基于过程强化的铜冶炼烟灰中砷选择性去除工艺及机理
210978599_铜冶炼烟尘综合回收工艺浅析及建议

M etallurgical smelting冶金冶炼铜冶炼烟尘综合回收工艺浅析及建议焦晓杰,句世俊,郝璐瑶摘要:随着社会的发展,对铜资源的需求也越来越大,但是在铜冶炼的过程当中,烟尘是一种潜在的二次资源,但同时也是一种破坏生态环境的物质,因此,需要通过对烟尘的回收利用,更好地提升资源的利用价值,进而促进对环境的保护。
近年来,很多铜工业为了实现资源的最大化利用,越来越关注铜冶炼烟尘综合回收工艺,更好地控制铜工业生产带来的烟尘污染。
在烟尘的综合回收当中,由于涉及的工艺流程比较复杂,很容易出现一些工艺上的问题,不仅不能实现二次资源的有效利用,而且还会对环境带来污染,因此本文在研究当中将通过对铜冶炼烟尘综合回收的工艺进行分析,进而更好的发现在铜冶炼烟尘综合回收当中存在的一些问题,结合烟尘回收工艺的要求,提出铜冶炼烟尘综合回收的有效建议,进而提升铜冶炼烟尘回收的效率和质量。
关键词:铜冶炼;烟尘综合回收;工艺浅析;建议铜作为一种稀有的自然资源,在开发之后也需要经过一定的处理才能够得到满足要求的铜,在当前的发展当中,铜已经被广泛地应用在各个领域当中,对于铜的需求也越来越大,也使得铜工业的发展得到了迅速的进步,但是在铜工业的生产当中,会产生一些烟尘及废气等物质,对环境带来的污染和伤害也是很大的。
在铜工业当中,铜冶炼是生产铜精矿的重要手段,随着时代的发展,铜冶炼的工艺技术也在不断地提升,通过烟尘回收工艺,使得铜冶炼也正在朝着绿色的方向发展。
目前在铜冶炼当中,也出台了《铜冶炼行业规范条例》,其中明确强调了铜冶炼的环保要求,要采用清洁能源来确保铜冶炼的环保达标。
在铜冶炼的烟尘当中具有十分重要的铅、铜、锌等价值元素,通过对烟尘的综合回收,也能够有效地实现对资源的二次利用,进而为铜工业的发展带来更大的经济效益与社会效益。
在铜冶炼烟尘的综合回收当中,通过对价值元素的回收,更好地提升资源的利用价值,还能够减少对生态环境带来的危害。
砷滤饼的铜砷分离工艺研究

砷滤饼的铜砷分离工艺研究砷滤饼是含有高浓度砷的固体废料,主要通过铜矿矿石的提取过程产生。
砷是一种有害物质,对环境和人体健康造成严重危害,因此砷滤饼的处理和砷的分离成为一项重要的工艺研究。
铜矿矿石中的砷主要以砷酸盐的形式存在,而铜则以硫化铜的形式存在。
因此,砷滤饼的铜砷分离工艺的关键在于将砷酸盐与硫化铜分离开来。
常用的砷滤饼的铜砷分离工艺主要包括浸出、沉淀和萃取三个步骤。
浸出是将砷滤饼中的砷酸盐溶解出来的过程。
常用的浸出剂有氢氧化钠、氢氧化钾和硫酸等。
在浸出过程中,需要控制浸出剂的浓度和温度,以提高砷酸盐的溶解度和浸出效率。
沉淀是将砷酸盐与硫化铜进行分离的过程。
一般采用金属离子沉淀剂,如铁离子或钙离子,将砷酸盐转化为难溶性的砷酸铁或砷酸钙沉淀物。
通过控制沉淀剂的加入量和pH值,可以实现砷酸盐与硫化铜的有效分离。
萃取是将砷酸盐从砷酸铁或砷酸钙沉淀物中提取出来的过程。
常用的萃取剂有有机溶剂,如酮类、酯类和醚类等。
通过与砷酸盐形成络合物,然后用有机溶剂进行萃取,可以实现砷酸盐的分离和回收。
除了上述传统的工艺方法,近年来还出现了一些新型的砷滤饼的铜砷分离技术。
例如,利用离子交换树脂可以实现砷酸盐的选择性吸附和分离。
另外,利用化学法或生物法将砷酸盐还原成亚砷酸盐,然后再进行分离和回收。
砷滤饼的铜砷分离工艺研究是一项重要且具有挑战性的课题。
通过浸出、沉淀和萃取等步骤,可以实现砷酸盐与硫化铜的分离,从而达到对砷滤饼的处理和砷的回收利用的目的。
未来的研究还需要进一步改进工艺方法,提高分离效率和回收率,以及解决废水和废渣的处理问题,从而实现砷滤饼的资源化利用和环境友好型处理。
试论有色冶炼烟气骤冷收砷技术

试论有色冶炼烟气骤冷收砷技术有色冶炼是指对有色金属矿石进行加工,从中提取出有色金属的工艺过程。
虽然有色冶炼在提供大量有色金属资源方面具有重要地位,但它也会产生大量污染物,其中之一就是烟气中的砷。
砷是一种有害物质,它在环境中具有累积性和毒性,对人体健康和环境都有潜在风险。
如何有效地收集和处理含砷烟气已成为有色冶炼行业亟需解决的问题。
目前,一种常用的砷收集技术是骤冷收砷技术。
该技术通过将烟气迅速冷却,使砷以颗粒的形式凝结并固化,然后通过不同的方法进行回收或处理。
这种技术相对简单且操作成本较低,因此在实际应用中广泛采用。
骤冷收砷技术的关键是如何控制烟气的冷却速度和温度梯度。
过快的冷却速度会导致烟气中的砷凝结不完全,从而难以回收;而过慢的冷却速度则会增加冷凝设备的体积和能耗。
寻找合适的冷却介质和优化冷却设备的结构是提高骤冷收砷技术效果的关键。
常用的冷却介质包括水,制冷剂和废热回收等。
水是一种常见且经济的冷却介质,但其冷却效果有限,需要大量的水资源和处理成本。
制冷剂具有较高的冷却效率,但成本较高且需要特殊的设备和操作。
废热回收则是一种相对环保和经济的方式,通过利用冶炼过程中产生的废热进行骤冷,既可以降低能耗,又可以减少环境污染。
除了冷却介质的选择外,骤冷设备的结构也对技术的效果产生重要影响。
常见的设备包括骤冷器和除尘器。
骤冷器可以将烟气迅速冷却,并通过特定的结构和设备,使砷以颗粒的形式凝结并固化。
除尘器则是用于去除烟气中的固体颗粒,在净化烟气的也可以回收其中的砷。
骤冷收砷技术也存在一些问题和挑战。
砷的收集和处理涉及到化学物质的使用和后续处理,需要注意环境和安全问题。
砷的凝结和固化需要适当的温度和时间,否则可能导致砷的再挥发和扩散。
砷的凝结和固化过程还与烟气中其他成分的影响有关,需要进行综合考虑和优化。
有色冶炼烟气骤冷收砷技术在砷污染治理中具有重要的应用价值。
随着技术的不断发展和完善,相信这项技术将在有色冶炼行业得到更广泛的应用,为保护环境和人体健康提供更好的保障。
探讨铜冶炼烟尘处理技术

探讨铜冶炼烟尘处理技术摘要:铜冶炼烟尘是铜火法冶炼中产出的典型危废,具有砷及有价金属含量高的特点,运输及处理过程中极易造成环境污染,对其就地资源化利用日益受到企业重视。
国内外针对铜烟尘处理开展了大量研究,大致分为火法和湿法两大类。
早期火法应用较多,目前以湿法为主。
根据反应介质的不同,湿法可分为硫酸、氯盐和碱性体系三种。
硫酸体系易与主工艺流程结合,应用最广,具有较强的竞争力。
由于各企业烟尘性质存在差别,处理工艺多样,小型企业多采用硫酸常压浸出—鼓风炉工艺,溶液中砷以砷酸铁等形式沉淀。
关键词:金属冶炼;烟尘处理;环保措施前言近年来,我国的铜冶炼行业进步迅猛,极大地带动了我国工业化的进步,为经济发展增添强大的动力。
不过,随之而来的是一些环保问题。
铜冶炼过程会排放大量的有害烟尘,包含诸多有害物质,严重地破坏了自然环境。
因此,探究铜冶炼过程中的烟尘处理技术对于环境保护具有重要的意义。
国内外针对烟尘处理进行了大量研究及生产实践,大致可分为火法和湿法两大类。
火法主要是将砷挥发进入烟尘,焙砂浸出回收铜等,早期工业应用较多,但砷回收率低,难以避免砷污染问题。
湿法可分为硫酸体系、氯盐体系和碱性体系几大类,近几年针对碱性浸出工艺进行了大量研究,但该工艺成本相对较高,砷以砷酸钠形式进入溶液,需进行转化回收。
由于硫酸体系处理技术成熟,易与主工艺流程结合,工业生产中多采用硫酸浸出工艺处理烟尘,铅渣经火法熔炼生产电铅,或送铅冶炼企业进行处理,高砷浸出液多采用二氧化硫还原生产三氧化二砷,低砷溶液多采用铁盐法沉淀砷酸铁。
国家及行业相关污染防治政策及法案的出台,使得企业对危险废物无害化处理高度重视,含砷物料的就地协同处理及砷的产品化是今后发展的重要方向。
1我国铜冶炼工业背景1.1 国内铜矿冶概况近几年来,我国铜工业在规模和装备水平上有了很大的发展,各大炼铜企业的设备、技术已达到国际先进水平,高污染的工艺、设备被淘汰、替代,自主开发了闪速熔炼工艺;还引进了方圆氧底吹熔炼多金属捕集工艺,经本土化改造后,能耗、炉龄、废气排放等方面与欧美同类冶炼方法相当。
有色冶金工业含砷烟尘处理及利用研究进展
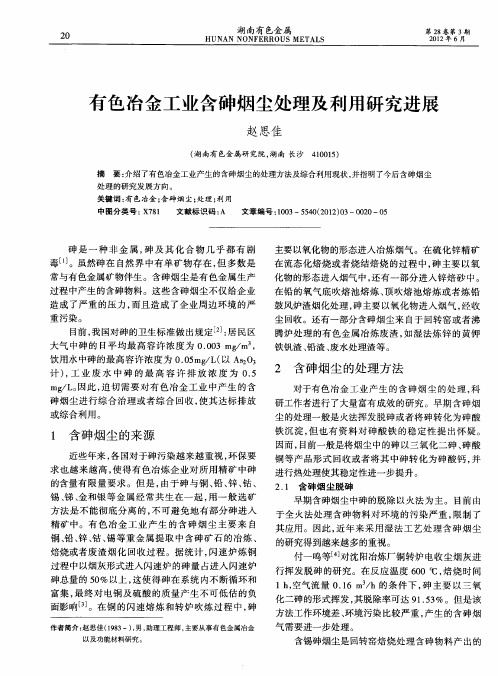
1 含 砷 烟 尘 的来 源
近些 年来 , 国对 于砷 污染 越 来 越重 视 , 保要 各 环
2 1
烟气 经 收尘 系统捕 集得 到 的 。 回转 窑 焙烧 产 生 的 冷 凝 烟尘含 砷 4 %左右 , 2 %左 右 。柏宏 明l 对 从 5 锡 0 j
法 。砷 固体废 物 的化 学 方 法 处 理 成 本 较 高 , 有 的 且 还 会 产 生大 气 污 染 , 对 产 生 量 大 的无 机 固体废 物 针 应 用较少 , 外 , 生 物 作 用 下 , 机 砷 转 化 为挥 发 另 在 无 性 甲基砷 后 , 的毒 性 作 用 会 显 著 增 加 , 以 , 它 所 目前 还 没有合 适 的生 物方 法 处 理含 砷 有 害 固体 废 物 】 。 物 理方 法是 有害废 物无 害 化处 理应 用 较 多 的一 种方 法, 尤其 对 固体 有 毒 物质 的 长期 安 全 堆 存 。美 国 环
处理 的研究发展方 向。 关键词 : 色冶金 ; 有 含砷烟 尘; 处理 ; 利用
中 图分 类 号 : 7 1 X 8 文献 标 识 码 : A 文 章 编 号 :0 3—54 (0 2 0 —0 2 —0 10 5021)3 00 5
砷 是 一 种 非 金 属 , 及 其 化 合 物 几 乎 都 有 剧 砷 毒 u 。虽 然砷 在 自然 界 中有 单 矿 物存 在 , 多 数 是 J 但 常 与有 色金属 矿物伴 生 。含砷 烟 尘 是有 色 金属 生 产 过程 中产 生 的含砷 物料 。这 些含 砷 烟尘 不 仅 给企 业
重有色金属冶炼中砷的脱除与回收

2003年8月中国有色金属学会第五届学术年会论文集Aug.2003收稿日期:3--重有色金属冶炼中砷的脱除与回收魏昶,姜琪,罗天骄,黄孟阳(昆明理工大学材料与冶金学院,云南昆明650093)摘要:介绍了铜、锡、铅、锌重有色金属冶炼过程中砷的分布和脱除情况。
铜冶炼的脱砷重点在铜电解液的净化,主要采用电解法和溶剂萃取法,而铜冶炼过程中火法脱砷研究较少。
锡精矿含砷0.5%~5.5%,一般在熔炼前进行焙烧脱砷,而冶炼过程中产生的高砷烟尘则采用电热回转窑焙烧法或湿法脱砷。
铅锌冶炼过程脱砷的研究集中在高铅砷转炉烟尘、铅阳极泥及次氧化锌的脱砷研究。
关键词:脱砷;重有色金属冶炼;高铅砷A r s eni c R e m ova l a nd Recover y i n H ea vy M et a l s Sm el t i ng Pr oces sW e i Chang,J i ang Q i ,L uo T i an-j i ao,H uang M e ng-yang(School of M at er i al s a nd M et al l ur gy,K unm i ng U ni ve r si t y of Sci ence and T echnol ogy,K unm i ng 650093)A bsr t act :T he di st r i but i on and r em oval t e chnol ogy of A r seni c i n t he he avy m et al s such a s c opper ,t i n,l ea d and z i nc sm el t i ng pr oces ses ar e i nt r oduced.I n t he copper m e t al l ur gi cal pr ocess ,a r seni c i s dom i nant l y el i m i nat ed i n t he el e ct r ol yt e pur i f i cat i on by t he e l ect r ol ysi s and s ol ve nt ext r act i on pr ocess.Ther e ar e f ew r esul t s on t he a r se ni c r e m oval w i t h t he pyr o-pr ocess f or coppe r sm el t i ng.The cont ent of ar se ni c i n t he t i n concent r at e i s about 0.5%~5.5%,pr e-t r ea t m ent f or ar seni c r e m ova l by t he r oast i ng pr ocess i s adopt ed c om m onl y.H ow e ver t he hi gh-ar seni c dus t f r om t he sm el t i ng pr ocedur e i s deal t w i t h by t he e l ect r i c -heat i ng ki l n or hydr om et al l ur gi ca l pr ocess.T he a t t ent i on i s pai d on t he hi gh-ar se ni c l ea d conver t er dust ,l ead sl i m e a nd secondar y zi nc oxi de i n t he f i el d of l e ad a nd zi nc sm el t i ng.K ey W or ds :removal of Arsenic,heavy metals smelting,high-arsenic lead1C u 冶炼过程中砷的脱除砷在铜冶炼过程中是有害元素,而且分布极广,几乎所有冶炼中间产品都含有砷,就杂质元素对电铜质量的影响程度来看,影响最大的是A s ,Sb 和B i ,它们的析出电位与C u 相近,极易在电解过程中与C u 同时析出,造成电铜中杂质含量过高。
铜冶炼过程中的砷的行为

火法炼铜中砷的流向图1.火法炼铜过程中砷的走向垣曲冶炼厂铜冶炼砷流向图如下图所示:阴极铜(铜砷固溶体)图1 砷的流向图砷在黄铜矿中主要以毒砂(FeAsS2)或硫化砷(AS2S3)形态存在[1]。
FeAsS2在850~900℃焙烧时受热迅速分解As4,As4在氧化气氛下发生如下反应:As4+3O2=2As2O3(1-1)硫化砷在氧化气氛下发生如下反应:2As2S3+9O2=2As2O3+6SO2(1-2)砷在铜的造锍熔炼过程中,氧化砷会和炉内的部分氧化物发生如下反应:As2O3+2SO3=As2O5+2SO2(1-3)As2O3+2Fe2O3=2As2O5+2FeO(1-4)As2O3+2Fe3O4=2As2O5+2SO2(1-5)As2O5在火法炼铜过程中,部分可与金属氧化物Cu2O、CuO、ZnO、、PbO和CaO等结合成稳定的砷酸盐(Cu3(AsO4)Z、Pb3(AsO4)2)从而进入阳极铜中[2];部分As2O5与Fe2O3生成FeAsO4进入炉渣;绝大多数中的As以三氧化砷的形态挥发进入烟气中,由于其可能使硫酸系统催化转换阶段的催化剂中毒,因此在进入硫酸转化阶段前对其进行回收。
砷的氧化物在烟气和阳极板中的分配系数与矿石成分、送氧速率以及炉温有关,因此控制好炉温对砷的脱除有着至关重要的作用。
2.铜电解精炼过程中砷的行为铜精矿经造锍熔炼—转炉吹炼—火法精炼后,As在阳极铜的形态主要以砷酸盐及砷锑铋混合物形式存在。
电解液中As含量与阳极板中砷含量、电解液成分和电解工艺条件有关。
铜电解精炼过程中,游离态的As主要以三价阳离子的形式进入电解液,进入电解液的As(℃)容易发生水解,反应方程式如下:As3++2H2O=HAsO2+3H+(1-3)As3++H2O=AsO++2H+(1-4)进入电解液中三价砷离子部分与Cu+离子生成Cu3As沉淀进入阳极泥中[3]。
以砷锑铋混合物形式存在的(Pb·Bi)2(As·Sb)4·O12随着阳极铜不断地溶解而逐渐显现与阳极表面,从而随着电解反应的继续进行,混合物中的大部分As被分解出来进入电解液中[4]。
试论有色冶炼烟气骤冷收砷技术

试论有色冶炼烟气骤冷收砷技术有色冶炼是指在冶金工业中,通过对有色金属矿石进行提炼加工,生产出各种有色金属的工艺过程。
在有色冶炼过程中,燃烧烟气所含有的有害物质,如砷、硫、铅等,对环境和人体健康造成了极大的威胁。
如何有效地处理有色冶炼烟气中的有害物质,成为了工业界和环保部门关注的焦点之一。
砷是有色冶炼烟气中的一种常见有害物质,针对烟气中的砷的处理技术备受研究和讨论。
在有色冶炼过程中,由于硫化矿石燃烧产生的硫化气体中常含有大量的砷,而烟气骤冷技术是一种处理这种烟气的有效方法。
烟气骤冷技术通过将高温烟气快速降温,使其中的粉尘和烟雾凝结,将其中的有害物质隔离出来。
而烟气骤冷收砷技术则是在此基础上,将骤冷后的烟气中富含的砷尽可能地收集和回收利用的工艺技术。
以下将从烟气骤冷原理、烟气中砷的特点以及烟气骤冷收砷技术的应用展开论述。
一、烟气骤冷原理烟气骤冷技术是通过将高温烟气快速降温来实现烟气中有害物质的凝结和分离。
具体而言,烟气骤冷技术通常是通过在烟气管道中设置冷却器或喷淋装置,将冷却介质如水或空气与高温烟气进行充分接触,使烟气温度迅速下降,从而使其中的颗粒物和烟雾凝结聚集。
在此过程中,也伴随着有害物质的凝结和分离,将有害物质隔离出来。
二、烟气中砷的特点在有色冶炼的烟气中,砷是一种常见的有害物质。
砷尤其难以处理的原因在于其化学性质的复杂性和毒性的高度。
一般而言,烟气中的砷以氧化物的形式存在,这种形式的砷在常温下比较容易挥发,使得其在烟气骤冷过程中难以快速凝结。
砷的毒性也使得在处理烟气时不能简单地将其排放到大气中,必须对砷进行有效地收集和处理,以免对环境和人体造成危害。
三、烟气骤冷收砷技术的应用随着对环境保护和资源利用要求的不断提高,烟气骤冷收砷技术在有色冶炼过程中的应用也日益成为了研究的热点。
烟气骤冷收砷技术主要通过两个步骤来实现对烟气中砷的有效处理,即砷的收集和砷的资源化利用。
砷的收集过程通常是在烟气骤冷过程中将砷凝结和固定在一定的介质中,例如布袋除尘器、静电除尘器等设备中,以减少砷的排放。
- 1、下载文档前请自行甄别文档内容的完整性,平台不提供额外的编辑、内容补充、找答案等附加服务。
- 2、"仅部分预览"的文档,不可在线预览部分如存在完整性等问题,可反馈申请退款(可完整预览的文档不适用该条件!)。
- 3、如文档侵犯您的权益,请联系客服反馈,我们会尽快为您处理(人工客服工作时间:9:00-18:30)。
基于过程强化的铜冶炼烟灰中砷选择性去除工艺及机理我国是世界第一大铜生产和消费国,在矿产资源开采、运输和选冶过程中,会产生大量含重金属固体废弃物,与开采及尾矿处理过程产生的烟尘相比,冶炼过程中产生的烟灰粒径较小(≤0.1μm)、比表面积较大,不仅可进行长距离的迁移造成区域性污染,而且易通过呼吸系统被人体吸收,从而对生态环境产生更大的危害;另外,有色金属矿物冶炼被IPCS认定为最重要的砷排放点源之一,据统计,全球大气中的砷约40%来自于冶炼过程,其中铜矿冶炼排放量占80%。
因此,从环境保护的角度,冶炼烟灰中砷的脱除及稳定化对于全球砷污染的控制具有积极意义。
从地球资源角度,冶炼烟尘除含有大量Cu、Pb、Zn等金属外,还含有大量稀贵金属,如In、Ge、Ga等,相对日渐贫乏的精矿品味,烟尘中的有价金属含量甚至超过很多富矿,可作为十分珍贵的金属资源。
然而,杂质砷的大量存在不仅增加资源化过程的负担,而且影响所产金属质量,已成为此类烟灰资源化的主要限制因素。
随着铜精矿进一步匮乏,冶炼过程中产生固体废弃物(炉渣、烟尘等)必将成为“再生铜”资源重要组成部分,而如何实现此类材料中有价金属高效资源化已成为湿法冶金领域重要研究课题之一。
目前,针对冶炼废弃物中有价金属元素资源化,大部分研究仍聚焦于有价金属元素湿法冶金技术的开发及机理,然而,与其他金属化合物相比,含As化合物热力学稳定性较低,易溶解于强酸、强碱等常用浸出剂。
冶炼烟灰常与铜矿等制样后返回熔炼炉,但随着铜矿资源的锐减,高砷铜由砷化合物具,矿的广泛使用必将导致冶炼烟灰中砷含量的持续增大.有较高反应活性,因此极易进入后续分离工序,致使阴极铜质量下降。
鉴于此,开发选择性浸出技术对烟灰进行脱砷预处理后再熔炼对其资源化具有积极意义。
NaOH-Na<sub>2</sub>S复合浸出体系理论上可选择性除砷,但仍存在药剂消耗量大、耗时长、浸出率低等缺点,并且随着烟灰中砷含量增高,这种缺点则越突出。
考虑到烟灰中砷和其它金属的价态和存在形式等是决定其浸出率的主要控制因素,因此,准确确定砷及其它金属在烟尘颗粒内部的赋存状态是开发强化浸出技术的首要问题;另外,仍缺乏从微观水平上NaOH、Na<sub>2</sub>S等药剂浸出砷各自作用机理及其协同作用机制。
为此,本文以铜冶炼澳炉烟灰为研究对象,在分析烟灰组成成分、物相、形貌分析所用烟灰ANC\BNC等特征基础上,对比研究了水洗预处理前后烟灰中有价金属元素(Cu、Zn、Bi、Sn、Mo、Sb、Ba、Al等)及有毒有害金属元素(Pb、Ni、As、Cd、Co等)浸出特性并构建了烟灰中重金属赋存状态与其浸出特性之间关系,揭示了溶解-沉控制机制、吸附-解吸控制机制、传质控制机制对其浸出作用规律各金属元素在不同pH条件下浸出机理及主要控制因素;为了开发符合清洁生产标准的高效脱砷技术,确定了微波、超声、球磨三种新型辅助浸出技术对As在NaOH-Na<sub>2</sub>S浸出体系分离浸出效率,并从微观尺度上揭示了NaOH、Na<sub>2</sub>S浸出砷作用机制。
论文的主要工作及结论如下:(1)从热力学角度构建了烟灰中重金属赋存状态与其浸出特性之间关系,揭示了溶解-沉控制机制、吸附-解吸控制机制、传质控制、Cl、K、Na、Fe、Al、As、Cd、Zn机制对其浸出作用规律。
烟灰中Zn等易被洗脱,存在可溶物相组分,其浸出主要其在烟灰颗粒径向分布相关,即受传质过程影响;酸性条件下,Pb不易浸出主要受PbSO<sub>4</sub>溶解度控制,而Cd、Mo则可吸附在铁\铝氧化物表面;烟灰中As浸出特性与其存在形态及吸附过程密切相关,其中As<sup>Ⅲ</sup>主要以As<sub>2</sub>O<sub>3</sub>状态存在,呈水溶性、易于在环境中迁移;而As<sup>V</sup>则主要与Cu、Zn形成复杂沉淀物;pH为3时残余物中As主要以砷酸盐态吸附在Fe氧化物表面,呈现典型的双齿双核(As-Fe=3.25?)、双齿单核(As-Fe=2.85?)As-Fe化合物构型,在2.85?处不存在Fe原子,则表明溶液中游离砷酸根再吸附过程的存在;而pH为5时的As主要吸附在Al氧化物表面,在3.19?处出现As-Al原子间距,与溶液中Al氧化物再沉淀过程密切相关。
(2)确定了微波辅助条件下A s在N aO H-N a<sub>2</sub>S 浸出体系中浸出率及速率的主要影响因素及控制步骤,从微观结构角度揭示了微波辅助下A s选择性浸出机制。
与传统水浴方式相比,微波可显著提高烟灰中As浸出(最终As浸出率提高14%),而且可将浸出时间缩短为其1/9,因此,该方法可实现常压下Cu和As高效、快速、选择性分离。
正交试验结果表明,烟灰中重金属元素浸出率在微波辅助NaOH-Na<sub>2</sub>S浸出体系中差别较大,其中As浸出率最高,主要受浸出剂浓度影响;Cu、Cd、Zn亦有部分浸出,但其主要控制因素不尽相同,Cd、Pb浸出率除与浸出剂浓度密切相关外,亦受液固比、反应温度影响,而Zn浸出率则主要由液固比决定;Cu浸出率较浸出率主要As用量是该浸出体系中NaOH受各因素影响较小。
,平稳.控制因素,其浸出率随着转速提升显著增大,当其用量由M<sub>NaOH:Ash</sub>=0.1:1增至0.3:1时,As浸出率显著增大,最大可达100%,但过大则不利于As与Zn的分离浸出。
微波强化Na OH-Na<sub>2</sub>S浸出体系实现As分离浸出的最优工艺条件为:M<sub>NaOH:Ash</sub>=0.3:1,液固比=20:1,M<sub>NaOH:Ash</sub>=0.4:1,反应温度=80℃,反应时间15min。
SEM结果表明,微波后烟灰颗粒表面出现“裂解”,增加表面反应活性;XANES及EXAFS结果表明,微波有助于As<sup>Ⅲ</sup>氧化为As<sup>V</sup>,且与Zn氧化物共吸附在Al氧化物形成复杂共沉化合物的As<sup>V</sup>控制其浸出;两种浸出剂对As浸出具有协同作用,足量Na OH可促使吸附在铝氧化物表面的双齿单核、双齿双核内层吸附物上As<sup>V</sup>解吸;而Na<sub>2</sub>S则通过与Fe形成溶解度极低的硫化物沉淀,从而抑制As<sup>V</sup>在铁氧化表面吸附。
(3)确定了超声辅助条件下As在NaOH-Na<sub>2</sub>S浸出体系中浸出率及速率的主要影响因素及控制步骤,从微观结构角度揭示了超声辅助下As选择性浸出机制。
与传统水浴方式相比,超声场不仅可提高烟灰中As浸出率,而且可将反应时间缩短4/5;浸出后残余固体物中As含量降至0.57%,Cu含量升至2.34%,与水浴碱浸后所得固体沉淀物相比,其砷含量降了0.3%,Cu 含量增加了0.2%,有利于此类高砷、低铜烟灰进一步资源化。
正交及单因素试验结果表明,烟灰中重金属元素浸出率在超声场辅助受,浸出率最高As其中,浸出体系中差别较大NaOH-Na<sub>2</sub>S.NaOH用量影响较大,但过高NaOH浓度致使Zn、Pb浸出率升高,从而不利于As分离浸出;Na<sub>2</sub>S用量是实现As与Pb分离浸出主要影响因素;而液固比、温度则影响浸出速率,浸出达平衡所需时间随着液固比增加而延长,随着温度升高而减少。
根据As与其他重金属分离浸出效果,超声场辅助NaOH-Na<sub>2</sub>S浸出体系实现As 分离浸出的最优工艺条件为:M<sub>NaOH:Ash</sub>=0.3:1,M<sub>Na<sub>2</sub>S:Ash</su b>=0.4:1,液固比20 mL/g,超声功率80 W,搅拌速率400 r/min,反应时间=15 min,反应温度=60℃。
动力学研究表明,超声场中As浸出速率仅在较低温度下受内扩散及界面传质的混合控制,且与水浴浸出体系不同,其不易受界面化学反应速率控制。
SEM-EDS结果表明,超声场对烟灰具有分散作用,促使烟灰颗粒由密实状变为松散状,从而减小烟灰颗粒粒径并增大其比表面积,进一步促进液-固浸出体系中烟灰颗粒表面空化作用;XRD结果表明,超声场并未改变NaOH-Na<sub>2</sub>S复合浸出体系化学反应本质,在水浴及超声浸出体系中,烟灰中PbSO<sub>4</sub>、ZnSO<sub>4</sub>等组分与NaOH、Na<sub>2</sub>S反应均生成PbS、ZnS、ZnO等化合物;XPS结果表明,在空气中超声场作用可实现烟灰中部分As<sup>Ⅲ</sup>àAs<sup>V</sup>的价态转化,对于砷在NaOH溶液中浸出的重要的热力学意义。
(4)确定了球磨对A s在N aO H-N a2S浸出体系中浸出率及速率的主要影响因素,从微观结构角度揭示了其选择性浸出A s浸出(最终As球磨可显著提高烟灰中,机制。
与传统水浴方式相比.As浸出率提高11%),并减少浸出残余物中As含量(仅余0.5%),与原烟灰相比重金属含量减少了5.04%,可见,该方法可实现此类烟灰中As选择性浸出,其浸出主要受转速及料球比影响,随着转速提升显著增大,当转速由100 r/min增至350r/min时,增加了49%,而后,则随着转速增加呈下降趋势,Zn浸出率随着液固比增加而减小,而Pb则呈相反趋势;当液固比为20:1,As浸出率最大而Zn、Pb浸出率最低;As 浸出率随着料球比增加呈先上升后下降的趋势,当料球比由0.2升至0.6时,由77%增至85%,进一步增加料球比,砷的浸出率显著降低,当料球比为1.2时,砷的浸出率大幅降至46%,在实际应用中应合理分配投料量与磨球体积比;As浸出率随着反应时间延长逐渐增大,反应60min后,砷的浸出率基本趋于稳定。