,
工作台导轨润滑油压过大,运行
中产生波动
调整压力
头架和尾座中心不重合修正使其重合
6工
件
有
鼓
型
工件刚性差,磨削时产生弹性弯
曲变型
减小工件的弹性变化;(1)减小磨削深度(2)及
时修正砂轮(3)工件很长时,适当使用中心架。
中心架调整不适当正确调整支撑肯支承块对工件的压力。
7工件两
端尺寸
过大或
过小
砂轮超出工件端面台小或过大调整换向撞块位置,使砂轮超出工件端面1/3-1/2
个砂轮宽度
工作台换向时停留时间太长或太
短调整时间
8阶台旁
外圆尺
寸大
工作台换向时停留时间太短延长停留时间
砂轮磨损,靠阶台旁外角变或母
线不直修正砂轮
9阶台轴
各外圆
表面不
同轴
磨削用量过大或光磨时间不够精磨时减小磨削深度,多做光磨
磨削步骤安排不当
同轴度要求高的表面应分粗精磨,同时尽可能一次
装夹中精磨完毕
用卡盘装夹磨削时,工件找正不
对,或头架主轴径向跳动大仔细找正工件基准面
10阶
台
端
面
内
部
凸
起
吃刀过大,退刀过块吃刀时纵向摇动工作台要慢而且均匀,光磨时间要
充分
冷却液不充分
加大冷却液
砂轮主轴有轴向窜动
机床检修
头架主轴轴承间隙大
调整间隙
用卡盘磨削端面时,头架主轴轴
承窜动大。
调整间隙
进刀太快,光磨时间不够进刀要慢而均匀,光磨至没有火花为止
砂轮与工件接触面积大,磨削压
力大。
把砂轮端面修成内凹,使工作面尽量狭小,同时先
把砂轮退出一段距离后再吃刀,然后逐渐摇进
砂轮,磨出整个端面
工件顶得过紧或过松
调节尾架顶尖压力
砂轮主轴中心与工作台运动方向
不平行调整砂轮架的位置
与椭圆度原因1和5相同
与椭圆度1和5的消除方法一样。