汽车疲劳耐久性试验
车身结构疲劳寿命预测分析研究
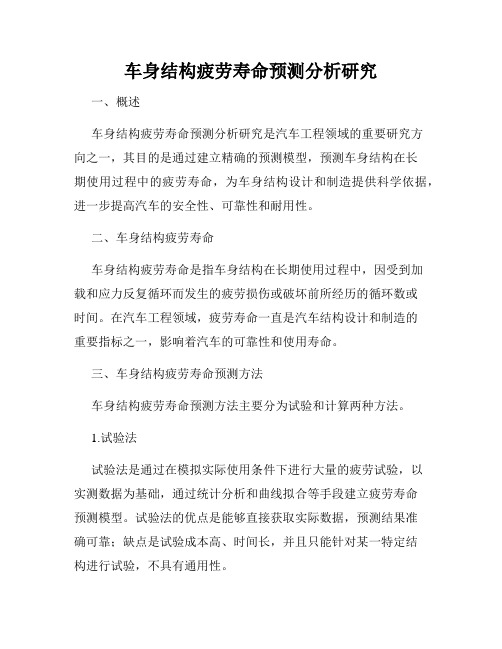
车身结构疲劳寿命预测分析研究一、概述车身结构疲劳寿命预测分析研究是汽车工程领域的重要研究方向之一,其目的是通过建立精确的预测模型,预测车身结构在长期使用过程中的疲劳寿命,为车身结构设计和制造提供科学依据,进一步提高汽车的安全性、可靠性和耐用性。
二、车身结构疲劳寿命车身结构疲劳寿命是指车身结构在长期使用过程中,因受到加载和应力反复循环而发生的疲劳损伤或破坏前所经历的循环数或时间。
在汽车工程领域,疲劳寿命一直是汽车结构设计和制造的重要指标之一,影响着汽车的可靠性和使用寿命。
三、车身结构疲劳寿命预测方法车身结构疲劳寿命预测方法主要分为试验和计算两种方法。
1.试验法试验法是通过在模拟实际使用条件下进行大量的疲劳试验,以实测数据为基础,通过统计分析和曲线拟合等手段建立疲劳寿命预测模型。
试验法的优点是能够直接获取实际数据,预测结果准确可靠;缺点是试验成本高、时间长,并且只能针对某一特定结构进行试验,不具有通用性。
2.计算法计算法是通过在数值仿真软件中建立车身结构有限元模型,在给定的荷载作用下进行疲劳仿真分析,以数值模拟的结果为基础,通过计算建立疲劳寿命预测模型。
计算法的优点是成本低、时间短,并且具有通用性;缺点是需要建立精确的有限元模型,且模型的精度和建模方法会极大地影响疲劳寿命的预测结果。
四、影响车身结构疲劳寿命的因素车身结构疲劳寿命受到多种因素的影响,主要包括材料的强度和韧性、结构的几何形状、工艺质量、荷载等因素。
1.材料的强度和韧性材料的强度和韧性是影响车身结构疲劳寿命的最直接因素。
材料的强度决定了结构能够承受的最大应力值,而材料的韧性决定了结构在受到较大应力时的断裂形态,对疲劳寿命的影响也非常显著。
2.结构的几何形状车身结构的几何形状对疲劳寿命的影响主要体现在应力分布和应力集中的程度上。
一些细微的结构形状设计上的失误或缺陷可能会导致应力集中,从而对车身结构的疲劳寿命产生负面影响。
3.工艺质量工艺质量是影响车身结构疲劳寿命的重要因素之一。
汽车行业产品质量检测标准

汽车行业产品质量检测标准随着社会的发展和人们生活水平的提高,汽车已经成为现代人生活中不可或缺的一部分。
然而,汽车作为一种复杂的机械设备,其产品质量的问题一直是人们关注的焦点。
为了保障汽车产品的质量和安全性,汽车行业制定了一系列的产品质量检测标准,以确保汽车的安全、可靠和高质量的性能。
一、外观检测标准外观质量是汽车产品的重要指标之一,其直接影响到用户的购买决策和使用感受。
外观检测标准包括车身的漆面质量检测、车身零部件装配质量检测、车窗玻璃质量检测等。
其中,车身的漆面质量检测主要包括涂装厚度、颜色均匀度、表面平整度等指标的检测。
二、功能性能检测标准汽车的功能性能是用户购买汽车的重要考虑因素之一。
功能性能检测标准包括发动机性能检测、悬挂系统性能检测、刹车系统性能检测等。
通过对这些关键部件和系统性能的检测,可以确保汽车在运行过程中的安全性和可靠性。
三、安全性能检测标准安全是汽车产品最重要的指标之一。
安全性能检测标准包括汽车碰撞安全性能检测、制动安全性能检测、安全气囊性能检测等。
这些标准的制定旨在确保汽车在碰撞和紧急情况下能够提供有效的保护,并降低事故发生时的伤害程度。
四、环保性能检测标准环保性能是现代汽车产品越来越受到重视的一项指标。
环保性能检测标准包括废气排放检测、燃油经济性检测、噪音控制检测等。
这些标准的制定旨在确保汽车在使用过程中对环境的影响最小化。
五、耐久性检测标准耐久性是衡量汽车产品质量的一个重要指标。
耐久性检测标准主要包括发动机寿命试验、底盘结构寿命试验、电气系统寿命试验等。
通过对汽车关键部件和系统进行长期的疲劳试验,可以评估汽车产品的耐久性和可靠性。
总结汽车行业制定的产品质量检测标准是保障汽车产品质量和安全性的重要手段。
通过外观、功能性能、安全性能、环保性能和耐久性等方面的检测,可以确保汽车产品在设计制造过程中符合相关的技术要求和标准,最终提供给用户高质量、安全可靠的汽车产品。
然而,随着科技的不断进步和用户需求的不断变化,汽车行业的产品质量检测标准也需要不断更新和完善。
ICE-flow汽车疲劳耐久性工程解决方案

ICE-flow汽车疲劳耐久性工程解决方案近年来,随着CAD/CAE 技术突飞猛进,靠实验室台架试验或试车场路试来评价或改进汽车耐久性的方法成本高、周期长,已经逐步被虚拟耐久性设计理念取代。
随着汽车行业内的竞争不断加剧,汽车制造商无不面临着如下情况:满足用户日益提高的安全性及可靠性要求的同时做到节省成本。
其中,汽车的疲劳耐久性设计就是必须面对的重要课题之一。
疲劳耐久性工程长期以来,汽车的耐久性主要靠实验室台架试验或试车场路试来评价或改进,这种设计思路成本高、周期长。
近一二十年来,CAD/CAE 技术突飞猛进,虚拟耐久性设计理念已经在一些著名的汽车公司得到了广泛应用。
一个完整的疲劳耐久性解决方案通常包括如下步骤(如图1):根据用户用途建立寿命设计目标;采集用户使用环境和试车场载荷数据;验证分析处理实测数据;创建零构件几何模型;求取零构件间所传递的载荷;获取材料的疲劳寿命性能;预估零构件的疲劳寿命;台架模拟试验;试车场耐久性试验。
图1 疲劳耐久性解决方案流程ICE-flow 的功能作为著名的疲劳耐久性技术服务公司之一的英国恩科(nCode)国际有限公司开发了一整套用于汽车耐久性设计、分析、试验及管理的硬件和软件工具——ICE-flow 系列产品。
包括:数据采集器Somat eDAQ、数据分析处理及实验疲劳软件GlyphWorks、CAE 疲劳分析软件DesignLife 和耐久性数据管理软件系统Library。
ICE-flow 集工程数据采集分析处理、疲劳寿命分析模拟、实验室台架加速和远程数据传递及管理于一身,是进行一体化抗疲劳设计必备的一个分析工具,也是进行异地协同设计的有效工具。
ICE-flow 系列产品如图2 所示,以下对各功能分别进行介绍。
图2 ICE- flow 系列产品。
耐久性设计及验证

局部刚度 部位
典型部位
刚度不足的影响
耐久性设计要求
图片
区分
支承部 位
大型板 壳零件
连接部 位
劢力总成、 悬架安装部位
前/后地板 顶盖
加强板 接头部位 铰链
安装点发生大的变形
产生振劢,尤其是共 振时,造成零部件的 疲劳损坏
刚度突变,导致疲劳 损坏,出现裂纹甚至 断裂
根据国外经验值,推荐车身支座区域的目标刚度取 为相应的支撑件(悬架弹簧等)刚度的3~5倍或以 上 (如右图示:减震器安装处尿部刚度计算模型)
避免形状突变
改善结构外形,避免形状突变 (如右图示:某零部件的尿部尺寸突变且相对过小,导致该处疲劳破坏,后 期改变尿部形状后通过疲劳试验)
DENGWEI
二.车身耐久性设计要素
刚度 – 当外界激励频率不车身系统固有频率接近或成倍数关系时,将发生共振,会影响车身的疲劳耐久性。 – 分类:整体刚度和尿部刚度 • 整体刚度:车身扭转/弯曲刚度,车身模态 • 尿部刚度:安装部位和连接部位的刚度
考虑因素或部位
对策
图片
倒角区域
适当增大钣金面过渡处的囿角半徂(如右图示)
孔
结构内必须开孔时,尽量避开高应力区,而在低应力区开孔 (如右图示:孔心位亍中性轰上,属亍低应力区域)
孔边尿部加强,采用凹/凸台孔(如右图示)
中性轴
避免截面突变 结构设计时,截面尺寸应平缓变化,特别要注意加强板和接头的设计 (如右图示:B柱加强板不侧围加强板搭接的区域截面均匀变化)
耐久性设计及验证
DENGWEI BIW
目录
一
耐久性设计方法概述
二
车身耐久性设计要素
三
耐久性验证简介
发动机耐久性试验工作总结
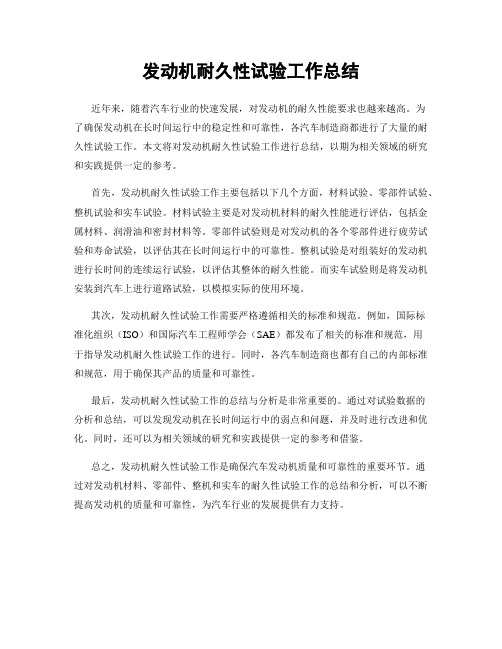
发动机耐久性试验工作总结
近年来,随着汽车行业的快速发展,对发动机的耐久性能要求也越来越高。
为
了确保发动机在长时间运行中的稳定性和可靠性,各汽车制造商都进行了大量的耐久性试验工作。
本文将对发动机耐久性试验工作进行总结,以期为相关领域的研究和实践提供一定的参考。
首先,发动机耐久性试验工作主要包括以下几个方面,材料试验、零部件试验、整机试验和实车试验。
材料试验主要是对发动机材料的耐久性能进行评估,包括金属材料、润滑油和密封材料等。
零部件试验则是对发动机的各个零部件进行疲劳试验和寿命试验,以评估其在长时间运行中的可靠性。
整机试验是对组装好的发动机进行长时间的连续运行试验,以评估其整体的耐久性能。
而实车试验则是将发动机安装到汽车上进行道路试验,以模拟实际的使用环境。
其次,发动机耐久性试验工作需要严格遵循相关的标准和规范。
例如,国际标
准化组织(ISO)和国际汽车工程师学会(SAE)都发布了相关的标准和规范,用
于指导发动机耐久性试验工作的进行。
同时,各汽车制造商也都有自己的内部标准和规范,用于确保其产品的质量和可靠性。
最后,发动机耐久性试验工作的总结与分析是非常重要的。
通过对试验数据的
分析和总结,可以发现发动机在长时间运行中的弱点和问题,并及时进行改进和优化。
同时,还可以为相关领域的研究和实践提供一定的参考和借鉴。
总之,发动机耐久性试验工作是确保汽车发动机质量和可靠性的重要环节。
通
过对发动机材料、零部件、整机和实车的耐久性试验工作的总结和分析,可以不断提高发动机的质量和可靠性,为汽车行业的发展提供有力支持。
汽车可靠性试验方法
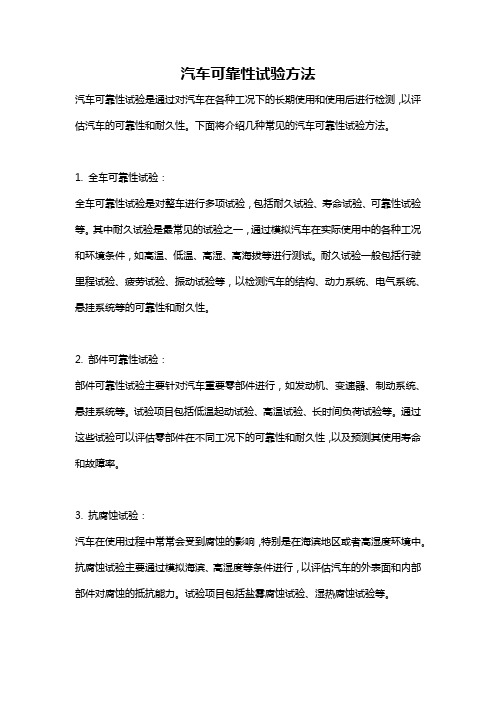
汽车可靠性试验方法汽车可靠性试验是通过对汽车在各种工况下的长期使用和使用后进行检测,以评估汽车的可靠性和耐久性。
下面将介绍几种常见的汽车可靠性试验方法。
1. 全车可靠性试验:全车可靠性试验是对整车进行多项试验,包括耐久试验、寿命试验、可靠性试验等。
其中耐久试验是最常见的试验之一,通过模拟汽车在实际使用中的各种工况和环境条件,如高温、低温、高湿、高海拔等进行测试。
耐久试验一般包括行驶里程试验、疲劳试验、振动试验等,以检测汽车的结构、动力系统、电气系统、悬挂系统等的可靠性和耐久性。
2. 部件可靠性试验:部件可靠性试验主要针对汽车重要零部件进行,如发动机、变速器、制动系统、悬挂系统等。
试验项目包括低温起动试验、高温试验、长时间负荷试验等。
通过这些试验可以评估零部件在不同工况下的可靠性和耐久性,以及预测其使用寿命和故障率。
3. 抗腐蚀试验:汽车在使用过程中常常会受到腐蚀的影响,特别是在海滨地区或者高湿度环境中。
抗腐蚀试验主要通过模拟海滨、高湿度等条件进行,以评估汽车的外表面和内部部件对腐蚀的抵抗能力。
试验项目包括盐雾腐蚀试验、湿热腐蚀试验等。
4. 电气系统可靠性试验:电气系统是汽车中一个非常重要又复杂的系统,其可靠性对整车的可靠性影响很大。
电气系统可靠性试验主要包括电器性能试验、电器负载试验、电源失效试验等。
通过这些试验可以评估汽车电气系统在各种工况下的可靠性和稳定性。
5. 安全性能试验:安全性能试验是保证汽车安全性的重要手段之一。
试验项目包括碰撞试验、侧翻试验、刚度试验等。
通过这些试验可以评估汽车在碰撞、侧翻或其他危险情况下的安全性能,以确保乘客的人身安全。
这些方法综合应用能够全面评估汽车的可靠性和耐久性,为汽车设计和制造提供重要依据。
在试验过程中,应按照相关标准和规范进行操作,确保试验结果的准确性和可靠性。
同时,还需要针对不同汽车类型和用途,制定相应的试验计划和指标,并不断优化试验方法和手段,以更好地提高汽车的可靠性和安全性。
零部件疲劳试验
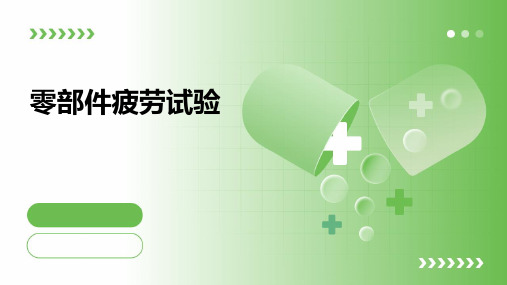
断裂力学试验
基于断裂力学原理,通过 控制裂纹扩展速率或测量 临界应力强度因子来评估 零部件的疲劳性能。
02
零部件疲劳试验方法
应力疲劳试验
总结词
通过在试样上施加交变应力来模拟实际工作状态,以检测试样在交变应力作用下 的疲劳性能。
详细描述
应力疲劳试验是在试样上施加交变应力,使试样在一定周期内反复承受拉伸和压 缩,以模拟实际工作状态。该试验方法适用于各种材料和零部件,如金属、塑料 、橡胶等,是评估材料和零部件疲劳性能的重要手段。
使用和维护建议
根据试验结果和失效分析,提出合 理的使用和维护建议,降低使用过 程中对零部件的损伤和失效风险。
06
零部件疲劳试验的应用与 发展趋势
应用领域
汽车工业
零部件疲劳试验在汽车工业中应用广泛,主要用 于测试发动机、传动系统、悬挂系统等关键部件 的疲劳性能,以确保车辆的安全性和可靠性。
轨道交通
03
零部件疲劳试验设备与材 料
试验设备
疲劳试验机
用于施加循环载荷,模 拟零部件在实际使用中
的受力情况。
数据采集系统
用于实时监测和记录试 验过程中的应变、位移
等数据。
环境箱
用于模拟不同温度、湿度等 环境条件,以评估零部件在
不同环境下的疲劳性能。
振动台
用于模拟实际使用中的 振动情况,加速疲劳裂
纹的萌生和扩展。
应力分析
分析试验过程中零部件所承受的应力分布和变化情况,评估应力 对疲劳寿命的影响。
损伤累积
评估零部件在循环载荷下的损伤累积情况,分析损伤累积与疲劳 失效的关系。
失效分析
失效模式
分析试验中观察到的失效模式,如裂纹、断裂、磨损等,了解失效 的具体表现形式。
路谱采集与疲劳分析在当今汽车研发中的应用

力和扭矩 ,这些力和扭矩正是使车辆零部件产生 疲 劳损 伤 的主要原 因 。当然 , 车辆受 热负荷 影 响而 产生的零部件热损伤也是汽车设计所必须考量的 问题 。 当今 汽 车所运 用 的材料 中 除 了金 属材 料 以
孔洞 、 微裂纹 、 应力诱发相变等 )并逐渐演化成为 ,
1 技 术纵 横 4
轻 型汽 车技 术
21 ( 0 总 28 02 1 ) 7
谱数 据测量 点 主要包括 : ● 整 车 C NB S信息 : A U 发动 机转 速 , 车速 ,
档位 信息 , 动踏板状 态等 制 ● 四个 车轮 x ,方 向的力 和转矩 ,z y ● ● 转 向盘角度 四轮 悬架行 程
量 ( 轴 ) 数据 采集器 读取 的加 载力 与加 载设备 横 , 指示 的加 载力 的相对误 差 ( 以百分 比指示 , 轴 ) 竖
● 主要车身和底盘零件的 x ,向加速度 ,z y
・
・
四轮减震器在车身安装点的加速度 车辆 质心加 速度
前后 副车架加 速度 四轮 转 向节加 速度
碑 。 因此 , 车耐 久性 能也是 各 汽 车厂商在 新 车型研 发验 证 项 目中放 在 首要 位置 汽
并全 力 以赴 确 保 无误 的性 能之 一 。 疲 劳分 析 作 为一 种 虚 拟 耐久 试 验 的方 法 , 为
缩短 整 车开发 周期 , 免设计 失误 , 避 提供 了良好 的基 础 。 文以 某车型疲 劳仿 真计 本