概述变速器的设计与噪声
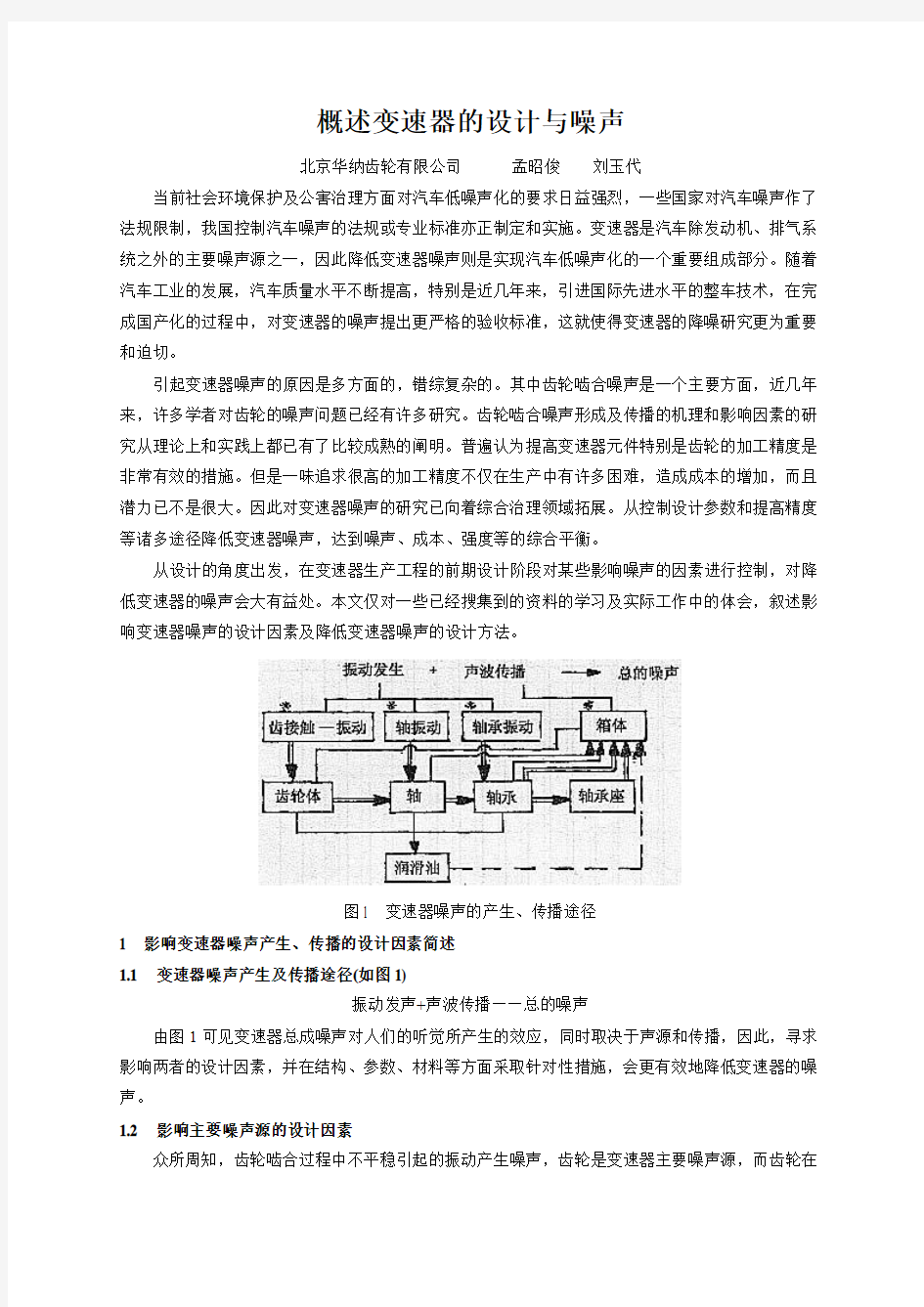
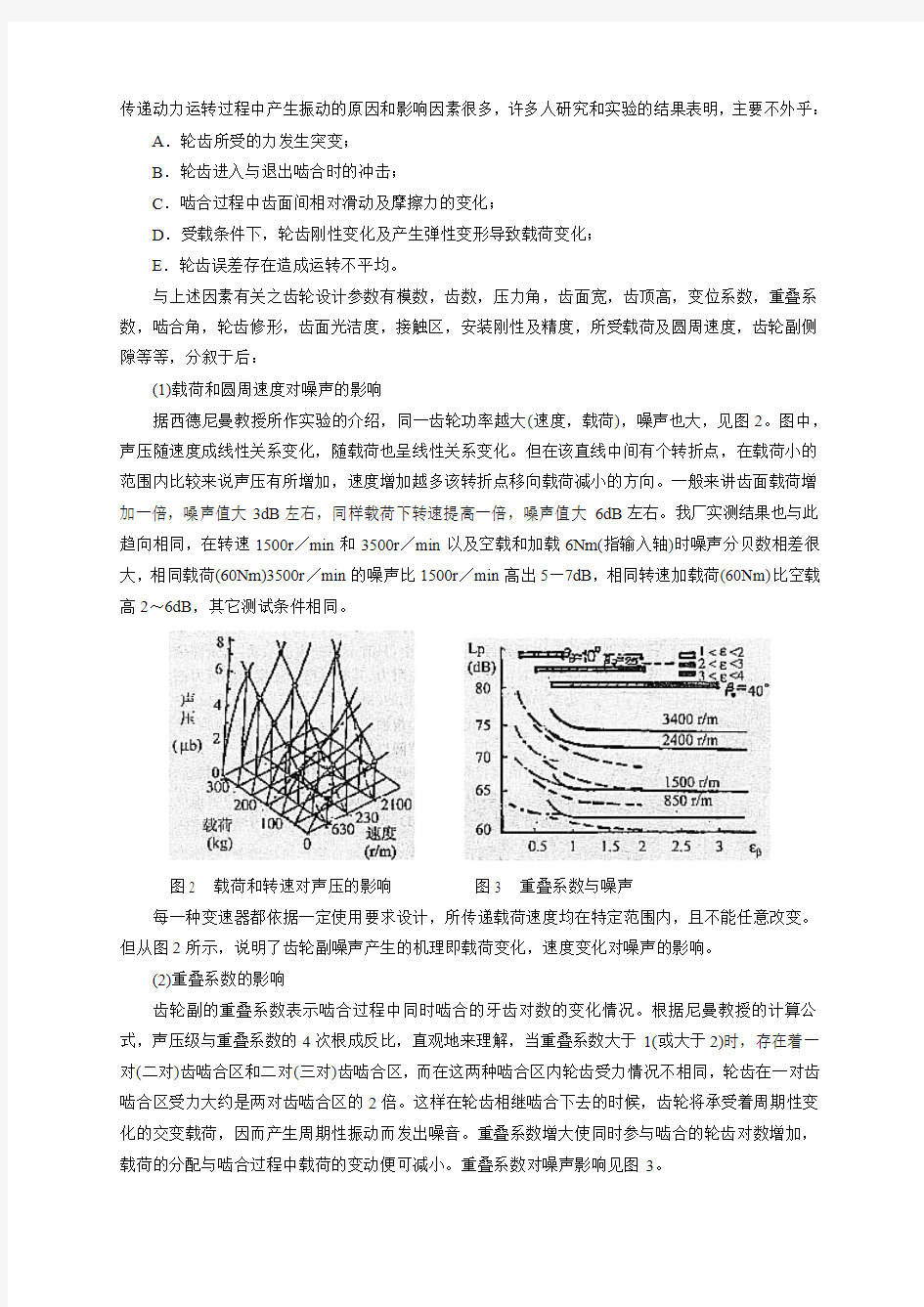
概述变速器的设计与噪声
北京华纳齿轮有限公司孟昭俊刘玉代
当前社会环境保护及公害治理方面对汽车低噪声化的要求日益强烈,一些国家对汽车噪声作了法规限制,我国控制汽车噪声的法规或专业标准亦正制定和实施。变速器是汽车除发动机、排气系统之外的主要噪声源之一,因此降低变速器噪声则是实现汽车低噪声化的一个重要组成部分。随着汽车工业的发展,汽车质量水平不断提高,特别是近几年来,引进国际先进水平的整车技术,在完成国产化的过程中,对变速器的噪声提出更严格的验收标准,这就使得变速器的降噪研究更为重要和迫切。
引起变速器噪声的原因是多方面的,错综复杂的。其中齿轮啮合噪声是一个主要方面,近几年来,许多学者对齿轮的噪声问题已经有许多研究。齿轮啮合噪声形成及传播的机理和影响因素的研究从理论上和实践上都已有了比较成熟的阐明。普遍认为提高变速器元件特别是齿轮的加工精度是非常有效的措施。但是一味追求很高的加工精度不仅在生产中有许多困难,造成成本的增加,而且潜力已不是很大。因此对变速器噪声的研究已向着综合治理领域拓展。从控制设计参数和提高精度等诸多途径降低变速器噪声,达到噪声、成本、强度等的综合平衡。
从设计的角度出发,在变速器生产工程的前期设计阶段对某些影响噪声的因素进行控制,对降低变速器的噪声会大有益处。本文仅对一些已经搜集到的资料的学习及实际工作中的体会,叙述影响变速器噪声的设计因素及降低变速器噪声的设计方法。
图l 变速器噪声的产生、传播途径
1 影响变速器噪声产生、传播的设计因素简述
1.1 变速器噪声产生及传播途径(如图1)
振动发声+声波传播——总的噪声
由图1可见变速器总成噪声对人们的听觉所产生的效应,同时取决于声源和传播,因此,寻求影响两者的设计因素,并在结构、参数、材料等方面采取针对性措施,会更有效地降低变速器的噪声。
1.2 影响主要噪声源的设计因素
众所周知,齿轮啮合过程中不平稳引起的振动产生噪声,齿轮是变速器主要噪声源,而齿轮在
传递动力运转过程中产生振动的原因和影响因素很多,许多人研究和实验的结果表明,主要不外乎:A.轮齿所受的力发生突变;
B.轮齿进入与退出啮合时的冲击;
C.啮合过程中齿面间相对滑动及摩擦力的变化;
D.受载条件下,轮齿刚性变化及产生弹性变形导致载荷变化;
E.轮齿误差存在造成运转不平均。
与上述因素有关之齿轮设计参数有模数,齿数,压力角,齿面宽,齿顶高,变位系数,重叠系数,啮合角,轮齿修形,齿面光洁度,接触区,安装刚性及精度,所受载荷及圆周速度,齿轮副侧隙等等,分叙于后:
(1)载荷和圆周速度对噪声的影响
据西德尼曼教授所作实验的介绍,同一齿轮功率越大(速度,载荷),噪声也大,见图2。图中,声压随速度成线性关系变化,随载荷也呈线性关系变化。但在该直线中间有个转折点,在载荷小的范围内比较来说声压有所增加,速度增加越多该转折点移向载荷减小的方向。一般来讲齿面载荷增加一倍,噪声值大3dB左右,同样载荷下转速提高一倍,噪声值大6dB左右。我厂实测结果也与此趋向相同,在转速1500r/min和3500r/min以及空载和加载6Nm(指输入轴)时噪声分贝数相差很大,相同载荷(60Nm)3500r/min的噪声比1500r/min高出5—7dB,相同转速加载荷(60Nm)比空载高2~6dB,其它测试条件相同。
图2 载荷和转速对声压的影响图3 重叠系数与噪声
每一种变速器都依据一定使用要求设计,所传递载荷速度均在特定范围内,且不能任意改变。但从图2所示,说明了齿轮副噪声产生的机理即载荷变化,速度变化对噪声的影响。
(2)重叠系数的影响
齿轮副的重叠系数表示啮合过程中同时啮合的牙齿对数的变化情况。根据尼曼教授的计算公式,声压级与重叠系数的4次根成反比,直观地来理解,当重叠系数大于1(或大于2)时,存在着一对(二对)齿啮合区和二对(三对)齿啮合区,而在这两种啮合区内轮齿受力情况不相同,轮齿在一对齿啮合区受力大约是两对齿啮合区的2倍。这样在轮齿相继啮合下去的时候,齿轮将承受着周期性变化的交变载荷,因而产生周期性振动而发出噪音。重叠系数增大使同时参与啮合的轮齿对数增加,载荷的分配与啮合过程中载荷的变动便可减小。重叠系数对噪声影响见图3。
图4 齿轮模数与啮合起始点
图5 摩擦力、法向力示意图
(3)模数、齿数影响
一旦中心距确定,则齿数和愈大,模数愈小。相同重叠系数
下,较小模数之齿轮较之较大模数的齿轮的噪声敏感低,可理解
为模数小的齿轮啮合起始点曲率半径大,远离基圆,避开了滑动
比大摩擦力大的根部区域,由(1)式和图4明显可见。
同时,模数小,可使重叠系数加大,从而使载荷在轮齿上分配愈均匀;使传动愈平稳。
(4)压力角及齿高系数的影响
轮齿刚性对齿轮运转过程中轮齿上载荷变化有着直接的影
响,轮齿具有较大的“柔性”——即较低的刚性,则可以降低轮
齿啮入,啮出起始和终了点的载荷突变,并可在一定程度上弥补
轮齿误差引起的载荷变动。压力角愈小则轮齿刚度愈低,这种适
应性就愈强。
齿高系数愈大,则不仅重叠系数加大,而且齿变得更长,在
一定程度上增加其轮齿的“柔性”。
(5)变位系数的影响
由于轮齿啮合过程中,只有节点处为纯滚动,其余部位均存
在相对滑动,产生摩擦阻力。其相对滑动速度与摩擦力的大小方
向在节点上下是变化的。对于主动轮节圆以下部位(称为啮入段—
又叫进弧区)齿面相对滑动速度方向朝齿顶,摩擦阻力f P 朝齿根。
而在节圆以上部位(称为啮出段——又称退弧区)齿面间相对滑动
速度方向及摩擦阻力方向刚好相反,由于齿面摩擦阻力存在,使
得齿面法向力在啮入段和啮出段不同,见图5及公式(2)、(3),设n P 为法向力,μ为摩擦系数。 啮入段: )1(2x tg d M P b n αμ-=
(2) 啮出段: ()
x tg d M P b n αμ+=12 (3) 式中:M ——传递扭矩m N ?
b d ——基圆直径mm
μ——摩擦系数
n P ——齿面法向力
x α——接触点X 处压力角
注意从动轮法向力在节点上下两部位的变化与主动轮相反。
由此可见,如果主动轮啮入段减小,啮出段增大则将对降低噪声有利。
(6)齿面粗糙度的影响
齿表面粗糙度直接影响齿面间相对滑动的摩擦系数,特别在润滑不良或润滑油质量不好时,齿面越粗糙,摩擦系数就愈大,按式(2)、(3)则直接影响齿面法向力的变化。在高速运转时发出非常难听的尖叫声,齿面粗糙度对噪声的影响与齿轮运转速度和载荷也有关系。据Berthoud 对不同方法加工的齿轮所作的实验,当转速为550r /min ,载荷为0—30Nm 时,齿面粗糙度对噪声的影响不太大,但当转速大于800r /min ,载荷大于200Nm ,就可以明显地看出齿面粗糙度对噪声的影响,而且其差别随速度和载荷的增加而变大。所以对于变速器中速度较高之常啮合齿轮副,其齿面粗糙度一般要求比低档齿轮为高。西德ZF 公司该齿轮副采用磨齿,—则提高精度,二则提高表面粗糙度。
(7)齿轮副侧隙对噪声之影响
齿轮副侧隙及其变动量对噪声的影响特别表现在轻负荷,扭矩变化大时,(例如汽车发动机怠速时)高速工况,加速、减速时齿轮正反工作面交替变化,齿轮副侧隙偏大将会引起敲击,侧隙的变化量则是齿轮精度的综合反映,它直接影响齿轮运转的不平均性,见图6。
(8)螺旋角、齿面宽和接触区对噪声的影响
图6 中心距变动与噪声 图7 螺旋角和载荷与声压的关系 噪声与螺旋角β及齿宽的关系可归结为其与重叠系数的关系。在尼曼教授的计算公式中,噪声级与(2/1βtg -)成正比,螺旋角越大(不超过40?),或齿宽增大,重叠系数都增大,因而噪声降低。但是螺旋角与齿宽对噪声的影响是有限的。这种影响同时与载荷有关,在载荷较大时,螺旋角愈大,则噪声级愈小,见图7。
(9)轮齿误差及轮齿修形对噪声的影响。
无论如何,轮齿各类型误差总是客观存在的,不管是大是小。即使绝对准确的轮齿,由于安装误差及受载后的弹性变形的影响也会呈现啮合过程中的不均匀,因此,多年来许多研究者对轮齿特性、修形的原理、方法进行了大量的分析研究和实验。寻求具有一定轮齿几何特性的齿轮在特定载荷体特定使用条件下的最佳修形。对于某种齿轮,须经反复试验,才能得到理想的修形曲线。
1.3 影响噪声传播的设计因素
实际上耳闻之噪声是经固体传播和空气传播向外部发射的总噪声。
大量实验结果表明,这种发射噪声的声压近似地与箱壁振动加速度成正比;发射功率与发射面积成正比;固体传播噪声的能量密度大约为噪声能量密度的95%;箱壁阻止了空气传播噪声的绝大部分:
图8 润滑油量和粘度对噪声的影响
(1)箱体的形状、刚性、自振频率表面辐射面积及材料,表面上开设窗口的位置大小及总体布局均是噪声产生共振、声压合成、噪声发射影响的因素。
(2)轴及轴承的刚度、精度不仅影响自身振动而且做为固体传播噪声的环节也影响着噪声的发射。
(3)作为连体之离合器壳及后体零件自身的固有频率也极易与齿轮系振动产生共振而激发噪声和使声压合成。也是影响因素之一。
(4)润滑油质量及注油量。
有阻尼作用,且能防止齿面直接接触,故噪声一般随油量、油的粘度的增加而变小,而对于全为斜齿轮的变速器油量过多,搅拌损失增大油温上升,反而使噪声增大。图7为尼曼教授所做的润滑油对噪声影响之实验结果。
2 变速器的降噪设计方法
人们对各种影响因素做了大量分析、研究,提出许多有效控制措施,不过目前仍限于定性研究或个别因素在一定范围内的定量研究,迄今尚未见较为成熟,且能普遍应用于设计的定量的研究成果报道,一些设计方法只能作为原则予以考虑。现将已在实际工作予以应用的设计原则概述如下:2.1 常啮合,高档、超速档齿轮副的设计
在工作时,这些齿轮副转速高,利用率高,但承受负荷相对于低档齿轮副小,噪声要求相对于承载能力为主要矛盾,因此应按噪声要求选取参数,精度和齿面粗糙度也较低档齿轮相应高一级左右。例如:西德ZF公司,S4—18/3变速器,其中常啮合齿轮副精度为6级(DIN3962),齿面粗糙地Rz6.3~3.2采用磨齿方法加工。其它各档齿轮副精度均为7级(DIN3962),剃齿方法加工。
2.2 增大齿轮副重叠系数
确定齿部基本参数应考虑尽可能地增大重叠系数。重叠系数为整数2,或3最宜。但考虑误差的存在,允许重叠系数>2.1—2.5。由国外一些变速器采用的齿轮基本参数(见表1)证实,增加齿数和,减小模数;加大齿顶高系数——即采用长齿;采用小压力角;增大螺旋角和齿面宽等均可达到增大重叠系数目的。
我国标准规定渐开线齿轮基准齿形压力角20?,齿顶高系数1.0。但国外已普遍采用长齿齿顶,即顶高系数高达1.3—1.5,压力角减小到16?、17.5?、15?和14.5?。在中心距限定的配齿计算中,选择大齿数和、模数小之齿轮对。加大螺旋角和齿宽的同时要相应地控制接触精度,以防止出现现端、偏接触。
2.3 按噪声指标要求分配变位系数
(1) 根据啮合起始点远离基圆可降低噪声的研究,英国邱吉尔公司推荐:
式中:f d ——啮合起始点圆直径mm
b d ——基圆直径mm
n t ——法向齿距mm
(2) 根据齿轮副啮入长度小于啮出段长度可降低噪音的研究,推荐用公式(5)验算噪音指
标:
s b s b RB tg d tg d αραρβ1max 12max 222-?-?= (5)式中:RB ρ——噪音指标 m a x
2m a x 1,ρρ——小、大轮啮合终了点曲率半径mm b b d d 21, ——小、大轮基圆直径mm
s α ——端面啮合角(度)
在选择基本参数和变位系数后,按(4)、(5)式验算噪音指标,一般要求10.1 cg β
和0.1 cg β 。最佳方案为0.1 cg β,和9.0 RB β。高档齿轮副首先应满足噪音指标,其次满足强度、寿命要求,低档齿轮副在满足强度、寿命的前提下,亦应使此指标值愈小愈好。
2.4 合理地选择齿轮副侧隙,确定齿厚偏差
按GB10095—88规定来选取侧隙,从控制噪音的角度出发。
最小侧隙[]n k J tg Fr Fr fpt fpt n α??+?+?+?=)()2121(min 。
式中:2,1fpt ?——小、大轮齿距偏差 ; 2,1Fr ?——小、大轮径向跳动公差 K ——考虑热变形,热膨胀尘屑等的系数 ;
n α——法向法力角 一般轻型汽车变速器齿轮副侧隙应保证在0.1~0.25mm 范围内。表2是一些厂家选定之侧隙,供设计者对照参考。
在确定各档位齿轮侧隙时,应注意使其步调一致,以消除系统侧隙对噪音的不利影响。齿轮侧隙与许多因素有关,例如:齿轮体热膨胀系数,齿轮受载后轮齿变形,制造误差,安装误差,润滑油膜厚度等,根据一般推荐数值考虑上述最小侧隙的要求,再按其侧隙的近似计算公式,参照国际规定来分配齿厚上下极限偏差。日本五十铃公司设计了一种消除因侧隙引起的冲击的新结构,即在中间轴常啮合齿轮处附加一薄层齿轮周围方向与齿轮相错一个小角度,并在周围方向布置弹簧,起缓冲作用,实用结果在发动机怠速工况下噪音可降低3~5dB 。
表2 齿轮副侧隙
2.5 正确地进行轮齿修形(设计齿形,设计齿向)
轮齿修形即设计齿形、设计齿向是降低齿轮噪声最合理最有效的途径。一直是国内外齿轮技术界研究的热门课题。所见国外一些变速器齿轮图纸均有设计齿形、设计齿向要求。修形原理已为众多学者阐明,修形方法和计算也有所别。正是因为每种齿轮之工作条件(载荷变化幅度、转速、油温)及轮齿几何特征、综合刚度不相同,所以任何一厂家的修形计算公式都有它的局限性,都不可能适用于所有的齿轮的修形。确定自己产品的修形要求时,最有效的途径是进行大量的试验。以获得适合本齿轮的齿形、齿向要求在生产中予以执行。
一般齿轮修形有以下几种情况:
(1)齿顶修缘:仅对齿顶部分进行修整,如图9。
其中,max ?——最大修缘量;21max ?+?=?;
1?——考虑加工误差的修缘量,对于固定工艺和精度等级,其值为常数;
2?——为克服啮合过程中由双对齿向单对齿啮合过渡引起载荷突变的修缘量,其值与载荷成正比。
例如:美国AGMA (航空齿轮设计所)的修形计算为:
主动齿轮:21max ?+?=?=11.5+0.05Ft/±33.5(m μ)
从动齿轮:21max ?+?=?=4—0.05Ft / b ±4(m μ)
式中:Ft /b 为单位齿宽法向力(N /mm)。
英国的Rools-Royce 公司设计航空齿轮的修缘量计算:
m a x ?=0.008-0.00066ft /fd(英寸)
式中:ft ——齿根弯曲计算应力(磅/时2
) d f ——齿轮
修缘高度x x e y r r h ,-=?取在双齿啮合区中点。
修缘部分的齿形曲线:可为直线也可为曲线,汽车齿轮一般速度、载荷数属中等,取为直线即可。 对于齿顶修缘还应注意因有效齿高的降低重叠系数。所以有厂家在计算齿高的基础上将齿顶高有意加大,例如ZF 公司,将齿顶圆直径加大0.2一0.4mm 。但此时须验算加大直径的顶圆齿顶宽以防变窄。并验算齿轮副径向间隙。
(2)渐开线齿形齿形修正:除齿顶、齿根部分较理论渐开线稍短一些,希望沿整个齿高方向称为凸形,即正力角齿形为宜,具体齿形形状仍要通过大量实验确认。
(3)齿向修正(设计齿向):为避免端接触和偏接触出现,沿轮齿长度方向应做成中凸——即鼓形齿。一般中凸量为0.005~0.012mm 。
齿轮设计齿形、设计齿向图见图10。
2.6 齿轮体结构形状的设计
从限制噪声传播的角度考虑,为了降低噪声,应该减小齿轮表面辐射面积,要达到这一目的方法之一是尽量减小齿轮直径,方法之二是在齿轮上钻孔,日本KONDA 分动器齿轮上在幅板位置直接锻造出四个孔。另外增加齿轮体厚度和布上环状筋,可降低噪声,但要受变速器轴向尺寸的限制。
2.7 增强轴的刚性,选择低噪声轴承
轴,轴承两种运转部件即是噪声源之一,又是固体传声媒介。设计轴时,直径、长径比的设 计应保证在满负荷作用下其总绕度和转角分别不大于0.13~0.15 mm 和0.00123弧度,以使轴具有足够刚性,不致破坏齿轮的正常安装和啮合。
轴承的精度和游隙对变速器噪声的影响是明显的,特别在高转速区一般设计均选用普通级轴承,但当选用较高级(D 级)轴承时,通常可降低1~2dB ,不过这种高一级的轴承价格要高2~3倍。近年来轴承行业研制推出同等级别低噪声轴承,价格不高,降噪效果不错,举BCl84B 变速器装用普通轴承和低噪声轴承的试验数据见表3。 表3 (单位 Db )
测试条件:样品BC184B24#
输入轴转速:2000r/min
输入轴扭矩:60Nm
测试距离:100mm
油温:35?C
ZF 实验台。
2.8 箱体的降噪设计
已有不少国内外厂家研究箱体对噪声的影响,并已见多篇研究成果的介绍。研究结果表明箱体的降噪设计是降低变速器噪声的另一有效的途径,潜力很大。如果条件具备,在设计阶段利用计算机进行分析,并且在样品试制时期用仪器对已经生产的箱体进行振动和固有频率的测量分析,找出薄弱环节及部位予以修改设计。
箱体的降噪设计包括以下几个方面:
(1)箱体形状应能使其刚度大,声辐射面积减小,避免大平面过渡,表面应设计成法向方向各异的小面相连接,以降低箱壁振动和减小辐射能量。
(2)箱体各窗口——取力孔、倒档孔、顶部换档部位孔,相对位置予以合理布置,并且应予以拿铁盖代替薄钢板盖或者采用带阻压层的盖板,起到吸振作用。
(3)箱体材料由于轻量化的要求,多由铸铁改为铝合金,铝合金吸振阻压性能较差,现正在研究在其铝合金中加入适当添加剂来改善此性能。
(4)在箱壁内表面上敷以吸声材料,吉林工大常文祥教授曾对哈齿131型变速器取力孔盖上进行噪声试验,吸声效果最好时可降低4~5dB。
(5)连体的离合器壳也属于箱体范围,设计不当则会产生扩音,对于离合器壳体有条件应做固有频率测定,检测共振性,合理地布置加强筋。例如BCl84B变速器,实测带离合器壳和不带离合器壳时的噪声可大约差3~4dB。
(6)合理选用润滑油样和规定润滑油量。
润滑油主要起润滑作用也起一定的冷却作用,一般轻型汽车用变速器采用油浴润滑,其油量应使齿轮浸入润滑油的深度为20~40mm为好,或者是齿高的2~3倍。