热轧工艺润滑与粘铝的关系
3 压力加工中的金属粘着与粘着摩擦解析

对许多金属材料进行的试验表明,金属 的本身性质对于粘着影响很大 。 1) 晶体结构: 面心立方与体心立方金属都比密排六 方金属有较多的滑移系统,有利于通过 塑性粗糙化过程与相接触表面在几何外 形上很好的吻合。 2)硬度:金属越软,越有利于这种吻合。 因此,硬度高的金属,表现出较低的粘 着系数。 3)弹性模量:弹性模量越小,硬度越低, 粘着的点由于各部分的弹性作用而被拉 开的可能性就越小,也就越有利于金属 粘着的发展。
由此可见,影响工具与变形金属间粘着的 条件和因素是很复杂的。金属粘着现象的产生 条件简单归结为: 临界温度条件;临界膜厚条件以及热不稳定 条件等。 影响粘着的因素有:工具材料、变形金属与润 滑剂的性质,金属的表面增加率,面压,工具 与坯料的运动速度与温度,润滑剂导入条件, 工具与坯料相对滑移距离,变形程度,变形温 度与变形速度等。 事实上,我们可以把影响金属粘着的因素区 分为内部因素与外部因素两大类。
3.4 压力加工中的金属粘着磨损 3.4.1 热轧铝及铝合金时的轧辊粘铝 铝及铝合金对工具表面具有很强的粘着性, 在轧制,特别是热轧时很容易在轧辊辊 面上形成粘铝层(覆面铝)。 • 其结果,不仅使摩擦加大,使热轧坯料 表面出现种种在冷轧或精整等后续工序 中难以消除的缺陷,以及使制品在阳极 氧化处理中出现大量表面“黑斑”。
4) 加工硬化系数、熔点与再结晶温度和 粘着系数密切相关,实质都是接触界面 温度所能引起的诸如扩散等动力学过程。 硬化系数大的金属,不仅可使粘着点不 易切断。表现出较强的粘着力。而且根 据物理—化学的观点,这些剧烈强化的 局部区域内有较高的位错密度,即内能 较高,原子处于不稳定的高能态。当接 触界面温度(体积、表面及局部闪发温 度)升高时,使原子扩散运动能力增强, 有条件时,甚至可以穿过界面进行相互 扩散过程,使粘着进一步加强。
冷轧机工作辊粘铝现象分析及对策

冷轧机工作辊粘铝现象分析及对策摘要:考察和分析了南方某厂冷轧机工作辊频繁发生粘铝现象的主要原因,针对实际情况提出了预防粘铝的措施。
关键词:冷轧机工作辊;铝板带材;粘铝;对策进入盛夏,南方高温地区铝加工厂的高速冷轧机常发生工作辊粘铝现象,严重影响正常生产。
就常规而言,高速冷轧机粘铝现象一般是发生在高速轧制时突然断带;或者是铝板带材冷轧时,在一定温度、压力条件下,铝及其氧化物粘在轧辊表面形成亲和现象,导致粘铝现象。
粘铝程度取决于轧制铝及铝合金的性质、轧制温度、轧制油和轧制环境等实际情况。
南方某厂的冷轧机工作辊连续多次发生粘铝现象,笔者就此进行了深入分析,对产生原因及预防措施提出了粗浅意见。
1 相关因素介绍1.1 主要设备(1)轧冷轧:1110mm可逆式;轧制力,4000kN;轧制速度,0-150-420m/min;卷取张力,0.75MPa(最大);主电机,900kW;压下速度,5.5mm/min (一般),26.6mm/min(快速)。
(2)轧辊:支承辊规格,Φ610mm×1100mm(随轧机一同由英国购入);工作辊,Φ255mm×1150mm(国产)。
1.2粘铝情况笔者到现场查阅了原始换辊通知单和磨辊记录,并进行统计与排列。
发现在7月22日~8月20日期间共换辊40余次,而平时每月只有10余次。
通过排列分析发现:工作辊由于擦伤、辊印而换辊7次;由于粘铝换辊33次,其中有5次注明严重粘铝。
从原始记录中记载粘铝现象有3/5发生在上工作辊或下工作辊的中部,其余的出现在轧辊的两侧或端面。
在现场又对冷轧机支撑辊的辊表面进行查看,发现在上、下支撑辊中心部位均有剥落带。
上工作辊在辊的中心部位有70㎜宽、400㎜长的剥落带(见图一),其凹陷深度为3~4㎜,同时看到铝带材表面有90㎜的辊印痕带,说明支承辊的剥落缺陷已反映到工作辊的辊表面上。
通过仔细查看,发现支承辊两侧表面也存在不同程度的细小裂纹或擦伤。
轧制油相关知识解析

7、添加剂主要技术指标:
分析项目 使用类型
运动粘度(40℃)( mm2/s)
密度(40℃)(g/m3) 闪点(闭口)(℃) 酸值(mgkoH/g) 皂化值(酯)(mgkoH/g) 羟值(醇)(mgkoH/g) 机械杂质(%)
性能指标
板带用
铝箔用
8.0~9.0
3.0~4.0
0.84~0.85 ≥100
5、基础油主要技术指标:
分析项目 运动粘度(40℃)(mm2/s) 密度(40℃)(g/m3) 闪点(闭口)(℃) 酸值(mgkoH/g) 皂化值(mgkoH/g) 碘值(mgkoH/g) 馏程(℃) 灰分(%) 芳烃含量(%) 水分(%) 硫含量(%)
性能指标 1.6~2.1 0.79~0.82
3、对轧制油的要求:
(1)有良好的润滑性能,摩擦系数小; (2)有较高的比热容;容易带走较多的热量; (3)有足够的承载能力,能达到预期压下量; (4)退火时不易形成油斑; (5)有良好的抗氧化稳定性; (6)对设备、铝带无腐蚀作用; (7)无毒无难闻气味,对人体健康无害; (8)容易过滤和净化,资源丰富,价格低廉。
轧制油相关知识
1、轧制油的作用:
(1)减小轧制时的摩擦系数和轧制力; (2)带走轧制时所产生的热量; (3)控制板型; (4)防止轧辊粘铝; (5)冲洗轧辊,除掉残留在轧辊上的铝粉,改
善轧件表面光洁度。
2、轧制油的润滑机制:
轧制时,旋转的轧辊表面和轧件表面通过机械夹带 和物理吸附作用,使轧制油增压进入轧辊和轧件的楔形 缝隙间,轧制油越靠近楔顶,润滑楔内产生的压力就越 大,当其压力达到轧件的屈服强度极限时,一定厚度的 润滑层进入轧件轧制变形区,形成油膜。轧辊与轧件间 的摩擦逐渐由干摩擦转变为液体摩擦。干摩擦时轧辊与 轧件直接接触,轧辊和轧件表面磨损严重。液体摩擦时 轧辊和轧件完全被润滑油膜隔开,当变形区呈现油膜极 薄且牢固连续时,轧件可获得最佳表面光洁度。
轧制过程中形成动压润滑的条件
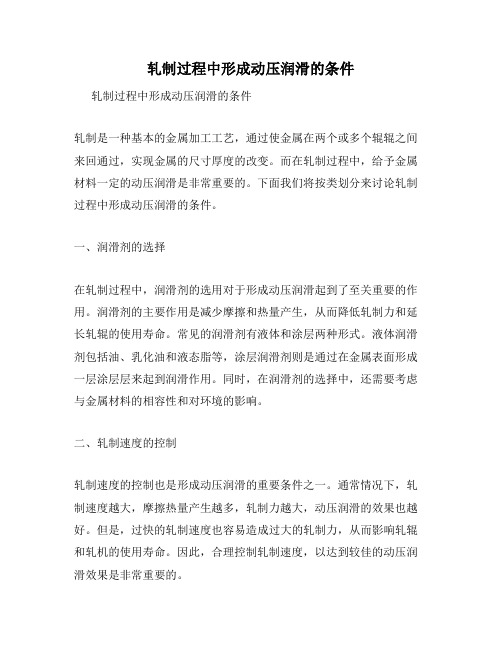
轧制过程中形成动压润滑的条件轧制过程中形成动压润滑的条件轧制是一种基本的金属加工工艺,通过使金属在两个或多个辊辊之间来回通过,实现金属的尺寸厚度的改变。
而在轧制过程中,给予金属材料一定的动压润滑是非常重要的。
下面我们将按类划分来讨论轧制过程中形成动压润滑的条件。
一、润滑剂的选择在轧制过程中,润滑剂的选用对于形成动压润滑起到了至关重要的作用。
润滑剂的主要作用是减少摩擦和热量产生,从而降低轧制力和延长轧辊的使用寿命。
常见的润滑剂有液体和涂层两种形式。
液体润滑剂包括油、乳化油和液态脂等,涂层润滑剂则是通过在金属表面形成一层涂层层来起到润滑作用。
同时,在润滑剂的选择中,还需要考虑与金属材料的相容性和对环境的影响。
二、轧制速度的控制轧制速度的控制也是形成动压润滑的重要条件之一。
通常情况下,轧制速度越大,摩擦热量产生越多,轧制力越大,动压润滑的效果也越好。
但是,过快的轧制速度也容易造成过大的轧制力,从而影响轧辊和轧机的使用寿命。
因此,合理控制轧制速度,以达到较佳的动压润滑效果是非常重要的。
三、轧制温度的控制轧制温度的控制同样也会对动压润滑产生重要影响。
当轧制温度较低时,金属材料会强度较高,摩擦系数也相对较大,从而增加了动压润滑的难度。
而当轧制温度适中时,金属材料的塑性较好,摩擦系数较小,动压润滑更容易形成。
因此,通过合理控制轧制温度,使其处于适宜的范围内,有利于形成较好的动压润滑条件。
四、辊辊几何形状的设计辊辊几何形状的设计也会对动压润滑产生一定影响。
通常情况下,辊辊的凸度较小,轧制面的接触面积较大,会增加摩擦,并使动压润滑更容易实现。
而辊辊的凸度较大,则会减小摩擦力,并使动压润滑的效果较差。
因此,通过合理设计辊辊的几何形状,可以提高动压润滑的效果。
五、辊辊与金属材料的表面质量辊辊与金属材料的表面质量也会对动压润滑产生一定影响。
当辊辊和金属材料的表面粗糙度较大时,会增加摩擦力,破坏动压润滑的效果。
因此,提高辊辊和金属材料的表面质量,减小摩擦,有助于形成较好的动压润滑条件。
铝板热轧机乳化液工艺润滑系统设计

铝板热轧机乳化液工艺润滑系统设计陈敏【摘要】介绍了乳化液工艺润滑系统在热轧铝板轧机上的应用、设备组成及工艺参数.【期刊名称】《中国重型装备》【年(卷),期】2016(000)002【总页数】4页(P6-8,12)【关键词】热轧铝板;乳化液;润滑系统【作者】陈敏【作者单位】中国第二重型机械集团公司,四川618000【正文语种】中文【中图分类】TG333.7+1铝及铝合金的热轧温度一般在320~520℃之间,由于铝材的特殊性,极易与轧辊发生粘连,造成热轧板带表面缺陷,因此必须采用润滑与冷却性能好的乳化液进行工艺润滑。
喷射到轧机上的乳化液与高温铝板和轧辊接触时,稳定的乳化状态被破坏,油水分离,油吸附在铝板和轧辊表面并进入轧制变形区,起到润滑作用,减少轧辊表面粘铝,降低轧制力;分离的水由于蒸发对轧辊起到冷却作用,通过调节乳化液的喷射流量、压力,能更好地控制辊型,从而提高产品的板型和表面质量。
乳化液的正确使用与润滑冷却效果密切相关,在设计乳化液工艺润滑系统时应满足使用乳化液介质的如下要求:(1)粒径效应:系统能使油在水中均匀分布;(2)使用浓度:系统能方便调整乳化液浓度;(3)使用温度:系统能自动控制介质的温度;(4)使用周期:系统能方便维护和管理,防止乳液腐败变质,尽量延长乳液使用寿命;(5)循环过滤:系统能有效防止其它因素对其污染,同时去除沉淀物及液面上的悬浮物。
本文以1 850 mm“1+4”铝带热连轧精轧机区为主要介绍对象。
乳化液工艺润滑系统是以乳化液为工作介质的设备,乳化液主要由基础油、乳化剂、添加剂和水组成。
精轧机区乳化液系统是循环供送工艺润滑介质的设备,用作热轧铝带精轧机区辊系及带材的润滑和冷却。
阶段性喷射小流量的乳化液用于对精轧机区的辊道、圆盘剪、卷筒等设备的冷却和润滑。
系统流量/L·min-1:30 000扬程/m:90工作介质:95%软水+5%基础油(可溶性脂)工作温度/℃:50~60主乳液箱容积/m3:520精轧机区乳化液工艺润滑系统由五个子系统组成,即配液系统、净液系统、污液系统、过滤系统、分段控制系统。
压铸 积碳和粘铝的关系

压铸积碳和粘铝的关系英文回答:Die Casting Buildup and Sticking.Die casting is a high-pressure casting process that forces molten metal into a mold cavity. The high pressure used in die casting can cause carbon buildup on the die surface, which can lead to sticking. Sticking occurs when the molten metal adheres to the die surface, preventing the casting from being ejected from the mold.There are several factors that can contribute to carbon buildup on the die surface, including:The type of metal being cast: Some metals, such as aluminum, are more likely to cause carbon buildup than others.The temperature of the molten metal: The higher thetemperature of the molten metal, the more likely it is to cause carbon buildup.The speed at which the molten metal is injected into the mold: The faster the molten metal is injected into the mold, the more likely it is to cause carbon buildup.The condition of the die surface: A rough or damaged die surface is more likely to cause carbon buildup than a smooth, well-maintained die surface.There are several ways to prevent carbon buildup on the die surface, including:Using a die lubricant: A die lubricant can help to reduce friction between the molten metal and the die surface, which can help to prevent carbon buildup.Maintaining the die surface: A smooth, well-maintained die surface is less likely to cause carbon buildup.Controlling the temperature of the molten metal: Thetemperature of the molten metal should be kept as low as possible to reduce the risk of carbon buildup.Injecting the molten metal into the mold at a slow, steady speed: Injecting the molten metal into the mold at a slow, steady speed can help to reduce the risk of carbon buildup.中文回答:压铸积碳和粘铝的关系。
热轧工艺润滑
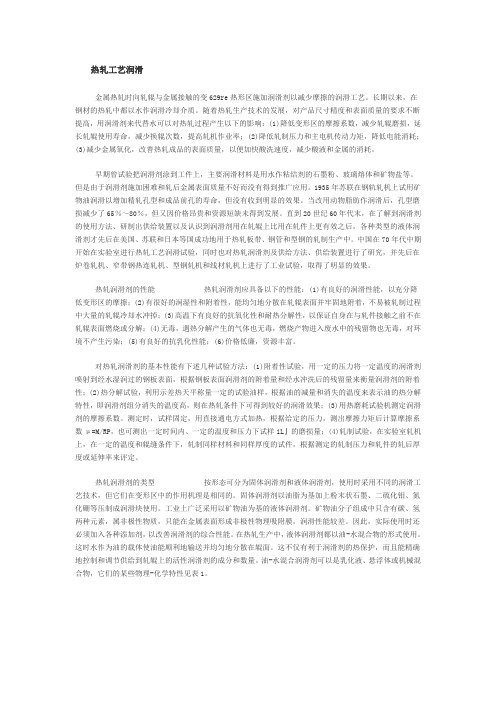
热轧工艺润滑金属热轧时向轧辊与金属接触的变629re热形区施加润滑剂以减少摩擦的润滑工艺。
长期以来,在钢材的热轧中都以水作润滑冷却介质。
随着热轧生产技术的发展,对产品尺寸精度和表面质量的要求不断提高,用润滑剂来代替水可以对热轧过程产生以下的影响:(1)降低变形区的摩擦系数,减少轧辊磨损,延长轧辊使用寿命,减少换辊次数,提高轧机作业率;(2)降低轧制压力和主电机传动力矩,降低电能消耗;(3)减少金属氧化,改善热轧成品的表面质量,以便加快酸洗速度,减少酸液和金属的消耗。
早期曾试验把润滑剂涂到工件上,主要润滑材料是用水作粘结剂的石墨粉、玻璃熔体和矿物盐等。
但是由于润滑剂施加困难和轧后金属表面质量不好而没有得到推广应用。
1935年苏联在钢轨轧机上试用矿物油润滑以增加精轧孔型和成品前孔的寿命,但没有收到明显的效果。
当改用动物脂肪作润滑后,孔型磨损减少了65%~80%,但又因价格昂贵和资源短缺未得到发展。
直到20世纪60年代末,在了解到润滑剂的使用方法、研制出供给装置以及认识到润滑剂用在轧辊上比用在轧件上更有效之后,各种类型的液体润滑剂才先后在美国、苏联和日本等国成功地用于热轧板带、钢管和型钢的轧制生产中。
中国在70年代中期开始在实验室进行热轧工艺润滑试验,同时也对热轧润滑剂及供给方法、供给装置进行了研究,并先后在炉卷轧机、窄带钢热连轧机、型钢轧机和线材轧机上进行了工业试验,取得了明显的效果。
热轧润滑剂的性能热轧润滑剂应具备以下的性能:(1)有良好的润滑性能,以充分降低变形区的摩擦;(2)有很好的润湿性和附着性,能均匀地分散在轧辊表面并牢固地附着,不易被轧制过程中大量的轧辊冷却水冲掉;(3)高温下有良好的抗氧化性和耐热分解性,以保证自身在与轧件接触之前不在轧辊表面燃烧或分解;(4)无毒,遇热分解产生的气体也无毒,燃烧产物进入废水中的残留物也无毒,对环境不产生污染;(5)有良好的抗乳化性能;(6)价格低廉,资源丰富。
轧制工艺润滑技术
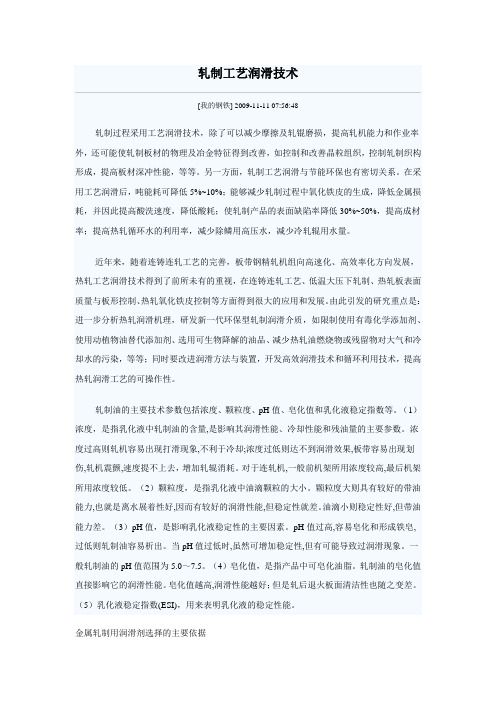
轧制工艺润滑技术[我的钢铁] 2009-11-11 07:56:48轧制过程采用工艺润滑技术,除了可以减少摩擦及轧锟磨损,提高轧机能力和作业率外,还可能使轧制板材的物理及冶金特征得到改善,如控制和改善晶粒组织,控制轧制织构形成,提高板材深冲性能,等等。
另一方面,轧制工艺润滑与节能环保也有密切关系。
在采用工艺润滑后,吨能耗可降低5%~10%;能够减少轧制过程中氧化铁皮的生成,降低金属损耗,并因此提高酸洗速度,降低酸耗;使轧制产品的表面缺陷率降低30%~50%,提高成材率;提高热轧循环水的利用率,减少除鳞用高压水,减少冷轧辊用水量。
近年来,随着连铸连轧工艺的完善,板带钢精轧机组向高速化、高效率化方向发展,热轧工艺润滑技术得到了前所未有的重视,在连铸连轧工艺、低温大压下轧制、热轧板表面质量与板形控制、热轧氧化铁皮控制等方面得到很大的应用和发展。
由此引发的研究重点是:进一步分析热轧润滑机理,研发新一代环保型轧制润滑介质,如限制使用有毒化学添加剂、使用动植物油替代添加剂、选用可生物降解的油品、减少热轧油燃烧物或残留物对大气和冷却水的污染,等等;同时要改进润滑方法与装置,开发高效润滑技术和循环利用技术,提高热轧润滑工艺的可操作性。
轧制油的主要技术参数包括浓度、颗粒度、pH值、皂化值和乳化液稳定指数等。
(1)浓度,是指乳化液中轧制油的含量,是影响其润滑性能、冷却性能和残油量的主要参数。
浓度过高则轧机容易出现打滑现象,不利于冷却;浓度过低则达不到润滑效果,板带容易出现划伤,轧机震颤,速度提不上去,增加轧辊消耗。
对于连轧机,一般前机架所用浓度较高,最后机架所用浓度较低。
(2)颗粒度,是指乳化液中油滴颗粒的大小。
颗粒度大则具有较好的带油能力,也就是离水展着性好,因而有较好的润滑性能,但稳定性就差。
油滴小则稳定性好,但带油能力差。
(3)pH值,是影响乳化液稳定性的主要因素。
pH值过高,容易皂化和形成铁皂,过低则轧制油容易析出。
- 1、下载文档前请自行甄别文档内容的完整性,平台不提供额外的编辑、内容补充、找答案等附加服务。
- 2、"仅部分预览"的文档,不可在线预览部分如存在完整性等问题,可反馈申请退款(可完整预览的文档不适用该条件!)。
- 3、如文档侵犯您的权益,请联系客服反馈,我们会尽快为您处理(人工客服工作时间:9:00-18:30)。
变形区 轧辊表面润滑层
转变区
热轧工艺润滑与粘铝的关系
作者:谢仁泽
我们厂的热轧运转已经三年了,表面质量一直是影响我们产品质量的主要瓶颈。
热轧工序控制表面质量至关重要,性能良好的热轧润滑液对表面质量的控制具有十分重要的意义。
通常热轧都是在300℃以上的温度下进行的,由于铝的熔点低,屈服强度低,极易粘附,在轧制过程中容易产生粘铝的表面缺陷。
经阳极氧化后显露为黑斑。
严重影响产品质量,经冷轧轧制后也难以消除。
1. 铝合金热轧特点与乳液润滑机理
1.1 铝合金热轧特点
铝合金热轧的一个显著特点是在轧辊上覆盖一层“铝膜”的情况下进行。
从John
A.Schey,<<LIGHT METAL AGE>>上可知这种“铝膜”主要由三氧化二铝和10%∽15%的铝粉及润滑剂及残渣的碳素物组成。
正因为轧制是在带有“铝膜”的辊面间进行,所以轧铝油性能的好坏和乳液的日常管理对铝材表面质量的控制具有十分重要的意义,它决定了辊面铝膜状态。
1.2 乳液润滑之物理分析
热轧乳液的基本功能是减少摩擦,防止轧辊与轧件粘结,同时控制工作辊
辊形与温度。
在轧制过程中乳液作为冷却润滑剂喷向轧辊和轧件,均匀而充足的乳液
在变形区入口处形成楔形油楔(如图1)。
由流体动力学基本原理可知,当固体表面运动时,粘附于轧辊和轧件表面的润滑
剂分别随运动的轧辊与轧件同步运动,中间流体作层流运动。
因此旋转的轧辊表面和运动的轧件表面使润滑剂增压进入楔形前区,越接近变形区入口平面润滑楔内产生的压力就越大。
当压力达到轧件发生塑性变形压力时,则有一定厚度的乳化液被带入变形区,还有轧辊与轧件的显微不平也将乳液带入变形区。
带入变形区的乳液受高温高压和剪切力作用而使油水分离,水蒸发带走热量,冷却轧辊轧件;分离出来的油相和添加剂与金属表面和金属屑反应,形成一层细密的辊面涂层,有效地隔离摩擦面而达到润滑的目的。
1.3乳液润滑之分子分析
我们目前使用的热轧润滑剂是由合成油和多种添加剂与水混合而成的一
种牛奶状液体,实际上是油以细小油滴形式分布于水中的水包油型乳化剂。
大家都知道油是由C 2n H 2n+2,CH 2n ,C n H 2n-x 等非极性烃类组成。
它们与金属表面接触时这种非极性
分子与金属之间仅靠瞬时偶极相互吸引形成物理吸附膜,其吸附能力仅为8.4—42千焦/摩尔。
(参考焦明山译的《金属压力加工中的摩擦与润滑》,董浚修写的《润滑原理及润滑油》等书)在变形区高温,高压,剪切力的苛刻条件下物理吸附膜易破坏或被挤走形成局部干摩擦。
这说明乳液没有良好的润滑性能,需加入油性剂加以改善。
油性剂分子带有极性基团,具有永久偶极。
与金属接触时,这些极性基团的价电子与金属表面的电子交换而产生化学结合力,呈定向排列吸附在金属表面上,吸附能力可达到42—420千焦/摩尔,被吸附分子相互间有吸引力从而以二聚体形式呈现紧密的定向排列分子栅。
非极性端在相反方向靠色散力与上层分子的非极性端吸引,形成定向排列的双分子层。
如此下去形成多分子层,将轧辊与轧件隔开。
从上述分析可知,轧制变形区处于流体润滑和边界润滑共存的半流体润滑状态。
2.热轧轧制中的粘铝分析
在轧制过程中变形区内的高温,高压及乳化液的化学活性使油从乳化液中分离出来,并在工作辊面上形成一层均匀的油膜,它防止了工作辊与轧件直接接触。
轧辊通过这层油膜向轧件施压使金属产生塑性变形。
同时轧制时的铝微粒从轧件向轧辊表面转移,在变形区内发生反应形成一层“铝膜”,组成粘铝层。
如果润滑剂性能好,工作辊上的粘铝层就薄。
但即使粘铝层很薄,也不能保证轧辊表面的粘铝不反映到轧件上。
生产过程中由于轧辊频繁地接触和碾压轧件,这时如果润滑控制不当,就会造成轧辊表面严重粘附的铝微粒显露在轧件上。
随着生产的延续,整个工作辊面的粘铝层就会越来越厚,随之增加了铝微粒的不稳定性而渐渐从辊面脱落,同时,又会有更多的新的铝微粒贴附上去,形成新的铝膜。
如此下去贴附在轧辊表面的粘铝层逐渐呈现出严重条痕。
在关铝的1300热轧机上由于个别地方的润滑不足使轧件表面轻者形成色差,重者造成粘铝缺陷的原因就是如此。
在现场轧制软铝时,我们常常会看到在轧制到4块料左右时粘铝缺陷就会越来越明显。
这时,如果我们不处理粘铝层区域的铝微粒就会在轧制过程中从轧辊表面脱落被压入铝材表面,形成金属压入。
这种由粘铝引起的金属压入呈无规则性。
它经过冷轧轧制后会出现表面起皮,孔洞等缺陷。
3. 影响热轧工艺润滑的因素
3.1 乳化液的热分离程度
乳化液的热分离指的是当乳化液和热的轧辊表面接触时所分离出的纯油量,是乳液最重要的性能指标。
乳液的稳定性实际上就是指它的热分离程度。
它关系到我们经常检测的ESI(既乳粒尺寸大小和分布)。
当ESI=1时润滑效果不好,说明稳定性太好,乳粒平均直径小,不易热分离,降低了润滑性能。
在生产中通常根据轧制合金的不同选用不同的 ESI值,在ESI一定时一般通过温度的控制使乳粒直径变大,增大热分离从而获得良好的润滑性能,减少轧辊粘铝改善轧件表面质量。
乳液稳定性的控制目的是调整乳粒尺寸大小及分布,它可以通过乳化剂的化学性质及HLB(既表面活性的亲油亲水平衡值)来调节。
在生产过程中我们也可以提高乳液库中乳液的温度增大乳液的热分离。
但是这个方法不可取,因温度升高冷却效果就会下降,不利于轧辊的降温,从而影响辊型。
辊温的升高又会导致辊面粘铝趋于严重。
所以生产中要根据具体情况调节乳液的稳定性。
3.2外来杂油的污染
3..2.1 外来杂油的危害
使乳液粘度不断增加,破坏了乳液的平衡,影响了乳液的流动性和润滑性能,增加了轧辊的粘铝倾向。
3.2.2 外来杂油的来源
轧机本体的液压油,齿轮油,润滑脂等。
3.2.3 外来杂油的控制
A. 首先必须有效地解决轧机本体的漏油问题,要勤检查,随时发现随时解决。
对发现了又无法解决的漏油点应采取相关措施把漏出的杂油引入收集装置中。
B. 将乳液静止一定的时间,使杂油充分地浮到液面上,然后进行撇油,使乳液中的杂油将至最少。
降低乳液中的灰份和疏水粘度。
4. 油中的金属铝屑
轧制时会产生许多金属铝屑,这些铝屑会粘附在油相上发生化学反应消耗添加剂。
乳液中的主要添加剂边界润滑剂,具有较高的化学活性,很易吸附于金属表面,对轧制性能和轧件表面的好坏起着关键作用。
大量细小铝屑在乳液中还会消耗有机酸直致逐渐耗尽。
因此轧机的过滤系统一定要经常开,选用好的过滤纸尽量滤掉乳液中的金属铝屑。
另外可定期对乳化液中的自由脂肪酸进行检测,发生表面质量问题或润滑问题时更需要频繁的检测。
5.乳化液配制用水
我们平常使用的自来水和地下水中含有较多的金属离子,如镁离子,钙离子等。
它们要与乳液中的自由脂肪酸反应生成金属皂,这就相当于减少了边界润滑剂的可使用量,使乳液变的不稳定。
所以配制乳液时一定要用去离子水。
总结:
通过分析乳液润滑和粘铝机理可知,要想获得高表面的热轧产品,首先必须控制轧辊表面粘铝层,使其变的薄而均匀。
为此我们可以使用清刷辊减轻工作辊辊面粘铝。
但是要根本解决辊面粘铝,使之保持理想的辊面状态,还得依靠润滑控制。
要切实保证热轧润滑的良好效果,就必须对乳化液的热分离程度,外来杂油的污染,油中的金属铝屑,乳化液的配制用水等关键因素严格控制。
由此就必须加强乳液的日常维护,采用合理的轧制润滑剂及其添加剂,严格控制轧机本体的漏油,保证良好的乳液过滤。
从而既保证了乳液良好的润滑性,又保证了乳液良好的清洁性,提高了生产效率,保证了产品表面质量,降低了生产成本,提高了经济效益。