先进塑性成形技术
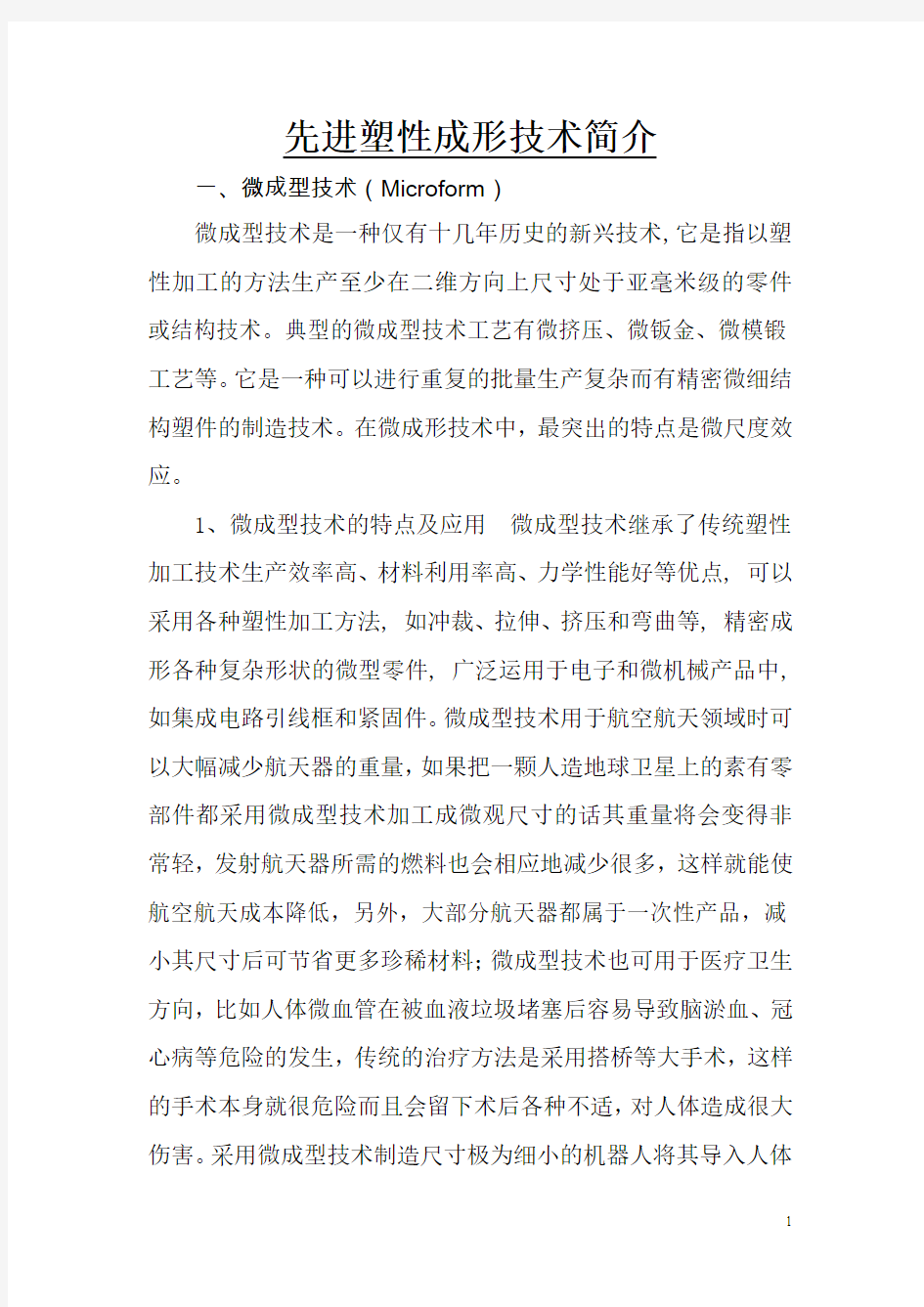
- 1、下载文档前请自行甄别文档内容的完整性,平台不提供额外的编辑、内容补充、找答案等附加服务。
- 2、"仅部分预览"的文档,不可在线预览部分如存在完整性等问题,可反馈申请退款(可完整预览的文档不适用该条件!)。
- 3、如文档侵犯您的权益,请联系客服反馈,我们会尽快为您处理(人工客服工作时间:9:00-18:30)。
先进塑性成形技术简介
一、微成型技术(Microform)
微成型技术是一种仅有十几年历史的新兴技术,它是指以塑性加工的方法生产至少在二维方向上尺寸处于亚毫米级的零件或结构技术。典型的微成型技术工艺有微挤压、微钣金、微模锻工艺等。它是一种可以进行重复的批量生产复杂而有精密微细结构塑件的制造技术。在微成形技术中,最突出的特点是微尺度效应。
1、微成型技术的特点及应用微成型技术继承了传统塑性加工技术生产效率高、材料利用率高、力学性能好等优点, 可以采用各种塑性加工方法, 如冲裁、拉伸、挤压和弯曲等, 精密成形各种复杂形状的微型零件, 广泛运用于电子和微机械产品中, 如集成电路引线框和紧固件。微成型技术用于航空航天领域时可以大幅减少航天器的重量,如果把一颗人造地球卫星上的素有零部件都采用微成型技术加工成微观尺寸的话其重量将会变得非常轻,发射航天器所需的燃料也会相应地减少很多,这样就能使航空航天成本降低,另外,大部分航天器都属于一次性产品,减小其尺寸后可节省更多珍稀材料;微成型技术也可用于医疗卫生方向,比如人体微血管在被血液垃圾堵塞后容易导致脑淤血、冠心病等危险的发生,传统的治疗方法是采用搭桥等大手术,这样的手术本身就很危险而且会留下术后各种不适,对人体造成很大伤害。采用微成型技术制造尺寸极为细小的机器人将其导入人体
血管后用其自带的微型道具便可以疏通血管减少病人的痛苦。
2、现阶段微成型技术领域微成型技术是一种只有十几年历史的新兴技术,其理论基础和制造技术还很不完善。现有的生产方法可以生产三维的单晶硅、纯金属和一些二元合金等微型部件, 在研究室中可以做出尺寸在微米级的齿轮等细小零部件,然而实际应用却并不多,并且多数情况下生产成本是非常高的, 且难以做到批量生产。但是由于这一技术的诸多优势和广泛的应用领域,许多世界工业发达国家,如美国、日本及欧洲各国投入了大量资金资助相关研究。美国国会把微电子机械系统作为21世纪重点发展的学科之一;日本政府和许多知名企业如Olympus等在微成型机械与微成型研究方面投入大量资金;德国研究技术部将微型机械系统列为新开发的重点项目,德国的CIRP成员也致力于微成型领域的研究。微成型技术未能得到广泛应用主要是因为对其研究时间短,有很多技术问题需要解决。
3、目前研究的主要技术问题:
A、微小尺度下材料的应力应变关系宏观下材料的应力与应变关系已为人所熟知,然而,当材料尺寸小到一定程度时宏观下的材料应力应变关系已不再适用,运用传统塑性成形工艺加工金属微型零件, 必须考虑尺度效应问题, 如零件的尺寸和形状、晶粒的大小和位置取向、摩擦作用和附着力等。它使得传统
的塑性加工工艺无法按相似理论比例缩小成形微型零件。当零件特征尺寸为微米量级时, 晶粒数量和缺陷减少, 位错效应发生
变化, 材料的塑性也随之改变; 零件的表面效应对尺度效应
发生显著影响, 表面积与体积之比( S/V) 随体积减小而增大, 与特征尺寸成反比。微小尺度小的应力应变关系掌握不了就很难加工出符合要求的微型零件。
B、模具的设计、制造由于微型模具的尺寸小, 加工精度高, 传统的模具制造方法已不能满足其要求。为了迎接微成型技术的挑战, 模具制造者们正在将铣削加工等传统的模具制造技术引入该领域, 并在不断开发研究新的加工方法。如瑞士的Momotec S. A 公司研究出利用紫外光和电铸技术制造模具嵌件的技术即LIGA 技术; 日本Sanyu 精密仪器公司以及美国Fraunhofer 研究所开发了微铣削技术; Fraunhofer 激光技术研究所开展了激光加工技术的研究。德国ThinXXS 微技术研究所的Luz. Weber认为各种加工方法可以通过其能加工的范围, 能达到的深宽比( Aspect Rat io) , 可加工的对象, 加工精度及生产效率来划分水平的高低。
除了以上两点最主要的技术难题外微成型技术大发展还要解决各向异性,表面积和体积之比增大对成型的影响;坯料材料的选择和制备;与微成型技术相关的测试技术还有如何利用数值模拟的方法去对微成型技术进行工艺等方面的模拟。只有真正解决这些问题才能使微成型技术走进人们的生活,造福社会,产生巨大经济效益。
二、超塑性成型/扩散连接技术(Superplastic Forming /
Diffusion Bonding,SPF/DB)
塑性是材料在某种给定载荷下产生永久变形而不破坏的能力。而超塑性是指材料在一定的内部条件和外部条件下,呈现出异常低的流变抗力、异常高的流变性能的现象。超塑性的特点有大延伸率,无缩颈,小应力,易成形。最近超塑性成形工艺将在航天、汽车、车厢制造等部门中广泛采用,所用的超塑性合金包括铝、镁、钛、碳钢、不锈钢和高温合金等。扩散连接是在一定的温度和压力下,经过一定的时间,连接界面原子间相互扩散,实现的可靠连接。可用于异种金属材料、陶瓷、金属间化合物、非晶态及单晶合金,在航空航天、仪表电子、机械化工及汽车制造领域有广泛应用。SPF/DB超塑性成形/扩散连接技术就是在超塑性下用扩散连接进行加工,这种加工技术集成了超塑性成形和扩散连接的优点,可以用于制造高精度大型零件和复杂零件的近无余量加工。
超塑性/扩散连接是在材料表现出超塑性的温度范围内进行的扩散连接, 它具有以下特征:1接合面无需抛光至镜面2可以在低温低压力下接合;3接合时问短;4接合强度高;5可与超塑性
成型同时进行。即它是利用超塑性流动和扩散实现连接、在短时问内获得高强度接合体的方法。
超塑成形/扩散连接的整体结构具有成形性好、设计自由度大、成形精确、无残余应力、零件数量少等优点,在减轻飞行器结构重量、降低生产成本方面显示极大的优越性,被誉为现代航
空航天工业生产的开创性技术。近些年来SPF/DB技术发展迅速,也得到了实际应用。例如,军用飞机需要有较高的机动性和良好的气动布局,这就需要机身有非常好的光洁度,而以往的方法仅仅是用铆钉把机身蒙皮铆接在机身上。这样生产出的飞机机身有很多铆钉,导致了机身光洁度很差。现代先进的军用战记如美国的F22,中国的J10都是采用SPF/DB技术将机身蒙皮直接焊接在机身上,所以其机身表面光滑阻力较小,有利于提高飞机的整体机动性能。可以说,美、欧等国的大型国防研究计划对于SPF、SPF/DB 技术的发展起到了至关重要的作用,尤其近年来先进武器装备作战性能越来越高,促使钛合金超塑成形整体结构在飞机、发动机、导弹、舰艇等工业领域的应用不断扩大,显示出旺盛的生命力,在已获得的工程应用领域内产生了巨大的技术经济效益:F-15E后机身结构采用SPF/DB整体结构后,减少了726个零部件,并取消了10000多个紧固件;联合战斗机(JSF)的后缘襟翼和副翼、F-22 后机身隔热板等重要结构均采用了钛合金超塑性成形/ 扩散连接的整体结构。
陶瓷材料以其固有的高熔点、高硬度、高耐磨性、耐氧化等优点在结构材料、刀具材料方面应用很广,又由于陶瓷还具有某些特殊的性能,又可作为功能材料。然而因为陶瓷质脆,且重量大工件整体又不可能全由陶瓷材料制成,所以陶瓷材料同基体材料的连接便成了关键。陶瓷之间的连接工艺主要有钎焊和扩散连接两种。而后者就是SPF/DB技术。在高温下施加一个压力,通