QA工作标准管理制度
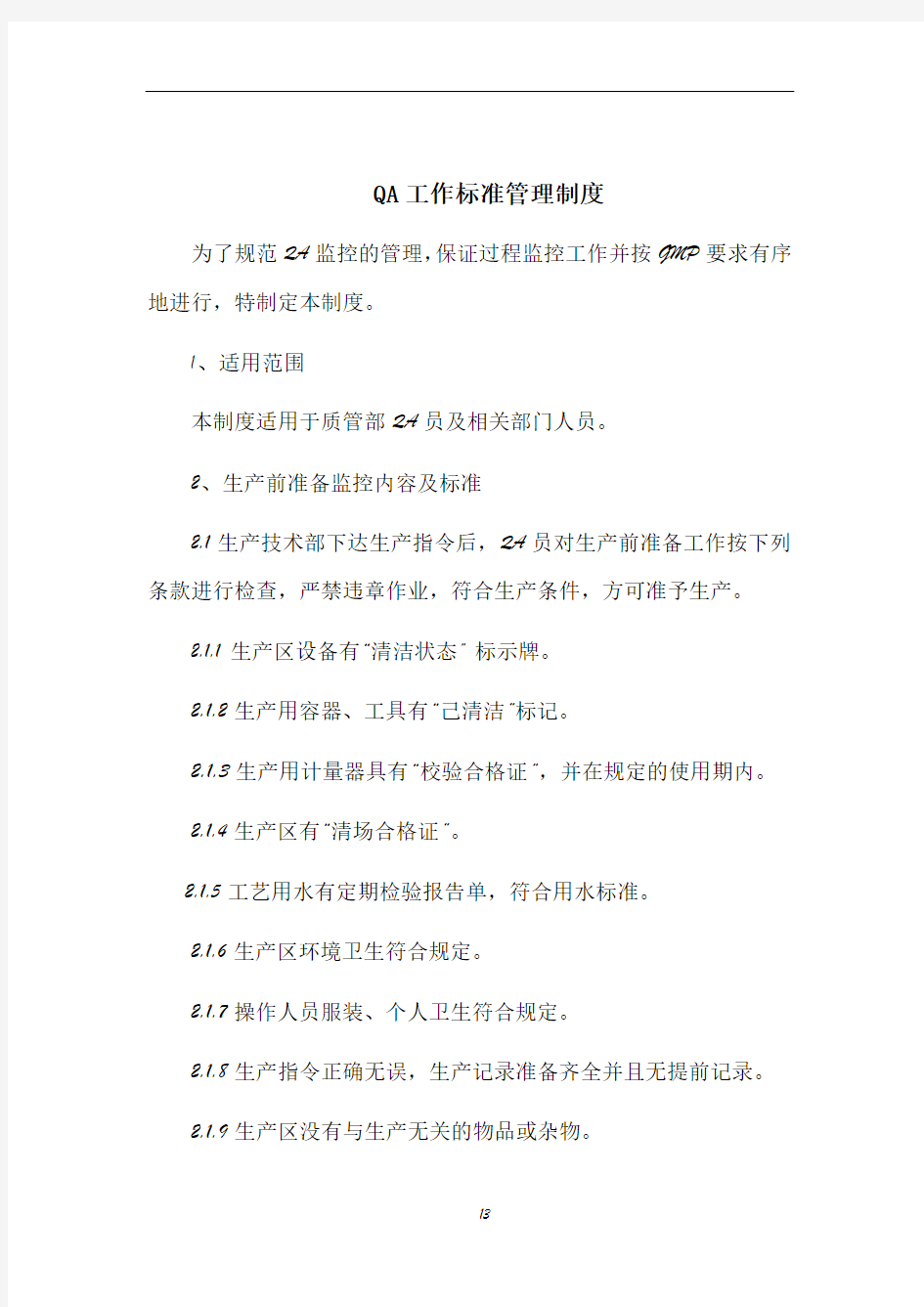

QA工作标准管理制度
为了规范QA监控的管理,保证过程监控工作并按GMP要求有序地进行,特制定本制度。
1、适用范围
本制度适用于质管部QA员及相关部门人员。
2、生产前准备监控内容及标准
2.1生产技术部下达生产指令后,QA员对生产前准备工作按下列条款进行检查,严禁违章作业,符合生产条件,方可准予生产。
2.1.1生产区设备有“清洁状态” 标示牌。
2.1.2生产用容器、工具有“己清洁”标记。
2.1.3生产用计量器具有“校验合格证”,并在规定的使用期内。
2.1.4生产区有“清场合格证”。
2.1.5工艺用水有定期检验报告单,符合用水标准。
2.1.6生产区环境卫生符合规定。
2.1.7操作人员服装、个人卫生符合规定。
2.1.8生产指令正确无误,生产记录准备齐全并且无提前记录。
2.1.9生产区没有与生产无关的物品或杂物。
2.1.10核对生产所领物料与生产指令单是否一致,并应有质管部出具的合格报告书。
3、按批准的工艺规程、岗位标准操作程序及卫生监控规程等进行生产全过程检查,详见生产
全过程监控管理制度。
4、物料平衡与偏差处理
4.1物料平衡
4.1.1制剂生产必须按照处方量的100%(标示量)投料。如已知某一成分在生产或贮存期间
含量会降低,工艺规程中可规定适当增加投料量。
4.1.2产品(或物料)的理论产量(或理论用量)与实际产量之间的比值应有可允许的正常
偏差。
4.1.3每批产品应在生产作业完成后,作物料平衡检查。如有差异,必须查明原因,在得出
合理解释、确认无潜在质量事故后,方可按正常产品处理。
4.2偏差处理
4.2.1 出现下列偏差时必须及时处理。
4.2.1.1物料平衡超出收率的正常范围。
4.2.1.2生产过程时间控制超出工艺规程规定的范围。
4.2.1.3生产过程中工艺条件发生偏移、变化。
4.2.1.4生产过程中设备突然出现异常,可能影响产品质量。
4.2.1.5产品质量(含量、外观、工序加工)发生偏移。
4.2.1.6跑料。
4.2.1.7标签、说明书、小盒的实用数、剩余数、残损数之和与领用数发生差额。
4.2.1.8生产过程中其他异常情况。
4.2.2偏差处理程序
4.2.2.1发生超限偏差时,必须填写偏差处理单,写明产品的品名、批号、规格、批量、工
序、偏差内容、发生的过程原因、地点、填表人签字、日期。将偏差处理记录交给生产部管
理人员。
4.2.2.2生产部负责人及车间管理人员会同有关人员进行调查,根据调查结果提出处理建议:
(A)继续加工,(B)重新加工,(C)回收或采取其他补救措施。如确认可能影响产品质量者,
必须报废或销毁。
4.2.2.3生产部管理人员将上述处理建议(必要时应验证),写出书面报告(一式两份),生
产部负责人签字后连同偏差通知单报质管部,由质管部负责人审核、总工批准。
4.2.2.4生产车间按批准的文件组织实施;同时将偏差报告单、调查报告、处理措施及实施
结果归档备查。
4.2.2.5如发现偏差批次与该批前后批次产品有关连时,必须立即通知质量部,作出相应处
理。
5、清场管理
5.1清场时间为了防止药品生产不同批号、品种、规格之间的污染和交叉污染,各生产工序在生产结束、更换品种及规格或换批号前,应彻底清理及检查作业场所。
5.2 清场要求
5.2.1地面无积灰、无结垢,门窗、室内照明灯、风管、墙面、开关箱外壳无积灰,室内不
得存放与生产无关的物品。
5.2.2使用的工具、容器应清洁、无异物,无前次产品的遗留物。
5.2.3设备内外无前次生产遗留的药品,无油垢。
5.2.4非专用设备、管道、容器、工具应按规定清洗、消毒或灭菌。
5.2.5直接接触药品的机器、设备及管道、工具、容器应每天或每批清洗、消毒。同一设备
连续加工同一非无菌产品时,其清洗周期可按设备清洗的有关规定执行。
5.2.6包装工序调换品种时,剩余的标签、小盒、说明书等包装材料应按规定处理。
5.2.7固体制剂工序调换品种时,对难以清洗的用品,如烘布、布袋、应予调换。
5.2.8 清场记录清场工作应有清场记录。清场记录应包括工序、清场前产品的品名、规格、批号、清场日期、清场项目、检查情况、清场人、复核人及其签字。清场记录须归入批生产记录存档。清场结束由质管部QA人员检查合格后发给“清场合格证”。清场合格证正本附入该批生产记录中,清场合格证副本作为下一个批号、品种(或同一品种不同规格)的生产凭证附入生产记录。未领得“清场合格证”不得进行下一步的生产。
6、状态标识管理
6.1生产区内设备、生产操作、中间站和物料均应挂状态标志。
6.1.1车间中间站内用红、黄、绿三种颜色的状态标志划分三个不同的存放区:
6.1.1.1绿色是合格品及存放区。
6.1.1.2黄色是待验品及存放区。
6.1.1.3红色是不合格品及存放区。
6.1.2 车间站的容器外均应有物料标志卡。
6.1.2.1 物料标志卡用红、黄、绿三种颜色的状态标志划分三个不同的状态:
6.1.2.1.1绿色《合格品》标识,注明品名、产品批号、规格、数量等。
6.1.2.1.2红色《不合格品》标识,注明品名、产品批号、规格、数量、生产日期、不合格项目等。
6.1.2.1.3黄色《待检品》标识,注明品名、批号、规格、数量、生产日期等。
6.1.2.2半成品、成品的状态挂于容器上醒目、显而易见处。
6.1.3操作间状态标志分以下三种:
6.1.3.1 生产状态标志:表明正在进行的生产操作的状态标志,用准产证作为标志,其内容包括该区域内所生产产品的品名、规格、批号等。
6.1.3.2 设备状态标志:工程部确认的是否可以使用的标志。
6.1.3.2.1绿色表示设备状态完好。
6.1.3.2.2红色表示设备状态待修。
6.1.4 清洁状态标志
6.1.4.1操作间:在生产结束后悬挂“待清洁”(黄色)标志,清场结束后悬挂“已清洁”(绿
色)标志。
6.1.4.1器具清洁间:划分洁净器具存放间和器具清洗间。对盛装药品的容器应有状态标志,未清洁的要挂黄色“待清洁”标识牌,放在器具清洗间,已清洁的容器挂绿色《已清洁》标识牌,存放在洁净器具存放间。
6.1.5 处于使用状态的容器应标明内容物品名、规格、批号、重量、使用日期。
7、QA检查管理
7.1 仓库检查
7.1.1 检查频率每月检查2次
7.1.2 抽查标准按物料管理相关规定进行
7.1.3 抽查方式采取抽查方式进行,时间、抽查人不进行确定,但不得进行抽查的事先通知。
7.1.4 抽查的基本要求抽查内容以物料的分区存放、物料状态标识、账物相符、存贮要求、包装情况等为主。
7.2 制水车间检查
7.2.1 检查频率每月检查2次
7.2.2 抽查标准按制水的相关规定进行
7.2.3 抽查方式采取抽查方式进行,时间、抽查人不进行确定,但不得进行抽查的事先通知。
7.2.4 抽查的基本要求抽查内容以制水车间记录、状态标识、自行监控内容复核、试剂及器具的存放、操作是否正规、检定情况为主。
7.3公用工程检查
7.3.1 检查频率每月检查2次
7.3.2 抽查标准按公用工程的相关规定进行
7.3.3 抽查方式采取抽查方式进行,时间、抽查人不进行确定,但不得进行抽查的事先通知。
7.3.4 抽查的基本要求抽查内容以记录、状态标识、自行监控内容复核、是否持证上岗、检定情况为主。
7.4 饮用水检查
7.4.1 检查频率每月检查1次
7.4.2 抽查标准按饮用水的相关规定进行
7.4.3 抽查方式由QC每月进行,QA进行监督执行。
7.4.4 抽查的基本要求检查主要是检验的相关记录。
7.4 纯化水、注射用水检查
7.4.1 检查频率按工艺用水布局图进行,其中总送、总回每周全检1次、每周抽一个使用
点全检1次。
7.4.2 抽查标准按工艺用水相关规定进行。
7.4.3 抽查方式由QC每月进行,QA进行监督执行。
7.4.4 抽查的基本要求检查主要是检验的相关记录。
7.5 环境检查
7.5.1 悬浮粒子测定频次静态每3个月测定1次,动态第半年测定1次。
7.5.2 沉降菌测定频次
7.5.2.1 100级、10000级:静态每星期测定1次(如停产超过1周,在生产前进行测定),动态每1个月测定1次。100级局部百级区每班测定一次(非灭菌制剂)。
7.5.2.2 100000级、300000级:静态每月测定1次(如停产超过1周,在生产前进行测定),动态每3个月测定1次。
7.5.3 抽查标准按环境监测管理规程进行。
7.4.4 抽查方式由QA按测定频次及沉降菌标准操作程序及悬浮粒子标准操作程序进行检查。
7.6 领料工序检查
7.6.1 检查频率按生产批次进行,每批一次。
7.6.2 抽查标准按注射剂生产过程质量控制扣罚细则进行。
7.6.3 抽查方式采取抽查方式进行,部分内容可与批生产记录现场审核同时进行。
7.6.4 抽查的基本要求检查主要以考核细则内容为主。
7.7 称量、配液或混合工序检查
7.7.1 检查频率按生产批次进行,中间体指标每批1次;可见异物按不同容器进行,每批
1次。
7.7.2 抽查标准项目及指标按中间体质量标准进行,并按注射剂生产过程质量控制扣罚细则进行。
7.7.3 抽查方式采取定时检查,采取放行控制。取样按中间体取样标准进行取样,应具有代表性。
7.7.4 抽查的基本要求检查主要以考核细则内容为主。
7.8 灌装、分装工序检查
7.8.1 检查频率按生产批次进行,西林瓶、胶塞可见异物检查每批3次;装量每批至少抽查3次。
7.8.2 抽查标准装量按中间体测定结果及工艺规程要求进行,并按注射剂生产过程质量控制扣罚细则标准进行。
7.8.3 抽查方式采取定时检查,放行控制。第一次检查在灌装调试时进行应,结合西林瓶、胶塞、中间体质量,合格后方可准许进行此工序。在生产过程中按检查频率进行,其时间应按设备产生偏差的时间做为参照进行,在合格的前提下,准许继续进行,如不符合要求应进行纠偏,并将检查前的质量情况进行调查分析,在不存在质量隐患的前提下准许继续进行。
7.8.4 抽查的基本要求检查主要是以西林瓶、胶塞可见异物检查、装量检查为主。按注射剂生产过程质量控制扣罚细则标准进行。
7.9 灯检、目检工序检查
7.9.1检查频率按生产批次进行,每批1次。
7.9.2 抽查标准按灯检、目灯标准要求进行抽检,并按注射剂生产过程质量控制扣罚细则标准进行。
7.9.3 抽查方式采取包装前定时检查,放行控制。
7.9.4 抽查的基本要求检查主要是对灯检后的成品、不合格品进行抽检,并进行灯检结果的统计,按实际情况决定是否放行。其灯检
内容应以可见异物、压盖质量为主。并按注射剂生产过程质量控制扣罚细则标准进行。
7.10 冻干、压盖、灭菌工序检查
7.10.1检查频率按生产批次进行,每批1次。
7.10.2 抽查标准按相应的工序监控标准操作程序进行。
7.10.3 抽查方式采取不定时抽查,可与批生产记录的审核同时进行。
7.10.4 抽查的基本要求抽查主要审核是否与工艺规程的参数是否相符,如进行工艺变更,应及时上报。并按注射剂生产过程质量控制扣罚细则标准进行。
7.11 包装工序检查
7.11.1检查频率按生产批次进行,每批1次。
7.11.2 抽查标准按相应的工序监控标准操作程序进行。
7.11.3 抽查方式采取不定时抽查。
7.11.4 抽查的基本要求按注射剂生产过程质量控制扣罚细则标准进行。
7.12 生产前准备检查
7.12.1检查频率按生产批次进行,每批1次。
7.12.2 抽查标准按生产前准备监控内容及标准管理制度,并按相应的工序监控标准操作程序进行。
7.12.3 抽查方式采取不定时抽查。
7.12.4 抽查的基本要求按注射剂生产过程质量控制扣罚细则标准进行。
7.12 批生产记录检查
7.12.1 检查频率按生产批次进行,每批1次。
7.12.2 抽查标准按批生产记录的相应规定,并按相应的工序监控标准操作程序进行。
7.12.3 抽查方式采取每批检查。
7.12.4 抽查的基本要求按注射剂生产过程质量控制扣罚细则标准进行。
本制度经总经理办公会议讨论通过后,自下达之日起执行。由质量管理部负责解释和修订。