超声振动辅助磨削技术研究进展ppt课件
磨削技术理论与应磨削几何学与动力学教学课件

磨削的分类
01
根据磨削方式和工具的不同,磨 削可以分为平面磨削、外圆磨削 、内圆磨削、无心磨削、工具磨 削等多种类型。
02
不同的磨削方式适用于不同的工 件材料、形状和加工要求,选择 合适的磨削方式和工具可以提高 加工效率、精度和表面质量。
磨削技术在航空航天领域的应用
总结词
高强度、高硬度材料加工
详细描述
航空航天领域需要加工高强度、高硬度材料 ,如钛合金、复合材料等。磨削技术能够有 效地处理这些难加工材料,实现高效、高质 量的加工。例如,在飞机发动机叶片的加工 中,磨削技术能够确保叶片的形状精度和表 面光洁度。
磨削技术在光学加工领域的应用
磨削技术的智能化与自动化
总结词
随着工业4.0和智能制造的兴起,磨削技术也在向智能化和自动化方向发展。通过引入传感器、机器视觉等技术 ,实现磨削过程的实时监测和智能控制,提高加工效率和加工质量。
详细描述
智能化磨削技术采用了先进的传感器和机器视觉技术,能够实时监测磨削过程中的各种参数,如磨削力、磨削温 度、工件表面粗糙度等,并根据监测结果自动调整磨削参数,实现高效、高精度的加工。此外,智能化磨削技术 还能够实现加工过程的远程监控和故障诊断,提高加工过程的可靠性和稳定性。
磨削的应用领域
磨削技术在机械制造、航空航天、汽车、能源等领域得到广 泛应用,主要用于加工各种高精度、高表面质量的零件和工 具。
随着技术的发展,磨削技术的应用领域不断扩大,如微细磨 削、超硬材料磨削等新兴领域的发展,为磨削技术的应用提 供了更广阔的空间。
02
磨削几何学
超声及其应用PPT课件

方向性强
超声波的波束狭窄,方向性好 ,能量集中,穿透能力强。
传播速度慢
在同一种介质中,超声波的传 播速度比普通声波慢。
超声波的产生与传播
01
02
03
超声波的产生
超声波通常由压电效应产 生,通过高频电信号驱动 压电晶体,产生机械振动 并发出超声波。
超声波的传播
超声波在介质中传播时, 会受到介质的吸收、散射 和干涉等影响,导致能量 衰减和波形畸变。
05 超声的未来发展与挑战
超声技术的研究前沿与热点
医学影像
高分辨率、高穿透深度 的超声成像技术,用于 早期发现病变和精准诊
断。
生物效应
研究超声对细胞和组织 的生物效应,探索无损、
无创的治疗方法。
超声药物传递
利用超声的物理效应, 实现药物的定向传输和
释放。
实时监测
开发实时、动态的超声 监测技术,用于手术导
超声波的波长是指相邻两个波峰之间 的距离,与频率成反比。
02 超声设备与技术
超声设备的基本构成
超声探头
用于产生超声波和接收回 声信号,是超声设备的核 心部件。
信号处理系统
对回声信号进行处理、分 析和显示,生成超声图像。
电源和控制系统
提供设备所需电源和控制 信号,确保设备正常工作。
超声成像技术
二维超声成像
安全性与可靠性
加强超声技术的安全性和可靠性研究, 确保其在医疗领域的应用安全有效。
THANKS FOR WATCHING
感谢您的观看
应用领域
超声波无损检测在航空航天、汽车、电子、化工等领域得到广泛应用,是保证产品质量和 安全的重要手段之一。
超声在环境监测中的应用
精密加工第5章超声波加工与振动加工
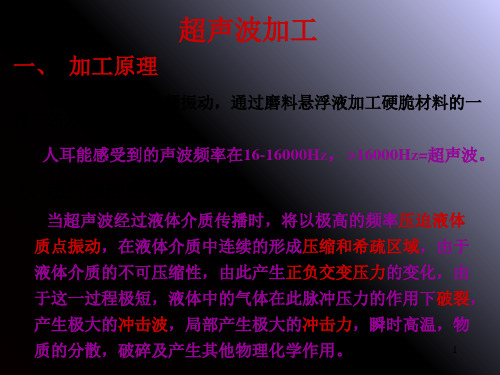
4. 加工复杂型面 ; 5. 生产效率低。
可编辑ppt
6
三、 应用
1. 硬脆、难切、贵重金属、模具加工; 2.孔径0.1-90mm,孔深280mm以上; 3.加工型孔和型腔、切割、清洗、焊接、表面处理及 薄壁、窄缝、低刚度的零件
压电材料主要是人工烧结多晶压电陶瓷。 磁致伸缩效应:铁、钴、镍及其合金的程度能随着所 处的磁场强度的变化而伸缩的现象。
❖ 磨料悬浮液
常用的磨料有:氧化铝、碳化硅、碳化硼、金刚砂等。 其中,氧化铝切割玻璃、锗、陶瓷,金刚砂切割金刚钻、红 宝石,碳化硼适用性较广,但价格较高。
可编辑ppt
5
二、加工特点
可编辑ppt
9
❖ 超声波在冶金中的应用
主要用于控制结晶过程,增加扩散和分散作用以改善材料 的性能,其中最为显著的作用是细化晶粒。
可编辑ppt
10
于这一过程极短,液体中的气体在此脉冲压力的作用下破裂,
产生极大的冲击波,局部产生极大的冲击力,瞬时高温,物
质的分散,破碎及产生其他可物编辑理ppt化学作用。
1
2、超声波加工的基本原理
可编辑ppt
2
3、 超声加工机床的构成
可编辑ppt
3
4、超声加工机床的构成
❖ 超声发生器 主要作用就是将工频交流电转变为一定功率输出的超声
频振荡,有电子管式、晶闸管式两种,超声发生器分为振荡 级、电压放大级、功率放大级和电源等四部分。
❖ 声学部分 主要作用就是超声发生器的高频电能转变为机械能,式
《磨削加工》课件

磨削加工的原理
总结词
磨削加工通过磨料和磨具的高速 旋转或往复运动,利用摩擦和切 削作用去除工件材料。
详细描述
在磨削加工过程中,磨料和磨具 的高速旋转或往复运动产生摩擦 和切削作用,将工件表面材料去 除,从而实现工件的加工。
磨削加工的应用领域
总结词
磨削加工广泛应用于机械制造、航空航天、汽车、能源等领域。
方法具有加工效率高、加工质量好的优点,是现代机械加工领域的重要技术之一。
03
磨削加工的主要技术参数
磨削速度
总结词
磨削速度是砂轮线速度,它直接影响磨削效率和磨削质量。
详细描述
磨削速度越高,单位时间内参与磨削的磨粒数越多,磨削效 率越高。但过高的磨削速度会导致工件表面温度升高,产生 烧伤和裂纹。因此,需要根据工件材料和砂轮特性选择合适 的磨削速度。
高效深切磨削
总结词
一种快速去除材料的磨削加工方法
详细描述
高效深切磨削是一种追求高效率的磨削方法,通过加大切深和切宽来快速去除材料。这种方法适用于 大型零件的粗加工和半精加工,具有加工效率高、加工成本低的优势。
超硬材料磨削
总结词
使用超硬材料作为磨料的磨削加工方法
详细描述
超硬材料磨削是指使用超硬材料(如碳化硅、金刚石等)作为磨料进行磨削加工的方法 。由于超硬材料的硬度极高,因此可以实现对硬质合金、陶瓷等高硬度材料的加工。该
磨削深度
总结词
磨削深度是砂轮表面与工件表面的距离 ,它决定了磨削层的厚度。
VS
详细描述
磨削深度对磨削效率和表面粗糙度有较大 影响。增加磨削深度可以提高磨削效率, 但过大的磨削深度会导致工件表面粗糙度 增加。因此,需要根据工件材料、砂轮特 性以及表面质量要求来选择合适的磨削深 度。
磨削加工技术PPT参考幻灯片共49页

1、最灵繁的人也看不见自己的背脊。——非洲 2、最困难的事情就是认识自己。——希腊 3、有勇气承担命运这才是英雄好汉。——黑塞 4、与肝胆人共事,无字句处读书。——周恩来 5、阅读使人充实,会谈使人敏捷,写作使人精确。——培根
磨Байду номын сангаас加工技术PPT参考幻灯片
1、合法而稳定的权力在使用得当时很 少遇到 抵抗。 ——塞 ·约翰 逊 2、权力会使人渐渐失去温厚善良的美 德。— —伯克
3、最大限度地行使权力总是令人反感 ;权力 不易确 定之处 始终存 在着危 险。— —塞·约翰逊 4、权力会奴化一切。——塔西佗
5、虽然权力是一头固执的熊,可是金 子可以 拉着它 的鼻子 走。— —莎士 比
切削加工振动及其控制技术47页PPT
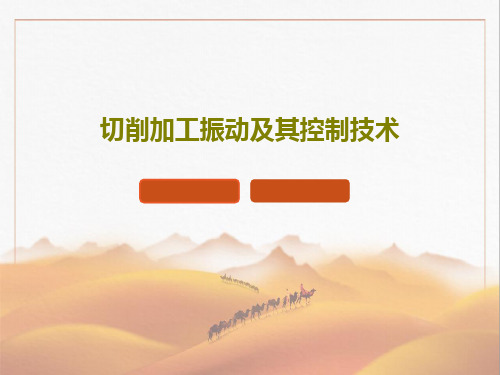
谢谢!
47
切削加工振动及其控制技术
31、园日涉以成趣,门虽设而常关。 32、鼓腹无所思。朝起暮归眠。 33、倾壶绝余沥,窥灶不见烟。
34、春秋满四泽,夏云多奇峰,秋月 扬明辉 ,冬岭 秀孤松 。 35、丈夫志四海,我、愉快,这是不可能的,因为人类必须具备一种能应付逆境的态度。——卢梭
▪
27、只有把抱怨环境的心情,化为上进的力量,才是成功的保证。——罗曼·罗兰
▪
28、知之者不如好之者,好之者不如乐之者。——孔子
▪
29、勇猛、大胆和坚定的决心能够抵得上武器的精良。——达·芬奇
▪
30、意志是一个强壮的盲人,倚靠在明眼的跛子肩上。——叔本华
超声振动切削加工

超声振动切削加工的研究现状及进展摘要:简述了超声振动切削技术的发展、优点及应用领域。
通过将超声振动切削与普通切削比较以及对振动切削过程特点的描述,探讨了超声振动切削的切削机理。
文章还分析了振动切削技术的最新发展, 认为超声振动切削是一项有发展前途的新型技术。
关键词:超声振动切削;难加工材料:切削机理Research of vibration assisted turning cutting technology andIts developmentAbstract:Introduces the history, advantages and application field of the ultrasonic cutting technology(UCT). By compared with ordinary cutting and the characteristics description of the ultrasonic vibration cutting process, explored Ultrasonic vibration cutting of the cutting mechanism. The paper also analyzes an up- to- date vibrating cutting technology and summarizes that the ultrasonic vibration cutting is a promising new technology.Key Words: Ultrasonically vibrating cutting; Difficult - to - machine materials; Cutting Mechanism0 前言超声振动切削技术是把超声波振动的力有规律地加在刀具上,使刀具周期性地切削和离开工件的加工技术, 是结合超声波技术和传统切削工艺的一种新型切削技术。
旋转超声波+磨削(1)

2、超声辅助磨削的发展超声辅助磨削技术的发展:超声辅助磨削通常分为:一维超声辅助磨削技术、二维振动磨削技术和旋转超声磨削技术,如图1所示。
一维超声辅助磨削技术可归结为三类①砂轮轴向振动磨削,即工件相对于砂轮做轴向反复振动;②砂轮径向振动磨削;③砂轮切向振动磨削。
二维振动磨削技术有两类:①平行于工件平面的二维振动磨削,即对工件同时施加砂轮切向和砂轮轴向的超声振动;②平行于砂轮端面的二维振动磨削。
一维轴向超声振动磨削关注的焦点在于加工表面质量的显著提高;一维径向超声辅助磨削关注的焦点在于加工效率的大幅度提高。
二维振动磨削技术充分利用了一维振动磨削的特点,具有优越的综合加工性能,但是加工过程中磨削速度较低,这在一定程度上限制了该技术的广泛应用。
(a)一维轴向超声磨削(b)一维径向超声磨削(c)一维切向超声磨削(d)二维超声磨削(e)旋转超声磨削旋转超声辅助磨削加工技术是在传统的超声游离磨粒加工技术的基础上发展而来的。
旋转超声辅助磨削加工分为两种,一种采用悬浮液游离磨粒,另一种则采用固着磨粒,通常所说的旋转超声辅助磨削加工技术是指采用固着磨粒的超声加工。
(通过烧结或者电镀的方式把磨粒固定在刀具上,带有中心孔的磨削刀具沿着刀轴方向高频振动的同时,也进行着高速的回转运动,切削液不再含有磨粒,并从刀具中心孔流出带走切屑并对加工区域进行冷却。
)超声加工机床的发展:旋转超声加工技术始于1964 年,早期的旋转超声加工设备只能用于孔结构的加工,而随着数控加工技术的发展,旋转超声加工设备已经可以用于复杂三维结构的加工。
2007 年德国的DMG/Sauer 公司研制的Ultrasonic 20 五轴联动超声振动高速加工中心,实现了多种加工功能的集成,不仅可以钻孔、攻螺纹,还可以加工复杂形状的硬脆材料零件,被认为是旋转超声加工设备的新飞跃。
国:对于旋转超声加工技术和设备的研究主要集中在部分高校戴向国探索了旋转超声加工机床的研制,该机床采用具有频率自动跟踪功能超声波电源;福令开发出基于Windows平台的旋转超声加工机床的数控系统,2002 年于思远等人开发了配置气浮工作台的旋转超声加工机2008 年,天津大学的房丰洲开发出集大电流放电铣削粗加工、旋转超声辅助磨削加工、超声辅助放电加工和传统铣削加工为一体的五轴超声复合加工机床。
- 1、下载文档前请自行甄别文档内容的完整性,平台不提供额外的编辑、内容补充、找答案等附加服务。
- 2、"仅部分预览"的文档,不可在线预览部分如存在完整性等问题,可反馈申请退款(可完整预览的文档不适用该条件!)。
- 3、如文档侵犯您的权益,请联系客服反馈,我们会尽快为您处理(人工客服工作时间:9:00-18:30)。
磨 界上首次提出并实现采用超声频调制电火花与
削
技 超声波复合的研磨、抛光加工技术。与纯超声
术
发 波研磨、抛光相比,效率提高5倍以上,并节约
展 回
了大量的金刚石磨料。
顾
发展回顾
超 声
20世纪80年代后期,天津大学李天基等人在
振 动
高速磨削的同时对磨头施以超声振动,提出了
磨 高效的超声磨削复合加工方法,效率比传统的
削 技
主要由垂直方向粗糙度决定,通过改变加工参数
术 方法很难显著降低表面粗糙度。
研究现状
一 维
Denkena研究发现在轴向振动磨削过程中,砂轮
轴 轴向分布的不同磨粒对工件起重复研磨作用,从
向
超 而能获得高质量加工表面。还指出使用普通粒径
声
振 大小的砂轮磨粒进行超声波磨削时,超声波辅助
动 磨
作用对表面质量不会有积极影响。
削
技 1945年,L.Balamuth申请了关于超声加工的
术
发 专利。
展
回
顾
发展回顾
超 声
20世纪50~60年代日本学者隈部淳一郎对振
振 动
动切削进行系统研究,提出了振动切削理论,
磨 并成功实现了振动磨削加工 。
削
技 20世纪60年代,英国Hawell原子能研究中心
术
发 的科学家发明了新的超声磨削复合加工方法。
超声振动辅助磨削技术研究 进展
内容
1
前言
2
发展回顾
3
研究现状
4
发展趋势
前言
不足
概念
优势
前言
航空、电子、光学及通信工业的新技术迅猛发展, 对硬脆性材料、难加工材料和新型先进材料的需求 日益增多,对关键零件的加工效率、加工质量和加 工精度提出了更高的要求。
前言
传统加工方法是超精密磨削和单点金刚石切削; 产生较大的磨削力以及磨削热,引起工件表面、 亚表面损伤以及砂轮寿命低; 严重制约着零件加工精度及加工效率。
削
技
术
研究现状
一 Tawakoli 开 发 了 一 种 干 式 轴 向 超 声 振 动 磨 削 维 轴 42CrMo4技术,试验证实表面粗糙度提高,法向
向 超
磨削力和热损伤显著降低。
声
振
动
磨
削
技
术
研究现状
机理:超声振动促使磨粒产生断续切削作用,而
一 冲击载荷促使工件材料更容易卷积,在切削区生
维 轴
术
发
展
回
顾
内容
研究现状
技术类型 一维轴向 一维径向 一维切向
二维
研究现状
技 术 类 型
研究现状
轴向超声振动被应用到工件或者砂轮上,能够同
一
维 时减小平行与垂直方向的粗糙度,从而有效提高
轴
向 表面质量。
超
声
振 Wang等证实工作台进给速度与砂轮转速对垂直
动 磨
于磨削方向的粗糙度影响较小,并且表面粗糙度
振 动
初步应用研究工作,对超声振动磨削机理进行
磨 了探索研究。
削
技 1985年前后机械电子工业部第11研究所研制
术
发 成功超声旋转加工机,在玻璃、陶瓷等硬脆材
展 回
料的内外圆磨削加工中取得了优异的工艺效
顾 果。
发展回顾
超 声
1987年北京市电加工研究所研究成功了超硬
振 动
材料超声电火花复合抛光技术。这项技术是世
成较多的微观裂纹扩展,促使磨削力以及摩擦系
向 超
数减小.
声
振 动
机理:材料的塑性变形主要发生在滑擦和犁削作
磨 削
用阶段,由于垂直于切削方向的超声振动促使滑
技 术
擦和犁削比例相对减小,从而比磨削能减小,表
面热损伤也显著降低。
研究现状
径向超声振动磨削在提高加工效率以及改善砂轮
一
维 使用性能等方面具有显著优势。
UV优AM点
提高脆性与研性域发生转变的临界切 削深度,实现脆性材料的延性域加 工,使复杂光学元件表面超精密加工 可以不须采用磨削和抛光的方法完成 加工。
发展回顾
超 声
首先是应用在材料的切削加工
振 动
1927年,R.W.Wood和A.L.Loomis发表了有
磨 关超声波加工的论文,超声加工首次提出。
展 回
超声振动磨削加工在难加工材料和高精度顾
超 声
1986年日本学者石川健一受超声电机椭圆振
振 动
动特性启发,首次提出了“椭圆振动切削方
磨 法”(elliptical vibration cutting)。 削
技
术
发
展
回
顾
发展回顾
超 声
20世纪90年代初,日本神户大学社本英二等
振 动
人对超声椭圆振动切削技术进行了深入研究,
磨 利用金刚石刀具采用双激励双弯曲合成椭圆振
削
技 动的方式对黑色金属、淬火不锈钢进行精密车
术
发 削,最小表面粗糙度可以达到Ra0.0106um,不
展 回
但解决了金刚石不能加工黑色金属的难题,而
顾 且使这项技术达到了实用化阶段。
发展回顾
超 声
20世纪50年代,我国开始进行了振动加工的
前言
UVAG是一种间歇式的加工方法; 小幅的振动以超声频率附加在工具或工件上,使 得加工工具的运动学发生改变; 结合了金刚石磨削加工材料去除机理和超声加工 特点的复合磨削加工技术。
前言
优点 可产生加工力减小和切屑减薄的效果 优点 改善工件表面精度和形状精度
前言
优点 提高材料去除率,延长工具的寿命
径
向
超
声
振 Mult等对烧结氮化硅以及氧化铝陶瓷进行径向超
动 磨
声磨削试验,发现磨削力大幅度减小以及材料去
削 技
除率显著增加,同时伴随着粗糙度的轻微增加以
术 及砂轮磨损加剧。
研究现状
法向磨削力减小的主要原因归结为超声振动的工
一 件与磨粒切削刃发生断续接触,减少了实际接触
维
径 时间,有效降低了摩擦系数。
削
技 超声加工提高了6倍以上,表面质量也有了大幅
术
发 提高。
展 回
20世纪90年代后,超声振动辅助加工成为了
顾 研究热点。
发展回顾
超 声
目前的研究集中在参数(砂轮转速、振动幅度
振 动
与频率、金刚石类型、磨粒尺寸、结合剂类型
磨 、冷却液和压力等)对加工性能(MRR、切削力和 削
技 表面粗糙度)的影响。
研究现状
一 Uhlmann通过单颗磨粒划擦试验,分析了先进陶 维 瓷径向振动磨削的表面形成机制。试验表明超声 径 向 辅助改变了磨粒加工运动轨迹,导致磨粒与工件 超 声 的断续接触,得到断续切削沟槽。 振 动 磨 削 技 术
向
超
声
振 动
砂轮磨损的增加是由于较低的摩擦力以及热载荷
磨 削
作用,磨粒整体脱落数量减少而单颗磨粒的微观
技 脆性断裂增加。
术
研究现状
粗糙度的轻微增加可能是由于同时发生切削作用 一 的有效磨粒切削刃数量增加以及工件表面塑性变 维 径 形减小所致。 向 超 声 振 在磨粒一次切削周期内,磨粒切削刃比普通磨削 动 磨 更早的切入以及更晚地脱离工件表面,这增长了 削 技 脉冲作用周期,增加了接触压力,由此产生了更 术 多材料微观断裂,促使材料去除率增加。