四辊卷板机
四辊卷板机卷圆的参数

四辊卷板机卷圆的参数
1.材料参数:
使用四辊卷板机卷圆时,需要考虑卷板材料的性质,如材料的厚度、
宽度、强度等。
各种材料的卷板参数不尽相同,这也是需要在操作过程中
进行调整的依据。
2.材料强度:
材料强度是卷板过程中需要考虑的重要参数之一、卷取半径较小的材
料时,其强度要求较高,否则材料可能会发生断裂或塑性变形,影响卷圆
的质量。
因此,需要根据材料的性质和要求合理选择卷板机的工作压力。
3.卷板机辊直径:
4.最小卷圆直径:
5.卷板机辊材料:
卷板机的辊材料一般使用高强度合金钢或合金铸铁,以保证其寿命和
工作效果。
辊材料的选择要视材料性能和卷板机的使用需求而定。
6.卷板机工作速度:
卷板机的工作速度也是卷圆的参数之一、在卷板过程中,辊的旋转速
度与进给速度的配合要适当。
过快或过慢的速度都可能导致卷板质量不佳。
7.上辊调整方式:
上辊是卷圆时起卫辅助作用的辊,辊的调整方式也是影响卷板质量的
重要因素之一、常见的调整方式有手动调整和液压调整两种。
液压调整方
式能够更精确地控制上辊位置,从而实现更好的卷板效果。
卷板机四辊安全操作及保养规程

卷板机四辊安全操作及保养规程卷板机四辊是金属板材加工的重要设备,使用需尤其注意安全操作和保养,以下为卷板机四辊的安全操作及保养规程。
安全操作规程1. 操作前的准备•操作前应先检查卷板机四辊的各个零部件、机油状态,并做好稳定支撑措施。
•操作前应先熟悉卷板机四辊的开启、停止、调整和维护操作方法,并根据要求检查认真检查机器是否正常运行。
•操作前一定要注意清理工作区和机器,确保无杂物,避免危险发生。
2. 安全操作•监控加工过程,定期对卷板机四辊进行擦拭和保养。
•各辊在工作时应保持协调,同时尽量减少挤压变形的风险。
•过程中禁止用手直接触摸卷板机四辊,以免被卷入机器内,造成人员伤害。
•在加工或维护过程中,禁止穿着外衣长裤,应穿戴防护服、手套、眼睛护具等,确保自身和机器不受伤害,出现问题及时暂停操作,防止交受损失。
•如果使用固定装置,则应如规定地安装和使用,以保证卷板机四辊在加工过程中稳定运行。
保养规程1. 定期检查和保养•检查和调整卷板机四辊间隙,确保各辊协调运转。
•定期清理机器内部杂物,并拆开清洗卷板机四辊表面及内部机件,以确保其顺畅。
•定期润滑卷板机四辊,确保机器各部位运转顺畅和完好。
•定期进行卷板机四辊表面防锈及两端孔防腐处理,以及对附属设备进行检修维护,使设备始终保持完好状态。
2. 维护过程中的注意事项•使用正确的工具或设备进行卷板机四辊的维护和保养,避免损坏机器内部部件。
•定期检查机器各置配件是否松动和磨损,及时将其更换或修复。
•保证机器外部及四卷表面均干燥清洁,避免腐蚀和受潮。
以上即为卷板机四辊的安全操作及保养规程,希望以上内容能对使用卷板机四辊的用户提供帮助,并引起大家对操作过程中的注意事项引起高度重视。
四辊卷板机操作规程
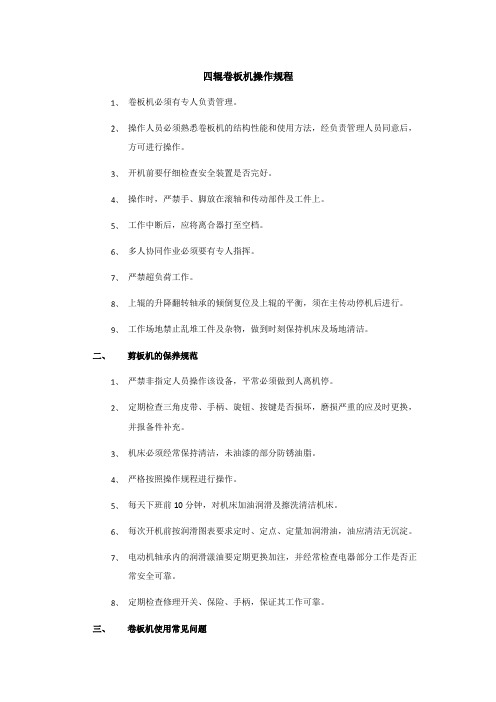
四辊卷板机操作规程卷板机必须有专人负责管理。
操作人员必须熟悉卷板机的结构性能和使用方法,经负责管理人员同意后,方可进行操作。
开机前要仔细检查安全装置是否完好。
操作时,严禁手、脚放在滚轴和传动部件及工件上。
工作中断后,应将离合器打至空档。
多人协同作业必须要有专人指挥。
严禁超负荷工作。
上辊的升降翻转轴承的倾倒复位及上辊的平衡,须在主传动停机后进行。
工作场地禁止乱堆工件及杂物,做到时刻保持机床及场地清洁。
二、剪板机的保养规范严禁非指定人员操作该设备,平常必须做到人离机停。
定期检查三角皮带、手柄、旋钮、按键是否损坏,磨损严重的应及时更换,并报备件补充。
机床必须经常保持清洁,未油漆的部分防锈油脂。
严格按照操作规程进行操作。
每天下班前10分钟,对机床加油润滑及擦洗清洁机床。
每次开机前按润滑图表要求定时、定点、定量加润滑油,油应清洁无沉淀。
电动机轴承内的润滑漾油要定期更换加注,并经常检查电器部分工作是否正常安全可靠。
定期检查修理开关、保险、手柄,保证其工作可靠。
三、卷板机使用常见问题由于卷板机额定容量不够或操作不当,导致瓦片或管节,在纵向焊接出现超标直边。
板料拼接后在进行卷制瓦片(管节),或卷制之后纵向焊接完后,在用卷板机进行滚压矫正修弧。
当板料压头是,由于上辊下压力很大,压头往往是确定卷板机额定容量的主要指标。
由于卷板机卷制能力额定容量达不到板料厚度压头所需力量,导致压头出现超标直边,,为此,为了防止超标直边的出现,被动的加长板料长度,即在板料两端头各自延长预留长度50mm以上,瓦片卷制成形后,再在其两端窃取多余长度余量。
四辊卷板机设计毕业论文

四辊卷板机设计毕业论文目录前言 (1)第1章绪论 (2)1.1卷板的分类及特点 (2)1.2卷板机的分类及特点 (2)1.3 W12X2000型四辊卷板机的用途 (5)1.4 传动系统设计 (6)第2章卷板机轴辊受力分析 (7)2.1作用在卷板机辊子上的弯曲扭矩 (7)2.2卷板机的空载扭矩 (8)2.3四辊卷板机的卷板力 (8)第3章电动机的选择与计算 (12)3.1功率计算 (12)3.2电动机的选择 (12)第4章主减速器的设计 (14)4.1电动机的确定 (14)4.2 传动比的分配 (15)4.3传动系统的运动和动力参数设计 (15)4.4 高速级斜齿圆柱齿轮传动的设计计算 (17)4.4.1选择精度等级,材料和齿数 (17)4.4.2 按齿面接触强度设计 (17)4.4.3按齿根弯曲疲劳强度设计 (21)4.4.4几何尺寸计算 (21)4.5中间级斜齿圆柱齿轮传动的设计计算 (22)4.5.1选择精度等级,材料和齿数 (22)4.5.2. 按齿面接触强度设计 (22)4.5.3.按齿根弯曲疲劳强度设计 (24)4.5.4几何尺寸计算 (26)4.6 低速级斜齿圆柱齿轮传动的设计计算: (26)4.6.1选择精度等级,材料和齿数 (26)4.6.2. 按齿面接触强度设计 (27)4.6.3按齿根弯曲疲劳强度设计 (29)4.6.4几何尺寸计算 (30)4.7高速轴的设计以及轴的校核 (32)第5章侧辊传动系统的设计 (36)5.1侧辊电动机的确定 (36)5.2侧辊减速器的确定 (36)5.3蜗轮蜗杆传动设计 (36)第6章下辊筒液压缸的设计 (41)6.1下辊液压系统的工作原理 (41)6.2下辊筒液压缸设计 (42)第7章辊筒轴的强度校核 (47)第8章专题论文 (50)8.1前言 (50)8.2四辊卷板机工作原理 (50)8.3液压同步控制系统研究及设计原理 (52)8.4.结论 (53)致谢 (54)参考文献 (55)前言我所设计的这台四辊卷板机由四个辊筒所组成,其中一个上辊、两个侧辊和一个下辊。
四辊卷板机标准

四辊卷板机标准一、引言四辊卷板机是一种广泛应用于金属加工领域的设备,用于将金属板卷进行平整或卷曲。
它的作用是将厚度不均匀的金属板材经过辊筒的作用,使其变得更加平整,达到所需的规格要求。
本文将深入探讨四辊卷板机标准及其应用。
二、四辊卷板机的基本原理四辊卷板机由上辊、下辊、左辊和右辊组成,其中,左右辊位于上下辊的中间位置。
通过控制辊筒的转动方向和速度,可以实现对金属板材的卷取、铺平和拉伸等操作。
主要的功能包括:1.卷取:将金属板材卷绕成卷形,方便储存和运输;2.铺平:将金属板材卷展开并平整,使其具备一定的平整度;3.拉伸:通过辊筒的作用,使金属板材发生一定的拉伸变形,以满足特定的加工要求。
三、四辊卷板机标准的重要性四辊卷板机标准是保证设备质量、安全性和可靠性的重要依据。
通过制定和遵循标准,可以确保四辊卷板机在设计、制造、安装和使用过程中符合相关要求,从而降低事故风险,提高生产效率和产品质量。
标准主要包括以下几个方面的内容:1. 设备要求•机床结构:包括辊筒直径、辊筒材质、辊筒表面硬度等要求;•动力系统:包括主电机功率、传动装置和传动比例等要求;•控制系统:包括控制方式、控制精度和安全保护装置等要求。
2. 使用要求•操作规程:包括设备的启停、调试和维护等操作规范;•安全要求:包括辊筒保护装置、急停系统和紧急救援措施等要求;•维护要求:包括设备的定期检修、润滑和清洁等要求。
3. 加工要求•加工能力:包括辊筒直径对应的最大板材宽度和最小板材厚度等要求;•加工质量:包括平整度、表面光洁度和尺寸偏差等要求;•加工速度:包括最大卷取速度和最大铺平速度等要求。
四、四辊卷板机标准的国际化趋势随着全球经济一体化的推进和国际贸易的发展,四辊卷板机标准逐渐朝着国际化方向发展。
国际标准化组织(ISO)和各国相关标准化组织联合制定了一系列涵盖设备设计、制造、使用和安全方面的国际标准。
通过遵循国际标准,可以提高设备的交互性、兼容性和可替代性,促进全球设备贸易的便利化。
四辊卷板机操作规程

四辊卷板机操作规程1.引言本操作规程适用于使用四辊卷板机的操作人员。
四辊卷板机是一种常用的金属加工设备,用于对金属板材进行卷板和成型。
为了确保操作人员的安全和设备的正常运行,遵循以下规程是必要的。
2.操作准备在开始操作四辊卷板机之前,操作人员应做好以下准备工作:检查四辊卷板机的工作区域,确保周围没有杂物和障碍物;确保四辊卷板机的电源和控制系统正常工作;检查四辊卷板机的润滑系统,确保润滑油充足;穿戴适当的个人防护装备,包括安全帽、护目镜和手套;熟悉四辊卷板机的操作面板和各个控制按钮的功能。
3.操作步骤按照以下步骤操作四辊卷板机:1.打开四辊卷板机的电源开关;2.将待加工的金属板材放置在四辊卷板机的进料台上,并通过压料器固定;3.根据需要调整四辊卷板机的辊子间距,保持合适的卷板厚度;4.通过操作面板上的控制按钮,启动四辊卷板机的卷板功能;5.监控卷板过程中的压力和速度,确保加工质量;6.当金属板材完成卷板后,停止四辊卷板机的运行;7.关闭四辊卷板机的电源开关。
4.安全注意事项在操作四辊卷板机时,操作人员应注意以下安全事项:避免将手部接近卷板机的辊子,以免被夹伤;不得随意调整四辊卷板机的辊子间距,必要时需停机后进行调整;维护好四辊卷板机的润滑系统,确保辊子的顺畅运转;在操作过程中,及时清理碎屑和废料,以保持工作区域的清洁;遇到异常情况或设备故障时,应立即停止操作,并向维修人员报告。
5.总结四辊卷板机的操作规程对操作人员的安全和设备的正常运行都至关重要。
遵循操作规程,正确操作四辊卷板机,可以确保加工质量和提升工作效率。
在操作过程中务必注意安全事项,并及时进行设备维护和检修。
以上为四辊卷板机操作规程的内容,参照该规程进行操作,可确保安全和高效完成工作。
赛乐四辊卷板机安全操作及保养规程

赛乐四辊卷板机安全操作及保养规程前言赛乐四辊卷板机是一种常用于加工金属板材的机械设备,采用四辊卷制工艺,能够高效地完成板材的弯曲和卷曲。
然而,由于其操作涉及高速旋转的辊轮和较高的机械压力,使用不当可能会导致人身安全事故或机器设备损坏。
因此,为了确保操作人员的安全和设备的正常运行,本文将介绍赛乐四辊卷板机的安全操作规程及保养维护方法。
安全操作规程1. 操作前须知在进行赛乐四辊卷板机的操作前,必须先了解以下内容:•机器的工作原理、性能和结构;•外观检查,确保机器没有松动、锈蚀及异物等;•机器的安全装置是否正常,如手动重置开关、急停按钮、安全门等;•切勿戴宽松衣物、珠宝、手套、脚套等易被机器卷入的物品;•操作人员需认真阅读和理解操作手册。
2. 操作时应注意的事项操作人员需在作业前佩戴好个人防护装备(如安全帽、护目镜、防护手套等),确认机器处于停止状态后,按以下步骤操作:1.启动前检查:确认无异物、工具、人员等在卷板机工作区域内,并检查机器的润滑油量及质量是否充足;2.操作前加油:用油枪对卷板机的润滑点进行加油,按照润滑油说明书的要求进行加油;3.打开电源开关:按照说明书的要求按下启动开关,使卷板机启动;4.调整卷板机辊轮:根据板材厚度、长度等参数,调整卷板机辊轮,使其与板材紧密接触;5.开始卷制板材:将板材放在卷板机的进料口处,然后按照说明书的要求进行开始卷制板材;6.注意板材的卷曲方向:在操作时应注意板材卷曲方向,避免与预期方向相反;7.确认卷板机停止:当卷板机完成工作后,应按照说明书的要求停止机器,并确认机器完全停止后再将板材取出;8.关闭电源开关:操作完成后应立即关闭电源开关;3. 常见的安全事故和对策在使用赛乐四辊卷板机时,常见的安全事故有以下几种:1.手指被卷入机器:卷板机轧制过程中,手指被卷入机器,造成受伤;2.处理过程中杂物进入机器:散落在现场的打螺丝等杂物被卷入辊轮内,引起机械故障;3.操作人员不当:懈怠、麻痹、操作不当引起卷板机出现故障,严重损坏机器设备甚至人身安全事故。
四辊卷板机卷锥技巧

四辊卷板机卷锥技巧
一、材料准备
在进行四辊卷板机卷锥操作前,需要准备以下材料:
1.板材:选择适合卷锥的板材,如不锈钢、镀锌板、铝合金等。
2.垫板:用于支撑板材,防止卷锥过程中板材变形。
3.量具:测量板材的长度、宽度和厚度,以确保卷锥效果符合要求。
4.夹具:用于固定板材,以便进行卷锥操作。
二、调整四辊间距
在开始卷锥操作前,需要调整四辊间距,以适应不同厚度的板材。
调整间距时,应确保两辊之间的距离与板材厚度相适应,以免造成板材弯曲或损坏。
三、卷锥操作
1.将板材放置在垫板上,用夹具固定住。
2.调整四辊间距,使其与板材厚度相匹配。
3.开启四辊卷板机,将板材卷入四辊之间。
4.在卷锥过程中,需要不断调整四辊的位置,以确保卷锥效果均匀。
5.当板材完全卷入四辊后,逐渐增加压力,使板材逐渐成型。
6.完成卷锥操作后,将板材取出,并进行质量检查。
四、质量检查
完成卷锥操作后,需要进行质量检查,以确保卷锥效果符合要求。
检查内容包括:
1.检查板材的形状是否符合要求,是否出现弯曲、变形等现象。
2.检查板材的边缘是否整齐,无毛刺、裂纹等现象。
3.检查板材的表面质量,无划痕、压痕等现象。
4.检查板材的尺寸是否符合要求,包括长度、宽度和厚度等。
五、安全操作
在进行四辊卷板机卷锥操作时,需要注意以下安全事项:
1.确保四辊卷板机处于良好状态,无故障隐患。
2.操作时应穿戴防护眼镜、手套等个人防护用品。
- 1、下载文档前请自行甄别文档内容的完整性,平台不提供额外的编辑、内容补充、找答案等附加服务。
- 2、"仅部分预览"的文档,不可在线预览部分如存在完整性等问题,可反馈申请退款(可完整预览的文档不适用该条件!)。
- 3、如文档侵犯您的权益,请联系客服反馈,我们会尽快为您处理(人工客服工作时间:9:00-18:30)。
M. Hua et aL / Journal of Materials Processing Technology 48 (1995) 159-172
161
2. Four-Roll Bender Configurations and Bending Sequences
Figure 1 shows the configuration of the operational roll and plate specimen of a four-roll horizontal bender. Generally, in such benders the top roll is normally connected to a drive system so that the continuous conveyance of a bent plate can be performed. At this instance the two side rolls and the bottom pinch roll are free to rotate but are powered to translate along their predetermined directions in their respective positional planes. The positional plane of either the pre-bending active or the pre-bending inactive (subsequently referred to as pre-active or pre-inactive, respectively) side roll powered direction depends upon the geometric setting of Xo and -Xo, and also upon the inclination of the preliminary positional angle, ~ and -~o. For a set geometry of a four-roll bender, the positional powering centre, Op (Figures 6 and 7) of the preactive and the preinactive side rolls remains constant. However, the instantaneous contact centre, Oo, and the instantaneous contact angle, ~o, of the bent plate and the active side roll, varies as bending proceeds. When in operation gripping of a plate is performed by moving the axis of the bottom roll centre towards that of the top roll. For a particular fourroll horizontal bender with the top pinch roll rotational driven both clockwise and anticlockwise, the nomination of the pre-active and pre-inactive side roll is arbitrary, unless specific plate handling features are allocated to the bender. To assist further discussion, the r.h.s, side roll is referred to as the pre-active side roll and the I.h.s. side roll as the preinactive side roll. Figure 2 shows the detailed operational sequences for thin plate four-roll bending. In principle, they consist of some or all of the following modes: (i) edge setting preparation, (ii) edge prebending, (iii) pre-bending continuous bending, (iv) roller swapping bending, (v) steady continuous bending and (vi) completion roller bending. The combination of the bending modes depends mainly upon the material flexural rigidity and the bender capacity, and partly upon the size and accuracy required of the finished tubular sections. It sometimes even depends upon the personal preference of the operators.
1. Introduction
Large cylindrical tubular sections are widely used in heavy engineering and civil construction environments. A relatively economical method of production of various sizes of tubes is to weld cylindrical sections bent from plates. In the metal bending industry, one of the most versatile techniques for the production of large diameter tubes is the continuous four-roll plate bending process. The advantage of the technique over the other processes of stampbending, stretch-bending and pressbrake bending, is to reduce the setting up time, to reduce cost in tooling investment, to minimise the length of the straight end-edge remaining in the finished product (subsequently, lowering the machining cost and material wastage), and to achieve much greater finished dimensional accuracy and better circularity of an accomplished cylindrical section. In addition, it only occupies a relatively small space on the shop floor. Generally, the completed tube formed has only a single welded seam. By Data Products Components(HK) Ltd. Sime Darby Industrial Estate Centre, 420 Kwung Tong Rd, Kowloon, Hong Kong.
Elsevier Science S.A.
S S D I 0924-0136(94)01646-I
160
M. Hua et aL / Journal o f Materials Processing Technology 48 (1995) 159-172
continuous four-roll plate bending [5] was initiated at Aston University, Birmingham, England. Some preliminary results from bending aluminium plates, with thicknesses of 8mm and
operating a roller bender at its designed capacity, a comprehensive range of tubediameters with a minimum just larger than that of the top roll of the bender, for different plate thicknesses and widths, can be produced. Despite the versatility of the process, there is limited understanding of the bending mechanisms and available literature concerning the process is limited. Although Winshop [1] discussed various configurations of the threeand four-roll plate benders, he did not provide any insight into the bending mechanisms. Roggendorf and Haeusler [2] only traced the historical development of the Haeusler roller benders before 1979, whilst Basset and Johnson [3] and Hansen and Jannerup [4] initiated merely the theoretical analysis for three-roll pyramid benders. Consequently, the operation of the process is heavily dependent on the experience of skilled operators and working by "template" or "trial and error" remains common practice. In order to gain an understanding of the bending process and to introduce C.N.C. operation, a study of Departmentof MechanicalEngineering, Universityof Adelaide,SouthAustralia5005