降低铁水单耗和提高废钢比的研究与探讨
影响转炉废钢比原因的分析及对策
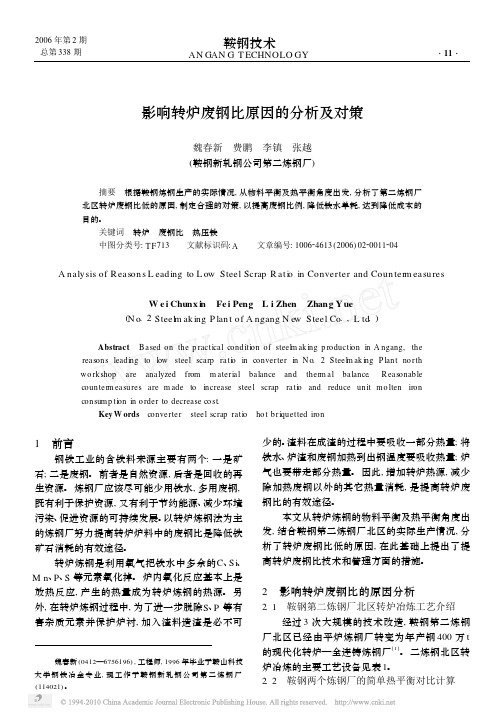
(1) 铁水的硅含量低 铁水硅含量的高低主要受分配铁水的高炉情 况的限制, 分配给二炼钢北区铁水的高炉都是大 高炉, 其铁水硅含量低于小高炉铁水。 (2) 铁水的温度低 供给第二炼钢厂北区铁水温度低的原因如 下: ① 运输时间长 铁水运到第二炼钢厂北区南端需要 1h, 运到 北端需要 2h, 比一炼钢和二炼钢南区的运输时间 都长。 铁水在运输过程中温降为 1℃ m in, 因此到 达第二炼钢厂北区的铁水温度低。 ② 三罐兑铁 二炼钢厂北区三罐兑铁, 兑铁时间长, 导致铁 水温降大。 第一炼钢厂和第二炼钢厂南区都是兑 一罐铁, 兑铁的温降小于二炼钢北区。 ③ 脱硫扒渣的比率大 脱硫扒渣操作引起铁损和温度损失, 每罐铁 水脱硫扒渣后平均温度至少损失 20℃ (实测)。 脱 硫扒渣操作对铁水的温度影响较大, 统计结果如 表3 所示。北区铁水的脱硫扒渣处理率比南区高, 铁损也比南区大。
大 学 钢 铁 冶 金 专 业, 现 工 作 于 鞍 钢 新 轧 钢 公 司 第 二 炼 钢 厂 (114021)。
少的。渣料在成渣的过程中要吸收一部分热量; 将 铁水、炉渣和废钢加热到出钢温度要吸收热量; 炉 气也要带走部分热量。 因此, 增加转炉热源, 减少 除加热废钢以外的其它热量消耗, 是提高转炉废 钢比的有效途径。
关键词 转炉 废钢比 热压铁 中图分类号: T F 713 文献标识码: A 文章编号: 100624613 (2006) 0220011204
A na lysis of R ea son s L ead ing to L ow Steel Scrap R a t io in Converter and Coun term ea su res
炼钢生产中废钢的应用现状及增吃废钢降低铁钢比的方式探索

炼钢生产中废钢的应用现状及增吃废钢降低铁钢比的方式探索作者:严铭伟来源:《科学导报·学术》2019年第21期摘 ;要:废钢铁是一种可以循环利用的再生绿色资源,是转炉炼钢中重要的原材料之一,也是冷却效果显著的冷却剂。
当前废钢铁在炼钢生产中应用已达到20%,废钢单槽重量处于历史较高水平,目前仍然在冶煉过程中增加废钢使用量。
面对当前市场环境,如何通过增吃废钢降低铁钢比成为当前攻关的主要方向及降本增效有力措施。
关键词:废钢应用;增吃废钢;降低铁钢比2018年,全国生铁产量7.71亿吨,粗钢产量9.28亿吨,废钢铁消耗总量突破2亿吨,废钢单耗202kg/t(其中转炉单耗152 kg/t)。
废钢铁利用水平走向了一个新台阶,达到了《废钢铁产业“十三五”规划》提出的废钢比20%的要求,达到了去除大型平炉以来的历史最好水平,也标志着我国废钢铁产业进入了一个新的重要转折期2018年公司产铁1485万吨,产钢1530万吨,仓储中心输出废钢铁99万吨。
根据2018年铁钢比的攻关情况,公司正倡导逐渐增持废钢,包钢正在追赶行业的较高水平。
一、当前包钢废钢铁的应用情况1、废钢铁的回收状况当前废钢铁的回收分为外部采购和内部回收两种。
2018年废钢铁的回收量总量98万吨,其中外部采购达到82万吨,占比达到总回收量的83.7%;内部回收达到16万吨,占比达到总回收量的16.3%。
内部回收废钢主要以非生产检修拆除废钢以及生产线产生的废钢为主,大多数内部回收废钢需要再次加工,达到合格尺寸才可以装槽输出。
外部采购废钢以外部生活废钢及工业回收废钢为主,均为合格废钢,可以直接装槽输出。
内外部回收废钢主要有以下料型及标准:2、废钢铁输出情况仓储中心目前向包钢内部四个钢厂的12座转炉输出废钢保产,其中炼钢厂5座(3座100吨,2座150吨);薄板2座210吨,钢管公司2座120吨转炉,金属制造公司3座260吨转炉。
因此,废钢单槽输出量也不相同,炼钢厂单槽重12-25吨,薄板厂36吨,钢管公司15吨,金属制造公司50吨。
影响钢铁料消耗因素探讨与实践

2017年第2期LYS Science-Technology& Management・8・影响钢铁料消耗因素探讨与实践一炼轧厂黄伟豪摘要本文对影响钢铁料消耗的因素进行了具体分析。
通过改进入炉料结构、优化造渣工艺、减少转炉喷溅率、加强内部含铁资源回收,有效提高了转炉钢水收得率,降低了钢铁料消耗。
1 引言目前钢铁行业竞争日益激烈,钢材利润空间急剧压缩,为应对市场带来的挑战,必须采取措施来降本增效。
而钢铁料消耗占转炉炼钢生产成本的70%以上,且钢铁料指标的好坏直观体现了该厂综合技术水平、管理水平的高低,它关系到炼钢厂以挖潜增效为主的竞争活动的成败,因此降低钢铁料消耗对炼钢企业来说显得尤为迫切。
本文综合分析了涟钢一炼轧厂转炉线的实际生产情况,提出针对性的改进措施,付诸实施后,钢铁料消耗取得了明显进步。
2 炼钢线生产现状涟钢一炼轧厂转炉线现有公称容量100t氧气顶底复吹转炉3座,铁水预处理一座,吹氩站3座,2台6机6流弧形连铸机。
年产钢390万吨。
主要品种有HRB系列、CSP低碳钢、CSP普碳钢、低碳合金钢、高碳高强钢及其它新钢种。
3 钢铁料消耗计算口径与现状3.1 钢铁料消耗计算方法钢铁料消耗(kg/t)=入炉钢铁料(kg)÷合格钢产量(t);钢铁料消耗量(t)=铁水量(t)+生铁量(t)+废钢量(t)+矿石(t);废钢从来源上分为外购废钢和自产废钢,加生铁是由于炼钢能力大于高炉生产能力,铁水量不足,靠采购生铁块来发挥转炉产能。
3.2 钢铁料消耗现状2016年一炼轧厂的钢铁料实物消耗1079.31kg/t,较往年明显好转。
4 影响钢铁料消耗的主要因素涟钢6#高炉处于炉役后期,铁水质量较差,入炉铁水渣量、温度、成分波动大,转炉炉容比小,受入炉原材料质量以及入炉料结构的影响较大。
转炉冶炼过程易喷溅、喷溅渣含铁量大,熔剂消耗高,终渣TFe高,终点温度、成分控制较差导致回炉与中断连铸次数较多,过吹、高温现象较严重;连铸操作稳定性差,铸余钢水流失多,严重影响着钢铁料消耗的降低。
探讨如何做好炼钢厂的节能降耗工作
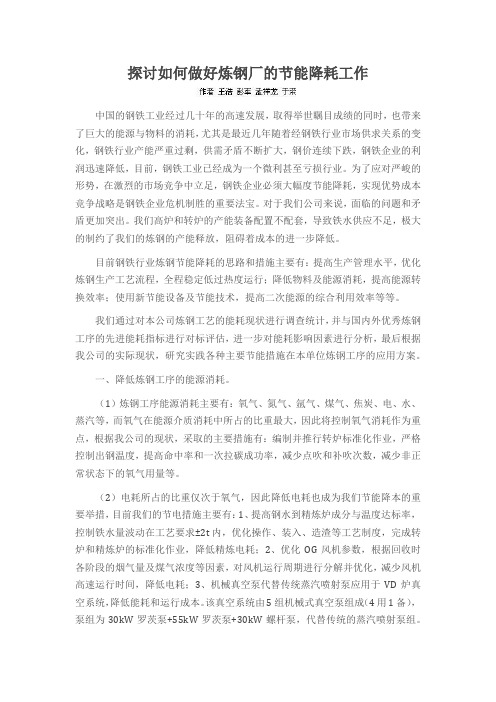
探讨如何做好炼钢厂的节能降耗工作中国的钢铁工业经过几十年的高速发展,取得举世瞩目成绩的同时,也带来了巨大的能源与物料的消耗,尤其是最近几年随着经钢铁行业市场供求关系的变化,钢铁行业产能严重过剩,供需矛盾不断扩大,钢价连续下跌,钢铁企业的利润迅速降低,目前,钢铁工业已经成为一个微利甚至亏损行业。
为了应对严峻的形势,在激烈的市场竞争中立足,钢铁企业必须大幅度节能降耗,实现优势成本竞争战略是钢铁企业危机制胜的重要法宝。
对于我们公司来说,面临的问题和矛盾更加突出。
我们高炉和转炉的产能装备配置不配套,导致铁水供应不足,极大的制约了我们的炼钢的产能释放,阻碍着成本的进一步降低。
目前钢铁行业炼钢节能降耗的思路和措施主要有:提高生产管理水平,优化炼钢生产工艺流程,全程稳定低过热度运行;降低物料及能源消耗,提高能源转换效率;使用新节能设备及节能技术,提高二次能源的综合利用效率等等。
我们通过对本公司炼钢工艺的能耗现状进行调查统计,并与国内外优秀炼钢工序的先进能耗指标进行对标评估,进一步对能耗影响因素进行分析,最后根据我公司的实际现状,研究实践各种主要节能措施在本单位炼钢工序的应用方案。
一、降低炼钢工序的能源消耗。
(1)炼钢工序能源消耗主要有:氧气、氮气、氩气、煤气、焦炭、电、水、蒸汽等,而氧气在能源介质消耗中所占的比重最大,因此将控制氧气消耗作为重点,根据我公司的现状,采取的主要措施有:编制并推行转炉标准化作业,严格控制出钢温度,提高命中率和一次拉碳成功率,减少点吹和补吹次数,减少非正常状态下的氧气用量等。
(2)电耗所占的比重仅次于氧气,因此降低电耗也成为我们节能降本的重要举措,目前我们的节电措施主要有:1、提高钢水到精炼炉成分与温度达标率,控制铁水量波动在工艺要求±2t内,优化操作、装入、造渣等工艺制度,完成转炉和精炼炉的标准化作业,降低精炼电耗;2、优化OG风机参数,根据回收时各阶段的烟气量及煤气浓度等因素,对风机运行周期进行分解并优化,减少风机高速运行时间,降低电耗;3、机械真空泵代替传统蒸汽喷射泵应用于VD炉真空系统,降低能耗和运行成本。
降低转炉铁水单耗实践

降低转炉铁水单耗实践作者:贺劲松来源:《智富时代》2019年第09期【摘要】本文通过转炉热平衡计算,指导现场科学合理的制定各项降低铁钢比的一些措施,也涉及到在降低铁钢比过程中出现的一些实际问题及解决方案。
通过这些措施湘钢某厂铁水单耗从870Kg/吨降至目前的810Kg/t钢。
【关键词】铁水单耗;热平衡;废钢比1、引言在全国正在淘汰钢铁企业落后产能的大环境下,国内废钢资源比较充裕,提高废钢比降低铁水单耗有利于钢铁企业大幅降低综合能耗,提高废旧物资的回收利用效率,具有可观的经济、环保和社会效益。
由于公司高炉产能长期小于炼钢的产能,废钢比一直比较低,产量严重受限,处于微利状态。
2018年提出铁水单耗必须降低至820Kg/t钢以内。
为此从两方面开始进行攻关:一方面通过热平衡计算,制定合理的装入制度、温度制度、炉内加入发热剂等措施;另一方面通过通过改进废钢尺寸,对废钢槽进行扩容,铁水罐加入干燥的清洁废钢等方措施,使得铁水单耗从870Kg/吨降至目前的810Kg/t钢,取得了显著的经济效益和社会效益。
2、热平衡计算2.1初始条件为给降低铁水单耗提供理论支持,按照目前按照已有的铁水初始条件进行设定(冶炼过程不加入萤石、石灰石及矿石),选100kg铁水进行热平衡计算:2.2热收入项(1)铁水物理热铁水熔点:=1536-([C]%×100+[Si]%×8+[Mn]%×5+[P]%×30+[S]%×25)-7式中100、8、5、30、25分别为C、Si、Mn、P、S元素增加1%含量降低铁水熔点值;7为气体O2、H2、N2共降低铁水熔点值;1536℃为纯铁熔点.铁水熔点=1536-(5×100+0.6×8+0.35×5+0.12×30+0.06×25)-7=1017.0℃铁水物理热=100×[0.178×(1017-30)+52+0.20×1330-1017]=27360千卡(2)铁水中各元素氧化放热及成渣热C→CO 4.428×2616.9=11587.63千卡C→CO2 0.492×8250.7=4059.34千卡Si→SiO2 0.6×6767.2=4060.32千卡Mn→MnO 0.23×1677.9=385.92千卡FE→FeO 0.576×1150.5=662.58千卡FE→Fe2O3 0.207×1758.1=364.50千卡P→P2O5 0.105×4522.6=474.87千卡P2O5→4CaO·P2O5 0.240×1162.1=279.47千卡SiO2→2CaO·SiO2 1.299×495=643.13千卡共计:=22517.76106千卡(3)烟尘氧化放热=1.6×(0.77×56/72×1150.5+0.2×112/160×1758.1)=1496.249067千卡则热收入总量为:27360+22517.7611+1496.2491=51374.01013千卡注:对于炉衬中的C、原料中的P,其氧化放热甚少,故忽略之。
浅析钢铁企业的能耗现状及节能对策
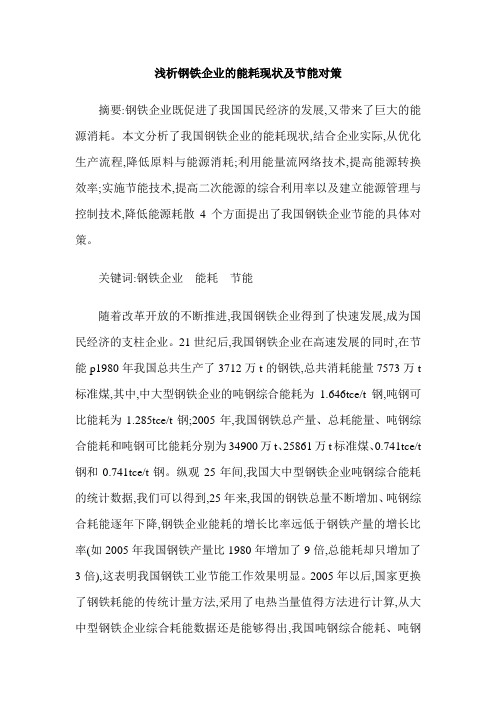
浅析钢铁企业的能耗现状及节能对策摘要:钢铁企业既促进了我国国民经济的发展,又带来了巨大的能源消耗。
本文分析了我国钢铁企业的能耗现状,结合企业实际,从优化生产流程,降低原料与能源消耗;利用能量流网络技术,提高能源转换效率;实施节能技术,提高二次能源的综合利用率以及建立能源管理与控制技术,降低能源耗散4个方面提出了我国钢铁企业节能的具体对策。
关键词:钢铁企业能耗节能随着改革开放的不断推进,我国钢铁企业得到了快速发展,成为国民经济的支柱企业。
21世纪后,我国钢铁企业在高速发展的同时,在节能p1980年我国总共生产了3712万t的钢铁,总共消耗能量7573万t 标准煤,其中,中大型钢铁企业的吨钢综合能耗为1.646tce/t钢,吨钢可比能耗为1.285tce/t钢;2005年,我国钢铁总产量、总耗能量、吨钢综合能耗和吨钢可比能耗分别为34900万t、25861万t标准煤、0.741tce/t 钢和0.741tce/t钢。
纵观25年间,我国大中型钢铁企业吨钢综合能耗的统计数据,我们可以得到,25年来,我国的钢铁总量不断增加、吨钢综合耗能逐年下降,钢铁企业能耗的增长比率远低于钢铁产量的增长比率(如2005年我国钢铁产量比1980年增加了9倍,总能耗却只增加了3倍),这表明我国钢铁工业节能工作效果明显。
2005年以后,国家更换了钢铁耗能的传统计量方法,采用了电热当量值得方法进行计算,从大中型钢铁企业综合耗能数据还是能够得出,我国吨钢综合能耗、吨钢可比能耗也是逐年下降(2008年受金融危机影响例外),2005年我国吨钢综合能耗、吨钢可比能耗分别为695kgce/t钢、714kgce/t钢,2010年这两项数据为604kgce/t钢和581kgce/t钢。
总之,我国将进30年钢铁发展历程表明我国钢铁企业节能工作取得了伟大的成就[2]。
1.2 我国钢铁企业能耗存在的问题虽然我国钢铁企业能耗逐年下降,但是从2005年起,吨钢能耗的降幅不断减少,继续节能的难度在不断增加,存在着一些突出问题:第一,我国钢铁企业能耗总体水平与发达国家先进水平相比,还存有一定差距。
烧结工序降低水耗的改造工作探究

烧结工序降低水耗的改造工作探究随着钢铁生产的发展和市场形势的不断变化,降低生产过程中的工序能耗,显得越来越重要,其中尤其以降低水耗为关键。
因此,降低烧结工序水耗越来越受到重视,但鉴于国内外大多数钢铁企业均已年代久远,采用老工艺生产,而许多新建成的烧结工序给水排水工程工艺缺陷,管网复杂,循环率低,同时用水量大,且生产加水和设备冷却水循环系统运行都有很大缺陷的现状,如何解决好降低水耗和设备冷却的平衡问题是同类企业均需要解决的问题。
梅钢炼铁厂烧结工序同样存在着水耗高、设备冷却水量不平衡的问题。
1、背景介绍2013年6月以前,该炼铁厂烧结分厂1、2号烧结系统生产新水的用量平均为11万t/月左右,生产水单耗平均450kg/(t-s)左右;3号烧结系统生产新水的用量平均为10万t/月左右,生产新水单耗平均480kg/(t-s)左右。
新老系统的耗水量同样居高不下,在很大程度上提高了生产成本。
因此为解决这个问题而实施的改造工作是紧迫而有意义的工作。
2、技术现状及问题分析2.1 1、2 号烧结系统1、2号烧结系统原来的新水运行方式是新水供给管路组成关键设备,1~4号抽风机冷却和低标高区域生产加水管网系统,冷却回水回至联合泵站蓄水池,但同时未设冷却塔;然后通过泵站加压输送,形成主厂房区域设备冷却水和高标高区域生产加水管网,供给生产物料加水以及部分环保除尘用水。
设备冷却管网(即新水管网)和生产加水管网相互独立。
然而,经过理论计算以及生产现场实际数据,设备冷却水量(Q1)一直维持在11.0万t/月(平均值155 m3/h)左右;生产物料加水所需量(Q2)正常生产一般维持在6.5万t/月(平均值90 m3/h)左右。
由Q1-Q2=155-90=60m3/h可以看出,泵站蓄水池进水量远大于泵出水量,因此大量水溢流造成浪费。
由以上分析可知,关键的问题在于给水排水的运行方式和管网布置的不合理。
2.2 3 号烧结系统3号烧结系统原来的新水运行方式是新水供给管路形成设备冷却管网系统,冷却回水回至联合泵站蓄水池,但同时未设冷却塔;然后通过泵站加压输送,形成生产加水管网,供给生产物料加水以及部分环保除尘用水。
浅谈提高转炉废钢比的措施

浅谈提高转炉废钢比的措施作者:汪培来源:《西部论丛》2019年第01期摘要:中国逐渐进入工业化后期,势必会降低对钢铁产品的需求,随着时间的推移,废钢可用量将接近甚至大于粗钢产量。
另外,废钢是可限循环利用的铁资源,提高转炉废钢比,有助于降低铁水消耗,将大幅降低环境污染和综合能耗,具有较高的经济、环保和社会效益。
所以,提高废钢比是历史发展的必然,同时也是钢铁企业发展的最佳选择。
本文主要对目前国内外成功应用的提高转炉废钢比的技术进行概述和比较,希望可以为相关从业者提供一些有价值的参考和借鉴。
关键词:转炉废钢比废钢加热近十年来,全球废钢比维持在35-40%的水平,平均在37%左右。
废钢比最高的为土耳其,达到85-90%的水平,发达国家中,美国的废钢比最高,在75%上下,波动较大。
欧盟也较高,大体在55~60%的水平,此外韩国平均也能达到50%左右。
中国由于“地条钢”的存在扰乱了废钢市场,造成转炉废钢比偏低,不仅浪费转炉热量,而且使吨钢综合能耗大幅上升,环境污染严重。
2016年国内炼钢废钢比为11%,2017年我国政府严厉打击地条钢,淘汰1~1.5亿吨落后产能,短期内使废钢市场价格大幅跌落,也使各钢厂开始大幅增加转炉废钢比,2017年国内废钢比约为17%。
虽然2017年国内转炉炼钢废钢比大幅增加,但仍有很大的提升空间,如果不进行热补偿,仅通过向转炉多加废钢的方式增加废钢比,范围极其有限,以湘钢五米板厂为例,极限情况下转炉综合废钢比也才25%。
目前国内外利用热补偿成功应用的增加转炉废钢比的方法主要有:炉气二次燃烧、熔池增碳、废钢预热。
一、炉气二次燃烧二次燃烧的思路是利用炉气中的CO二次燃烧放热加热金属熔池,随着当前新型二次燃烧氧枪的发展,二次燃烧效率有了明显提高。
新型二次燃烧氧枪通过对枪体及出口处新型设计,提高了喷出氧气与脱碳反应产生的CO之间的反应效率,将产生更多的二次燃烧热。
提高CO 的二次燃烧有助于增加炉内热量,其效果与炉子大小、二次燃烧氧枪类型有关。
- 1、下载文档前请自行甄别文档内容的完整性,平台不提供额外的编辑、内容补充、找答案等附加服务。
- 2、"仅部分预览"的文档,不可在线预览部分如存在完整性等问题,可反馈申请退款(可完整预览的文档不适用该条件!)。
- 3、如文档侵犯您的权益,请联系客服反馈,我们会尽快为您处理(人工客服工作时间:9:00-18:30)。
( t l meigPa tfSel no oLd o B o uSe ( ru ) o . B oo 10 0 N i o g o , hn ) Se — ln ln o t inC . t. a t t l Gop C r , a t 0 4 1 , e M n g lC i e t eU f o e p u a
只 能 在 提 高 铁 水 温 度 的前 提 下 进 行 , 则 对 生 产 、 量 及 操作 会带 来 不 利 的影 响 。 否 质
关 键 词 : 炉 ; 水 单 耗 ; 钢 比 转 铁 废
中 图分 类 号 :F4 . T 3 18 文 献 标 识 码 : B 文 章 编 号 :09—5 3 ( 0 1 0 0 7 10 4 8 2 1 )6— 04—0 4
Ke y wor s: o e tr untc ns mpto fh tme a ; c a ais d c nv res; i o u inso o t l s rp r t o
废 钢是转 炉生 产冶炼 过程 中金属料 的重要 组成
状况 为基础 , 理论 上 计 算废 钢 的加 入量 。计 算 所 从 需基 本数 据有 : 水成 分见 表 1 溶 于 铁 中元 素对 铁 铁 ; 熔 点 的降 低值 见 表 2 各 种 人 炉料 及 产 物 的温 度 见 ; 表 3 钢水成分 表 见表 4 假 设 条 件 为炉 渣 中 铁珠 量 ; ;
第 6期
降低 铁 水 单 耗 和 提 高 废 钢 比 的研 究 与探 讨
7 5
表 2 溶 于 铁 中 元 素 对 铁 熔 点 的 降 低值
%
成 渣热 , 烟尘氧化 热 , 炉衬 中碳 的氧 化热 。根据纯 铁
第3 7卷第 6期
21 年 l 01 2月
包
钢
科
技
Vo . 7, . 1 3 No 6 De e e , 01 c mb r 2 1
S e c n c noo fBa tu Ste cin e a d Te h lgyo oo e l
降低 铁 水单 耗 和 提高 废钢 比的研 究 与 探讨
为渣 量 的 8 ; 溅 的损 失 为铁 水量 的 1 ; 池 中 % 喷 % 熔
部分 , 转炉入 炉废 钢 比 的提 高可 以降低 吨钢 铁水 消 耗 。降低铁 钢 比 , 是铁 水 不 足情 况 下 提高 钢 产量 的
行之有 效 的方法之 一 , 实
1 基 本 原理 计 算
1 1 理论 计算 .
表 I 铁水成分( 量分数) % 质
以实际生产 中所需 的 出钢温度 , 实际铁 水
收 稿 日期 :0 1— 8— 3 2 1 0 2
作 者 简 介 : 宏 (9 0一) 男 , 蒋 16 , 江苏 省 南 通 市 人 , 炼 工 程 师 , 从 事 炼 钢 工 艺 管 理工 作 。 冶 现
t e te r tc lc l ua in n cua r d t n d t Th mprv me to ca ai sc u d b mp e ne n y i h h h o eia ac lto s a d a t lp o uci aa. o e i o e n fs r p r to o l e i l me td o l f te tm p r tr s o o tlae i c e s d, t e wie i wilaf c h r d c in qu lt s a pea in n a o a l . e e au e fh tmea r n r a e o h r s t l fe tt e p o u to s, aii nd o r to s u f v r b y e
S u nd Dic s i n n Re ucng Uni ns m p i n t dy a s u so s o d i t Co u to s
o o e a nd I pr v n c a to fH t M t la m o i g S r p Ra i s
A s atR aoal cag e h o rp s ba e i c a t prtrs n [i f o m t s e s bt c: esnb hrew i t f cas t ndwt at le e ue ad r e g s io i h u m a s]o t ea a la h l w l
蒋 宏 , 建 平 , 明泉 唐 赵
( 内蒙古 包钢钢联股 份有 限公 司炼钢厂 , 内蒙古 包头 041) 10 0
摘
要 : 章 通 过 实 际 的 铁 水 温度 和 埘 [ i的理 论 计 算 , 实 际 生 产 数 据 得 出 合 理 的 废 钢 装 入 量 , 提 高 废 钢 比 , 文 s] 与 若
铁水 W[ i 、 s] 废钢 种类配 比、 型等方面 的影 响。根 炉
据不 同 的炉型 、 铁水状况 以及 生产钢 种的情 况 , 过 通 热平 衡理论 计算 以及 实 际 冶 炼情 况 提高 废 钢 比 , 确 保铁 水单 耗降到 9 0k/ 以下 。 5 g t
碳 氧化产 物 W [ O] 0 , [ O ] 0 ; 尘 量为 C 9 % W C 1% 烟 铁 水 量 的 1 ,W [ e 为 7 % ,W [ eO ]为 % F O] 5 F , 2 % ; 衬 侵 蚀 量 为 铁 水 量 的 0 5 ; 气 成 分 为 0 炉 .% 氧