硫酸烧渣的综合利用研究
硫酸渣选铁试验研究
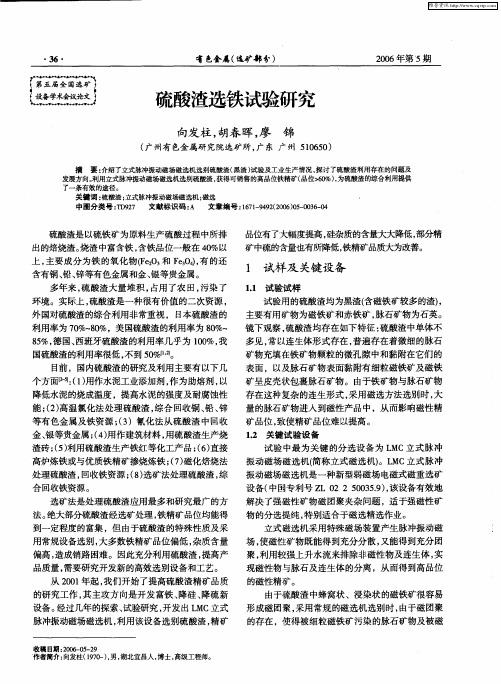
脉冲振荡磁场的存在 , 面 , 一方 磁性物在分选腔中只
能形成细长的横向磁聚体 ; 另一方面 , 细长的横向磁 聚体在振荡磁场 中“ 张一弛”交替团聚、 散 , 一 , 松 为
其 中夹杂 的脉石及连生体颗粒分 离出来创 造 了条 件, 采用较强的上升水流清除夹杂的脉石及连生体 ,
矿品位 , 致使精矿品位难 以提高。
1 关键 试 验设 备 . 2
金、 银等贵金属 ;4 用作建筑材料 , () 用硫酸渣生产烧 渣砖 ;5利用硫酸渣生产铁红等化工产品 ;6直接 () () 高炉炼铁或与优质铁精矿掺烧炼铁 ;7 磁化焙烧法 ()
处理硫酸渣 , 回收铁资源 ;8选矿法处理硫酸渣 , () 综 合 回收铁资源 。 选矿法是处理硫酸渣应用最多和研究最广的方 法。 绝大部分硫酸渣经选矿处理 , 铁精矿品位均能得 到一定程度的富集 , 由于硫酸渣 的特殊性质及采 但 用常规设备选别 , 大多数铁精矿品位偏低 , 杂质含量 偏高 , 造成销路困难。因此充分利用硫酸渣 , 提高产
的磁性精: 。 旷 由于琉酸渣 中蜂窝状、浸染状的磁铁矿很容易 形成磁团聚 , 采用常规的磁选机选别时 , 由于磁团聚 的存在 ,使得被细粒磁铁矿污染 的脉石矿物及被磁
品质量 , 需要研究开发新的高效选别设备和工艺。 从 20 年起 , 01 我们开始了提高硫酸渣精矿品质 的研究工作 , 其主攻方 向是开发富铁 、 降硅 、 降硫新 设备 。 经过几年的探索、 试验研究 , 开发出 L C立式 M 脉冲振动磁场磁选机 , 利用该设备选别硫酸渣 , 精矿
目前 ,国内硫酸渣 的研究及利用主要有以下几
主要有用矿物为磁铁矿和赤铁矿 , 脉石矿物为石英 。 镜下观察 , 硫酸渣均存在如下特征 : 硫酸渣中单体不 多见 , 常以连生体形式存在 , 普遍存在着微细的脉石 矿物充填 在铁矿物颗粒的微孔 隙中和黏附在它们的 表面 ,以及脉石矿物表面黏附有细粒磁铁矿及磁铁 矿呈皮壳状包裹脉石矿物。由于铁矿物与脉石矿物
利用硫酸烧渣进行煤系硫铁矿的综合利用

利用硫酸烧渣进行煤系硫铁矿的综合利用
葛圣松;邵谦
【期刊名称】《煤炭加工与综合利用》
【年(卷),期】1997(000)006
【摘要】将硫酸生产中形成的烧渣用于处理煤系硫铁矿,回收反应物中的元素硫,并利用生成的铁离子生产氧化铁红。
【总页数】3页(P32-34)
【作者】葛圣松;邵谦
【作者单位】山东矿业学院济南分院;山东矿业学院济南分院
【正文语种】中文
【中图分类】TD98
【相关文献】
1.重庆市煤系硫铁矿综合利用发展现状与建议 [J], 胡波;龚业超;周霞;陈敏;谌麒宇
2.川南煤系硫铁矿综合利用新工艺研究 [J], 徐明;张渊;杨永涛;张俊辉;徐建林
3.川南煤系硫铁矿尾矿高岭土综合利用研究 [J], 叶巧明;刘建;张其春
4.煤系硫铁矿综合利用新工艺研究 [J], 廖舟;杨小中;许彬;吉庆锋;李先柏;梁经东;鲍超
5.煤系硫铁矿综合利用发展现状与建议 [J], 罗道成;刘俊峰;易平贵;李佳秋
因版权原因,仅展示原文概要,查看原文内容请购买。
硫酸烧渣提金新工艺和新设备

硫酸烧渣提金新工艺和新设备一.硫酸烧渣提金技术现状与研究方向目前我国黄金资源的利用明显出现勘探跟不上生产要求的局面,制约着我国黄金产量的提高,与此同时,从含金废料中和难选矿石中回收金的技术和扶持政策却不够理想,这部分金资源尚未得到充分的利用.含金硫酸烧渣回收金技术急待开发.我国每年产生含金硫酸烧渣几十万吨,目前仅大于3克/吨的烧渣得以利用.每年仅有7.5万吨的处理能力,其余烧渣或废崐弃或以十几元/吨的价格出售给水泥厂做原料,•所含黄金白白流失,十分可惜.从国内外的技术文献看,从烧渣中回收金的技术也只限于氰化工艺,重选、浮选、磁选、硫脲工艺等均处于研究阶段.现时的氰化工艺仅适合处理金品位高于2.5克/•吨的硫酸烧渣,品位再低则利润太低,投资难以在短期内收回,因此尽管具有较好的社会效益,但经济效益不明显而无建提金厂的积极性;堆浸法虽然能使生产成本降低,•但不能连续生产而且冬季无法生产,因此这种工艺也难以推广;重选、•磁选和浮选均能崐回收烧渣中的一部分金,但回收率不如氰化法高而且从产生的精矿中再回收金时回收率不理想,也难以推广.•硫脲法药剂成本高且浸出条件不易控制,溶液中金的回收尚满意的方法,•还处在探索阶段,距工业应用尚远.我们认为,影响从烧渣中提金的主要因素有两个,•一是投资过大、二是生产成本过高.如果能解决这两个问题,•低品位硫酸烧渣提金技术将被顺利推广.通过对我国推广使用的氰化法工艺进行研究,发现该工艺存在如下问题:1.长春黄金研究院的多年研究证明,硫酸烧渣不须再磨氰化浸出率就能保证,采用磨矿工段的目的仅仅是为了保证氰化反应时矿浆被搅拌均匀,不沉槽.磨矿工段投资达40余万元,生产成本高达15元/吨,如果能通过其它办法砍掉该工段,氰化法的崐投资和生产成本会大幅度下降.2.由于靠排放磨矿后浓密机溢流进行洗矿--•除去烧渣中溶出的铁铜等杂质,在磨矿过程中就不能加氰化物,•因此贫液也不能全部循环使用,贫液处理后排放不但使生产成本提高,•还产生环境污染问题,在一些环境质量要求高的地区,•环保部门就不会批准建氰化厂.3.不少硫酸厂建在城市内•,无足够的场地建较大的尾矿库.采用现在的氰化工艺时,无论用锌粉置换还是用炭浆法,•都必须过滤氰尾分离出废渣,用机动车把渣运到它处.•过滤工段增加了投资,又因磨矿使渣粒度变细增加了过滤难度、增加了生产成本.4.采用锌粉置换将使贫液中锌浓度不断增加,恶化浸出条件,造成金回收率降低;由于烧渣硬度大,用炭浆法炭磨损大,金流失多,生产成本增高.5.氰化法的最大不足不在于反应时间太长,一般至少要16小时,这就要求建很大体积的浸出槽,投资增大、电耗增加,厂房面积增加.综上所述,从低品位硫酸烧渣中提金必须开发新的浸出技术或新的工艺,降低投资和成本.•其具体研究内容包括以下几个途径:1.使用新的浸出设备,不磨矿即可保证浸出反应顺利进行.•而且浸出电耗不增加或增加较少.2.使用浸出速度快的浸出方法,浸出时间仅几小时或更短.•可增加搅拌强度来保证浸出效果,由于反应时间短,•单位电耗也不会增加很多.3.采用贫液全循环工艺,不外排废水,节约废水处理费用,节约浸出药剂.4.用固定床吸附法从贵液中回收金,不设洗涤工段或炭浆工段,浸后直接过滤,提高贵液金浓度以使吸附剂上金品位提高,•减少设备投资和生产成本.通过大量的研究和试验,选择了水氯法工艺.•小试结果表明,浸出率比氰化法高,•其原因是氰化过程中烧渣颗粒上金表面产生阻碍金浸出和扩散的膜.均由烧渣的性质决定--氰尾渣制酸时的焙烧温度致关重要.二.新工艺和新设备的技术经济指标1.技术工艺指标金回收率: 55%浸出时间: 3min •石灰耗量: 3kg/t电耗: 15kwh/t水耗: 0.15m3•/t 液氯耗量: 3kg/t投资: 80万元生产成本: 38.6元•/t 生产人员: 35人2.黄金产量和产值、利润按每年生产300天,处理能力为•100m3•/d,烧渣金品位1.5g/t,回收率55%计,产金量如下:每吨烧产金量: 1×1.5×55%=0.825g日产黄金: 100×0.825=82.5g年产金量: 300×82.5=24750g每吨烧渣产值: 0.825×96=79.2元日产值: 100×79.2=0.792万元年产值: 300×0.792=237.6万元年利润: 300×100×(79.2-38.6)=120万元按100万元投资计算,返还期为10个月.用本工艺提金的最低经济品位为0.75g/t.3.新工艺与常规氰化工艺比较新工艺:4.新式固液分离设备的特点常规固液分离设备有板框压滤机、带式过滤机、浓密机,板框压滤机的配套高压泵易损不易防腐,而且在压滤前要设搅拌槽平衡流量,设备投资达150万元,电耗大;带式真空过滤机过滤带易损,不易防止氯的腐蚀,投资达200万元;浓密机不易处理大颗粒物料.而且防腐也不易,占地大,投资达150万元.新式固液分离设备类似池浸用的浸出池,多池串联,上部设溢液口,下部设分布板,矿浆进入后,大颗粒物料很快沉降到池下部,水颗粒物料将通过溢液口向后面的池中流去,经过较长时间的沉降,较清的贵液从固液分离设备中流出,进入吸附工段.待前面的池中充满浸渣后,打开分布板下面的排液阀并从池上部加水洗涤,从分布板下液出的贵液也进入吸附工段.新设备用混凝土制成,涂以防腐材料即可.投资仅30万元.三.新工艺和设备的优点浸出方法的优点:1.本浸出方法使用工业上广泛使用的氯气(开始使用少量食盐)做浸出药剂及少量助剂,避免了氰化物的污染,使用的助剂降低氯气的消耗,使其药剂成本低于氰化法.2.本方法浸出时间仅3分钟,因此浸出设备有效容积仅为氰化法的0.2%~0.4%,以处理能力100t/d的工厂为例,浸出设备有效容积仅0.3立米.不但投资可减少20%,浸出的电耗也可降低4~5kwh/t.新式浸出设备的优点:采用新式反应器,适应大颗粒物料的浸出.常规浸出设备只适用于处理200目以下的矿浆,否则就会出现"沉槽"、压搅拌浆等故障.本设备容积很小,采用其它方法解决反应器问题,避免搅拌不均.新式固液分离设备具有投资少、生产成本低、易防腐等特点.现有的过滤设备不能解防腐问题,而且价格很高,大约需要投资100万元,新式固液分离设备投资仅30万元.新工艺的优点:1.省去了磨矿及相应的分级、浓密设备,减少投资40%左右;节省占地400平米;减少材料消耗10元/t;减少电费5元/t;减少操作工3--6人.2.不磨的烧渣本身粒度较大,一般在-80目占70%以上,40-80目占25%左右,其余5%在20-40目之间,沉降速度快.特别适合用新式固液分离设备进行液固分离.这种设备易于操作.与氰化工艺相比,省去了浓密机和压滤机,易于控制浸出液物量平衡.3.选用活性炭吸附法回收浸出液中的金,考虑到在吸附过程中可能产生沉淀物,采用我单位已获专利的吸附槽.吸附装置投资仅2万元.4.由于在酸性含氯溶液中吸附金氯络合物,并使金离子最终转变为单质金.因此载金炭上金品位至少可富集到10kg/t,采用焚烧—王水溶解—还原的联合工艺即可生产出纯金.冶炼工艺设备简单,仅使用常规药剂,与氰化法比,冶炼工段节约设备投资30万元,冶炼成本也低于常规工艺.5.贫液中杂质主要是铁、锌和铜,可用石灰沉淀,分离掉杂质的溶液可循环使用;由于不断加氯,浸出液的酸度将不断增加,加石灰除杂的过程还会起到调节酸度的作用.6.与常规氰化工艺相比,采用本工艺建设100t/d处理能力的提金厂,可节约设备投资80万元,降低生产成本30元/t.使那些用氰化法处理没有利润的低品位烧渣提金成为可能,换句话说,使烧渣的提金经济品位大幅度降低.以处理能力100t/d的工厂为例,投资60~80万元,供电不超过50kw,处理成本约40元/t,即使烧渣品位低至1.5g/t,浸出率为55%,年利润也可达到100万元.我国有这类烧渣的工厂至少10座,金品位都在2g/t以下,如果推广本工艺,每年至少回收金250kg.利润1000万元以上.硫酸烧渣提金工艺设计一.工艺数据1.处理能力: 100t/d2.浸出液浓度: 氯气1.5kg/M3 PH=1.5-2.5 Cl-4kg/M33.液固比: 2~5:14.反应时间: 3 分钟5.反应类型: 全返混6.液固分离方法:新式固液分离设备7.贵液中金回收方法:活性炭固定床吸附法8.贫液循环措施:石灰中和沉淀杂质后再循环9.金浸出率:55%10.废气处理方法: 烧碱液吸附再利用二.原料1.烧渣金品位:1.67克/t2.液氯3.石灰4.活性炭:木质炭或果核炭5.自来水6.烧碱三.物料流量1.硫酸烧渣: 4.17t/h2.浸出液流量: 8.34~20M3/h3.活性炭吸附剂用量: 1t4.废气处理排气量: >500M3/h收液流量: 2-4M3/h 四.工艺流程。
钛白粉废硫酸回收利用技术研究进展

调查研究160产 城钛白粉废硫酸回收利用技术研究进展田甜 刘磊 刘金龙 李晶晶 周菲菲摘要:大多数钛白粉生产企业将废硫酸经过蒸发浓缩、除去析出物和杂质等处理后返回酸解工序使用,目前配套废硫酸除杂回用装置的钛白粉生产企业废酸回用率达到40%左右。
个别生产装置如将处理后废硫酸用于磷化工生产,靠近东部市场的少数企业也可将处理后废硫酸用于生产水处理剂聚合硫酸铁,则可全部回收利用废酸;其余企业只能将废硫酸进行中和处理,以钛石膏的形式外销或堆存。
关键词:钛白粉;废硫酸;回收利用;技术进展;聚合硫酸铁;浓缩化工或冶金等领域生产会消耗大量硫酸,产出以硫酸物质为主,掺杂各类混合物、有机物的废硫酸,对生产成本及周围生态环境造成严重影响。
针对废硫酸处理问题,我国已开发研制出多种废硫酸回收利用技术,切实提升了废硫酸利用率,为实现生产经济效益、生态效益最大化发展目标奠定了坚实技术基础。
1 废硫酸特征1.1 来源分散废硫酸除在钛白粉、染料、石油、化纤等生产环节中产出外,其他行业也会或多或少生产出的废硫酸,致使废硫酸来源分散,产出数量存在极大差异性。
1.2 产出量大经不完全统计,每年我国废硫酸产出量达1亿吨以上,除产出量较大生产领域外,其他单体废硫酸产出单位的废硫酸量较少,在废硫酸处理回收方面的投资力度不同。
1.3 处理难度高一方面,废硫酸浓度含量不同,含有害物质及重金属的废硫酸数量较多,大大提升了废硫酸回收处理难度;另一方面,废硫酸含大量有机物,处理工序繁杂,在未经处理或处理不完善就排出的情况下,对周围生态环境造成极为严重的污染。
2 废硫酸的回收再利用2.1 废硫酸中的成分分析硫酸含量Wt%:78%~82%水含量Wt%:16%~20%其他杂质(硫、磷、砷、铅、汞等)Wt%:微量由于废硫酸是乙炔净化所产生,废硫酸中主要成分为硫酸,还有少量的水分,废硫酸洗涤的乙炔气为干法乙炔生产工艺,结合本地实际情况,乙炔气中含有少量的有机物,在酸洗过程中有机物等固态杂质转移至浓硫酸中,使得在废硫酸中有微量的其他元素。
我国硫铁矿加工业现状及硫铁矿烧渣利用综述
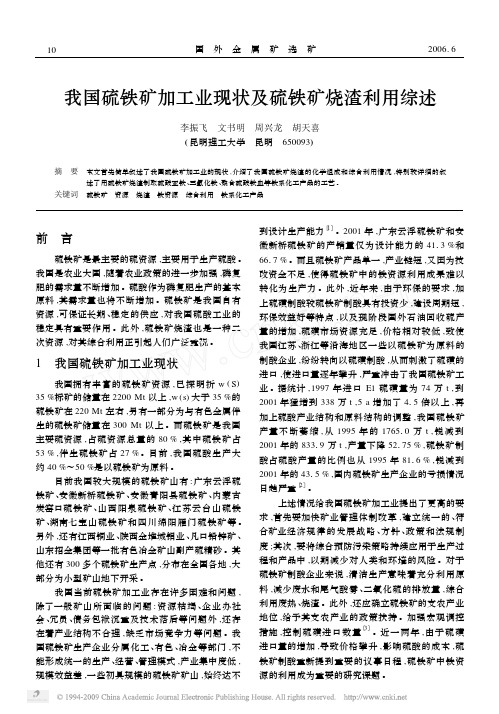
我国硫铁矿加工业现状及硫铁矿烧渣利用综述李振飞 文书明 周兴龙 胡天喜(昆明理工大学 昆明 650093)摘 要 本文首先简单叙述了我国硫铁矿加工业的现状,介绍了我国硫铁矿烧渣的化学组成和综合利用情况,特别较详细的叙述了用硫铁矿烧渣制取硫酸亚铁、三氯化铁、聚合硫酸铁血等铁系化工产品的工艺。
关键词 硫铁矿 资源 烧渣 铁资源 综合利用 铁系化工产品前 言硫铁矿是最主要的硫资源,主要用于生产硫酸。
我国是农业大国,随着农业政策的进一步加强,磷复肥的需求量不断增加。
硫酸作为磷复肥生产的基本原料,其需求量也将不断增加。
硫铁矿是我国自有资源,可保证长期、稳定的供应,对我国硫酸工业的稳定具有重要作用。
此外,硫铁矿烧渣也是一种二次资源,对其综合利用正引起人们广泛重视。
1 我国硫铁矿加工业现状我国拥有丰富的硫铁矿资源,已探明折w(S) 35%标矿的储量在2200Mt以上,w(s)大于35%的硫铁矿在220Mt左右,另有一部分为与有色金属伴生的硫铁矿储量在300Mt以上。
而硫铁矿是我国主要硫资源,占硫资源总量的80%,其中硫铁矿占53%,伴生硫铁矿占27%。
目前,我国硫酸生产大约40%~50%是以硫铁矿为原料。
目前我国较大规模的硫铁矿山有:广东云浮硫铁矿、安徽新桥硫铁矿、安徽青阳县硫铁矿、内蒙古炭窑口硫铁矿、山西阳泉硫铁矿、江苏云台山硫铁矿、湖南七宝山硫铁矿和四川绵阳雁门硫铁矿等。
另外,还有江西铜业、陕西金堆城钼业、凡口铅锌矿、山东招金集团等一批有色冶金矿山副产硫精砂。
其他还有300多个硫铁矿生产点,分布在全国各地,大部分为小型矿山地下开采。
我国当前硫铁矿加工业存在许多困难和问题,除了一般矿山所面临的问题:资源枯竭、企业办社会、冗员、债务包袱沉重及技术落后等问题外,还存在着产业结构不合理,缺乏市场竞争力等问题。
我国硫铁矿生产企业分属化工、有色、冶金等部门,不能形成统一的生产、经营、管理模式,产业集中度低,规模效益差,一些初具规模的硫铁矿矿山,始终达不到设计生产能力〔1〕。
硫铁矿烧渣综合利用试验研究报告
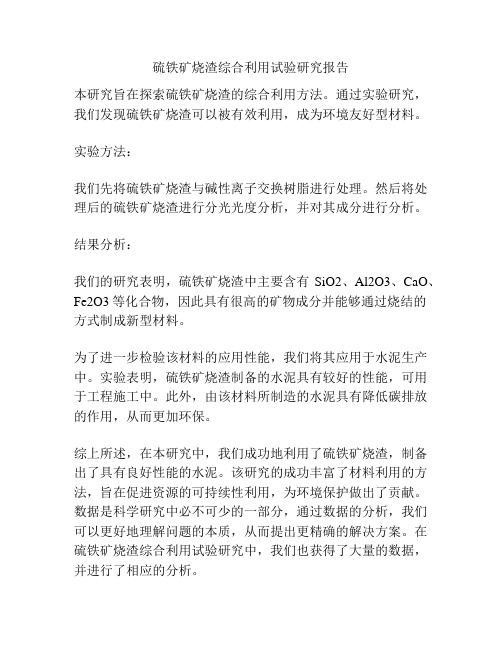
硫铁矿烧渣综合利用试验研究报告本研究旨在探索硫铁矿烧渣的综合利用方法。
通过实验研究,我们发现硫铁矿烧渣可以被有效利用,成为环境友好型材料。
实验方法:我们先将硫铁矿烧渣与碱性离子交换树脂进行处理。
然后将处理后的硫铁矿烧渣进行分光光度分析,并对其成分进行分析。
结果分析:我们的研究表明,硫铁矿烧渣中主要含有SiO2、Al2O3、CaO、Fe2O3等化合物,因此具有很高的矿物成分并能够通过烧结的方式制成新型材料。
为了进一步检验该材料的应用性能,我们将其应用于水泥生产中。
实验表明,硫铁矿烧渣制备的水泥具有较好的性能,可用于工程施工中。
此外,由该材料所制造的水泥具有降低碳排放的作用,从而更加环保。
综上所述,在本研究中,我们成功地利用了硫铁矿烧渣,制备出了具有良好性能的水泥。
该研究的成功丰富了材料利用的方法,旨在促进资源的可持续性利用,为环境保护做出了贡献。
数据是科学研究中必不可少的一部分,通过数据的分析,我们可以更好地理解问题的本质,从而提出更精确的解决方案。
在硫铁矿烧渣综合利用试验研究中,我们也获得了大量的数据,并进行了相应的分析。
首先,我们进行了对硫铁矿烧渣样品的成分分析,结果显示该样品中主要含有SiO2、Al2O3、CaO、Fe2O3等化合物。
硫铁矿烧渣作为一种工业废料,其主要成分含量的测定对于后续研究的开展有着十分重要的意义。
通过该数据,我们得出结论,硫铁矿烧渣可以成为一种潜在的环境友好型材料。
接着,我们将处理后的硫铁矿烧渣进行了分光光度分析,也就是酸性溶液浸出试验。
结果显示,经过处理后硫铁矿烧渣中的Fe、Cu等有害元素被明显地去除,同时其含量也得到有效的降低。
这说明我们所采用的处理方式能够有效地净化硫铁矿烧渣,降低对环境的污染。
最后,我们将利用硫铁矿烧渣所制造的水泥进行试验,并对其性能进行了测定。
结果表明,该水泥的初凝时间为31分钟,终凝时间为5小时45分钟,强度符合相关标准,具有一定的应用前景。
硫酸烧渣制备永磁锶铁氧体预烧料的工艺研究
第1 期
赵建湘 : 酸烧渣制备永磁锶铁氧体预烧料的工艺研究 硫
表 3 各种不同铁红的化学元素分析结果 %
子和离子通过 晶体缺陷 , 如空位或晶格边 界相互扩 散及迁移 , 促进 固相反应的进行 , 产生新 的复合氧化 物 SO・ F2 3 r n e0 。
22 制 备锶铁 氧体 预 烧料 的基 本工 艺流 程 .
注: 粒度单位为 M 。 m
试验用高品位铁 红和碳酸锶按一定 比例 , 加入 其它添加剂 , 在砂磨机里加水细磨强混 , 然后放人烘 箱烘干, 成散料装钵 , 在高温 电炉里进 行预烧 , 其工 艺 流程 如 图 1 示 。 所
2 制备锶铁氧体预烧料的试验研究
2 1 预 烧 的反应 机理 .
铁 氧体 有利 。
E R铁红( 湿法生产) 见表 3 比较 ,i: ( ) SO 含量略有偏 高 , 产锶铁 氧体 预烧 料时一 般 会添 加 SO , 以在 生 i:可
作者简介 : 赵建 湘( 9 3 , 工程师 , 1 7 一) 男, 主要 从事 固体废弃物 资源综
合利用研究 。
维普资讯
关键 词 : 硫酸烧渣 ; 纯 ; 提 锶铁氧体预烧料 ; 磁性 能 中图分类号 : Q 1 1 T I .9 1 文献标识码 : A 文章 编号 :0 3 5 0 2 0 ) 1 0 0— 3 10 —5 4 ( 0 60 —0 1 0
硫酸烧渣是生产硫 酸过程 中的副产品, 其主要 成分为 F2 3 e 。目前除 了部分供应炼铁厂或水泥厂 O 作添加剂外 , 大部分 以堆存方式处置 。为 了充分 利
表达该 固相 反应 :
图 1 制备锶铁氧体预烧料的工艺流程
23 预烧 料性 能 的评价 及检 测 方法 .
硫酸渣与冶金渣综合利用
Jn 0 2 u e2 o
硫 酸 渣 与 冶 金 渣 综 合 利 用
彭 志 坚 , 卫 国 吴
( 武汉科技大学化工与资源环境学院 , 湖北 武汉 ,30 1 40 8 )
摘要 : 阐发 了二 次资源综合 利 用与环境 问题 、 经济发展 问题 密切 相关 , 具有 综合 的社会 效益和 经济效益 , 出 提
烧 工艺 的差异 , 致 了硫 酸 渣 的组 分及 性 质 不 尽 导 相 同: 一是铁 品位 波 动较 大 , 一般 为 3 % ~5 % ; 0 5 二 是硫 酸渣 中有 未燃 尽 的硫 , 一般 在 1 以上 ; % 三 是 有 的含有 量 的有 色金 属及 贵金 属 。所 以硫 酸
第2 5卷第 2期
20 0 2年 6月
武 汉 科 技 大 学 学 报 (自 然 科 学 版 )
J fWu a i fS i& T c . Nau a ce c dt n .o h n Un.o c. e h ( trlS in e E io ) i
Vo . 5 , 1 2 No. 2
剂外 , 中绝大 多数 作 为废 弃物堆 放 , 其 不仅 长期 占 用 土地 , 浪费 铁矿 资 源 , 而且 造 成 环境 污 染 , 响 影
将硫 酸 渣与硫 酸 混合后 , 经熟 化 处理 , 回收 可 硫 酸渣 中 的铁 。其 回收 率 达 到 9 % 。熟 化 法 具 0
农 业生 产 , 害人 类健康 。 危 由于制备硫 酸渣 的原料 黄铁 矿成 分不 同及 焙
随着社 会 的发展 、 业化程 度 的提 高 , 工 人们 生
活与 工业 生产 中所 产 生 的 固体 废 弃 物 与 1 增 , 3俱 它不 仅 占用大 量 的土地 , 而且 对环 境造 成污 染 , 因 此解 决 固体废 弃 物对 环 境 的污 染 问 题 迫在 眉 睫 ;
硫酸渣高效生产铁精粉的研究及应用
硫酸渣高效生产铁精粉的研究及应用作者:温继红,陈基文来源:《创新科技》2013年第06期[摘要] 硫酸渣富含铁,产量大。
筛分实验获得100~+600目级别、产率55%的高铁低硫硫酸渣用于选铁精粉,大于100目和小于600目、产率45%的低铁高硫硫酸渣用于水泥添加剂。
硫酸渣中的硫主要是以硫酸盐形式存在,通过水洗实验降低硫和提高铁的效果明显,在矿浆浓度小于150g渣/L水和搅拌15分钟的情况下,铁回收率高达95%,获得含Fe60%、S0.32%和产率91%的铁精粉。
在水洗结合重选时,获得更高品质的铁精粉。
[关键词] 硫酸渣;筛分;水洗;降硫;重选;铁精粉[中图分类号] TQ172.62 [文献标识码] A1 前言我国是世界上铁矿石需求量最大的国家,又是铁矿石资源贫缺的国家,矿石品位低、质量差,开采成本高,对进口铁矿依存度高达50~60%。
进口矿价格涨幅不断提高,导致进口费用增加,威胁到国家经济的安全运行。
硫酸渣是硫铁矿生产硫酸过程中排出的工业废渣,每生产1吨硫酸大约产生 0.6~0.9吨烧渣。
我国每年排出量约1 000万吨,加上历年积存,其总量相当大。
除部分作为水泥厂的添加剂和少量高品位烧渣配进铁矿粉成炼铁原料外,绝大部分作为废弃物堆放,不仅长期占用了土地,又污染了环境。
因此,开发利用烧渣对于实现节能减排,缓解矿产资源的紧张现状,提高矿产资源的综合利用率,保护环境有很大的现实意义。
国内外对硫酸渣的利用已有几十年的历史,但到目前为止,对烧渣的处理技术并无重大突破。
其原因是:一是生产工艺复杂、过程控制困难、产品指标不稳定以及利用率偏低、生产成本过高等问题所致。
所选用的工艺有:磁选、重选、浮选、化学选矿、磁选—重选联合、磁化焙烧、氯化焙烧法等,磁选、重选、磁重联合虽然可获得一定品位烧渣精矿,但无法排除精矿中的硫和对精矿中的硫进行有效控制,烧渣利用率低;浮选由于经过焙烧后的矿物表面活性不足导致无法进行有效分选,效果差,与化学选矿一样都要投入较高废水处理成本;磁化焙烧、氯化焙烧,涉及高温热工,工艺流程复杂,处理成本高。
硫铁矿渣处理技术
硫铁矿渣处理技术摘要本文简述了硫铁矿渣对环境带来的危害,在建筑材料、提取有价贵金属、制备铁系产品等方面的综合利用与实践,并且总结了近十年内国内外对硫铁矿渣二次利用的研究进展。
关键词硫铁矿烧渣综合利用1、引言我国硫酸生产过程中生产的硫铁矿烧渣(又称硫酸渣、黄铁矿烧渣),是化学工业产生的主要固体废物之一。
每生产1吨硫酸会排放烧渣0.8~1.5吨的硫铁矿烧渣,全国每年将会排放约7x10吨,占化工废渣的。
由于硫铁矿烧渣大多采用堆填处理,从而出现“晴日红尘飞,雨天红水流”的现象,不仅对环境造成了严重污染,而且堆填挤占土地,减少了耕地,对资源也是一种严重的浪费。
我国是资源相对不足的国家,在45种重要矿产资源中,有10多种不能满足需求。
目前,我国铁矿生产能力将比上世纪末减少10%以上,如能把硫铁矿烧渣加以利用,可大大缓解铁矿石的供应不足。
而且这两年铁价上涨,综合利用硫铁矿烧渣,不仅可以保护环境,也避免了资源的浪费,并且也可为企业赢得利润。
硫铁矿烧渣是一种非常有价值的二次资源。
国外对硫铁矿烧渣的利用非常重视,在综合利用方面取得了很好的成果。
日本硫铁矿烧渣的利用率为70%~80%,美国为80%~85%,德国和西班牙几乎为100%。
我国硫铁矿烧渣的利用率较低,还不到50%。
造成这一现象的一个重要原因是硫铁矿烧渣的质量不高。
比如铁品位低,硫和二氧化硅的含量高等。
而烧渣质量不高是由于焙烧原料硫铁矿质量不高造成的。
产品质量标准反应了国家的生产现状和生产水平。
我国将硫铁矿的标矿含硫量定为含硫35%,烧渣的铁品位在45%左右。
而国外对硫铁矿的要求为含硫量45%以上,如前苏联将硫铁矿的标矿含硫量定为48%,日本为49%~50%,美国为52%,西班牙要求48%以上,砷、氟含量一般均不大于0.05%。
2、国内外利用现状如何对硫铁矿烧渣综合利用,已引起国内外广泛的重视。
目前国内外对硫铁矿烧渣的综合利用已经进行了一些研究,下面具体罗列出了国内外对于硫铁矿烧渣的一些利用现状。
- 1、下载文档前请自行甄别文档内容的完整性,平台不提供额外的编辑、内容补充、找答案等附加服务。
- 2、"仅部分预览"的文档,不可在线预览部分如存在完整性等问题,可反馈申请退款(可完整预览的文档不适用该条件!)。
- 3、如文档侵犯您的权益,请联系客服反馈,我们会尽快为您处理(人工客服工作时间:9:00-18:30)。
第26卷第1期 2010年2月 有色矿冶
N0N—FERROUS MINING AND METALLURGY Vo1.26.№1
February 2010
文章编号:1007—967X(2010)01—0024—04 硫酸烧渣的综合利用研究
马 涌 ,路殿坤 ,金哲男 ,李斌川 [1.山东黄金矿业(莱州)有限公司精炼厂,261441;2.东北大学材料与冶金学院有色所,110004] 摘要:采用盐酸一氯化钠体系对硫酸烧渣中的有价金属进行浸出了探索性浸出试验研究,并对 浸出脱硫效果进行了跟踪研究。根据正交试验的结果分析,得到了Pb、zn和鲰金属浸出 和脱硫的最优化条件。对最优条件下的试验结果进行估算,同时对该最佳条件进行了验 证性实验。验证实验所得的Pb、zn和Ag金属的浸出率和脱硫率与估算结果吻合良好。 关键词:硫酸烧渣;银;锌;浸出;脱硫 中图分类号:TD926.4 文献标识码:B
L——L 1 日IJ 舌
某硫酸厂采用铅锌选矿厂尾矿浮选出的硫铁矿 为原料,年产硫酸4万t。13焙烧硫精矿约100 t,产 出的硫酸烧渣也约有100 t,渣中有价元素及硫的定 量分析结果见表1,半定量分析结果见表2。 表1烧渣试样中主要有价元素分析
No. 组分 结果 单位
样品:烧渣;分析方法:Oxide—cp30一BNCO;模式:厚样 根据定量分析结果,该烧渣中铅、锌和银等有价
金属具有提取价值。从表2可知,该烧渣含铁较高, 约为57%。因此针对该渣的综合利用应该主要考 虑生产铁球团。但作为铁精粉要求S<0.5%,TFe
>60%_1 J,因此其含硫量超标。从黄铁矿烧渣中去
除元素S,使其含量低于0.5%有以下一些处理方 法。意大利蒙特卡梯尼厂采用磁化焙烧一磁选一球 团法来生产铁精粉,从沸腾炉出来的烧渣经磁选以 后,含铁量可从49%提高到67%,铁的回收率为 94%。此外,美国田纳西州铜公司采用残硫燃烧烧 结法,德国鲁奇和杜依斯堡厂采用高温氯化挥发一 竖炉球团法,日本同和矿业公司冈山厂采用硫酸化 焙烧一水浸一烧结法等都取得了不错效果 。我 国也对烧渣制取铁精粉进行了试验研究,一般采用 磁选、重选或磁一重联合流程等对烧渣进行选矿,达 到富铁降硫的目的 J。这些方法多为火法与选矿 联合工艺,均为炼铁原料脱硫研究,没有兼顾有价金 属的提取。 氯化浸出法在硫酸烧渣中有价金属的提取方面 研究较多,效果较好 I5 J。若能在生产球团原料之 前采用某种湿法冶金的方法,将其中的有价金属提 取出来,同时除去多余的元素硫是最为理想的选择。 这将会极大地提高资源的利用率和经济效益,因此 针对该烧渣中的有价元素进行提取和脱硫试验研究 具有重要的意义。
2实验 (1)实验原料:本实验的硫酸烧渣取自硫酸厂, 该厂烧渣与收集的烟尘混合在一起,烧渣较干,粒度 较细,经过进一步烘干、称重后保存于干燥皿中,用 于化验分析与试验研究。 (2)主要的实验仪器及化学试剂:
收稿日期:2009—08—13 作者简介:马涌(1972一),男,河南扶沟人,本科,冶金工程师,从事黄金精炼技术研究及管理工作。 第1期 马涌等:硫酸烧渣的综合利用研究 25 仪器:DZTW调温电热套500mL,北京市永光明 医疗仪器厂; IRW 20 DZM无级调速搅拌机,德国KA ̄集团 公司; 试剂:氯化钠,过氧化氢30%,盐酸均为分析纯。 (3)试验方法及程序: 将一定量的矿样与浸出液介质混合后,升到所 需的温度,搅拌并加入所需的氧化剂进行浸出试验, 浸出结束后经过滤洗涤后,将滤饼称重并送去化验 铅、锌和银。根据浸出前后固相化验的结果计算金 属的浸出率。金属元素化验分析采用AAS法测定。
3实验结果与讨论 3.1 试验方案的设计与结果 参考国外类似焙烧矿的浸出方法 ,采用相似 的HC1一NaC1一H O 浸出体系作氧化浸出试验研 究。对影响铅、锌、银浸出率和脱硫深度的因素进行 优化试验。试验采用L, (4 )正交表设计试验,每次 实验用硫酸烧渣量为50 g,试验考察的主要因子及 水平见表3,根据L。 (4 )正交试验表设计的试验方 案及试验后计算出的铅、锌和银的浸出率和脱硫率 见表4。 表3 L, (4 )正交试验的因子水平表 因子 水平 l 2 3 4 氯化钠 双氧水 c‘盐酸 D( ̄f,.[Ntzg) 度 v-/L mL mL oc l5O 3.93 2 5 200 7.85 5 250 I1.78 7.5 3o0 l5.70 l0 20 40 6o 80
3.2铅、锌、银浸出及脱硫正交试验结果的极差分析 对于烧渣中铅的浸出来说,浸出率最差也在 92%以上,浸出效果非常好,而最好的浸出率也不超 过95%。由此可见,烧渣中的铅很容易在本溶液体 系中浸出,因此在本实验的因子水平范围内,浸出条 件不必优化。 关于锌的浸出,在A、B、c、D、E各因子中,对锌 浸出率影响的主次顺序为E(25.85)>B(18.60)> C(16.5)>D(12.13)>A(7.68),其最佳条件组合 为A3BlC4D4E3。锌的浸出率波动在18%~64% 之间,可见浸出因子水平的变动对浸出率的影响十 分显著,所以有必要对锌的浸出条件进行分析和优化。 对于银的浸出,在A、B、C、D、E这5个因子中, 对银浸出率影响的主次顺序为E(14.88)>A(8.2) >D(6.88)>C(6.78)>B(6.53),其最佳条件组合 为A4B4C4D2E3。银的浸出率波动在24%~62% 之间,可见因素水平的变动对浸出率的影响十分显 著,有必要对银的浸出条件进行分析和优化。 对于硫的脱除来说,在A、B、c、D、E这5个因 子中,对脱硫率影响的主次顺序为E(0.73)>D (0.66)>B(0.61)>C(0.26)A(0.23)>,其最佳 条件组合为A4B1C3D2E3。硫的含量波动在 0.15%~1.79%之间,可见因素水平的变动对脱除 率的影响十分显著,有必要对硫的脱除条件进行分 析和优化。 3.3最佳浸出工艺条件的选择与论证 3.3.1金属浸出率及经济性的的比较 (1)铅的浸出率均高于92%,且最高不超过 95%。因此各因素对铅的浸出影响不够显著,因此 在金属提取的技术条件优化时可以将其放在次要地 位考虑,甚至不用考虑。 (2)锌的浸出率比较低,波动在18%~64%之 间,可见浸出条件对锌浸出率的影响十分显著。锌 浸出的最佳工艺条件是:A3B1 C4D4E3。 (3)银的浸出率波动在24%~62%之间,其波 动范围与锌类似,浸出条件对浸出效果的影响也很 显著。银浸出的最佳工艺条件是:A4B4C4D2E3。 (4)硫的脱除波动范围很大,浸出条件对脱除 效果的影响十分显著。银浸出的最佳工艺条件是: A4B1 C3D2E3。 在金属浸出中要兼顾锌和银两种金属的回收, 每吨烧渣中的银和锌价值相当,在浸出条件的确定 上,应该以药剂消耗和成本较低为主。同时硫的最 佳脱除条件与银的浸出很相近,而且由于银的价值 略高于锌,因此在条件冲突时可优先考虑银的回收 和硫的脱除。 3.3.2浸出条件的选择与论证 A:氯化钠浓度的选择:氯化钠浓度为250 g/L 时(3水平),锌的浸出率最高,在此条件下银的浸出 率与最佳条件300 g/L的结果相比变化不大,而对 于脱硫来说属于次要因素。因此可以选择浸出液的 氯化钠浓度为250 g/L。 B:双氧水用量的确定:锌和银浸出的最佳双氧 水用量分别处于l水平和4水平,即锌的浸出不需 要太多的双氧水,3.93 mL/50 g渣(相当于78.6 L/t 渣),而银的浸出双氧水需要最高,达到l5.72 mL/ 50 g渣(相当于314.4 L/t渣),但银的浸出在双氧 水最低时效果与最高时相差不大。同时硫的脱除与 锌的浸出最佳双氧水用量相同,因此选择最低的双 氧水用量,即78.6 L/t渣。 26 有色矿冶 第26卷 C:盐酸用量的确定:浸出锌和银时盐酸的最佳 用量均为4水平的最高值,而且盐酸剂量对脱硫属 于次要因素,因此选盐酸用量为最高水平,相当于 200 I/t渣。 D:液固比的选择:浸出锌和银的最佳液固比分 别为4水平和2水平,即L/S分别为6和4。但液 固比对锌的浸出影响是相对次要的因素,而对于银 的浸出来说略微重要一点,但对于脱硫十分重要,因 此可取2水平,即选择液固比为4。 E:浸出温度的选择:从锌和银的浸出来看,温 度处于3水平最佳,这一点与脱硫条件相同,此时温 度为60℃,因此选择最佳的浸出温度为60℃。 因此,从多金属浸出和脱硫综合考虑来看,可将 最佳浸出工艺条件定为:A3B1C4D2E3,即:氯化钠 浓度250 g/L;双氧水用量3.93 mL;盐酸用量10 mL;液固比为4;浸出温度为60℃。
3.4最佳浸出工艺条件下的浸出率估算与验证性 实验 3.4.1 最佳条件下铅、锌和银浸出率数值的估算 按照前面选定的最佳实验条件:A3B1C4D2E3, 根据模型。6 X优=X+AXA3+AXBl+AXC4+AXD2 +AX睇,式中△x∞是A因子为3水平时的平均浸 出率减去均值X;同理,AXBl、AXc4、AX。 和AXE3 分别为B4、C4、D4和E3水平下的平均浸出率减去 x。由以上公式分别计算计算可得X 优=95.28%, Xz 优=70.70%和XA 优=64.15%,Xs优=0.45%。
3.4.2最佳条件下浸出铅、锌和银的验证试验 取烧渣试样50 g,用蒸馏水配置成200 mL浓度 为250 g/L的NaC1溶液,加入双氧水3.93 mL置于 烧杯中,加入浓HC1 10 mL,将矿样溶于其中,60℃ 搅拌浸出1 h。浸出结果及与估算值的对比见表5。