汽车台架耐久性试验与道路试验相关性探讨
汽车动力总成悬置耐久性模拟试验研究

汽 车零 部件 的疲 劳 耐久 性 试 验 是整 车 耐 久 性试 验
悬 置为 液压 悬 置 。本 文 以发 动 机 悬 置 为 试 验 对 象 , 研
的一个 重要 组成 部分 。一般 其 耐 久 性试 验 分 为 试 车场 试 验与 实验 室道 路模 拟 试 验 。其 中试 验 室 道 路 模 拟试 验 由于具 备 周期 短 、 复现 精 度 高 、 验强 化 程 度 可 调等 试
—
开 。根 据工 程 经 验 , 试 工 装 或 夹 具 的 固有 频 率 应 大 测
.
于 40Hz 0 以上 , 以确 保测 试 系统 所使 用 的工 装 在 工 作
频 率范 围内不会 产生 共振 ;
O
l 0
2 0 t 『 s
3 O
4 0
( )工 装夹 具 的 各 向刚 度 足够 大 , 保 受 力 后 其 2 确
采集 的是 支架 2作 用在 橡胶 主簧 上 的力 。
动机 悬置 、 速 箱 悬 置 、 悬 置 和 后 悬 置 , 中发 动 机 变 前 其
基金项 目:国家 自然科学基金 (0 7 0 3 5557 ) 收稿 日期 :2 1 0 0 0— 4—0 修改稿收到 日期 :0 0— 6—2 2 21 0 2
ts w spo oe n i usdh r.T ehda l n iem u t( E et a rp sda dds s ee h y rui e g o n H M)o a a k na td bet e n c e c n f cr st e sas yojci ,ad a w a u v
图 1 试 验 车 悬 置 上 力 传 感 器 布 置
F g 1 F r e ta s u e a o to h n i e mo n i . o c rn d c rly u n t e e g n u t
GB T 12679-90汽车耐久性行驶试验方法

中华人民共和国国家标准汽车耐久性行驶试验方法GB/T 12679—90代替GB 1334-77Motor vehicles-Durability running—Test method1 主题内容与适用范围本标准规定了汽车耐久性行驶试验方法。
本标准适用于大批量生产的汽车(矿用自卸汽车参照执行)。
2 引用标准GB/T 12534汽车道路试验方法通则GB/T 12545汽车燃料消耗量试验方法GB/T 12548汽车速度表、里程表检验校正方法GB/T 12678汽车可靠性行驶试验方法JB 3743汽车发动机性能试验方法3 术语3.1 汽车耐久性指汽车在规定的使用和维修条件下,达到某种技术或经济指标极限时,完成功能的能力。
3.2 汽车耐久度指汽车在规定的使用和维修条件下,能够达到预定的初次大修里程而又不发生耐久性损坏的概率。
3.3 汽车耐久性损坏指汽车构件的疲劳损坏已变得异常频繁;磨损超过限值;材料锈蚀老化;汽车主要技术性能下降,超过规定限值;维修费用不断增长,已达到继续使用时经济上不合理或安全不能保证的程度。
其结果是更换主要总成或大修汽车。
4 试验条件按GB/T 12678的规定。
5 试验车辆5.1 用于汽车耐久性行驶试验的汽车数量按表2确定.5.2 本试验可用汽车使用试验、常规可靠性试验的同一组汽车。
5.3 整车、各总成及零部件的制造装配调整质量应符合该车技术条件的规定。
6 试验项目及方法6.1 试验程序试验程序按表1进行.6.2 验收试验汽车6.2.1 应按GB/T 12534中第4章之规定,调整内容须纳入故障统计。
6.3 磨合行驶6.3.1 汽车磨合行驶里程及规范应按该车使用说明书的规定.出现故障须纳入故障统计。
6.3.2 在汽车磨合行驶最后1000 km时测量机油消耗量.6.4 发动机性能初试按JB 3743中8.4之规定仅测量总功率。
注:在汽车耐久性行驶试验中,如果发动机大修,则在发动机大修前、后,均要按上述的规定各测量一次总功率。
装甲车辆耐久性试验现状与对策

性试 验研 究工 作 ,解决 好 耐久性 试验 这一 影 响装 甲
车辆 综合 性 能提 高 的关 键 问题 ,为新 一代 装 甲车辆
LICh — n un mi g, W EILa- h n is e g
( hn ot V hc eerhIstt,B in 0 0 2 C ia C iaN r e i eR sac tue e ig10 7 , hn ) h l ni j
Absr c t a t:I h sp p r h o rd r b l y t s d s o r u e e i l n t rs ae s mma ie n t i a e ,t e f u u a ii e tmo e fa mo r d v h ce a d i pa r u t s t rz d. Af r a ay i g t e p o l msn w x se n t r ci e,s me s g sinsa e ma e a c r i o a t rS t n lzn h r b e o e it d i he p a tc e o ug e to r d c o d ngt uho ’ e p re c x e n e,wh c l e hep u o i r v h u a ii e two k o r u e e c e a d i a s i ih wi b l f lt mp o e te d r b lt ts r fa mo r d v hil n t p r . l y s t
K e o ds:a mo r d v h c e;d r blt yw r r ue e il u a i y; t s i et
固定反力式台架道路模拟试验迭代方法

固定反力式台架道路模拟试验迭代方法孙野;于长清;巫洋;李云鹏【摘要】为提高固定反力式台架道路模拟试验的准确度,实现对汽车悬架疲劳强度精确考核,基于MTS 329道路模拟试验设备,结合某车型前悬架总成建立固定反力式试验台架,通过内部载荷参与迭代的方法对悬架系统进行非方阵迭代.结果表明,内部载荷参与迭代的台架响应信号与试验场载荷谱在时域和频域下基本一致,各测点伪损伤误差在合理范围,固定反力式台架道路模拟试验采用内部载荷与车轮六分力载荷共同进行非方阵迭代的方法取得了较好的迭代结果.【期刊名称】《汽车工程师》【年(卷),期】2018(000)003【总页数】5页(P32-35,58)【关键词】道路模拟试验;迭代;内部载荷;固定反力式台架【作者】孙野;于长清;巫洋;李云鹏【作者单位】中国第一汽车股份有限公司技术中心;汽车振动噪声与安全控制综合技术国家重点实验室【正文语种】中文整车耐久性试验在汽车结构强度设计中起着举足轻重的作用,它可以在整车设计开发中及早暴露设计缺陷,为汽车结构的改进优化提供依据。
道路模拟试验能够快速有效地对车身系统、悬架系统及主要零部件进行耐久性能评价,实现对汽车结构强度的考核。
道路模拟试验可分为惯性反力式台架试验和固定反力式台架试验。
固定反力式台架试验在节约试验成本方面有着显著优势,但由于刚性连接的存在,悬架内部零件受力与实际汽车行驶受力状态有所不同,使道路模拟试验准确度受到影响。
文章针对此问题提出使用内部载荷参与非方阵迭代的方法以提高悬架道路模拟的准确度,并基于伪损伤理论,对各测点进行了伪损伤分析,对台架响应载荷谱与试验场相同工况路段载荷谱进行了对比研究。
1 非方阵迭代算法假设试验台架与汽车(或悬架)构成的系统为线性时不变系统[1],由白噪声驱动系统可求出系统的频响函数矩阵,频响函数矩阵代表了输入信号与输出信号的关系,根据期望响应信号与所求得的频响函数即可反求出所需要的驱动信号。
而在实际试验中,系统各环节均存在非线性因素,如汽车(或悬架)、夹具、执行机构及测试系统等,由于非线性因素的存在,当使用线性系统假设求得驱动信号去激励系统时,所得的台架响应与期望响应存在较大误差。
基于等效应力的试验载荷谱开发与研究

基于等效应力的试验载荷谱开发与研究黄庆;王海沛【摘要】以某型轿车稳定杆为研究对象,采集试车场道路载荷谱并对其进行统计分析,在传统基于广义力的载荷谱编制方法基础上,考虑结构的真实损伤计算,提出一种基于等效应力的编谱方法。
通过CAE和台架试验验证可知,寿命与失效位置与实车路试结果基本一致。
新方法相比传统方法能更准确预估损伤等效结果,减少试验频次,更快速地模拟出汽车结构件实际受载情况,试验加速效果明显。
%In this research, the road load spectrum of a proving ground is acquired and analyzed with stabilizer bar of a passenger car as research object. Based on the establishment method of generalized force equivalent stress, and with consideration of the real damage calculation of the structure, a new establishment method of load spectrum based on equivalent stress is proposed. It is known from CAE and rig test that life and location of failure are basically consistent with that of road test. Compared with the traditional method, the new method can more accurately estimate equivalent results of the damage, reduce the test frequency, simulate real loading conditions of structural parts more rapidly, and the accelerated test has obvious result.【期刊名称】《汽车技术》【年(卷),期】2015(000)002【总页数】5页(P53-57)【关键词】轿车;稳定杆;载荷谱;等效应力;加速试验【作者】黄庆;王海沛【作者单位】泛亚汽车技术中心有限公司;泛亚汽车技术中心有限公司【正文语种】中文【中图分类】U461.99载荷谱是在处理随机载荷时最常用的载荷表示方法,被广泛用于结构的疲劳试验。
乘用车悬架系统极限载荷虚拟台架试验方法研究与应用
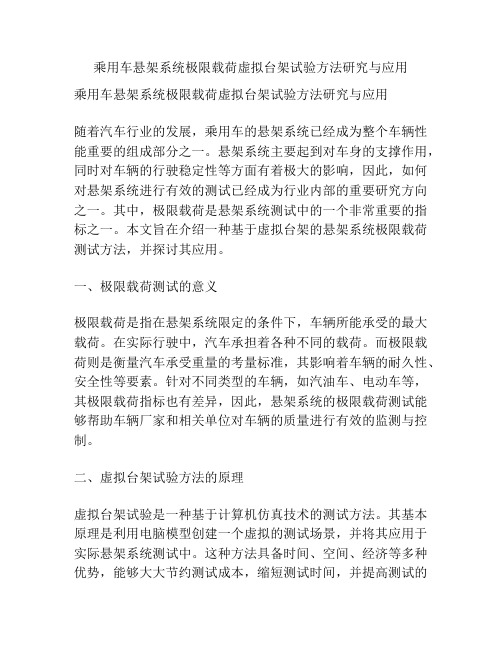
乘用车悬架系统极限载荷虚拟台架试验方法研究与应用乘用车悬架系统极限载荷虚拟台架试验方法研究与应用随着汽车行业的发展,乘用车的悬架系统已经成为整个车辆性能重要的组成部分之一。
悬架系统主要起到对车身的支撑作用,同时对车辆的行驶稳定性等方面有着极大的影响,因此,如何对悬架系统进行有效的测试已经成为行业内部的重要研究方向之一。
其中,极限载荷是悬架系统测试中的一个非常重要的指标之一。
本文旨在介绍一种基于虚拟台架的悬架系统极限载荷测试方法,并探讨其应用。
一、极限载荷测试的意义极限载荷是指在悬架系统限定的条件下,车辆所能承受的最大载荷。
在实际行驶中,汽车承担着各种不同的载荷。
而极限载荷则是衡量汽车承受重量的考量标准,其影响着车辆的耐久性、安全性等要素。
针对不同类型的车辆,如汽油车、电动车等,其极限载荷指标也有差异,因此,悬架系统的极限载荷测试能够帮助车辆厂家和相关单位对车辆的质量进行有效的监测与控制。
二、虚拟台架试验方法的原理虚拟台架试验是一种基于计算机仿真技术的测试方法。
其基本原理是利用电脑模型创建一个虚拟的测试场景,并将其应用于实际悬架系统测试中。
这种方法具备时间、空间、经济等多种优势,能够大大节约测试成本,缩短测试时间,并提高测试的准确度和精度。
三、虚拟台架试验方法的应用在进行虚拟台架试验前,需要先通过计算机仿真技术建立一个包含悬架系统组成部分的电脑模型。
其次,根据仿真结果,可以对模型进行一些必要的修改和调整,以便模拟出现实情况。
在进行试验时,利用电脑模型对悬架系统进行载荷的模拟测试。
通过测试结果,可以得出悬架系统在不同载荷情况下的应力和变形情况,并且可以提供悬架系统的优化方案。
四、结论在当前汽车行业发展中,虚拟台架试验方法已经成为汽车测试的一个重要环节。
在悬架系统任务中,通过虚拟台架试验方法能够有效的监测悬架系统承重性能,对悬架系统的优化及提升有着至关重要的作用。
五、虚拟台架试验方法的优势虚拟台架试验方法相较于传统的实验验证方法具有以下优势:1.成本节约。
轿车后桥耐久性数值仿真和试验研究

t e a p i a in o h o u e i l t n a d t s e h oo y,i h l s t e e t r r e t ov h r c ia h p lc t f t e c mp t r smu ai n e t tc n lg o o t e p h n e p i o s le t e p a t l s c
c mp n n v l ai n,t i a tce a p i s a me h d o i i ls mu a i n t c n lg o i e t e tt o u o o e t au t e o h s ri l p l t o fd gt i l t e h oo y c mb n d wi t s o f c s e a o h
( ,上海变 通大学 , 1 上海 20 3 ;.上海汇众汽车制 造有 限公 司 , 海 2 02 ) 0002 0 12 摘要 : r 为 解决引进 车型零部什试制开发 中出现的同外引进 台架试验 规范的不适应性 问题 , 以某轿车后桥为研究对象 , 采用
数值仿真与试 验相结合 的方法 。 通过计算机仿真 , 埘后桥进行丁应 力应 变分析 及疲 劳分 析 , 同时 , 进行道路应变采集及分析 , 结合计算机仿 真与道路试验情况 , 对原有 的台架试验标准进 行修改 , 采用改进后 台架 试验标 准的试 验结果 道 路试验破坏 情况取得 了基本一致 的效果 。 通过讣算机仿真技术与试 验技术 的结合 , 帮助企业快速地解决 r 实际 问题 , 大大缩短 r 开发周 期, 提高台架试验规范的适虚性 , 促进 丁企 、 一主试验开发。
ABS TRACT:n od rt ov h rbe o n d pa i t fte f rin rg ts p cfc t n frlc l e I r e o s le te p o lm fia a tbl y o h o eg i e ts e i ai o o ai d i i o z
电动汽车用驱动电机系统下线测试台架 技术要求与试验方法
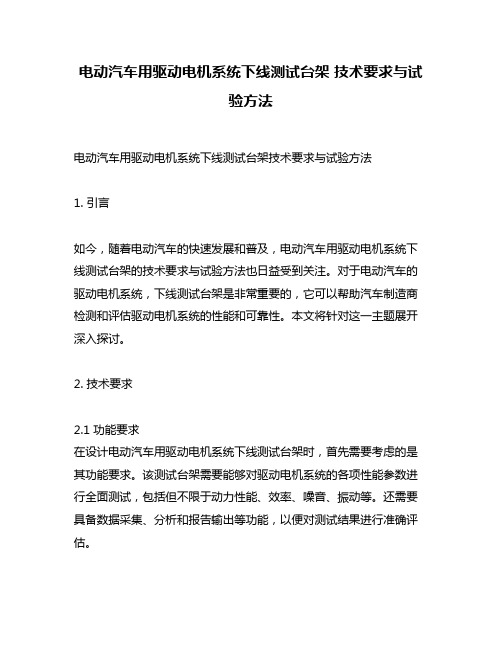
电动汽车用驱动电机系统下线测试台架技术要求与试验方法电动汽车用驱动电机系统下线测试台架技术要求与试验方法1. 引言如今,随着电动汽车的快速发展和普及,电动汽车用驱动电机系统下线测试台架的技术要求与试验方法也日益受到关注。
对于电动汽车的驱动电机系统,下线测试台架是非常重要的,它可以帮助汽车制造商检测和评估驱动电机系统的性能和可靠性。
本文将针对这一主题展开深入探讨。
2. 技术要求2.1 功能要求在设计电动汽车用驱动电机系统下线测试台架时,首先需要考虑的是其功能要求。
该测试台架需要能够对驱动电机系统的各项性能参数进行全面测试,包括但不限于动力性能、效率、噪音、振动等。
还需要具备数据采集、分析和报告输出等功能,以便对测试结果进行准确评估。
2.2 安全要求考虑到测试台架在实验过程中可能会涉及高电压和高速旋转的部件,安全要求显得尤为重要。
测试台架需要具备完善的安全防护措施,如过流、过压、过载等保护装置,以防止意外事件发生。
2.3 精度要求在进行驱动电机系统的性能测试时,测试台架需要具备较高的精度要求。
这包括传感器的精度、数据采集与处理的精度等方面。
只有具备较高的测试精度,才能准确评估驱动电机系统的性能指标。
3. 试验方法3.1 静态试验静态试验是评估驱动电机系统静态性能的重要手段。
在测试台架上,可以通过施加适当的负载,测量电机的静态响应特性,并据此评估其输出扭矩、效率等指标。
3.2 动态试验动态试验则是评估电动汽车驱动电机系统动态性能的关键方法。
通过在测试台架上模拟汽车行驶过程中的加速、减速、匀速等工况,可以评估电机的动态响应特性、控制性能等指标。
3.3 耐久性试验电动汽车用驱动电机系统在实际使用中需要具备较高的可靠性和耐久性。
测试台架还需要能够进行耐久性试验,包括连续工作、循环工作等。
通过耐久性试验,可以评估电机系统在长时间工作状态下的性能表现。
4. 个人观点与理解电动汽车用驱动电机系统下线测试台架的技术要求与试验方法对于保障电动汽车的性能和可靠性具有重要意义。
- 1、下载文档前请自行甄别文档内容的完整性,平台不提供额外的编辑、内容补充、找答案等附加服务。
- 2、"仅部分预览"的文档,不可在线预览部分如存在完整性等问题,可反馈申请退款(可完整预览的文档不适用该条件!)。
- 3、如文档侵犯您的权益,请联系客服反馈,我们会尽快为您处理(人工客服工作时间:9:00-18:30)。
万方数据
工程与试验June2009
较近,这样应用Neuber法则,从鼓包14、15点应变片的测餐信号和螺栓固定点处的局部应力——应变响应,并应用局部应力——应变法和雨流技术对这两点的疲劳损伤累积进行统计,结果见表1。
图1应变片贴片位置
表l14点试验场和四通道台架的疲劳损伤数据对比
试验方式循环次数n疲劳寿命疲劳损伤总疲劳损伤
从表l可以看出,14点SEV()TEST四通道道路模拟试验台上的疲劳损伤与试验场的疲劳损伤的参数相对误差=(0.0300—0.0302)/0.0302≈0.7%;15点SEVOTEST四通道道路模拟试验台上的疲劳损伤与试验场的疲劳损伤的参数相对误差=(o.0301一o.0300)/0.0300≈0.3%。
从试验结果分析可以得出,台架试验数据与试验场试验数据的数值结果很逼近。
3等幅加载试验
对汽车前悬鼓包进行等幅加载试验,试验的同时对上述两点的应力应变进行采集。
对采集到的信号应用基于局部应力一应变法的疲劳寿命估算和等损伤原则,对这两点进行疲劳损伤估计,之后再与试验场进行对比,结果见表2。
从表1、表2可以看出,14点等幅台架试验台上的疲劳损伤与试验场的疲劳损伤的参数相对误差=(0.0333—0.0302)/0.0302≈10.3%;15点等幅台架试验台上的疲劳损伤与试验场的疲劳损伤的参数相对误差一(o.0325--0.0300)/0.0300≈8.3%。
从试验结果分析可以得出,台架等幅加载试验数据与试验场试验的数值结果很逼近。
·】4·
表214点试验场和等幅台架振动的疲劳损伤数据对比试验方式循环次数13.疲劳寿命疲劳损伤总疲劳损伤
4试验结论
从表1和表2可以看出,对汽车鼓包处用随机加载试验和用等幅加载试验得到的试验参数相对误差很接近。
这表明,对于这种具体的试件、装夹和加载情况,用等幅加载试验也能得出与用复杂得多、昂贵得多的随机加载试验相接近的试验结果。
根据分析得出,鼓包处的损伤主要由在垂直平面内的弯曲负荷所引起,所以在它们的随机加载试验中。
仅通过在鼓包卜施加垂直载荷,模拟复现在上述结构危险点附近的在垂直平面内的弯曲负荷即可。
而在等幅试验中,也是通过施加垂直载荷来考验其疲劳强度,也仅承受在垂直平面内的弯曲负荷。
所以,对于这类较简单的加载情况,采用等幅试验,再结合应用基于局部应力一应变法的疲劳寿命估算和等损伤原则,同样可得出对试件的疲劳寿命评价结果,并且相对于随机加载试验可以大大降低试验成本。
5结束语
上述等幅和随机加载试验结果表明,应用等幅试验同样能得到好的对试件疲劳寿命的评价结果,并应用等幅试验相对于应用随机试验大大降低试验成本。
结合应用局部应力一应变法、雨流统计、Neuber法则或等损伤原则来估算室内疲劳试验结果与道路行驶里程之间的当量关系是有效的。
参考文献
rll王霄锋.汽车零部件耐久性试验室内模拟研究[D].北京:清华大学.1990,
[2]J.EBirchrneierandKvISmith.OptimizationofLightTruckRoughRoad1)urabilityProcedureUsingFa‘
tigueAnal)rsisMethodology[C].SAEpaper820693.[3]R八LundandKH.Donaldson,Jr.ApproachestOVehicleDynamicsandDurabilityTesting[C].SAEpa‘
per
820092. 万方数据
汽车台架耐久性试验与道路试验相关性探讨
作者:孙华锋, Sun Huafeng
作者单位:长城汽车股份有限公司,河北,保定,071000
刊名:
工程与试验
英文刊名:ENGINEERING & TEST
年,卷(期):2009,49(2)
被引用次数:1次
1.R A Lund;K H Donaldson Jr Approaches to Vehicle Dynamics and Durability Testing[SAE paper 820092]
2.J E Birchmeier;K V Smith Optimization of a Light Truck Rough Road Durability Procedure Using Fatigue Analvsis Methodology[SAE paper 82069
3.]
3.王霄锋汽车零部件耐久性试验室内模拟研究 1990
1.李飞.郭孔辉.丁海涛.张建伟.张立浩.梁雄军汽车耐久性分析底盘载荷预测方法研究综述[期刊论文]-科学技术与工程 2010(24)
本文链接:/Periodical_syjsysyj200902004.aspx。