年产25万吨电铜的铜电解精炼车间工艺设计(已处理)

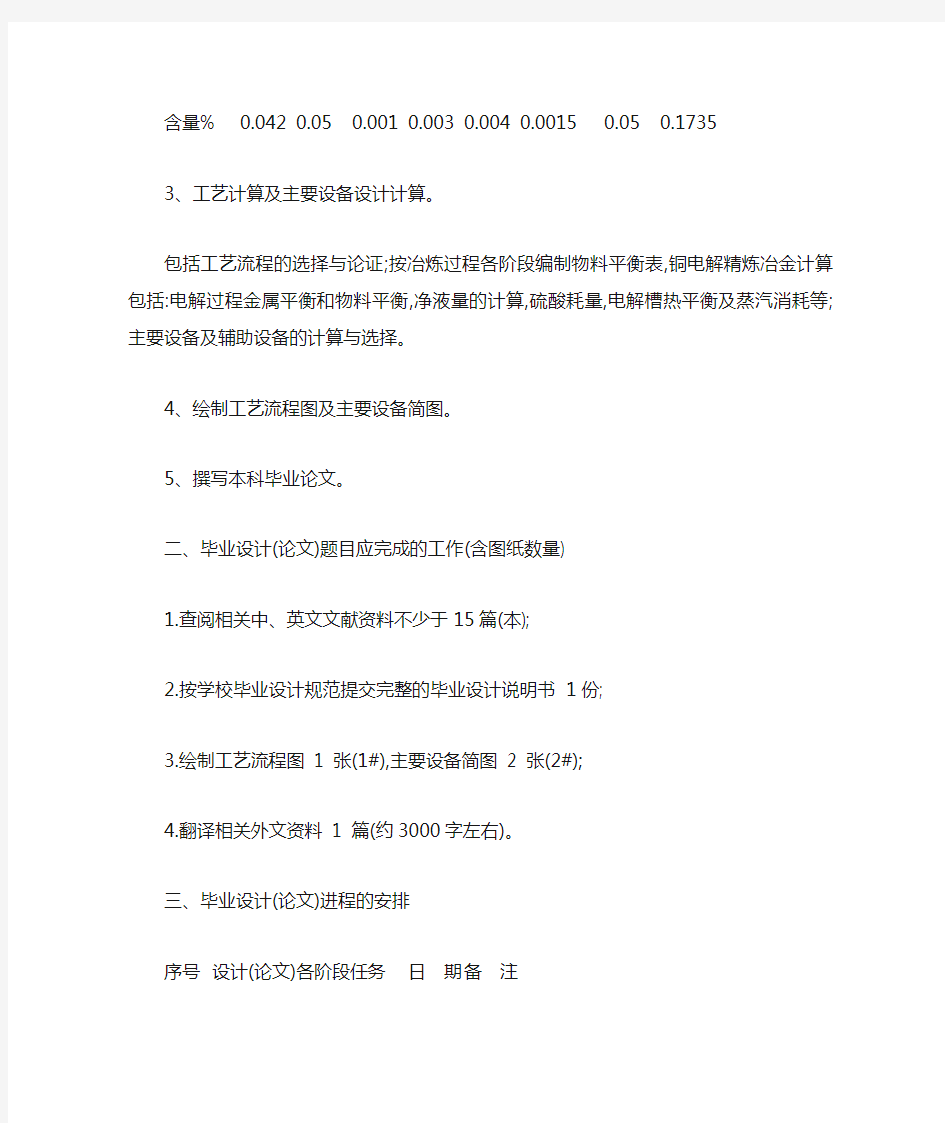
年产25万吨电铜的铜电解精炼车间工艺设计
西安建筑科技大学华清学院
毕业设计(论文)任务书
题目: 25万吨/年电铜的铜电解精炼车间工艺设计
院(系): 冶金工程学院
专业: 冶金工程
学生姓名:学号:指导教师:一、毕业设计(论文)的主要内容(含主要技术参数)
1、查阅有关铜电解精炼技术等方面的文献,写出文献综述;说明设计的任务和目的,铜在国民经济建设及有色金属工业的发展概况。
2、根据给定铜阳极成份,设计年产25万吨电铜的铜电解精炼车间,年工作日360天。铜阳极成份如下表:
元素Cu Au Ag As Sb Ni Bi Pb
含量% 99.3 0.062 0.08 0.01 0.011 0.178 0.002 0.032
元素Se Te Fe Zn Sn S O 其他
含量% 0.042 0.05 0.001 0.003 0.004 0.0015 0.05 0.1735
3、工艺计算及主要设备设计计算。
包括工艺流程的选择与论证;按冶炼过程各阶段编制物料平衡表,铜电解精炼冶金计算包括:电解过程金属平衡和物料平衡,净液量的计算,硫酸耗量,电解槽热平衡及蒸汽消耗等;主要设备及辅助设备的计算与选择。
4、绘制工艺流程图及主要设备简图。
5、撰写本科毕业论文。
二、毕业设计(论文)题目应完成的工作(含图纸数量)
1.查阅相关中、英文文献资料不少于15篇(本);
2.按学校毕业设计规范提交完整的毕业设计说明书 1份;
3.绘制工艺流程图 1 张(1#),主要设备简图 2 张(2#);
4.翻译相关外文资料 1 篇(约3000字左右)。
三、毕业设计(论文)进程的安排
序号设计(论文)各阶段任务日期备注
1 毕业实习 3.1~3.14
2 查阅相关文献资料,完成文献综述 3.15~3.28
3 铜电解精炼工艺流程的确定3.29~4.4
4 详细工艺计算及主要设备设计计算 4.5~5.19
5 撰写设计说明书,绘制相应图纸 5.20~5.30
6 检查、完善设计说明书及图纸,准备答辩 5.31~6.11四、主要参考资料及文献阅读任务(含外文阅读翻译任务)
1.阅读有铜电解精炼方面的文献(其中英文文献不少于3篇);
2.主要参考资料:
朱祖泽,贺家齐.现代铜冶金学,北京:科学出版社,2003,1.
罗孝玲,Jules.中国铜工业存在的问题及对策探讨.技术经济,2002,12:7-8.
于润沧.再议我国铜工业发展的若干战略问题.铜工业工程,2001,17:7-10
曹异生.世界铜工业进展及前景展望. 世界有色金属,1997,4:17-21.
黄海根,余斌,张绍才.铜工业的近来走势与发展对策探讨.矿产保护与利用,2004,42:8-12.
五、审核批准意见教研室主任签(章)
25万吨/年电铜的铜电解精炼车间工艺设计
专业:冶金工程
学生:朱浪涛
指导教师:张秋利
设计总说明
铜电解精炼过程,主要是在直流电的作用下,铜在阳极上失去电子后以铜离子的形态溶解,而铜离子在阴极上得到电子以金属铜的形态析出的过程。目前世界铜冶炼厂使用的主要熔炼工艺为闪速熔炼和熔池熔炼,其中熔池熔炼包括诺兰达连续炼铜法、艾萨熔炼法、瓦纽科夫法。
本设计为年产25万吨电铜的铜电解精炼车间,铜的电解精炼是以火法精炼产出的精铜为阳极,以电解产出的薄铜(始极片)作阴极,以硫酸铜和硫酸的水溶液作电解液。在直流电的作用下,阳极铜进行电化学溶解,纯铜在阴极中沉积,杂质则进入阳极泥和电解液中,从而实现了铜与杂质的分离,确定了铜电解过程中的主要技术经济指标。本设计还进行了物料平衡、热平衡、水平衡、主要设备及辅助设备的计算与选择。进一步提高铜电解精炼的技术水平,从而达到对铜电解精炼技术有更深刻了解的目的。
关键字:铜;电解精炼;平衡计算;设计
The Process Design of Electrolytic Refining Workshop with Annual Output 250,000 Tons Electrolytic Copper
Specialty:Metallurgical engineering
Name:Zhu langtao
Tutor:Zhang qiuli
Design Description
The copper electrolysis fining process is mainly under the direct current function,copper loses the electron after the anode by cupric ion shape dissolution,but the cupric ion obtains the electron on the negative pole by the metal copper shape separation process.At present the world copper refinery use main smelting craft to dodge the fast smelting and the molten bath smelts,the molten bath smelts including the Landa continual copper smelting,Isa smelts,Niu Shinao smelts.
Originally designed to produce per 250,000 the first electrolytic copper refine the work shop,refining the precise copper produced electrolytically and concisely as the positive pole with fire law of copper,take copper sulfic acid and aqueous solution of the sulfuric acid as the electrolytic liquid very much with the electrolytic thin copper beginning that produces.Under the funcition of the direct current,positive pole copper carries on electrochemistry to dissolve,pure copper is deposited in the negative pole,the impurity is entered in positive pole mud and electrolytic liquid,thus realized the
separation of the copper and impurity,have confirmed the main technical and economic index in the electrolytic course of copper.Have originally designed and also carried on supplies equilibrating,calculation and choice of the thermal balance,horizontal weighing apparatus,capital equipment and auxiliary equipment. Further improve the standard of the electrolytic refining and reached for the refinement of the electrolytic technology is a profound understanding of purpose.
Keywords:Copper;Electro refining;balanced computing;design
目录
1 文献综述 6
1.1铜的简介 6
1.2铜生产技术7
1.2.1传统炼铜技术7
1.2.2现代炼铜技术7
1.2.3冰铜吹炼7
1.2.4铜的精炼7
1.2.5湿法炼铜8
1.3铜的电解精炼9
1.3.1铜电解精炼现状 9
1.3.2铜电解精炼的基本原理9
1.3.3铜电解精炼中杂质的主要行为11
2 设计原则及要求 14
2.1设计原则14
2.2设计要求14
2.3主要设备及辅助设备的计算与选择 14 2.4冶金计算15
2.5制图内容和要求15
3 主要设备的计算与选择16
3.1电解槽16
3.1.1电解槽的材质16
3.1.2电解槽的构造16
3.1.3电解槽衬里的材质17
3.1.4电解槽的安装17
3.1.5阳极18
3.1.6阴极19
3.1.7种板19
3.2电解槽各有关设备选择和计算20
3.3整流器的选材及计算22
3.4车间运输设备的选择与计算22
3.5车间及跨的选择23
3.6极板作业机组23
4 主要技术经济指标的论证与选择 25
4.1主要技术条件25
4.1.1电解液的组成25
4.1.2添加剂26
4.1.3电解液温度26
4.1.4电解液循环27
4.1.5电流密度27
4.1.6同极中心距27
4.1.7阳极寿命和阴极周期27
4.2主要经济指标28
4.2.1电流效率28
4.2.2残极率29
4.2.3铜电解回收率29
4.2.4槽电压29
4.2.5直流电能单位消耗30
4.2.6硫酸单位消耗30
4.2.7蒸汽单位消耗30
5 冶金计算31
5.1铜电解精炼物料平衡计算31
5.1.1阳极泥率和阳极泥成分计算31
5.1.2电解精炼物料计算32
5.2铜电解精炼热平衡计算34
5.2.1计算电解槽液面水蒸发热损失35
5.2.2电解槽液面的辐射与对流的热损失35 5.2.3电解槽壁的辐射与对流热损失36
5.2.4管道内溶液热损失36
5.2.5电流通过电解液所产生的热量36 5.2.6全车间需要补充热量37
5.3电解液净化及硫酸盐生产冶金计算 37 5.3.1净液量计算37
5.3.2硫酸铜的物料平衡计算38
5.3.3脱铜电解物料平衡计算40
5.3.4粗硫酸镍生产计算41
5.4电解循环系统设备及管道计算42
5.4.1循环贮槽材质及容积确定42
5.4.2高位槽43
5.4.3阳极泥贮槽43
5.4.4电解液循环泵43
5.4.5电解液加热器43
6 厂址选择46
6.1厂址的选择依据46
6.2厂址选择47
7 环保与安全48
7.1环境保护48
7.2安全生产48
致谢50
参考文献51
附:专题52
1 文献综述
1.1铜的简介
铜是人类最早发现和应用的金属之一,据考证,西亚地区是世界上最早应用铜并掌握炼铜技术的地区。在靠近西亚的土耳其南部的查塔尔萤克发现的含有铜粒的炉渣距今已有8000~9000年的历史。我国是世界四大文明古国之一,大批出土文物表明,我国在夏代就进入了青铜时期,在甘肃马家窑文化遗址发现的青铜刀,距今已达5000年,湖北大冶铜绿山矿附近的古矿冶遗址距今已达2500~2700年。该矿址已出土8座竖炉,炉周边堆放着大量炼铜炉渣和金属铜。19世纪后期转炉的出现引发了炼铜工艺大改革。用转炉吹炼铜硫,简化了流程,缩短了周期。1865年欧洲出现了电解精炼,从而使铜的纯度大大提高。上世纪20年代以前,火法熔炼大多采用鼓风炉,到70年代则以反射炉熔炼为主。自上世纪60年代以来,以闪速熔炼为代表的一批强化冶炼新工艺,逐渐取代了反射炉熔炼。我国虽然很早就生产和应用铜,但直到1949年新中国建立前,我国炼铜工业一直处于落后地位,全国仅有几个小的再生铜冶炼厂。新中国成立后我国整个工业水平迅速提高,从上世纪50年代后期开始,我国逐渐建立起几座现代化炼铜厂,近20年来,几乎世界上的各种先进炼铜工艺都在我国得到应用,近年来我国的铜产量已跃居世界前列。
现行炼铜方法分为火法和湿法两大类。火法炼铜的简要流程为“熔炼??吹炼??火法精炼??电解精炼”;湿法炼铜的简要流程为“焙烧??侵出??电积”。近年来,尽管湿法炼铜,尤其是细菌侵出炼铜方面发展很快,但目前世界上所产的铜仍有80%以上来自火法工艺,在我国更是高达95%以上。
铜电解精炼得到的产品称为阴极铜。阴极铜中含有一定量的杂质时,铜的电导性、可塑性变差,影响铜加工产品的使用性能,因此工业上要求阴极铜中的杂质含量要低。
随着铜矿的逐步开发,原料品味逐渐下降,杂质的含量不断升高(尤其是砷锑),但在铜冶炼过程中,火法冶金不能有效除去As、Sb、Bi等杂质,产出阳极铜的杂质含量往往比较高。这些杂质必须经过电解精炼才能有效除去[1]。
由于铜的优良传导性,机械强度大,延展性好,鲜艳的金属光泽等,使铜一度成为有色金属之首。
1.2铜生产技术
1.2.1传统炼铜技术
中世纪末,德国和英国发明了从硫化矿中生产铜,采用小型鼓风炉熔炼。约在1700年英国创立了反射炉熔炼,进入20世纪,相继出现了大型鼓风炉和反射炉炼铜,随后又出现了电炉炼铜。
(1)鼓风炉熔炼。鼓风炉适宜处理块状物料,因其生产效率低和环境污染等问题,现已逐步被淘汰。
(2)反射炉熔炼。20世纪初随着粉状铜精炼大量出现,反射炉逐渐成为主要炼铜手段。后来,由于石油危机和环境压力,污染严重和高能耗的反射炉逐渐被一些现代炼铜工艺所取代。少数反射炉经富氧和炉子结构现代化改造保留了下来。
(3)电炉熔炼。在电价便宜或精矿含高熔点物料时适宜电炉熔炼,首先在北欧国家应用。
1.2.2现代炼铜技术
为节能和减轻环境污染,半个世纪来相继研制和创立了许多新的炼铜工艺,统称为现代炼铜技术,其共同特点是:
为节能和减轻污染,将焙烧和熔炼作业合并到一个反应器中完成;
不断提高燃料空气中氧量,甚至采用纯氧;
余热利用以及采用预热鼓风;
不用或仅用少量辅助燃料。
这些措施导致:生产效率高;能耗低;烟气SO2浓度高。普遍缺点是:渣含铜量高,需要进一步处理。
闪速熔炼的主要方法有:诺兰达法;三菱法;瓦钮可夫法;艾萨法[2]。
1.2.3冰铜吹炼
传统的冰铜吹炼设备是卧式转炉,现在全世界有上1000台这种转炉在操作。比利时霍波肯公司开发了一种虹吸式转炉,由于炉子特殊结构和作业,是转炉烟气SO2浓度达到12%,环境污染大大减轻。上述提到的许多现代化火法炼铜工艺本身也包括冰铜吹炼过程,而且许多还是连续吹炼,如诺兰达法、三菱法等。新近开发的闪速熔炼-闪速吹炼,已在其他铜厂应用。
1.2.4铜的精炼
传统的铜精炼大致为三个过程:火法精炼;点解;阴极重熔和铸锭。
(1)间歇式火法精炼。主要设备有发射炉、阳极转炉和阳极鼓风炉(用于固体料),还原剂有各种碳质还原剂、天然气、石油气以及氨等。
(2)连续火法精炼
1)HCCR法。由Humboldt公司开发。第一室加入液态或固态粗铜;第二室用氧气氧化;第三室用甲烷或丙烷还原。
2)Contimelt法。由北德精炼公司和霍波肯公司联合开发。由鼓风炉和圆筒炉用溜槽相连组成。鼓风炉加料、融化和氧化;圆筒炉还原。
阳极浇铸:传统的圆盘浇铸还在许多中小铜厂应用。
点解:世界80%以上精铜由电解法产出。
3电极制备和处理的全机械化,在奥托昆普公司,霍波肯公司等广泛应用。
4)巨型电解槽应用。1972年首先在小名兵精炼厂应用,巨型槽有效使用容积式普通槽20倍,阴、阳极周期相同,为10天,极距10毫米,电解液与电极表面呈不平行流动。
5)艾萨电解法。由艾特公司开发,首先汤斯韦尔铜精炼厂应用。工艺特点是采用不锈钢阴极,并由锌生产中移植机械化阴极剥离技术,电流密度和电流效率都比一般铜电解高,并节省劳力,世界已有30几家铜精炼厂应用[3]。
1.2.5湿法炼铜
目前,世界湿法炼铜约占铜的大部分,主要产品是电解铜或置换铜。
(1)浸出方法主要有:
1)就地浸出,处理零星矿或残矿;
2)块矿堆浸出或堆摊浸出;
3)细矿槽浸出或渗滤浸出;
4)加压浸出。
采用的浸出剂有“三酸”、三价铁盐、氧-铵溶液、CuCl2、二价铬酸盐等。细菌浸出主要有铁氧杆菌等,也获得了广泛应用。
(2)溶剂萃取。这是从稀铜浸出液中富集铜最普遍应用的方法。当前有两
种最重要的铜萃剂系列:德国汉高公司的LIX系列和美国阿希兰德公司的Kelex 系列。新近开发的新萃取剂增加了溶剂萃取的重要性。
(3)固体离子交换。虽不像溶剂萃取那么广泛应用,但在溶液净化、废水处理等方面亦有应用。
(4)置换。加铁从铜溶液中置换铜是很古老的方法,一般铜回收率是60%~90%,置换铜多用火法精炼,少数较纯置换铜用于生产硫酸铜。
(5)电积。电积与容积萃取配套,是当今湿法炼铜应用最广泛的工艺。电积电耗一般2000~2600kWh/tCu,通常采用铅-锑不溶阳极。智利丘基卡马塔用Chilex阳极;新进出现了钛阳极,表面有一层铂族涂层。钛有抗腐蚀、节能和阳极不会被铜污染等优点[4]。
1.3铜的电解精炼
1.3.1铜电解精炼现状
铜的火法精炼一般能产出含铜99.0%~99.8%的粗铜产品,但仍然不能满足电气工业对铜的性质的要求,其他工业也需要使用精铜。因此,现代几乎所有的粗铜都经过电解精炼,以除去火法精炼难以出去的杂质。铜的电解精炼,是将火法精炼的铜浇铸成阳极板,用纯铜薄片作为阴极片。相间地装入电解槽中,用硫酸铜和硫酸的水溶液作电解液,在直流电的作用下,阳极上的铜和电位较负的贱金属溶解进入溶液,而贵金属和某些金属(如硒、碲)不溶,成为阳极泥沉于电解槽底。溶液中的铜在阴极上优先析出,而其他电位较负的贱金属不能在阴极上析出,留于电解液中,待电解液定期净化时除去。这样,阴极上析出的金属铜纯度很高,称为阴极铜或电解铜,简称电铜。
含有贵金属和硒、碲等稀有金属的阳极泥,作为铜电解的一种副产品另行
处理,以便从中回收金、银、硒等元素。在电解液中逐渐积累的贱金属杂质,当其达到一定的浓度后,会妨碍电解过程的正常进行。例如,曾加电解液的电阻和密度,使阳极泥沉降速度减慢,甚至在阴极上与铜一起放电,影响阴极铜的质量,因此必须定期定量地抽出净化,并相应地向电解液中补充新水和硫酸。抽出的电解液在净化过程中,常将其中的铜、镍等有价元素以硫酸盐的形态产出,硫酸则返回电解系统重复使用。
在电解车间,通常设有几百个甚至几千个电解槽,每一个直流电源串联其中的若干个电解槽成为一个系统。所有的电解槽中的电解液必须不断循环,使电解槽内的电解液成分均匀。在电解液循环系统中,通常设有加热装置,以将电解液加热至一定的温度。近十年来,我国铜电解精炼操作技术有很大改进,操作电流密度大幅度提高[5],使生产得到强化。进行了周期反向电流电解试验,操作电流密度达到400A/m2。
1.3.2铜电解精炼的基本原理
传统的铜电解精炼是采用纯净的电解铜薄片作阴极,阳极铜板含有少量杂质(一般为0.3%~1.5%)。电解液主要为含有游离硫酸的硫酸铜溶液。
由于电离的缘故,电解液中的各组分按下列反应生成离子: CuSO4Cu2++SO42-
H2SO42H++SO42-
H2OH++OH-
在未通电时,上述反应处于动态平衡。但在直流电通过电极和溶液的情况下,各种离子作定向运动,在阳极上可能发生下列反应:
种板阳极初始片阳极
初始片残极阳极泥电解液电解液电铜阳极泥残极
送电解返火法送阳极送阳极返火法
精炼精炼泥处理泥处理精炼
再生铜粗硫酸镍结晶硫酸铜粗硫酸
返火法精炼生产精制硫酸镍返回电解精炼
图1.1 铜电解精炼一般工艺流程图
式中M′只指Fe、Ni、Pb、As、SB等比Cu更负电性的金属。因其浓度很低,其电极电位将进一步降低,从而它们将优先进入电解液。由于阳极主要成分是铜,所以阳极的主要反应将是铜溶解形成Cu2+的反应。至于H2O和SO42-失去电子的氧化反应,由于其电极电位比铜正的多,故在阳极上是不可能进行的。另外,如Ag、Au、Pt等电位更正贵金属、铂族金属和稀有金属,更是不能溶解,而落到电解槽底部。
此外,杨的析出还具有相当大的超电位。因此,在铜电解精炼过程中不可能发生水放电,只有当铜离子的浓度达到极高或电解槽内阳极严重钝化,使精炼电压升高至1.7V以上时才可能有氧在阳极上放出。至于SO42-离子的放电反应,因为其电位更正,故在铜电解精炼过程中式不能进行的。
在阴极上可能发生下列反应:
氢的标准电位较铜负,且在铜阳极上的超电压使使氢的电极电位更负,所以在正常的电解精炼条件下,阴极不会析出氢,而只有铜的析出。同样,标准电位比铜低而浓度又小的负电性金属M′,不会在阴极析出。
电解过程中还形成一价铜离子Cu+并建立下列平衡:
表1-1 上式在不同温度下的平衡数据
温度(℃) 10160 50 40 30 21
KCu 1.6×103 4.2×104 1.0×105 2.5×1057.0×105
2.0×106
综上所述,铜电解精炼过程,主要是在直流电的作用下,铜在阳极上失去电子后以Cu2+的形态溶解,而Cu2+在阴极上得到电子以金属铜的形态析出的过程。除此之外,还不可避免地有Cu2+的产生,并引起一系列的副反应,使电解过程复杂化。
根据以上情况,可以认为铜电解精炼时较有利的工作条件是:电解液中含有足够高的游离硫酸和二价铜离子;电解液的温度不宜过高;采用足够高的电流密度;尽量减少电解液与空气的接触[6]。
1.3.3铜电解精炼中杂质的主要行为
在电解精炼过程中,阳极铜中的各种杂质的行为,按其电位序可分为四类:
(1)比铜更负电性的元素。如:锡、锌、铁和镍,大部分进入电解液,并在电解液中积累,需定期净化除去;当阳极溶解时,以金属形态存在的该类杂质均电化溶解,并以二价离子形态进入溶液,其中铅、锡由于产生难溶的盐类或氧化物,大部分转入阳极泥,其余则在电解液中积累。共同特点是:消耗溶液中的硫酸,增加溶液的电阻。
锌、铁和锡都是在火法精炼中容易除去的杂质,在阳极中含量很低。锌在阳极溶解时,全部成为硫酸锌进入电解液;铁以Fe2O3形式存在于铜晶体间的缝隙中,阳极溶解时绝大部分以二价形式进入电解液;锡在阳极溶解时最终水解为
溶解度不大的碱式盐,沉入槽底成为阳极泥。铅主要生成PbSO4进入阳极泥。
镍是火法精炼时难以除去的杂质。为了提高冶炼流程中镍的综合利用率,火法精炼时,力求将镍最大限度地以金属镍的形式保存在阳极泥中,即调铜保镍。实践表明,镍在阳极上的溶解与阳极含氧量有很大的关系。阳极含氧量低,镍绝大部分进入溶液;阳极含氧量高,则镍很大部分进入阳极泥。
(2)比铜更正电性的元素。如:金、银、铂和钯,一般以金属状态进入阳极泥;银、金和铂族元素比铜具有较大的正电性,但他们通常只以很小的浓度与铜形成固溶体,若浓度较高,则形成过饱和溶体。对阳极泥进行的物相分析结果发现,阳极泥中绝大部分的银以硫酸银形式存在,少量以氯化银存在,以金属银形式存在的更少,而且氯化银相与硫酸银相混合;而金几乎100%地进入阳极泥,阴极铜含有极微量的金,是阳极泥的机械粘附所引起的。
(3)电位接近于铜的元素。如:砷、锑和铋,电解时呈三价离子形式进入电解液,是电解过程中最有害的杂质。这类杂质应尽量在火法精炼时除去,其在电解液中的含量也应适当控制。
砷、锑、铋的电位与铜比较接近,在正常的电解过程中,一般很难在阴极析出。阳极溶解时,这些元素成为离子进入溶液,大部分水解成为固态氧化物,一部分则在电解液中积累。
为了避免阳极铜中的杂质砷、锑、铋进入阴极,保证电解过程能产出合格的阴极铜特别是高纯阴极铜,应采取如下措施:
1粗铜在火法精炼时,应尽可能地将这些杂质除去;
2控制电解液中适当的酸度和铜离子浓度,防止杂质的水解和抑制杂质离子的放电。
3维持电解液有足够高的温度(60~650C)以及适当的循环速度和循环方式。4电流密度不能过高。目前采用的常规电解方法,电解密度以不能超过300A/m2为宜。
5加强电解液的净化,保证电解液中较低的砷、锑、铋浓度。一般维持电解液中砷为1~5g/L,最高不超过13g/L;锑为0.2~0.5g/L,不超过0.6g/L;铋一般为0.01~0.3g/L,不超过0.5g/L。
6加强电解液的过滤。实践证明,保证电解液中漂浮阳极泥含量低于20~30mg/L,有利于高纯阴极铜的正常生产。
7向电解液中添加配比适当的添加剂,保证阴极铜表面光滑、致密,减少漂浮阳极泥或电解液对阴极铜的污染。 (4)其他杂质
阳极铜中的氧通常与硫、硒、碲、硅等元素形成化合物存在,这些化合物大部分是难溶于电解液的,在电解过程中它们主要进入阳极泥。前已述及,NiO的行为对电解过程有很大的影响。随阳极铜中氧含量增加,镍进入阳极泥的分配率随之增大的同时,也常在阳极表面形成不易脱落的化合物薄膜,引起阳极电位升高,槽电压增大,严重时甚至造成阳极钝化。因此,粗铜火法精炼时,应该把阳极铜中的含氧量控制在低限内,以消除上述不利影响,保证电解生产地正常进行。
阳极铜中的硫大多以CuS的形态存在。国内外现行的火法精炼技术都能使阳极铜中的硫含量低至0.01%以下,因此对电解过程的影响很小。
阳极铜中的硫大多以Cu2Se颗粒夹杂于Cu2O之间。在电解过程中,硒化物、碲化物并不溶解,而在阳极上形成程度不同的松散外壳或从阳极表面脱落,沉入电解槽底,成为阳极泥。
通常,硅在阳极铜中的含量是很小的,在铜电解精炼过程中,存在的硅量
也并不多,但它也有可能影响阳极钝化。电解过程中,一部分富铜的硅酸盐包裹物溶解形成硅胶,但大部分仍被带入阳极铜中。而阳极铜中的硅酸盐不溶解,从阳极撒谎能够脱落后进入阳极泥[7]。
2 设计原则及要求
2.1设计原则
1)设计过程认真执行国家工程建设中现行的有关方针、政策、法律、标准及规定。
2)重视环境保护,充分考虑采用减少“三废”污染的工艺和设备,做到环保工程和建设工程“三同时”,确保各类排放物达到国家规定的排放标准,实现清洁成产。
3)设备选择立足国内,关键技术和设备可考虑国外引进,尽量减少工程投资。
4)电解铜产品质量和规格品种适应国际和国内市场要求。
5)采用各种节能设备和材料,寻求合理的节能工艺,同时也要考虑降低投资和生产成本。
6)在选择设计方案时要注意提高系统控制水平,实现生产过程、人力资源和设备资源优化控制[8]。
2.2设计要求
本次设计依据为西安建筑科技大学下达的《毕业设计任务书》,通过查阅有关文献资料,在毕业实习的基础上进行的电解铜车间初步设计。设计重要内容包括:
1)查阅有关铜电解精炼技术方面的文献,写出文献综述;说明设计的任务
和目的,铜在国民经济建设及有色金属工业的发展概况。
2)根据给定铜阳极成分,设计年产8万吨电铜的铜电解精炼车间,年工作日360天。
3)工艺计算及主要设备计算。
4)绘制工艺流程图1张及主要设备简图。
5)撰写本科毕业论文。
通过本次毕业设计,旨在检验我们在本科阶段的学习效果,以及我们对所学的专业知识灵活运用的能力。使我们的专业知识不仅仅停留在书本上,走出了理论和实践相结合的重要的一步。
2.3主要设备及辅助设备的计算与选择
根据工艺流程各个主要工程,合理地选择主要冶炼设备和确定个数、容量、对其主要尺寸加以计算,计算中采用的数据应当有根据地引用文献和生产实践资料。
辅助设备应进行选择和计算,确定其规格和数量。
运输设备的选择和计算时,应说明冶炼工艺流程各主要工序的联系,物料运输方式,运输及提升设备型号选择依据及采用的运输方法并进行计算。
铜电解精炼主要设备和辅助设备计算包括:电解槽的计算(普通槽和种板槽)。整流器及导电材料的计算和选择,电解液循环系统设备及管道计算,车间运输设备计算与选择,其他设备及设施。
2.4冶金计算
(1)详细计算过程中所需的物料及产物,中间产物的产量、成分。
在计算中所采用的数据,都应根据参考文献或工厂实践,经过生产实践验
铜电解精炼
使用电化学噪声测量检测坏铜电解精炼条件 B.VEILLEUX-1,https://www.360docs.net/doc/c414938932.html,FRONT-1,E.GHALI-1and P.R.ROBERGE-2 1-采矿,冶金和材料工程,Ste-Foy,加拿大魁北克拉瓦尔大学 2-化学和化学工程系,加拿大皇家军事学院,加拿大安大略省的金斯顿 收到2001年7月1日,接受2002年6月12日修订的形式 关键词:添加剂、氯化铜电解精炼、电化学噪声测量(EN)、频域变换、明胶、胶水、峰度、偏态统计分析、硫脲 摘要:使用添加剂硫脲、明胶和氯化铜电解精炼过程中可促进流利的沉淀。然而,当他们的比率或浓度是不够时,添加剂也可以促进结疤的形成。进行一个的初步调查确定电化学噪声(EN)测量是否可以用来监视和检测效率低下的铜电解精炼条件不当比率或浓度添加剂。电化学噪声(EN)测量在实验室模拟工业条件下进行。进行恒电流实验使用了含有不同浓度的添加剂的合成电解质。A316LL阴极和工业铜阳极也被应用了。对三种不同的数据采集频率的影响也进行了调查。使用统计分析和频域转换来研究电化学噪声(EN)信号作为潜在的时间记录系列。不同的计算参数给所有条件研究了相似的结果,除非添加剂在电解液导致结疤形成。数据结果还显示,数据获取频率必须至少10赫兹频率去检测比例不适宜或浓度不好的添加剂。 一、简介 在工业铜电解精炼,添加剂如硫代脲(TU),明胶(G)和氯(Cl)被添加到电解浴维持阴极质量和促进平稳阴极沉淀[1,2]。这些添加剂主要起抑制剂的作用,吸附在阴极表面,他们参加电化学结晶过程[3,4]。虽然在电解过程中的机制尚未完全了解[3],但是对于阴极沉淀的需求显然被建立了。但是,当他们的比例或浓度不足[5,6],这些添加剂也有利于结疤形成时。了解电解浴中每个单独的添加剂的活性浓度,因此裂解浴是非常重要的,以确保更好地控制电化学结晶过程和阴极的质量。不幸的是,这个工作非常的难,因为不同的有价值的技术很灵敏和耗时的。更何况,结果可能会由于不同的技术工作而显著不同[8]。
化妆品生产车间工作流程
化妆品生产车间工作流 程 公司标准化编码 [QQX96QT-XQQB89Q8-NQQJ6Q8-MQM9N]
化妆品生产车间工作流程 1、乳化车间 (要求不断自检每道工序产品质量并要求下一道工序监督上一道工序) --原料接收(按配方单核实原料数量和重量并签字确认)--配料(按配方生产工艺单要求严格操作)--乳化(关键控制点:设备工具消毒和运行状况、纯水、蒸汽、抽真空、均质、搅拌、温度等)―― 出料(料桶消毒、请检、称重)--贮存(半成品料请检)--待灌装(检验合格主方可灌装) 2、灌装车间(要求不断自检每道工序产品质量并要求下一道工序监督上一道工序)――领料(核对半成品料和灌装包材的名称、数量、质量并开具领料单签字确认)――灌装(设备工具消毒、运行状况)―― 称量(净含量是否与灌装要求一致)――拧盖(确认瓶与盖是否相配、 拧紧)――首支产品确认(确认与所灌装产品名称、净含量、样板是否相符,确认无误后开始批量生产)――包装(在线检确认合格后方可送出进行外包装) 3、包装车间 (要求不断自检每道工序产品质量并要求下一道工序监督上一道工序)――领料(核对包装材料的名称、数量、质量并开具领料单
签字确认――喷生产日期(确认与所包装产品名称生产日期、样板是否相符)――包装材料检查(确认与所包装产品名称、外观质量、样 板是否相符)――喷生产批号(确认与所包装产品名称生产批号、样板是否相符)――半成品检查(确认与所包装产品名称、外观质量、 样板是否相符)――装彩盒(按要求折好与产品相对应的彩盒并统放入固定位置)――装说明书(按要求折好与产品相对应的彩盒并统一放入固定位置)――封盒盖(确认盒内所放入物料齐全方可封盖) ――套膜(确认与所包装、外观质量、样板是否相符)――裁膜(要求平整、压实、无破裂)――封膜(光滑、无破损)――首支产品确认(确认与所包装产品名称、样板是否相符,确认无误后开始批量生产)――装箱前检查(检查产品名称、生产日期、外观是否合格)――装箱(确认与所包装产品规格、外箱质量)――核数(装箱数量)――入库(核实成品数量并开具入库单签字确认)4、辅助车间 (要求不断自检每道工序产品质量并要求下一道工序监督上一道工序)――领料(核对包装材料的名称、数量、质量并开具领料单签字确认)――清洗(设备工具消毒、运行状况,按不同种类不同的清洗方法操作):1、气压吹尘;2、纯水清洗、烘干;3、酒精擦试;――首支产品确认(确认与所清洗包装产品名称、方法、样板
电解原理的应用——电解精炼铜、电镀
1.2.3 电解原理的应用——电解精炼铜、电镀 课型:新授课主备人:李琴审核人:万社娟韩守霞 学习目标: 学会运用电解的原理分析铜的电解精炼;通过学习电镀的内容,了解具有一定特殊性的、另一种电解原理的应用方法,并进一步体会电解对人类社会的重要贡献。 重点难点: 铜的电解精炼和电镀的原理 旧知链接: 1.离子放电顺序: 常见阳离子放电顺序为: 常见阴离子放电顺序为: 2. 写出用惰性电极电解下列溶液的电极反应式:①CuCl2②H2SO4③ CuSO4 ①阳极: 阴极: ②阳极: 阴极: ③阳极: 阴极: 预习检测: 1、铜的电解精炼:粗铜中含Fe、Zn、Ni、Ag、Pt、Au等少量杂质金属,下图为电解法精炼铜的装置。 其中阳极为,阴极为,电解质溶液为。(并标在图上) 阳极发生的主要反应为: (杂质Fe、Zn、Ni也发生电极反应:由于Pt、Ag、Au的金属性比Cu弱且量又少,这三种金属不反应,以单质的形式沉积在底部,得到阳极泥)。 阴极的反应为
分析电解精炼过程中电解质溶液的变化: 总结: 阳极: 电解精炼装置的构成阴极: 电解质溶液: 2、电镀 阅读教材,设计试验,在铁制品上镀铜(教材第17页“活动·探究)。 要求:画出电镀铜的实验装置图,指出电极材料和电解质溶液,写出电极反应式。 总结: (1)电镀: 阳极: (2)电镀池的构成阴极: 电镀液: 交流·研讨: 1.下列叙述中不正确的是() A.电解池的阳极上发生氧化反应,阴极上发生还原反应 B.不能自发进行的氧化还原反应可通过电解的原理实现 C.电镀时,电镀池里的阳极材料发生氧化反应 D.电解饱和食盐水时,阳极得到氢氧化钠溶液和氢气 2.金属镍有广泛的用途。粗镍中含有少量Fe、Zn、Cu、Pt等杂质,可用电解法制备高纯度的镍,下列叙述正确的是(氧化性Fe2+<Ni2+<Cu2+)( ) A.阳极发生还原反应,其电极反应式:Ni2++2e-→Ni B.电解过程中,阳极质量的减少与阴极质量的增加相等 C.电解后,溶液中存在的金属阳离子只有Fe2+和Zn2+ D.电解后,电解槽底部的阳极泥中只有Cu和Pt 3、下列关于铜电极的叙述正确的是( ) A、铜锌原电池中铜是负极 B、用电解法精炼铜时纯铜作阳极 C、在镀件上电镀铜时可用金属铜作阳极 D、电解稀硫酸制H2、O2时铜作阳极 4、将分别盛有熔融的氯化钾、氯化镁、氧化铝的三个电解槽串联 , 在一定条件下通电一段时间后,析出钾、镁、铝的物质的量之比为( )
流程溶液回收电解精炼铜工艺方案
流程溶液回收电解精炼铜工艺方案 工艺背景 根据国土资源部呼和浩特矿产资源监督检测中心出具的检测报 告指出:内蒙古太平矿业有限公司的约300万吨堆浸喷淋提金过程中的流程循环水所含铜、镍等重金属离子超标,达到排放标准的数十至数百倍。其中铜离子严重超标,急需一种有效的处理办法。 现江苏大学已为我公司初步研制出添加特殊药剂的阳离子交换 树脂,该研发产品对于循环水中铜、铁、镍金属离子有良好的吸附效果。其中铜离子的浓度从200mg/L以上降低至1mg/L左右,吸附率超过99%。经过改进后的处理过程所需时间短,且可以利用现有的设备进行工程搭建,降低了成本投入。除此之外,对于去除后的铜等金属可以进行浓缩电解回收,创造新的经济效益。 流程溶液回收铜工艺方案 采用江苏大学研制添加特殊药剂的阳离子交换树脂,进购8吨,均匀添加至选冶厂一车间PC、CC吸附槽尾槽中,进行杂质离子吸附,在吸附一定时间达到饱和后,用提炭器提至解吸柱中,采用常温常压解吸电解,解吸液为饱和氯化钠溶液,当解吸液进入电解槽后,按照一定电流密度及极间距进行电解,将铜电解至阴极纯铜板上,当阴极板达到要求重量后取下销售,工艺流程图及设备形象联系图如下:
铜回收工艺流程图 1、基建 采用选冶厂二车间闲置储炭罐及塑料罐,安装在选冶厂一车间7区北侧,根据需要进行基础及平台建设,并合理布置管路,厂房布置图及设备形象联系图如下。
铜回收工艺厂房布置图.
铜回收工艺设备形象联系图.
2、吸附阶段 将基建等工作完成后,开始进入生产阶段,将CC、PC吸附槽6号槽用来装离子交换树脂,为了有效拦截树脂不溢出吸附槽,根据离子交换树脂粒度筛分结果,6号槽隔炭筛采用80目筛网,可以100%拦截树脂。为保证炭粉能全部通过6号吸附槽,5号吸附槽隔炭筛采用100目筛网。 3、解吸电解阶段 待树脂吸附饱和后,采用空气提炭器将树脂提至解吸柱中,满 罐后,进行解吸,开启解吸泵,此时进行解吸,电解槽不通电,待解吸液浓度达到电解要求后,电解槽通电,同时进行解吸电解,根据试验得出合理解吸液流量,当解吸完成后,将树脂用高压水流返回吸附槽。 溶液中的Zn、Fe、Ni呈离子状态溶于电解液中,As、Sb、Bi可在阴极放电析出,可以附着在阴极上,也可以造成管道堵塞,其中,Sb比As进入阴极的量多。如果含铅的话,阳极板上也有可能附着PbO2,电解液中Cu2+的浓度如果不足,易使杂质在阴极析出;如果过高,会增大电解液电阻和在阴极表面形成CuSO4·5H2O。镍的电解电流一般控制在180-300 A/m2,与电解铜电解电流相近,阴极板上有可能混有杂质镍。 设备运行参数 1、同名极距:80mm; 2、电解槽阳极板(不锈钢板)10片,阴极板(铜网)11片;
包装车间工艺流程汇总
包装车间工艺流程 一.周转收货工艺流程; 1.清点工件数量和包装班组分配; 由制作车间反馈包装车间项目进度情况,包装依据信息按项目排产要求进行收货,由对皮带机工件熟知的工人,依据设备清单到制作车间进行清点数量和包装班组的分配。 2.制作车间周转运输喷砂车间; 清点工件完成后,由周转运输班组负责转运至抛丸车间进行除锈,班组针对不同的工件使用不同的周转底托和设备,对所周转运输的产品进行保护,确保工件完整的转运至车间。 3.抛丸车间周转运输涂装车间; 抛丸除锈结束以后,周转运输班组依据设备对应的包装班组,进行分配运输,合理的安排转运的时间,确保各个涂装班组可以正常生产,确保及时将工件转至涂装车间,以达到除锈后的涂漆时间,以免在此氧化生锈。 二.抛丸除锈工艺流程; 1.收货运输班组将产品工件转运抛丸车间,抛丸车间依据钢材表面锈蚀和除锈等级标准为国家标准GB8923-88《涂装前钢材表面锈蚀等级和除锈等级》。 2.标准将除锈等级分成喷射或抛射除锈、手工和电动除锈、火焰除锈三种类型。 3.喷射和抛射除锈,用字母“sa”表示,分四个等级: sa1——轻度的喷射后抛射除锈。钢材表面无可见的油脂、污垢、无附着的不牢的氧化皮、铁锈、油漆涂层等附着物。 sa2——彻底的喷射或抛射除锈。钢材表面无可见的油脂、污垢,氧化皮、铁锈等附着物基本清除。 sa21/2——非常彻底的喷射或抛射除锈。钢材表面无可见的油脂、污垢、氧化皮、铁锈、油漆涂层等附着物,任何残留的痕迹仅是点状或条状的轻微色斑。sa3——使钢材表面非常洁净的喷射或抛射除锈。钢材表面无可见的油脂、污垢、氧化皮、铁锈、油漆涂层等附着物,该表面显示均匀的金属色泽。 手工除锈等级: St2 彻底的手工和动力工具除锈 钢材表面应无可见的油脂和污垢,并且没有附着不牢的氧化皮、铁锈和油漆涂层等附着物。 St3 非常彻底的手工和动力工具除锈 钢材表面应无可见的油脂和污垢,并且没有附着不牢的氧化皮、铁锈和油漆涂层等附着物。除锈应比St2更为彻底,底材显露部分的表面应具有金属光泽。
铜冶炼基础知识
冶金概论讲义 1 冶金基本知识 1.1 冶金的概念及冶金方法分类 冶金就是从矿石或二次金属资源中提取金属或金属化合物,用各种加工方法制成具有一定性能的金属材料的过程和工艺。 冶金的技术主要包括火法冶金、湿法冶金以及电冶金, 根据冶炼金属的不同,冶金工业又了可以分黑色冶金工业和有色冶金工业,黑色冶金主要指包括生铁、钢和铁合金(如铬铁、锰铁等)的生产,有色冶金指后者包括其余所有各种金属的生产。 1.2 火法冶金 火法冶金是在高温条件下进行的冶金过程。矿石或精矿中的部分或全部矿物在高温下经过一系列物理化学变化,生成另一种形态的化合物或单质,分别富集在气体、液体或固体产物中,达到所要捉取的金属与脉石及其它杂质分离的目的。实现火法冶金过程所需热能,通常是依靠燃料燃烧来供给,也有依靠过程中的化学反应来供给的,比如,硫化矿的氧化焙烧和熔炼就无需由燃料供热;金属热还原过程也是自热进行的。火法治金过程没有水溶液参加,所以又称为干法冶金。火法冶金是提取金属的主要方法之一,其生产成本一般低于湿法治金。 火法冶金包括:干燥、焙解、焙烧、熔炼,精炼,蒸馏等过程。 1.3 湿法冶金 湿法冶金是在溶液中进行的冶金过程。湿法冶金温度不高,一般低于100℃,现代湿法冶金中的高温高压过程,温度也不过473K左右,极个别情况温度可达573K。 湿法冶金包括:浸出、净化、制备金属等过程。 (1)浸出用适当的溶剂处理矿石或精矿,使要提取的金属成某种离子(阳离子或络阴离子)形态进入溶液,而脉石及其它杂质则不溶解,这样的过程叫浸出。浸出后经沉清和过滤,得到含金属(离子)的浸出液和由脉石矿物绢成的不溶残渣(浸出渣)。对某些难浸出的矿石或精矿,在浸出前常常需要进行预备处理,使被提取的金属转变为易于浸出的某种化合物或盐类。例如,转变为可溶性的硫酸盐而进行的硫酸化焙烧等,都是常用的预备处理方法。 (2)净化在浸出过程中,常常有部分金属或非金属杂质与被提取金属一道进入溶液,从溶液中除去这些杂质的过程叫做净化。
铜电解槽精炼车间工业设计
铜电解槽精炼车间工业设 计 Newly compiled on November 23, 2020
铜电解槽精炼车间工艺设计 一、概述 1、粗铜经火法精炼后仍含有一点数量的杂质。这些杂质的存在会使铜的某些物理性质和机械性能变坏,不能满足电气工业对铜的要求。因此,粗铜在火法精炼后需要电解精炼以除去有害杂质。铜的电解精炼以火法精炼产出的铜为阳极,以电解产出的薄铜片为阴极,以硫酸和硫酸铜水溶液作电解液。在直流电作用下,阳极铜电化学溶解,在阴极上沉积,杂质则进入阳极泥和电解液中,从而实现铜于杂质的分离。 下图为铜电解精炼一般工艺流程图: 种板阳极 阳极 阳极泥 送阳极泥 处理法精炼 结晶硫酸铜粗硫酸 图1-1铜电解精炼一般工艺流程图: 2、铜阳极 铜电解精炼的原料是火法精炼后烧铸而成的铜阳极。生产中应尽量获得质量良好的铜阳极板。 二、技术条件及技术经济指标的选择 1、操作技术条件 ⑴、电流密度
电流密度是指单位面积上通过的电流安培数。电流密度的范围为200-360A /m 2.。种板电解槽电流密度比普通电解槽电流密度稍低,本设计中普通电解槽电流密度取300 A /m 2,种板电解槽电流密度取230A /m 2。 ⑵、电解液成分 电解液成分主要由硫酸和硫酸铜水溶液组成。其铜和硫酸的含量视电流密度、阳极成分和电解液的纯净度等条件而定。在电解生产中,必须根据具体条件加以掌握,以控制电解液的含铜量处于规定的范围。 ⑶、极距 极距一般指同极中心距。本设计取极距为90mm 。 ⑷、阳极寿命和阴极周期 阳极寿命根据电流密度、阳极质量及残极率来确定,一般为18-24天。阴极周期与电流密度、阳极寿命及劳动组织等因素有关,一般为阳极寿命的1/3。本设计中阳极寿命为18天,阴极寿命为6天。 2、技术经济指标 ⑴、电流效率 电流效率是指电解过程中,阴极实际析出量占理论量的百分比。本设计中电流效率为% ⑵、残极率 残极率是指产出残极量占消耗阳极量的百分比。本设计中残极率17%。 ⑶、电解回收率 铜电解回收率反应在电解过程中铜的回收程度,其计算方法如下: 铜电解回收率×100 %
铜电解精炼过程中的节能措施与实践
Total 107铜业工程总第107期No.12011 COPPER ENGINEERING 2011年第1期 铜电解精炼过程中的节能措施与实践 别良伟 (金川集团有限公司精炼厂,甘肃金昌737100) 摘 要:本文结合生产实践,针对铜电解精炼过程中电消耗和蒸汽消耗的问题进行了分析,研究了电解液温 度、 电解液成分、电流密度、添加剂、阴阳极周期和极间短路对电消耗的影响,同时研究了电解液温度、阴极铜烫洗、换热器热效率和气候因素蒸汽消耗的影响,通过严格控制相关电解工艺技术条件等措施,达到了铜电解精炼过程中节能降耗的目的,这对传统铜电解技术水平的提升具有重要的实际意义。 关键词:铜电解精炼;电解液;电消耗;蒸汽消耗中图分类号:TF811 文献标识码:B 文章编号:1009-3842(2011)01-0043-03 收稿日期:2010-11-19 作者简介:别良伟(1981-),男,汉族,河南南阳人,工学硕士,冶金工程师,主要从事铜电解生产技术管理工作, E -mail :bie -liangwei@163.com Energy Saving Measures and Practice in Copper Electrolytic Refining Process BIE Liang -wei (Refinery of Jinchuan Group Limited ,Jinchang ,Gansu ,China 737100) Abstract :Combining with the production practice ,the causes for the issues of electricity consumption and steam consumption in copper electrolytic refining process are analyzed in this article.The effects of electrolytic temperature ,electrolytic composition ,current density ,additives ,anode and cathode cycle and short circuit to electricity consumption are investigated in this article.At the same time ,the factors including temperature of the electrolytic solution ,cathode hot wash ,thermal efficiency of heat exchanger and climate which impacting steam consumption are also studied in this article.The purpose of energy saving can be achieved by controlling related electrolysis processing technology condition.It also had vital practical significance meaning for improving traditional copper electrolysis technology level. Key words :copper electrolytic refining ;electrolyte ;electricity consumption ;steam consumption 1前言 在铜电解精炼过程中电消耗和蒸汽消耗是主要的能源消耗,因此,做好电消耗与蒸汽消耗的节能降 耗工作是降低电解铜的综合成本, 提高产品的市场竞争力的关键所在。2010年国内某公司阴极铜产品的生产规模为400kt /a ,其中小极板电解系统处理自产料铜阳极板能力为60kt /a ,产出48kt /a 标准阴极铜;大极板电解系统处理矿铜阳极板能力为440kt /a ,产出350kt /a 高纯阴极铜。小极板和大极板电解系统工艺均采用传统法电解工艺技术,铜电解的能耗主要是指电消耗和蒸汽消耗,这两项之和约占总能耗的99.0% 99.5%以上,可见铜电解精炼过程中节能的关键是节电和节汽。 2010年,国内某公司大板电解系统处理外购料中电耗指标为440 460kW ·h /t ·Cu ,蒸汽消耗指标为1.7 1.9t /t.Cu ,为了降低阴极铜的生产成本 和车间加工费,优化和提高铜电解精炼过程中的主 要技术经济指标,从而达到节能降耗的目的。本文针对铜电解精炼过程中电消耗和蒸汽消耗耗的问题进行了分析,并采取了相应的措施进行控制和解决。 2影响电单耗的主要因素 [1-2] 铜电解车间电耗有两种,一种是直流电单耗,一种是交流电单耗,它是电解铜生产的关键指标,它综合反映了电解铜生产的技术水平和经济效果。交流电单耗是指单位产品阴极铜所消耗的交流电量。交流电电耗量包括高压和低压交流电的全部消耗量,一般包含机电设备用电,生活生产用电等。影响交流电单耗的因素主要有用电设备的电能利用率;用电设备的选择配置及合理使用;用电的管理等方面。直流电单耗是指单位产品阴极铜所消耗的直流电量。直流电消耗量包括生产槽、种板槽、脱铜槽、 3 4
车间生产工艺流程图
车间生产工艺流程图 实木车间 1.文件柜类:素板→大平砂→开毛料→贴面→精截→封边→钻孔→ 试装→半成品 2.茶几或沙发架: 锯材→干燥→截断→纵剖→压刨→划线→铣型→ 开榫头、榫槽→钻孔→手工组装→打磨→半成品 3.班台或会议桌: 素板(锯材)→大平砂(干燥)→开毛料(截断)→加厚 (纵剖)→精截(压刨)→加宽(胶贴)→贴面(热压)→ 铣型(精截)→手工组装(包括打磨、打腻子、封边、 钻孔)→试装→半成品 油漆车间 白坯→机磨(大平面)→手磨(小面、曲边)→擦色(打水灰、打底得宝、打腻子)→机磨(大平面)→手磨(小面、曲面)→PU(第1道底漆)→ 机磨(打平面)→手磨(小面、曲面)→PE(第2道底漆)→打磨(机磨、 手磨)→修补→修色→手磨→面漆→干燥→试装→包装 板式车间 1.开料→手工→封边→钻孔→镂铣、开槽→清洗→试装→包装 2.开料→力刨→涂胶→贴面→冷压→精截→手工→封边→钻孔 →镂铣、开槽→清洗、修边→试装→包装 沙发车间 裁皮、开棉→打底(电车)→粘棉→扪皮(组装)→检验→包装
转椅车间 裁布(皮)、开棉→车位、粘绵→扪皮→组装→检验→包装 屏风车间 开料(铝材)→喷胶→贴绵→扪布(打钉)→组装→试装→包装 五金车间 1.椅架类: 开料→弯管→钻孔、攻牙→焊接→打磨→抛光→喷涂 2.钢板类: 开料→冲板(圆孔、圆凸、方孔、方凸、小梅花、大梅花、 网孔、菱凸)→折弯→焊接→打磨→喷涂 3.台架类: 开料→冲弯→钻孔、攻牙→焊接→打磨→抛光→喷涂 4.电镀类: 开料→开皮→冲弯→焊接→打磨→精抛→电镀 总:开料(裁剪、剪板)→制造(冲床、弯管、钻孔、攻牙)→成型(焊接、打磨、抛光)→喷涂、电镀 喷涂车间 清洗→凉干→打磨→喷漆(喷粉)→电烤→包装
铜电解精炼冶金计算
铜电解精炼冶金计算 1、物料平衡计算 计算条件:产量为100000t电解铜/a,年工作日为355天。 火法精炼后阳极成分见表7-1。 表7-1 阳极成分 元素Cu Ni As Sb Ag Fe Bi Te Se+S O Au Pb 99.0 0.08 0.2 0.126 0.06 0.002 0.025 0.01 0.002 0.10 0.025 0.1 含 量% 电回收率:99.0%;残极率:15%。 铜电解过程元素分配%) / (W: 表7-2 铜电解过程元素分配%) (W / 元素进入电解液进入阳极泥进入电解铜 Cu 1.75 0.15 98.10 Ni 81.00 18.70 0.20 As 63.40 36.30 0.3 Sb 17 78 5 Ag —95 2 Bi 18 82.5 1.5 Se+—94 6 Te S —96 4 O —97 3 Au —98.5 1.5 Pb —93 7 Fe 74 53 21 假设以溶解100kg的阳极铜平衡进行计算 1.1阴极铜产量和电铜品味计算
Cu:99.0×98.1%=97.119kg Ni:0.08×0.2%=0.00016kg As:0.2×0.3%=0.0006kg Sb:0.126×5%=0.0063kg Ag:0.06×5%=0.003kg Bi:0.025×1.5%=0.000375kg Se+Te:0.01×6%=0.0006kg Fe:0.002×21%=0.00042kg S:0.002×4%=0.00008kg O:0.1×3%=0.003kg Au:0.025×1.5%=0.000375kg Pb:0.1×7%%=0.007kg 合计:97.141kg 电铜品位:97.119÷97.141=99.98% 1.2阳极泥率和成份计算 Cu:99×0.15%=0.1485kg Ni:0.08×18.7%=0.1496kg As:0.2×36.3%=0.0726kg Sb:0.126×78%=0.09828kg Ag:0.06×95%=0.057kg Se+Te:0.01×94%=0.0094kg S:0.002×96%=0.00193kg O:0.1×97%=0.097kg Au:0.025×98.5%=0.024625kg Pb:0.1×93%=0.093kg Fe:0.002×3%=0.00006kg
年产10万吨电解铜的铜电解车间设计本科毕业设计(论文)任务书
本科毕业设计论文 年产35万吨电解铜的铜电解车间设计
目录 1 前言 (1) 1.1铜的性质 (1) 1.1.1铜的物理性质 (1) 1.1.2铜的化学性质 (3) 1.1.3铜的主要化合物的性质 (3) 1.2铜的用途 (4) 1.3铜资源状况 (5) 1.3.1世界铜资源 (5) 1.3.2中国资源 (7) 1.4中国铜的生产状况和消费 (8) 1.4.1中国铜的生产状况 (8) 1.4.2铜的消费 (9) 1.5.1铜的湿法冶金 (10) 1.5.1铜的火法冶金 (11) 1.6铜的新技术......................... 错误!未定义书签。 1.6.1一种采用溶剂萃取净化铜电解液的方法本错误!未定义 书签。 1.6.2分散强化型电解铜箔及其制造方法错误!未定义书签。 1.6.3硫化矿细菌浸出............... 错误!未定义书签。 1.7设计的内容 (12)
1.7.1冶金计算 (12) 1.7.2重要设备及辅助设备计算 (12) 1.7.3制图内容和要求 (12) 2 厂址选择 (14) 3.1铜电解精炼流程简述 (16) 3.2铜电解精炼的理论基础 (18) 3.2.1阳极过程 (18) 3.2.2阴极过程 (18) 3.2.3阳极上杂质 (19) 3.3电解液的净化 (20) 4 铜电解精炼的主要设备选择 (21) 5 铜电解技术指标 (24) 5.1铜电解的条件 (24) 5.1.1电解液组成 (24) 5.1.2添加剂 (24) 5.1.3电解液温度 (25) 5.1.4电解液循环 (25) 5.1.5电流密度 (25) 5.1.6同极中心距 (26) 5.2阳极寿命和阴极周期 (26) 6 主要经济技术指标 (27)
铜电解生产成本构成及影响分析
铜电解生产成本构成及影响分析 孙发昌 (云南铜业股份有限公司冶炼加工总厂电解分厂,云南昆明 650102) 摘要:本文简要介绍了铜电解生产成本构成情况,分析了铜电解生产过程中变动成本的主要影响因素,并从成本管理的角度,对生产组织中成本控制措施进行探讨。 关键词:铜电解;成本构成;变动成本;成本控制 1 引言 在市场经济条件下,铜电解生产除了保证产品质量满足标准要求以外,在目前铜资源有限,冶炼企业产能过甚的前提下,如何降低企业生产加工成本,对提升企业市场竞争力,延续企业生命显得至关重要。本文对铜电解生产厂成本构成及影响进行分析,并对成本控制措施进行探讨。 2 成本构成及影响分析 2.1电铜产量变化对变动成本的影响分析 某电解厂历年电铜产量与单位加工成本的关系见图1。 图1 某电解厂历年产量与单位加工成本关系图 某电解厂2010年电铜产量与单位加工成本的关系见图2。
图2 某电解厂2010年各月变动成本与产量之间的关系图 由图1或图2可看出,单位加工成本随主产品产量降低而增加,产量越低,单位加工费用成本越高,相反,产量越高,单位加工成本降低;成本的变化在高产量情况下相对稳定于某一值;在低产量情况下比较,单位成本随产量变化趋势不明显。 可以得出,在生产负荷可控制范围内,产量的高低与变动成本高低近似成反比列关系。2.2 铜电解成本构成分析 下面以2010年某电解厂成本完成情况表来做分析,2010年某电解成本完成情况见下表1。 表1 2010年某电解厂不变价成本报表 费用项目 累计产量:236490.858吨所占比列1-12月累计单耗(元/t-cu) (%) …………………… 一、固定费用合计32465545.63 137.28 30.56 11、动力费用58957674.70 249.30 55.49 其中:水274309.00 1.16 0.26 电33274944.50 140.70 31.32 排水188550.00 0.80 0.18 蒸汽21214311.10 89.70 19.97 压缩风177491.20 0.75 0.17 12、材料6404447.45 27.08 6.03 其中:辅料3331276.36 14.09 3.14 备件2523408.98 10.67 2.38 低值易耗品549762.11 2.32 0.52 13、修理费688993.29 2.91 0.65 其中:外委修理费0.00 0.00 0.00 机修加工费355876.30 1.50 0.33 动力修理费23433.45 0.10 0.02 机动车修理费309683.54 1.31 0.29 14、其它费7732340.19 32.70 7.28 运输费43227.28 0.18 0.04 差旅费48108.00 0.20 0.05 办公费4084.80 0.02 0.00 劳务费5407635.22 22.87 5.09 其它分摊2229284.89 9.43 2.10 二、变动费用合计73783455.63 311.99 69.44 合计106249001.26 449.27 100.00 从表1中可以看出,2010年某电解厂成本完成情况为每吨铜449.27元(注:不包括三项费用),其中变动费用部分成本为每吨铜311.99元,约占70%,固定成本为每吨铜137.28元,约占30%,就电解厂来说,分厂能够控制的费用部分主要为变动费用,以下对变动费用成本构
包装车间操作流程
包装车间操作流程及要求 1、包装主管首先了解《生产计划》和《出货计划》,然后 根据需求针对每个款的《包装需求通知单》要求安排自 己车间的每周生产计划。 2、领料 1)根据《生产计划》和《包装需求通知单》,由主管/统计员先查询生产系统,确认品种、数量能否满足生产需求。 如无库存或者数量不足,须及时通知生产部处理。 2)主管核对无误后填写《领料单》,内容、单号、物料名称、物料编码单位、数量等按要求填写相应栏内。 3、付料、送料 物料送至包装部指定地点后,仓储保管员与车间主管现场共同核对品种和数量,并在《领料单》上签字。 4、包装物的品种核对要求 1)外箱、贴标、挂牌等核对款名、色号、数量是否准确。2)辅料,如胶带、牛皮纸、汽泡纸等是都够用,胶钉、脚垫、配套螺丝、螺母等。 3)所有工具、刀片、胶纸、胶纸机等要备齐。 5、车间生产要有“生产通知单”和“首件确认样”方可批 量生产。所有工作都按包装要求,质量标准操作,做到 自行检验,自检出不合格品。 6、工作中有垃圾的工位,要随手放人垃圾桶中,下班统一
清理,不可随地吐痰,保证公共区域的清洁。 7、搬动产品或其他物品,不可再地上拖拉,应用搬运车或 者人工抬动,掉落地面的产品或物品要及时捡起,保持地面整洁。 8、整形平台要有标准样,按照要求进行整形,完成后要归 位存放,不可占用工作场地。 9、使用工具要定点存放,注意保养、保管。 10、产品要经过员工自检,质检人员确认方可入包装箱,入 库。 11、工作中检验的不合格品要放在指定区域,并有管理人员 每天定时清理。 12、生产所需要的辅助物品要管理人员统一收发管理。 13、生产单结束后,管理人员要清点尾数,结余物料要分类 清理后及时退回仓库。 14、任何工作必须遵循“安全为先、质量为重、效益为主” 的原则。 15、车间地面要每天清扫,每周除尘一次。 16、下班时要清扫工作台面,整理好物品,按要求关电、关 气、关设备、关门窗。 17、进出车间要安静有序,不可喧哗。
铜的电解精炼技术
铜的电解精炼 铜的电解精炼,是将火法精炼的铜浇铸成阳极板,(现在普遍的工艺)用永久性不锈钢阴极作为阴极片,相间的放入电解槽中,用硫酸铜和硫酸的水溶液作为电解液,在直流电的作用下,阳极上的铜会失去两个电子生成-2价铜离子,而贵金属和某些金属不溶,成为阳极泥沉淀于电解槽低。溶液中的-2价铜离子会在阴极上优先析出,而其他电位较负的贱金属不能在阴极上析出,留在电解液中,待电解液定期净化时除去。这样,得到的铜纯度很高,称电铜。 简单说一下电解精炼的工艺:电解液由循环槽经电解液循环泵泵至板式换热器,加热至65℃左右以稳定的流量供到各个电解槽。电解槽供液采用底部给液(也有的采用侧面给液)、两端溢流出液的方式,槽两端溢流出的电解液汇总后返回循环槽。为保证电解液的洁净度,配备了专用的LAROX净化过滤机,循环系统每天抽取电解液循环量的约25%进行净化过滤。根据电解液中杂质的情况,每天抽取部分电解液进行脱铜、脱杂处理,保证电解液中铜、酸及杂质浓度不超过极限值。为保证电解液成分,调节阴极铜的物理性能,需在电解液中加入硫酸、添加剂。现在普遍采用的是永久性不锈钢阴极电解技术。它的主要优点:1、高电流密度2、极间距小3、残极率低4、阴极周期短5、蒸汽耗量低、6、机械化程度高,适用于大规模生产。 1、电解液 铜离子从阳极转移到阴极的载体。如果说阳极、阴极是铜电解过程的两个支柱,电解液则是铜电解过程中铜离子迁移的载体。组成:C U SO4、H2SO4、H2O、添加剂(盐酸、有机化合物)。 1)H2SO4一般波动于100—220g/L,电流密度在300A/m2、电解液温度在60~65℃时要把H2SO4控制在180g/L。 电解液的物理性质——影响比电导的因素:H2SO4>电解液温度>杂质>C U2+ 酸度越大,电解液的导电性越好。但是H2SO4不能无限地升高,硫酸升高时,硫酸铜的溶解度会降低,甚至析出沉淀(C U SO4·5H2O)。 2)电解液中C U2+的稳定性很重要。C U2+浓度不得小于35g/L,否则杂质A S、S b、B i可能在阴极析出,C U2+浓度升高时,电阻、槽电压、电能消耗都会升高,严重时会有 硫酸铜析出。要控制C U2+在45—48g/l范围内。C U2+大幅度波动会使阴极铜质量失
有色金属冶金技术作业答题
有色金属冶金技术作业答题汇总 第一篇轻金属冶金学 第一章氧化铝生产 【习题及思考题】 1、常见的氧化铝及其水合物有哪些?比较它们的化学活性。 铝土矿按其含有的氧化铝水合物的类型可分为:三水铝石型铝土矿;一水软铝石型铝土矿;一水硬铝石型铝土矿;混合型铝土矿。我国铝土矿资源丰富,储量大;高铝、高硅、低铁;铝硅比较低,中低品位铝土矿居多;多数铝土矿是一水硬铝石型铝土矿。 2、试比较国内外铝土矿的特点。 中国铝土矿的特点 我国铝土矿的特点高硅、高铝和低铁,为一水硬铝石型,矿石中铝硅比在4~7之间 [m(Al2O3)/ m(SiO2)]。福建、河南和广西有少量的三水铝石型铝土矿。 3、砂状氧化铝和面状氧化铝各有什么特点?为什么砂状氧化铝的生产已发展成为主流? 4、指出衡量铝土矿的质量的指标 铝土矿质量评价标准:A、矿石类型 B、矿石中可溶性氧化铝含量 可溶性氧化铝含量是由氧化铝总量减去由氧化硅生成羟基方钠石化合物所损失的氧化铝 量。铝土矿的可溶性碱液溶出次序:三水铝石型、一水软铝石型、一水硬铝石型。 5、目前生产氧化铝的最主要的原料有哪些 生产氧化铝的原料有铝矿土,明矾石矿和霞石矿。 6、铝酸钠溶液的稳定性对生产过程有什么影响? 7、指出拜耳法的原理及实质?拜耳法原理:用苛性钠溶液(其质量浓度为130~350gNa2O/L)在加热的条件下将铝土矿中的各种氧化铝水合物溶解出来,生成铝酸钠溶液,此种溶液经稀释后在冷却的条件下分解出纯的氢氧化铝,同时重新生成苛性钠溶液,供循环使用。流程见下页 拜耳法流程包括三个主要步骤:铝土矿溶出;铝酸钠溶液分解;氢氧化铝煅烧 溶出:指把铝土矿中的氧化铝水合物(Al2O3·xH2O)溶解在苛性钠(NaOH)中,生成铝酸
年产10万吨电解铜的铜电解车间设计本科毕业论文设计40论文41任务书
(此文档为word格式,下载后您可任意编辑修 改!) 本科毕业设计论文 年产35万吨电解铜的铜电解车间设计
目录 1 前言 (61) 1.1铜的性质 (61) 1.1.1铜的物理性质 (61) 1.1.2铜的化学性质 (64) 1.1.3铜的主要化合物的性质 (64) 1.2铜的用途 (66) 1.3铜资源状况 (67) 1.3.1世界铜资源 (67) 1.3.2中国资源 (69) 1.4中国铜的生产状况和消费 (71) 1.4.1中国铜的生产状况 (71) 1.4.2铜的消费 (72) 1.5.1铜的湿法冶金 (73) 1.5.1铜的火法冶金 (74) 1.6铜的新技术........................ 错误!未定义书签。 1.6.1一种采用溶剂萃取净化铜电解液的方法本错误!未定义 书签。
1.6.2分散强化型电解铜箔及其制造方法错误!未定义书签。 1.6.3硫化矿细菌浸出.............. 错误!未定义书签。 1.7设计的内容 (76) 1.7.1冶金计算 (76) 1.7.2重要设备及辅助设备计算 (76) 1.7.3制图内容和要求 (77) 2 厂址选择 (78) 3.1铜电解精炼流程简述 (81) 3.2铜电解精炼的理论基础 (83) 3.2.1阳极过程 (83) 3.2.2阴极过程 (84) 3.2.3阳极上杂质 (85) 3.3电解液的净化 (86) 4 铜电解精炼的主要设备选择 (88) 5 铜电解技术指标 ......................... 错误!未定义书签。 5.1铜电解的条件...................... 错误!未定义书签。 5.1.1电解液组成.................. 错误!未定义书签。 5.1.2添加剂...................... 错误!未定义书签。
年产10万吨电解铜的铜电解车间设计
年产35万吨电解铜的铜电解车间设计 目录 1 前言 (1) 1.1铜的性质 (1) 1.1.1铜的物理性质 (1) 1.1.2铜的化学性质 (3) 1.1.3铜的主要化合物的性质 (3) 1.2铜的用途 (4) 1.3铜资源状况 (5) 1.3.1世界铜资源 (5) 1.3.2中国资源 (7) 1.4中国铜的生产状况和消费 (8) 1.4.1中国铜的生产状况 (8) 1.4.2铜的消费 (9) 1.5.1铜的湿法冶金 (10) 1.5.1铜的火法冶金 (11) 1.6铜的新技术......................... 错误!未定义书签。 1.6.1一种采用溶剂萃取净化铜电解液的方法本错误!未定义 书签。 1.6.2分散强化型电解铜箔及其制造方法错误!未定义书签。
1.6.3硫化矿细菌浸出............... 错误!未定义书签。 1.7设计的内容 (12) 1.7.1冶金计算 (12) 1.7.2重要设备及辅助设备计算 (12) 1.7.3制图内容和要求 (12) 2 厂址选择 (14) 3.1铜电解精炼流程简述 (16) 3.2铜电解精炼的理论基础 (18) 3.2.1阳极过程 (18) 3.2.2阴极过程 (18) 3.2.3阳极上杂质 (19) 3.3电解液的净化 (20) 4 铜电解精炼的主要设备选择 (21) 5 铜电解技术指标 (24) 5.1铜电解的条件 (24) 5.1.1电解液组成 (24) 5.1.2添加剂 (24) 5.1.3电解液温度 (25) 5.1.4电解液循环 (25) 5.1.5电流密度 (25) 5.1.6同极中心距 (26)
包装车间规章制度
包装车间规章制度 1。包装车间管理制度 1.目的:为了维护车间良好的生产秩序,提高劳动效率,保证生产工作的顺利进行。 2.详细内容: 一、会议制度: 1.包装车间员工每天提前10分钟到达车间参加早会,不得迟到、早退。 2.员工在开早会时必须站立端正,认真听讲,不得喧哗吵闹,不得做与早会无关的事。 3.车间班组长开早会时必须向员工传达前一天的工作情况以及当天的生产计划,时间控制在10分钟以内。 二、车间卫生及管理制度: 1.车间工作人员应保持良好的个人卫生,勤洗澡,勤换衣服,勤理发,不得留长指甲和涂指甲油。 2.进入车间必须穿戴工作服,头发不得外露,不得穿拖鞋、背心、赤膊,短裤、超短裙及肉色丝袜进入车间. 3.不得将生产无关的个人用品和饰物(如手表、耳环、首饰等)带入车间,更不得把生产工具带出车间。 4.车间内严禁吸烟(含在厕所内),一经发现200元/次. 5.车间内使用的工具和设备每天上下班之前进行5s活动,并保证安全有效,工作过程中必须按相关规定进行操作。
6.每道工序必须接受车间管理人员的检查、监督,不得蒙混过关,虚报数量,并配合管理人员的工作,不得顶撞、辱骂管理人员否则给予50元罚款如情节严重者开除出厂。 7.对于工作中出现的工作漏失,(如漏放附件与包错板子等),视情节轻重分别予以5-50元不等处罚。 8.员工在工序操作过程中不得随意损坏物料、工作器具等设备,违者按原价赔偿。 9.员工在上班过程中不得随意走动(管理人员因工作需要除外),不得大声吵闹、喧哗,不得播放音乐。 10.员工上班期间随时保持工作环境的整洁,不可乱扔垃圾,不可浪费公司的产品。11所有员工要听从管理人员的安排,服从生产安排、调动,努力学习生产技术,提高自身素质,提高劳动效率。 12.员工在运送物料时要尽量做到轻拿轻放,避免因个人失误给公司造成损失和浪费。因此造成的损失由员工自己负责。 13.员工之前要互相监督,对包庇、隐瞒不良行为者一经查实严厉处罚。14员工在作业时必须按要求戴好手套,同时必须做好自检和互检工作,如发现问题要及时向车间负责人反映,不可擅自使用不良材料和让不合格品进入下一道工序,必须严格按照品质要求作业。 15.每天工作结束后要对工作台面、及地面进行清洗清洁,地面不得出现积水现象,同时整理好工作器具并摆放整齐。 三、请假制度: