电机振动在线监测系统解决方案
风电机组齿轮箱在线振动监测系统开发
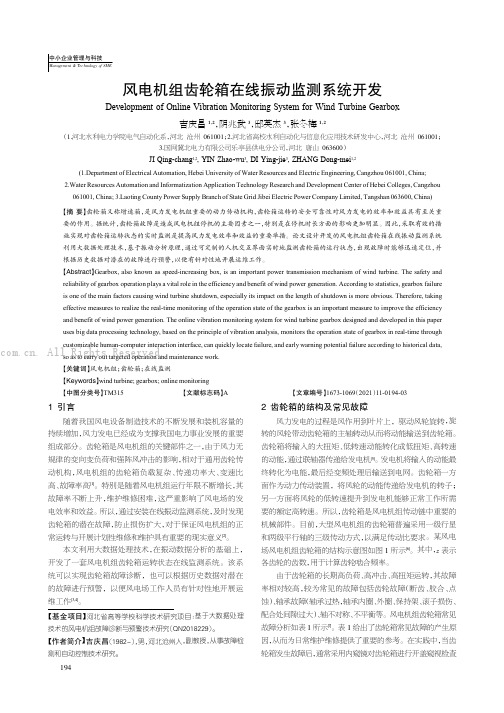
1引言随着我国风电设备制造技术的不断发展和装机容量的持续增加,风力发电已经成为支撑我国电力事业发展的重要组成部分。
齿轮箱是风电机组的关键部件之一,由于风力无规律的变向变负荷和强阵风冲击的影响,相对于通用齿轮传动机构,风电机组的齿轮箱负载复杂、传递功率大、变速比高、故障率高[1]。
特别是随着风电机组运行年限不断增长,其故障率不断上升,维护维修困难,这严重影响了风电场的发电效率和效益。
所以,通过安装在线振动监测系统,及时发现齿轮箱的潜在故障,防止损伤扩大,对于保证风电机组的正常运转与开展计划性维修和维护具有重要的现实意义[2]。
本文利用大数据处理技术,在振动数据分析的基础上,开发了一套风电机组齿轮箱运转状态在线监测系统。
该系统可以实现齿轮箱故障诊断,也可以根据历史数据对潜在的故障进行预警,以便风电场工作人员有针对性地开展运维工作[3,4]。
2齿轮箱的结构及常见故障风力发电的过程是风作用到叶片上,驱动风轮旋转,旋转的风轮带动齿轮箱的主轴转动从而将动能输送到齿轮箱。
齿轮箱将输入的大扭矩、低转速动能转化成低扭矩、高转速的动能,通过联轴器传递给发电机[5]。
发电机将输入的动能最终转化为电能,最后经变频处理后输送到电网。
齿轮箱一方面作为动力传动装置,将风轮的动能传递给发电机的转子;另一方面将风轮的低转速提升到发电机能够正常工作所需要的额定高转速。
所以,齿轮箱是风电机组传动链中重要的机械部件。
目前,大型风电机组的齿轮箱普遍采用一级行星和两级平行轴的三级传动方式,以满足传动比要求。
某风电场风电机组齿轮箱的结构示意图如图1所示[6]。
其中,z 表示各齿轮的齿数,用于计算齿轮啮合频率。
由于齿轮箱的长期高负荷、高冲击、高扭矩运转,其故障率相对较高,较为常见的故障包括齿轮故障(断齿、胶合、点蚀)、轴承故障(轴承过热,轴承内圈、外圈、保持架、滚子损伤、配合处间隙过大)、轴不对称、不平衡等。
风电机组齿轮箱常见故障分析如表1所示[7]。
风力发电机振动在线监测系统
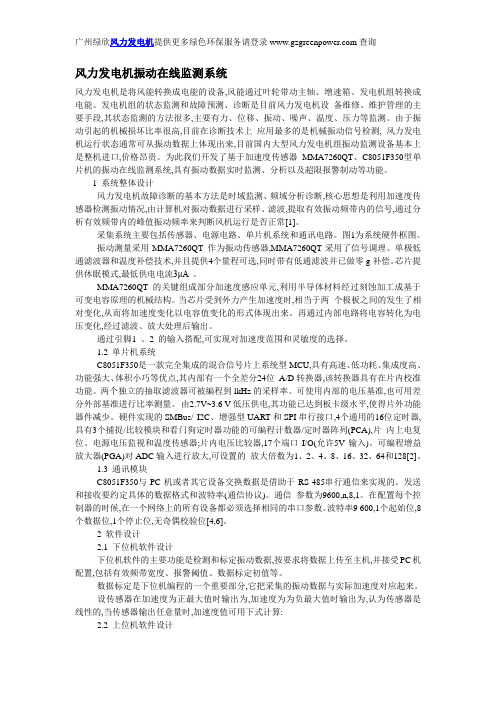
风力发电机振动在线监测系统风力发电机是将风能转换成电能的设备,风能通过叶轮带动主轴、增速箱、发电机组转换成电能。
发电机组的状态监测和故障预测、诊断是目前风力发电机设备维修、维护管理的主要手段,其状态监测的方法很多,主要有力、位移、振动、噪声、温度、压力等监测。
由于振动引起的机械损坏比率很高,目前在诊断技术上应用最多的是机械振动信号检测, 风力发电机运行状态通常可从振动数据上体现出来,目前国内大型风力发电机组振动监测设备基本上是整机进口,价格昂贵。
为此我们开发了基于加速度传感器MMA7260QT、C8051F350型单片机的振动在线监测系统,具有振动数据实时监测、分析以及超限报警制动等功能。
1 系统整体设计风力发电机故障诊断的基本方法是时域监测、频域分析诊断,核心思想是利用加速度传感器检测振动情况,由计算机对振动数据进行采样、滤波,提取有效振动频带内的信号,通过分析有效频带内的峰值振动频率来判断风机运行是否正常[1]。
采集系统主要包括传感器、电源电路、单片机系统和通讯电路。
图1为系统硬件框图。
振动测量采用MMA7260QT 作为振动传感器,MMA7260QT采用了信号调理、单极低通滤波器和温度补偿技术,并且提供4个量程可选,同时带有低通滤波并已做零g补偿。
芯片提供休眠模式,最低供电电流3μA 。
MMA7260QT的关键组成部分加速度感应单元,利用半导体材料经过刻蚀加工成基于可变电容原理的机械结构。
当芯片受到外力产生加速度时,相当于两个极板之间的发生了相对变化,从而将加速度变化以电容值变化的形式体现出来。
再通过内部电路将电容转化为电压变化,经过滤波、放大处理后输出。
通过引脚1 、2 的输入搭配,可实现对加速度范围和灵敏度的选择。
1.2 单片机系统C8051F350是一款完全集成的混合信号片上系统型MCU,具有高速、低功耗、集成度高、功能强大、体积小巧等优点,其内部有一个全差分24位A/D转换器,该转换器具有在片内校准功能。
风力发电机振动监测系统维修手册

风力发电机振动监测系统维修手册引言:风力发电机作为一种现代化的可再生能源发电设备,具有环保、高效、可持续的特点,在全球范围内得到广泛应用。
而风力发电机振动监测系统作为该设备的核心部件,对于确保设备的正常运行和减少损耗具有重要意义。
本维修手册旨在提供风力发电机振动监测系统的维修指导,从而帮助用户有效解决设备故障和提高系统性能。
一、系统概述风力发电机振动监测系统通过测量风力发电机振动参数,如振动加速度、振动速度和振动位移等,实时监测设备的运行状态,从而及时识别问题和进行预警。
该系统由传感器、数据采集模块、数据处理单元和显示控制终端等组成。
其主要功能包括:1. 监测风力发电机的振动水平,判断设备的工作状态和软硬件性能;2. 分析和识别设备振动异常,预警设备发生故障的潜在风险;3. 提供实时数据和报表,为维修和调试工作提供数据支持;4. 进行设备故障诊断,提供维修建议和方案。
二、振动监测系统的维护与维修振动监测系统的正常维护和维修对于确保其长期稳定运行和准确监测非常重要。
以下是相关的维护和维修指南:1. 传感器维护传感器是振动监测系统中非常关键的组成部分,其灵敏度和准确性直接影响系统的监测效果。
因此,传感器的维护非常重要。
(1)定期校准传感器的灵敏度,确保其准确度和可靠性;(2)检查传感器与设备的连接接头,确保传感器与设备之间的电气连接良好;(3)在传感器正常工作时,及时清洁传感器并保持传感器周围环境清洁,防止灰尘和杂质影响传感器的运行。
2. 数据采集模块维护数据采集模块负责将传感器采集的数据进行模拟/数字转换,并传输至数据处理单元。
以下是数据采集模块的维护要点:(1)检查数据采集模块的电源和信号连接,确保其正常工作;(2)定期清理数据采集模块和连接线路的灰尘和杂质,保持其通畅和良好的接触性能;(3)及时更换损坏的数据采集模块,确保其正常功能。
3. 数据处理单元维护数据处理单元负责接收和处理数据采集模块传输的数据,并进行分析和判断。
振动监测及分析系统(VMAS)在发电厂的应用

振动监测及分析系统(VMAS)在发电厂的应用摘要:振动状态监测及分析系统自动连续地采集与设备安全有关地主要状态参数:机组的振动、摆度、键相/转速、轴振、瓦振、轴位移、胀差、偏心、机组轴承负荷及温度、压力和开关量等,并自动形成各种数据库。
它能够自动识别设备的运行状态,预测和诊断设备的故障;能够促进设备维修方式向预知维修(状态维修)的转变,确保设备安全稳定地运行。
关键词:振动状态监测及分析系统(VMAS);信号处理;诊断。
0. 引言随着对发电厂主要设备可靠性、稳定性、以及对电厂设备寿命要求的提高,越来越多的监测和诊断分析系统应用到实际电厂项目中。
汽轮机、发电机、以及主要高压电动机设备作为发电厂的主要运行设备,更是成为监测和诊断的重要对象。
随着先进信号处理技术以及诊断技术的发展,振动监测及分析系统(VMAS)能在故障出现的早期阶段及时地预告故障的存在和发展,避免灾难性事故发生,并可以将现有的周期预防性维修改为预知性的维修, 选择最佳停修时间,提高机组可利用率。
1. 振动状态监测及分析系统(VMAS)的定义振动状态监测及分析系统,英文全称是Vibration monitoring and analyze system ,缩写为VMAS。
振动状态监测及分析系统的主要功能是用于主辅机(通常包括汽轮机、发电机、以及主要的高压设备)状态监测与故障诊断,实现监测、控制、报警、诊断功能。
而在早期,振动状态监测和分析系统主要应用于汽轮发电机组,叫做旋转机械诊断监测管理系统,英文TDM (Turbine diagnosis management) ,在电厂中一般是指汽轮发电机组振动在线状态监测和分析系统。
实际上,这两个叫法是针对一套系统,只是监测的范围不同。
2. 振动状态监测及分析系统基本配置振动状态监测及分析系统是以计算机为平台的旋转机械振动状态在线监测及故障诊断系统,用于对汽轮机、发电机、电动机、风机、泵等设备的振动、转速、压力、流量、温度等信号进行连续监测。
电机运行状态在线综合监测系统的研究与构建

电机运行状态在线综合监测系统的研究与构建【摘要】电机运行状态在生产线安检中是重点监测对象,传统采用人工离线方式定期巡检。
本文应用传感设备检测状态信号,现场总线传输数据,组态软件采集管理数据的方法实现了电机运行状态的在线监测。
通过实时监测电机运行状态,及时诊断设备故障并维修设备,避免经济损失,保证生产安全稳定。
【关键词】电机;在线监测;专家系统;冗余一、引言针对鲍店煤矿选煤厂电动机的运行环境,为减少事故,降低能耗,确保安全生产,运用测控技术、计算机技术、网络通信技术等方法,对重要关键设备的电动机进行在线监测技术研究与应用。
在设备不停机的情况下通过对电动机的三相电压、电流、温度、振动等参数进行实时在线监测,对采集的参数数据进行算法分析,以信息融合理论来综合判断其运转是否正常,有无异常与劣化征兆。
通过对监测数据的分析处理,实现能耗评估,设备故障报警、检修预警等功能,以便提前制定采取针对性措施来控制和防止事故的发生,从而避免设备突发性故障造成的设备损坏以及停工停产等巨大损失,减少计划维修所造成的一些浪费,不断提高设备完好率与使用率,从而实现对电机的综合监控及保护。
二、系统设计方案电机在线监测网络拓扑图见图1,为增加系统可靠性,采用冗余设计方案,主从设备互为备份自动切换。
在选煤厂原煤车间生产线上,选取16台重要关键设备电机和2个分级筛作为重点监测对象,主要监测电机三相电压、三相电流、功率、电量、温度、振动等运行状态参数。
电压和电流互感器检测电机三相电信号,经三相电参数模块计算出各个电参数并通过RS485总线传送到串口服务器。
串口服务器通过以太网交换机向电机综合监测系统提供各个电参数模块的数据。
温度传感器检测电机温度,经温度变送器输出模拟信号到信号隔离器。
振动传感器检测分级筛振动,经振动模块输出模拟信号到信号隔离器。
信号隔离器输出模拟信号到西门子PLC。
PLC计算温度和振动值并通过以太网交换机向电机综合监测系统提供温度和振动数据。
汽轮发电机组振动在线监测系统失真原因分析及处理

Ke r s t r o g n r t ru i o l e mo i r g vb ain sg a ; itrin a ay i y wo d : u b — e e ao n t n i nt i ; i r t i n l d s t ; n l s ; n on o o o s
风力发电机组在线振动监测系统及现场应用研究

风力发电机组在线振动监测系统及现场应用研究为了能够更好的避免和减少风力发电机故障带来的重大事故和安全隐患,并且在日常对风力发电机进行维护节省成本,在线振动监测系统必不可少。
本文介绍了在线监测系统的功能简介、工作原理、传感器测点选取和数据处理等关键技术及系统实际应用,对风电振动监测具有一定借鉴意义。
标签:风力发电机组;在线振动监测;现场应用1 系统功能简介风力发电机组工作条件通常比较艰苦,经常地处风沙四起的荒漠或海风盛行的海上,且在变速变载条件下运行。
因此,风电机组设备的相关零部件出故障的几率大大高出其他机械设备,为避免风电机组零件损坏造成的不必要经济损失,机组在线监测势在必行。
风电场中的在线监测系统,需对每一台机组都进行实时的状态监控与故障监测。
所以,监测系统采用分布式设计,主要由硬件和软件两个部分组成:硬件包括振动一体传感器、数据采集仪、现场服务器以及中心服务器等;软件部分包括数据传输和数据诊断分析与报警等功能。
系统软件设计较为复杂,数据传输功能,包括数据采集、数据存储、数据上传等单元;诊断分析功能,先进行信号提取,再进性处理,识别信号特征,接着对故障进行诊断,最后显示报警状态。
其中,采集的信号主要包括发电机前后轴承处的振动信号、发电机接地电压等信号。
2 系统工作原理目前,风力发电机组的故障检测与诊断技术有多种:振动检测、温度检测、声发射检测及润滑油分析检测等多种方法。
针对每种检测方法各有其优缺点:温度检测方法简单,但引起温度变化原因复杂多变;声发射检测技术通过故障设备本身发出的高频应力波信号检测,受周围环境噪声的干扰较小,但是相关测试设备费用贵、误报警率高,且对测试条件、测试环境以及测试信号的消噪预处理技术等环节要求较高;振动检测技术应用较为广泛,技术相对成熟,主要实时监测风电机组发电机前后轴承座表面的振动数据,这些实时的数据能够被规整在一个较长的周期内形成波形图,便于工作人员在这个周期内进行趋势分析,确定发电机前后轴承的工作情况,以及各个零件的健康状况,便于尽早发现发电机内部的零件损伤。
智能化振动在线监测与故障诊断系统的应用

70 EPEM 2019.12发电运维Power Operation当今工业企业的生产越来越趋向智能化、信息化,对设备的稳定性、安全性的要求也越来越高,状态监测和故障诊断技术也更加受到电力企业的重视。
传统燃煤发电厂一直采用计划维修与事后维修方式,该维修体制无法全面、及时地了解设备运行状况,事后维修则因事前准备不足,往往造成维修工作旷日持久,损失重大。
当前,面对火电机组运维成本高的问题,电力企业和设备厂商都在寻求技术解决方案。
华能莱芜公司所使用的智能决策系统,可实现数据采集、故障诊断、结论推送等功能,为生产运维提供支撑。
1传统运维方式和智能化运维方式的比较与分析发电企业中的大型转机设备,如大型水泵、大型风机等,普遍安装有振动检测系统,该类配套监测装置能够从一定程度上反映设备振动的大小或作为设备保护动作信号的来源。
但从在线监测与故障诊断的角度看,传统在线监测系统已满足不了智能化、信息化时代的要求,具体体现在两个方面:不能及时发现并诊断故障,经常引起非停及降负荷事故,使企业蒙受巨大的经济损失;传统的DCS 系统软件界面中,监测数据只有振动超标报警值输出及保护跳机值输出,对确定故障部位及严重程度没有任何诊断价值,更无法精确指导设备的优化检修和精细化检修。
为补充传统在线监测的不足,华能莱芜公司对#6、#7机组智能决策系统对重要辅机设备实施了基于现代化的运维思想的可视化在线监测系统,与传统的在线监测相比,该系统可以实现:同步在线采集数据;内置故障判断和轴承特征频率数据库;具备故障诊断功能,系统自动生成诊断结果;冲击解调方法准确判断轴承状态;设备故障时自动报警并推送诊断结论和维护建议;可与现有在线系统数据进行对接,多运行参数展示;可视化平台一体展示。
智能化振动在线监测与故障诊断系统的应用华能莱芜发电有限公司 张兰庆 董 鹏 王奉平 杨柏依 任建永 马道锋北京必可测科技股份有限公司 张 敬 曹定华 徐建伟 祁双鹤2 系统的组成华能莱芜公司与北京必可测科技股份有限公司合作,在莱芜发电厂共同构建#6、#7机组智能化的在线监测系统。
- 1、下载文档前请自行甄别文档内容的完整性,平台不提供额外的编辑、内容补充、找答案等附加服务。
- 2、"仅部分预览"的文档,不可在线预览部分如存在完整性等问题,可反馈申请退款(可完整预览的文档不适用该条件!)。
- 3、如文档侵犯您的权益,请联系客服反馈,我们会尽快为您处理(人工客服工作时间:9:00-18:30)。
.
.
钛能科技根据多年来的状态监测实践,针对电机故障研发出了一套电机振动在线监测系统解决
方案,对全面推动我司电机状态监测工作深入开展发挥了重要作用。
1. 引言
电机是现代工业生产中的重要电气设备,是现代工业生产的重要物质和技术基础,广泛应用于
钢铁、石油、化工、电力、建材、机械制造、汽车、轻纺、交通运输、环保等各个行业。各种电机
设备的技术水平和运行状况是影响一个工业企业各项经济技术指标的重要因素,电机故障会对企业
生产运营造成严重影响。一般说来,电机故障约有 60%-70%是通过振动和由振动辐射出的噪声反映
出来的,因此现场应用中,振动监测技术是应用比较普遍的故障诊断方法。
电机振动主要由电枢不平衡、电磁力、轴承磨损、转轴弯曲和安装不良使电机与负载机械的轴
心线不对中或倾斜等原因引起的。电机振动三个基本参数,分别是振幅、频率和相位。其中振幅可
用位移、速度和加速度来表示。在测量过程中我们一般对高频故障(如滚动轴承、齿轮箱故障等)
或高速设备进行测量时,应选加速度为参考量;在对低频故障(如不平衡、不对中等)或低速设备
测量时,应选位移为参考量;而在进行振动的总体状态测量时,选速度为参考量。电机振动大小必
须要满足国家的电机振动标准,否则会造成很严重的后果。
要做好电机振动的监测诊断,首先要对诊断对象做全面的了解以及必要的机理分析,比如 : 机
器的结构和动态特性(齿轮与轴承规格、特征频率等),机器的相关机件连接情况(如动力源、基座
等),机器的运行条件(如温度、压力、转速)及维修技术(如故障、维修、润滑、改造),异常振
动的形态和特性。
2. 解决方案
2.1 方案概述
钛能科技根据已有的技术规范,在对钢铁、石化、水泥客户广泛深入调研的基础之上,结合自
身多年来的技术积累,精心开发了电机振动在线监测系统,受到了客户的肯定和好评。
钛能科技电机振动在线监测系统依托先进的物联网传感技术,通过测定电机设备特征参数(如
振动加速度、速度、位移等),计算并存储设备的运行参数,自动生成日数据库、历史数据库及报警
库。将特征参数值与设定值进行比较,来确定设备当前是处于正常、异常还是故障状态,设备一旦
出现异常或者故障,及时报警通知运行管理人员。尽可能多的采集故障信息,从而获得设备的状态
变化规律,预测设备的运行发展趋势,帮助用户查找产生故障的原因,识别、判断故障的严重程度,
1
.
.
为科学检修提供指导。
2.2 引用标准
1) GB/T 29531-2013《泵的振动测量与评价方法》
2) GB 4832-1984《大电机振动测定方法》
3) GB/T 10068.2-1988《旋转电机振动测定方法及限值 振动限值》
4) GB14711-93《中小型旋转电机安全通用要求》
5) GB/T 33904-2017《工业物联网仪表服务协议》
6) GB/T 34072-2017《物联网温度变送器规范》
2.3 方案介绍
钛能科技电机振动在线监测系统,采用了模块化设计,包括数据采集单元、通讯单元(无线、
有线)、数据计算与存储单元、状态显示与报警单元和诊断分析与报表单元。这些模块既可以组建全
程无线监测系统、也可以组建无线+有线监测系统,由用户根据现场环境和自身需求灵活选用。系
统具有标准的网络接口,传输距离无限扩展,支持跨平台操作系统,设计界面友好,数据文件管理
科学有效。
图 1 系统架构图
数据采集
电机振动在线监测系统的关键在于数据采集获取,为此我们选用动态特性好、频响范围宽、工
2
.
.
作温度量程大、多场合使用、测量范围宽、信号分辨率高、响应速度快、抗干扰能力强、不受油污
介质影响的传感器,为电机振动在线监测系统可靠运行打下了坚实的基础。
通讯层
电机监测点传感器采集的信息,在通讯层通过状态变送器、中继器(可选)、接收器上传数据。
变送器数据无线传输到中继器,经过中继器(可选)接力到接收器,接收器通过 2G/4G 网络上传数
据到服务器,整体架构完全无需布线,降低用户通讯组网的施工成本与改造时间。
应用平台系统
将数据采集体系采集到的数据,输入至系统进行结果分析和推算。分析中需要用到的行业经验
数据等参考数据,系统自动从专家数据库提取,最后形成用户使用数据。需要指出的是,对于关键
重要设备,为了及时发现机组的突发故障和潜在隐患,必须采用实时监测分析系统。利用每个通道
内置的 DSP 实时处理系统,实时不丢点的对所有数据进行分析处理。
2.4 基本功能
电机振动在线监测系统,可以实现电机设备的温度、振动、轴承状态进行自动监测,运行可靠、
使用便捷,实时反映设备的运行状态,为异常设备的故障诊断提供可靠的数据和方便的分析手段,
其技术性、可靠性、经济性取代了传统的人工巡检方式,实现了工业企业大量电机设备的在线监测,
将企业的设备管理水平提升到新的高度。
设备监测
设备监测图,显示设备测点名称、测点位置、当前监测数据。
图 2 设备监测图
趋势分析
3
.
.
趋势分析包括振动、包络、轴位移或者其他参数随时间的变化趋势。可以切换显示振动的通频、
1 倍频幅值相位、2 倍频幅值相位等特征值的趋势。可同时显示单个测点或者多个测点的振动趋势。
图 3 测点趋势图
波形分析
可设定任意时间段的趋势图,波形图显示趋势图光标所在位置的振动波形,以趋势为导航,定
位到需要分析的数据,趋势导航可打开或者关闭。
图 4 振动波形图
波形频谱分析
可设定任意时间段的趋势图,同时显示光标所在位置的波形图和频谱图,以趋势为导航,定位
到需要分析的数据组,趋势导航可关闭或者打开。
4
.
.
图 5 振动波形与频谱图
3. 应用案例
案例 1:某油田采油厂 2#离心泵泵端振动超标,日常运行振动在 6 个烈度以上,对应频谱图如
图 6 所示,分析认为存在“跑套”现象,与现场负责人员交流,得出结论:泵长期运行,导致泵轴
磨损,与轴承配合间隙严重超标导致。
图 6 采油厂振动烈度频谱图
案例 2:离心泵振动值逐渐上升,趋势图信息如图 7、8 所示,主要频率为 125Hz,对应叶片通
过频率,检查为管道堵塞,流通不畅。
5
.
.
图 7 离心泵振动值超标设备图
图 8 离心泵振动值超标波形图
案例 3:螺杆压缩机,2985rpm,垂直方向振动大,主要频率成分为 200Hz,对应螺杆啮合频率,
现场诊断发现为基础共振。如图 9、10 所示。
6
.
.
图 9 螺杆压缩机垂直方向振动案例
图 10 螺杆压缩机垂直方向振动案例
案例 4:多级离心泵,2985rpm,电机垂直方向振动大,主要频率成分为 50Hz 工频,泵端振动
正常,分析认为电机部分基础刚度不足,现场检查为支撑框架开裂,如图 11、12 所示。
7
.
.
图 11 多级离心泵垂直方向振动案例
图 12 多级离心泵垂直方向振动案例
4. 客户价值
1) 通过对电机振动的基本参数(比如振幅、频率和相位等)进行采集、分析,用户能够远程
实时掌握电机设备的状态信息。系统界面友好,操作方便,注重用户体验,电机状态信息一目了然,
能够帮助用户提高电机的运维管理水平。
2) 当生产设备有突发状况或者异常时,系统能够及时有效的回应,并根据系统设置决定停机
或者报修,有效延长机器寿命,大幅减少维护成本。
8
.
.
3) 完整记录各种生产信息,不但可以提供生产效能及过程分析,还可以为制造执行系统提供
有效的信息,优化生产调度管理过程,提高企业生产效益。
4) 根据即时的设备运行状况,构建有效的动态预防保养策略,可以确保良好的设备运行状态,
保证设备的可靠性。
9