烧结矿冷却的目的和意义
烧结矿的固结机理
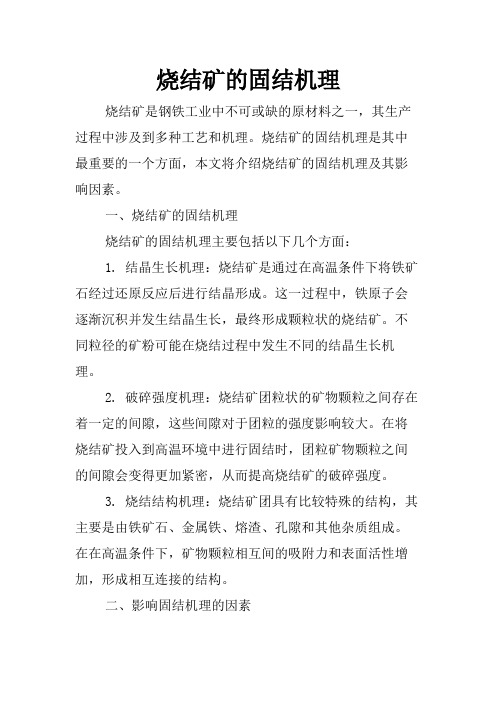
烧结矿的固结机理烧结矿是钢铁工业中不可或缺的原材料之一,其生产过程中涉及到多种工艺和机理。
烧结矿的固结机理是其中最重要的一个方面,本文将介绍烧结矿的固结机理及其影响因素。
一、烧结矿的固结机理烧结矿的固结机理主要包括以下几个方面:1. 结晶生长机理:烧结矿是通过在高温条件下将铁矿石经过还原反应后进行结晶形成。
这一过程中,铁原子会逐渐沉积并发生结晶生长,最终形成颗粒状的烧结矿。
不同粒径的矿粉可能在烧结过程中发生不同的结晶生长机理。
2. 破碎强度机理:烧结矿团粒状的矿物颗粒之间存在着一定的间隙,这些间隙对于团粒的强度影响较大。
在将烧结矿投入到高温环境中进行固结时,团粒矿物颗粒之间的间隙会变得更加紧密,从而提高烧结矿的破碎强度。
3. 烧结结构机理:烧结矿团具有比较特殊的结构,其主要是由铁矿石、金属铁、熔渣、孔隙和其他杂质组成。
在在高温条件下,矿物颗粒相互间的吸附力和表面活性增加,形成相互连接的结构。
二、影响固结机理的因素烧结矿固结机理受到多种因素的影响,主要包括以下几个方面:1. 矿石成分:矿石的成分会显著影响烧结矿的固结机理。
在不同的还原反应条件下,矿石的不同成分在烧结过程中发挥着不同的作用。
2. 烧结温度:烧结温度是烧结矿固结机理中最为重要的因素之一。
不同的矿粉在不同的烧结温度下会发生不同的固结反应,形成不同的团粒结构。
3. 气氛控制:在固结过程中,气氛的控制也是十分重要的。
氧气、水蒸气、二氧化碳等气体的含量都有可能对烧结团粒的形成产生影响。
4. 压力控制:固结过程中的压力控制也十分关键。
烧结矿的压力会影响其团粒结构的形成和稳定性。
5. 冷却方式:在固结后的冷却过程中,冷却速率和方式都有可能对烧结团粒的微观结构和力学性能产生影响。
三、结论烧结矿固结机理是复杂的,受到多种因素的影响。
在烧结矿的生产过程中,需要综合考虑多方面因素的影响,并采取相应的措施来进行优化和调控。
通过研究烧结矿的固结机理,可以更好地掌握其生产过程和性能特征,对于提高钢铁生产的效率和质量都具有重要意义。
烧结矿竖式冷却过程中流动与传热特性研究

烧结矿竖式冷却过程中流动与传热特性研究烧结矿竖式冷却过程中流动与传热特性研究摘要:烧结矿的质量直接影响到烧结后铁制品的质量和生产效率。
烧结矿的冷却过程会影响到烧结矿的物理特性和化学组成,从而影响到烧结后铁制品的质量。
研究烧结矿竖式冷却过程中的流动与传热特性对于实现优质烧结矿的生产有着重要的意义。
本文基于对烧结矿竖式冷却过程的分析,采用数值模拟方法研究了其中的流动与传热特性,并对研究结论进行了分析。
结果表明,竖式冷却过程中,流体的速度分布不均,存在较强的层流现象,同时热传输主要由对流传热和辐射传热组成,其中对流传热是主要的传热机制。
同时,通过对不同工艺参数的影响分析可以得出,冷却风速和冷却氧气含量对流动与传热特性的影响明显,需要合理设置工艺参数以优化竖式冷却过程的设计。
关键词:烧结矿;竖式冷却;流动特性;传热特性;数值模拟1.引言烧结矿是冶金生产中的重要原料之一,烧结矿的质量直接影响到烧结后铁制品的质量和生产效率。
烧结矿的冷却过程是影响其物理特性和化学组成的一个重要因素,从而影响到烧结后铁制品的质量。
因此,研究烧结矿冷却过程中的流动和传热特性对于实现优质烧结矿的生产具有重要的意义。
竖式冷却是烧结矿冷却的主要方式之一,其优点在于占地面积小,冷却效果好等。
在竖式冷却中,流动和传热是竖式冷却过程中的核心问题之一。
因此,研究竖式冷却过程中的流动和传热特性,对于优化烧结矿生产工艺、提高生产效率有着重要意义。
2.研究方法本文采用数值模拟的方法对竖式冷却过程中的流动和传热进行了研究。
采用计算机模拟软件对竖式冷却过程的流动和传热进行建模和分析,得出竖式冷却过程中流体的速度分布、温度分布等数据,同时分析竖式冷却过程中不同工艺参数的影响。
3.模型建立和分析建立了一个三维数值模拟模型,并对竖式冷却过程的物理过程进行建模和分析。
模型中,考虑了竖式冷却过程中的气相流动、传热和烧结矿颗粒动力学过程等相互作用过程,并分析了竖式冷却过程中热传输机制。
铁矿石烧结过程的热工分析
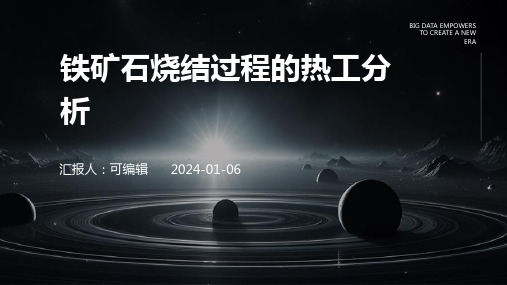
固相反应
不同矿物颗粒在高温下 发生化学反应,生成新
的矿物相。
液相形成
部分易熔组分熔化,促 进颗粒粘结,形成块状
烧结矿。
气体逸出
分解反应和固相反应过 程中产生的气体逸出, 影响烧结矿的孔隙率和
气孔形状。
BIG DATA EMPOWERS TO CREATE A NEW ERA
03
铁矿石烧结过程的热工分析方法
意义
烧结是钢铁工业中的重要环节, 通过烧结可以大规模地生产高质 量的铁块,满足钢铁生产的需求 。
铁矿石烧结的基本流程
配料与混合
将铁矿石、燃料和溶剂等原料 按照一定比例混合,加入适量
的水搅拌成料浆。
造球
将料浆注入造球机中,通过滚 动和压缩作用形成一定粒度的 球形颗粒。
烧结
将球形颗粒送入烧结机中,在 高温下进行燃烧和熔融,使铁 矿石中的氧化物还原并熔化成 液态。
01
铁矿石烧结过程简介
BIG DATA EMPOWERS TO CREATE A NEW
ERA
铁矿石烧结的定义
• 铁矿石烧结:将铁矿石、燃料和溶剂等原料按照一定比例混合 ,在高温下进行燃烧和熔融,使铁矿石中的氧化物还原并熔化 成液态,最终冷却凝固成块状铁的过程。
铁矿石烧结的目的和意义
目的
将铁矿石中的氧化物还原成铁, 并去除其中的杂质,提高铁的纯 度和质量。
在新产品开发中的应用
1 2
开发新型烧结矿
通过对铁矿石烧结过程中的热工分析,可以了解 铁矿石的烧结特性,开发新型烧结矿。
优化新产品配方
通过对铁矿石烧结过程中的热工分析,可以了解 不同原料的烧结特性,优化新产品的配方。
3
提高新产品质量
烧结环冷密封

烧结环冷密封主要应用于烧结矿的冷却过程中,以减少粉尘污染和提高能效。
在实际操作中,例如天铁第一炼铁厂新一烧烧结矿冷却系统就采用了双层结构的台车、新型的环形密封槽装置、端部密封等技术。
此外,动态自平衡卸料、全密封及保温等技术也被广泛应用,这些技术可以有效增加通风面积,降低冷却风机电耗,增加余热发电量。
中国中冶北方自主研发的多功能高效烧结环冷机则对框架结构、台车型式、上下密封、温度控制、卸料系统、配风、余热收集等方面进行了全面升级和创新。
而由中国中冶所属中冶长天国际工程有限责任公司自主研发的“LSCC550液密封环冷机的研制”研究成果,是一次在烧结矿冷却技术及装备上的重大突破。
另外,实施环冷低温段密封,可以消除粉尘污染,实现绿色烧结。
在环冷台车运行时,含尘气流向四周扩散,有一部分含尘气流不能被环冷板矿除尘罩捕捉,此时可以通过采用百叶窗+冲孔板”优化结构来提高改造效果,使得外部进入的气流带着扬起的含尘气流被吸入除尘系统,达到快速降尘的目的。
烧结生产工艺流程知识讲解
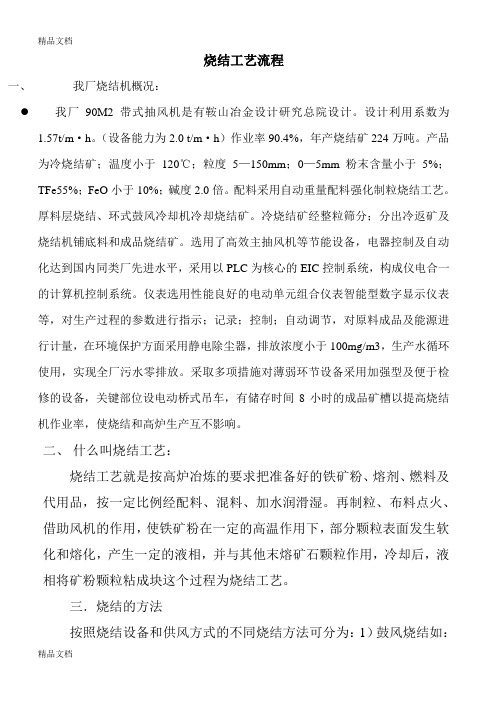
烧结工艺流程一、我厂烧结机概况:我厂90M2带式抽风机是有鞍山冶金设计研究总院设计。
设计利用系数为1.57t/m·h。
(设备能力为2.0 t/m·h)作业率90.4%,年产烧结矿224万吨。
产品为冷烧结矿;温度小于120℃;粒度5—150mm;0—5mm粉末含量小于5%;TFe55%;FeO小于10%;碱度2.0倍。
配料采用自动重量配料强化制粒烧结工艺。
厚料层烧结、环式鼓风冷却机冷却烧结矿。
冷烧结矿经整粒筛分;分出冷返矿及烧结机铺底料和成品烧结矿。
选用了高效主抽风机等节能设备,电器控制及自动化达到国内同类厂先进水平,采用以PLC为核心的EIC控制系统,构成仪电合一的计算机控制系统。
仪表选用性能良好的电动单元组合仪表智能型数字显示仪表等,对生产过程的参数进行指示;记录;控制;自动调节,对原料成品及能源进行计量,在环境保护方面采用静电除尘器,排放浓度小于100mg/m3,生产水循环使用,实现全厂污水零排放。
采取多项措施对薄弱环节设备采用加强型及便于检修的设备,关键部位设电动桥式吊车,有储存时间8小时的成品矿槽以提高烧结机作业率,使烧结和高炉生产互不影响。
二、什么叫烧结工艺:烧结工艺就是按高炉冶炼的要求把准备好的铁矿粉、熔剂、燃料及代用品,按一定比例经配料、混料、加水润滑湿。
再制粒、布料点火、借助风机的作用,使铁矿粉在一定的高温作用下,部分颗粒表面发生软化和熔化,产生一定的液相,并与其他末熔矿石颗粒作用,冷却后,液相将矿粉颗粒粘成块这个过程为烧结工艺。
三.烧结的方法按照烧结设备和供风方式的不同烧结方法可分为:1)鼓风烧结如:烧结锅、平地吹;2)抽风烧结:①连续式如带式烧结机和环式烧结机等;②间歇式如固定式烧结机有盘式烧结机和箱式烧结机,移动式烧结机有步进式烧结机;3)在烟气中烧结如回转窑烧结和悬浮烧结。
四.烧结矿的种类:CaO/SiO2小于1为非自熔性烧结矿;碱度为1-1.5是自熔性烧结.矿碱度为1.5~2.5是高碱度烧结矿;大于2.5是超高或熔剂性烧结矿。
探讨提高烧结矿质量的措施

江西冶金职业技术学院毕业论文论文题目:浅谈提高烧结矿的质量的措施姓名:班级:系部:指导老师:时间:1 烧结的起因 32烧结的目的意义 33影响烧结矿质量的因素 33.1烧结矿的品位 33.2 SiO2含量 33.3烧结矿碱度 33.4 MgO%含量 33.5水分 33.6料层厚度 34 提高烧结矿质量的措施 34.1优化入烧原料结构 34.1.1 优化入烧原料结构,稳定控制烧结矿化学成分 34.1.2改善入烧燃料质量 34.2生产高碱度烧结矿 34.3操作技术改进 34.3.1自动配料技术 34.3.2低温点火技术 34.3.3强力造球技术 34.3.4厚料层技术 34.4设备技术改造 34.4.1添加剂仓技术改造 34.4.2混料系统技术改造 34.4.3筛分系统技术改造 3摘要:本文简述了影响烧结矿质量的因素,系统的介绍了提高烧结矿质量的技术措施。
关键词:烧结矿质量技术措施1 烧结的起因烧结生产起源于英国和德国。
大约在1870年,这些国家就开始使用烧结锅,用来处理矿山开采、冶金工厂、化工业厂等废弃物。
1892年美国也出现了烧结锅。
世界钢铁工业第一台带式烧结机于1910年在美国投入生产。
这台烧结机的面积为8.325m2(1.07m×20.269m),当时用于处理高炉炉尘,每天生产烧结矿140t。
它的出现引起了烧结生产的重大变革,从此带式烧结机得到了广泛的应用。
我国铁矿资源十分丰富。
由于历史的原因,建国前钢铁工业十分落后,烧结生产更为落后,1926年3月在鞍山建成四台21.63m2(1.067m×20.269m)带式烧结机,日产量1200t。
1935年,1937年有相继建成四台50m2烧结机,每年产量达19万t。
建国后,我国烧结工业有了很大的发展,1952年鞍钢从苏联引进75m2烧结设备和技术,这套在当时具有国际先进水品的设备,对新中国的烧结工业起到了示范作用。
随着我国钢铁工业的不断发展,一些钢铁公司的烧结厂相继建成投产。
烧结试题

练习题一填空题1、炼铁用的熟料是指烧结矿。
2、目前世界上90%以上的烧结矿是通过带式抽风烧结方法来生产的。
3、按照烧结料层中温度的变化和烧结过程中多发生的物理化学反应,烧结料层可分为五个带,从上往下依次出现烧结矿层、燃烧层、干燥层、预热层、过湿层。
4、烧结过程中的水分迁移是指蒸发和冷凝。
5、水蒸汽冷凝成水时的温度叫露点温度。
二、选择题1、在烧结料的五个层中,水汽冷凝,使料层透气性大大恶化,必须减少或消除的一层为D 。
A、燃烧层B、预热层C、烧结矿层D、过湿层2、在烧结料的五个层中,温度最高,反应进行最活跃的一层为 A 。
A、燃烧层B、预热层C、烧结矿层D、过湿层3、烧结料层温度按分布所发生物理、化学反应分为( B )层。
A.4 B.5 C.6 D.34、烧结矿固结主要靠( B )完成。
A.固相反应B.发展液相C.冷却固相D.还原反应5、烧结过程中,透气性最好是( C )。
A.过湿层B.干燥层C.烧结矿层6、烧结机每平方米有效面积( B )生产的烧结矿数量为烧结机利用系数。
A.每昼夜B.每小时C.每分钟7、烧结过程中,开始出现液相是在( C )。
A.干燥带B.预热带C.燃烧带8、某班产烧结矿1000吨,其中未验品、废品、二级品、试验品各100吨,试问该班烧结矿一级品率为( A )。
A.60% B.75% C.85.7% D.50%9、垂直烧结速度是指( A )。
A.燃烧带移动速度B.固体燃料燃烧速度C.料层传热速度10、某厂有6台烧结机,某班5台机生产,1台检修,其作业率是( B )。
A.70% B.83.33% C.90% D.60%11、在烧结过程中水汽冷凝发生在( C )。
A.干燥带B.预热带C.过湿带12、一台烧结机( A )的生产量称为烧结机台时能力,又称台时产量。
A.一小时B.一天C.一昼夜13、烧结机的有效面积是台车宽度与烧结机( A )的乘积。
A.有效长度B.台车长度C.总长度D.机头至机尾的长度14、垂直烧结速度与烧结矿产量的关系是(A )。
烧结矿冷却方式

烧结矿冷却方式及国内生产实践2006-8-14 15:56:37 中国选矿技术网浏览981 次收藏我来说两句(一)烧结矿冷却方式的分类烧结矿的冷却靠介质进行。
冷却介质可以是空气、水或两者联合使用。
因此,国内外曾出现了多种的冷却方法和设备,可分为图1所示的类型。
(二)国内烧结矿冷却的生产实践1.机上冷却工艺机上冷却工艺是在烧结机上完成烧结和冷却过程。
即在烧结终了时,不立即卸下烧结矿,而让其继续停留在烧结机上,与此同时,利用冷却段风机吸入的冷空气使烧结矿冷却。
机上冷却的简图见图2.(1)机上冷却工艺的优缺点机上冷却工艺的优点是单辊破碎机的工作温度低,不需热矿振动筛和单独的冷却机,可以提高设备作业率、降低设备维修费;返矿量少、成品率高、燃料耗量低;简化了设备配置,改善操作环境,减少污染,便于冷却系统和环境除尘。
机上冷却工艺的缺点是冷却产生的废气温度高(可达600℃)、压力损失大(风机压力需8000Pa左右)、需要高温风机、功率消耗大;台车和箅条受热循环作用大;不能利用返矿的废热来预热混合料。
(2)机上冷却工艺的主要影响因素机上冷却工艺的主要影响因素如下:矿石性能对机上冷却工艺的影响较大,见图3.从图3可知,贫铁矿。
特别是褐铁矿烧结,其初始堆积密度低、烧损高,这类矿石烧成的烧结矿所需的冷却时间短,冷烧比小。
如水城烧结厂采用机上冷却工艺,冷烧比为0.77。
富矿中的磁铁矿烧结时,因所得烧结矿堆积密度大、透气性差,以及冷却过程的氧化放热,故其冷却时间长,但由于磁铁矿烧结时间也长,所以对冷烧比影响不大,冷烧比为1.0。
赤-针铁矿烧结所需冷烧比在上述两者之间。
不同矿物原料烧结所需的冷烧比,应通过烧结试验来确定。
烧结矿碱度(m(CaO)/m(SiO2))升高时,所得的烧结饼透气性得到改善,其冷却时间减少,从而减少冷烧比。
混合料的均匀性、料层高度与烧结负压、冷却负压等操作条件,都会影响机上冷却的冷却时间和冷却效果。
冷却时间在很大程度上取决于冷却风量和冷却负压。
- 1、下载文档前请自行甄别文档内容的完整性,平台不提供额外的编辑、内容补充、找答案等附加服务。
- 2、"仅部分预览"的文档,不可在线预览部分如存在完整性等问题,可反馈申请退款(可完整预览的文档不适用该条件!)。
- 3、如文档侵犯您的权益,请联系客服反馈,我们会尽快为您处理(人工客服工作时间:9:00-18:30)。
烧结矿在烧结机上烧成之后从机尾卸下时其温度大约在750~800℃左右,对这样赤热的烧结矿,一般都要将其冷却到150℃以下,这是因为有以下几个原因。
(1)保护运输设备,使厂区培植紧凑。
如果烧结矿不冷却,运送赤热的烧结矿就需要使用较多的专用矿车来装载,当烧结配比不当、残炭较多时,烧结矿还会在专用的矿车中继续燃烧,致使矿车烧坏变形,而且使用矿车时还要有较长的铁路运输线,会使烧结厂与炼铁厂在配置上不得不拉的很远。
若将烧结厂冷却就可采用胶带机运输,使厂区配置紧凑,少占农田用地。
(2)保护高炉炉顶设备及高炉矿槽。
烧结矿如不冷却储存在高炉矿槽中,会很快损坏高炉矿槽,致使有时要停止生产修补矿槽,影响作业率,降低产量。
使用不经冷却的烧结矿,高炉炉顶温度高(500~600℃),为了保护炉顶设备,一般炉顶压力不敢提高,大都控制在49~78kPa(4.9~7.8N/cm2),而使用冷烧结矿的炉顶,由于烧结矿的温度低(350℃以下,实际烧结矿的温度在150℃左右),炉顶压力可提高到98~127 kPa(9.8~12.7N/cm2),对强化高炉冶炼有利,而且使用过的冷却烧结矿,高炉的上料系统及炉顶设备不易损坏,使用寿命大大提高。
(3)改善高炉、烧结厂的劳动条件。
由于烧结矿冷却后可以筛出粉末,冷烧结矿在由烧结厂到高炉矿槽以及高炉上料系统的一系列装卸运输转运过程中所产生的污染环境的灰尘比热烧结矿大大减少,从而改善了劳动条件和环境卫生。
(4)为烧结矿的整粒及分出铺底料创造了条件。
烧结矿不经过冷却,由于温度高,很难进行较彻底的破碎筛分以及分出烧结厂需要的铺底料。
烧结矿冷却到150℃以下,就可使用在常温下工作的破碎机,筛子及胶带运输机进行冷破碎,以及多次的筛分运输作业,较彻底的筛出粉末(5~0㎜),分出铺底料(10~20㎜)。
(5)为实现高炉生产技术现代化创造条件。
现代化的高炉生产技术已发展到超高压炉顶(19.6N/cm2)操作,无料钟炉顶,胶带机炉顶上料,外燃式热风炉,炉内料位控制等等,所有这些都必须建立在烧结矿冷却及整粒分级的基础上,因而烧结矿如不冷却也无法实现高炉技术现代化。