高速列车用6065A铝合金超高周疲劳性能试验研究.
高速列车轮对不同工况下应力及疲劳强度分析

高速列车轮对不同工况下应力及疲劳强度分析高速列车轮对不同工况下应力及疲劳强度分析一、引言随着高速铁路的发展,高速列车成为人们出行的重要方式之一。
高速列车的安全和可靠性是保障乘客出行的重要因素。
在运行过程中,轮对是高速列车中非常重要的部件之一,它承受着列车的重量和运行时产生的应力。
轮对在运行过程中面临着各种工况,包括加速、减速、制动、过弯等。
不同的工况会对轮对产生不同的应力,从而可能导致疲劳破坏。
因此,对高速列车轮对在不同工况下应力及疲劳强度进行分析,对于确保列车的安全和可靠运行具有重要意义。
二、高速列车轮对应力分析在高速列车运行过程中,轮对承受着来自列车本身重量以及运行时产生的动力学载荷。
这些载荷会导致轮对表面上的应力分布产生变化。
2.1 轮对静载荷分析:轮对承受的静载荷主要来自于列车本身的重量。
通过分析轮对在静态状态下的承载力和应力分布,可以得到轮对的最大接触应力和应力分布情况。
2.2 轮对动力学载荷分析:轮对在运行过程中,除了静载荷外,还要承受来自于列车运行时产生的动力学载荷,包括加速度、减速度、制动力等。
这些载荷会导致轮对表面应力分布产生动态变化。
三、高速列车轮对疲劳强度分析轮对在运行过程中所承受的应力会导致疲劳损伤,进而可能导致疲劳破坏。
因此,对轮对的疲劳强度进行分析,可以提前预测轮对的寿命,并采取相应的措施来延长轮对的使用寿命。
3.1 疲劳损伤计算:利用疲劳损伤累积理论,可以计算轮对在不同工况下的疲劳损伤量。
通过考虑应力幅值、循环次数以及材料的疲劳性能指标等参数,可以得到轮对在不同工况下的疲劳寿命。
3.2 疲劳强度分析:在获得轮对的疲劳寿命后,可以进一步分析轮对的疲劳强度。
通过比较轮对的疲劳寿命和实际使用寿命,可以评估轮对的疲劳强度,并采取相应的维修措施,以确保列车的安全和可靠运行。
四、应力及疲劳强度分析案例分析为了验证上述分析方法的准确性和有效性,可以选取一个具体的应力及疲劳强度分析案例进行分析。
6005A组织与力学性能测试方法及分析初稿
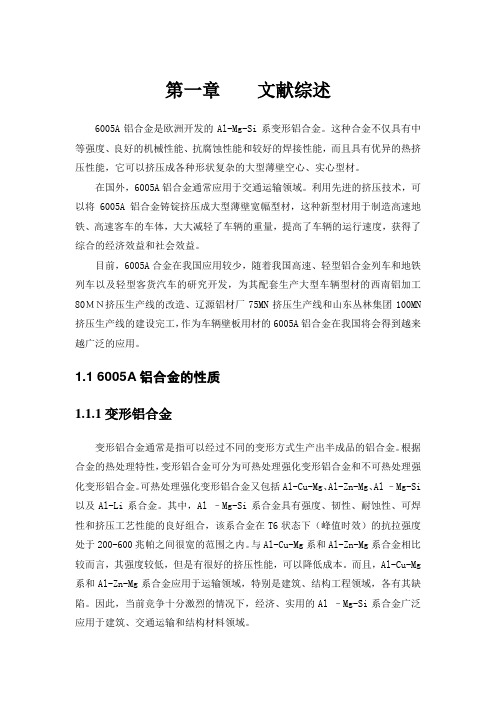
第一章文献综述6005A铝合金是欧洲开发的Al-Mg-Si系变形铝合金。
这种合金不仅具有中等强度、良好的机械性能、抗腐蚀性能和较好的焊接性能,而且具有优异的热挤压性能,它可以挤压成各种形状复杂的大型薄壁空心、实心型材。
在国外,6005A铝合金通常应用于交通运输领域。
利用先进的挤压技术,可以将6005A铝合金铸锭挤压成大型薄壁宽幅型材,这种新型材用于制造高速地铁、高速客车的车体,大大减轻了车辆的重量,提高了车辆的运行速度,获得了综合的经济效益和社会效益。
目前,6005A合金在我国应用较少,随着我国高速、轻型铝合金列车和地铁列车以及轻型客货汽车的研究开发,为其配套生产大型车辆型材的西南铝加工80MN挤压生产线的改造、辽源铝材厂75MN挤压生产线和山东丛林集团100MN 挤压生产线的建设完工,作为车辆壁板用材的6005A铝合金在我国将会得到越来越广泛的应用。
1.1 6005A铝合金的性质1.1.1变形铝合金变形铝合金通常是指可以经过不同的变形方式生产出半成品的铝合金。
根据合金的热处理特性,变形铝合金可分为可热处理强化变形铝合金和不可热处理强化变形铝合金。
可热处理强化变形铝合金又包括Al-Cu-Mg、Al-Zn-Mg、Al –Mg-Si 以及Al-Li系合金。
其中,Al –Mg-Si系合金具有强度、韧性、耐蚀性、可焊性和挤压工艺性能的良好组合,该系合金在T6状态下(峰值时效)的抗拉强度处于200-600兆帕之间很宽的范围之内。
与Al-Cu-Mg系和Al-Zn-Mg系合金相比较而言,其强度较低,但是有很好的挤压性能,可以降低成本。
而且,Al-Cu-Mg 系和Al-Zn-Mg系合金应用于运输领域,特别是建筑、结构工程领域,各有其缺陷。
因此,当前竞争十分激烈的情况下,经济、实用的Al –Mg-Si系合金广泛应用于建筑、交通运输和结构材料领域。
1.1.2 Al –Mg-Si1. Al-Mg-Si三元系平衡状态图Al-Mg-Si三元系富铝角状态图见图1-1,该系存在一个Al-Mg-Si伪二元截面,它把Al-Mg-Si三元系的富铝角分成两个独立的三元系:Al-Mg2Si –Si和Al-Mg2Si –Mg2Al3,其三元共晶温度分别为559℃和448℃。
霍普金森实验技术及6005A铝合金冲击动态实验

霍普金森实验技术及6005A铝合金冲击动态实验朱龙权;朱志武;张光瀚;车全伟【摘要】霍普金森实验是获得材料冲击动态力学性能的一种重要手段,从实验的基本原理出发,讨论了霍普金森压杆实验中的弥散效应、惯性效应、摩擦效应、波动效应和二维效应.从实验优化的角度出发,讨论了试样设计的要求、高温实验所需考虑的问题以及脉冲整形技术和光电测试技术等在霍普金森实验中的应用.对6005A 铝合金进行了霍普金森压杆实验.实验结果显示:2组不同方向制备的试样表现出相同的冲击动态力学性质;6005A铝合金表现出应变率弱敏感性,应变强化效应较为明显.【期刊名称】《成都大学学报(自然科学版)》【年(卷),期】2018(037)003【总页数】6页(P230-235)【关键词】霍普金森实验;脉冲整形;试样设计;高温实验;6005A铝合金【作者】朱龙权;朱志武;张光瀚;车全伟【作者单位】西南交通大学牵引动力国家重点实验室,四川成都610031;西南交通大学力学与工程学院,四川成都610031;西南交通大学牵引动力国家重点实验室,四川成都610031;西南交通大学力学与工程学院,四川成都610031;西南交通大学力学与工程学院,四川成都610031;中车青岛四方机车车辆股份有限公司,山东青岛266111【正文语种】中文【中图分类】O3480 引言随着科技的发展,材料的冲击动态力学性能对结构设计和材料研究有着越来越重要的意义,而传统的伺服实验机所提供的加载应变率仅在1 s-1以下,这样的应变率远远达不到测试冲击动态力学性能的要求.目前,材料的冲击动态力学性能的测试方法主要有高速液压装置、落锤实验、霍普金森实验、膨胀环、空气炮等.其中,霍普金森实验的加载应变率一般在102~104 s-1,是研究材料冲击动态力学性能的主要方式[1-3].Kolsky[4]针对霍普金森实验的不足,对实验设备进行了改进,通过将试样放置在两根弹性杆之间来测量材料的应力应变曲线,这也是目前最常见的分离式霍普金森压杆实验设备,同时他也提出了完整的实验技术以及数据处理方式.但该实验基于一维应力波假定和试样应力均匀性假定,因此在实际操作中仍存在一些不足,比如弥散效应、惯性效应、摩擦效应及波动效应等.铝合金具有着良好的比强度、比刚度与耐腐蚀能力以及优异的延展性等诸多优点,在车辆制造、交通运输、建筑工程、航空航天等领域得到广泛应用,在实际工程应用过程中,铝合金不可避免会受到冲击动态载荷的影响,比如鸟撞飞机、列车碰撞等.因此,对铝合金的冲击动态力学性能研究有较大的现实意义.本研究综述了霍普金森实验中需要考虑的几个问题,并探讨了减小这些问题影响的要求,讨论了高温实验和光电测试技术在霍普金森实验中的应用.同时,利用霍普金森压杆实验设备测试了6005A铝合金不同应变率下的动态压缩性能,为该型铝合金应用于列车车体设计提供了相关的实验数据,也为后续的对该型铝合金的本构关系的研究提供了技术支持.1 霍普金森实验及优化1.1 霍普金森实验存在的问题随着霍普金森实验技术的数十年发展,针对不同的实验的要求,科研人员研究出了不同类型的霍普金森实验设备.本研究针对的霍普金森实验中存在的问题主要还是基于霍普金森压杆实验设备.霍普金森压杆实验的应用必须遵从2个基本假定,即一维应力波假定和试样应力均匀性假定.这2个基本假定使得霍普金森压杆实验中的惯性效应和应变率效应解耦,使得问题得以简化.下面对遵从这2个假定情况下霍普金森压杆实验出现的具体问题进行分析.1.1.1 弥散效应.根据一维应力波假定,每一个应力波脉冲在杆中的传播速度是恒定的,但这一假定忽略了杆中质点的横向惯性运动.对此,Pochhammer[5]给出了弹性杆中波传播的解析解,即,(1)式中,μ和r分别为弹性杆的泊松比和半径,λ为应力波某个谐波的波长.式(1)表明组成应力脉冲的各个谐波是以各自的速度传播,高频波的传播速度慢,低频波的传播速度快.随着应力脉冲在杆中的传播,不同频率的波会产生相位差导致应力脉冲在弹性杆中发生弥散.弥散效应会使测得的应力波波形在波峰上出现高频振荡,这种振荡一般会掩盖材料本身的力学特性,甚至还可能会误把出现的第一个振荡当成材料的屈服极限.在实验中,为尽量减小弥散效应对实验的影响,可从式(1)入手,尽量减小弹性杆的半径,也可增加子弹的长度(增加入射波的波长),使得r/λ≤0.1[6],这是对实验装置的设计要求.此外,可在冲击端加上一层软介质[7],即波形整形器,用以过滤掉高频波,从而减小振荡.1.1.2 惯性效应.在霍普金森实验中,试样的变形速率很高,外部对试样做的功,除了转化为试样的变形能以外,还会有一部分转化为试样的横向动能和纵向动能,即试样质点引起的惯性效应.在研究材料的本身特性时,一般只关心变形和力的关系,即只考虑应变能,因此在确定试样的应力时,必须消除惯性效应引起的附加应力.对惯性效应的研究中,Kolsky[4]基于能量守恒定理提出试样惯性效应的修正公式,但他的研究没有考虑质点的纵向运动以及摩擦效应的影响.Davies等[7]基于能量守恒定理,在同样没有考虑摩擦效应的影响下提出了一个更完善的修正公式,(2)式中,ρ、μ、r和l分别为试样的密度、泊松比、半径和长度,σ0为实测的试样应力.按照此公式,并假设试样为近似不可压材料时(μ=0.5),消除惯性效应引起的附加应力的最佳试样长径比为,(3)Gorham[8]认为,试样中的应力可以表示为试样两端的平均应力和惯性效应引起的附加应力的总和,(4)式中,σ1和σ2分别为试样和入射杆与透射杆接触端的应力,ρ、r和l分别为试样的密度、半径和长度.为了减小惯性效应的影响,采用恒应变率的加载可以消除式(4)的第二项的影响,此外,由于在实验过程中应变率不为零,为了消除第三项的影响,可以将试样的长径比设计为,(5)1.1.3 摩擦效应.在霍普金森实验中,由于弹性杆和试样的横向运动的不同,会在两者的界面处产生摩擦,从而破坏了试样的一维应力状态,即出现端面摩擦效应.能够精确描述摩擦效应比较困难,对此,Klepczko等[9]提出一个简便的修正公式,(6)式中,σ0为实测的试样应力,μ为试样和弹性杆之间的摩擦系数.在霍普金森压杆实验中,当试样的长径比l/r~1,且试样和弹性杆之间又充分润滑的情况下,摩擦效应通常可以不予考虑.陶俊林等[10]在能量守恒原理上,考虑了摩擦效应的影响,其最终结果可以表示为,σ=(7)可以发现,式(7)中第一项只有摩擦效应的影响,如果忽略摩擦效应的影响,那么上式的结果就和式(4)一样;如果忽略惯性效应的影响,那么上式的结果就和式(6)相同.试样的惯性效应和界面的摩擦效应所导致的应力应变曲线的偏差很容易被人们误认为是应变率效应[6],此需要在实验中和处理数据时加以注意.1.1.4 波动效应.在霍普金森实验中,应力波在试样内部只需两到三个来回,试样的状态就可以达到均匀,这个时间远远小于应力波脉冲的宽度.因此,试样在应力波脉冲作用的大部分时间内都是处于应力均匀状态.但事实上,在应力波脉冲作用于试样的最开始阶段,试样内部的应力状态是不均匀的,即试样的波动效应.1)假设应力波为纯弹性波,根据一维应力波理论,在加载波为矩形强间断波时,试样两端的相对应力差αk[11]为,(8)(9)式(8)中,k为透射反射的次数,式(9)中(ρcA)s和(ρcA)0分别为试样和弹性杆的波阻抗,、ρ、c和A分别为试样和弹性杆的密度,弹性波波速和横截面积.按照Ravichandran等[12]的建议,当αk≤5%时,可以认为试样中已经达到应力均匀,从而可以计算出所要求的透射反射次数k,再根据,τ=kls/cs(10)则可以计算出应力均匀所需要的时间τ,式(10)中ls和cs为试样的长度和试样的弹性波速.2)假设应力波为纯塑性波,并且在试样中反射π次后试样中达到应力均匀[13],对于按照Taylorvon Karman理论进行塑性变形的固体而言,达到应力均匀所要的时间τ[14]为,(11)式(11)中,dσ/dε为试样真应力—真应变曲线的斜率,ls和ρ分别为试样的长度和试样材料的密度.在实际情况下,对于绝大部分材料而言,应力波在试样中传播时,既包含弹性波又包含塑性波,只以弹性波或只以塑性波计算得到的结果都是不符合实际的,按弹性波计算得到的均匀化时间偏低,而按塑性波计算得到的均匀化时间偏高.1.1.5 二维效应.在霍普金森实验中,试样的径向尺寸应尽量与弹性杆的径向尺寸相接近(面积匹配),以保证一维假定的有效性.由于特殊原因的限制,有时无法保证这种面积的匹配,比如在测量硬质材料的冲击动态力学性能时,为获得较大的加载应力,通常选用较小截面积的试样.肖大武等[15]分析发现,由于面积失匹所引起的二维效应主要是由于弹性杆端面发生了凹陷所造成的,当时间在弹性阶段时,凹陷二维效应影响很大,并且只有当试样弹性模量远远小于弹性杆的弹性模量时,这种影响才能忽略,而在塑性阶段时,除了试样材料的性质外,外加载荷对凹陷二维效应也有较大的影响,并且外加载荷相对试样材料屈服强度越大,影响越小.Kinra[16]等的研究表明,当试样(和弹性杆为同种材料)的直径仅为弹性杆的一半时,表现出显著的二维效应,当试样的半径设计得较小时,由于面积失匹所引起的二维效应就需要考虑进去.1.2 霍普金森实验的优化1.2.1 脉冲整形技术.在做霍普金森实验时,由于弥散效应,采集到的应力波上会有振荡,这种影响与弹性杆的杆径相关,杆径越细,弥散效应越不明显.由于某些材料的材料性质,比如岩土类材料,为了保证试样的均匀性,试样尺寸必须保证一定大的尺寸,所以也必须选择大尺寸的霍普金森实验装置,弥散效应的影响不可忽略.此外,尽管减小杆径可以减小弥散效应,但出现的振荡都会影响数据的处理.由于这种弥散效应引起的振荡明显依赖于子弹撞击弹性杆时所产生应力脉冲的上升时间,而较长的上升时间可以减小应力脉冲传播时的弥散效应和惯性效应.例如,通过将弹性杆的受撞击端加工成圆头产生一个非平面撞击[17],可以增加应力脉冲上升时间,但这种方法在应力脉冲传播一段较短距离后,修正效果就变得不明显.Frantz等[18]通过将一片薄的圆片状材料贴在SHPB入射杆的受撞击端,得到了更为有效的结果.在实验时该薄片在被子弹撞击后先屈服,从而软化了撞击,这种软化增加了应力脉冲的上升时间,减小了振荡.事实上,这个薄片将撞击后产生的高频脉冲过滤掉了.Ellwood等[19]提出的三杆技术最初是为了保证恒应变率加载,但通过实验结果还可以发现有很好的减小应力波波形振荡的功能.这种方法在基础的SHPB装置前增加一个预加载杆,在预加载杆和入射杆之间放置一个模拟试样,模拟试样一般和实验试样相同.在实验过程中,相当于将通过模拟试样的透射波当作实验试样的入射波加载.这种方法可以有效地减小弥散效应产生的振荡,也能实现恒应变率加载,但是其入射波其实是已经通过模拟试样的透射波,因此实验试样所能达到的应变率会大打折扣,无法达到高应变率加载,另外每次实验还都要消耗模拟试样.1.2.2 试样尺寸设计.霍普金森压杆实验的试样通常设计为直圆柱试样.试样的尺寸设计主要受惯性效应、摩擦效应、均匀性假定和二维效应所约束,前两者主要影响试样的长径比,均匀性假定主要影响试样的长度,二维效应主要影响试样和SHPB设备的弹性杆之间的直径比.理论上,为保证均匀性假定,所设计的试样要求越薄越好,使得应力在试样内能很快达到均匀状态,但是如果试样很薄,试样和弹性杆之间的摩擦所导致的二维效应会显著增加.仅考虑惯性效应的影响,根据Davies[7]的修正公式,最佳的长径比为,(12)仅考虑摩擦效应的影响,根据Klepczko和Malinowski的简便的修正公式,在试样和弹性杆之间充分润滑的情况下,试样的长径比应大致为.另外,考虑实验所要求的最大应变率和为了能体现材料整体特性的尺寸要求,美国金属学会(American Society for Metal,ASM)推荐的长径比为0.5~1.0[25].Davies等[7]提出的最佳长径比是在实验初始理想时刻的基础上提出的,只适用于小变形的情况.陶俊林等[10]考虑了试样在实验过程中的变形,在以变形率为定值的前提下,即恒应变率加载的条件下,同时考虑了惯性效应和摩擦效应的影响,提出试样的初始长径比和设计的最终应变之间的关系,其提出的最佳原始长径比为,(13)式中,εend为设计的最终应变.这样的试样设计能有效地减小惯性效应的影响,并优于Davies[7]的设计,但缺点也很明显,首先需要知道试样的最终应变,而这在做实验之前是不容易得到的.卢芳云等[20]认为试样的直径一般为弹性杆直径的80%左右,这样试样横向膨胀到直径和弹性杆相同时,轴向真实应变可达30%.对硬质材料的SHPB实验,为了获得更大的力,会通过减小试样直径来实现,但这会造成试样和弹性杆之间的面积失配,容易引起弹性杆的凹陷,造成一维假定不再成立,二维效应明显.1.2.3 高温实验.一般来说,温度是影响材料本构关系的一个重要参量,尤其像金属类材料,基本都存在温度效应,所以不同温度下的实验都很有必要.目前,高温霍普金森压杆实验主要有两种:一种是将试样和一部分的弹性杆同时在一个加热箱中加热至所要求的温度,然后进行实验;另一种方法是单独将试样加热,然后再进行实验.第一种方法首先需要考虑温度对弹性杆的软化作用,在实验过程中弹性杆是否依然处在弹性范围值得商榷.此外,由于温度梯度的影响,应力波在弹性杆中的传播也变得复杂,会对实验产生很大的偏差,采用这种方法需要利用一维应力波传播理论和传热学原理等,修正温度梯度场对波形的测量,在较小的温度范围内,也可以忽略温度梯度的影响.第二种方法需要在试样加热至所需温度后,立刻进行实验,避免试样的温度在准备实验过程中的下降,即在加热和实验之间要有精确的同步性.在这方面,Netmat-Nasser[21]设计出了一种同步组装系统,能够在高温下进行高应变率的力学测试.除了上述方法外,还有一些实验设计从加热方式出发,比如Rosenberg等[22]提出利用金属材料的涡流效应和磁滞现象来加热,这种方法能对试样集中加热,从而提高加热效率,但是缺点是只对金属材料有效;Macdougall[23]设计了一种辐射加热装置对试样进行加热,这种方法的优点在于加热方式是非接触的,并且加热效率高,速度快,但是加热设备比较复杂,成本也比较高.1.2.4 光电测试技术.目前,霍普金森实验获得应力应变数据的主要方法仍然是通过粘贴在弹性杆上的应变片来测出入射波、反射波和透射波的信号,然后再通过二波法或三波法进行计算.随着光学测试技术的发展,将光电测试引入霍普金森实验能够大大地提升实验的测试精度.例如,Griffiths等[24]用白光光源测量了试样中圆柱试样的端面位移;Ramesh等[25]则以激光为光源测量了试样的直径变化;傅华等[26]通过激光微位移测量技术,测量出入射杆和透射杆的端面速度,再根据一维应力波理论计算出试样的应力应变曲线,并且进行了实验和数值模拟,验证了这种方法的可行性.2 6005A铝合金冲击动态实验本研究对6005A铝合金进行了霍普金森压杆实验.试样尺寸为φ8 mm×6 mm,针对原材料为方形板材,实验时分别制备了2组试样:一组试样的轴线方向与方形板材的厚度方向平行,为厚度方向组;另一组试样的轴线方向与方形板材的厚度方向垂直,为长度方向组.每组试样分别进行了3个气压的实验,分别为0.6 MPa、1.0 MPa和1.5 MPa,最终获得了厚度方向应变率为998 s-1、1 862 s-1、2563 s-1的3组应力应变曲线,以及长度方向应变率为1 116 s-1、1 868 s-1、2 671 s-1的3组应力应变曲线,结果如图1所示.图1(a)中应变率为1862 s-1那组实验在应变达到0.1后流动应力比2563 s-1那组实验的流动应力大得多,应该是在实验过程中应变片发生了松动.因此,2563 s-1这组实验数据并不可靠.由于实验室的条件限制,实验用的子弹长度惟一,那么加载的脉冲时间也相同,所以应变率越大,理论上试样的最大应变越大.而图2(b)中应变率为1116 s-1那组实验的最大应变比应变率为1868 s-1那组实验的最大应变大得多,因此1116 s-1这组实验数据并不可靠.图1 6005A铝合金动态应力应变曲线图通过对图1分析可以发现,6005A铝合金无论在厚度方向还是长度方向曲线的趋势都基本一致,流动应力随应变的增大明显增大,表现出明显的应变硬化现象.排除2563 s-1和1116 s-1这两组不可靠的实验数据,剩下的实验曲线基本重合.而从应变率来分析,实验结果表明,在该应变率范围内,6005A铝合金表现出应变率弱敏感性,按不同方向来分析,表明6005A铝合金在这两个方向上的冲击动态性质大致相同.选取应变率为998 s-1、1868 s-1和2671 s-1的3组实验的最大应力和最大应变分析如图2所示.图2结果表明,6005A铝合金的最大应力和最大应变与应变率大致呈线性关系.3 结论本研究探讨了霍普金森实验中的弥散效应、惯性效应、摩擦效应、波动效应和二维效应.为了减少实验中这几个效应的影响,研究了脉冲整形技术和试样尺寸的设计要求.同时,为了拓宽传统霍普金森实验的应用,对高温霍普金森实验需要注意的问题,以及光电测试技术在霍普金森实验的应用也做了相关讨论.通过对6005A 铝合金的2个不同方向的霍普金森压杆实验,结果表明,在实验应变率范围内,6005A铝合金表现出为应变率弱敏感性,应变强化效应比较明显,另外2个不同方向表现出相同的性质,最大应力和最大应变和应变率大致呈线性关系.图2 6005A铝合金最大应力和最大应变与应变率的关系图参考文献:【相关文献】[1]Hopkinson B.A method of measuring the pressure produced in the detonation of high explosives or by the impact of bullets[J].Phil Trans R Soc Lond,1914,A213:437-456. [2]Hopkinson B.The effects of momentary stresses in metals[J].Proc R Soc,1905,A74:498-506.[3]Hopkinson J.Further experiments on the rupture of iron wire(1872)[C]//HopkinsonB.Original Paper by the Late John Hopkinson.Cambridge,UK:Cambridge University Press,1901.[4]Kolsky H.An investigation of the mechanical properties of materials at very high rates of loading[J].Proc Phys Soc B,1949,62(11):676-700.[5]Pochhammer L.On the propagation velocities of small oscillations in an unlimited isotropic circular cylinder[J].J Reine Angew Math,1876,81:324-326.[6]Bertholf I D.Feasibility of two-dimensional numerical analysis of the split-hopkinson pressure bar system[J].J Appl Mech,1974,41(1):137-144.[7]Davies E D H,Hunter S C.The dynamic compression testing of solids by the method of the split hopkinson pressure bar[J].J Mech Phy Solids,1963,11(3):155-179.[8]Gorham D A.Specimen inertia in high strain-rate compression[J].J Phys D Appl Phys,1989,22(12):1888-1893.[9]Kawata K,Shiuiri J.High velocity deformation of solids[M].Berlin,Germany:Springer-Verlag,1978.[10]陶俊林,陈裕泽,田常津,等.SHPB系统圆柱形试件的惯性效应分析[J].固体力学学报,2005,26(1):107-110.[11]王礼立,王永刚.应力波在用SHPB研究材料动态本构特性中的重要作用[J].爆炸与冲击,2005,25(1):17-25.[12]Ravichandran G,Subhash G.Critical appraisal of limiting strain rates for compression testing of ceramics in a split Hopkinson pressure bar[J].J Am Ceram Soc,1994,77(1):263-267.[13]Laz P J,Craig B A,Hilberry B M.A probabilistic total fatigue life model incorporatingmaterial inhomogeneities[J].Int J Fatigue,2001,23(Suppl 1):119-127.[14]刘瑞堂,果春焕,张智峰.分离式Hopkinson压杆系统冲击压缩过程中试样的应力均匀化过程[J].机械工程材料,2009,33(2):25-27,95.[15]肖大武,胡时胜.SHPB实验试件横截面积不匹配效应的研究[J].爆炸与冲击,2007,27(1):87-90.[16]Kinra V K,李培宁.在杆中切口间断处脉冲波的反射及透射[J].固体力学学报,1983,39(2):197.[17]Parry D J,Walker A G,Dixon P R.Hopkinson bar pulse smoothing[J].Meas Sci Technol,1995,6(5):443-446.[18]Frantz C E,Follansbee P S,Wright W T.Experimental Techniques with the split hopkinson pressure Bar[C]//Proceedings of the 8th International Conference on High Energy Rate Fabrication.San Antonio,TX,USA:Los Alamos National Laboratory,1984.[19]Ellwood S,Griffiths L J,Parry D J.Materials testing at high constant strain rates[J].J PhysE Sci Instr,1982,15(3):280-282.[20]卢芳云,陈荣,林玉亮,等.霍普金森杆实验技术[M].北京:科学出版社,2013.[21]Nemat-Nasser S,Guo W G.Thermomechanical response of HSLA-65 steelplates:Experiments and modeling[J].Mech Mater,2005,37(2):379-405.[22]Rosenberg Z,Dawicke D,Strader E,et al.A new technique for heating specimens in split-hopkinson-bar experiments using induction-coil heaters[J].Exp Mech,1986,26(3):275-278.[23]Macdougall D.A radiant heating method for performing high temperature high strain rate tests[J].Meas Sci Technol,1998,9(10):1657-1662.[24]Griffiths L J,Martin D J.A study of dynamic behavior of a carbon-fiber composite using the split Hopkinson pressure bar[J].J Phys D,1974,7(17):2329-2344.[25]Ramesh K T,Narasimhan S.Finite deformations and the dynamic measurement of radial strains in compression Kolsky bar experiments[J].Int J SolidsStruct,1996,33(25):3723-3738.[26]傅华,彭金华,李俊玲,等.一种适合于Hopkinson杆的实验测试方法探索[J].高压物理学报,2014,28(4):423-428.。
6061铝合金疲劳极限
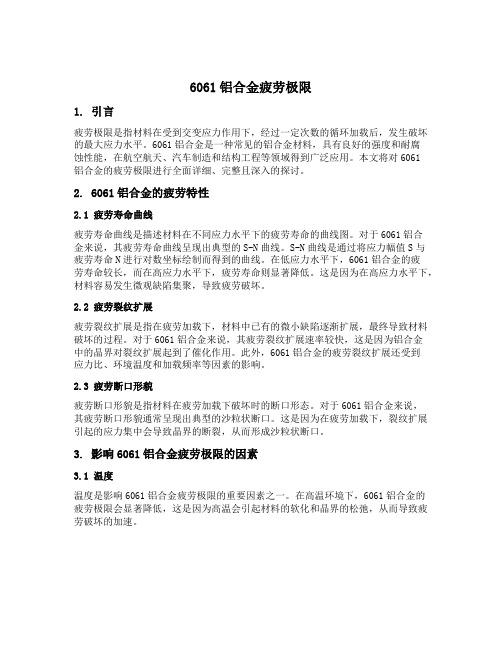
6061铝合金疲劳极限1. 引言疲劳极限是指材料在受到交变应力作用下,经过一定次数的循环加载后,发生破坏的最大应力水平。
6061铝合金是一种常见的铝合金材料,具有良好的强度和耐腐蚀性能,在航空航天、汽车制造和结构工程等领域得到广泛应用。
本文将对6061铝合金的疲劳极限进行全面详细、完整且深入的探讨。
2. 6061铝合金的疲劳特性2.1 疲劳寿命曲线疲劳寿命曲线是描述材料在不同应力水平下的疲劳寿命的曲线图。
对于6061铝合金来说,其疲劳寿命曲线呈现出典型的S-N曲线。
S-N曲线是通过将应力幅值S与疲劳寿命N进行对数坐标绘制而得到的曲线。
在低应力水平下,6061铝合金的疲劳寿命较长,而在高应力水平下,疲劳寿命则显著降低。
这是因为在高应力水平下,材料容易发生微观缺陷集聚,导致疲劳破坏。
2.2 疲劳裂纹扩展疲劳裂纹扩展是指在疲劳加载下,材料中已有的微小缺陷逐渐扩展,最终导致材料破坏的过程。
对于6061铝合金来说,其疲劳裂纹扩展速率较快,这是因为铝合金中的晶界对裂纹扩展起到了催化作用。
此外,6061铝合金的疲劳裂纹扩展还受到应力比、环境温度和加载频率等因素的影响。
2.3 疲劳断口形貌疲劳断口形貌是指材料在疲劳加载下破坏时的断口形态。
对于6061铝合金来说,其疲劳断口形貌通常呈现出典型的沙粒状断口。
这是因为在疲劳加载下,裂纹扩展引起的应力集中会导致晶界的断裂,从而形成沙粒状断口。
3. 影响6061铝合金疲劳极限的因素3.1 温度温度是影响6061铝合金疲劳极限的重要因素之一。
在高温环境下,6061铝合金的疲劳极限会显著降低,这是因为高温会引起材料的软化和晶界的松弛,从而导致疲劳破坏的加速。
3.2 应力水平应力水平是指加载到材料上的应力大小。
对于6061铝合金来说,较低的应力水平会延长其疲劳寿命,而较高的应力水平则会显著降低其疲劳寿命。
这是因为在高应力水平下,材料中的缺陷更容易集聚,从而加速疲劳破坏的发生。
3.3 加载频率加载频率是指单位时间内加载的循环次数。
服役高速列车车体铝合金材料率相关剩余强度预测

服役高速列车车体铝合金材料率相关剩余强度预测王小瑞;朱涛;张敬科;丁浩谞;肖守讷;鲁连涛;杨冰;阳光武【期刊名称】《中南大学学报(自然科学版)》【年(卷),期】2024(55)5【摘要】高速列车结构与材料在长期服役过程中因受复杂边界条件的影响将逐渐趋于劣化,存在潜在的安全风险。
本文以高速列车常用铝合金6005A-T6为对象,首先将材料细观微结构解耦为基体相与空洞相,推导符合微结构连续度Weibull分布特征的损伤演化方程;继而提出一种考虑应变率的试验−数值方法,识别材料颈缩后损伤的加速演化行为,进而推导得到覆盖空洞相萌生、生长、聚合全过程的损伤演化方程,并得出基体相的无损本构;最后结合细观物理机制提出损伤顺序交互作用模型,以实现仅测量材料表观弹性模量即可获取含先前服役损伤材料在后续延性变形中的损伤演化方程,准确预测含服役损伤材料的率相关剩余强度。
研究结果表明:预测值与试验值的平均相对误差不超过1%。
损伤随延性发展由应变率正敏感性转变为负敏感性;对于疲劳−延性机制,空洞在先前疲劳损伤发展的空洞基础上继续生长。
【总页数】11页(P2000-2010)【作者】王小瑞;朱涛;张敬科;丁浩谞;肖守讷;鲁连涛;杨冰;阳光武【作者单位】西南交通大学轨道交通运载系统全国重点实验室【正文语种】中文【中图分类】U270.2【相关文献】1.高速列车车体服役状态残余应力超声波法无损测量及验证2.加速工况下铝合金高速动车组车体服役性能评估3.高速列车铝合金车体中铆钉和螺栓联接结构的强度分析4.高速列车铝合金车体强度可靠性安全系数分析方法5.高速磁浮列车复合材料车体部件强度分析及结构优化因版权原因,仅展示原文概要,查看原文内容请购买。
动车组高速列车用6005A铝合金车体型材挤压工艺

动车组高速列车用6005A铝合金车体型材挤压工艺林树春【摘要】为适应我国高速铁路发展的需要,开发了动车组高速列车用6005A铝合金车体型材,通过试验研究,优化了合金成分配比,确定了公司内部合金成分控制标准,优化了挤压工艺参数和模具设计、制造方案.生产出了内部组织和力学性能合格的高速列车用的6005A铝合金车体型材.【期刊名称】《轻合金加工技术》【年(卷),期】2012(040)003【总页数】3页(P45-47)【关键词】动车组高速列车;大截面车体型材;6005A铝合金【作者】林树春【作者单位】吉林麦达斯铝业有限公司技术开发部,吉林辽源136200【正文语种】中文【中图分类】TG379为了适应我国高速铁路的发展,根据铁道部动车组列车(车速200 km/h~380 km/h)的需求,吉林麦达斯铝业公司引进国外大型铝挤压机生产线,2001年开始研制大截面铝合金车体型材挤压生产工艺。
6005A铝合金是动车组列车的首选材料,该合金属于Al-Si-Mg系可热处理强化变形铝合金,可以经过在线淬火后人工时效获得中等强度,广泛用于动车组列车的车体及结构件。
车体铝合金型材多为超长度(20 m~26 m)、大截面、多腔空心、形状复杂的型材,对型材的尺寸和形位公差、综合性能和组织要求较高。
生产这种高质量的铝合金型材需要有55 MN以上的油压挤压机、在线精密淬火装置和28 m长精确控温时效炉等设备,以及成熟的挤压生产工艺。
1 试验方法1.1 工艺流程铸锭车皮→铸锭加热→挤压→牵引机随动牵引→在线淬火→热锯切中断→张力矫直→锯切定尺、去头尾→检验→人工时效。
试验采用经均匀化退火的优质6005A铝合金圆铸锭,车皮去除表面疏松、偏析及氧化皮。
用德国进口IAS感应加热炉对圆铸锭进行梯度加热,分别在55 MN双动油压挤压机、75 MN单动油压挤压机和110 MN双动油压挤压机上等温、等速挤压,对挤压铝合金型材进行在线淬火,经拉伸矫直、精整后进行人工时效处理。
铁路用高强度铸造铝合金的研究
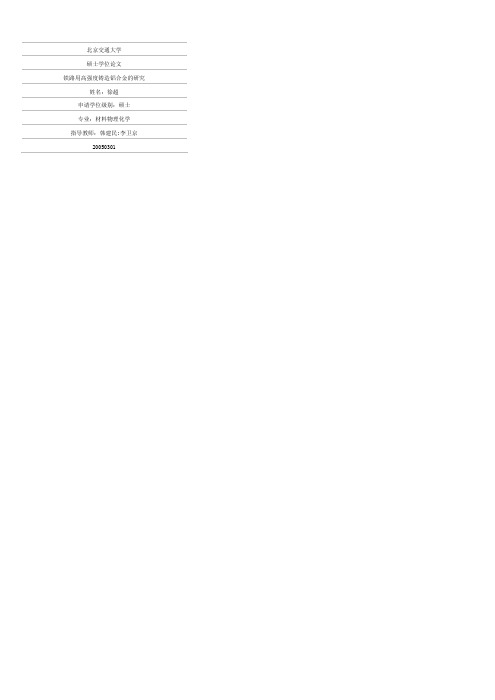
北京交通大学硕士学位论文铁路用高强度铸造铝合金的研究姓名:徐超申请学位级别:硕士专业:材料物理化学指导教师:韩建民;李卫京20050301摘要摘要高速列车已经成为我国铁路交通的发展方向,车辆轻量化是高速列车的关键技术之一。
目前,我国车辆零部件所用的材料主要是钢铁材料,使车辆的重量较重,已限制了我国高速列车的发展。
因此,开发出能够替代现有钢铁材料的新型轻质材料具有重要的理沦和实际意义。
铝是实现轻量化的首选材料。
但是,我国目前已有的铝合金材料的技术经济性与我国高速列车的要求还有一定的差距。
为了丌发出一种能在高速列车上应用的高强度铸造铝合金,本论文以Alcu系合金为基础,在理论分析和试验的基础上,确定了铝合金中基本元素的成分范围,考察了加入M异、Si、稀土等元素的作用和效果,测试了合金的力学性能与铸造性能,观察并分析了合金的金相和断口组织,可以得出以下主要结论:1)元素Mg能显著提高合金的抗拉强度,但降低合金的延伸率、冲击韧性和铸造性能;2)元素Si能显著提高合金铸造性能,但降低合金的力学性能:3)稀土对合金具有良好的变质细化作用,不仅使a(A1)晶粒和共晶组织得到一定程度的细化,而且使针、片状的共晶硅变成了粒状;4)在加入量相同的情况下(0.2%Ti),A卜Ti—c对合金的变质细化效果要优于Al—Ti~B对合金的变质细化效果。
关键词:高速列车高强铸造铝合金力学性能铸造性能变质细化效果AbstractHigh—speedtrainisthedevelopingtrendofrailwaytransportationinchina,ofwhichweightreductioniSoneofthekeytechniquesofHigh—speedtrain.Nowadaysinourcountry,mostmaterialSUsedinthepartSoftrainsareironandsteel,whichmakethetrainhavehighweight,and1imitthedevelopmentofhigh—speedtrain.Therefore,itiSofgreattheoretica]andpracticalsignificancetoexplorenewlightermaterialtotaketheplaceofcurrentSteelmaterial.AluminumalloyiStheoptimummaterialforweightreduction.ttowever,technicalandeconomictargetofthepresentlyexistingalumihumalloycan’tmeettherequirementofhigh—speedtrains.Inordertodevelopanewhighstrengthcastingaluminumalloy,onthebaseofAl—Cuseriesalloy.compositionrangeoffundamentalelementsofaluminumalloyiSdeterminedbytheoryanalysiSandexperiment.TheinfluenceandeffectofelementsofMg,Siandrareearthareobservedbytestingitsmechanicalpropertiesandcastingproperties.MetallurgicalstructuresandfractographofalloyarealSOobserved.MainconelusionscanbedrawnasfoliOWS:1)MgelementcanSignificantlYincreasethetensilestrengthofalloy,butdecreasetheelongation,impactductilityandcastingproperties:2)Sielementcanincreasecastingpropertiesofalloy,butdecreaseitsmechanicalproperties:3)Rareearthhavegoodmodificationandrefinementeffect.ItcannotonlYrefinethea(A1)grainandeutecticstructuretosomeextentbutalSOturntheneedle一1ikeandlaminareutectieSitogranularSi.4)Undertheconditionofsameaddition(0.2%Ti),therefinementeffectofA1一Ti-CtothealloyiSbetterthanthatofAl—Ti—B.KeyWords:High—speedtrain,highstrengthcastaluminnmalloy,mechanicalproperty,castingproperty,modificationandrefinementeffect2第一章绪论第一章绪论高速列车已经成为我国铁路交通的发展方向,高速铁路的发展对车辆零部件材料提出了更高的要求。
6005A铝合金CMT焊接接头微观组织和疲劳裂纹萌生

6005A铝合金CMT焊接接头微观组织和疲劳裂纹萌生刘浩博;杨尚磊;王远;谢超杰【摘要】使用冷金属过渡(CMT)焊接技术对6005A铝合金进行焊接,获得成形良好的焊接接头.应用光学显微镜、显微硬度仪、扫描电子显微镜和能谱分析仪研究接头的微观组织、硬度和疲劳性能.结果表明:接头焊缝区以小尺寸的等轴晶和胞状树枝晶为主;熔合区存在明显的熔合线;近熔合线附近的热影响区中晶粒发生明显的粗化.接头显微硬度显示,热影响区中软化区是整个焊接接头的最薄弱区域.维氏硬度(HV)最低,为55,焊缝区为70.疲劳试样表面分析发现焊缝中存在长条状的第二相粒子,经能谱分析为AlSiFe相,在循环载荷的作用下,该相内部萌生了微裂纹,但并未扩展,说明该相对接头的疲劳性能影响不大.【期刊名称】《上海工程技术大学学报》【年(卷),期】2017(031)004【总页数】5页(P307-310,346)【关键词】冷金属过渡焊;微观组织;显微硬度;疲劳裂纹萌生【作者】刘浩博;杨尚磊;王远;谢超杰【作者单位】上海工程技术大学材料工程学院,上海201620;上海工程技术大学材料工程学院,上海201620;上海工程技术大学材料工程学院,上海201620;上海工程技术大学材料工程学院,上海201620【正文语种】中文【中图分类】TG453近年来,随着经济的发展,人们越来越认识到环境保护的重要性,低碳环保、节能减排已然深入人心,同时也被列为政府工作重点.这对汽车、列车等主要能源消耗行业提出了更高的要求,实现车身轻量化迫在眉睫.铝(Al)是地壳中含量最多的金属元素,经过合金处理后得到的铝合金具有质量轻、强度高、抗冲击性能好、耐腐蚀、耐磨和易加工等优点,因此越来越多的企业开始使用铝合金来代替传统的钢材.6005A铝合金属于可热处理强化的Al-Mg-Si系列铝合金,具有较高的强度和良好的机械加工特性,且焊接性能优良,主要用于高铁、汽车的车架、车身以及部分零部件[1-2].目前,铝合金的焊接方法主要是搅拌摩擦焊和电弧焊,但是这两种方法在焊接过程中均存在缺陷.本文使用的冷金属过渡(Cold Metal Transfer,CMT)焊接是Fronius 公司在2004年推出的一种新型的电弧焊接方法,该方法基于熔化极气体保护焊,是一种适合薄板的无飞溅、低热输入的新型焊接技术.在焊接过程中通过短路过渡时焊丝的回抽和电流的减小实现冷热交替焊接,从而减少热输入[3].国内外众多学者对CMT焊接铝合金进行了研究,如 Shu 等[4]研究了厚板铝合金CMT的焊接,并利用有限元模拟技术分析了焊接残余应力,结果发现利用CMT焊接厚板铝合金容易出现残余应力的集中.Pickin等[5]实现了间隙2 mm的铝合金薄板CMT搭接焊接,且成形良好,说明CMT对焊接结构的工装要求较低,大大拓展了其使用范围.尽管对CMT 焊接铝合金的相关研究较多,但是关于6005A铝合金的CMT焊接性能,尤其是对焊接接头的疲劳性能的研究仍不多见.本文对6005A 铝合金CMT焊接接头微观组织和疲劳裂纹萌生及扩展特征进行了系统研究,以期对6005A铝合金的应用有一定的指导意义.1 材料和试验1.1 试验材料母材为厚度3 mm的6005A扎制铝合金薄板,T6热处理状态.保护气体为氩气(Ar).焊丝型号为ER4043合金,直径为1.2 mm.母材和焊丝的化学成分(质量分数ω,%)见表1.表1 母材和焊丝的化学成分Table 1 Chemical composition of base metal and wire %材料AlMgSiZnFeCuMnCrTi6005A余量0.40~0.700.50~0.90≤0.20≤0.35≤0.30≤0.50≤0.30≤0.10ER4043余量≤0.054.50~6.00≤0.10≤0.80≤0.30≤0.05—≤0.20从表1可以看出,6005A铝合金中的主要添加元素是镁(Mg)和硅(Si),这是所有6系铝合金的主要添加元素,目的是在进行热处理的过程中生成Mg2Si强化相以提高6005A铝合金母材的力学性能.而铜(Cu)元素则是6005A铝合金中独有的一种添加元素,Cu的加入可以提高强化相的密度从而提升材料性能[6].而铁(Fe)、锰(Mn)元素则是以杂质元素的身份存在于母材基体中,会生成较大的第二相粒子,这些第二相粒子容易成为疲劳微裂纹的萌生点.1.2 试验方法焊接试验采用机器人CMT焊接方法,母材对接无间隙,坡口为70°,钝边为1 mm,单道焊接.焊接电流、电压、速度分别为94 A、17.8 V、0.36 m/min(在进行多组试验后选取了最优成形下的试验参数).金相试样使用Keller试剂(2.5 mL硝酸(HNO3)+1.5 mL盐酸(HCl)+1 mL氢氟酸(HF)+95 mL水(H2O))进行腐蚀,之后在显微镜(VHK-600K)下对焊缝、热影响区、母材等区域进行观察.焊接接头疲劳试样尺寸如图1所示.图1 焊接接头疲劳试样尺寸Fig.1 Schematic of welded joint fatigue specimen 疲劳试验在Zwick高频疲劳机上进行.为了观察表面疲劳裂纹的萌生和扩展,每个疲劳试样都必须进行抛光处理.疲劳试验结束后,使用扫描电子显微镜和能谱分析仪对疲劳试样进行分析.2 结果与分析2.1 焊接接头的微观组织分析焊接接头微观组织如图2所示.图2(a)是焊缝中心(WZ)处的微观组织图,从图中可以看出焊缝中心处等轴晶尺寸较小,且数量不多,多为100 μm以下的胞状树枝晶.这些胞状树枝晶的尺寸、大小不一,生长方向各有不同,且横向生长出的二次分支很短,除了少量的等轴晶和大量的胞状树枝晶外,焊缝中心还存在很多的小晶粒,尺寸约为10 μm,这些小晶粒一般分布于大晶粒之间.焊缝中心没有大晶粒的原因是由于CMT焊接过程中电弧搅拌作用强烈,使得晶粒无法长大.图2(b)是焊缝熔合区(FZ)的微观组织图.图中,左边是焊缝,右边是热影响区(HAZ),白色虚线是熔合线,熔合区是所有熔化焊焊接接头都存在的一个区域.从图2(b)中可以看到熔合区左边的晶粒多为胞状树枝晶,长度约为100 μm,方向均朝向焊缝中心,这与焊接过程中焊缝区中的温度梯度方向有关.同时在熔合线处存在明显的竞争生长与联生结晶特征,见图中方框中标出的区域.图2(c)是母材(BM)的微观组织图.从图中可以看出母材中晶粒呈长条状,说明母材是典型的轧制母材,轧制方向为从左到右.图中白色圆圈内还可以看到许多黑色的小颗粒,尺寸约为5 μm,形状不一,但是多为块状.根据Kumar等[7]的研究成果和后续的能谱分析可以断定其为AlSiFe相.该相不是6005A铝合金中的主要强化相,而是杂质Fe与母材Al以及残余的Si在母材进行热处理过程中生成的一种杂质相.当该相尺寸较小时,对母材的力学性能影响不大,如果尺寸过大则会影响到母材的性能.母材的晶粒长度和宽度可以按照图中多个晶粒的平均值求出,分别为100和10 μm.图2(b)中HAZ的晶粒尺寸可以由多个晶粒的平均值得出,分别为50和55 μm.由此可以看出,HAZ中的晶粒在熔池热循环的作用下出现了明显的长大,这种情况会严重降低接头的力学性能.同时在图2(b)中HAZ区域看不到任何AlSiFe相的存在,这说明HAZ在近焊缝区域内出现了AlSiFe相回溶.图2 焊接接头微观组织Fig.2 Microstructures of welded joint2.2 焊接接头硬度分析6005A铝合金CMT焊接接头的维氏硬度(HV)曲线如图3所示.图3 焊接接头硬度分布Fig.3 Hardness distribution of welded joint由图可知,整个曲线呈现V字形,坐标原点代表焊缝中心,横坐标代表距离焊缝中心的位置.从曲线分布上看,接头明显分为焊缝区和热影响区,其中过渡区为熔合区.焊缝区长度为3 mm左右,平均硬度为70.在距离焊缝中心3 mm处硬度陡降至50,结合图2(b)可以知道该位置是熔合区,这里的化学元素在熔池热作用的影响下极度不均匀,导致力学性能显著下降.以该点作为分界线向右进入热影响区,硬度上升至80;到6 mm处开始下降,最低至40;随后上下波动,平均硬度保持在55;到9 mm处又开始上升;13 mm处达到母材的硬度90,之后趋于稳定,说明13 mm位置点是母材和热影响区的交接点.在HAZ中距离焊缝中心6~10 mm的区域内,硬度一直保持在55左右,最低点甚至低于熔合区,仅为40,称之为软化区.铝合金焊接接头中产生软化区是由于材料在焊接过程中强化相出现了回溶和再析出造成的.这种现象使得软化区成为整个焊接接头中最薄弱的环节,但这种情况可以通过焊后热处理进行改善.2.3 焊接接头表面裂纹萌生分析焊接接头疲劳试样表面裂纹萌生及第二相粒子能谱图如图4所示.从图4(a)中可以看到许多白色的长条状第二相粒子,长度为15 μm左右,宽度为1 μm左右.经能谱分析发现是AlSiFe相粒子,如图4(b)所示,属于杂质相,其化学成分见表2.从微观组织分析中可以发现,在母材中存在较多的AlSiFe相粒子,这些粒子的尺寸为5 μm左右,呈不规则的块状.在电弧作用下,母材发生熔化,第二相粒子也一起熔化,但是在熔池冷却的过程中,Fe和焊丝中添加的Si受到基体结晶的排挤发生聚集,即发生了偏析,最后生成不同于母材中第二相粒子形状的长条状相.图4 焊接接头表面裂纹萌生位置及第二相粒子能谱图Fig.4 Crack initiationposition on surface of welded jointand second phase energy spectrum表2 第二相粒子的化学成分Table 2 Chemical composition of second-phase particle成分ω/%Al68.7Si25.6Fe5.7在这些粒子内部可以发现不止一处微裂纹,这些微裂纹几乎贯穿了整个第二相粒子.而且在一些第二相粒子中裂纹附近可以看到有明显的滑移线,即滑移线与第二相粒子的相交的地方会产生微裂纹.这是由于试样在受到疲劳循环载荷的作用时,焊接接头中部分晶粒内部的位错源被激活,开始向外释放位错,这些位错在遇到第二相粒子后会受到第二相粒子的钉扎作用而无法继续向前运动,导致其在第二相粒子处不断塞积,当塞积的位错超过一定界限后便会使第二相粒子断裂.但研究发现,所有第二相粒子中的裂纹都没有进一步的扩展,这说明位错塞积在破坏第二相粒子后能量得到了释放,剩余的能量不足以促使裂纹的进一步扩展,因此微裂纹只局限于第二相粒子内部.在图4(a)右上角的位置同样发现了一条第二相粒子,这条第二相粒子尺寸略小,且长度方向几乎垂直于其他粒子,在这个第二相粒子中没有观察到微裂纹的存在,这说明不是所有的第二相粒子在循环载荷作用下都会产生微裂纹,还要考虑其尺寸和方向.因此可以判断,AlSiFe相粒子对焊接接头的疲劳性能影响不大,甚至可以通过钉扎位错而提升材料的强度.3 结语1) 焊接接头分为焊缝区和热影响区,其中过渡区为熔合区.焊缝中心的组织以等轴晶和胞状树枝晶为主,且尺寸较小;近熔合线的焊缝区主要是小尺寸胞状晶;热影响区的晶粒发生了明显粗化;母材为轧制材料,含有AlSiFe第二相粒子.焊缝区中晶粒尺寸较小说明CMT焊接技术具有一定的细晶作用,可以有效提高接头性能.2) 从硬度曲线上看,热影响区长度为10 mm,且存在软化区,软化区硬度值最低,为55;焊缝处平均硬度为70;母材硬度值为90.软化区的存在会严重影响焊接接头的力学性能,可以通过焊后热处理进行改善.3) 在疲劳试样中,焊缝位置表面存在长条状的AlSiFe第二相粒子,且大部分粒子内部萌生了微裂纹,但是微裂纹未进一步扩展,说明该第二相粒子对接头的疲劳性能影响不大.参考文献:[1] 刘杰,杨景宏,王炎金,等.35 mm厚板铝合金搅拌摩擦焊接头组织和性能[J].焊接学报,2012,33(6):101-104.[2] 王炎金.铝合金车体焊接工艺[M].北京:机械工业出版社,2009.[3] HUANG J Q,XUE L,HUANG J F,et al.Arc behavior and joints performance of CMT welding process in hyperbaric atmosphere[J].Acta Metallurgica Sinica,2016,52(1):93-99.[4] SHU F Y,TIAN Z,LYU Y H,et al.Prediction of vulnerable zones based on residual stress and microstructure in CMT welded aluminum alloyjoin[J].Transactions of Nonferrous Metals Society of China,2015,25(8):2701-2707.[5] PICKIN,C G,WILLIAMS,S W,LUNT,M.Characterisation of the cold metal transfer(CMT)process and its application for low dilutioncladding[J].Journal of Materials Processing Technology,2011,211(3),496-502.[6] DING L P,JIA Z H,LIU Y Y,et al.The influence of Cu addition and pre-straining on the natural aging and bake hardening response of Al-Mg-Si alloys[J].Journal of Alloys and Compounds,2016,688:362-367.[7] KUMAR N,GOEL S,JAYAGANTHAN R,et al.Effect of solution treatmenton mechanical and corrosion behaviors of 6082-T6 Alalloy[J].Metallography Microstructure Analysis,2015,4(5):411-422.。
- 1、下载文档前请自行甄别文档内容的完整性,平台不提供额外的编辑、内容补充、找答案等附加服务。
- 2、"仅部分预览"的文档,不可在线预览部分如存在完整性等问题,可反馈申请退款(可完整预览的文档不适用该条件!)。
- 3、如文档侵犯您的权益,请联系客服反馈,我们会尽快为您处理(人工客服工作时间:9:00-18:30)。
疲劳性能;疲劳裂纹萌生中图分类号:UCHINA RAILWAY S文章编号:10 01—4632 (2014) 01 — 0067 —0 5咼速列车用6 0 6 5 A 铝合金超咼周疲劳性能试验研究闫桂玲,王弘,康国政,代景安(西南交通大学力学与工程学院,四川成都6 1 0 0 3 1) 摘 要:对圆柱形和板状2种6 0 6 5 A 铝合金试件进行20kHz, 06 010周次的对称拉压超声疲劳试验,并用扫描电镜显微分析技术分析疲劳断口。
结果表明:这2种形状的6065A 铝合金试件的S —N 曲线与传统无限寿命型疲劳曲线不同,而是呈现阶梯下降型特征,疲劳寿命大于10周次的试件仍会发生疲劳断裂;试件的疲劳裂纹以剪切方式沿与试件轴向成约4 5 °方向扩展;圆柱形试件S —N 曲线的阶梯下降型特征对应着疲劳裂纹的双萌生机制,在疲劳寿命较低的低周、高周阶段,试件表面局部应力或应变集中区成为 疲劳裂纹源;在寿命较高的超高周阶段,试件次表面或内部存在的缺陷成为疲劳裂 纹萌生有利的位置;板状试件的疲劳性能明显低于圆柱形试件,其疲劳裂纹呈现多 源形核特征,且以表面裂纹萌生为主。
关键词:高速列车;铝合金;超高周;第35卷, 中国铁道科学VO1.35NO.1CIENCE Janu20270.41:TG111.8 文献标识码:A doi:10.3969/jissn.1001—4632.2014.01.11 收稿日期:20 13 — 01—20 ;修订日期:2013 — 11 —01 基金项目:国家自然科学基金资助项目(8 7 2 1 7 5 );国家重点实验室自主研究课题项目(2011T PL_Z03) 作者简介:闫桂玲(7 9 —),女,河北保定人,博士研究生。
目前,我国高速列车车体和转向架结构均采用钢板焊接结构或铝合金焊接结构,从而大大降低了车体的重量。
除了要求轻质之外,高速列车用铝合金还必须具有更高的强度、韧性、耐疲劳、抗裂纹等性能。
用于机车车辆的铝合金主要有6 心>和7心>系列合金,如用于高速列车车体的6 0 0 5和7 0 0 3等型号的铝合金[1]。
目前,我国高速列车的速度已经超过了 3 0 0 km 山一1,这对其车体材料的实际使用寿命提出了更高的要求。
对碳钢、高强度钢和铝合金等材料进行的大于107周次的超高周疲劳试验研究结果表明,直到10 10周次疲劳破坏仍会发生[2-8]。
因此,研究高速列车用6 0 6 5 A铝合金1010周次内的超高周疲劳性能,对列车构件的疲劳寿命预测、损伤容限设计和可靠性评定都具有非常31 . 6重要的意义。
本文对圆柱形和板形6 0 6 5 A 铝合金试件分别进行对称拉压超 声疲劳试验和试件断口扫描电镜显微分析的微观试验,从而揭示6 0 6 5 A 铝合金 的超高周疲劳性能及其疲劳断裂机理。
1 试件和试验方法试件的材料为6 0 6 5 A 铝合金,其化学成分5 Mn , 0 . 4〜0. 7 M g,0 . 3 C r , 0 . 2 Z n , 0 .弹性模量/G P a 屈服强度/ M P a 断裂强度/M P a 密度/ ( k g m — 3 )断后伸长率/%断面收 缩率/% 6 73 5.9对称拉压超声疲劳试验中使用的试件有圆柱形和板状2种,如图1所示。
试件尺寸需满足系统谐振条件,为了得到频率为2OkHz 第1阶纵向振动试件尺寸的解析解,假设圆柱形和板状试样中间段纵剖面曲线分别为悬链线和指数曲线,根据超声疲劳拉压试件应力位移系数公式得到试样(质量分数,%)为0 . 5〜0 •i , 0 . 3 5 F e , 0 . 3 C u , 0 .主要力学性能见表1。
表1 6 5 A 铝合金力学性能的应力位移系数值。
但由于加工悬链线和指数形状困难,通常用圆弧线替代上述2 种曲线。
此种替代产生的应力位移系数的误差可以略去不计[9]。
为了得到更精确的应力位移系数值,采用有限元软件Ansys计算,得到圆柱形试件和板状试件的应力位移系数Cs分别为8.28和4.31 MPa -1。
试件表面粗糙度达到O .2阿。
1.2 宏观试验方法对称拉压超声疲劳试验的循环周次为1O6O1O周次,系统的振动频率范围为2OkHz,上下浮动2.1 宏观试验图1 对称拉压超声疲劳试验试件(单位:mm )不得超过0.5kHz ,有限元软件Ansys 计算试件的共振频率为200 7 1Hz 。
试验在室温条件下进行,由于试件在共振时会升温,用压缩空气制冷装置保证试件表面温度与室温相当。
.3 微观试验方法用扫描电子显微分析技术(ScanningElectronMicroscopy,SEM )分别观察圆柱形试件和板 状试件的疲劳断口形貌,观察疲劳裂纹萌生位置、裂纹源区和裂纹扩展区形貌,分 析2种试件疲劳断口形貌的异同,研究其疲劳断裂行为。
2 试验结果.05 X10对称拉压超声疲劳试验得到的结果见表2。
表2 不同形状试件的对称拉压超声疲劳试验结果试件编号圆柱形板状应力ca/MPa疲劳寿命Nf/周次应力ca/MPa疲劳寿命Nf/周次1 184 6.49 X106 180 3.8 7 X1 0 5 22. 66 X107 1 7 5 5.6 8 X1 0 5 3 2. X107065 4.931 .46 X1 64 173 8.89 X1 06 20 6 X162 8. 22 X107 15 3.87 X1 076 62X107 6.52 X1077 162 2.2 X107 1 1.09 X1078 .82 X107 .17 X105 5.47 X1 07 5 4.43 X1 10 472.27 X108 4.2 6 X1 0 7 1 1 8 X10810 1.41 X10812 132.05 X10图2 6 0 6 5 A 铝合金对称拉压超声疲劳试验曲线(S —N 曲线)1 0 5 2.21 X1 08131 0 XI根据表2得到65A 铝合金对称拉压超声疲劳试验曲线(S—N 曲线)(a )圆柱形试件由图2可见:①在疲劳寿命大于1周次的超高周阶段,试件仍然会发生疲劳断裂,这与传统常规疲劳认为试件在周次后不会发生疲劳破坏的观点不同。
由于用频率为10 0Hz的传统疲劳试方法完成109周次的试验用时为1 16d,而用20kHz的超声疲劳试验技术进行大于1周次的超高周疲劳试验可更精确地保证构件的安全性; ②疲劳S —N曲线在1 0 6〜10 10周次试验范围内表现出阶梯下降型特征,在1 0 7〜1周次范围内呈现水平平台特征,在大于10周次的超高周疲劳寿命区有第2个更低的疲劳极限值。
目前认为S —N曲线阶下降型特征是与疲劳裂纹双萌生机制有关;③板状试件的疲劳性能明显低于圆柱形试件;④2种试件的下降型S —N曲线与传统S —N曲线具有相同的趋势和规律,在对数坐标中呈线性关系,故可用Basqu in 方程 cra=cf (2 Nf)b描述(cf 为疲劳强度系数,b 为疲劳强度指数) ,具体结果标注于图2中。
2.2 微观试验2.2.1 宏观疲劳断口试验得到的圆柱形试件和板状试件宏观疲劳断口如图 3所示图3 疲劳试件宏观断口形貌中国铁道科学0 由图3可见:试件的疲劳裂纹以剪切方式沿与试件轴向成约45 °方向扩展。
一些学者在对6063铝合金[10]、LY12铝合金[11]的疲劳宏观断口观察时也观察到了这种现象。
.2.2 圆柱形试件微观疲劳断口用扫描电镜显微分析技术分别得到图2中2#,4#和11#圆柱形试件的疲劳断口SEM形貌,如图4 Ail rishi?图4 2#圆柱形试件疲劳断口SEM形—图6所示Chou Jowital EM^Iishin^ H OH翳,tiilpMwww-cnkLnel貌(次表面裂纹形核,N f = 2周次,(Ta =17 7. 3 MP a)图 5 4 #圆柱形试件疲劳断口S EM形貌(表面裂纹形核,N f = 8周次,era =17 2. 5 MP a)图 6 1 1 #圆柱形试件疲劳断口S EM形貌(次表面裂纹形核,N f = 1周次,era =14 7. 1 MP a)由图4 —图6可以看出:2 #圆柱形试件的疲劳裂纹在试件的次表面夹杂处萌生;4 #圆柱形试件表面有较多夹杂,疲劳裂纹在试件的表面夹杂处萌生;1 1圆柱形试件的疲劳裂纹在试件的次表面夹杂处萌生,试验数据点处在圆柱形试件疲劳S -N曲线的第2下降阶段;S —N曲线的阶梯下降型特征对应疲劳裂纹的双萌生机制。
通常认为,在疲劳寿命较低的低周阶段,疲劳裂纹在试件表面萌生,其萌生机理是在表面局部应力或应变集中区塑性累积形成疲劳裂纹。
对超高周范围内发生疲劳破坏的试件进行SEM分析,结果表明试件内部存在的缺陷成为疲劳裂纹萌生的有利位置,在很多含有夹杂和缺陷的材料中清晰地观察到了内部裂纹萌生的现象[1 2-13]。
在显微镜下,内部疲劳裂纹萌生的断口可以观察到非金属夹杂的存在,夹杂外侧有黑色的鱼眼形”裂纹,该区域呈现白色的粗糙形貌,不同学者对其有不同的命名,FGA(fine granular area),GBF(gr anular brightfacet )和ODA(opticallydark area等。
虽然目前疲劳裂纹在夹杂处萌生的机理还没有完全研究清楚,但在大多数金属材料中已经观察到了这种现象。
本试验中,同样处于高应力区的2#试件和4#试件,应力幅值相当,疲劳寿命却相差较大。
试验表明6 0 6 5 A铝合金的表面粗糙度、内部夹杂、第二相粒子的尺寸、分布等因素对裂纹的扩展具有重要影响,对材料的疲劳性能影响较大。
所以,减小60 6 5 A铝合金内夹杂、第二相粒子等微观缺陷的尺寸和数量,对提高疲劳性能具有积极作用。
.2.3 板状试件微观疲劳断口用扫描电镜显微分析技术分别得到图2中1#和13#号板状试件的疲劳断口SEM形貌,如图7、图8所示AU rigHj71994-2014OiiuAffiHlimi; Jamil El«livnkPubk如BtfHouiie rcHTvedL biLpi^/kijKi图7 1#板状试件疲劳断口SEM形貌(多源形核,N f = 3.87 X105周次,(ra =18 0 MPa) 由图7和图8可以看出:1#板状试件疲劳断口微观形貌呈现多源形核特征,裂纹在试件表面萌生;13#板状试件疲劳断口同样呈现多源形核特征,拐角应力集中处、表面加工缺陷处为疲劳裂纹源区,裂纹在试件的次表面夹杂处萌生,裂纹扩展区形貌可见疲劳辉纹,瞬断区有类似于韧性断裂的韧窝状断口;板状试件疲劳裂纹以表面裂纹形核为主,且由于板状试件四周存在应力集中、表面或内部夹杂等缺陷,板状试件的疲劳裂纹均呈现多源形核特征,这也与图2所示的板状试件疲劳性能明显低于圆柱形试件这一结论吻合。