低氮分级燃烧技术介绍
火力发电锅炉低氮燃烧技术介绍

91.20% 91.45% 750-800
190-255
表5-6 #3炉空预器出口氮氧化物含量
•2011.5.28 •测点
•#3炉301.72MW •空预器出口A侧 •空预器出口B侧
•NOx(mg/Nm3)
•240.64
•242.58
•NOx(mg/Nm3)
•241.61
通过现场考核试验结果为A侧空预器出口NOx排放浓度为240.64 mg/Nm3,B侧空预器出口NOx排放浓度为242.58 mg/Nm3,空预器出 口平均NOx排放浓度为241.61 mg/Nm3,NOx排放浓度低于300 mg/Nm3。
发份燃烧率;
2. 在燃烧的初始阶段除了提供适量的氧以供稳定燃烧所需 要以外,尽量维持一个较低氧量水平的区域,以最大限 度地减少NOx生成;
3. 优化燃料富集区域的温度和燃料在此区域的驻留时间, 以最大限度地减少NOx生成;
4. 增加煤焦粒子在燃料富集区域的驻留时间,以减少煤焦 粒子中氮氧化物释出形成NOx的可能;
032 057p
NOx排放改造目标
烟煤和褐煤 NOx排放值控制在 150~350
mg/Nm3
贫煤
NOx排放值控制在 350~500 mg/Nm3
无烟煤 NOx排放值控制在 700-800 mg/Nm3
特别需要强调的是:对于比较好的烟煤如神华烟煤、 准东烟煤等煤种通过燃烧系统的低NOx改造,NOx排 放值即可控制在 200 mg/Nm3以下。
燃烧器改造范围
•主燃烧器更换为 区段控制低氮燃烧技 术的低NOx煤粉燃烧器; •增设燃尽风燃烧器; •增设燃尽风道、燃尽风箱、风箱挡板、 挡板执行机构、风量测量装置等; •设置燃尽风水冷壁喷口管屏; •配套平台扶梯的增加或改造; •其他配套设备;
低氮燃烧技术在蒲洲电厂的改造应用

低氮燃烧技术在蒲洲电厂的改造应用摘要:伴随我国工业化的快速发展,nox的排放总量也呈逐年上升的趋势,如此便造成了环境污染的不断加剧,因此有效控制nox 的排放量已势在必行。
为此,在低氮燃烧技术的基础上,通过对蒲洲发电锅炉设备现状的概述,阐述了低氮燃烧技术在蒲洲发电锅炉设备改造中的应用,并提出了相应的对策。
关键词:低氮燃烧技术;蒲州电厂;改造;应用为了我国的可持续发展,有效保护环境,控制氮氧化合物的排放量,提高其排放标准已是大势所趋,尤其是近年来我国兴建的多家大型火力发电企业,已经成改造的关键。
鉴于当前众多发电企业在炉燃料系统中所使用的先进的氮燃烧技术现状,本文以蒲洲发电锅炉改造为例,阐述了其应用价值和注意事项,以供参考。
1 低氮燃烧技术介绍低氮燃烧技术,即保证燃烧中氧化而成的氮化合物较低的技术,低nox燃烧技术投资低,且有较好的效果与运行经验,特别是低氮氧化物燃烧器与空气分级燃烧的联合使用,效果更佳;烟气脱硝技术中scr和sncr具有较多的商业化运行业绩,且脱硝效率较高。
一般,由燃料中氮的热分解温度低于煤粉燃烧温度,在600-800℃时就会生成燃料型。
在生成燃料型nox过程中,首先是含有氮的有机化合物热裂解产生n,cn,hcn和等中间产物基团,然后再氧化成nox。
由于煤的燃烧过程由挥发份燃烧和焦炭燃烧两个阶段组成,故燃料型的形成也由气相氮的氧化(挥发份)和焦炭中剩余氮的氧化(焦炭)两部分组成。
主要影响因素燃料中的氮和挥发份含量、温度、过剩空气系数等。
低氮燃烧技术中可分为3个关键点:1、主燃烧器区域的过量空气系数的选择,要取得一定的nox排放值,对不同容量大小和燃用不同煤质的机组,主燃烧器区域的过量空气系数会有所不同,但都有一个最佳的过量空气系数值。
2、sofa燃烧器离主燃烧器区域的距离,nox的生成量与sofa离主燃烧区域的距离成反比关系,但sofa离主燃烧区的距离越大,锅炉飞灰含碳量会有一定程度的增加。
低氮燃烧介绍
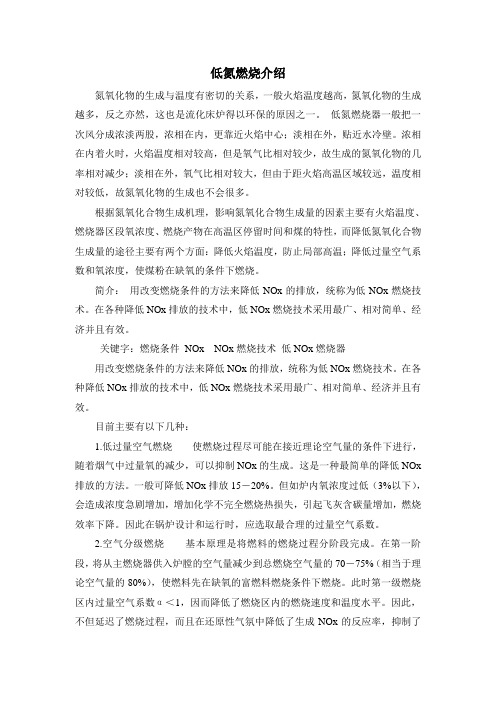
低氮燃烧介绍氮氧化物的生成与温度有密切的关系,一般火焰温度越高,氮氧化物的生成越多,反之亦然,这也是流化床炉得以环保的原因之一。
低氮燃烧器一般把一次风分成浓淡两股,浓相在内,更靠近火焰中心;淡相在外,贴近水冷壁。
浓相在内着火时,火焰温度相对较高,但是氧气比相对较少,故生成的氮氧化物的几率相对减少;淡相在外,氧气比相对较大,但由于距火焰高温区域较远,温度相对较低,故氮氧化物的生成也不会很多。
根据氮氧化合物生成机理,影响氮氧化合物生成量的因素主要有火焰温度、燃烧器区段氧浓度、燃烧产物在高温区停留时间和煤的特性,而降低氮氧化合物生成量的途径主要有两个方面:降低火焰温度,防止局部高温;降低过量空气系数和氧浓度,使煤粉在缺氧的条件下燃烧。
简介:用改变燃烧条件的方法来降低NOx的排放,统称为低NOx燃烧技术。
在各种降低NOx排放的技术中,低NOx燃烧技术采用最广、相对简单、经济并且有效。
关键字:燃烧条件NOx NOx燃烧技术低NOx燃烧器用改变燃烧条件的方法来降低NOx的排放,统称为低NOx燃烧技术。
在各种降低NOx排放的技术中,低NOx燃烧技术采用最广、相对简单、经济并且有效。
目前主要有以下几种:1.低过量空气燃烧使燃烧过程尽可能在接近理论空气量的条件下进行,随着烟气中过量氧的减少,可以抑制NOx的生成。
这是一种最简单的降低NOx 排放的方法。
一般可降低NOx排放15-20%。
但如炉内氧浓度过低(3%以下),会造成浓度急剧增加,增加化学不完全燃烧热损失,引起飞灰含碳量增加,燃烧效率下降。
因此在锅炉设计和运行时,应选取最合理的过量空气系数。
2.空气分级燃烧基本原理是将燃料的燃烧过程分阶段完成。
在第一阶段,将从主燃烧器供入炉膛的空气量减少到总燃烧空气量的70-75%(相当于理论空气量的80%),使燃料先在缺氧的富燃料燃烧条件下燃烧。
此时第一级燃烧区内过量空气系数α<1,因而降低了燃烧区内的燃烧速度和温度水平。
低NOx燃烧技术

欧洲标准:200 mg/m3 ,挥发分较高、发热量高的商品煤。
美国标准: 180 mg/m3,全部挥发分较高的烟煤; 日本标准: 150 mg/m3,基本是燃烧原煤(包括洗块、洗中、洗末) 中国标准: 200 mg/m3,2003年以前投产的锅炉。 100 mg/m3,2003年以后投产的锅炉。 劣质煤(洗中煤、洗末煤)挥发分低、灰分高、发热量低、高水 分的煤种。
4.2 锅炉过量空气系数的影响 当空气不分级燃烧时,降低过量空气系数,在一定程度上会起到限制 反应区内氧浓度的目的,因而对热力型NOx和燃料型NOx的生成都有明显 的控制作用,采用这种方法可使NOx生成量降低15%~20%。但是CO浓度 会随之增加,燃烧效率下降。当采用空气分级时,可以有效NOx排放量, 随着一次风量减少,二次风量增加,N被氧化的速度降低,NOx排放量也 相应下降。
1.3 美国洛杉机光化学烟雾
• 美国光化学烟雾对农业和林业的危害曾波及27个州。 • 1952年美国洛杉矶发生光化学烟雾,附近农作物一夜之间严重受害;6.5 万公顷的森林,29%严重受害,33%中等受害,其余38%也受轻度损害。
2
序号
“十二五”国家主要污染物总量控制(GB13223-2011)
污染物项目 烟尘 全部 新建锅炉 二氧化硫 适用条件 限值 30 100 200(1) 200 400(1) 100 200(2) 0.03 30 100 200 污染物排放监控位置
挥发分N/燃料N,%
时间,ms
影响NOx生成的主要因素是: 一、炉膛温度水平,炉膛温度越高,NOx排放量越大; 二、高温燃烧区的含氧量,过量空气系数越高,NOx排放量越大。 因此在低NOx燃烧器设计时,在高温区低氧、在相对低温区过氧的燃烧方 式。
FIR烟气内循环降氮技术讲解

FIR烟气内循环降氮技术讲解突破研发烟气内循环降氮技术,低氮50mg无需烟气外循环,达到国家环保验收标准。
低氮30mg标准,只需将烟气量3%与空气混合后送至燃烧室助燃,NOx(氮氧化物)达到国家排放标准30mg/每立方米。
一、分级燃烧:通过高压空气和燃气相混合,实现燃烧器在炉内出口处形成分级火焰,减少热力型NOx的形成;二、内循环(FIR):通过分级燃烧设计的分级火焰的燃烧速度不同,高速火焰带动低速火焰形成空气的内部卷吸,形成内部空气循环,实现内循环降氮技术NOx排放低于国家标准。
三、通过燃气和高压空气的直角相交,进行充分混合并喷射到1000℃的区域,来减少氮氧化物的生成,达到国家NOx排放标准。
四、无需连接外部烟气管道,没有烟气冷凝水对锅炉的腐蚀,彻底解决了烟气冷凝水对锅炉燃烧器本体的腐蚀问题,延长了锅炉燃烧器使用寿命。
烟气内循环氮燃烧器优点:1、不使用FGR,高温烟气在炉膛停留时间长,有利辐射放热,效率提升0.5~2%以上,节能效益好。
大容量锅炉(20吨以上)不使用烟气再循环风机,节省电能消耗。
2、不使用FGR,相对FGR低氮改造方式出力提升15~20%以上,经济效益好。
3、不使用FGR,无需连接外部烟气循环管道,安装简便容易,没有烟气冷凝水对锅炉的腐蚀,解决了烟气冷凝水对锅炉本体的腐蚀问题,延长锅炉寿命,经济效益好。
4、烟气内循环,炉膛内烟气总量没有增加,没有振动;不采用烟气外循环方式,没有多台锅炉共用烟道时烟气部分再循环对其他锅炉排烟的干扰问题,燃烧稳定性好。
5、不用烟气外循环,没有震动,无须担心烟气冷凝水对燃烧器燃烧稳定性的影响,安全效益高。
6、不采用烟气外循环方式,不会出现环保检查时使用FGR 功能,平时关掉FGR功能超标准排放的问题,社会效益好。
7、采用德国西门子燃烧控制系统,全电子比例调节方式,可以实现25%~100%范围内的无级调节。
低氮燃烧技术原理

低氮燃烧技术原理
低氮燃烧技术,是指在燃烧过程中将NOx的产生控制在一定范围内的一种技术。
对于燃煤锅炉,低氮燃烧主要是指减少燃料中的氮化合物的生成量。
燃烧过程中,生成的NOx有两种形态:一种是NOX,一种是氮氧化物。
当燃烧器中的空气过剩系数与燃料种类、负荷、煤种等因素相匹配时,NOX就会很低;当燃烧过程中存在高温区时,温度较高时,燃料中氮化合物被氧化成氮氧化氮,这样NOX就会急剧升高;当燃烧过程中存在还原性气氛时,燃料中的氮氧化合物被还原成氮气;当燃烧器结构设计不合理,空气过剩系数过大或燃料种类与负荷不匹配时,燃烧器中的氧气过量系数过小,这时燃烧反应生成的氮氧会以NOX形式向空气中逃逸。
为减少NOX排放,国内外均采用降低燃料氮化合物生成量的方法来控制锅炉的NOx排放。
主要措施是优化燃烧过程、改进空气系统及改善燃烧条件等。
1.合理选择燃料及负荷
合理选择燃料是控制锅炉NOx生成量的有效途径。
—— 1 —1 —。
低氮燃烧的脱氮效率-概述说明以及解释

低氮燃烧的脱氮效率-概述说明以及解释1.引言1.1 概述概述部分的内容可以是以下内容之一:1.1概述低氮燃烧技术是在保证燃烧过程中能量利用效率的同时,降低燃料燃烧产生的氮氧化物(NOx)排放的一种有效手段。
随着全球环境问题的日益突出,尤其是大气污染对人类健康和环境的危害越来越严重,低氮燃烧技术的研究与应用日益受到重视。
本文将重点探讨低氮燃烧的脱氮效率。
首先,将对低氮燃烧技术的原理进行简要介绍,包括燃料的燃烧过程、NOx的生成机理等。
其次,将详细阐述低氮燃烧技术的常用手段,包括气体调节、燃烧调控、燃烧器结构优化等。
在本文的结论部分,将对低氮燃烧的脱氮效率进行总结,并探讨未来低氮燃烧技术的发展前景。
通过对现有低氮燃烧技术的分析与比较,可以为进一步提高脱氮效率提供一定的指导和参考。
通过深入研究低氮燃烧技术的相关原理和应用,我们可以进一步了解如何优化燃烧过程以降低NOx排放,从而减少环境污染,保护人类健康。
此外,对未来低氮燃烧技术的展望也将为相关研究者提供前进方向,推动低氮燃烧技术的发展和应用。
1.2 文章结构文章结构部分的内容如下所示:文章结构本文主要包含以下几个方面内容:引言、正文和结论。
1. 引言引言部分将对低氮燃烧的脱氮效率进行概述,并介绍本文的目的和结构。
2. 正文正文将详细介绍低氮燃烧的原理和技术手段。
2.1 低氮燃烧的原理这一部分将对低氮燃烧的基本原理进行阐述。
包括通过调整燃烧方式、优化燃烧参数以及采用先进的燃烧技术等手段,降低燃烧过程中产生的氮氧化物排放。
2.2 低氮燃烧的技术手段这一部分将介绍低氮燃烧中常用的技术手段。
包括燃烧室设计优化、燃烧系统调节、燃料改进以及污染物后处理等多种手段,用于提高燃烧效率和降低氮氧化物排放。
3. 结论结论部分将对低氮燃烧的脱氮效率进行总结,并展望低氮燃烧的未来发展。
3.1 低氮燃烧的脱氮效率总结这一部分将对低氮燃烧的脱氮效率进行总结。
综合各种低氮燃烧技术手段的优劣,评估其在降低氮氧化物排放方面的效果,并提出相应的建议和改进措施。
燃气、燃油锅炉低氮治理技术

燃气、燃油锅炉低氮治理技术燃气锅炉由于天然气的理化特性导致其主要的污染物为氮氧化物。
目前主要通过改进燃烧技术来降低燃烧过程中NOx的生成与排放,其主要途径有:降低燃料周围的氧浓度,减小炉内过剩空气系数,降低炉内空气总量,或减小一次风量及挥发分燃尽前燃料与二次风的混和,降低着火区段的氧浓度;在氧浓度较低的条件下,维持足够的停留时间,抑制燃料中的氮生成NOx,同时还原分解已生成的NOx;在空气过剩的条件下,降低燃烧温度,减少热力型NOx的生成。
低氮燃烧技术一般可使NOx的排放量降低30%~60%。
01丨低氮燃烧器技术NOx生成机理简要总结如下:1.热力型NOx(ThermalNOx),在高温烟气(大于1400℃后)显著增加,N元素来源于空气中的N2;2.快速型NOx(Promp),N元素来源于助燃气体中的N2,生成量主要受氧气浓度和燃料与氧气化学当量比影响;3.燃料型NOx(FuelNOx),N元素来源于燃料中的氮成分,其生成主要受燃料中的氮成分和助燃气体中的氧气浓度影响。
下图综合展示了NOx的来源于决定因素,低氮燃气燃烧器的技术原理则围绕着以下的核心理念不断地发展和演变。
△三种类型NOx的生成源及主要影响因素如上图所示,NOx的生成主要由烟气温度和氧气浓度决定。
因此,当前工业中的燃气低氮燃烧技术的一个重要控制方式就是降低气体燃料燃烧过程中的烟气温度。
降低烟气温度的核心指导原则:(1)在时间将热量释放的峰值降低,降低化学反应速率、延长反应时间;(2)在空间上将热量分散在更广阔的空间。
针对以上指导原则,在燃气燃烧器的设计及布置方案中有若干具体的实施措施:(1)燃料分级:有烟气内循环、燃气和空气高速差配合等类型;(2)空气分级:有燃烧器喷嘴的空气分级和炉膛空间上的空气分级;(3)烟气再循环:有传统烟气再循环和O2/CO2烟气再循环。
燃料分级,即燃料分成若干股注入较大的燃烧空间中进行燃烧,释放的热量被较大空间内的烟气吸收,从而使烟气的温度得到降低,该技术也称为“火焰分割”。
- 1、下载文档前请自行甄别文档内容的完整性,平台不提供额外的编辑、内容补充、找答案等附加服务。
- 2、"仅部分预览"的文档,不可在线预览部分如存在完整性等问题,可反馈申请退款(可完整预览的文档不适用该条件!)。
- 3、如文档侵犯您的权益,请联系客服反馈,我们会尽快为您处理(人工客服工作时间:9:00-18:30)。
低氮分级燃烧技术 一.低NOx优化燃烧技术的分类及比较 为了实现清洁燃烧,目前降低燃烧中NO、排放污染的技术措施可分为两大类:一类是炉内脱氮,另一类是尾部脱氮。
1.1炉内脱氮 炉内脱氮就是采用各种燃烧技术手段来控制燃烧过程中NOx的生成,又称低NOx燃烧技术,下表给出了现有几种典型炉内脱氮技术的比较。 表2 技术名称 效果 优点 缺点
低氧燃烧 根据原来运行条件,最多降低20% 投资最少 导致飞灰含碳量增加
降低投入运行的燃烧器数目 15%—30% 投资低,易于锅炉改装 有引起炉内腐蚀和结渣的可能,并导致飞灰含碳量增加 空气分级燃烧(OFA) 最多30% 投资低 并不是对所有炉膛都适用,有可能引起炉内腐蚀和结渣,并降低燃烧效率 低NOx燃烧器 与空气分级燃烧相结合时可达60% 用于新的和改装的锅炉,中等投资,有运行经验 结构比常规燃烧器复杂.
烟气再循环(FGR) 最多20% 能改善混合燃烧,中等投资 增加再循环风机,使用不广泛 燃料分级(再燃) 达到50% 适用于新的和改造现有锅炉,可减少已形成的NOX,中等投资 可能需要增加第二种燃料,可能导致飞灰含碳量增加,运行经验较少 1.2尾部脱氮 尾部脱氮又称烟气净化技术,即把尾部烟气中已经生成的氮氧化物还原或吸附,从而降低NOx排放。烟气脱氮的处理方法可分为:催化还原法、液体吸收法和吸附法三大类。 催化还原法是在催化剂作用下,利用还原剂将NOx还原为无害的N2。这种方法虽然投资和运转费用高,且需消耗氨和燃料,但由于对NOx效率很高,设备紧凑,故在国外得到了广泛应用,催化还原法可分为选择性非催化还原法和选择性催化还原法相比,设备简单、运转资金少,是一种有吸引力的技术。 液体吸收法是用水或者其他溶液吸收烟气中的NOx。该法工艺简单,能够以硝酸盐等形式回收N进行综合利用,但是吸收效率不高。 吸附法是用吸附剂对烟气中的NOx进行吸附,然后在一定条件下使被吸附的NOx脱附回收,同时吸附剂再生。此法的NOx脱除率非常高,并且能回收利用。但一次性投资很高。 炉内脱氮与尾部脱氮相比,具有应用广泛、结构简单、经济有效等优点。表2中各种低NOx燃烧技术是降低燃煤锅炉NOx排放最主要也是比较成熟的技术措施。一般情况下,这些措施最多能达到50%的脱除率。当要进一步提高脱除率时,就要考虑采用尾部烟气脱氮的技术措施,SCR和SNCR法能大幅度地把NOx
排放量降低到200mg/m3,但它的设备昂贵、运行费用很高。
根据我国发展现状和当前经济实力还不雄厚的国情,以及相对宽松的国家标准CB13223一2003,在今后相当长一段时间内,我国更适合发展投资少、效果也比较显著的炉内脱氮技术。即使采用烟气净化技术,同时采用低NOx燃煤技术来控制燃烧过程NOx的产生,以尽可能降低化设备的运行和维护费用。 表2中各炉内脱氮技术又以燃料分级效率较高。燃料再燃技术是有效的降低NOx排放的措施,早在1980年日本的三菱公司就将天然气再燃技术应用于实际锅炉,NOx排放减少50%以上。美国能源部的“洁净煤技术”计划也包括再燃技术,其示范项目分别采用煤或天然气作为再燃燃料,NOx排放减少30%到70%。在日本、美国、欧洲再燃技术大量应用于新建电站锅炉和已有电站锅炉的改造,在商业运行中取得良好的环境效益和经济效益。在我国燃料再燃烧技术研究和应用起步较晚,主要是因为我国过去对环保的要求较低,另一方面则是出于技术经 济上的考虑。进入90年代,我国严重缺电局面开始缓和,大气污染日益严重,1994年全国85个大中城市中NOx超标的城市就有30个,占35%。1998年对全国322个省控城市量监测结果分析,NOx年日平均值范围在0.006一0.152mg/m3,全国平均为0.037mg/m3,治理大气污染成为十分迫切的任务。随着环保要求的不断提高,研究适应我国国情的低成本的再燃低NOx燃烧技术具有良好的前景。 二.分级燃烧原理 抑制NOx 的生成可采取的措施有: 1.降低锅炉峰值温度,将燃烧区的煤粉量降低。 2.降低氧浓度(即降低过量空气系数),将部分二次风管堵住。 3.由于要保证锅炉的出力,可将部分煤粉和空气从锅炉上部投入,这样就控制了燃烧火焰中心区域助燃空气的数量,缩短燃烧产物在高温火焰区的停留时间,避免了高温和高氧浓度的同时存在。 4.在炉膛中设立再燃区,利用在主燃区中燃烧生成的烃根CHi和未完全燃烧产物CO、H2、C和CnHm等,将NO的还原成N2。 如示意图1所示。 图1 分级燃烧原理图 将80%~85%的燃料送入主燃区,燃料在主燃区燃烧生成NOx ,15%~20%的燃料送入再燃区,再燃区过量空气系数小于1.0(α<1.0),具有很强的还原性气氛,在主燃区生成的NOx被还原;再燃区不仅能够还原已经生成的NOx,而且还抑制了新的NOx生成;在燃尽区供给一定量的空气(称为燃尽风),保证从再燃区出来的未完全燃烧产物燃尽。根据超细煤粉再燃低NOx燃烧技术原理和前期的研究结果,将整个炉膛燃烧区划分为主燃区、再燃区和燃尽区。各区域出口过量空气系数目标值为:主燃区出口α=0.9~1.0,再燃区出口α=0.8~0.9,燃尽区出口α=1.167。锅炉主、再燃区均以锅炉实际燃用煤为燃料,主燃区燃烧80%~90%的浓煤粉,再燃区喷入10%~20%的超细化煤粉作为再燃燃料。 超细煤粉是指粒径小于43μm的煤粉,根据有关研究,这个尺度的煤粉有与雾化燃油相同的燃烧特性。在工程应用中,可以用浓淡分离器从常规煤粉中分离。
燃料+空气→NO CO+O2→CO2 NO+CHi→N2等 燃料+空气→NO 燃尽区 α=1.167 再燃区 α=0.8~0.9 主燃区 α=0.9~1 燃尽风 再燃燃料 一次燃料 一、二次风 三.分级燃烧的技术特点 1.优异的低负荷不投油稳燃能力。 该设计的理念之一是建立煤粉早期浓缩着火,为此公司开发了高效浓淡分离装置、两层浓浓、淡淡一次风合用一层一次风室,中间完全分隔的一次风煤粉燃烧器、周界齿形的煤粉燃烧喷嘴,同时一次风煤粉反切射流技术,极大地提高锅炉的不投油低负荷稳燃能力。根据设计和校核煤种的着火特性,选用合适的煤粉浓缩比、煤粉喷嘴、和浓一次风反切角度,在煤种允许的变化范围内确保煤粉及时着火稳燃,并且燃烧器状态良好。 2.优异的煤粉高效燃尽、防结渣及高温腐蚀的特性 首先,高浓度煤粉的早期着火提高了燃烧效率;同时通过在炉膛的不同高度布置底部二次风、偏置二次风、上部OFA 和空间分离的S-OFA,将炉膛分成三个相对独立的部分:燃烧区,NOx还原区和燃尽区。在每个区域合理的控制各自的过量空气系数,这种改进的空气分级方法通过优化每个区域的过量空气系数,在有效降低NOx 排放的同时能最大限度地提高燃烧效率;第三,通过燃烧器区域的刚性偏置二次风,在炉膛壁面附近形成低煤粉浓度的氧化区,避免了炉膛结渣和高温腐蚀的发生。第四,本技术将煤粉浓淡分离,所有浓一次风煤粉都布置在了燃烧区域下部,相当于提高了煤粉燃尽高度及NOx还原高度,有利于提高锅炉燃烧效率及降低NOx的排放水平。 3.超低的NOx燃烧排放特性 分级燃烧技术的最突出特点是超低NOx燃烧特性,在保证稳燃高效的前提下,通过采用高效浓淡分离技术、空间燃烧分级技术、一次风逆向射流等手段不仅保证煤粉早着火,稳定燃烧,通过采用上下、左右可调燃尽风喷口技术,实现炉内按需供风和降低炉膛出口烟温偏差,更重要的是实现了锅炉超低NOx的燃烧排放。 4.优异的小油点火稳燃能力。 该设计采用公司经过了大量工业应用的煤粉气化小油燃烧点火技术,在第一层的浓、淡一次风的煤粉燃烧器中布置了小油点火装置,可以在锅炉冷态以及热态启动时完全不投入大油枪,极大地降低了锅炉的启动和在更低负荷下的稳燃油 耗。 5.分离燃尽风SOAF还具有较好的降低炉膛出口烟温偏差特性 采用空间空气的分级燃烧技术不仅是降低NOx排放、提高煤粉燃尽率的重要手段,同时采用对SOFA的水平摆动调整,更有助于降低炉膛出口两侧烟温偏差而导致的过热器及再热器壁温偏差的作用。 6. 五大技术特点保证锅炉改造后大幅提高锅炉运行经济性 CEE超低NOx燃烧技术无任何运行成本,它不仅实现锅炉的超低NOx排放,同时实现了锅炉高效稳燃、防结渣、防高温腐蚀、低负荷不投油稳燃、锅炉小油点火稳燃的特性,扩大了锅炉的煤种适应性等功能,在工业化应用中取得了优异的效果。 四、改造方案(烟煤) 下面以典型的300MW四角切圆燃烧锅炉为例介绍基于分级燃烧技术的CEE低氮燃烧技术: 整个燃烧系统的各喷嘴布置示意见图1所示。 图2 CEE燃烧技术的炉膛纵向空间 燃烧组织示意图 图1. 锅炉燃烧系统各喷嘴布置示 图3 CEE燃烧技术的一室两层浓一次风煤粉燃烧器示意图 图4 CEE主燃烧器区域炉膛水平截面燃烧组织示意图 首先,采用在各煤粉管道中布置的的旋风分离器对一次风煤粉进行浓淡分离,两个浓浓、淡淡的一次风煤粉进入一个一次风室,构成一个一室两层的煤粉燃烧器。从下往上,一次风煤粉喷嘴依次为:两室四层浓浓一次风、一层浓淡一次风、两层淡淡一次风,见图1所示。 第二,将燃烧区域分成上下三个区域,下部为由两层四室浓一次风构成的主燃烧稳燃区,中部为两层四室的淡一次风构成的NOx还原区,顶部为由在主燃烧区上部布置的两层分离SOFA构成的燃尽区,见图2所示。 第三,在炉膛燃烧区域的水平截面,一次风喷嘴射流反切,在每层浓一次风喷嘴上部布置一层刚性的偏置二次风,这样构成了在炉膛中央的高浓度煤粉、高温、低氧的主燃烧区,在炉膛壁面附近构成了低煤粉浓度、低温、高过量空气系数的氧化区;同时SOFA燃尽风喷嘴反切,并可水平、上下摆动,调节炉膛出口火焰温度和避免炉膛出口两侧烟温偏差,见图2、图4、图5所示。 第四,一次风煤粉燃烧器采用齿形低NOx煤粉喷嘴,见图6所示。该结构类似于WR宽调节比燃烧器,但采用了本公司的摆动配合结构,减少了煤粉喷嘴的周界风设计,而在煤粉喷嘴上下两侧各增加了一层二次风,见图2所示。 第五,在最下层的浓一次风和淡一次风燃烧器布置小油点火装置,以保证冷热态锅炉启动的少油点火启动,以及实现锅炉非正常的超低负荷(低于的30%MCR)的节油稳燃。 五、CEE超低NOx燃烧系统技术特点 CEE技术的最突出特点是超低NOx燃烧特性,在保证稳燃高效的前提下,通过采用高效浓淡分离技术、空间燃烧分级技术、一次风逆向射流等手段不仅保证煤粉早着火,稳定燃烧,通过采用上下、左右可调燃尽风喷口技术,实现炉内按需供风和降低炉膛出口烟温偏差,更重要的是实现了锅炉超低NOx的燃烧排放。它包含了两大核心技术特点: (一)、纵向空间的三区分布 在距主燃烧器区顶部约3米以上,布布置了三层SOFA燃尽风,约占总风量的25%左右,它首先保证了主燃烧器区与高位燃尽风之间有足够的还原高度,是降低燃料型及热力型NOx的主要手段;同时,所有燃尽风喷口均设计为可上下左右摆动喷口,实现按需靶向送风及调整锅炉出口烟温偏差。