感应淬火与火焰淬火的区别及优势
表面淬火工艺
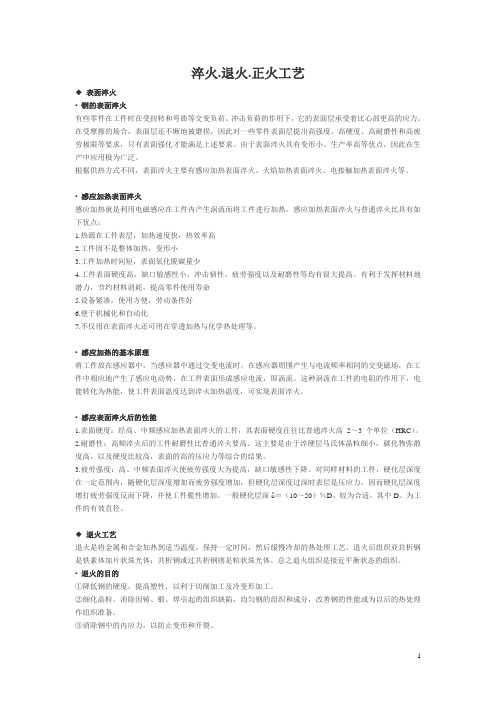
淬火.退火.正火工艺◆表面淬火• 钢的表面淬火有些零件在工件时在受扭转和弯曲等交变负荷、冲击负荷的作用下,它的表面层承受着比心部更高的应力。
在受摩擦的场合,表面层还不断地被磨损,因此对一些零件表面层提出高强度、高硬度、高耐磨性和高疲劳极限等要求,只有表面强化才能满足上述要求。
由于表面淬火具有变形小、生产率高等优点,因此在生产中应用极为广泛。
根据供热方式不同,表面淬火主要有感应加热表面淬火、火焰加热表面淬火、电接触加热表面淬火等。
• 感应加热表面淬火感应加热就是利用电磁感应在工件内产生涡流而将工件进行加热。
感应加热表面淬火与普通淬火比具有如下优点:1.热源在工件表层,加热速度快,热效率高2.工件因不是整体加热,变形小3.工件加热时间短,表面氧化脱碳量少4.工件表面硬度高,缺口敏感性小,冲击韧性、疲劳强度以及耐磨性等均有很大提高。
有利于发挥材料地潜力,节约材料消耗,提高零件使用寿命5.设备紧凑,使用方便,劳动条件好6.便于机械化和自动化7.不仅用在表面淬火还可用在穿透加热与化学热处理等。
• 感应加热的基本原理将工件放在感应器中,当感应器中通过交变电流时,在感应器周围产生与电流频率相同的交变磁场,在工件中相应地产生了感应电动势,在工件表面形成感应电流,即涡流。
这种涡流在工件的电阻的作用下,电能转化为热能,使工件表面温度达到淬火加热温度,可实现表面淬火。
• 感应表面淬火后的性能1.表面硬度:经高、中频感应加热表面淬火的工件,其表面硬度往往比普通淬火高2~3 个单位(HRC)。
2.耐磨性:高频淬火后的工件耐磨性比普通淬火要高。
这主要是由于淬硬层马氏体晶粒细小,碳化物弥散度高,以及硬度比较高,表面的高的压应力等综合的结果。
3.疲劳强度:高、中频表面淬火使疲劳强度大为提高,缺口敏感性下降。
对同样材料的工件,硬化层深度在一定范围内,随硬化层深度增加而疲劳强度增加,但硬化层深度过深时表层是压应力,因而硬化层深度增打疲劳强度反而下降,并使工件脆性增加。
低频静态整体感应加热淬火的明显优势
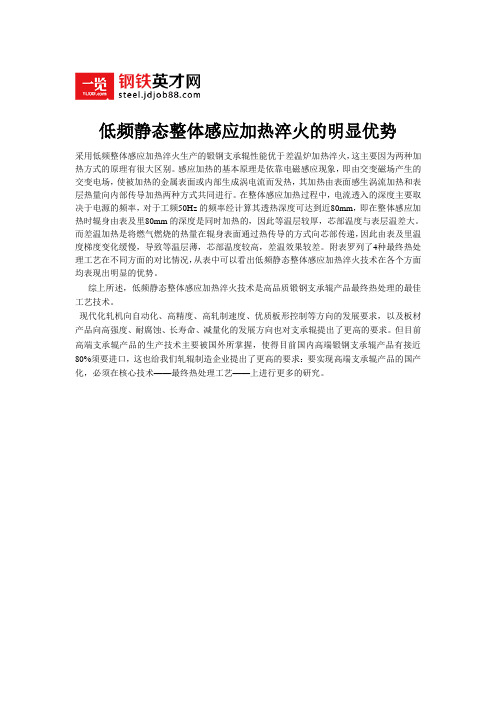
低频静态整体感应加热淬火的明显优势
采用低频整体感应加热淬火生产的锻钢支承辊性能优于差温炉加热淬火,这主要因为两种加热方式的原理有很大区别。
感应加热的基本原理是依靠电磁感应现象,即由交变磁场产生的交变电场,使被加热的金属表面或内部生成涡电流而发热,其加热由表面感生涡流加热和表层热量向内部传导加热两种方式共同进行。
在整体感应加热过程中,电流透入的深度主要取决于电源的频率,对于工频50Hz的频率经计算其透热深度可达到近80mm,即在整体感应加热时辊身由表及里80mm的深度是同时加热的,因此等温层较厚,芯部温度与表层温差大。
而差温加热是将燃气燃烧的热量在辊身表面通过热传导的方式向芯部传递,因此由表及里温度梯度变化缓慢,导致等温层薄,芯部温度较高,差温效果较差。
附表罗列了4种最终热处理工艺在不同方面的对比情况,从表中可以看出低频静态整体感应加热淬火技术在各个方面均表现出明显的优势。
综上所述,低频静态整体感应加热淬火技术是高品质锻钢支承辊产品最终热处理的最佳工艺技术。
现代化轧机向自动化、高精度、高轧制速度、优质板形控制等方向的发展要求,以及板材产品向高强度、耐腐蚀、长寿命、减量化的发展方向也对支承辊提出了更高的要求。
但目前高端支承辊产品的生产技术主要被国外所掌握,使得目前国内高端锻钢支承辊产品有接近80%须要进口,这也给我们轧辊制造企业提出了更高的要求:要实现高端支承辊产品的国产化,必须在核心技术——最终热处理工艺——上进行更多的研究。
表面淬火

3、高频感应加热表面淬火后的组织和性能
快速加热时钢的相变特点
1)临界温度升高,转变在较宽的温度范围内完成 2)奥氏体晶粒较细 3)奥氏体成分不均匀
ρ—工件电阻率 μ——工件的相对导磁率 f——电流频率 可见: 1)f愈高, δ小,淬硬层深度越浅。 2) ρ愈大, μ愈小,δ越大。
工频:50Hz,功率密度0.1~100W/cm2; 中频:<10kHz,功率密度< 5 W/cm2;
3.3、表面淬火
3.3 、表面淬火 3.3、表面淬火
• 要点:用快速加热法,使零件表面层很快地达到淬火温 度(A化),在热量传至内部之前,立即冷却使表 面层淬硬。 • 材料:中碳钢及中碳合金钢,如40、45、40Cr。 感应加热 • 分类(加热方法) 火焰加热 激光加热
(一)感应加热表面淬火
感应加热表面淬火示意图
下一页 返 回 金属热处理工艺 , SMSE,CUMT 本章首页 上一页
集肤效应示意图
表面淬火的发展
感应淬火原
50300
f
返 回
金属热处理工艺 , SMSE,CUMT
本章首页 上一页
下一页
返
回
金属热处理工艺 , SMSE,CUMT
本章首页 上一页
下一页
50300
f
2、分类(按电源频率)
预处理: 表面淬火前,须对零件进行正火或调质处理,以保证 零件心部具有良好的综合性能。 硬化层深度的确定: 抗磨损:1~6.5mm 抗疲劳:2~12mm 感应加热淬火温度 由于感应加热速度快,但组织转变又具有热滞后,为使组织 转变充分,所以感应加热温度应比常规加热温度提高30~50℃。 后处理: 表面淬火后,一般要对零件进行低温(160~200 ℃)回火 处理,以降低淬火应力和脆性。
各种淬火方法及其适用范围

各种淬火方法及其适用范围1. 第一种淬火方法是通过快速冷却金属材料以增加硬度和强度。
2. 水淬是一种常见的淬火方法,适用于中碳钢和高碳钢。
3. 油淬是另一种常见的淬火方法,适用于低合金钢和不锈钢。
4. 空气淬火适用于部分合金钢和精密零件,用以减少内部应力。
5. 盐浴淬火适用于高温合金钢和不锈钢,效果好且工艺复杂。
6. 固体表面淬火适用于需要局部提高硬度的工件,如齿轮或轴承。
7. 坩埚淬火适用于大型工件,能够在淬火中保持均匀的温度。
8. 悬浸淬火适用于金属丝和细小零件的表面硬化处理。
9. 感应淬火适用于需要精确控制加热和冷却的工件,如汽车零件和机械零件。
10. 激光淬火适用于需要局部加热的工件,效果快速且精准。
11. 火焰淬火适用于大型铸件或焊接接头的局部淬火。
12. 淬火渗碳适用于提高工件表面硬度和耐磨性,如齿轮和轴承。
13. 离子淬火适用于细小和复杂零件的表面强化处理。
14. 表面淬火适用于需要提高表面硬度的工件,如刀具和模具。
15. 淬火退火适用于同一工件先淬火后退火,以调整其组织和性能。
16. 淬火油是一种常用的冷却介质,适用于大多数碳钢和合金钢。
17. 淬火盐适用于提高淬火速度和表面质量,常用于碳化钢和合金钢。
18. 淬火水适用于快速冷却要求不高的低碳钢和中碳钢。
19. 淬火气体适用于需要精确控制冷却速度和保护表面的工件。
20. 淬火溶液适用于对淬火速度和表面质量要求高的合金钢和不锈钢。
21. 淬火工艺可根据工件材料和要求的硬度而定。
22. 淬火过程需要考虑工件的形状和尺寸,以保证其均匀性和质量。
23. 不同淬火方法对工件的影响有所不同,需根据具体情况选择合适的方法。
24. 淬火是金属热处理的重要环节,直接影响工件的使用性能。
25. 正确的淬火方法可以提高工件的硬度和强度,延长其使用寿命。
26. 淬火过程中要严格控制冷却速度和温度,以避免产生裂纹和变形。
27. 淬火后通常需要进行回火处理,以消除内部应力和提高韧性。
(工艺技术)退火、正火、淬火和回火热处理工艺比较

1.退火把钢加热到一定温度并在此温度下保温,然后缓慢冷却到室温.退火有完全退火、球化退火、去应力退火等几种。
a将钢加热到预定温度,保温一段时间,然后随炉缓慢冷却称为完全退火.目的是降低钢的硬度,消除钢中不均匀组织和内应力.b,把钢加热到750度,保温一段时间,缓慢冷却至500度下,最后在空气中冷却叫球化退火.目的是降低钢的硬度,改善切削性能,主要用于高碳钢.c,去应力退火又叫低温退火,把钢加热到500~600度,保温一段时间,随炉缓冷到300度以下,再室温冷却.退火过程中组织不发生变化,主要消除金属的内应力.2.正火将钢件加热到临界温度以上30-50℃,保温适当时间后,在静止的空气中冷却的热处理工艺称为正火。
正火的主要目的是细化组织,改善钢的性能,获得接近平衡状态的组织。
正火与退火工艺相比,其主要区别是正火的冷却速度稍快,所以正火热处理的生产周期短。
故退火与正火同样能达到零件性能要求时,尽可能选用正火。
3.淬火将钢件加热到临界点以上某一温度(45号钢淬火温度为840-860℃,碳素工具钢的淬火温度为760~780℃),保持一定的时间,然后以适当速度在水(油)中冷却以获得马氏体或贝氏体组织的热处理工艺称为淬火。
淬火与退火、正火处理在工艺上的主要区别是冷却速度快,目的是为了获得马氏体组织。
马氏体组织是钢经淬火后获得的不平衡组织,它的硬度高,但塑性、韧性差。
马氏体的硬度随钢的含碳量提高而增高。
4.回火钢件淬硬后,再加热到临界温度以下的某一温度,保温一定时间,然后冷却到室温的热处理工艺称为回火。
淬火后的钢件一般不能直接使用,必须进行回火后才能使用。
因为淬火钢的硬度高、脆性大,直接使用常发生脆断。
通过回火可以消除或减少内应力、降低脆性,提高韧性;另一方面可以调整淬火钢的力学性能,达到钢的使用性能。
根据回火温度的不同,回火可分为低温回火、中温回火和高温回火三种。
A 低温回火150~250.降低内应力,脆性,保持淬火后的高硬度和耐磨性.B 中温回火350~500;提高弹性,强度.C 高温回火500~650;淬火钢件在高于500℃的回火称为高温回火。
淬火时效及其材料的意义

淬火时效及其材料的意义淬火是把合金加热到固溶体溶解曲线上,保温一段时间,然后以大于临界冷却速度急速冷却,从而得到过饱和固溶体的热处理方法。
淬火的目的:强化钢件,充分发挥钢材性能的潜力.如:提高钢件的机械性能,诸如硬度、耐磨性、弹性极限、疲劳强度等,改善某些特殊钢的物理或者化学性能,如增强磁钢的铁磁性, 提高不锈钢的耐蚀性等。
淬火后对不同合金的性能也有所不同:对铝合金及大多数有色金属合金而言,经过淬火,不同合金也有不同①。
增加,6或W减少②。
减少,3或W增加③。
增加,6或W增加④。
、6、ψ基本不变淬火后性能出现差异的原因:固溶强化与第二相(或称过剩相,表示与固溶体平衡的其他相)强化之间的差异造成的。
若淬火前第二相的强化效果<淬火后固溶强化效果,则淬火后合金强度增加;反之淬火前第二相的强化效果>淬火后固溶强化效果,则淬火后合金强度减少。
钢的淬火:将钢件加热到AC3或ACl相变点以上的某一温度,保持一段时间,然后以大于Vk的速度冷却,获得马氏体或下贝式体组织的热处理工艺。
淬火后必须进行回火处理。
回火的目的是:⑴降低脆性,消除应力,防止钢件变形甚至开裂。
⑵获得工件所需要的力学性能,调整硬度,减小脆性,得到韧性和塑性。
⑶稳定工件尺寸,因为马氏体是不稳定组织。
淬火是提高材料的强度和硬度,就是材料抗弯曲扭曲变形的能力和抗划痕的能力,可淬火后材料内部有很高的内应力,容易降低材料的疲劳强度(就是材料抵抗中高频率轻微震动产生裂纹的能力),回火可以有效的去处材料的内应力一般根据具体应用不同可以分为淬火 +高温回火(就是调质处理),淬火+中温回火和淬火+低温回火,淬火的目的是使材料内部形成马氏体组织,不同材料的结晶温度也不一样,要使此种材料在何种温度下及在某一温度段保温时间都很有讲究,是非常专业的一门学科,所以选用的淬火介质和多少材料使用多少淬火介质溶液都有相当高的要求。
表面淬火钢的表面淬火有些零件在工件时在受扭转和弯曲等交变负荷、冲击负荷的作用下,它的表面层承受着比心部更高的应力。
《表面感应加热淬火》课件
涡流影响
介绍感应加热中涡流的产生及其影响。
淬火原理
讲解淬火基本原理,包括淬火介质的选择和淬火过程。
设备
发生器
介绍感应加热的设备原理,包括 发生器的工作原理和调制器。
感应线圈
讲解感应线圈的结构和作用。
淬火设备
介绍淬火设备的类型和工作原理。
应用
1
钢铁
介绍表面感应加热淬火在钢铁行业中的应用。
2
有色金属
《表面感应加热淬火》 PPT课件
表面感应加热淬火PPT课件介绍了表面感应加热淬火的基本原理和应用领域, 讲解了感应加热中磁感应强度和涡流的影响,以及淬火的原理和设备类型, 还探讨了表面感应加热淬火在不同领域的应用及其未来发展趋势。
简介
介绍表面感应加热淬火基本原理和应用领域。
原理
磁感应强度
讲解磁感应强度的计算方法。
介绍表面感应加热淬火在有色金属加工中的应用。
3
机械加工
介绍表面感应加热淬火在机械加工领域中的应用。
结论
1 优点
总结表面感应加热淬火的优点。
2 局限性
总结表面感应加热淬火的局限性。
3 未来发展
展望表面感应加热淬火的未来术资料,供读者参考。
淬火介绍
淬火介绍(1)钢的淬火淬火时将钢加热到Ac3或Ac1以上,保温一定时间使其奥氏体化,再以大于临界冷却速度快速冷却,从而发生马氏体转变的热处理工艺。
淬火钢得到的组织主要是马氏体(或下贝氏体),此外,还有少量残余奥氏体及未溶的第二相。
淬火的目的是提高钢的硬度和耐磨性。
1、淬火加热温度碳钢的淬火加热温度可利用Fe-Fe3C相图来选择。
对于亚共析碳钢,适宜的淬火温度为Ac3+30~50℃,使碳钢完全奥氏体化,淬火后获得均匀细小的马氏体组织。
对于过共析碳钢,适宜的淬火温度为Ac1+30~50℃。
淬火前先进行球化退火,使之得到粒状珠光体组织,淬火加热时组织为细小奥氏体晶粒和未溶的细粒状渗碳体,淬火后得到隐晶马氏体和均匀分布在马氏体基体上的细小粒状渗碳体组织。
对于低合金钢,淬火加热温度也根据临界点Ac1或Ac3来确定,一般为Ac1或Ac3以上50~100℃。
高合金工具钢中含有较多的强碳化物形成元素,奥氏体晶粒粗化温度高,故淬火温度亦高。
2、淬火加热时间为了使工件各部分完成组织转变,需要在淬火加热时保温一定的时间,通常将工件升温和保温所需的时间计算在一起,统称为加热时间。
影响淬火加热时间的因素较多,如钢的成分、原始组织、工件形状和尺寸、加热介质、炉温、装炉方式及装炉量等。
钢在淬火加热过程中,如果操作不当,会产生过热、过烧或表面氧化、脱碳等缺陷。
过热是指工件在淬火加热时,由于温度过高或时间过长,造成奥氏体晶粒粗大的现象。
过热不仅使淬火后得到的马氏体组织粗大,使工件的强度和韧性降低,易于产生脆断,而且容易引起淬火裂纹。
对于过热工件,进行一次细化晶粒的退火或正火,然后再按工艺规程进行淬火,便可以纠正过热组织。
过烧是指工件在淬火加热时,温度过高,使奥氏体晶界发生氧化或出现局部熔化的现象,过烧的工件无法补救,只得报废。
(2)钢的表面淬火表面淬火是对工件表层进行淬火的工艺。
它是将工件表面进行快速加热,使其奥氏体化并快速冷却获得马氏体组织,而心部仍保持原来塑性、韧性较好的退火、正火或调质状态的组织。
《钢的表面淬火》课件
表面淬火的原理
钢的相变点
钢的相变点:钢在加热过程中,从固态转变为液态的温度点
相变点温度:钢的相变点温度通常在1300-1500摄氏度之间
相变点影响:相变点温度对钢的淬火效果有重要影响
淬火原理:钢的表面淬火是通过快速冷却,使钢的表面达到相变点温度,形成马氏 体组织,提高钢的硬度和耐磨性。
钢的加热过程
添加项标题
钢的相变主要包括奥氏体相变、马氏体相变和贝氏体相变
添加项标题
马氏体相变是指钢在冷却过程中,其内部组织结构由奥氏体 转变为马氏体的过程
添加项标题
钢的相变是表面淬火的基础,通过控制钢的相变过程,可以 实现钢的表面淬火,提高钢的硬度和耐磨性。
表面淬火的工艺 方法
火焰加热法
原理:利用火焰的高温对 钢的表面进行加热
加热温度:根据钢的种类和淬 火要求,选择合适的加热温度
加热时间:根据钢的种类和淬 火要求,选择合适应加热、电阻加热等
加热过程中的温度控制:确保 钢的温度均匀,避免局部过热 或过冷
钢的冷却过程
加热:将钢加热到 一定温度,使钢内 部达到奥氏体状态
冷却:将钢迅速冷 却到临界温度以下, 使钢内部形成马氏 体组织
回火:将钢加热到 一定温度,使马氏 体组织转变为回火 马氏体组织
冷却:将钢冷却到 室温,使回火马氏 体组织保持稳定
钢的相变
添加项标题
钢的相变是指钢在加热或冷却过程中,其内部组织结构发生 变化的现象
添加项标题
奥氏体相变是指钢在加热过程中,其内部组织结构由铁素体 转变为奥氏体的过程
添加项标题
贝氏体相变是指钢在冷却过程中,其内部组织结构由奥氏体 转变为贝氏体的过程
离子注入技术: 通过离子注入 改变材料表面 成分和结构, 实现表面淬火
5点,机械零件感应淬火的主要目的有哪些?
5点,机械零件感应淬火的主要目的有哪些?
1.提高零件表面的耐磨性
感应淬火最初应用于曲轴颈表面,其目的就是为提高轴颈的耐磨性,在此以前曲轴是采用调质的,感应淬火使曲轴颈的耐磨性大大提高。
2.提高零件的疲劳强度
感应淬火进一步的应用是提高淬火件的疲劳强度,例如汽车半轴,以EQ1092汽车半轴为例,在±3000N·M扭转载荷下,疲劳试验200万次,仍然完好无损,而原来调质工艺,半轴的疲劳寿命不到30万次,又如转向节球头销原工艺为18CrMnTi钢渗碳淬火,后改用45钢感应淬火,零件的弯曲疲劳寿命从8万次提高到200万次以上。
曲轴圆角感应淬火则使曲轴的疲劳强度提高一倍,有些产品曲轴疲劳强度达到≥700MPa。
3.减少畸变
渗碳齿轮由于工艺时间长,淬火后畸变大;而齿轮感应淬火,特别是同步双频(SDF)齿轮淬火,工艺时间短,畸变小,使齿轮精度提高,噪声减低。
4.节能、节材、节省劳动力与环保
采用低谇透性钢制造齿轮等零件,用感应淬火,它首先是钢材无合金元素,节省了材料费用;感应加热是局部加热淬火,时间短,因此大大节能;感应淬火可实现自动化在线生产,这样节省了劳动力,无油污、无有害气体排放,更加保护环境。
5.取代深层渗碳
深层渗碳是周期长,电耗大的工艺。
近年来国外已研发成功用感
应淬火来取代深层渗碳,取得了很好效果。
版权所有,转载注明出处。
- 1、下载文档前请自行甄别文档内容的完整性,平台不提供额外的编辑、内容补充、找答案等附加服务。
- 2、"仅部分预览"的文档,不可在线预览部分如存在完整性等问题,可反馈申请退款(可完整预览的文档不适用该条件!)。
- 3、如文档侵犯您的权益,请联系客服反馈,我们会尽快为您处理(人工客服工作时间:9:00-18:30)。
感应淬火与火焰淬火的区别及优势
感应淬火的原理
感应加热表面淬火,是利用电磁感应、集肤效应、涡流和电阻热等电磁原理,使工
件表层快速加热,并快速冷却的热处理工艺
感应加热表面淬火时,将工件放在铜管制成的感应器内,当一定频率的交流电通过
感应器时,处于交变磁场中的工件产生感应电流,由于集肤效应和涡流的作用,工件表
层的高密度交流电产生的电阻热,迅速加热工件表层,很快达到淬火温度,随即喷水冷
却,工件表层被淬硬
感应加热时,工件截面上感应电流的分布状态与电流频率有关。电流频率愈高,集
肤效应愈强,感应电流集中的表层就愈薄,这样加热层深度与淬硬层深度也就愈薄
因此,可通过调节电流频率来获得不同的淬硬层深度。
感应淬火与火焰淬火的区别和优势
表面热处理是通过改变零件表层组织,以获得硬度很高的马氏体,而保留心部韧性
和塑性(即表面淬火),或同时改变表层的化学成分,以获得耐蚀、耐酸、耐碱性,及表面
硬度比前者更高(即化学热处理)的方法。
感应淬火:感应加热速度极快,只需几秒或十几秒。淬火层马氏体组织细小,机械
性能好。工件表面不易氧化脱碳,变形也小,而且淬硬层深度易控制,质量稳定,操作
简单,特别适合大批量生产。常用于中碳钢或中碳低合金钢工件,例如45、40Cr、40Mn
B等。也可用于高碳工具钢或铸铁件,一般零件淬硬层深度约为半径的1/10时,即可得
到强度、耐疲劳性和韧性的良好配合。感应加热表面淬火不宜用于形状复杂的工件,因
感应器制作困难
表1-1 感应加热种类及应用范围
感应加热 类型 常用频率 一般淬硬层深
度/mm
应 用 范 围
高频 200~1000kHz 0.5~2.5 中小模数齿轮及中小尺寸的轴类零件
中频 1~10kHz 2~10 较大尺寸的轴和大中模数齿轮
超音频 30~36kHz 淬硬层能沿工件轮廓分 中小模数齿轮
工频 50Hz 10~20
较大直径零件穿透加热,大直径零件如轧
辊、火车车轮的表面淬
感应淬火的优点
1表层硬度比普通淬火高2-3HRC,并具有较低的脆性:
2疲劳强度,冲击韧性都有所提高,一般工件可提高20-30%:
3变形小:
4淬火层深度易于控制:
5淬火时不易氧化和脱碳:
6可采用较便宜的低淬透性钢:
7操作易于实现机械化和自动化,生产率高
8电流频率愈高,淬透层愈薄。
火焰淬火的原理
火焰表面淬火:是用乙炔-氧或煤气-氧的混合气体燃烧的火焰,喷射到零件表面上,
快速加热,当达到淬火温度后,立即喷水或用乳化液进行冷却
淬透层深度一般为2-6mm,过深往往引起零件表面严重过热,易产生淬火裂纹。
表面硬度:钢可达HRC65,灰铸铁为HRC40-48,合金铸铁为HRC43-52
这种方法简便,无需特殊设备,但易过热,淬火效果不稳定,因而限制了它的应用
适用于单件或小批生产的大型零件和需要局部淬火的工具或零件,如大型轴类、大模数
齿轮等
常用钢材为中碳钢,如35、45及中碳合金结构钢(合金元素<3%),如40Cr,65Mn等,
还可用于灰铸铁、合金铸铁件。
碳含量过低,淬火后硬度低,而碳和合金元素过高,则易碎裂,因此,以含碳量右
0.35-0.5%之间的碳素钢最适宜。
常用中碳钢(0.4-0.5%C)和中碳合金结构钢,也可用高碳工具钢和低合金结构钢,以
及铸铁。
对于小直径10-20mm的零件,建议用较深的淬透层深度,即可达半径的1/5;一般零
件淬透层深度为半径的1/10左右时,可得到强度、耐疲劳性和韧性的最好配合。对于截
面较大的零件可取较浅的淬透层深度,即小于半径1/10以下。
表1-2感应淬火、火焰淬火、电炉淬火后碳钢的疲劳强度比较
含碳量% 热处理方法 扭转弯曲疲劳强度
0.33 高频表面淬火 600
0.33 火焰表面淬火 350
0.33 电炉内整体加热淬火 90
0.41 高频表面淬火 600
0.41 电炉内整体加热淬火 110
0.41 正火 130
0.63 高频表面淬火 360
0.63 火焰表面淬火 390
0.63 电炉内整体加热淬火 150
恒进科技,专业生产感应淬火成套设备,QQ:2502249701。如果您的产品需要感应
加热,恒进科技将为您提供完善的解决方案与周到的服务!我们提供的设备属于全自动
化成套设备,包括数控淬火机床、IGBT中高频电源、冷却机组、变压器等。