热轧工艺润滑技术的开发与应用
热轧带钢工艺润滑系统的应用

0
1
5
左右
。
擦
。
由 于 润 滑 油 水 混 合 物 进行 轧 辊 与
,
带钢 之 间 润
(
2)
3
轧 制力
电耗
:
一
:
般 轧制 力可 降低
5
 ̄
5
%
。
 ̄
30
%
。
滑 油 燃烧 后 生 成 碳
,
在 轧 辊 与 带 钢 间 起 到 润 滑 作
正 因 为降 低 了 轧 辊
一
(
)
(
3]
:
—
部分润 滑
辊 表 面 黑 皮 的 产 生 提 髙 了 带 钢 表 面 质量
(
剂 燃 烧 之 后 的 残 留 物 主 要 是 残 碳 将 金 属 和 乳 辊
)
6
)
使 冷 轧 带 酸 洗 效 率提 高
、
。
由
于 采用工艺
表 面 隔 开 从 而 减 少 金 属 与 乳 辊 之间 的 摩 擦 另
,
;
一
润 滑 提 高 了 热 乳 带 钢 表 面 质 量 减 少 了 表 面 铁皮
,
部 分 润 滑 剂 在 变 形 区 内 高 温 髙 压 下 急剧 汽 化 和 分
解 在 封 闭 区 内 形 成气 垫 将 金 属 与 乳 辊 隔 开 起 到
, , ,
产 生 从 而 使 带 钢 表 面 铁 皮 厚 度减 薄
一
系 列 优 点 已 为 世 界各 热 乳 厂 的 实
热 轧 带 钢 工 艺 润 滑 达到 的 指 标
际 应 用所 证 实 工 艺 润 滑 系 统 在 热 轧 带 钢 乳 机 上 应 用 后 的 效
工艺润滑技术在热轧精轧机组中的应用
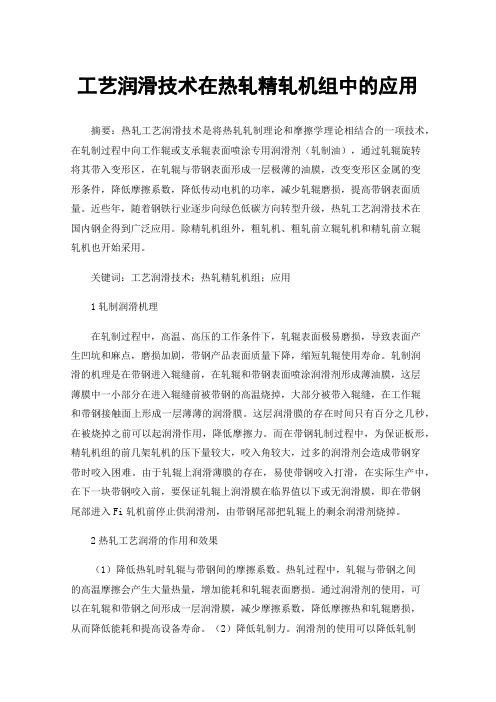
工艺润滑技术在热轧精轧机组中的应用摘要:热轧工艺润滑技术是将热轧轧制理论和摩擦学理论相结合的一项技术,在轧制过程中向工作辊或支承辊表面喷涂专用润滑剂(轧制油),通过轧辊旋转将其带入变形区,在轧辊与带钢表面形成一层极薄的油膜,改变变形区金属的变形条件,降低摩擦系数,降低传动电机的功率,减少轧辊磨损,提高带钢表面质量。
近些年,随着钢铁行业逐步向绿色低碳方向转型升级,热轧工艺润滑技术在国内钢企得到广泛应用。
除精轧机组外,粗轧机、粗轧前立辊轧机和精轧前立辊轧机也开始采用。
关键词:工艺润滑技术;热轧精轧机组;应用1轧制润滑机理在轧制过程中,高温、高压的工作条件下,轧辊表面极易磨损,导致表面产生凹坑和麻点,磨损加剧,带钢产品表面质量下降,缩短轧辊使用寿命。
轧制润滑的机理是在带钢进入辊缝前,在轧辊和带钢表面喷涂润滑剂形成薄油膜,这层薄膜中一小部分在进入辊缝前被带钢的高温烧掉,大部分被带入辊缝,在工作辊和带钢接触面上形成一层薄薄的润滑膜。
这层润滑膜的存在时间只有百分之几秒,在被烧掉之前可以起润滑作用,降低摩擦力。
而在带钢轧制过程中,为保证板形,精轧机组的前几架轧机的压下量较大,咬入角较大,过多的润滑剂会造成带钢穿带时咬入困难。
由于轧辊上润滑薄膜的存在,易使带钢咬入打滑,在实际生产中,在下一块带钢咬入前,要保证轧辊上润滑膜在临界值以下或无润滑膜,即在带钢尾部进入Fi轧机前停止供润滑剂,由带钢尾部把轧辊上的剩余润滑剂烧掉。
2热轧工艺润滑的作用和效果(1)降低热轧时轧辊与带钢间的摩擦系数。
热轧过程中,轧辊与带钢之间的高温摩擦会产生大量热量,增加能耗和轧辊表面磨损。
通过润滑剂的使用,可以在轧辊和带钢之间形成一层润滑膜,减少摩擦系数,降低摩擦热和轧辊磨损,从而降低能耗和提高设备寿命。
(2)降低轧制力。
润滑剂的使用可以降低轧制力,减少轧制过程中的变形阻力。
润滑剂能够在轧制过程中形成一层润滑膜,减少金属间的接触阻力,从而降低轧制力,提高轧制效率。
热轧油的应用及改进

热轧油的应用及改进本文介绍了热轧油的益处、系统组成及系统的改进。
标签:工艺润滑;混合器;热轧油1 热轧油的益处1.1 降低轧制力热轧工艺润滑的原理是通过喷嘴将油水混合液以一定的压力均匀地喷射到工作辊表面形成牢固的油膜,并咬入辊缝使辊面与带钢表面的摩擦系数减小,降低了轧制力。
各个机架轧制力降低幅度不完全一样,一般轧制力降幅在10-30%。
1.2 降低轧辊消耗采用工艺润滑后,在轧辊表面形成的一层薄薄的氧化膜将工作辊与带钢隔开,使轧制力明显降低的同时,减少了轧辊表面的磨损量,从而轧辊单次的磨削量也明显减少,一般可使轧辊消耗降低10-40%。
1.3 延长轧制周期,减少换辊次数,提高生产效率由于轧辊的磨损减小了,轧辊的单次轧钢计划就可以延长,使轧制公里数增加,换辊次数减少,生产率得到提高。
1.4 减少带钢表面缺陷,提高带钢的表面质量工艺润滑的应用有利于减少轧制过程中二次氧化铁皮的生成,从而可以提高冷轧的酸洗的生产效率,降低酸洗的成本。
由于轧辊磨损的降低,提高了辊形精度,使轧制计划后期的产品表面质量得到提高。
1.5 由于轧制电流降低,从而节约了能源消耗随着轧制力降低,电机的负荷也相应减小,从而降低了轧机电能的消耗。
这也是热轧工艺润滑最直接产生经济效益的方面。
1.6 为能生产出更薄规格的产品创造有利条件。
2 热轧油系统的应用要点2.1 选择品质优良的润滑油品具有良好的润滑性及足够的油膜强度;具有良好的吸附性和润湿性,在轧辊表面形成牢固油膜;具有较高的闪点和热分解稳定性;具有良好的抗乳化性。
2.2 采用完善的应用系统的设计,工作辊润滑系统。
2.3 稳定热轧油系统的功能投入率轧钢过程中连续使用,保持低辊耗;提高轧机的稳定性,所有轧制规格全部使用轧制油通过使用有效的轧制工艺润滑,使薄规格的轧制生产难度降低,使轧机在轧制薄规格时出现的振动现象减少甚至消失,为超薄规格的轧制提供有效的帮助。
3 热轧油系统的应用方式图1 切水板上方工作辊润滑图2 切水板下方工作辊润滑3.1 切水板上方工作辊润滑(图1)特点:热轧油使用时,工作辊入口冷却水停掉。
热轧工艺专业组——轧制工艺润滑

热轧生产也需要润滑 哪里需要?
1.2 热轧生产中的润滑
一、工艺润滑在热轧中的应用
1、设备润滑 2、轧制工艺润滑
1886年,润滑力学的创始人O.Reynolds推导出著名的雷诺方程。 20世纪初,开始在矿物油中加入活性添加剂以提高润滑效果,同时
在冷轧窄带钢工艺中已开始用水作为润滑剂。 20世纪30 年代,前苏联采用动物油进行热轧型钢工艺润滑。 1968年,美国国家钢铁公司GREAT LAKE在热轧精轧机组上成功地应
乳化剂
添加剂和水
两种不相溶的液相,如油 和水,不能形成稳定的平 衡体系,故加入表面活性 剂,也就是乳化剂
2.2 轧制工艺润滑剂的应用
二、轧制工艺润滑剂
热轧生产中使用乳化油。
基础油
乳化剂
添加剂
加热搅拌
乳化油
在使用时兑水即可应用于实际生产。
3.1 轧制工艺润滑技术的应用
三、轧制工艺机理
热轧生产中润滑应用的研究相对冷轧远远落后 主要原因就是温度
• 作用机理:降低轧辊与带钢之间的摩擦系数 • 工作状况:在高温、高压下,部分被燃烧,以残炭形式
存在;部分急剧汽化和分解,形成油膜将轧辊与带钢隔 开;部分以流体形式通过变形区
四、轧制工艺润滑应用实例
工艺润滑作用 降低轧辊与带钢之间的摩擦系数,减小轧制力、轧制扭矩降 低能耗 降低轧辊消耗,延缓工作辊的磨损,延长轧辊使用周期,提 高轧机作业率 改善产品质量,减少二次氧化皮的产生
最佳使用浓度由具体轧制钢种、厚度、温度等 而定
4.1 热轧应用区域
精轧区域 具体点? 喷射点
四、轧制工艺润滑应用实例
4.2 供油方式
四、轧制工艺润滑应用实例
按比例在管路中通过混合器直接混合 浓度0.1—0.8% 用喷嘴向辊面喷射 一般0.15—0.2L/min
轧制润滑工艺在莱钢1500mm热连轧精轧机组中的应用

轧制润滑工艺在莱钢1500mm热连轧精轧机组中的应用热轧时采用轧制工艺润滑能明显起到降低轧机负荷,减少轧辊消耗、改善成品表面质量的作用,本文系统介绍轧制工艺润滑在莱钢1500mm热连轧精轧机组中的应用。
标签:轧制润滑;轧制力;轧辊磨损。
1、概述莱钢1500mm热轧生产线于2005年投产,经过近两年多的运行,设备状况、工艺过程基本稳定,随着产量的逐步提高,产品厚度逐渐向薄规格延伸,轧辊工作负荷明显增加,加速了轧辊的剥落和磨损,频换的换辊又造成轧制作业率的降低。
为此在该生产线增设轧制润滑装置: 精轧机组采用油-水混合喷射润滑系统对工作辊进行润滑的轧制方式。
热轧时采用工艺润滑后,轧辊与轧件之间被一层边界润滑膜隔开,可以起到如下作用:1) 降低热轧时轧辊与轧件间的摩擦系数,从而降低轧制力,容易轧制薄规格带钢。
2) 减少轧辊消耗和储备,提高作业率。
3) 减少氧化皮压入,改善轧辊表面状态和轧后成品表面质量4) 改善制品内部组织性能,提高深冲钢的深冲性能。
2、系统组成及控制原理2.1系统组成:本系统设备主要由贮油箱、工作油箱、工作水箱、加油泵、计量泵站、水泵站、上下集水管、喷嘴和电控系统等组成。
2.2系统原理储油箱中加热至一定温度的油经供油泵送至工作油箱中;并由计量泵经供油电磁阀送至各架轧机的油水混合器。
水箱中加热至一定温度的水由供水泵送至各架轧机旁的混合器与油混合后送至各架轧机的上下工作辊面上进行润滑。
如图1所示。
图1:轧制润滑示意图2.3系统控制:2.3.1系统配置本系统由PLC一套。
其主要配置有:电源、CPU、通讯摸板、开关量输入、开关量输出、模拟量输入、研华工控机、变频器。
系统见图2:控制系统用PLC实施自动控制。
本系统在地下室配有两面柜子,一个PLC 柜子,一个变频器柜。
在控制室操作台上放置计算机作为监控使用。
有网线连接柜子和计算机完成通讯;另外,由DP网连接S7-400与变频器完成通讯。
2.3.2控制过程润滑轧制时喷油水混合液程序的控制如下:轧钢时,在轧机前的热金属检测器首先检测到来钢的信号,当钢咬入F6架后(可根据需要设定延时),同时控制F1、F2、F3、F4、F5和F6架喷水、喷油。
板带热轧工艺润滑及喷油系统

愿与供应商和用户本着互惠互利的原则精诚合作
DAS Tech
公司创始人- 斯图尔特先生
建于1865年,有着140年的老公司,从做润滑脂起家, 现发展成为专业化的化学油脂品生产商,从事向汽车、 航空、矿山、钢业和铝业及金属加工业提供各种各样的 润滑油脂品。
D.A.Stuart 的业务遍及全球五大洲,总部设于美国芝 加哥,分别在美国、加拿大、巴西、澳洲、德国、英国 和南非建设有生产基地,为了更好地服务日益活跃和勃 勃生机的亚太地区,2005年1月在上海浦东浦江经济 开发区投资600万美元成立了斯图尔特上海有限公司, 将其作为亚太地区的生产和研发中心。
DAS Tech
热轧油油品的主要参数
序号
项目
1
外观
2
粘度
3
皂化值
4
游离脂肪酸
5
硫
6
闪点
7
着火点
8
倾点
9
比重
单位
40摄氏度下 cSt mgKOH/g % % 摄氏度 摄氏度 摄氏度 Mg/mm3
DAST HM400(例) 暗琥珀
100 111 2-3
0.1-6.5 270 315 -18 0.905
Sy stem
喷油系统示例图一
DRAIN
DSP
1
20A 20A 15A
DSP
1
20A 20A 15A
DAS Tech
to F1 ~ F3 Oil Application Sy stem
OIL Booster Pump Unit
2-Gear pump 5l/min x 1Mpa
10kgf /cm2 AC 0.75kw x
热轧工艺润滑系统的应用与设计要点
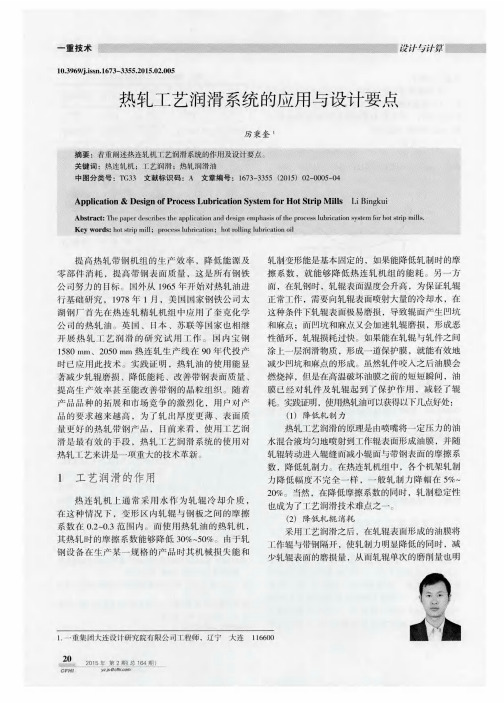
应 尽量选 用 性能稳 定 ,故 障率 低 的电器元 件及 检测 元 件 ,元 件 的可靠 运 行是保 证 热轧 工艺 润滑 系
统稳 定性 的关 键 。 2 . 3 系统 维 护要点
( 6 ) 可 生产 更薄规 格 的产 品
通过使用有效的轧制工艺润滑 ,降低薄规格产 品的 轧制难 度 ,使 以往 轧制 薄规 格产 品 时经 常 出现 的轧机 共振 现 象减少 甚 至 消失 ,为生 产合 格 的薄带
润 滑前 后 的轧 辊磨 损情 况作 出对 比 ( 见表 1 ) 。
表 1 热 轧 油 的 使 用 对辊 耗得 影 响
越 容易 降低 轧制 力 ,节约 能耗 ,改 善板形 。在轧 制 时 ,减 少轧 制力 是必要 的 ,但 是摩擦 系数 过 小也会 带来 咬人 稳定 性 变 差 的 问题 ,当无 法 稳定 咬入 时 , 可 以采 用切 断供 油 的方 式 ,在前 一 个轧件 尾部 轧制
润滑 作用 。对 于热轧 润滑 油 的工作 原理 和 各种 添加
工艺 润滑 喷 嘴布置 在轧 机入 口侧 工作 辊冷 却水 的 上 方 ,在 轧 钢 时 轧 辊 表 面 先 被 喷 涂 上 工 艺 润 滑
剂 的润 滑特性 ,许多 油 品制造 公 司 以及 专 门 的机构
2 。 5 年第 2 期 ( 总 1 6 4 期 );
时间都有减少 ,生产效率大幅提高 。
( 4 )减 少氧 化铁 皮 生成 量
轧 辊 的瞬 时表 面温 度 可 以达到 7 0 0 o 【 = ,所 以一 定 要保 证热 轧油 在 7 0 0℃的环境 中处 于稳 定状 态 。
( 4 ) 良好 的环保 性 能
工艺 润 滑 的应 用有 利 于减少 轧 制过 程 中氧化 铁
1700生产线热轧工艺润滑系统开发与应用

架 各 由一 个 油泵 独 立供 油 , 个 混合 器 完成 油水 一
混合 图 1为热 轧油 系统布 置简 图 。
2 12 水 系统 . .
目前 , 国内 很多 热 轧厂 在 设 计 热轧 工 艺润 滑 系统 时 , 水 系 统 都与 其 它冷 却 系统 共 用 一个 系 其 统 , 样很难保 证 水压稳 定 , 影 响热 轧油使 用效 这 且
a da r d I edd o g t dut n cus n p l a o aeo ti lb c t n ss m e n bo ." e g t u h ,ajs a h n h me t o r a da p c t ns t f hs u r a o t a e ii t i i ye r
安 装 与应用 。
2 系 统设 计 方 案
2 1 硬件设计 .
2 1 1 系统布局 . .
F ~F 机 架共 用 一个水 系统 和油箱 , I 6 每个 机
得 到 了普 遍应 用 。最 初 提 出润 滑轧 制 的 目的 只是 为了提 高热轧 带钢 的质 量 , 发展 到今 天 , 但 它已成
轧 工艺 润 滑技 术 以减轻 精 轧 机组 负 荷 、 低 能耗 降 和 提高 生产 率就显 得非 常重要 。 为此 , 过 吸收 国 通
内外 热轧 工 艺润 滑 先进 技 术 , 发设 计 了一 套工 开
艺 润滑 系统 , 并在 1 0 7 0生产线 的精轧机 组 进行 了
史 乃 安 , 钢 技 术 专 家 , 级 工 程 师 , 9 9年 毕 业 予 西 安 冶 鞍 高 18 金建 筑 学 院金 属 塑 性 加 工 专业 , 工作 于 鞍 钢股 份 有 限 公 司 热 轧 现 带 钢厂 ( 10 1 。 14 2 )
- 1、下载文档前请自行甄别文档内容的完整性,平台不提供额外的编辑、内容补充、找答案等附加服务。
- 2、"仅部分预览"的文档,不可在线预览部分如存在完整性等问题,可反馈申请退款(可完整预览的文档不适用该条件!)。
- 3、如文档侵犯您的权益,请联系客服反馈,我们会尽快为您处理(人工客服工作时间:9:00-18:30)。
热轧工艺润滑技术的开发与应用何晓明杨春平摘要:阐述了热轧工艺润滑的机理及作用,并结合工艺润滑技术在宝钢2050mm热轧厂的开发与应用,探讨了工艺润滑对带钢表面质量及环境的影响。
关键词:热轧;工艺润滑The application and development of lubrication technology for hotrollingHE Xiao-ming, YANG Chun-ping(Hot Rolling Dept., Baoshan Iron & Steel (Group) Co., Shanghai 200941, China)Abstract: The mechanism and effects of lubrication technology for hot rolling are described. Combining with the practice development and application in Baosteel, the influence of lubrication on surface quality of strip and surroundings are discussed.Keywords: hot rolling; lubrication technology1 热轧工艺润滑技术的发展1957年,热轧工艺润滑技术在美国获得成功应用,当时使用的润滑剂为水溶性的油,应用在精轧机组的支撑辊上。
近10几年来,由于钢铁市场对薄带材质量的要求日益提高,而且热带钢轧机向连续、高速、大型、自动化方向发展,轧辊的使用周期明显相对缩短,频繁换辊对轧机产量有很大影响。
因此,以减少轧辊磨损为主要出发点的热轧工艺润滑的研究逐步引起重视。
发展到现在,世界上已有数10套热轧带钢轧机应用了工艺润滑。
美国内陆钢厂在使用高速钢轧辊的同时也应用了工艺润滑,取得了更好的效果。
从目前应用来看,热轧工艺润滑按润滑作用点可分为支撑辊润滑和工作辊润滑;按作用方式可分为喷嘴式、毛刷式、毛毡式和喷雾式等。
宝钢2050mm精轧机组采用工作辊喷嘴润滑方式。
2 热轧工艺润滑的机理及作用2.1 热轧工艺润滑的机理热轧工艺润滑是一个动态过程,在变形区高温、高速、高压状态下润滑油所起的变化难以实验模拟,因而目前对热轧的润滑机理尚无统一认识。
一般认为,热轧润滑剂以3种状态起润滑作用:一部分润滑油被燃烧,燃烧残留物主要是残炭,使轧辊与金属表面隔开,残炭与金属和轧辊之间的摩擦小于金属与轧辊之间的固体摩擦。
另一部分润滑油在变形区高温、高压下急剧气化和分解,形成高温、高压的气垫,将金属与轧辊表面隔开,起到润滑作用,这种气体间的摩擦远小于流体间的摩擦。
其余部分润滑油可能保持原来的状态,以流体形式通过变形区。
由于现代热轧工艺特点是高温、高速、高压、工作辊辊面瞬时温度可达600~700℃,经冷却散热而稳定在50~80℃。
因此,为适应热轧工艺特点,热轧润滑剂要满足如下要求:(1)热轧时具有良好的润滑性,降低摩擦,减少磨损;(2)应具有良好的吸附性和润湿性,以便在轧辊表面形成连续牢固的润滑膜;(3)粘度要适中,易于输送和喷涂,不易从变形区挤出;(4)具有较高的闪点和热分解稳定性;(5)润滑油燃烧生成气体量少,燃烧物应无毒,对环境污染小。
2.2 热轧工艺润滑的作用热轧工艺润滑具有以下作用:(1)使热轧力能参数发生变化,由于轧制力的降低,减少了电能消耗;(2)由于润滑油形成覆盖在轧辊表面的保护膜,缓和了水对轧辊的急冷与氧化作用,同时这层保护膜还起着阻碍轧件向轧辊传热的作用,降低了轧辊的热疲劳,从而使磨损减轻。
(3)改善热轧板的表面质量。
由于保持了轧辊表面状况和外形处于满意的状态,可提高轧辊断面和轧件的几何尺寸精度以及防止三次氧化铁皮被粗糙轧辊压入。
(4)延长轧制公里数,减少换辊次数,增加作业时间。
(5)减少轧辊购置费用。
3 热轧工艺润滑的应用热轧工艺润滑是一项实践性很强的新技术,因为每套轧机的结构与特性不同,在原有系统应用这项技术是一项较复杂的工程。
3.1 应用系统整个应用系统如图1所示。
系统包括以下几部分:(1)润滑剂储罐此为大型容器,可储存60m3润滑剂,避免每周补充润滑剂。
(2)工作油箱此油箱容积2.3m3。
配备有如下装置。
①蒸汽加热装置。
可保持润滑剂温度恒定在40~60℃。
保持润滑剂粘度的恒定是整个应用系统中很重要的环节。
②温度、液位指示器。
③液位控制器。
控制润滑剂从储油罐到工作油箱的输送泵的关闭与启动。
④液位报警器。
具有低、高位报警功能,当液位处于高位报警状态时能自动关闭输送泵。
⑤流量计。
记录由储油罐打入工作油箱的油量,用于测定润滑剂的消耗量。
图1 轧制润滑应用系统1-润滑油储罐;2-储罐液位;3-输送泵;4-流量计;5-温度计;6-工作罐;7-背压调节箱;8-工作罐液位;9-过滤器;10-泵前压力;11-泵1;12-泵2;13-泵后压力;14-压力开关;15-压力指示;16-平衡管;17-F1~F6控制电磁阀;18-F1~F6上辊油压;19-F1~F6下辊油压;20-油背压;21-飞剪;22-PLC控制箱(3)工作泵组润滑剂循环泵和备用泵都配备有真空过滤器、真空指示表及真空报警器。
每个泵都配备压力表、压力报警器及止回阀、安全阀和隔离阀。
(4)热平衡管热平衡管保证每个喷油口能得到相同的油温和油压。
(5)立式控制盒F1~F6轧机均有1个控制盒,控制和监测注入混和喷嘴的润滑剂量。
(6)注入点润滑剂从立式控制盒流出至注入点的混合喷嘴,混和喷嘴将润滑剂和轧辊冷却水均匀混和,冷却水携带着分散的润滑剂至轧辊表面。
(7)PLC控制箱PLC控制箱和操作面板是系统的信息和控制中心,显示系统工作状态,诊断系统故障。
3.2 系统的操作通过安装在操作室的控制箱对系统进行操作。
液位控制器、液位报警器都在操作台显示并监控。
系统启动时,立式控制盒里的所有电磁阀处于关闭状态,直至钢板进入精轧机。
电磁阀开闭的顺序是:钢板进入轧机,轧制力信号通过PLC 延迟6s后启动,Fn(n=1~6)机架上的电磁阀,一旦带钢尾部离开切头剪,F1电磁阀关闭;尾部离开F2,关闭F3电磁阀,依此类推。
其目的是防止润滑油在轧辊表面堆积和燃烧不净造成下一块带钢进钢时打滑。
同时,头部延时时间的设定也考虑了避免对轧制力遗传系数产生影响,以保证数学模型的设定精度。
操作面板上,通过对系统油压的选择可控制油量大小。
在计划轧制过程中,随轧辊磨损加剧,系统油压呈分段阶梯自动控制,以达最佳润滑效果。
3.3 润滑剂润滑剂分为固体和液体2种。
由于固体润滑剂不能连续供给,且更换不便,因而未能推广应用。
液体润滑剂按其基础油的不同,可分为3种:(1)以矿物油为基的润滑剂;(2)以植物油或动物油为基的润滑剂;(3)化学合成型润滑剂。
目前宝钢2050热轧厂使用的润滑剂为恒丰公司生产的HYG-1和Nalco公司生产的HM-40。
润滑剂在水中具有良好的分散性能,能与水混合形成均匀的混合物,当它以高速湍流状态喷射到工作辊上,其分子极性使其牢固地吸附在轧辊表面。
润滑剂的高分子量酯类化合物和碳氢化合物使其具有高温润滑特性。
3.4 润滑的转移现象在F1~F4机架使用轧制润滑,而在没有使用润滑剂的F5机架也看到了和使用润滑剂类似的现象,最明显的是轧制力下降。
这种现象可解释为润滑剂在前面的机架中没有完全燃烧,而随带钢一起进入下一个机架。
另外,带钢头尾无润滑部分的表面比中部有润滑的部分表面相对粗糙,摩擦系数发生了变化。
4 轧制润滑对带钢表面质量的影响带钢表面状况是一个重要的质量指标。
通常,一次和二次氧化铁皮通过采用合理的加热制度和高压水除鳞可以控制。
而三次氧化铁皮压入造成的氧化铁皮细孔则与精轧前部机架工作辊表面状态密切相关。
氧化铁皮细孔发生在轧制计划的后半期,为了避免其发生,通常临时换辊,这样不仅中断了轧制计划的连续性,而且造成轧制作业率下降。
在轧制变形区的前滑区和后滑区,带钢和轧辊表面产生相对运动。
在实际生产过程中,和轧辊表面接触的薄氧化铁皮层要强烈地被冷却,从而使其硬度增高。
当轧辊和带钢表面间相对移动时,将发生氧化铁皮层变形和金属接触层被犁沟。
轧辊表面越粗糙,这种机械作用越大。
这样,在接触面发生氧化铁皮的聚集并且压入相对软的带钢中。
在热轧过程中,工作辊始终处于高温,高负荷和高速状态下,随轧制的进行,轧辊表面逐渐磨损、粗糙。
润滑油在变形区可降低轧辊磨损速度。
另外,由于润滑油形成覆盖在轧辊表面的保护膜,缓和了水对轧辊的急冷与氧化作用;同时,这层保护膜还有阻碍轧件向轧辊传热的作用,降低了轧辊的热疲劳,从而使磨损减轻。
使用润滑油后,轧制润滑平均计划长度可达到153km,比使用前薄板平均计划长度90km增加41%,轧制润滑最大计划长度可达到180km。
5 轧制润滑对轧辊使用寿命的影响由于轧制润滑减少了轧辊磨损,因而轧制润滑计划公里数及轧制吨位数增加,但下机后磨削量并未增加,使吨钢辊耗降低,如表1所示。
表1轧辊磨削量比较举例6 轧制润滑对环境的影响在润滑轧辊辊缝的过程中,绝大部分润滑剂被轧辊以及带钢表面的高温燃烧掉,燃烧产物为二氧化碳和水,没有毒性。
而没有燃烧掉的少许润滑剂会在铁皮坑里浮至水面或吸附在氧化铁皮表面。
浮在水面的润滑剂可撇去,吸附在氧化铁皮上的润滑剂可随氧化铁皮一起除去。
对轧制润滑前和轧制润滑期间对轧线回水含油量、经撇油机处理后水中含油量作了抽样分析,见表2。
表2 轧线回水含油量和经撇油机处理后水中含油量的比较表2说明投入润滑油后轧线回水中油含量比平时上升,但经撇油机处理后,含油量可下降到平时水平,轧制润滑对C系统水质无明显影响。
作者简介:何晓明(1970~),男(汉族),福建人,工程师。
作者单位:宝山钢铁(集团)公司热轧部,上海200941参考文献1Wandrei C L. Review of Hot Rolling Lubricant Technology for Steel. Inland Steel Company.2Barzan D. The Use and Performance of High Speed Steel Rolling at Inland's 80 Inch Strip Mill. Inland Steel Company.3Petre L T. Hot Strip Mill Roll Bite Lubrication. New Zealand Steel.4叶茂.金属塑性加工中摩擦润滑原理及应用[M].沈阳:东北工学院出版社,1990.5中南工业大学机电学院.金属塑性加工摩擦与润滑[M].长沙:中南工业大学,1996。