镍基催化剂的制备、表征及选择加氢性能
加氢精制催化剂的组成制备及其性能评价
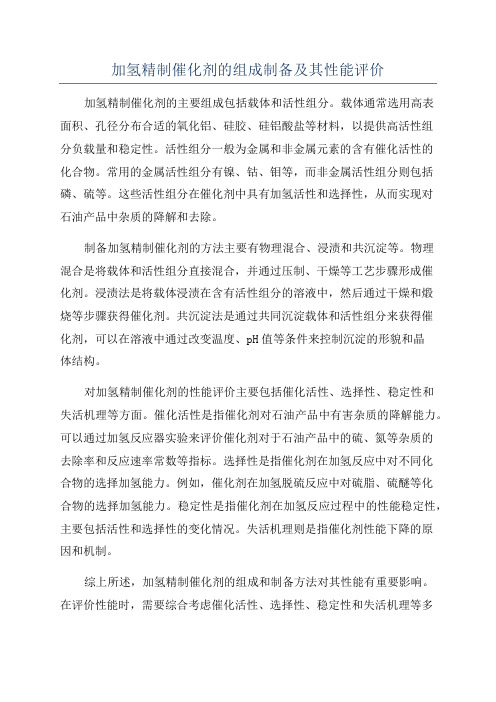
加氢精制催化剂的组成制备及其性能评价加氢精制催化剂的主要组成包括载体和活性组分。
载体通常选用高表面积、孔径分布合适的氧化铝、硅胶、硅铝酸盐等材料,以提供高活性组分负载量和稳定性。
活性组分一般为金属和非金属元素的含有催化活性的化合物。
常用的金属活性组分有镍、钴、钼等,而非金属活性组分则包括磷、硫等。
这些活性组分在催化剂中具有加氢活性和选择性,从而实现对石油产品中杂质的降解和去除。
制备加氢精制催化剂的方法主要有物理混合、浸渍和共沉淀等。
物理混合是将载体和活性组分直接混合,并通过压制、干燥等工艺步骤形成催化剂。
浸渍法是将载体浸渍在含有活性组分的溶液中,然后通过干燥和煅烧等步骤获得催化剂。
共沉淀法是通过共同沉淀载体和活性组分来获得催化剂,可以在溶液中通过改变温度、pH值等条件来控制沉淀的形貌和晶体结构。
对加氢精制催化剂的性能评价主要包括催化活性、选择性、稳定性和失活机理等方面。
催化活性是指催化剂对石油产品中有害杂质的降解能力。
可以通过加氢反应器实验来评价催化剂对于石油产品中的硫、氮等杂质的去除率和反应速率常数等指标。
选择性是指催化剂在加氢反应中对不同化合物的选择加氢能力。
例如,催化剂在加氢脱硫反应中对硫脂、硫醚等化合物的选择加氢能力。
稳定性是指催化剂在加氢反应过程中的性能稳定性,主要包括活性和选择性的变化情况。
失活机理则是指催化剂性能下降的原因和机制。
综上所述,加氢精制催化剂的组成和制备方法对其性能有重要影响。
在评价性能时,需要综合考虑催化活性、选择性、稳定性和失活机理等多个方面的指标。
只有通过合理的组成制备和全面的性能评价,才能获得更高效、更稳定的加氢精制催化剂。
镍基Ni-Mo合金电极的制备及其电催化析氢性能研究

College of Chemistry and Chemical Engineering of Chongqing University, Chongqing, China May, 2013
重庆大学硕士学位论文中文摘要摘 Nhomakorabea要
氢能作为一种高效,清洁,理想的二次能源,越来越受到各国的重视。其中, 电解水制氢具有操作简单、产品纯度高、无污染等优点,有望成为替代化石燃料 制氢的有效方法。目前,工业中运用电解水制氢的阴极材料主要是 Rany Ni,低碳 钢等材料,但它们存在过电位高、槽电压大、能耗过大和易腐蚀等劣势,严重制 约了电解水以及氯碱工业的发展。因此,为了解决上述问题,研究和开发一种高 效、稳定、廉价的析氢电极具有非常重要的现实意义和实用价值。镍基合金材料 由于具有较好的催化析氢活性和良好的稳定性而成为近年来的研究热点。本论文 分别采用脉冲电沉积和磁控溅射法制备了 Ni-Mo-P/Ni 和 Ni-Mo/Ni 析氢电极, 系统 探究了电极的制备条件及其析氢性能的影响。 以硫酸镍,钼酸铵,次亚磷酸钠分别作为镍源、钼源和磷源,采用脉冲电沉 积制备了 Ni-Mo-P/Ni 电极。运用 XRD,SEM 和 EDS 等材料表征手段和现代电化 学测试方法考察了镀层的表面组成、结构、微观形貌及其催化析氢性能。实验结 果表明,通过脉冲电沉积制备的 Ni-Mo-P 镀层表面粗糙,颗粒细小,分布均匀。 XRD 和 EDS 测试结果显示,Mo 的引入使催化剂镀层进一步呈现非晶态化,从而增 大镀层真实表面积, 进而提高析氢催化性能。 当 Mo 的含量为 30 wt%时, Ni-Mo-P/Ni 电极具有最好的催化析氢性能。与纯 Ni 片相比,Ni-Mo-P/Ni 电极的析氢电位正移了 270 mV; 与 Ni-P/Ni 电极相比,正移了 100 mV 左右。在碱性条件下电解的计时电位 曲线显示,Ni-Mo-P/Ni 电极具有较好的稳定性。 利用磁控溅射法对 Ni 基表面进行改性, 沉积 Ni-Mo 薄膜。 通过改变溅射功率、 真空室内的气压、反应时间和温度,调控薄膜的厚度、微观形貌及元素组成,制 得 Ni-Mo 合金电极,并考察其催化析氢性能。实验结果表明,溅射功率决定薄膜 的组分,而溅射气压决定薄膜的表面的粗糙度。当溅射室气压为 4 Pa,Ni 靶和 Mo 靶的溅射功率分别为 80 W 和 180 W,基体温度为 500℃时,制备的电极具有较好 的催化析氢性能。在 6M NaOH 电解液中,电流密度为 100 mA.cm-2 时,与纯 Ni 片相比,Ni-Mo 合金电极的催化析氢电位正移了 281 mV。这主要是由于 Ni-Mo 合 金为纳米晶型,颗粒分布均匀,具有较小的晶粒直径,使电极的比表面积显著增 大;同时,与纯 Ni 相比,Ni-Mo 合金电阻减小,因而 Ni-Mo 合金电极具有更好的 催化析氢性能。 关键词:镍基合金电极,析氢反应,稳定性,脉冲电沉积,磁控溅射
镍基材料nimopso催化剂

镍基材料nimopso催化剂全文共四篇示例,供读者参考第一篇示例:镍基催化剂是一类重要的催化剂,具有良好的稳定性和活性,在许多领域有着广泛的应用。
本文将重点介绍一种新型的镍基催化剂——NiMoPSo催化剂,探讨其制备方法、结构特点以及在催化应用中的潜在价值。
NiMoPSo催化剂是一种由镍、钼、磷和硫组成的复合材料,具有优良的催化性能和热稳定性。
该催化剂制备方法相对简单,一般是以合成气或氢气氛围下,在高温下将镍盐、钼盐、磷酸盐和硫化物等原料经过一系列处理和反应,得到NiMoPSo催化剂。
在制备过程中,控制不同配比的原料比例以及反应条件,可以调控催化剂的结构和性能。
NiMoPSo催化剂的结构特点主要表现在其纳米级的颗粒结构和高比表面积。
这一独特的结构特点使得NiMoPSo催化剂具有较高的活性和选择性,对一些重要的催化反应具有良好的催化效果。
NiMoPSo催化剂在氢气化反应、重整反应和硫脱硫反应等领域均表现出色。
NiMoPSo催化剂还具有较好的抗硫性能和抗积炭性能,能够有效地延长其使用寿命。
在实际的工业应用中,NiMoPSo催化剂有望在石油加工、化学合成、环境保护等领域发挥重要作用。
以石油加工为例,NiMoPSo催化剂可以应用于重质油加氢裂解、脱硫脱氮等反应中,提高产品质量和降低污染物排放。
在化学合成领域,NiMoPSo催化剂可以用于制备有机化合物、燃料等重要产品,提高生产效率和产物纯度。
在环境保护方面,NiMoPSo催化剂可以应用于废气处理、废水处理等领域,减少排放的有害气体和废水,保护环境并促进可持续发展。
第二篇示例:首先我们来说说nimopso催化剂的制备方法。
nimopso催化剂是由镍、钼、磷、硅等元素组成的复合物,通常制备过程中包括溶胶-凝胶法、共沉淀法、水热法等。
溶胶-凝胶法是制备nimopso催化剂的常用方法之一。
该方法首先将镍盐、钼盐、磷盐和硅源等原料按一定比例溶解于适当的溶液中,然后通过水解、凝胶化、干燥、焙烧等过程,制备出nimopso催化剂。
镍基催化剂:制备及水相催化糠醛加氢脱氧反应性能

镍基催化剂:制备及水相催化糠醛加氢脱氧反应性能张兴华;王铁军;马隆龙;江婷;刘琪英;章青【摘要】以SiO2-Al2O3、γ-Al2O3为载体采用浸渍法制备了不同负载量的镍基催化剂,以XRD、H2-TPR、NH3-TPD与低温N2吸附等技术对催化剂特性进行了表征,并进行了水相催化糠醛加氧脱氧实验研究以制备以C5为主要成分的生物汽油.重点考察了催化剂的镍负载量、载体种类及反应温度对糠醛转化牢、目标产物C5选择性的影响,并对催化剂的重复利用性能和糠醛水相加氢脱氧反应机理进行了探讨.结果表明,Ni/SiO-Al2O3催化性能明显优于Ni/γ-Al2O3.在140℃、氢冷压3.0 MPa的优化反应条件下,14wt%Ni/SiO2-AlO3催化糠醛反应的转化率为63%,C5选择性高达93%.升高反应温度町以提高糠醛的转化率,但反应产物的选择性降低.催化剂在第3次重复使用时糠醛的转化率明显降低,催化剂表面有明显的残留有机聚合物和积碳,达到25wt%左右.【期刊名称】《无机化学学报》【年(卷),期】2010(026)012【总页数】7页(P2182-2188)【关键词】镍催化剂;加氢脱氧;糠醛;生物汽油【作者】张兴华;王铁军;马隆龙;江婷;刘琪英;章青【作者单位】中国科学院可再生能源与天然气水合物重点实验室,中国科学院广州能源研究所,广州,510640;中国科学院研究生院,北京,100049;中国科学院可再生能源与天然气水合物重点实验室,中国科学院广州能源研究所,广州,510640;中国科学院可再生能源与天然气水合物重点实验室,中国科学院广州能源研究所,广州,510640;中国科学院可再生能源与天然气水合物重点实验室,中国科学院广州能源研究所,广州,510640;中国科学院研究生院,北京,100049;中国科学院可再生能源与天然气水合物重点实验室,中国科学院广州能源研究所,广州,510640;中国科学院可再生能源与天然气水合物重点实验室,中国科学院广州能源研究所,广州,510640【正文语种】中文【中图分类】O614.83+3;TQ221.1近年来随着化石资源的日益紧张,以及人类对能源资源需求的迅速增长,化石原料供给的稳定性变得日益脆弱[1-2]。
镍基CO加氢反应催化剂及其设备制作方法与应用与设计方案
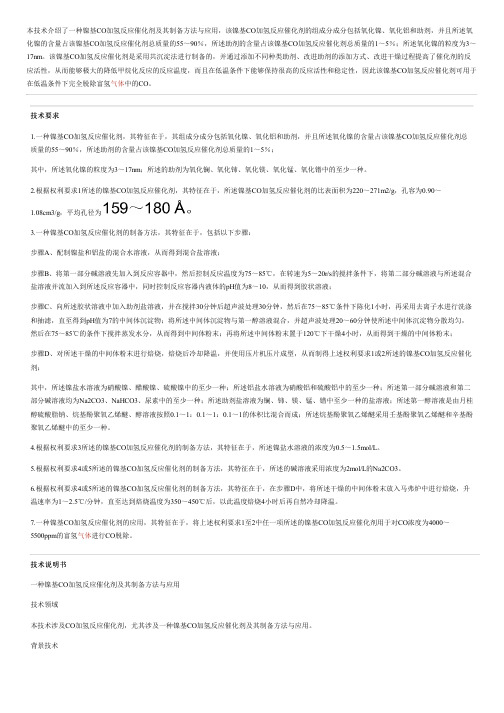
本技术介绍了一种镍基CO加氢反应催化剂及其制备方法与应用,该镍基CO加氢反应催化剂的组成分成分包括氧化镍、氧化铝和助剂,并且所述氧化镍的含量占该镍基CO加氢反应催化剂总质量的55~90%,所述助剂的含量占该镍基CO加氢反应催化剂总质量的1~5%;所述氧化镍的粒度为3~17nm。
该镍基CO加氢反应催化剂是采用共沉淀法进行制备的,并通过添加不同种类助剂、改进助剂的添加方式、改进干燥过程提高了催化剂的反应活性,从而能够极大的降低甲烷化反应的反应温度,而且在低温条件下能够保持很高的反应活性和稳定性,因此该镍基CO加氢反应催化剂可用于在低温条件下完全脱除富氢气体中的CO。
技术要求1.一种镍基CO加氢反应催化剂,其特征在于,其组成分成分包括氧化镍、氧化铝和助剂,并且所述氧化镍的含量占该镍基CO加氢反应催化剂总质量的55~90%,所述助剂的含量占该镍基CO加氢反应催化剂总质量的1~5%;其中,所述氧化镍的粒度为3~17nm;所述的助剂为氧化镧、氧化铈、氧化镁、氧化锰、氧化镨中的至少一种。
2.根据权利要求1所述的镍基CO加氢反应催化剂,其特征在于,所述镍基CO加氢反应催化剂的比表面积为220~271m2/g,孔容为0.90~1.08cm3/g,平均孔径为3.一种镍基CO加氢反应催化剂的制备方法,其特征在于,包括以下步骤:步骤A、配制镍盐和铝盐的混合水溶液,从而得到混合盐溶液;步骤B、将第一部分碱溶液先加入到反应容器中,然后控制反应温度为75~85℃,在转速为5~20r/s的搅拌条件下,将第二部分碱溶液与所述混合盐溶液并流加入到所述反应容器中,同时控制反应容器内液体的pH值为8~10,从而得到胶状溶液;步骤C、向所述胶状溶液中加入助剂盐溶液,并在搅拌30分钟后超声波处理30分钟,然后在75~85℃条件下陈化1小时,再采用去离子水进行洗涤和抽滤,直至得到pH值为7的中间体沉淀物;将所述中间体沉淀物与第一醇溶液混合,并超声波处理20~60分钟使所述中间体沉淀物分散均匀,然后在75~85℃的条件下搅拌蒸发水分,从而得到中间体粉末;再将所述中间体粉末置于120℃下干燥4小时,从而得到干燥的中间体粉末;步骤D、对所述干燥的中间体粉末进行焙烧,焙烧后冷却降温,并使用压片机压片成型,从而制得上述权利要求1或2所述的镍基CO加氢反应催化剂;其中,所述镍盐水溶液为硝酸镍、醋酸镍、硫酸镍中的至少一种;所述铝盐水溶液为硝酸铝和硫酸铝中的至少一种;所述第一部分碱溶液和第二部分碱溶液均为Na2CO3、NaHCO3、尿素中的至少一种;所述助剂盐溶液为镧、铈、镁、锰、镨中至少一种的盐溶液;所述第一醇溶液是由月桂醇硫酸脂钠、烷基酚聚氧乙烯醚、醇溶液按照0.1~1:0.1~1:0.1~1的体积比混合而成;所述烷基酚聚氧乙烯醚采用壬基酚聚氧乙烯醚和辛基酚聚氧乙烯醚中的至少一种。
镍催化剂催化加氢的机理探究

镍催化剂催化加氢的机理探究镍催化剂催化加氢的机理探究在化学领域中,催化剂的使用极为广泛,而镍催化剂作为一种重要的催化剂,具有在加氢反应中的广泛应用。
本文将深入探究镍催化剂催化加氢的机理,并分享我对这一主题的观点和理解。
我们来了解一下加氢反应的基本原理。
1. 加氢反应的基本原理加氢反应是指将氢气与有机化合物在催化剂的作用下发生反应,将有机化合物中的双键或多键转化为单键的过程。
这种反应在化学工业中具有广泛的应用,常见的加氢反应包括饱和烃的制备、不饱和化合物的加氢脱氢、氢化物的还原和环代谢等。
2. 镍催化剂的特点与应用镍催化剂具有许多独特的特点,例如催化性能高、催化活性可调节、易得性好等。
镍催化剂在许多加氢反应中都表现出优秀的催化活性和选择性。
镍催化剂还具有较低的成本和环境友好性,因此被广泛应用于工业生产中的加氢反应。
3. 镍催化剂催化加氢的机理镍催化剂催化加氢的机理涉及多个步骤,以下为具体内容:3.1 吸附和激活氢气镍催化剂首先通过吸附氢气使其激活。
在催化剂表面,氢气分子会与表面的镍原子形成键合,从而使氢气中的化学键变得更容易断裂。
3.2 吸附和激活有机化合物在催化剂表面,有机化合物分子与镍原子形成键合,吸附在催化剂表面,从而使有机化合物中的双键或多键易于断裂。
3.3 反应步骤在催化剂表面上,吸附的氢气和有机化合物发生反应,产生中间体。
这些中间体随后发生反应,断裂原有的化学键,生成新的化学键,最终得到目标产物。
4. 我对镍催化剂催化加氢机理的观点和理解镍催化剂催化加氢的机理是一个复杂的过程,涉及多个步骤和反应中间体的生成。
我认为,在研究镍催化剂催化加氢机理时,需要综合考虑各个因素的影响,如镍催化剂的结构、活性位点的形成以及反应条件等。
镍催化剂的催化性能也受到催化剂的负载、助剂的添加等因素的影响。
总结:镍催化剂催化加氢是一种重要的反应,具有广泛的应用前景。
在镍催化剂催化加氢的机理探究中,深入理解反应的步骤和中间体生成的机制对于提高催化剂的活性和选择性具有重要意义。
氢气高温还原制备的负载型镍基催化剂用于苯酚加氢的性能

高温还原 法制备 了 负载型镍基催化 剂 ,考察 了 镍 前体 、载体种 类 、镍 负载量 、反应条件 等对镍基催化 剂苯酚加
氢性能 的影响 。结果表 明,对 比 3 种镍 前体 ,在 H 2 高温还原体 系中 Ni ( NO3 ) 2 最容 易被还原 ,制备 的镍 基催 化剂
苯酚加氢活性 最高。S i O 2 负载的镍基催化剂活性远 高于 丫 . A 1 2 O 3 催化 剂。适宜的 N i 负载 量有 助于活性组分 的分
散 和催化 活性的提 高 镍基 催化剂 的苯酚加 氢产 物以环 己醇为主 ,相对缓 和的反应条件 更容 易生成环 己酮。在 非极性溶 剂正 庚烷或环 己烷存在 下,苯酚加 氢反应速 率远远 高于极 性溶 剂水或 乙醇存在 下的结果 ,而且环 己酮 的选择性 更高。
关键词 :苯酚 ;加 氢;镍基催化剂 ;环 己酮;环 己醇;还原 中图分类号 :O 6 4 3 . 3 ;T E 6 6 5 . 6 2 文献标志码 :A 文章编号 :1 0 0 0— 6 6 1 3( 2 0 1 5)1 0—3 6 7 1 —0 5
s t u d i e d ,Ni ( NO 3 ) 2 wa s t h e mo s t e a s i l y r e d u c e d b y H2 a n d t h e c a t a l y s t p r e p a r e d d i s p l a y e d t h e b e s t
DoI :1 0 . 1 6 0 8 5  ̄ . i s s n . 1 0 0 0 - 6 6 1 3 . 2 0 1 5 . 1 0 . 0 2 3
Pe r f o r ma nc e o f ni c ke l s uppo r t e d c a t a l y s t s o n phe no l h yd r 0 g e na t i 0 n
镍基催化剂的苯加氢性能研究的开题报告
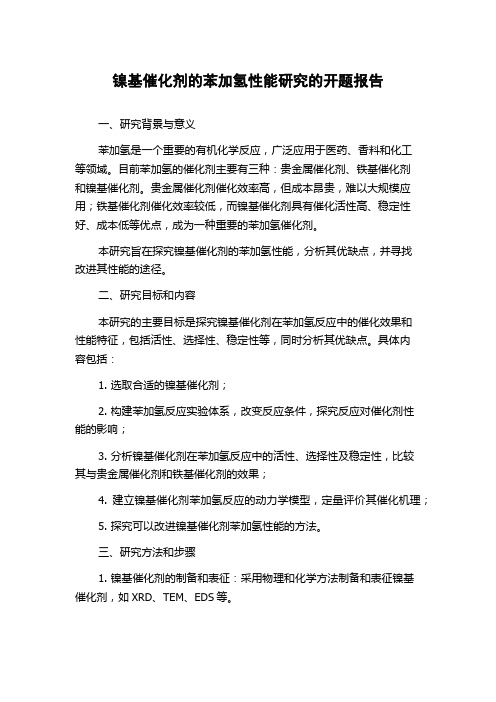
镍基催化剂的苯加氢性能研究的开题报告一、研究背景与意义苯加氢是一个重要的有机化学反应,广泛应用于医药、香料和化工等领域。
目前苯加氢的催化剂主要有三种:贵金属催化剂、铁基催化剂和镍基催化剂。
贵金属催化剂催化效率高,但成本昂贵,难以大规模应用;铁基催化剂催化效率较低,而镍基催化剂具有催化活性高、稳定性好、成本低等优点,成为一种重要的苯加氢催化剂。
本研究旨在探究镍基催化剂的苯加氢性能,分析其优缺点,并寻找改进其性能的途径。
二、研究目标和内容本研究的主要目标是探究镍基催化剂在苯加氢反应中的催化效果和性能特征,包括活性、选择性、稳定性等,同时分析其优缺点。
具体内容包括:1. 选取合适的镍基催化剂;2. 构建苯加氢反应实验体系,改变反应条件,探究反应对催化剂性能的影响;3. 分析镍基催化剂在苯加氢反应中的活性、选择性及稳定性,比较其与贵金属催化剂和铁基催化剂的效果;4. 建立镍基催化剂苯加氢反应的动力学模型,定量评价其催化机理;5. 探究可以改进镍基催化剂苯加氢性能的方法。
三、研究方法和步骤1. 镍基催化剂的制备和表征:采用物理和化学方法制备和表征镍基催化剂,如XRD、TEM、EDS等。
2. 苯加氢反应实验:根据文献和实验条件,选择合适的实验条件,设计苯加氢反应实验,记录反应数据,如反应产率、选择性等。
3. 催化剂性能分析:根据实验结果,分析镍基催化剂在苯加氢反应中的活性、选择性、稳定性,并比较其与贵金属催化剂和铁基催化剂的效果。
4. 动力学模型建立:根据实验数据,建立镍基催化剂苯加氢反应的动力学模型,并分析反应机理。
5. 性能改进研究:根据研究结果和文献资料,探究可以改进镍基催化剂苯加氢性能的方法。
四、论文结构本研究论文主要分为以下部分:1. 绪论:介绍苯加氢反应和三种催化剂的优缺点,阐述本研究目标、意义和研究框架。
2. 实验方法:详细介绍镍基催化剂的制备和表征方法、苯加氢反应实验方法和数据记录方法。
3. 结果与分析:详细介绍实验结果,分析镍基催化剂在苯加氢反应中的活性、选择性、稳定性,并比较其与贵金属催化剂和铁基催化剂的效果,建立反应动力学模型。