板坯连铸机粘接漏钢事故分析.doc
板坯连铸机粘结漏钢的原因分析及预防 刘雷锋

板坯连铸机粘结漏钢的原因分析及预防刘雷锋摘要:随着连铸技术的发展和广泛应用,连铸坯的质量和品质受到了人们的广泛关注,提高连铸坯的质量成为连铸生产中重点关注的问题之一。
连铸过程开始广泛运用于有色金属行业,尤其是铜和铝。
连铸技术迅速发展起来。
本文对此进行了分析研究。
关键词:坯;连铸;连铸工艺连铸漏钢是个常见现象。
钢水在结晶器内形成坯壳,连铸坯出结晶器后,薄弱的坯壳抵抗不住钢水静压力,出现断裂而漏钢。
对于薄板坯连铸来说更易发生漏钢事故。
漏钢对连铸生产危害很大。
即影响了连铸车间的产量,又影响了连铸坯的质量,更危及操作者的安全。
因此,降低薄板坯连铸漏钢率是提高生产效率,提高产量,提高产品质量,降低成本的重要途径。
现对某厂自2008~2013年薄板坯漏钢率进行统计。
2008年漏钢率达0.56%;2009年漏钢率达0.19%;2010年漏钢率达0.19%;2011年漏钢率达0.19%;2012年漏钢率达0.15%;2013年漏钢率达0.07。
1 工艺流程某厂第一钢轧厂工艺流程为:鱼雷罐供应铁水/混铁炉供应铁水→铁水预处理→转炉炼钢→氩站→精炼→薄板坯连铸2 薄板坯漏钢类型某厂薄板坯连铸漏钢主要有:粘结漏钢、裂纹漏钢、卷渣漏钢、开浇漏钢、鼓肚漏钢五个类型。
3 薄板坯漏钢特征、原因及预防措施3.1 粘结漏钢粘结漏钢是指钢水直接与结晶器铜板接触形成粘结点,粘结点处坯壳与结晶器壁之间发生粘结,此处在结晶器振动和拉坯的双重作用下被撕裂,并向下和两侧扩展,形成倒“V”形破裂线,钢水补充后又形成新的粘结点,这一过程反复进行,粘结点随坯壳运动不断下移,此处坯壳较薄,出结晶器后,坯壳不能承受上部钢水的静压力,便会发生漏钢事故。
据统计,粘结漏钢发生率最高,高达50%以上。
(1)铸坯粘结漏钢后特征。
粘结漏钢后铸坯特征。
坯壳呈“V”字型或“倒三角”状,粘结点明显。
(2)粘结漏钢的原因:1)保护渣性能不好。
保护渣在结晶器铜板与凝固坯壳之间起润滑的效果。
板坯连铸机粘结漏钢的原因分析及解决措施
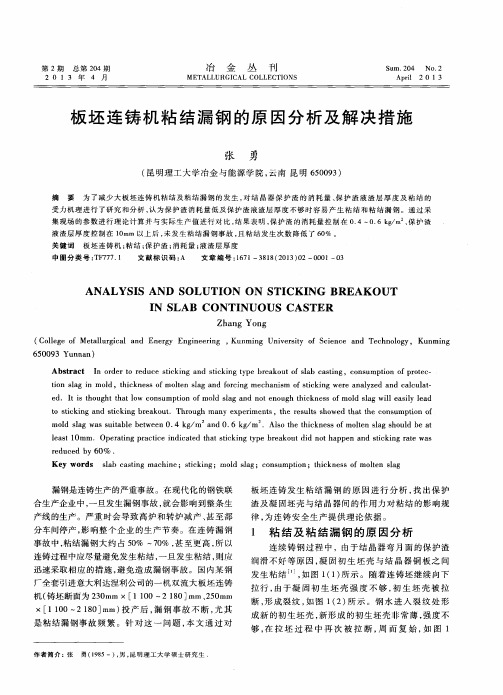
漏 钢是连铸生产的严重事故。在现代化 的钢铁联
板坯 连 铸发 生粘 结 漏 钢 的原 因进 行 分 析 , 找 出保 护 渣及 凝 固坯壳 与 结 晶器 间的作 用力 对粘 结 的影 响规 律, 为连 铸安 全生 产 提供理 论依 据 。
张 勇
( 昆明理 工大 学 冶金 与能 源学 院 , 云南 昆 明 6 5 0 0 9 3 )
摘 要 为 了减 少 大 板 坯 连 铸 机 粘 结 及 粘 结 漏 钢 的 发 生 , 对结 晶器保 护渣 的消耗 量 、 保 护 渣 液 渣 层 厚 度 及 粘 结 的
受 力 机 理 进 行 了研 究 和 分 析 , 认 为保 护 渣 消 耗 量 低 及 保 护 渣 液 渣 层 厚 度 不 够 时 容 易 产 生 粘 结 和 粘 结 漏 钢 。 通 过 采 集 现 场 的参 数 进 行 理 论计 算 并 与 实 际 生 产 值 进 行 对 比 , 结果表 明 , 保 护 渣 的消 耗 量 控 制 在 0 . 4~0 . 6 k g / m 、 保 护 渣
板坯连铸机漏钢成因分析及预防措施

;: 常规板坯连铸机参数及漏钢情况
; 5 9: 常规板坯连铸机的主要工艺参数 酒钢第二炼钢常规板坯连铸机主要工艺参数见 表 8。
第 ! 期8 8 8 8 8 8 8 8 8 8 8 8 程子建: 板坯连铸机漏钢成因分析及预防措施8 8 8
表 !" !##$ % !##& 年逐月漏钢情况
项目 产量 ( +) 综合合格率 (, ) 漏钢次数 !""# 年 %月 )’ """ **- )) ’ !月 $* #’* **- ) % &月 )) %#" **- $ ! ’月 $$ ("" **- )# % (月 ** ’&# **- ) % #月 )# &!$ **- )’ % $月 )" ((’ **- *’ & )月 $% $&# **- *& " *月 #% *&* **- *& " %" 月 !* ($& **- *! " %% 月 ($ )&" **- *$ " %! 月 $$ !’) **- *) " !""$ 年 %月 #"#&) **- *) " !月 #"""" **- *( " 合计
(
% "%’ (*" **- )* %&
表 ’" 漏钢情况统计结果
次数 % ! & ’ ( # $ ) * %" %% %! %& 时间 !""#."%."! !""#."%.%" !""#."%.&" !""#."%.&" !""#."!.%! !""#."&.") !""#."&.%# !""#."’.%! !""#."(.%( !""#."#.!( !""#."$."$ !""#."$.%$ !""#."$.%) 钢种 //’"" //’"" //’"" //’"" //’"" //’"" 5!&(67 5!&(6 5!&(6 ( 改) 5!&(67 ( 改) 5!&(67 ( 改) 5!&(67 ( 改) 5!&(67 ( 改) 规格 %#" 0 (!" %#" 0 (!" !!" 0 (&" !!" 0 (&" !!" 0 (&" !!" 0 (&" !!" 0 (&" !!" 0 (&" !!" 0 (&" !!" 0 (&" !!" 0 (&" !!" 0 (&" !!" 0 (&" 炉次 换包第 ! 炉 换包第 ! 炉 换包第 ! 炉 第( 炉 第) 炉 第 %& 炉 第( 炉 第# 炉 第 %! 炉 第* 炉 第# 炉 第) 炉 第( 炉 拉速 %- ! 1 2 134 %- !& 1 2 134 %- "( 1 2 134 %- " 1 2 134 %- "( 1 2 134 %- "& 1 2 34 %- "( 1 2 134 "- $( 1 2 134 "- *( 1 2 134 %- ") 1 2 134 %- " 1 2 134 %- " 1 2 134 "- $( 1 2 134 漏钢位置 内弧距坯头 #(" 11, 中间位置 内弧出结晶器, 距坯头 )%" 11, 中间位置 内弧中部距坯头 *"" 11 处 内弧中部偏西距结晶器上口 *"" 11 处 漏钢部位位于窄右出结晶器足辊位置 内外弧距结晶器上口 % &)" 11 外弧正中部, 漏钢点距结晶器上口 )(" 11 外弧中部偏西距结晶器上口 )"" 11 处 内弧出结晶器, 距坯头 )%" 11, 中间位置 内弧出结晶器下口位置 外弧宽面下口处 漏钢位置在结晶器窄左距上口 % 1 处 外弧宽面结晶器下口中部 漏钢形式 粘结漏钢 粘结漏钢 粘结漏钢 粘结漏钢 粘结漏钢 卷渣漏钢 粘结漏钢 粘结漏钢 粘结漏钢 粘结漏钢 粘结漏钢 机械外力划破坯壳 粘结漏钢
黑色冶金技术《连铸机漏钢事故分析4》

连铸机漏钢事故分析4一、事故经过丁白班发生漏钢事故。
经分析此次漏钢为粘结漏钢,漏钢发生在外弧侧,此次漏钢更换了结晶器和弯曲段,一段有局部粘钢,在线清理后继续使用。
二次拉钢开浇时间为18:46分,漏钢处理5小时零8分钟。
事故经过为:发生漏钢的炉次为快换中包第一炉,钢种Q235B,铸机等钢水到站大包未测温,中包温度为1542〔℃〕,钢水成分未见异常。
本炉次13:19分大包开浇,13:21分中包开浇。
〔1〕开浇后,待结晶器内钢液面没过坯壳后,试棒,再开流,待液面上升正常后,启动拉矫,拉速升至0.3m/min。
此时主控室通知结晶器外弧第9、8、3个热电偶温度异常,中包工立即停拉矫收流;〔2〕再次启动拉矫后,拉速升至0.3m/min,主控室再次通知结晶器外弧第9个热电偶温度仍异常,中包工打到拉速爬行状态,收流观察坯壳未见异常。
〔3〕主控通知第9个热电偶温度异常消除,中包工开流操作上升液面,拉速由0.3m/min自动升至0.4m/min,开始更换结晶器内的旧保护渣;〔4〕保护渣更换完毕后,缓慢提速至0.6m/min,此时,结晶器北侧的中包工发现内弧露出坯壳〔换包后7分钟,漏钢前10分钟〕,立即停拉矫。
〔5〕停拉矫几秒后,再次启动拉矫,拉速升至0.3m/min,收流观察液面及坯壳未见异常,拉速自动升至0.4 m/min;〔6〕提速至0.5 m/min时,再次收流观察液面及坯壳,无异常,缓慢升速至0.6 m/min时,结晶器南侧的操作工发现外弧露出坯壳,立即打到爬行拉速,收流观察液面及坯壳,无异常后,升速至0.3 m/min,再次收流观察液面及坯壳,无异常后开大流升液面缓慢提速至0.70 m/min时发生漏钢。
漏钢点发生在外弧侧,距换包接头距离为3200mm,踞结晶器液面为800mm,踞结晶器左窄面为900mm,位于热电偶第4、5位置。
漏钢时水口插入深度为140mm,塞棒行程82mm。
漏钢前热电偶有波动,北侧结晶器液面有结壳现象。
连铸机典型漏钢的特征及成因分析
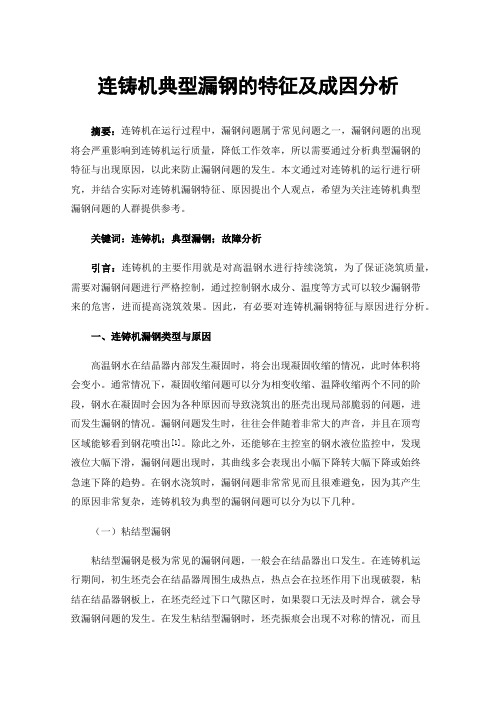
连铸机典型漏钢的特征及成因分析摘要:连铸机在运行过程中,漏钢问题属于常见问题之一,漏钢问题的出现将会严重影响到连铸机运行质量,降低工作效率,所以需要通过分析典型漏钢的特征与出现原因,以此来防止漏钢问题的发生。
本文通过对连铸机的运行进行研究,并结合实际对连铸机漏钢特征、原因提出个人观点,希望为关注连铸机典型漏钢问题的人群提供参考。
关键词:连铸机;典型漏钢;故障分析引言:连铸机的主要作用就是对高温钢水进行持续浇筑,为了保证浇筑质量,需要对漏钢问题进行严格控制,通过控制钢水成分、温度等方式可以较少漏钢带来的危害,进而提高浇筑效果。
因此,有必要对连铸机漏钢特征与原因进行分析。
一、连铸机漏钢类型与原因高温钢水在结晶器内部发生凝固时,将会出现凝固收缩的情况,此时体积将会变小。
通常情况下,凝固收缩问题可以分为相变收缩、温降收缩两个不同的阶段,钢水在凝固时会因为各种原因而导致浇筑出的胚壳出现局部脆弱的问题,进而发生漏钢的情况。
漏钢问题发生时,往往会伴随着非常大的声音,并且在顶弯区域能够看到钢花喷出[1]。
除此之外,还能够在主控室的钢水液位监控中,发现液位大幅下滑,漏钢问题出现时,其曲线多会表现出小幅下降转大幅下降或始终急速下降的趋势。
在钢水浇筑时,漏钢问题非常常见而且很难避免,因为其产生的原因非常复杂,连铸机较为典型的漏钢问题可以分为以下几种。
(一)粘结型漏钢粘结型漏钢是极为常见的漏钢问题,一般会在结晶器出口发生。
在连铸机运行期间,初生坯壳会在结晶器周围生成热点,热点会在拉坯作用下出现破裂,粘结在结晶器钢板上,在坯壳经过下口气隙区时,如果裂口无法及时焊合,就会导致漏钢问题的发生。
在发生粘结型漏钢时,坯壳振痕会出现不对称的情况,而且在多数时间都会在结晶器的内部残留一截坯壳。
粘结型漏钢的出现原因大致可以分为以下几种。
1.保护渣当保护渣自身的理化性能无法与钢种、钢水温度等参数匹配时,就有可能出现粘结型漏钢的问题,因为保护渣的熔化速度、熔点等参数性能都将会影响到连铸机的浇筑质量。
3%b8Q345B板坯粘结漏钢的原因分析和预防措施

晶器的倒锥度比较大。有关文献表明:在拉钢 过程中。结晶器的振动有防止初生坯壳同结晶
器壁发生粘结而被拉破以及在负滑脱期间愈合 已拉裂坯壳的作用,因此,合理的振动参数是 稳定连铸拉钢的必要条件。结晶器振动对结晶
铺展性变差,摩擦力增大。
4.2钢水的影响 钢水过热度的高低和钢水中夹杂物的含量
对钢水在结晶器中是否发生粘结甚至漏钢有直 接的影响,钢水过热度对粘结漏钢的影响主要反 映在钢液表面张力上。一般认为,随着温度的
升高。钢液表面张力逐渐减少。Eotvos提出的实
器保护渣的消耗量有影响,而保护渣消耗量又 对铸坯的表面质量产生影响:消耗量过大。振
流量偏大(达O.41Ⅱ13/h)。
表5
韶钢现用Q345B保护渣(D1)的理化指标
(2)提供温度、成分合格的钢水。改进了 中间包的结构(见图4)。提高转炉冶炼钢水命 中率,避免拉后吹,优化脱氧工艺,减少钢水
中的氧含量,严格控制钢中的Al:O,夹杂含量,
l
\下挡渣墙
提高钢水的纯净度和到站温度,LF炉保证一定 的白渣时间和软吹时间,保证钢水质量和钢水 温度稳定良好。严格控制中间包温度,避免浇 注温度过低,保证保护渣的化渣良好。同时还 改进了中间包的结构。在中间包内的钢包注流 区,采用一种新的控流装置一湍流控制器限制 钢包长水口的高速注流对中间包钢水流动的不 利影响;同时,将中间包的下挡渣墙移至上挡 渣墙和塞棒间位置砌筑,使夹杂物充分上浮。 增加钢水停留时间,减少中间包钢水死区面积.
合理、结晶器液面波动(如水口插入深度不合 要求、吹氩过大等)、钢水条件、拉速变化及操
作不当等。
韶钢板坯连铸机粘结漏钢情况
连铸漏钢的事故类型及原因、预防措施

连铸漏钢的事故类型及原因、预防措施所谓漏钢是指连铸初期或浇注过程中,铸坯坯壳凝固情况不好或因其他外力作用引起坯壳断裂或破漏使内部钢水流出的现象。
漏钢是连铸生产中恶性事故之一,严重的漏钢事故不仅影响连铸机的正常生产,降低作业率,而且还会破坏铸机设备,造成设备损坏。
漏钢事故因发生的时间不同及发生在铸机上的位置不同分为多种形式,其产生的原因也各不相同,主要分为以下几点:⑴开浇漏钢:开浇起步不好而造成漏钢。
⑵悬挂漏钢:结晶器角缝大,角垫板凹陷或铜板划伤,致使在结晶器中拉坯阻力增大,极易发生起步悬挂漏钢。
⑶裂纹漏钢:在结晶器坯壳产生严重纵裂、角裂或脱方,出结晶器后造成漏钢。
⑷夹渣漏钢:由于结晶器渣块或异物裹入凝固壳局部区域,使坯壳厚度太薄而造成漏钢。
⑸切断漏钢:当拉速过快,二次冷却水太弱,使液相穴过长,铸坯切割后,中心液体流出。
⑹粘结漏钢:铸坯粘结在结晶器壁而拉断造成的漏钢。
开浇漏钢(1)中包塞棒头部及上水口碗部烘烤不良。
因碗部较低,传统烘烤方法烘烤火焰达不到碗部,致使碗部温度比其他部位温度低100~200℃。
钢水温度低易造成冷钢垫棒、钢流失控,被迫提高拉速,导致坯头未充分凝固,造成开浇漏钢。
(2)纸绳松动,钢水从其缝隙中渗漏;纸绳受潮,遇钢水后爆炸产生缝隙,钢水从缝隙中渗漏。
(3)铁屑层过薄,造成钢水将纸绳燃烧后从缝隙渗出;铁屑层过厚,将导致坯头强度不足,坯壳被拉断;铁屑受潮、有油污或有杂物,遇钢水后爆炸或燃烧,钢水将纸绳燃烧后从缝隙渗出或坯头强度不足,坯壳被拉断。
(4)传统的封堵引锭方式是用纸绳将引锭头与结晶器间四周的缝隙塞紧、塞实。
钢水到站测温时,先在引锭头上均匀铺撒20~30mm厚的铁钉屑,然后在铁钉屑上按规定交叉摆放好钢板条。
如果钢板条摆放不好,会使钢水直接冲刷铁屑和纸绳;若钢板条熔化不充分,则初生坯壳过薄,拉坯时将导致坯壳撕破。
(5)操作中存在以下问题:开浇钢流过大,将铁屑冲散或将钢水溅到结晶壁上、角缝上形成夹钢;起步提速过快,每次超过0.1m/min,初生坯壳承受不了其拉力;有异物进入结晶器,并咬入初生坯壳中。
连铸机漏钢的原因及防范措施
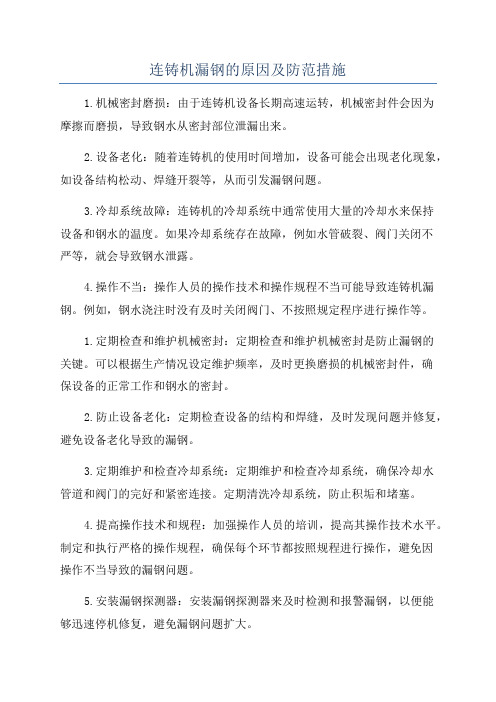
连铸机漏钢的原因及防范措施1.机械密封磨损:由于连铸机设备长期高速运转,机械密封件会因为摩擦而磨损,导致钢水从密封部位泄漏出来。
2.设备老化:随着连铸机的使用时间增加,设备可能会出现老化现象,如设备结构松动、焊缝开裂等,从而引发漏钢问题。
3.冷却系统故障:连铸机的冷却系统中通常使用大量的冷却水来保持设备和钢水的温度。
如果冷却系统存在故障,例如水管破裂、阀门关闭不严等,就会导致钢水泄露。
4.操作不当:操作人员的操作技术和操作规程不当可能导致连铸机漏钢。
例如,钢水浇注时没有及时关闭阀门、不按照规定程序进行操作等。
1.定期检查和维护机械密封:定期检查和维护机械密封是防止漏钢的关键。
可以根据生产情况设定维护频率,及时更换磨损的机械密封件,确保设备的正常工作和钢水的密封。
2.防止设备老化:定期检查设备的结构和焊缝,及时发现问题并修复,避免设备老化导致的漏钢。
3.定期维护和检查冷却系统:定期维护和检查冷却系统,确保冷却水管道和阀门的完好和紧密连接。
定期清洗冷却系统,防止积垢和堵塞。
4.提高操作技术和规程:加强操作人员的培训,提高其操作技术水平。
制定和执行严格的操作规程,确保每个环节都按照规程进行操作,避免因操作不当导致的漏钢问题。
5.安装漏钢探测器:安装漏钢探测器来及时检测和报警漏钢,以便能够迅速停机修复,避免漏钢问题扩大。
6.提高设备的自动化程度:通过提高设备的自动化程度,减少人为的操作,从而降低操作失误导致的漏钢风险。
总之,连铸机漏钢的原因多种多样,需要通过定期检查和维护设备,提高操作技术和规程,安装漏钢探测器等方式来加强防范措施,确保连铸机的正常运行和钢水的安全。
- 1、下载文档前请自行甄别文档内容的完整性,平台不提供额外的编辑、内容补充、找答案等附加服务。
- 2、"仅部分预览"的文档,不可在线预览部分如存在完整性等问题,可反馈申请退款(可完整预览的文档不适用该条件!)。
- 3、如文档侵犯您的权益,请联系客服反馈,我们会尽快为您处理(人工客服工作时间:9:00-18:30)。
YJ0701-板坯连铸机粘接漏钢事故分析案例简要说明:依据国家职业标准和冶金技术专业教学要求,归纳提炼出所包含的知识和技能点,弱化与教学目标无关的内容,使之与课程学习目标、学习内容一致,成为一个承载了教学目标所要求知识和技能的教学案例。
该案例是连续铸钢事故分析与处理案例,体现了连续铸钢等岗位工艺参数、凝固理论知识点和具体岗位操作步骤,与本专业连续铸钢等课程事故预防与处理单元的教学目标相对应。
板坯连铸机粘接漏钢事故分析1 背景介绍某中型转炉炼钢厂,采用喷吹颗粒镁预脱硫,拥有三座100t的转炉, 采用CAS-OB、LF炉、RH精炼装置,四台不同断面的大型厚板坯连铸机,连铸机采用双排热电偶漏钢预报装置。
该厂主要生产管线、船板等中厚板。
2 主要内容2.1 事故经过2012年12月26日,某铸机浇注浇次1212B26(断面2000mm×250mm,钢种45-1)第21炉2Q08199浇注4:46时发生结晶器外弧粘连漏钢,至当日22:00处理完毕,共造成铸机非计划停浇17小时14分,构成粘连漏钢事故。
2.1.1 精炼处理2Q08199炉次是3#LF炉处理,使用12#钢包,包龄44次。
钢水到站后热修包报12#钢包为正常周转包,但在处理过程中升温速度慢,温降异常。
铸机要点4:20,要温1538℃。
2Q08199炉次在3#LF炉处理61min,加热40min,软吹4min。
具体处理过程如下:3:15到站,到站温度1514℃,3:17进加热位并加入一批渣料。
3:20第一次升温,3:33停止 (升温13min),测温1506℃,取钢样。
3:35第二次升温,3:45钢样成分回来后,调硅铁133kg、锰铁61kg、碳粉60kg,3:54升温结束。
进行钙处理,取钢样,并进行软吹。
因钢包包况不好,钢水温降大,4:05测温1516℃。
温度低向工长室反馈,并与热修包核实钢包状况。
经再次核实,12包为小修2次包(12#钢包,小修1次,0:30出钢,进站后因无氩气倒14#包,未在LF炉处理)。
4:05第三次升温,加热10min,其间在4:11测温(1529℃、1527℃),4:14钢样成分回来,4:15停止加热测温1540℃,补喂钙线80m,底吹氩控制为软吹流量,汇报工长室,通知铸机钢水温度、软吹状况。
4:19停止软吹,吊包上2#铸机连浇,吊包前测温1534℃、1535℃。
2.1.2 连铸浇注2Q08199炉次4:24完成座包,4:27正常开浇,拉速控制0.95m/min。
该炉次中包测温依次为1509、1505、1503、1498、1499、1501℃(该钢种液相线温度1490℃),平均过热度12.5℃。
在过热度小于10℃时,4:41提拉速至1.00m/min。
4:46操作工发现外弧水口位置附近液面发死,坯壳较厚,立刻要求停浇。
在机长按急停时,液面出现下降,浇注平台上升起大量白气,随后有燃烧黑烟冒出。
最后确定为漏钢,而漏钢预报未发出报警。
炉次开浇时,连铸主值及主控被通知本炉钢水温度较低,待后续炉次钢水上铸机后即可停浇转出。
2Q08199炉次浇注19分钟时发生漏钢,此时第22炉钢水刚完成座包1分钟。
从液面控制曲线来看,在4:35出现自动抬棒趋势变化,到停浇时共提升棒量5mm,证明存在套眼情况。
2.2 事故原因分析从漏钢坯壳看,外弧水口位置附近有粘连痕迹,在吊出结晶器过程,坯壳在粘连处撕裂,如图1、图2所示:图1结晶器内坯壳粘连部分(外弧) 图2 二冷0段内坯壳部分根据漏钢坯壳确认漏钢原因为粘连漏钢。
因浇次第21包钢水已浇注19分钟,浇注钢水超过50吨,能够确定结晶器漏钢处所浇注钢水为浇次第21包钢水,即2Q08199炉次。
2Q08199炉次钢水从精炼处理到浇注过程共存在以下几个问题:(1)使用的12#钢包尽管为周转包(小修2次),但其小修1次时投用过程运转并不完整,仅在出钢和精炼进站期间承载钢水。
未经LF炉钢水加热和连铸浇注,包壁温度很不稳定,使其再次投用时,实际上并未达到周转包包温。
钢包指车工未将该异常信息及时传递给调度室和精炼;(2)精炼处理过程的操作受到包况影响很大,全处理61min,其中分三次加热累计达到40min。
过程脱硫效果一般(进站S:0.013%,成品S:0.012%),钙处理结果很差(成品Ca:0.0007%)。
在钢水条件差的情况下仅实现软吹4min。
(3)炉次开浇8-10分钟时,塞棒出现缓慢提升,说明存在一定的套眼情况。
成品Ca含量偏低也能证明这一问题。
这也反映了钢水纯净度确实并不理想。
(4)在结晶器外弧发生实际粘钢过程,结晶器漏钢预报系统未出现报警,漏钢之前液面监控并无异常,操作工最后依据经验控制停浇为时已晚。
连铸漏钢预报系统是监控浇注过程坯壳状况最重要的辅助手段,针对此次粘连漏钢发生过程未出现报警的问题,特对漏钢预报进行了检查。
图3 漏钢之前结晶器外弧热电偶数据图4 漏钢时结晶器外弧热电偶数据按系统内时间进行推算,在4:45:36之前,结晶器外弧热电偶并无温度变化,基本保持图3中的趋势。
在4:45:36之后,9#上排热电偶最先出现温度升高,之后7#、8#、10#等周围的热电偶(上排)也出现不同程度的升温。
而9#热电偶升温最大值为21℃。
到4:46:36时出现漏钢,过程中热点偶变化时间为1分钟,但下排热电偶的温度变化量非常小。
程序设定要求,上、下两排热电偶需独立统计,并且同时满足上下两排热电偶温度变化曲线交叉条件时(见图5)才能触发粘钢报警。
而本次粘钢过程,低位热电偶升温并未达到设定要求,因此未能提前报警。
图5 结晶器漏钢热电偶温度变化规律综合以上因素,造成本次粘连漏钢的主要因素包括以下三方面:(1)12#钢包小修一次使用异常,本次使用时为非正常周转包(小修2次),修砌作业区未将该信息传递给调度室和精炼作业区,造成处理时过程温降异常。
(2)当班精炼作业区对钢包出现温降异常处理不当,造成LF炉处理周期紧,软吹时间不足造成钢水纯净度下降,是造成本次事故的主要原因。
(3)连铸浇钢工在浇注过程中未能发现结晶器液面异常,而结晶器漏钢预报系统在关键时刻未能发挥作用,未能及时避免事故发生。
2.3 预防措施(1)最大限度的降低有害杂质(如S、P)和夹杂物含量,以保证铸机的顺行和提高铸坯质量。
如钢水中S含量大于0.03%,容易产生铸坯纵裂纹,钢水中夹杂物含量高,容易造成弧形铸机铸坯中内弧夹杂物集聚,影响产品质量。
(2)钢水的成分:保证加入钢水中的合金元素能均匀分布,且成分控制在较窄的范围内,保证产品性能的稳定性。
(3)钢水的可浇性,要保持适宜的稳定的钢水温度和脱氧程度,以满足钢水的可浇性。
如铝脱氧,钢水中Al2O3夹杂含量高,流动性差,容易造成中间包水口堵塞而中断浇注。
(4)观察保护渣的使用状况,确保保护渣有良好性能。
如测量结晶器液渣层厚度经常保持在8~15mm,保护渣消耗量不小于0.4kg/t钢,及时捞出渣中的结块等。
(5)提高操作水平,控制液位波动。
浇注过程中采取自动浇注,随时观察结晶器漏钢预报系统动态,发现问题及时处理。
(6)确保合适的拉速,拉速变化幅度要小。
升降拉速幅度以0.05m/min为宜。
3 分析路径该案例是连续铸钢事故分析与处理案例,本生产案例体现了连续铸钢等岗位工艺参数、凝固理论知识点和具体岗位操作步骤,与钢铁冶炼专业连续铸钢等课程事故预防与处理单元的教学目标相对应。
根据国家职业标准关于连续铸钢工种要求,对应教学目标,从此生产案例归纳提炼出所包含的知识和技能点,弱化与教学目标无关的内容,使之与课程学习目标、学习内容一致,成为一个承载了教学目标所要求知识和技能的教学案例。
采用现场参观、记录数据、分组头脑风暴、汇报讲评等手段,引导学生通过复习、观察、记录、讨论、讲评、讲授等方式学习连续铸钢事故预防与处理知识,掌握工序工艺参数、工艺制度确定技能,达到教学目标要求。
学生走上工作岗位,减少事故是保证企业经济效益,稳定生产,保证质量的重要项目。
漏钢是连铸生产最常见的事故,而粘结漏钢又占漏钢事故的最大比例。
事故预防与分析是高技能人才的重要能力,牵涉到“人、机、料、法、环”多方面因素,事故分析与处理也是一个很好的代表性工作任务。
下面以某厂连铸坯粘接漏钢为例,通过对事故经过、事故原因分析、提出预防改进措施,说明案例教学的经过。
4 教学目标(1)进行事故判定,掌握粘接漏钢的成因和相关的预防措施;(2)严细操作,注重岗位接口沟通。
(3)全面复习所学知识,并将知识转化为能力。
5 教学方式方法建议采用现场调研、问题讨论、点评、案例分析、讲授、课堂练习、大作业。
具体教学过程设计如下:5.1 课前计划(1)学生掌握知识:连续铸钢生产的基本原理、工艺、设备;(2)学生分组,指定组长;(3)与现场联系,进行现场教学准备,包括安全教育、劳保用品、行走路线,现场兼职教师,现场教室等;(4)安全教育,教师带领学生下厂调研,记录10炉钢连铸生产工艺参数,收集事故相关资料;(5)学生根据所学知识和实习、调研中获得的资料,总结漏钢事故的产生原因、预防措施;(6)与技术人员交流,请技术人员准备讲授连铸生产中出现的漏钢事故。
(可选)(7)教室设置成学习岛,准备投影,为每组准备2张0开白纸,大号记号笔1支、作业纸每人2张。
5.2 课中计划(1)学生按小组就座学习岛周围,选举记录人、发言人。
(2)每人总结一条漏钢事故的产生原因并提出预防措施,按顺时针顺序轮流发言,记录人将操作要点在0开白纸上按人、机、料、法、环分别记录。
要求每人发言,可以轮空,直到所有人员无法补充为止,时间8~10分钟;(3)整理完成后,小组发言人上台展示0开白纸上的记录,并向全体师生汇报交流漏钢事故的产生原因和预防措施;发言学生汇报完成后,同组学生可以补充。
汇报完成,本组自评,其它组进行点评打分,现场技术人员参与对学生汇报的操作要点评价,指出优点和不足,每组时间5~8分钟;(4)技术人员讲授实际生产中漏钢事故案例,时间20分钟;(可选)(5)教师讲授漏钢事故案例,引导学生分析本案例漏钢的产生原因,熟悉预防措施,时间30分钟。
5.3 课后计划布置作业,见6.3。
6 思考题及考评6.1 课前思考题布置课前思考题,保证学生下厂调研知道找什么材料、看什么操作、思考为什么如此操作。
(1)连铸机漏钢分为哪几种类型?(2)连铸坯粘接漏钢的产生原因、处理手段和预防措施是什么?(3)从凝固理论讲,铸坯裂纹、漏钢产生的根本产生原因是什么?6.2 课堂练习课堂提问或者集体回答,目的:及时复习、巩固知识,检查教学效果。
练习题(1)(多选题)防止连铸发生粘结漏钢的措施有()。
BCDA.提高浇注温度,促进保护渣熔化B.使用低粘度保护渣C.确保合适的负滑脱率D.加强钢水管理,提供合格钢水(2)(多选题)防止连铸过程发生漏钢的有效措施有()等。