固定床反应器的数学模型..
第六章 固定床

水力半径
• 湿周---在总流的有效截面上,流体与固体壁面的接 触长度称为湿周,用字母L表示。
• 水力半径---总流的有效截面积A和湿周L之比。用字
母RH表示
RH = A / L
44
• 对于圆形截面的管道,其几何直径用水力半径表示 时可表示为
• A=(1/4)×πd2 • L=πd • 则 R=A/L=(1/4)×d → d = 4 R
当ReM>1000 湍流, 局部阻力损失为主, f≈1.75 , 略去第一项
结论: 对ΔP影响最大的是ε和u
49
Pf L
'(duSm 2 )(1B3B)
f ' 1501.75 ReM
一般床压不宜超过床内压力的15%,所以颗粒不 能太细,应做成圆球状。
50
➢ 压降的计算 ΔP=ΔP1+ ΔP2
= 15fu 0 OG L 0(1)21.75fuO 2 G L 0(1)
dS 2
3
dS
3
Pa
式中混合物的粘度
1
yi
fi M
2 i
f
1
yiM
2 i
kg/m.s
51
6.3 固定床中的传热
传热包括: 粒内传热,颗粒与流体间的传热,床层与器壁的传热
给热系数 αP 给热系数αW ,λer 总给热系数α t
当单纯作为换热装置时,以床层的平均温度tm与 管壁温差为推动力-----总给热系数αt
n
算术平均直径: d xWidi i1
调和平均直径:
1 n xWi
d
d i1 i
几何平均直径:
di
didi
30
6.2.3 床层空隙率及分布
固定床列管式反应器设计说明书(曾礼菁)
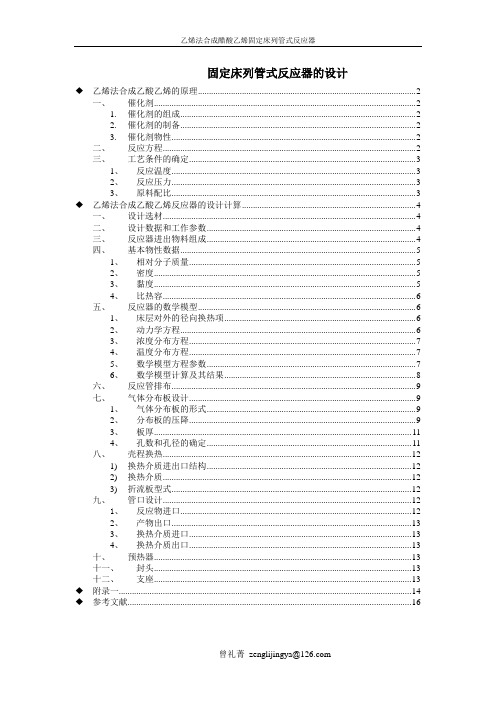
固定床列管式反应器的设计◆乙烯法合成乙酸乙烯的原理 (2)一、催化剂 (2)1. 催化剂的组成 (2)2. 催化剂的制备 (2)3. 催化剂物性 (2)二、反应方程 (2)三、工艺条件的确定 (3)1、反应温度 (3)2、反应压力 (3)3、原料配比 (3)◆乙烯法合成乙酸乙烯反应器的设计计算 (4)一、设计选材 (4)二、设计数据和工作参数 (4)三、反应器进出物料组成 (4)四、基本物性数据 (5)1、相对分子质量 (5)2、密度 (5)3、黏度 (5)4、比热容 (6)五、反应器的数学模型 (6)1、床层对外的径向换热项 (6)2、动力学方程 (6)3、浓度分布方程 (7)4、温度分布方程 (7)5、数学模型方程参数 (7)6、数学模型计算及其结果 (8)六、反应管排布 (9)七、气体分布板设计 (9)1、气体分布板的形式 (9)2、分布板的压降 (9)3、板厚 (11)4、孔数和孔径的确定 (11)八、壳程换热 (12)1) 换热介质进出口结构 (12)2) 换热介质 (12)3) 折流板型式 (12)九、管口设计 (12)1、反应物进口 (12)2、产物出口 (13)3、换热介质进口 (13)4、换热介质出口 (13)十、预热器 (13)十一、封头 (13)十二、支座 (13)◆附录一 (14)◆参考文献 (16)◆乙烯法合成乙酸乙烯的原理一、催化剂[6]选用Bayer-I型催化剂1.催化剂的组成:●活性组分——钯、金:组分金的作用是防止活性组分钯产生氧化凝聚,使钯在载体上维持良好的分散状态。
●助催化剂——乙酸钾:乙酸钾的存在有助于反应组分乙酸在钯金属上缔合,促进物理吸附的乙酸的离解和释放氢离子,使钯-氧间的键结合力减弱,促使乙酸钯的分解;此外,还可抑制深度氧化反应,从而提高了反应的选择性。
●载体——硅胶:承载活性组分及助催化剂,使其在载体表面上呈高度分散状态。
2.催化剂的制备:●结构:μ;中间的第二层是一层黑Bayer-I型催化剂为球星颗粒,最外面的第一层是灰色的表皮层,厚度约为100mμ;最里面的第三层是载体硅胶,呈浅土黄色。
固定床反应器的设计计算

固定床反应器的设计计算固定床反应器是一种广泛应用于化工工业中的反应器。
它由一个固定的反应床和气体或液体通过床体流动的装置组成。
固定床反应器通常用于进行催化反应,例如催化剂的制备、氢气的生成以及石油炼制过程中的裂化反应等。
在设计固定床反应器时,需要考虑反应床的尺寸、催化剂的选择、反应温度和压力等因素。
下面将介绍固定床反应器的设计计算流程。
首先,设计固定床反应器时需要确定反应物的种类和摩尔比。
通过摩尔比可以计算出反应物的总流量以及各个组分的摩尔流量。
接下来,需要考虑反应床的尺寸和形状。
反应床通常为一根或多根管子,可以是圆柱形、方形或其他形状。
根据反应床的形状和尺寸,可以计算出反应床的体积。
在确定了反应床的尺寸后,需要选择合适的催化剂。
催化剂的选择应考虑反应的速率和选择性。
常见的催化剂有金属催化剂、氧化物催化剂和酸碱催化剂等。
选择催化剂后,需要计算催化剂的质量和体积。
在反应过程中,需要控制反应温度和压力。
反应温度对于反应速率和选择性具有重要影响。
根据反应的热力学数据和催化剂的性质,可以计算出反应的热效应和放热量。
根据反应的放热量和反应床的热传导性能,可以计算出反应床的冷却要求。
在设计固定床反应器时,还需要考虑反应物和产物的流动情况。
根据流动特性可以计算出反应床的压降和流速。
压降对于反应过程有重要影响,它影响着反应物在床体中的停留时间和反应速率。
最后,需要考虑反应物的进料方式和产物的排放方式。
进料和排放方式应选择合适的装置,以保证反应物的均匀分布和产物的高效排放。
在设计固定床反应器时,需要综合考虑以上因素,并进行相应的计算。
通过计算可以确定反应床的尺寸和形状、催化剂的选择、反应温度和压力以及进料和排放方式。
这些计算可以保证固定床反应器的高效运行和最佳性能。
总结起来,设计固定床反应器需要考虑反应物的种类和摩尔比、反应床的尺寸和形状、催化剂的选择、反应温度和压力、反应床的冷却要求、反应物和产物的流动情况以及进料和排放方式等因素。
固定床反应器的操作与控制—固定床反应器工艺计算
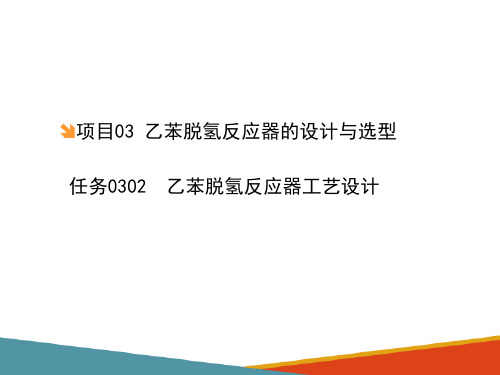
n
dP xidi i 1
2、调和平均直径
1 n xi
dP d i1 i
在固定床和流化床的流体力学计算中,用调和平均直径较为符合实验数据。
三、空隙率(ε) 催化剂床层的空隙体积与催化剂床层总体积之比。
颗粒形状 颗粒装填方式 颗粒的粒度分布
颗粒表面的粗糙度
影响因素 越接近球形
越紧密 越不均匀
越光滑
为降低热点温度,减少轴向温差,工业上从工艺上采取措施,其思路是调 整放热速率或移热速率。
0302-6 固定床反应器的工艺计算
总结固定床反应器的工艺计算内容和计算方法 固定床反应器的工艺计算,一般包括催化剂用量、反应器床层高 度和直径、传热面积及床层压力降的计算等。
固定床反应器的工艺计算,主要有经验法和数学模型法。
务点及其要求
0302-1 固体催化剂基础知识 理解催化剂的作用、基本特征,固体催化剂的组成、性能及其表征 0302-2 气固相反应宏观过程 了解气固相反应特点,理解气固相反应宏观过程,了解气固相反应本征动力学及
宏观动力学的含义 0302-3 固定床反应器内的流体流动及压力降计算 理解气固相流体流动相关的特性参数,了解流体在固定床中流动的特性,会应用
项目03 乙苯脱氢反应器的设计与选型 任务0302 乙苯脱氢反应器工艺设计
任务引入:
中山石化原3万吨/年苯乙烯,采用绝热式固定床反应器,试根据以下条件: 主反应:
C6H5-C2H5→C6H5CH = CH2+H2 (△H=124KJ/mol) 副反应: C6H5-CH2CH3 →C6H6+C2H4 工艺条件:反应温度:550~650 ℃; 常压; 蒸汽 / 乙苯质量比:8:1; 催化 剂:沸石催化剂或EBZ-500 沸石催化剂; 年生产时间为8300小时,乙苯总转化 率达40%,选择性为96%,空速为4830h-1,催化剂堆积密度为1520Kg/m3,生产中 苯乙烯的损失可忽略. 确定(1)催化剂用量;(2)床层的压力降;(3)所需换热面积。
催化重整固定床反应器传递及反应过程的数值模拟

催化重整固定床反应器传递及反应过程的数值模拟催化重整固定床反应器的传递及反应过程的数值模拟可以通过以下步骤进行:
1. 建立反应器的数学模型:根据反应机理和物理性质,建立反应器的数学模型,包括传递过程和反应过程的方程。
传递过程方程通常包括质量传递、能量传递和动量传递方程,反应过程方程通常包括反应速率方程。
2. 离散化反应器:将反应器分为若干小段,分别进行离散化处理。
可以选择均匀离散或非均匀离散的方法,根据实际情况选取最合适的离散化方法。
3. 运用数值方法求解方程:根据离散化后的方程,运用数值方法(如有限差分法、有限体积法、有限元法等)求解方程组,得到各个离散段上的物理量分布。
4. 确定边界条件:根据反应器的实际情况,确定反应器的边界条件。
边界条件通常包括流体的入口温度、压力、物质浓度等。
5. 进行数值模拟和计算:根据离散化后的方程和边界条件,进行数值模拟和计算。
可以采用迭代方法,不断更新每个离散段上的物理量,直至达到收敛条件。
6. 分析和评估模拟结果:根据模拟结果,分析反应器的性能、效率等指标,评估反应器的优化方案和潜在问题。
需要注意的是,在进行数值模拟时,需要考虑反应器内部的催化剂颗粒的分布和反应速率方程的影响。
这可以通过引入催化剂颗粒床层的物理结构参数和反应速率方程来进行模拟。
同时,还需要考虑传递和反应过程之间的相互作用,以及其他因素(如温度、压力)对反应过程的影响。
6气固相催化反应固定床反应器

解: ①求颗粒的平均直径。
0.60 0.25 0.15 3 dS 3.96mm 3.9610 m xi 3.40 4.60 6.90 d i 1
1
②计算修正雷诺数。
dSG 3.96103 6.2 Re m 1906 5 g 1 B 2.3 10 1 0.44
2、径向传质 对于实际反应器,由于存在径向温度分布和径向流速 分布,因而径向必然存在浓度分布和扩散。 同时,流体撞击固体颗粒时,将产生再分散,改变 流体流向,从而造成返混。
Per d p um / Er
Er值应在5~13之间,在不同Re下近于常数。 在多数反应器内,流体处于充分湍流状态,Per=10。
主要固定床催化反应过程
基本化学工业
烃类水蒸气转化 一氧化碳变换 一氧化碳甲烷化 氨合成 二氧化硫氧化 甲醇合成
石油化学工业
催化重整 二氯化烷 丁二烯 苯酐 苯乙烯 异构化 醋酸乙烯酯 顺酐 环已烷 加氢脱烷基
气固相催化反应固定床反应器
[学习目的] 掌握一维拟均相理想流动模型及其应用; 了解流体在固定床内的传递特性、固定床催化 反应器的特点、一维拟均相非理想流模型等其 它模型。 [重点与难点] 流体在固定床内的传递特性; 采用一维拟均相理想流动模型对反应器进行设 计。
工业应用: 石油的连续催化重整、二甲苯异构化、连续法离子交换水处理
优点: A、固体物料可以连续进出反应器,而且可以在 较大范围内独立改变固体和流体的停留时间, 对固体物料性状以中等速度变化的反应过程也 能适用; B、固体和流体的运动均接近活塞流,返混较小, 对固相加工过程,固相转化率比较均匀,对气 相加工过程,则可达到较高的单位体积生产能力。
固定床反应器内的流体流动
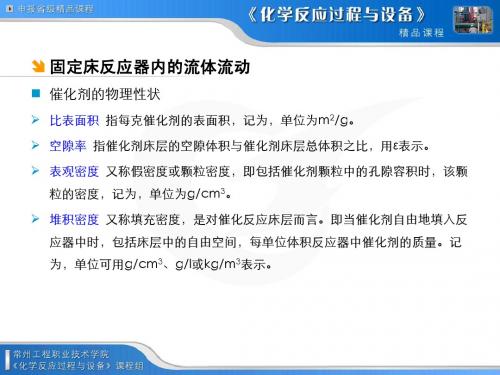
固定床反应器内的流体流动
催化剂的物理性状
比表面积 指每克催化剂的表面积,记为,单位为m2/g。 空隙率 指催化剂床层的空隙体积与催化剂床层总体积之比,用ε表示。 表观密度 又称假密度或颗粒密度,即包括催化剂颗粒中的孔隙容积时,该颗 粒的密度,记为,单位为g/cm3。 堆积密度 又称填充密度,是对催化反应床层而言。即当催化剂自由地填入反 应器中时,包括床层中的自由空间,每单位体积反应器中催化剂的质量。记 为,单位可用g/cm3、g/l或kg/m3表示。
AP VP
=
π d S2 π 3
6 dS
6VP dS = AP
形状系数:用体积相同的球形颗粒的外表面积比上非球形颗粒的外表面积。
AS ϕS ≡ ≤1 AP
三种直径的关系:
ϕ S dV= ϕ S 1.5 d a dS=
平均直径
算术平均直径:
d = ∑ xWi d i
i =1
n
n
调和平均直径:
1 = d
流体通过固定床的压力降
压降产生原因: 摩擦阻力ΔP1:由于流体颗粒表面之间的摩擦产生。 局部阻力ΔP2:流体在孔道内的收缩、扩大及再分布所引起的。
压降的计算 ∆P=∆P1+ ∆P2
2 µ f uOG L0 (1 − ε ) 2 ρ f uOG L0 (1 − ε ) = 150 ⋅ + 1.75 ⋅ 2 3 dS dS ε ε3
Pa
式中混合物的粘度 µ
f
∑ y i µ fi M = 1 ∑ y i M i2
1 2 i
固定床反应器设计计算

固定床反应器设计计算固定床反应器是化工领域中常见的一种反应器类型,特点是固定催化剂床,反应物通过固定床的床层进行反应,反应产物从固定床的出口处得到。
固定床反应器设计是化工生产中的重要环节,涉及反应器的尺寸、催化剂的选择、操作条件的确定等方面。
下面将介绍固定床反应器设计的基本原理和计算方法。
1.催化剂床的选择:催化剂床的选择应根据反应物的性质和反应条件来确定。
常见的固定床催化剂床有球形、多孔材料和填料等,催化剂床的选择应考虑到活性、稳定性和成本等因素。
2.反应器尺寸的确定:反应器尺寸的确定与催化剂床的选择等因素有关。
反应器的长度、直径、催化剂床的高度等参数需要根据反应物的流量、反应速率和传质传热等条件进行计算。
3.操作条件的确定:反应器的操作条件包括温度、压力和流量等参数,这些参数的确定与反应物的性质、反应速率和反应体系等因素有关。
操作条件的设计需要尽可能提高反应速率和产物的选择性。
1.传质和传热计算:传质和传热是固定床反应器中重要的过程,需要考虑到传质和传热的速率以及催化剂床的吸附和扩散等因素。
传质和传热计算可以通过质量传递和能量传递方程进行,根据质量传递和能量传递方程可以计算出反应器中流体的温度和浓度分布。
2.反应动力学计算:反应动力学是固定床反应器设计中的关键环节,可以通过实验和理论模型来确定反应物的反应速率和产物的选择性。
反应物的反应速率可以通过实验测定得到,也可以通过理论模型进行计算。
反应物的选择性可以通过反应速率常数和转化率来计算。
3.负载平衡计算:固定床反应器的负载平衡是指催化剂床的催化剂负载均匀性和催化剂的失活过程。
负载平衡计算需要考虑到催化剂床的催化剂负载情况和催化剂的失活速率。
催化剂的负载均匀性可以通过实验和模拟计算得到,催化剂的失活过程可以根据反应动力学和传质传热过程进行计算。
以上是固定床反应器设计的基本原理和计算方法的介绍,固定床反应器设计是化工生产中的一个重要环节,需要充分考虑到传质和传热、反应动力学和负载平衡等方面的因素来确定反应器的尺寸和操作条件。
- 1、下载文档前请自行甄别文档内容的完整性,平台不提供额外的编辑、内容补充、找答案等附加服务。
- 2、"仅部分预览"的文档,不可在线预览部分如存在完整性等问题,可反馈申请退款(可完整预览的文档不适用该条件!)。
- 3、如文档侵犯您的权益,请联系客服反馈,我们会尽快为您处理(人工客服工作时间:9:00-18:30)。
固定床反应器的数学模型 1、概述 凡是流体通过不动的固体物料所形成的床层而进行反应的装置都称作固定床反应器,其中尤以用气态的反应物料通过由固体催化剂所构成的床层进行反应的气-固相催化反应器占最主要的地位。如炼油工业中的催化重整,异构化,基本化学工业中的氨合成、天然气转化,石油化工中的乙烯氧化制环氧乙烷、乙苯脱氢制苯乙烯等等。此外还有不少非催化的气-固相反应,如水煤气的生产,氮与电石反应生成石灰氮(CaCN2)以及许多矿物的焙烧等,也都采用固定床反应器。固定床反应器之所以成为气固催化反应器的主要形式,是由于具有床内的流体轴向流动可看作为平推流,在完成同样的生产任务时,所需的催化剂用量(或反应器体积)最小;床内流体的停留时间可严格控制,温度分布可适当调节,因而有利于提高化学反应的转化率和选择性;床内催化剂不易磨损,可以在高温高压下操作等优点,但固定床中传热较差,对于热效应大的反应过程,传热与控温问题就成为固定床技术中的难点和关键,为解决这一问题而提出了多种形式的床层结构。
2、固定床反应器的结构形式
固定床反应器类型很多.按换热方式不同可分为:绝热式反应器和换热式反应器。
2.1绝热式反应器 在反应器中的反应区(催化剂层)不与外界换热的称为绝热式反应器。一般来说,反应热效应小;调节进A反应器的物料温度,就可使反应温度不致超出反应允许的温度范围的反应过程等可采用绝热式反应器。绝热式反应器具有结构简单,反应空间利用率高,造价便宜等优点。图1是绝热床反应器的示意图。 如果反应热效应较大,为了减小反应区内轴间温度分布不均,可将绝热反应器改成多段绝热式反应器,在各段之间进行加热或冷却,它可使各段反应区接近适宜温度。图2是多段绝热床反应器的示意图。 总之,不论是吸热或放热的反应,绝热床的应用相当广泛。特别对大型的,高温的或高压的反应器,希望结构简单,同样大小的装置内能容纳尽可能多的催化剂以增加生产能力(少加换热空间),而绝热床正好能符合这种要求。不过绝热床的温度变化总是比较大的,而温度对反应结果的影响也是举足轻重的,因此如何取舍,要综合分析并根据实际情况来决定。此外还应注意到绝热床的高/径比 物料气 产物 催化剂
不宜过大,床层填充务必均匀,并注意气流的预分布,以保证气流在床层内的均匀分布。
图1 绝热式反应器 图2 多段绝热床反应器的示意图 2.2换热式反应器
为了改善热效应大的反应过程反应区内的温度条件,可在反应区内进行热交换,这种反应器称为换热式反应器。换热式反应器又有自热式和外热式两种。自热式是以原料气体来加热或冷却反应区(图3),外热式则是用载热体加热或冷却反应区换热式反应器以列管式为多,通常在管内放催化剂,管外走热载体(图4)。列管的管径一般取25~50mm为宜,催化剂的粒径应小于管径的8倍,以防管壁处出现沟流。
图3换热式反应器(乙炔法合成氯乙烯反应器) 图4 自热式反应器示意图 3、固定床反应器的数学模型
反应器是整个化工生产过程的核心装置,其中固定床反应器是应用较为广泛的反应设备,建立能准确描述其特性的数学模型,不但可以给反应器设计和最优化操作提供理论依据,更减少了工作量。实现其优化操作,具有重要意义。 描述固定床反应器的数学模型按其传递过程的不同可分为拟均相模型和非均相模型两大类。拟均相模型不考虑流体与催化剂间的传热、传质阻力,把流体和催化剂看成均相物系,催化剂粒子和流体之间没有温度和浓度上的差别。拟均相模型又可分为拟均相一维模型和拟均相二维模型(表1)。非均相模型则考虑了流体与催化剂外表面间的温度梯度和浓度梯度,须对流体和催化剂分别列出物料衡算式。 表1 固定床反应器的数学模型
蒸汽 原料 调节阀
催化剂 补充水
产物 TC Tf Tf T0 逆流 并流 T0 拟均相模型 非均相模型 一维 基本模型 (A-Ⅰ) +相间梯度 (B-Ⅰ) +轴向混合 (A-Ⅱ) +颗粒内梯度(B-Ⅱ) 二维 +径向混合 (A-Ⅲ) +径向梯度 (B-Ⅲ)
3.1拟均相基本模型(A-I)(拟均相一维活塞流模型) 将实际非均相反应系统简化为均相系统处理。适用于:(1)化学反应为控制步骤;(2)流固相间或固相内部存在传递阻力; “拟均相”是只指将实际上为非均相的反应系统简化为均相系统处理,即认为流体相和固体相之间不存在浓度差和温度差。 “一维”的含义是只在流动方向上存在浓度梯度和温度梯度,而垂直于流动方向的同一截面上各点的浓度和温度均相等。 “活塞流”的含义则是在流动方向上不存在任何形式的返混。 物料衡算方程:
当为等摩尔反应时,
能量衡算方程: 管内:
管外: 流动阻力方程:
ddddAAABAABANNNrVNrV
ddddABAABAuAc
rAzucrz
d4dgpRBActTUucHrTTzd
d4dcccpcctTU
ucTTzd
2ddgkpup
fzd 边界条件: 对于绝热反应器:
对反应物流和载热体并流的列管式反应器:
求解方法用龙格库塔法。 对反应物流和载热体逆流的列管式反应器:
求解方式:打靶法。 3.2拟均相轴向分散模型(A-Ⅱ) 反应物流通过固体颗粒床层是不断分流和汇合,并作绕流流动,造成一定程度的轴向混合(返混),用分散模型描述。 管内物料衡算方程:
管内能量衡算方程:: 管外EB和流动阻力方程同拟均相基本模型。 边界条件:
与拟均相基本模型相比,引入轴向混合项的作用主要在于: (1)降低转化率; (2)当轴向混合足够大时,反应器可能存在多重定态。 对于反应速率随床层轴向距离单调减小的情形,如果进口条件满足下面两式,可忽略轴向混合影响的判据:
00000, , , , AAcc
zccTTppzLTT处
处
0000, , , AAzccTTpp处00000, , , , AAcczccTTTTpp处
22ddddAAeaBAcuc
Drzz
22dd4ddeagpRBActTTU
ucHrTTzzd
000d0, dd d dd, 0ddAAAea
gpea
A
czuccDzTucTTzppcTzLzz处
处 3.3拟均相二维模型(A-Ⅲ) 对于管径较粗或反应热较大,造成径向位置处反应速率和反应物浓度的差别, 需采用二维模型,同时考虑轴向及径向分布。 在列管反应器的某反应管中,以反应管轴线为中心线,取以半径为r,径向厚度为dr,轴向高度为dz的环状微元体,如图5所示
图5 拟均相二维模型 对微元体作组分A的物料衡算: 气相主体流动自z面进入微元体的组分A的量为:
气相主体流动自(z+dz)面流出微元体的组分A的量为:
从r面扩散进入微元体的组分A的量:
maAPBAPeucdr0
0
haPgWPBAPecuTTdrH0
0
Ardruc2
dzzc
crdruAA2
rcrdzDAer2从r+dr面扩散出微元体的组分A的量: 组分A在微元体内的反应量: 在定态条件下: 进入微元体的量-出微元体的量=微元体反应的量
3.4考虑颗粒界面梯度的活塞流非均相模型(B-I) 对于热效应很大而且速率极快的反应,可能需要考虑流体相和固体相之间的浓度差和温度差。 气相衡算方程:
固相衡算方程: 边界条件:
)()(222drrcrcdzDdrrAAerABrrdrdz2
HrrTrrTzTcurrcrrcDzcuABerpgABAAerA
1
12222
能量守恒方程:
物料衡算方程:
000,000rTr
T
rczrTTccrzsAAA为任意值处,,
为任意值处,,边界条件:
ddd4dAgAAsgpsctc
ukacczTUuchaTTTTzd
,,gAAsAAssBsAAssBkaccrcThaTTrcTH
000, , AAzccTT处