冷轧工艺润滑定义及基本要求
轧制过程中形成动压润滑的条件
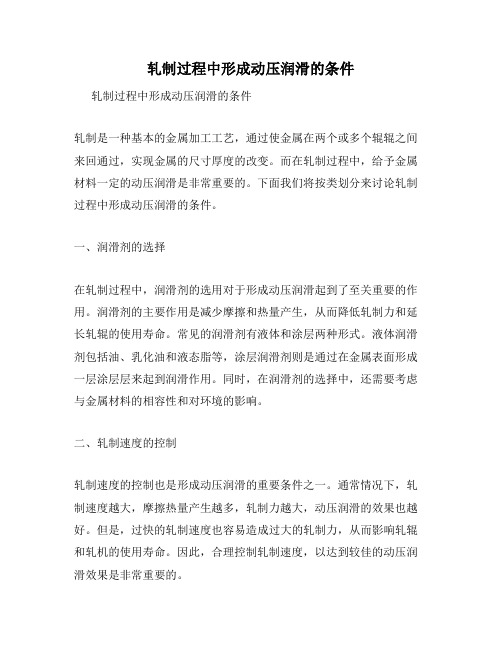
轧制过程中形成动压润滑的条件轧制过程中形成动压润滑的条件轧制是一种基本的金属加工工艺,通过使金属在两个或多个辊辊之间来回通过,实现金属的尺寸厚度的改变。
而在轧制过程中,给予金属材料一定的动压润滑是非常重要的。
下面我们将按类划分来讨论轧制过程中形成动压润滑的条件。
一、润滑剂的选择在轧制过程中,润滑剂的选用对于形成动压润滑起到了至关重要的作用。
润滑剂的主要作用是减少摩擦和热量产生,从而降低轧制力和延长轧辊的使用寿命。
常见的润滑剂有液体和涂层两种形式。
液体润滑剂包括油、乳化油和液态脂等,涂层润滑剂则是通过在金属表面形成一层涂层层来起到润滑作用。
同时,在润滑剂的选择中,还需要考虑与金属材料的相容性和对环境的影响。
二、轧制速度的控制轧制速度的控制也是形成动压润滑的重要条件之一。
通常情况下,轧制速度越大,摩擦热量产生越多,轧制力越大,动压润滑的效果也越好。
但是,过快的轧制速度也容易造成过大的轧制力,从而影响轧辊和轧机的使用寿命。
因此,合理控制轧制速度,以达到较佳的动压润滑效果是非常重要的。
三、轧制温度的控制轧制温度的控制同样也会对动压润滑产生重要影响。
当轧制温度较低时,金属材料会强度较高,摩擦系数也相对较大,从而增加了动压润滑的难度。
而当轧制温度适中时,金属材料的塑性较好,摩擦系数较小,动压润滑更容易形成。
因此,通过合理控制轧制温度,使其处于适宜的范围内,有利于形成较好的动压润滑条件。
四、辊辊几何形状的设计辊辊几何形状的设计也会对动压润滑产生一定影响。
通常情况下,辊辊的凸度较小,轧制面的接触面积较大,会增加摩擦,并使动压润滑更容易实现。
而辊辊的凸度较大,则会减小摩擦力,并使动压润滑的效果较差。
因此,通过合理设计辊辊的几何形状,可以提高动压润滑的效果。
五、辊辊与金属材料的表面质量辊辊与金属材料的表面质量也会对动压润滑产生一定影响。
当辊辊和金属材料的表面粗糙度较大时,会增加摩擦力,破坏动压润滑的效果。
因此,提高辊辊和金属材料的表面质量,减小摩擦,有助于形成较好的动压润滑条件。
2024年轧钢安全技术工艺润滑介绍(2篇)
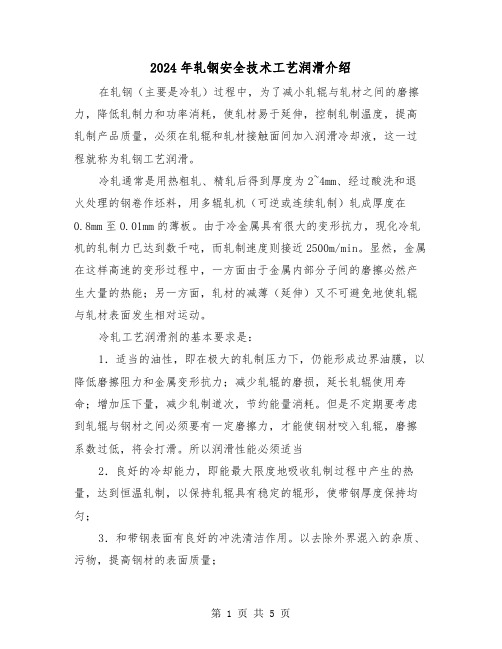
2024年轧钢安全技术工艺润滑介绍在轧钢(主要是冷轧)过程中,为了减小轧辊与轧材之间的磨擦力,降低轧制力和功率消耗,使轧材易于延伸,控制轧制温度,提高轧制产品质量,必须在轧辊和轧材接触面间加入润滑冷却液,这一过程就称为轧钢工艺润滑。
冷轧通常是用热粗轧、精轧后得到厚度为2~4mm、经过酸洗和退火处理的钢卷作坯料,用多辊轧机(可逆或连续轧制)轧成厚度在0.8mm至0.01mm的薄板。
由于冷金属具有很大的变形抗力,现化冷轧机的轧制力已达到数千吨,而轧制速度则接近2500m/min。
显然,金属在这样高速的变形过程中,一方面由于金属内部分子间的磨擦必然产生大量的热能;另一方面,轧材的减薄(延伸)又不可避免地使轧辊与轧材表面发生相对运动。
冷轧工艺润滑剂的基本要求是:1.适当的油性,即在极大的轧制压力下,仍能形成边界油膜,以降低磨擦阻力和金属变形抗力;减少轧辊的磨损,延长轧辊使用寿命;增加压下量,减少轧制道次,节约能量消耗。
但是不定期要考虑到轧辊与钢材之间必须要有一定磨擦力,才能使钢材咬入轧辊,磨擦系数过低,将会打滑。
所以润滑性能必须适当2.良好的冷却能力,即能最大限度地吸收轧制过程中产生的热量,达到恒温轧制,以保持轧辊具有稳定的辊形,使带钢厚度保持均匀;3.和带钢表面有良好的冲洗清洁作用。
以去除外界混入的杂质、污物,提高钢材的表面质量;4.良好的理化稳定性。
在轧制过程中,不与金属起化学反应,不影响金属的物理性能;5.退火性能好。
现代冷轧带钢生产,为了简化工艺,提高劳动生产率,降低成本,在需要进行中间退火时,采用了不经脱脂清洗而直接退火的生产工艺。
这就要求润滑剂不因其残留在钢材表面而发生退火腐蚀现象(即在钢材表面产生斑点);6.过滤性能好。
为了提高钢材表面质量,某些轧机采用高精度的过滤装置(如硅藻土)来最大限度地去除油中的杂质。
此时,要避免油中的添加剂被吸附掉或被过滤掉,以保持油品质量;7.搞氧化安定性好,使用寿命长;8.防锈性好。
钢冷轧工艺润滑及冷轧油相关知识
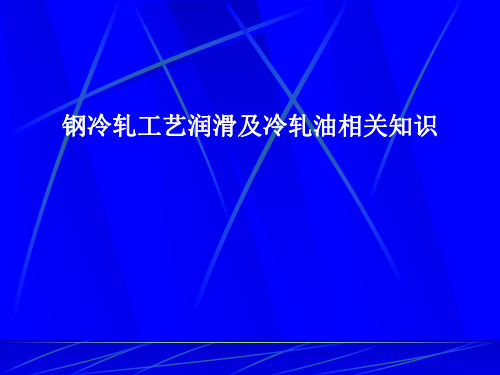
3、乳化液的热分离性
当乳化液喷射到轧辊或变形金属表面上时,由于 受热,乳化液的稳定状态被坏,分离出来的油吸附金 属表面上,形成润滑油膜,起防黏减摩作用。而水则 起冷却轧辊的作用。乳化液正是通过这种热分离性来 达到润滑冷却的目的。即冷轧乳化液的两大主要功能 为润滑和冷却。
乳化液的热分离性除了乳化液本身性质外,基础 油的黏度、添加剂、乳化液中油滴尺寸及分布,乳化 液的使用温度和时间都会影响乳化液的热分离性,进 而影响乳化液的使用效果。
镀锡钢板最早于14世纪在德国问世,首先是锻造方法,到18 世纪才改为轧制生产。1790年开始热轧,由于镀锡板需求增加, 促进了宽带冷轧机发展。但是,由于矿物油等润滑问题未解决, 使生产受到限制。由于轧制速度不断提高,变形量很大,因而迫 切要求同时解决轧辊的润滑与冷却问题,于是,出现了冷却性能 良好的乳化液润滑以代替纯油润滑。
亲油基端 亲油基端
油
乳化剂 油
搅拌
水 水
亲水基端
油 水
根据乳化液中分散相所带电荷性质,乳化液可分为:
(1) 阴离子型乳化剂。阴离子型乳化剂具有乳化效率高、 润滑性能好、清洗性和防锈性强以及破乳容易等特点, 同时也是目前使用较为广泛的轧制润滑乳化液。但是, 其对水质要求较高,易腐败变质,使用寿命短。
1.2、乳化剂
由于两种互不相溶的液相,如油和水混合时不能 形成稳定的平衡体系,故需加入表面活性剂,也即乳 化剂。乳化剂具有独特的分子结构,其分子一端为亲 油基,而分子的另一端为亲水基。这样,通过乳化剂 把油和水结合起来形成稳定的油水平衡体系。乳化剂 结构及乳化液形成过程示意图如下:
乳化剂结构及乳化液形成过程示意图
轧制示意图
2、轧制工艺润滑剂的基本功能 一种工艺润滑剂除了要满足其工艺要求外,往往还要求其实
轧钢机的润滑要求及用油

轧钢机的润滑要求及用油冶金设备的品种繁多,主要包括烧结设备、炼铁、炼钢及有色冶金设备、轧压设备等,冶金设备的润滑具有许多特殊问题,特别是现代大型成套设备,自动化程度高,需要承受带冲击性的重负荷,工作温度高及运动速度高,有些露天作业设备在恶劣环境条件下作业,具有多粉尘、潮湿的作业,易于腐蚀。
对设备润滑提出了较高的要求。
轧钢机的润滑1.轧钢机对润滑的要求(1)轧钢机轧钢机的主要设备包括轧钢机工作机座、万向接轴及其平衡装置、齿轮机座、主联轴器、减速机、电动机联轴器和电动机以及前后卷取机、开卷机等。
(2)轧钢机对润滑的要求1)干油润滑。
如热带钢连轧机中炉子的输入辊道、推钢机、出料机、立辊、机座、轧机辊道、轧机工作辊、轧机压下装置、万向接轴和支架、切头机、活套、导板、输出辊道、翻卷机、卷取机、清洗机、翻锭机、剪切机、圆盘剪、碎边机、垛板机等都用干油润滑。
2)稀油循环润滑。
如宝钢2030五机架冷连轧机为例,带钢冷却与润滑的乳液系统和给油系统的开卷机、五机架、送料辊、滚动剪、导辊、转向辊和卷取机、齿轮轴、平整机等的设备润滑;各机架的油膜轴承系统等。
3)高速高精度轧机的轴承,用油雾润滑和油气润滑。
(3)轧钢机工艺润滑冷却常用介质在轧钢过程中,为了减小轧辊与轧材之间的摩擦力,降低轧制力和功率消耗,使轧材易于延伸,控制轧制温度,提高轧制产品质量,必须在轧辊和轧材接触面间加入工艺润滑冷却介质。
对轧钢机工艺润滑冷却介质的基本要求有:①适当的油性;②良好的冷却能力;③良好的抗氧化安定性、防锈性和理化稳定性;④过滤性能好;⑤对轧辊和制品表面有良好的冲洗清洁作用;⑥对冷轧带钢的退火性能好;⑦不损害人体健康;⑧易于获得油源,成本低。
2.轧钢机润滑采用的润滑油、脂(1)轧钢机采用的润滑油、脂轧钢机经常采用的润滑油、脂,参看表2。
(1)稀油和干油集中润滑系统由于各种轧钢机结构对润滑的要求有很大差别,故在轧钢机上采用了不同的润滑系统和方法。
冷轧工艺知识
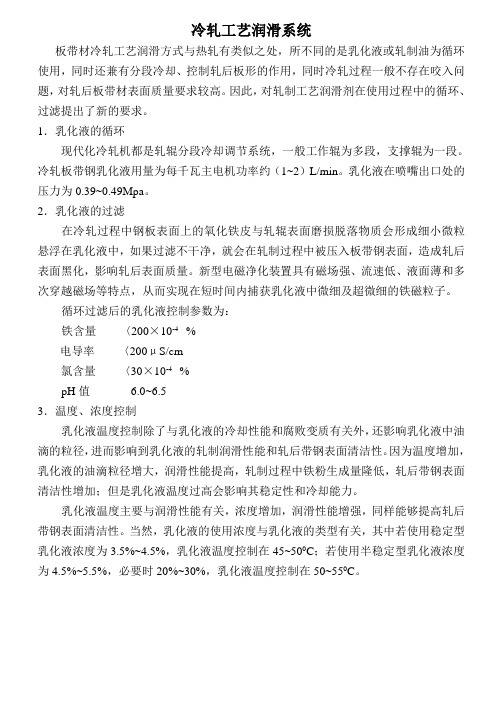
冷轧工艺润滑系统板带材冷轧工艺润滑方式与热轧有类似之处,所不同的是乳化液或轧制油为循环使用,同时还兼有分段冷却、控制轧后板形的作用,同时冷轧过程一般不存在咬入问题,对轧后板带材表面质量要求较高。
因此,对轧制工艺润滑剂在使用过程中的循环、过滤提出了新的要求。
1.乳化液的循环现代化冷轧机都是轧辊分段冷却调节系统,一般工作辊为多段,支撑辊为一段。
冷轧板带钢乳化液用量为每千瓦主电机功率约(1~2)L/min。
乳化液在喷嘴出口处的压力为0.39~0.49Mpa。
2.乳化液的过滤在冷轧过程中钢板表面上的氧化铁皮与轧辊表面磨损脱落物质会形成细小微粒悬浮在乳化液中,如果过滤不干净,就会在轧制过程中被压入板带钢表面,造成轧后表面黑化,影响轧后表面质量。
新型电磁净化装置具有磁场强、流速低、液面薄和多次穿越磁场等特点,从而实现在短时间内捕获乳化液中微细及超微细的铁磁粒子。
循环过滤后的乳化液控制参数为:铁含量〈200×10-4 %电导率〈200μS/cm氯含量〈30×10-4 %pH值 6.0~6.53.温度、浓度控制乳化液温度控制除了与乳化液的冷却性能和腐败变质有关外,还影响乳化液中油滴的粒径,进而影响到乳化液的轧制润滑性能和轧后带钢表面清洁性。
因为温度增加,乳化液的油滴粒径增大,润滑性能提高,轧制过程中铁粉生成量隆低,轧后带钢表面清洁性增加;但是乳化液温度过高会影响其稳定性和冷却能力。
乳化液温度主要与润滑性能有关,浓度增加,润滑性能增强,同样能够提高轧后带钢表面清洁性。
当然,乳化液的使用浓度与乳化液的类型有关,其中若使用稳定型乳化液浓度为3.5%~4.5%,乳化液温度控制在45~500C;若使用半稳定型乳化液浓度为4.5%~5.5%,必要时20%~30%,乳化液温度控制在50~550C。
二、坯料准备冷轧薄板带钢的坯料是通过热轧提供的热轧卷,热轧带卷的质量对冷轧薄板带钢的质量有明显的影响,材料的性能取决于化学成份和组织结构,保证冷轧板带质量的第一个基础是钢的化学成份。
浅谈铝轧制工艺和润滑
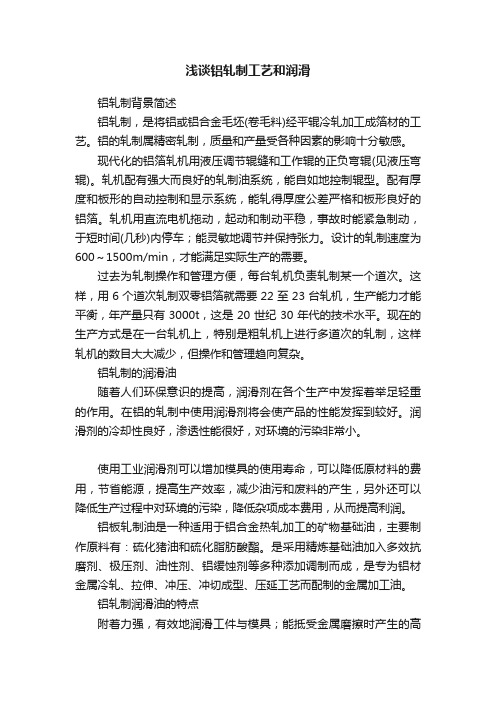
浅谈铝轧制工艺和润滑铝轧制背景简述铝轧制,是将铝或铝合金毛坯(卷毛料)经平辊冷轧加工成箔材的工艺。
铝的轧制属精密轧制,质量和产量受各种因素的影响十分敏感。
现代化的铝箔轧机用液压调节辊缝和工作辊的正负弯辊(见液压弯辊)。
轧机配有强大而良好的轧制油系统,能自如地控制辊型。
配有厚度和板形的自动控制和显示系统,能轧得厚度公差严格和板形良好的铝箔。
轧机用直流电机拖动,起动和制动平稳,事故时能紧急制动,于短时间(几秒)内停车;能灵敏地调节并保持张力。
设计的轧制速度为600~1500m/min,才能满足实际生产的需要。
过去为轧制操作和管理方便,每台轧机负责轧制某一个道次。
这样,用6个道次轧制双零铝箔就需要22至23台轧机,生产能力才能平衡,年产量只有3000t,这是20世纪30年代的技术水平。
现在的生产方式是在一台轧机上,特别是粗轧机上进行多道次的轧制,这样轧机的数目大大减少,但操作和管理趋向复杂。
铝轧制的润滑油随着人们环保意识的提高,润滑剂在各个生产中发挥着举足轻重的作用。
在铝的轧制中使用润滑剂将会使产品的性能发挥到较好。
润滑剂的冷却性良好,渗透性能很好,对环境的污染非常小。
使用工业润滑剂可以增加模具的使用寿命,可以降低原材料的费用,节省能源,提高生产效率,减少油污和废料的产生,另外还可以降低生产过程中对环境的污染,降低杂项成本费用,从而提高利润。
铝板轧制油是一种适用于铝合金热轧加工的矿物基础油,主要制作原料有:硫化猪油和硫化脂肪酸酯。
是采用精炼基础油加入多效抗磨剂、极压剂、油性剂、铝缓蚀剂等多种添加调制而成,是专为铝材金属冷轧、拉伸、冲压、冲切成型、压延工艺而配制的金属加工油。
铝轧制润滑油的特点附着力强,有效地润滑工件与模具;能抵受金属磨擦时产生的高温。
保证连续有效的油膜厚度,避免模具的局部刮伤或烧结;具有优异的极压抗磨性,优良的润滑性能,减少模具磨损,减少产品毛刺;防锈性能好,防止工件腐蚀。
极高润滑效果,在塑性变化中不断提供高效润滑减摩膜,能有效地提高工件表面质量,有效减少划痕、划伤、烧结焊合、破裂等现象的发生;优异的极压性能保证在高、深、难的加工工况下,有效提高工件的质量和加工功率,增加模具寿命。
冷轧工艺特点及冷轧工艺参数

冷轧工艺特点及冷轧工艺参数一、冷轧工艺特点金属一般都是由无数单个晶粒构成的多晶体,要了解金属的塑性变形性质,必须先了解单个晶粒或单晶体的塑性变形机构。
塑性变形时加在金属上的力,使金属中大量原子群定向地、多次地从一个稳定平衡位置转移到另一个稳定平衡位置,在宏观上便产生不能恢复的塑性变形。
根据原子成群移动发生的条件和方式不同,可观察到各种不同的塑性变形机构,如滑移、孪生及其他机构等。
(1)滑移。
滑移是指晶体在外力的作用下,其中一部分沿着一定晶面和这个晶面上的一定晶向,对其另一部分产生的相对移动,此晶面称为滑移面,此晶向称为滑移方向。
滑移时原子移动的距离是原子间距的整数倍,滑移后晶体各部分的位向仍然一致。
滑移结果,使大量原子逐步地从一个稳定位置移到另一个稳定位置,晶体产生宏观的塑性变形。
如图3-1所示为晶体以滑移方式进行的塑性变形。
用金相显微镜所观察到的每一条纹是由许多滑移面与试样抛光平面的交线所组成的,称为滑移带。
滑移带是由一群滑移层所形成的滑移线组成的(见图3-2)。
一般,在各种金属(晶体点阵)中,滑移不是沿任意晶面和晶向进行的,而总是沿着原子密度最大的晶面和晶向发生的。
这是因为原子密度最大的晶面,原子间距小,原子间的结合力强,同时其晶面间的距离较大,即晶面与晶面间的结合力较弱。
同理也可以解释滑移为什么沿着原子密度最大的晶向发生。
滑移面与滑移方向数值的相乘积称为滑移系。
图3—1 晶体滑移示意图图3-2单晶体的滑移带、滑移线和滑移层示意图金属的3种常见晶格的主要滑移面、滑移方向和滑移系如表3-1所示。
(2)孪生(孪晶、双晶)。
金属的塑性变形除以滑移方式进行外,孪生也是其重要方式之一。
孪生是晶体在切应力的作用下,其一部分沿某一定晶面和晶向,按一定的关系发生相对的位向移动,其结果使晶体的一部分与原晶体的位向处于相互相称的位置,如图3-3所示。
表3-1金属的主要滑移面、滑移方向和滑移系图3-3 晶体的孪生示意图在孪生变形时,所有平行于孪生面的原子平面都朝着一个方向移动。
轧钢设备的润滑管理

轧钢设备的润滑管理轧钢设备作为钢铁生产线的重要组成部分,对润滑管理要求严格。
良好的润滑管理能够保证轧钢设备的正常运转,延长设备的使用寿命,提高生产效率,减少能源消耗,降低维护成本,确保生产安全。
对轧钢设备的润滑管理工作进行规范化、系统化的管理十分必要。
2. 要求(1)设备润滑要坚持“定期、定点、定量、定质”的原则,以确保设备部件的正常工作。
(2)要确保设备零部件的摩擦副间的摩擦副设计正确定位,油脂、润滑油能够接触到摩擦副的工作表面。
(3)根据设备的使用情况和工作环境,在不同地段和设备之间采用不同的润滑方式。
(4)定期对设备的润滑情况进行检查,对不良的润滑情况及时调整和更换。
二、润滑管理的内容和方法1. 润滑管理的内容(1)选用合适的润滑油和润滑脂对轧钢设备的润滑油和润滑脂的选择要根据设备的使用情况和工作环境来进行合理搭配,确保设备在各种工况下都能正常工作。
(2)确定润滑点通过分析轧钢设备的结构和工作原理,确定设备的润滑点,并根据设备的使用情况和工作环境进行优化。
(3)制定润滑计划根据设备的使用情况和工作环境,制定合理的润滑计划,并严格执行,确保设备在规定的时间内得到合理的润滑。
(4)设备润滑记录建立设备的润滑记录,对设备的润滑情况进行跟踪和记录,及时发现问题并及时处理。
2. 润滑管理的方法(1)手动润滑手动润滑是最常见的润滑方法之一,通过人工对设备的摩擦副进行定期润滑,适用于一些小型设备和一些特殊的部位。
(2)自动润滑自动润滑是利用一些设备进行全自动、定时、定量的润滑。
这种方法可以减少人工干预,提高生产效率,适用于一些大型设备和一些需要频繁润滑的部位。
(3)喷雾润滑喷雾润滑可以将润滑剂通过喷雾的方式直接喷洒到摩擦副上,可以减少润滑剂的浪费,提高润滑效率,适用于一些摩擦副间隙较小的部位。
三、润滑管理的责任和监督1. 润滑管理的责任(1)设备负责人设备负责人必须建立健全设备的润滑管理制度,指导和监督设备的润滑工作。
- 1、下载文档前请自行甄别文档内容的完整性,平台不提供额外的编辑、内容补充、找答案等附加服务。
- 2、"仅部分预览"的文档,不可在线预览部分如存在完整性等问题,可反馈申请退款(可完整预览的文档不适用该条件!)。
- 3、如文档侵犯您的权益,请联系客服反馈,我们会尽快为您处理(人工客服工作时间:9:00-18:30)。
[分享]轧钢(冷轧)工艺润滑定义及基本要求
在轧钢(主要是冷轧)过程中,为了减小轧辊与轧材之间的磨擦力,降低轧制力和功率消耗,使轧材易于延伸,控制轧制温度,提高轧制产品质量,必须在轧辊和轧材接触面间加入润滑冷却液,这一过程就称为轧钢工艺润滑。
冷轧通常是用热粗轧、精轧后得到厚度为2~4MM、经过酸洗和退火处理的钢卷作坯料,用多辊轧机(可逆或连续轧制)轧成厚度在0.8MM至0.01MM的薄板。
由于冷金属具有很大的变形抗力,现化冷轧机的轧制力已达到数千吨,而轧制速度则接近2500M/MIN。
显然,金属在这样高速的变形过程中,一方面由于金属内部分子间的磨擦必然产生大量的热能;另一方面,轧材的减薄(延伸)又不可避免地使轧辊与轧材表面发生相对运动。
冷轧工艺润滑剂的基本要求是:
1、适当的油性,即在极大的轧制压力下,仍能形成边界油膜,以降低磨擦阻力和金属变形抗力;减少轧辊的磨损,延长轧辊使用寿命;增加压下量,减少轧制道次,节约能量消耗。
但是不定期要考虑到轧辊与钢材之间必须要有一定磨擦力,才能使钢材咬入轧辊,磨擦系数过低,将会打滑。
所以润滑性能必须适当
2、良好的冷却能力,即能最大限度地吸收轧制过程中产生的热量,达到恒温轧制,以保持轧辊具有稳定的辊形,使带钢厚度保持均匀;
3、和带钢表面有良好的冲洗清洁作用。
以去除外界混入的杂质、污物,提高钢材的表面质量;
4、良好的理化稳定性。
在轧制过程中,不与金属起化学反应,不影响金属的物理性能;
5、退火性能好。
现代冷轧带钢生产,为了简化工艺,提高劳动生产率,降低成本,在需要进行中间退火时,采用了不经脱脂清洗而直接退火的生产工艺。
这就要求润滑剂不因其残留在钢材表面而发生退火腐蚀现象(即在钢材表面产生斑点);
6、过滤性能好。
为了提高钢材表面质量,某些轧机采用高精度的过滤装置(如硅藻土)来最大限度地去除油中的杂质。
此时,要避免油中的添加剂被吸附掉或被过滤掉,以保持油品质量;
7、搞氧化安定性好,使用寿命长;
8、防锈性好。
对工序间的短期存放,能起到良好的防锈作用;
9、不应含有损害人体健康的物质和带刺激性的气味;
10、油源广泛,易于获得,成本低。
热轧工艺润滑
提高热轧带钢机组的产量,降低消耗,提高生产率,这是轧钢工艺中一件极为重要的事。
各国实践已经证明,使用热轧油能显著减少轧辊的磨损,降低电耗、改善钢板表面质量,提高生产率。
使用热轧就可以获得以下好处(已为实践证明):
1、改善了轧辊的表面状况。
2、降低了轧辊的单位消耗。
3、降低了电能的消耗。
4、提高了带钢的表面质量。
5、降低轧制压力,容易实现轧制薄规格带钢。
6、促进热轧理论的研究。