轧制润滑
粗轧阶段的轧制方法

粗轧阶段的轧制方法粗轧是金属加工中的一个重要工序,用于将金属坯料经过轧制设备的多道次轧制,将其变形成为所需的中间截面形状和尺寸,为下一道加工工序提供必要的条件。
下面将详细介绍粗轧阶段的轧制方法。
1.粗轧设备粗轧阶段主要采用的轧制设备有酸洗轧机、立式轧机、斜轧机和辊床等。
其中,酸洗轧机常用于去除坯料表面的氧化皮和锈蚀,提高轧制效果和质量。
立式轧机可用于实现多通道轧制,将坯料逐步压延至所需尺寸。
斜轧机主要用于轧制较大尺寸的坯料,具有轻巧灵活的特点。
辊床是一种水平加工设备,可以对坯料进行横轧,具有较大的轧制强度。
2.轧制方法(1)单道轧制法:即将完整坯料一次性通过一套轧制辊,使坯料厚度得到一次减小。
这种方法的优点是轧制过程简单快捷,适用于一些要求较低的加工工序。
缺点是轧制力较大,轧制效果较差,易产生轧制缺陷,一般用于轧制坯料中较低的轧制强度。
(2)多道次轧制法:即将坯料通过多套不同粗糙度的轧制辊,逐个轧制,使坯料逐步减小厚度和增加宽度。
这种方法的优点是轧制力分散,轧制效果好,能够轧制出高精度的金属材料。
缺点是轧制过程时间较长,设备复杂,成本较高。
适用于对轧制质量要求较高的工件。
(3)反复轧制法:即在多次轧制中,将坯料的轧制方向依次改变,增加坯料内部的位错,使坯料的晶粒得到更细小的变形。
这种方法的优点是能够显著提高金属的塑性和韧性,减少金属材料的断裂和表面缺陷。
缺点是轧制过程复杂,轧制力较大,适用于轧制要求高强度和塑性的金属材料。
(4)硬轧法:即在轧制过程中,通过调整轧制温度、轧制速度以及轧制辊的间距,使坯料在轧制过程中发生较大的变形,改变金属材料的原子结构和晶格排列,提高金属材料的机械性能和强度。
这种方法适用于轧制高强度和高硬度的金属材料。
3.操作要点(1)轧制温度:粗轧一般在金属材料的再结晶温度以下进行。
再结晶温度是金属在轧制过程中的一种热敏性温度,轧制温度低于再结晶温度能够使金属材料保持塑性和变形能力。
高功效、低油斑轧制油添加剂与润滑油的研制

添加剂含量 图 3 五 种 添 加 剂 油 斑 定 量 对 比
的摩擦学优于 R 2 1 和R 3 1 单剂 , 说明醇酯复配具有很 好 的增效 效益 。
1 . 3 油斑 特性 分析
Q u a n t i t a t i v e c o mp a r o s o n o n t h e o i l m a r k s f o r
压油添加剂能确保抗磨液压润滑效果 良好 的抗泡沫 特性 , 其优 良的抗磨性能和无渍特性尤其适合铝轧机 或铜轧机液压系统。符合 D e n i s o n H F - O 及D I N 5 1 5 2 4 ,
P 2 ( HL P ) 规格 要求 。
2 . 1无渍润滑油摩擦学性能分析比较
2 6
有色金属加工
第4 3卷
1 . 1 添 加剂分 子 结构 比较 除了 R 2 1 、 R 3 1 及R 4 1 , 又选取 了市 场 常见 的 2种 复合 类 产 品 A、 B, 用 F r r . I R对 产 品进行 分 子级 别 的对
1 . 2 添 加剂摩 擦 学性 能分析 比较 为 了进 一 步考 察 不 同添 加剂 的 润滑 效果 , 在 轧 制 油 的基 础油 ( 4 0  ̄ G运 动 粘 度 为 2 . 3 6 m m / s ) 中分 别 加
产品相比, R 2 1 、 R 3 1 、 R 4 1 具有优 良的低油斑特性。
2无 渍 润 滑 油 的性 能 比较 及 研 发
油斑污染 中, 根据图 1 润滑油 占比例为 3 9 %位居
研究 , 成功开发出既能满足润滑又能大幅降低油斑污
第 1 期
有色金属加工
2 7
染 的无 渍 液压 油 AL系列 和无 渍 齿轮 油 G L系列 。
轧制油的组成
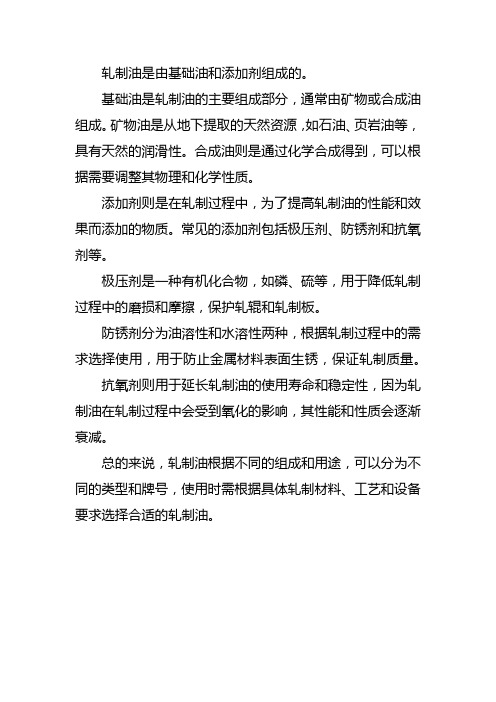
轧制油是由基础油和添加剂组成的。
基础油是轧制油的主要组成部分,通常由矿物或合成油组成。
矿物油是从地下提取的天然资源,如石油、页岩油等,具有天然的润滑性。
合成油则是通过化学合成得到,可以根据需要调整其物理和化学性质。
添加剂则是在轧制过程中,为了提高轧制油的性能和效果而添加的物质。
常见的添加剂包括极压剂、防锈剂和抗氧剂等。
极压剂是一种有机化合物,如磷、硫等,用于降低轧制过程中的磨损和摩擦,保护轧辊和轧制板。
防锈剂分为油溶性和水溶性两种,根据轧制过程中的需求选择使用,用于防止金属材料表面生锈,保证轧制质量。
抗氧剂则用于延长轧制油的使用寿命和稳定性,因为轧制油在轧制过程中会受到氧化的影响,其性能和性质会逐渐衰减。
总的来说,轧制油根据不同的组成和用途,可以分为不同的类型和牌号,使用时需根据具体轧制材料、工艺和设备要求选择合适的轧制油。
冷轧轧制油使用说明及安全说明书书
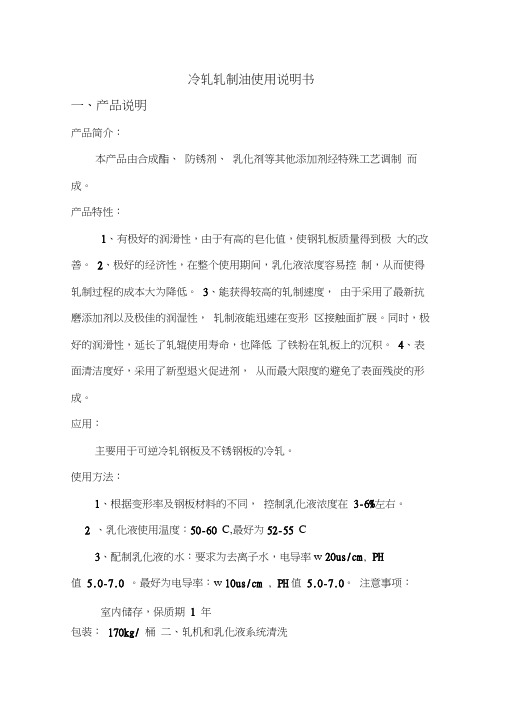
冷轧轧制油使用说明书一、产品说明产品简介:本产品由合成酯、防锈剂、乳化剂等其他添加剂经特殊工艺调制而成。
产品特性:1、有极好的润滑性,由于有高的皂化值,使钢轧板质量得到极大的改善。
2、极好的经济性,在整个使用期间,乳化液浓度容易控制,从而使得轧制过程的成本大为降低。
3、能获得较高的轧制速度,由于采用了最新抗磨添加剂以及极佳的润湿性,轧制液能迅速在变形区接触面扩展。
同时,极好的润滑性,延长了轧辊使用寿命,也降低了铁粉在轧板上的沉积。
4、表面清洁度好,采用了新型退火促进剂,从而最大限度的避免了表面残炭的形成。
应用:主要用于可逆冷轧钢板及不锈钢板的冷轧。
使用方法:1、根据变形率及钢板材料的不同,控制乳化液浓度在3-6%左右。
2 、乳化液使用温度:50-60 C,最好为52-55 C3、配制乳化液的水:要求为去离子水,电导率w 20us/cm, PH值5.0-7.0 。
最好为电导率:w 10us/cm , PH值5.0-7.0。
注意事项:室内储存,保质期1 年包装:170kg/ 桶二、轧机和乳化液系统清洗A设备准备阶段1、检查所有相关设备,包括排液泵,注入泵,溢流口及管道,脱盐水管道等,保证正常使用。
B乳化液切换清洗从一种乳化液切换到另一种乳化液,由于配方的机制不同,不能相互滥用,必须进行清洗,以使乳化液的影响降到最低,保证新乳化液的功能。
乳化液切换清洗过程如下:1、将轧机收集槽内的乳化液全部打回乳化液箱2、排放乳化液3、清洗乳化液全部循环系统的淤泥(包括轧机周围,收集槽、管道、过滤器、乳化液箱等)4、淤泥清洗完毕后,在乳化液箱中注入足够配制水5、循环2-5 小时,清洗所有设备和附属设备6、排放清洗水7、在乳化液箱中注入足够的配制水,升温至35-45 C8、配制合适0.5%浓度的新乳化液9、循环2-5 小时,充分清洗所有设备和附属设备10、排放乳化液,准备新乳化液的配制C乳化液的配制在完成必要的清洗工作后,可以进行乳化液的配制。
轧制油的技术参数
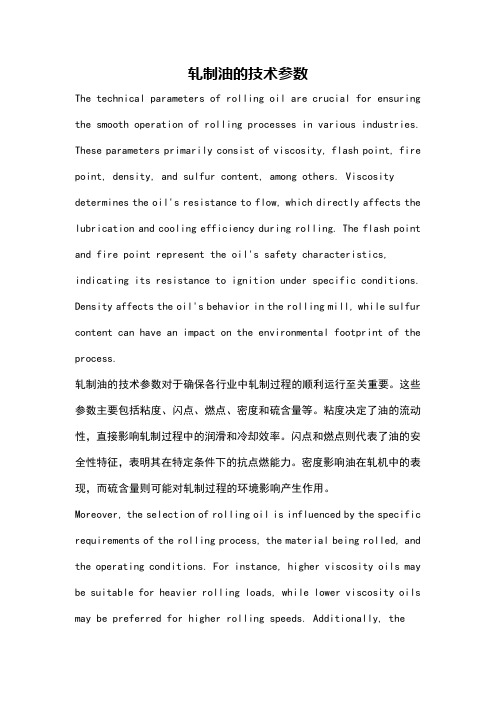
轧制油的技术参数The technical parameters of rolling oil are crucial for ensuring the smooth operation of rolling processes in various industries. These parameters primarily consist of viscosity, flash point, fire point, density, and sulfur content, among others. Viscosity determines the oil's resistance to flow, which directly affects the lubrication and cooling efficiency during rolling. The flash point and fire point represent the oil's safety characteristics, indicating its resistance to ignition under specific conditions. Density affects the oil's behavior in the rolling mill, while sulfur content can have an impact on the environmental footprint of the process.轧制油的技术参数对于确保各行业中轧制过程的顺利运行至关重要。
这些参数主要包括粘度、闪点、燃点、密度和硫含量等。
粘度决定了油的流动性,直接影响轧制过程中的润滑和冷却效率。
闪点和燃点则代表了油的安全性特征,表明其在特定条件下的抗点燃能力。
密度影响油在轧机中的表现,而硫含量则可能对轧制过程的环境影响产生作用。
2024年铝板轧制油市场发展现状

铝板轧制油市场发展现状概述铝板轧制油是一种用于铝板轧制工艺的润滑、冷却和防锈润滑剂。
随着全球铝板产能的增加以及对高品质铝板需求的不断增长,铝板轧制油市场正面临着巨大的发展机遇。
本文将对当前铝板轧制油市场的发展现状进行分析,并展望未来的趋势。
市场规模铝板轧制油市场的规模正在不断扩大。
根据市场研究机构的数据,2019年全球铝板轧制油市场规模达到X万吨,并预计到2025年将增长至X万吨。
亚太地区是最大的市场,占据了全球市场份额的X%,其次是欧洲和北美地区。
市场驱动因素铝板轧制油市场的增长主要受以下因素驱动:1. 铝板产能扩张随着建筑、汽车、造船等行业对铝板需求的增加,铝板产能也在不断扩张。
铝板是一种轻质、耐腐蚀的材料,广泛应用于各个领域。
此趋势推动了轧制油市场的增长,因为铝板轧制过程中需要使用润滑剂来保证生产效率和产品质量。
2. 技术进步随着轧制技术的不断进步,对铝板轧制油的要求也在提高。
高速轧制等先进工艺要求润滑剂具有更好的润滑性、冷却性和防锈性能。
市场上的轧制油产品不断创新,以满足新工艺的要求,这进一步推动了市场的发展。
3. 环保压力环保问题正成为全球关注的焦点,润滑剂行业也受到了压力。
铝板轧制油市场也在不断寻求更环保的产品和生产工艺。
例如,水溶性轧制油在一些地区得到了广泛应用,取代了传统的石油基轧制油。
这种趋势将继续推动市场的发展。
市场竞争格局铝板轧制油市场竞争激烈,主要厂商包括Shell、Mobil、Total、ExxonMobil等国际知名品牌。
此外,国内一些润滑油生产厂商也在快速崛起。
由于市场规模的增大和需求的多样化,竞争格局可能会发生变化。
发展趋势展望1.创新型产品的推出:随着技术的不断进步,市场需要创新型的铝板轧制油产品来满足新工艺的需求。
生产厂商将继续加大研发投入,提供更高效、更环保的产品。
2.区域市场的发展:亚太地区是全球最大的市场,未来将继续保持强劲增长。
而在其他地区,如中东、非洲等新兴市场,铝板轧制油的需求也将逐渐增加。
轧制油介绍(DAStuart)

轧制油介绍招聘(广告)一. 简介1. 轧制润滑的历史第一台冷轧带钢的四辊连轧机在1930年之前开始投产。
在30年代和40年代初期,冷轧机所采用的润滑油的类型主要以棕榈油和水的混合物为基础,而润滑方法则采用直喷式系统向轧机喷油润滑(这种润滑系统类型现在仍然在使用)。
以后,开发了乳化液系统。
用棕榈油配制的粗乳化液以循环的方式向轧机喷乳化液润滑。
这种不稳定的乳化液总要求进行维护,而且不能很好地实现轧机的性能。
在1940年以后,由于棕榈油越来越难找到,而且价格很昂贵,因此,所开发的大部分在美国使用的冷轧油都使用动物油为基础。
随着工业的发展,更新、更高速度的连轧机变得更加盛行,改进轧制油的乳化技术成为更加关键的问题。
由于成本更高、环境保护的要求更加严格,直喷式乳化液润滑系统被逐步淘汰,并且开发了更先进的乳化液润滑技术。
由于每台轧机的乳化液系统的大小、泵的规格、集管喷头的设计、乳化液系统的设计、过滤器的设计、水源的情况、乳化液的配制步骤以及总体乳化液的维护方案等与其它轧机的都不相同,因此,每台轧机的轧制油的配方都与其它轧机的轧制油的配方不同。
在此期间内,极端压力添加剂的使用进一步增强了加到轧制油中的动物油的润滑性能。
由于对乳化液性能的要求越来越高,乳化液系统和添加剂的性能也必须改进和发展。
这些工业上的需求要求在乳化液技术领域内连续进行研究和开发,以便满足不断变化的对冷轧润滑油的要求。
2. 轧制油技术的发展1) 棕榈油直喷式润滑油系统(1940年前)2) 棕榈油加乳化剂循环式润滑系统(1940年前)3) 动物油加乳化剂直喷式和循环式润滑系统(战前)4) 动物油加先进的乳化剂系统(40-50年代)5) 动物油加:(60-70年代)1. 极端压力添加剂2. 先进的乳化剂系统(带油量和粒度概念)6) 动物油加:(当前)1. 各种润滑性添加剂2. 弥散剂(粒度与带油量之间的关系)3. 抗氧化剂4. 杀菌剂5. pH缓冲剂3. 应用轧制油的目的轧制油的功能是在轧辊和带钢的表面形成一个保护膜,由限制金属与金属之间的接触的方法来减小摩擦系数。
轧液率计算公式

轧液率计算公式轧液率是指材料在轧制过程中润滑液延续作用下的润滑效果,通常用于评价轧制工艺的质量和效率。
轧液率的计算公式可以根据轧制工艺和材料特性来选择。
一般而言,轧液率的计算需要考虑润滑液的性质、润滑液流动的速度和润滑液在轧制过程中的消耗。
以下是一些常见的计算公式和相关参考内容。
1. 轧液率计算公式轧液率的计算可以采用以下公式:轧液率 = (出口润滑液质量 - 入口润滑液质量) / 轧制材料质量其中,出口润滑液质量和入口润滑液质量可以通过流量计和质量计进行测量,轧制材料质量可以通过称重来获得。
2. 润滑液性质的测量方法润滑液的性质对于轧液率的计算非常重要,可以通过以下方法来测量:- 粘度:可用粘度计来测量润滑液的粘度,粘度越大,液膜的保持能力越好。
- 界面张力:可以通过动态方法或静态方法来测量界面张力,界面张力越小,润滑效果越好。
- 氧化安定性:可以通过加速氧化实验来评估润滑液的氧化稳定性,氧化不稳定性会导致润滑效果下降。
3. 润滑液流动速度的测量方法润滑液的流动速度对轧液率也有影响,可以通过以下方法进行测量:- 流量计:可以选用合适的流量计来测量润滑液的流量。
- 测速方法:可以采用激光多普勒测速仪等设备来测量润滑液的流速。
4. 润滑液消耗的测量方法润滑液在轧制过程中会消耗一部分,可以通过以下方法进行测量:- 润滑液质量测量:可以通过称重法来测量进出润滑液的质量差距,从而可以得到润滑液消耗的量。
- 流量计测量:可以通过流量计来测量进出润滑液的流量差距,从而可以得到润滑液消耗的量。
综上所述,轧液率的计算是基于润滑液的性质、流动速度和消耗量进行的。
通过合理选择计算公式和合适的测量方法,可以准确评估轧制工艺的润滑效果,从而提高轧制质量和效率。
- 1、下载文档前请自行甄别文档内容的完整性,平台不提供额外的编辑、内容补充、找答案等附加服务。
- 2、"仅部分预览"的文档,不可在线预览部分如存在完整性等问题,可反馈申请退款(可完整预览的文档不适用该条件!)。
- 3、如文档侵犯您的权益,请联系客服反馈,我们会尽快为您处理(人工客服工作时间:9:00-18:30)。
一. 简介
1. 轧制润滑的历史
第一台冷轧带钢的四辊连轧机在1930年之前开始投产。在30年代和40年代初期,冷轧机所
采用的润滑油的类型主要以棕榈油和水的混合物为基础,而润滑方法则采用直喷式系统向轧机喷
油润滑(这种润滑系统类型现在仍然在使用)。以后,开发了乳化液系统。用棕榈油配制的粗乳
化液以循环的方式向轧机喷乳化液润滑。这种不稳定的乳化液总要求进行维护,而且不能很好地
实现轧机的性能。
在1940年以后,由于棕榈油越来越难找到,而且价格很昂贵,因此,所开发的大部分在美国
使用的冷轧油都使用动物油为基础。随着工业的发展,更新、更高速度的连轧机变得更加盛行,
改进轧制油的乳化技术成为更加关键的问题。由于成本更高、环境保护的要求更加严格,直喷式
乳化液润滑系统被逐步淘汰,并且开发了更先进的乳化液润滑技术。由于每台轧机的乳化液系统
的大小、泵的规格、集管喷头的设计、乳化液系统的设计、过滤器的设计、水源的情况、乳化液
的配制步骤以及总体乳化液的维护方案等与其它轧机的都不相同,因此,每台轧机的轧制油的配
方都与其它轧机的轧制油的配方不同。在此期间内,极端压力添加剂的使用进一步增强了加到轧
制油中的动物油的润滑性能。
由于对乳化液性能的要求越来越高,乳化液系统和添加剂的性能也必须改进和发展。这些工业上
的需求要求在乳化液技术领域内连续进行研究和开发,以便满足不断变化的对冷轧润滑油的要
求。
2. 轧制油技术的发展
1) 棕榈油直喷式润滑油系统(1940年前)
2) 棕榈油加乳化剂循环式润滑系统(1940年前)
3) 动物油加乳化剂直喷式和循环式润滑系统(战前)
4) 动物油加先进的乳化剂系统(40-50年代)
5) 动物油加:(60-70年代)
1. 极端压力添加剂
2. 先进的乳化剂系统(带油量和粒度概念)
6) 动物油加:(当前)
1. 各种润滑性添加剂
2. 弥散剂(粒度与带油量之间的关系)
3. 抗氧化剂
4. 杀菌剂
5. pH缓冲剂
3. 应用轧制油的目的
轧制油的功能是在轧辊和带钢的表面形成一个保护膜,由限制金属与金属之间的接触的方法来减
小摩擦系数。水是润滑油的载体,其作用是冷却,带走在轧辊咬入过程中由于摩擦产生的热。因
此,轧制乳化液实现了为了满足轧机的速度和带钢的质量等要求所必须的功能,既提供了润滑性
能,又提供了冷却性能。
对每台轧机,所采用的轧制油都必须特别配制,以便提供控制金属与金属之间的接触所必须的润
滑性能。在金属与金属之间发生接触时,就会产生摩擦,如果没有摩擦,就会产生诸如打滑和厚
度控制的结果不良等问题。因此,轧制油的目的并不是消除摩擦,而是必须控制它以满足轧机的
要求。
4. 使用轧制乳化液的目的
轧制油提供限制金属与金属(带钢与轧辊)之间接触的一层保护膜。水的作用是作为油的载体和
轧辊及带钢的冷却剂。
二. 轧制摩擦
在冷轧带钢时,轧辊与带钢之间的摩擦是必要的,这是因为所有变形能都是从轧辊与带钢之间的
工作表面所产生的剪切应力转换来的。这就产生了这样的印象,即,摩擦力越大轧制的效率越高,
或者说更容易轧制。然而,事实并不是这样的;在轧辊咬入时的摩擦力水平太高,反而趋向于阻
碍材料的流动;另一方面,如果摩擦力的水平太低,轧辊就会在带钢上打滑。显然,这种允许在
最容易的方式下有效地轧制的摩擦力水平的大小必须是一个优选的值。在这种优选的摩擦条件
下,轧制力将为最低值,而且所要求的能量也将为最小值。
除了考虑轧制力和能量之外,轧制咬入的摩擦也相当严重地影响了所轧制的产品的材料的质量。
轧制压力超过发生在轧辊和带钢表面的所轧材料的屈服应力的超额量要适当。在此阶段中,正在
轧制一个新的带钢表面,太高的摩擦力水平对钢板表面产生不利的影响,导致带钢的表面质量不
佳,因而拒收率很高。这类的带钢表面缺陷被称为摩擦啄印,它对高速的连轧机最为有害。其它
由于摩擦而产生的不良影响是由于高温而增大的棕色边、单向皱纹或者由于在材料的宽度上的不
均匀的摩擦而产生的皱折,以及由于产生金属细粉使表面脏污。
轧制摩擦力采用特殊的润滑油来控制,尽管可以使用纯油,但通常用水作为承载的介质。在冷轧
工艺中所使用的轧制油被比喻为生命中的血液,它极大地影响了轧机的产量和产品的质量。
轧制油的润滑能力通过对轧机的轧制性能的影响表现出来,轧制油的润滑能力是以在轧辊的咬入
区内对摩擦系数的影响为基础决定的。
在带钢进入轧辊的咬入点处,轧辊的速度比带钢的速度大。这个速度差被称为逆向滑差;在带钢
进一步进入到轧辊咬入点时,此滑差的幅度增大。当带钢的速度与轧辊的速度相同而且逆向滑差
的值为零时,达到了一个点。此点被称为中性点。从咬入点到此中性点之间的接触弧被称为进入
面。
在大多数情况下,轧制的带钢离开工作辊的速度比轧辊的速度稍微大一些,这个差被成为前向滑
差。从中性点到离开点,滑差的幅度增加,从中性点到此离开点之间的接触弧被称为离开面。
此中性点的位置受到所采用的前后张力的相关值的影响。
具体的轧制力按照带钢的每单位宽度上所要求的轧制力中的描述,轧制力的幅度取决于下列各个
参数:
1. 带钢来料的厚度
2. 轧机的布置
3. 前后张力
4. 带钢的压缩屈服应力
5. 轧辊的弹性模量
6. 轧辊的尺寸
7. 轧辊咬入的摩擦系数
在没有摩擦力和张力的情况下,轧制力就是简单地由接触弧的有效长度和带钢的压应力的屈服强
度产生的。张力减小了材料的有效屈服强度。在有摩擦力的情况下,轧制力增加,这是由于这种
摩擦力产生了被称为摩擦斜坡的影响。
对于一台轧机的实际轧制程序来说,从第1到第6条都是固定的,因此,轧机操作的第7条-
摩擦系数是这些参数中最重要的参数。必须对轧机润滑这个变量进行控制。
在冷轧的情况下,轧辊与带钢之间的具体的压力值大约为50-250公斤/平方毫米,这取决于所
轧的钢种和轧制的条件。
摩擦系数的值通常为0.1到0.03,而且润滑增加了轧制速度,这种情况与滑动轴承类似。然而,
在非常高的轧制速度下,所产生的大量的热趋向于减小润滑油的粘度,结果是润滑油层减薄,甚
至可能完全消失,因此,摩擦系数再次增加。这就是为什么把各种润滑油所能达到的润滑系数作
为指导性的值来考虑的原因。因为此值在各个不同的条件下是变化的。
三. 润滑油的基本情况
1. 轧制润滑油
影响冷压下轧制性能的主要参数是:
1) 轧制油的化学成份通过极性和非极性结构对性能的影响。
2) 纯轧制油的粘度和粘度指数等物理性能。
3) 轧制油在90-95%水中或者其它在轧机现场所用的浓度及轧制液的温度情况下的弥散程
度。
4) 添加剂或者指定含量的轧制油。
5) 带钢或者钢板(扁平产品)的成份。
6) 操作实际情况。
7) 工作辊的直径和轧机的设计。
8) 轧制之前钢卷的情况。
9) 在使用期间内轧制液中产生的污染物。
10) 轧制油的使用方法和乳化液存储设备。
11) 要求的冷轧的产品的表面光洁度和清洁程度。
12) 工作辊的成份、表面光洁度和凸度。
13) 与热轧板卷酸洗及酸洗油涂层之间的兼容性。
14) 对下道清洗和退火工序的影响。
轧制油基本上是根据轧机的类型、应用方法和稳定性设计的。分类如下。
1) 生产薄板和镀锡板的3、4和5机架连轧机的直喷式系统用的润滑油。
2) 生产薄板和镀锡板的3、4、5和6机架连轧机的循环系统用的润滑油。
3) 可逆轧机用的润滑油。
4) 双压下镀锡板轧机用的润滑油。(DCR)