含铜钼精矿的处理方法与设计方案
一种对浮选后的钼精矿的脱油处理方法

预计 到 2 1 0 0年 , 利 铜 基 础 矿 山 产 量 将 达 到 智 5 4万 t铜 精 矿产 量 将 达 到 3 8万 t 7 、 5 。而 铜 基 础 矿
元 。20 年 , 利 国 家 铜 业 公 司 生 产 精 炼 铜 09 智
1 8万 t这 个数 字相 当于世 界铜 产量 的 1 % 。其 主 7 。 1 要商业 产 品是 A 级 阴极 铜 。另 一 个 是 智 利 国家 矿
山产 量 将 逐 步 增 加 ,04年 将 达 到 57万 t但 到 21 9 ,
21 0 5年则 会 出现小 小 的下 降 , 达 到 5 5万 t而 铜 将 7 , 精矿 产 量 将 达 到 4 2万 t 而 铜 潜 在 产 量 可 达 到 7 ,
第3 4卷 第 6期
智利 : 铜王国” “ 前景依然看好
・5 7・
利进 口的铜 精矿远 远超 过智 利 出 口到世界 其他 国家
的量 。
力 的“ 模 经济 ” 范 围经济 ” 规 和“ 。 从 2 1 0 5年 , 0 0~2 1 智利 对铜 矿和金 矿 的投资 估 计 将达 到 5 0亿美 元 , 投 资 额既 考 虑到 了在建 项 0 此 目, 又考 虑到 了 2 1 2 1 0 0— 0 5年期 间有可 能建设 的项 目, 中 8 . % 的投 资用 于铜 矿 开采 ( 1 . 8亿美 其 28 44 3 元 ) 1 . %用 于金矿 开采 ( 6 2 ,7 2 8 .5亿美元 ) 。 对 于用 于铜 矿 的投资 , 利 国家 铜 业公 司 占的 智 比重 为 4 . % , 数 量 上 与大 型私 营公 司类 似 , 88 在 大 型私 营公 司用于 铜矿 的投 资 占总 铜矿投 资 的 比重为 3 未 来智 利ຫໍສະໝຸດ 铜 业 仍 将 保持 增 长 态势
铜矿选矿原理及工艺
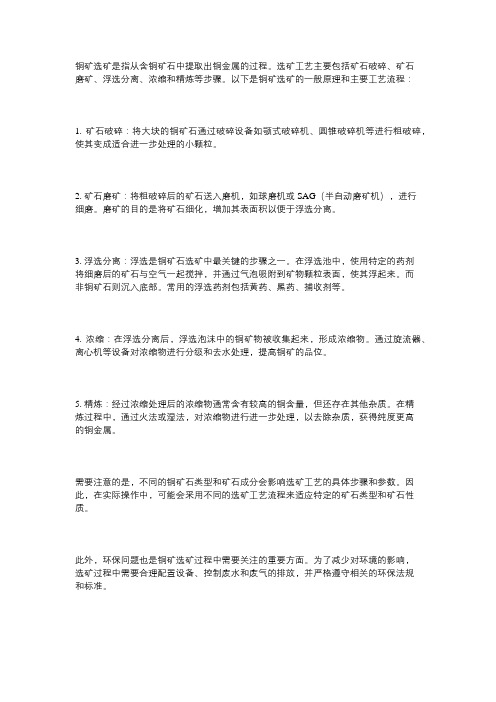
铜矿选矿是指从含铜矿石中提取出铜金属的过程。
选矿工艺主要包括矿石破碎、矿石
磨矿、浮选分离、浓缩和精炼等步骤。
以下是铜矿选矿的一般原理和主要工艺流程:
1. 矿石破碎:将大块的铜矿石通过破碎设备如颚式破碎机、圆锥破碎机等进行粗破碎,使其变成适合进一步处理的小颗粒。
2. 矿石磨矿:将粗破碎后的矿石送入磨机,如球磨机或SAG(半自动磨矿机),进行
细磨。
磨矿的目的是将矿石细化,增加其表面积以便于浮选分离。
3. 浮选分离:浮选是铜矿石选矿中最关键的步骤之一。
在浮选池中,使用特定的药剂
将细磨后的矿石与空气一起搅拌,并通过气泡吸附到矿物颗粒表面,使其浮起来。
而
非铜矿石则沉入底部。
常用的浮选药剂包括黄药、黑药、捕收剂等。
4. 浓缩:在浮选分离后,浮选泡沫中的铜矿物被收集起来,形成浓缩物。
通过旋流器、离心机等设备对浓缩物进行分级和去水处理,提高铜矿的品位。
5. 精炼:经过浓缩处理后的浓缩物通常含有较高的铜含量,但还存在其他杂质。
在精
炼过程中,通过火法或湿法,对浓缩物进行进一步处理,以去除杂质,获得纯度更高
的铜金属。
需要注意的是,不同的铜矿石类型和矿石成分会影响选矿工艺的具体步骤和参数。
因此,在实际操作中,可能会采用不同的选矿工艺流程来适应特定的矿石类型和矿石性质。
此外,环保问题也是铜矿选矿过程中需要关注的重要方面。
为了减少对环境的影响,
选矿过程中需要合理配置设备、控制废水和废气的排放,并严格遵守相关的环保法规
和标准。
钼精矿成分分析报告

钼精矿成分分析报告摘要:本文通过对一批钼精矿的成分分析,详细探讨了其主要成分的含量以及可能的矿物组成。
实验结果表明,该钼精矿中的主要元素包括钼、硫、铁、铜等,且钼的含量较高。
此外,根据化学组成分析和矿物鉴定结果,发现钼精矿主要由黄铁矿、辉钼矿、方铅矿等矿物组成,为一种较为常见的钼矿石。
1. 引言钼是一种重要的金属元素,广泛应用于冶金、化工、电子、材料科学等领域。
而钼精矿是钼的主要原料之一,其成分分析对于钼矿石资源的开发利用具有重要意义。
本文针对一批钼精矿进行了详细的成分分析,旨在揭示其主要成分含量及可能的矿物组成,为钼矿石的综合利用提供参考依据。
2. 实验方法2.1 样品准备所选取的钼精矿样品来自某钼矿石矿产区,为干燥的块状样品。
2.2 成分分析采用化学分析方法,包括化学溶解和原子吸收光谱法,对钼精矿样品进行成分分析,测定钼、硫、铁等主要成分的含量。
2.3 矿物组成鉴定通过显微镜下的颜色、断口特征等观察,结合X射线衍射分析,对钼精矿样品中的主要矿物组成进行鉴定。
3. 实验结果与分析3.1 主要成分含量实验结果表明,钼精矿样品中,钼的含量较高,约为40%;硫的含量为35%;铁和铜的含量分别为15%和10%。
这说明该钼精矿样品是一种富钼矿石。
3.2 矿物组成通过矿物组成鉴定,发现钼精矿主要由黄铁矿、辉钼矿、方铅矿等矿物组成。
其中,黄铁矿的黑色、金属光泽以及断口呈弯曲状的特征较为明显;辉钼矿的颜色呈灰黑色,呈片状状断口;方铅矿的颜色为黑色,断口呈方形。
这些矿物的存在表明该钼精矿是一种较为常见的钼矿石。
4. 结论通过对一批钼精矿样品的成分分析,本实验得出以下结论:(1) 该钼精矿样品主要含有钼、硫、铁、铜等元素,其中钼的含量较高;(2) 钼精矿主要由黄铁矿、辉钼矿、方铅矿等矿物组成。
这些研究结果为钼矿石的综合利用提供了重要依据。
然而,本研究还存在一些不足之处,例如只针对了一批样品进行了成分分析,存在一定的局限性。
国内矿山钼精矿干燥的几种方式

国内矿山钼精矿干燥的几种方式杨少燕;何荣权【摘要】浮选钼精矿过滤脱水后,滤饼含水率普遍在8%以上.为进一步降低钼精矿含水量,满足后续精矿运输和钼深加工的要求,需要对滤饼进行干燥.本文介绍了国内几个大型钼矿山的钼精矿干燥方法、采用的设备、工作原理以及运行情况.【期刊名称】《有色冶金节能》【年(卷),期】2017(033)002【总页数】4页(P17-20)【关键词】钼精矿;干燥;含水率;能耗【作者】杨少燕;何荣权【作者单位】中国恩菲工程技术有限公司,北京100038;中国恩菲工程技术有限公司,北京100038【正文语种】中文【中图分类】TD926.2浮选得到的钼精矿过滤脱水后,滤饼含水率普遍在8%以上。
为进一步降低钼精矿含水量,满足后续精矿运输和钼深加工的要求,需要对滤饼进行干燥。
目前,可用于钼精矿干燥的干燥设备种类较多,使用效果也各不相同。
金堆城钼矿百花岭选矿厂曾采用7组蒸汽螺旋干燥机进行干燥作业(现已取消),环境污染严重,且钼精矿损失量和能耗均较高;金堆城钼矿三十亩地选矿厂采用2台双电源电磁螺旋干燥机进行钼精矿干燥,取得了较好的干燥效果;德兴铜矿采用一套闪蒸干燥机,该套装置在国内为首次应用,并已充分显示出了其优越性;乌努格吐山(以下简称乌山)的钼精矿干燥则采用一台XFG型电加热粉体干燥机。
下文将进一步介绍上述几个大型矿山的钼精矿干燥方法、采用的设备、工作原理以及运行情况。
金堆城钼矿百花岭选厂在开展钼精矿脱水新工艺改造之前,一直采用“浓缩—过滤—干燥”的三段脱水工艺。
过滤机滤饼经螺旋输送机给入7组Φ500蒸汽螺旋干燥机干燥(现已取消干燥作业)。
干燥后的钼精矿经螺旋输送机给入2台PL250型斗式提升机,再经螺旋输送机给入10个10 t的钼精矿矿仓,矿仓中的钼精矿先后经DB13型封闭式圆盘给料机、螺旋输送机装入钼精矿料斗,料斗中的钼精矿经过10 t混矿机混矿,混矿机下的出料螺旋将混好的精矿输送至包装处,通过人工计量、包装成最终产品。
铜矿选矿工艺流程
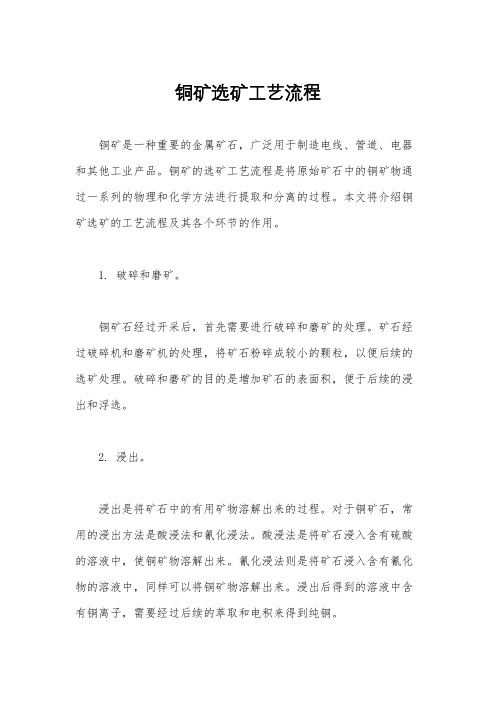
铜矿选矿工艺流程铜矿是一种重要的金属矿石,广泛用于制造电线、管道、电器和其他工业产品。
铜矿的选矿工艺流程是将原始矿石中的铜矿物通过一系列的物理和化学方法进行提取和分离的过程。
本文将介绍铜矿选矿的工艺流程及其各个环节的作用。
1. 破碎和磨矿。
铜矿石经过开采后,首先需要进行破碎和磨矿的处理。
矿石经过破碎机和磨矿机的处理,将矿石粉碎成较小的颗粒,以便后续的选矿处理。
破碎和磨矿的目的是增加矿石的表面积,便于后续的浸出和浮选。
2. 浸出。
浸出是将矿石中的有用矿物溶解出来的过程。
对于铜矿石,常用的浸出方法是酸浸法和氰化浸法。
酸浸法是将矿石浸入含有硫酸的溶液中,使铜矿物溶解出来。
氰化浸法则是将矿石浸入含有氰化物的溶液中,同样可以将铜矿物溶解出来。
浸出后得到的溶液中含有铜离子,需要经过后续的萃取和电积来得到纯铜。
3. 浮选。
浮选是将矿石中的有用矿物通过气泡的吸附和分离来实现的。
对于铜矿石,常用的浮选方法是将矿石浸入含有吸附剂的浮选剂中,通过气泡的作用使铜矿物粘附在气泡上,然后分离出来。
浮选后得到的铜精矿含有较高的铜含量,需要经过后续的冶炼和精炼来得到纯铜。
4. 冶炼和精炼。
铜精矿经过冶炼和精炼的处理,可以得到纯铜。
冶炼是将铜精矿加热至高温,使其中的铜矿物氧化还原,得到粗铜。
精炼是将粗铜经过电解或火法处理,使其中的杂质得到去除,得到纯铜。
冶炼和精炼是铜矿选矿工艺流程中非常重要的环节,直接影响着最终铜的品质。
5. 废水处理。
铜矿选矿过程中会产生大量的废水,其中含有铜离子和其他有害物质。
废水处理是铜矿选矿工艺流程中必不可少的环节,通过沉淀、过滤、离子交换和电解等方法,将废水中的有害物质去除,得到清洁的水体,以保护环境和节约资源。
以上就是铜矿选矿工艺流程的主要环节及其作用。
铜矿选矿是一个复杂的过程,需要各种物理和化学方法的配合,才能最终得到纯铜。
在实际生产中,还需要根据矿石的特性和工艺条件进行调整和改进,以提高选矿效率和降低成本。
钼矿

西部三江印支褶皱系铜-钼成矿带。该区沿深断裂带的构造-岩浆活动强烈,燕山-喜马 拉雅早期的中酸性岩浆活动频繁,在喜马拉雅期形成玉龙斑岩型铜(钼)矿床和马厂箐 斑岩-夕卡岩型钼(铜)矿床。 钼矿床的成矿时代,就全世界而言,主要为中生代和新生代,这两个时期形成的钼矿 床约占世界上已探明钼总储量的90%左右。我国除少数铜(钼)矿床形成于古生代的海西期 和新生代的喜马拉雅期外,绝大多数钼矿床和铜(钼)矿床均为中生代燕山期的产物,这是 由于我国东部广大地区的燕山期断裂构造和花岗岩类侵入活动广泛发育所致。
钼矿矿床时空分布及成矿规律
我国东部的钼、铜-钼、钼-钨等矿床归属于环太平洋钼成矿带,西部在三江地区的铜-钼 矿床隶属三江褶皱系铜-钼成矿带(属古地中海成矿带)。根据钼矿床与大地构造单元的关 系及成矿特点,把东部环太平洋钼成矿带进一步划分成为四个成矿省:①中朝准地台钼 成矿省;②东北海西褶皱系铜-钼成矿省;③扬子准地台铜-钼成矿省;④华南褶皱系钨铜-钼成矿省。其中最引人注目的是中朝准地台钼成矿省。业已查明,北缘的燕辽钼矿带 和南缘的东秦岭钼矿带,是我国最重要的两个钼矿带,它们约占全国已探明工业钼储量 的60%以上,尤其是东秦岭钼矿带,钼矿总储量达360万t,共有钼(钨)矿床(点)46个,其 中特大型矿床4个:金堆城钼矿、上房沟钼(铁)矿、南泥湖钼(钨)矿、三道庄钼(钨)矿; 大型矿床4个:大石沟钼(铼)矿、石家湾钼矿、夜长坪钼钨矿、雷门沟钼矿;中型矿床有 :南台钼钨矿、银家沟钼矿、秋树湾铜钼矿等等。区内东西向构造具有一级控制意义; 不同构造体系的联合、复合部位控制着岩群及矿带的分布,具有二级控制意义,成矿带 内的大矿田或矿区等,均处在新华夏系或弧形构造与纬向构造斜接叠加部位,像金堆城、 黄龙铺等矿区处于纬向构造与祁吕贺山字型构造前弧东翼复合部位,栾川南泥湖矿田处 在纬向构造与伏牛-大别弧形构造叠加部位;低序次的构造变动或构造交接复合部位,控 制着小岩体或矿体,具有三级控制意义。
铜矿的选矿方法及工艺
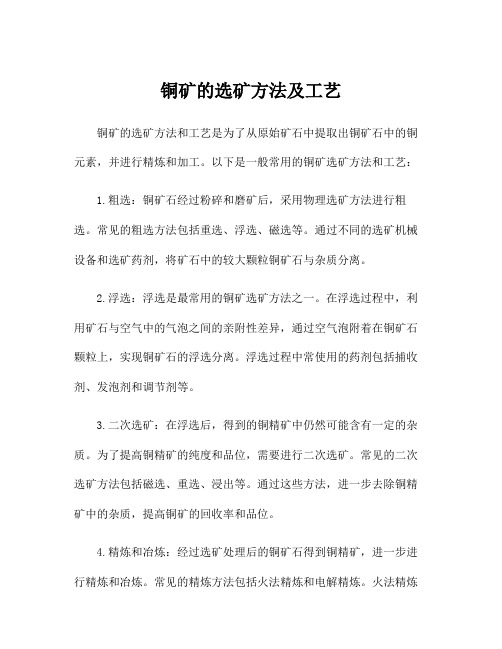
铜矿的选矿方法及工艺
铜矿的选矿方法和工艺是为了从原始矿石中提取出铜矿石中的铜元素,并进行精炼和加工。
以下是一般常用的铜矿选矿方法和工艺:
1.粗选:铜矿石经过粉碎和磨矿后,采用物理选矿方法进行粗选。
常见的粗选方法包括重选、浮选、磁选等。
通过不同的选矿机械设备和选矿药剂,将矿石中的较大颗粒铜矿石与杂质分离。
2.浮选:浮选是最常用的铜矿选矿方法之一。
在浮选过程中,利用矿石与空气中的气泡之间的亲附性差异,通过空气泡附着在铜矿石颗粒上,实现铜矿石的浮选分离。
浮选过程中常使用的药剂包括捕收剂、发泡剂和调节剂等。
3.二次选矿:在浮选后,得到的铜精矿中仍然可能含有一定的杂质。
为了提高铜精矿的纯度和品位,需要进行二次选矿。
常见的二次选矿方法包括磁选、重选、浸出等。
通过这些方法,进一步去除铜精矿中的杂质,提高铜矿的回收率和品位。
4.精炼和冶炼:经过选矿处理后的铜矿石得到铜精矿,进一步进行精炼和冶炼。
常见的精炼方法包括火法精炼和电解精炼。
火法精炼
通过高温熔炼铜精矿,去除残留的杂质;电解精炼通过电解的方式,将铜精矿中的铜溶解并沉积在阴极上,得到纯铜。
5.加工和利用:经过精炼和冶炼后得到的纯铜可以进行加工和利用。
常见的加工方法包括铸造、轧制、拉拔等,将铜制成不同形态和规格的铜制品,用于各种工业和消费领域。
需要注意的是,具体的选矿方法和工艺会因不同的铜矿石矿种、矿石性质和工艺要求而有所差异。
铜矿选矿过程中还可能涉及到环境保护和废弃物处理等问题,需要遵守相关法规和规范,确保选矿过程的安全和环保。
铜精矿浮选流程
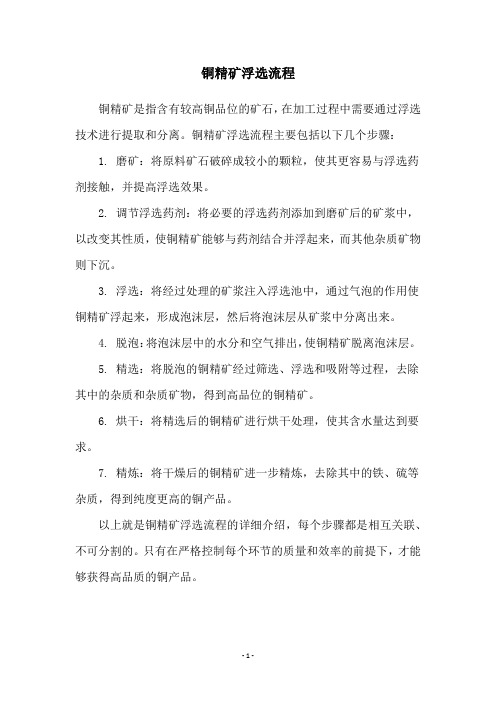
铜精矿浮选流程
铜精矿是指含有较高铜品位的矿石,在加工过程中需要通过浮选技术进行提取和分离。
铜精矿浮选流程主要包括以下几个步骤:
1. 磨矿:将原料矿石破碎成较小的颗粒,使其更容易与浮选药剂接触,并提高浮选效果。
2. 调节浮选药剂:将必要的浮选药剂添加到磨矿后的矿浆中,以改变其性质,使铜精矿能够与药剂结合并浮起来,而其他杂质矿物则下沉。
3. 浮选:将经过处理的矿浆注入浮选池中,通过气泡的作用使铜精矿浮起来,形成泡沫层,然后将泡沫层从矿浆中分离出来。
4. 脱泡:将泡沫层中的水分和空气排出,使铜精矿脱离泡沫层。
5. 精选:将脱泡的铜精矿经过筛选、浮选和吸附等过程,去除其中的杂质和杂质矿物,得到高品位的铜精矿。
6. 烘干:将精选后的铜精矿进行烘干处理,使其含水量达到要求。
7. 精炼:将干燥后的铜精矿进一步精炼,去除其中的铁、硫等杂质,得到纯度更高的铜产品。
以上就是铜精矿浮选流程的详细介绍,每个步骤都是相互关联、不可分割的。
只有在严格控制每个环节的质量和效率的前提下,才能够获得高品质的铜产品。
- 1 -。
- 1、下载文档前请自行甄别文档内容的完整性,平台不提供额外的编辑、内容补充、找答案等附加服务。
- 2、"仅部分预览"的文档,不可在线预览部分如存在完整性等问题,可反馈申请退款(可完整预览的文档不适用该条件!)。
- 3、如文档侵犯您的权益,请联系客服反馈,我们会尽快为您处理(人工客服工作时间:9:00-18:30)。
本技术涉及一种含铜钼精矿的处理方法,将含铜钼精矿磨细,获得矿粉;将矿粉与水按1:35的质量比混合均匀,进行一段氧压浸出后,固液分离,获得第一浸出液和第一浸出渣;将第一浸出渣与水按1:69的质量比混合均匀,进行二段氧压浸出后,固液分离,获得第二浸出液和第二浸出渣;对第二浸出渣进行碱浸处理,获得pH值为810的矿浆;将第二浸出液与矿浆混合,反应,获得混合浆液;对混合浆液进行固液分离后,获得第三浸出渣和富含钼的第三浸出液。
本技术的处理方法浸出率高,且酸得到有效利用。
技术要求1.一种含铜钼精矿的处理方法,其特征在于,包括如下步骤:S1、将含铜钼精矿磨细,获得矿粉;其中,含铜钼精矿中,Mo含量为 25~35wt%,Cu含量为5~9wt %;S2、将S1获得的矿粉与水按1:3-5的质量比混合均匀,进行一段氧压浸出后,固液分离,获得第一浸出液和第一浸出渣;其中,一段氧压浸出时,控制温度为110-150℃,总压力为0.6-1.0Mpa,浸出时间为1-3h;所述第一浸出液中,铜含量为12-30g/L,硫酸浓度<25g/L;S3、将S2获得的第一浸出渣与水按1:6-9的质量比混合均匀,进行二段氧压浸出后,固液分离,获得第二浸出液和第二浸出渣;其中,二段氧压浸出时,控制温度为210-230℃,总压力为2.5-3.5MPa,浸出时间为2-4h;所述第二浸出液中,钼含量为3-20g/L,硫酸浓度<100g/L;S4、对S3获得的第二浸出渣进行碱浸处理,获得pH值为8-10的矿浆;S5、将S3获得的第二浸出液与S4获得的矿浆混合,反应,用第二浸出液进行调酸,获得混合浆液;S6、对S5获得的混合浆液进行固液分离后,获得第三浸出渣和富含钼的第三浸出液。
2.其中,所述第三浸出液中,钼含量为20-40 g/L,硫酸浓度<40g/L;根据权利要求1所述的处理方法,其特征在于,S1中,将含铜钼精矿磨细至D90<30μm。
3.根据权利要求1所述的处理方法,其特征在于,S2中,所述第一浸出液中,铜含量为15~25g/L,硫酸浓度15-23g/L。
4.根据权利要求1所述的处理方法,其特征在于,S2之后,通过萃取法回收第一浸出液中的铜。
5.根据权利要求1所述的处理方法,其特征在于,S3中,所述第二浸出液中,钼含量为4-16g/L,硫酸浓度80-98g/L。
6.根据权利要求1所述的处理方法,其特征在于,S4中,碱浸处理时,控制浸出温度为20-80℃,液固质量比为1-3:1,浸出时间为2-4h。
7.根据权利要求1所述的处理方法,其特征在于,S4中,碱浸处理时,所用浸出液含有碳酸钠、氢氧化钠、氨水中的一种或几种。
8.根据权利要求1所述的处理方法,其特征在于,S6中,所述第三浸出液中,钼含量为25-38g/L,硫酸浓度25-35g/L。
9.根据权利要求1-8任一项所述的处理方法,其特征在于,S6之后,通过萃取法回收第三浸出液中的钼,获得水相和富含钼的有机相。
10.根据权利要求9所述的处理方法,其特征在于,用氨水对所述有机相进行反萃取,然后进行酸沉、结晶,获得钼酸铵。
技术说明书一种含铜钼精矿的处理方法技术领域本技术涉及一种含铜钼精矿的处理方法,属于湿法冶金领域。
背景技术钼作为一种重要的稀有金属被广泛用于钢铁、催化剂、颜料等工业领域。
地壳中钼平均含量仅为1.11g/t,铜钼矿石是金属钼的主要来源之一,通常赋存在斑型铜矿床中,接近一半的钼产量来源于铜钼矿石中伴生回收,因此钼精矿中通常含有铜。
目前,工业上处理钼精矿(辉钼矿)主要采用直接氧化焙烧—氨浸—酸程是钼精矿经氧化焙烧转化为易被氨水浸出的三氧化钼,浸出液净化后、酸沉生产钼酸铵。
钼精矿焙烧一般采用多膛炉、沸腾焙烧炉、回转窑及反射炉等。
烧工艺存在温度过高导致焙烧产物三氧化钼易升华损失、三氧化钼与伴生金属钼酸盐生成低共熔物使物料烧结而影响产品脱硫、低SO2浓度烟气难以制酸利生的铼元素挥发损失等缺点。
因此,亟需一种环保、高效、经济的冶炼技术替代现有的冶炼技术。
全湿法冶金可从根本上避免有害气体SO2的产生,金属回收率较传统方法有较大提高,可综合回收伴生金属铼,而且能处理低品位、复杂的辉钼矿,并易实过程的自动化。
目前已经形成了较多辉钼矿湿法冶金方法,一般分为常压氧化分解和高压氧化分解。
常压氧化分解主要有硝酸或硝酸盐氧化分解法、次氯酸出、生物氧化浸出等,该类工艺存在氧化剂耗量大、污水处理难度大、氯气污染或浸出效率低等缺点。
钼精矿高压氧化分解主要有加压碱浸法和加压氧化法。
加压碱浸法采用Na2CO3、NaOH等碱性试剂浸出钼精矿,该工艺存在耗碱量大,辅助生产成本高。
加一定量水,在氧压条件下浸出,将MoS2转化为MoO3,再进行后续的碱浸工序。
中国专利CN101323915B提出了将磨细的钼镍矿进行氧压水浸,得到含钼和镍氧化物的浸出渣,再将浸出液进行萃取分离钼、镍,产出镍盐和钼酸铵或三氧化钼,将浸出渣中的钼进行常压碱浸、净化、酸沉钼酸铵加以回收。
中国专利辉钼矿进行氧压水浸,液固分离后,浸出液送离子交换法或萃取工艺回收钼酸根离子,浸出渣经氨浸、过滤、结晶制得钼酸铵产品。
美国专利US 8753591B2浸、浸出渣常压碱浸、混合酸浸、钼萃取的工艺处理辉钼矿。
技术内容针对现有技术的不足,本技术提供一种含铜钼精矿的处理方法,以实现对铜、钼的高效浸出。
为了解决上述技术问题,本技术的技术方案如下:一种含铜钼精矿的处理方法,包括如下步骤:S1、将含铜钼精矿磨细,获得矿粉;其中,含铜钼精矿中,Mo含量为25~35wt%,进一步为27-33wt%,Cu含量为5~9wt%,进一步为5.2-8.5wt%;S2、将S1获得的矿粉与水按1:3-5(进一步为1:3.2-4.8)的质量比混合均匀,进行一段氧压浸出后,固液分离,获得第一浸出液和第一浸出渣;其中,一段氧压浸出时,控制温度为110-150℃,进一步为120-140℃,总压力为0.6-1.0Mpa,进一步为0.7-0.9MPa,浸出时间为1-3h,进一步为1.2-2.8h;所述含量为12~30g/L,硫酸浓度<25g/L;S3、将S2获得的第一浸出渣与水按1:6-9(进一步为1:7-8)的质量比混合均匀,进行二段氧压浸出后,固液分离,获得第二浸出液和第二浸出渣;其中,二段氧压浸出时,控制温度为210-230℃,进一步为215-225℃,总压力为2.5-3.5MPa,进一步为2.7-3.2MPa,浸出时间为2-4h,进一步为2.5-3.5h;所述钼含量为3-20g/L,硫酸浓度<100g/L;S4、对S3获得的第二浸出渣进行碱浸处理,获得pH值为8-10的矿浆;S5、将S3获得的第二浸出液与S4获得的矿浆混合,反应,用第二浸出液进行调酸,获得混合浆液;S6、对S5获得的混合浆液进行固液分离后,获得第三浸出渣和富含钼的第三浸出液。
其中,所述第三浸出液中,钼含量为20-40g/L,硫酸浓度<40g/L;进一步地,S1中,将含铜钼精矿磨细至D90<30μm。
申请人反复研究发现,采用该磨细程度出需要,又不至于大幅增加成本、磨细时间。
进一步地,S2中,所述第一浸出液中,铜含量为15~25g/L,硫酸浓度15~23g/L。
进一步地,S2之后,通过萃取法回收第一浸出液中的铜。
可选的,萃取剂浓度为15%~30%,相比(O/A)为0.25/1~2.5/1。
采用铜电积废液作为反萃剂,相比进一步地,S3中,所述第二浸出液中,钼含量为4-16g/L,硫酸浓度80-98g/L。
进一步地,S4中,碱浸处理时,控制浸出温度为20-80℃,进一步为25-75℃,液固质量比为1-3:1,进一步为1.2-2.8:1,浸出时间为2-4h,进一步为2.2-3.5h。
优进一步地,S4中,碱浸处理时,所用浸出液含有碳酸钠、氢氧化钠、氨水中的一种或几种。
进一步地,S6中,所述第三浸出液中,钼含量为25-38g/L,硫酸浓度25-35g/L。
进一步地,S6之后,通过萃取法回收第三浸出液中的钼,获得水相和富含钼的有机相。
可选的,所述有机相为常规工艺溶剂。
进一步地,用氨水对所述有机相进行反萃取,然后进行酸沉、结晶,获得钼酸铵。
本技术的工艺原理如下:2CuFeS2+H2SO4+8.5O2=2CuSO4+Fe2(SO4)3+H2OCu2S+2.5O2+H2SO4=2CuSO4+H2OMoS2+4.5O2+2H2O=MoO3+2H2SO4MoS2+4.5O2+3H2O=H2MoO4+2H2SO4MoO3+Na2CO3=Na2MoO4+CO2MoO3+2NaOH=Na2MoO4+H2O申请人利用CN101323915B、CN106477630B、US8753591B2对本技术的含铜钼精矿(Mo含量为25~35wt%,Cu含量为5~9wt%)进行浸出研究时发现,最终的60%,无法获得相关技术的预期结果,且随着原料中铜含量升高,钼的转化率急剧降低。
例如当铜含量为5.5%时,钼转化率为54.51%;当铜品位为7.1%时45.81%;当铜品位为8.5%时,钼转化率为28.5%。
因此,钼精矿中的铜对硫化钼转化为氧化钼有明显抑制作用。
与现有技术相比,本技术的有益效果如下:(1)由于钼精矿中的铜含量对硫化钼转化为氧化钼的效率有很大的抑制作用,本技术采用两段氧压浸出工艺,第一段在较温和条件下浸出铜,一段浸出液萃取工艺,实现钼精矿中铜、钼的分离及回收。
一段浸出渣在强化的条件下使硫化钼转化为氧化钼,便于后续常压碱浸,最终钼浸出率可达98%以上。
(2)由于第一段氧压浸出条件温和,浸出液含酸低,无需中和,可直接进行铜萃取。
将碱浸滤液与含酸较高的二段浸出液混合,可达到降酸的技术效果,进而取,也解决了酸的后处理问题。
(3)可采用石灰中和钼萃余液,获得了石膏产品,增加了产品的附加值。
附图说明图1是本技术的一种含铜钼精矿的处理方法的工艺流程图。
具体实施方式下面将对本技术实施例中的技术方案进行清楚、完整地描述,显然,所描述的实施例仅是本技术一部分实施例,而不是全部实施例,基于本技术中的实施例人员在没有做出创造性劳动前提下所获得的所有其他实施例,都属于本技术保护的范围。
实施例1本实施例中,含铜钼精矿的处理方法如下:(1)取100g含铜钼精矿(含Mo 27.5wt%,Cu 5.5wt%,S 24.6wt%),磨矿至D90<30μm。
(2)将细磨的钼精矿与水按1:3.2混匀后加入高压釜进行一段氧压浸出,浸出条件为135℃,总压力0.7Mpa,浸出1.5h。
液固分离获得一段含铜滤液(铜16.9g/L,段浸出渣(含铜0.11wt%),铜浸出率为98.16wt%。
(3)将一段含铜滤液采用25%萃取剂+75%煤油(v/v)萃取铜,相比(O/A)为1:1,两级萃取,萃余液含铜0.15g/L,铜萃取率为99.11wt%。