腐蚀评价讲义
第1章概论及第2章常用腐蚀评定方法

试样
试样制备 平行试样 试样标记 试样暴露
重现性,可比性 重现性,准确性
1.2.3试验介质
主要影响因素:
(1)介质的类型、主要成分和杂质成分、浓度及分布 (2)pH值 (3)电导率 (4)腐蚀产物 (5)固体粒子数量和尺寸 (6)介质的容量 实际介质 (7)生物因素 模拟溶液 试验介质 加速溶液 纯溶液
2.3失厚测量与孔蚀深度测量
测量腐蚀前后的厚度损失后单位时间的腐蚀失厚(mm/a) 失 厚 测 量 无损检测:涡流法、超声波法、射线照相法、电阻法 计量工具和仪器:卡尺、卡钳、螺旋测微器、带标度 的双筒显微镜。
孔蚀密度 蚀孔直径 孔蚀深度 孔蚀表征
测量1dm2试样上10个最深的蚀孔深度的P平均、P
2.7 溶液分析与指示剂法
溶液分析:当腐蚀产物完全溶于介质时,通过定量分析可获得腐 蚀量~时间曲线。 极谱分析、离子选择电极和原子吸收光谱均被用于溶液分析。 指示剂法:利用某些试剂与特定金属离子或腐蚀产物的颜色反应 例:用铁羟指示剂确定阳极区和阴极区,检验镀层质量。
知识点:
常用腐蚀评定方法的种类 利用质量损失法计算平均腐蚀速度的方法 孔蚀的表征 电阻法评定腐蚀的原理及技术特点
课程介绍
学时
32 学时 课堂讲授16学时+实验16学时
学分
2学分
考 核
平时考核(占总成绩50%) 笔试(占总成绩50%)
教材及参考书
教材: 李久青,杜翠薇,腐蚀试验方法及监测技术,中国石化出版社, 2007 参考书: 1.吴荫顺主编,金属腐蚀研究方法,冶金工业出版社,1993 2.金属腐蚀研究方法实验指导书,北京科技大学 3. 周伟舫主编,电化学测量,上海科学技术出版社,1985.4 4.史美伦编著,交流阻抗谱原理及应用 ,国防工业出版社, 2001.3 5.曹楚南,电化学阻抗谱导论,科学出版社,2004年5月第二次 印刷 5.中国腐蚀与防护学会主编,金属的局部腐蚀:点腐蚀·缝隙腐 蚀·晶间腐蚀·成分选择性腐蚀,化学工业出版社 1995
ICDA管道内腐蚀直接评价方法探析

ICDA管道内腐蚀直接评价方法探析在传统的管道内腐蚀评价中,采用了一些常见的方法,比如电化学法、超声波检测法,X射线检测法等。
这些方法虽然具有一定的可行性,但是在实际应用中存在着一些不足之处,例如需要大量的人力物力、高昂的成本、操作复杂等。
需要进一步探索管道内腐蚀直接评价的方法,提高评价的准确性和效率,保障管道的安全运行。
二、ICDA管道内腐蚀直接评价方法ICDA(Internal Corrosion Direct Assessment)管道内腐蚀直接评价方法是一种目前比较先进的评价方法。
该方法主要是通过对管道内壁进行直接的腐蚀评价,以确定管道内部的腐蚀情况,并进一步确定管道的安全状态。
ICDA方法主要包括以下几个步骤:1.数据收集:需要对管道进行全面的数据收集,包括管道的材质、管道使用年限、介质性质等信息,并结合实地调查记录管道的运行情况。
2.风险评估:在数据收集的基础上,对管道的腐蚀风险进行评估,包括腐蚀速率、腐蚀形式、腐蚀位置等因素进行综合分析。
3.直接评价:通过对管道内壁进行直接腐蚀评价,采用现代化的检测设备,结合实际情况对管道内部腐蚀情况进行准确评估。
4.安全评价:利用评估结果进行管道的安全评价,确定管道的安全状态,包括安全使用寿命、修复方案等。
ICDA方法的优点在于可以直接对管道内部进行腐蚀评价,减少了对外部环境的依赖,评价的准确性和可靠性更高。
而且ICDA方法相对传统方法来说,操作简单,成本低,效率高,更适合实际工程中的应用。
三、ICDA方法的不足尽管ICDA方法在管道腐蚀直接评价中具有一定的优势,但是也存在一些不足之处需要进一步改进和完善。
1.检测技术:目前,ICDA方法中所采用的检测技术还不够成熟,对于一些特殊材质和结构的管道难以有效检测,需要进一步研发和改进相关技术。
2.评价准确性:由于管道内腐蚀具有一定的随机性,ICDA方法在评价准确性上还需要不断提高,避免误判。
3.数据分析:ICDA方法中数据量大,需要进行大量的数据分析工作,当前的数据分析方法还不够完善,需要引入更多的先进技术和算法。
腐蚀电位评价
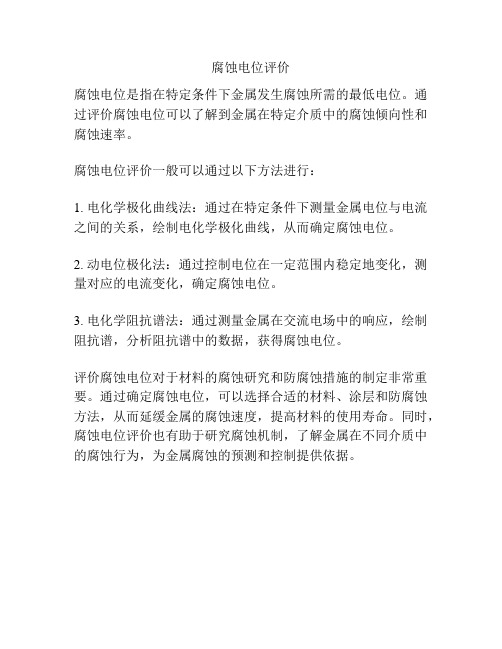
腐蚀电位评价
腐蚀电位是指在特定条件下金属发生腐蚀所需的最低电位。
通过评价腐蚀电位可以了解到金属在特定介质中的腐蚀倾向性和腐蚀速率。
腐蚀电位评价一般可以通过以下方法进行:
1. 电化学极化曲线法:通过在特定条件下测量金属电位与电流之间的关系,绘制电化学极化曲线,从而确定腐蚀电位。
2. 动电位极化法:通过控制电位在一定范围内稳定地变化,测量对应的电流变化,确定腐蚀电位。
3. 电化学阻抗谱法:通过测量金属在交流电场中的响应,绘制阻抗谱,分析阻抗谱中的数据,获得腐蚀电位。
评价腐蚀电位对于材料的腐蚀研究和防腐蚀措施的制定非常重要。
通过确定腐蚀电位,可以选择合适的材料、涂层和防腐蚀方法,从而延缓金属的腐蚀速度,提高材料的使用寿命。
同时,腐蚀电位评价也有助于研究腐蚀机制,了解金属在不同介质中的腐蚀行为,为金属腐蚀的预测和控制提供依据。
危险化学品的腐蚀性与防腐措施

危险化学品的腐蚀性与防腐措施在工业和实验室领域中,危险化学品的处理和储存一直是一个重要的问题。
对于危险化学品的腐蚀性,以及如何采取防腐措施,本文将深入探讨。
一、腐蚀性的定义和分类腐蚀性是指物质对其他物质产生破坏性的作用,主要通过化学反应导致。
根据腐蚀性的不同特性,可以将其分为酸性、碱性和氧化性腐蚀性。
酸性腐蚀性:酸性物质具有强酸性质,能与金属发生反应,形成金属盐和水进行腐蚀。
例如,硫酸、盐酸等。
碱性腐蚀性:碱性物质具有强碱性质,能与金属发生反应,形成金属氢氧化物和水进行腐蚀。
例如,氨水、氢氧化钠等。
氧化性腐蚀性:氧化性物质具有强氧化作用,能与金属和非金属发生反应,形成金属或非金属的氧化物进行腐蚀。
例如,硝酸、过氧化氢等。
二、常见危险化学品腐蚀性评价标准为了评估危险化学品的腐蚀性,学术界和工业界普遍采用了一些标准和指标。
其中,最常用的标准是美国国家消防协会(NFPA)的704标志。
NFPA的704标志将危险化学品的腐蚀性分为四个等级:- 0级:无腐蚀性;- 1级:稍腐蚀性;- 2级:中度腐蚀性;- 3级:严重腐蚀性。
这些等级可以帮助人们更好地了解危险化学品的腐蚀性,并采取相应的防护措施。
三、危险化学品腐蚀性防护措施为了保护人员和设备免受危险化学品的腐蚀性侵害,必须采取一系列的防护措施。
1. 防腐涂层在处理和储存危险化学品的设备和容器上,使用耐腐蚀涂层是一种有效的防护方法。
这些涂层可以防止腐蚀性物质对设备和容器表面的侵蚀,延长其使用寿命。
2. 贮存区域划分将危险化学品按照其性质和腐蚀等级划分为不同区域进行贮存,可以减少腐蚀性物质的污染和泄漏风险。
同时,要确保贮存区域通风良好,定期检查和维护设备和容器的完整性。
3. 个人防护措施对于与危险化学品接触的工作人员,个人防护装备是必不可少的。
例如,戴上适当的防护手套、护目镜和防护服,确保皮肤、眼睛和呼吸系统不受腐蚀性物质的侵害。
4. 泄漏应急处理当发生危险化学品泄漏时,立即采取措施进行应急处理。
长输管道腐蚀缺陷的评价

第3 2 卷第 6 g g( 2 0 1 3 . 0 6 )( 基建管理)
长输管道腐蚀缺陷的评价
郭宏 大 庆 油田 设 计院
摘要 :对埋 地 输 油 管线 全线 腐 蚀检 测 数据 分析 表 明 ,管线 不 同 区段 腐 蚀程 度 差 别很 大 ,在 预 测其 腐蚀 管道 剩余 寿命 时 亦应 采 用分段 预 测 的原 则进 行 。 最普遍 的预测 腐 蚀增 长 率 的方 法就 是 对 比 两组 近 些 年 内的检 测数 据 。全 寿 命 腐 蚀 增 长 率 预 测 适 用 于 两 次检 测 间 隔时 间较 短 的情 况 ;半寿命 腐蚀 增 长率 预 测适 用 于 两次检 测 间隔 时间较 长 或 只有 一 次且距 投 产之 日起 时 间较 长 的情况。依据腐蚀增长速率可预测腐蚀缺 陷的未来发展 I 青 况 ,从 而判定 出计划修复时间和再检测时 间。
时间。
高的 高强度 钢 。
1 . 3 R S T R E N G 有效 面积法 该 方 法 不 再需 要 用 B 3 1 G法 中 的抛 物线 或 矩形
对腐蚀 的几何形 状进 行 面积近 似 。 由于 在对 检测数 据进 行分 析过 程 中 ,很难 获取 有效 面积 ,故 此方 法
金属损 失 面积 的表达 式 。 同样 不适 用于 强度 等级较
安全策略和可接受准则, 来确定所采用的腐蚀增长率 。 全寿 命腐 蚀增 长率 预测适 用 于两 次检测 间隔 时
间 较短 的情况 ;半 寿命腐 蚀增 长率 预测 适用 于两 次 检 测 间隔时 间较长 或 只有一 次且距 投产 之 日起 时 间 较 长 的情 况 。依据 腐蚀增 长 速率可 预测 腐蚀缺 陷 的 未 来发 展情况 ,从 而判 定 出计划修 复 时间 和再 检测
内腐蚀直接评价标准

内腐蚀直接评价标准
内腐蚀直接评价标准应包括以下方面:
1.内腐蚀程度:根据腐蚀量大小和深度来评估内腐蚀程度,可以采用
切割法、X射线透视、超声波检测等方法进行评价。
2.腐蚀分布范围:评估内腐蚀在管道、容器等设备内的分布范围,包
括局部腐蚀、范围腐蚀、点腐蚀等,以便制定相应的检修计划。
3.腐蚀速率:评估内腐蚀的速率,包括初始速率和稳态速率,以便制
定定期检查和维护计划。
4.腐蚀质量:评估腐蚀产生的物质对设备的影响,如造成管道、容器
等设备的损坏或漏气等,以便确定应采取的修理措施。
5.安全风险等级:根据内腐蚀的程度、分布范围、速率和质量等因素,评估设备的安全风险等级,以便制定相应的管控措施和预防措施。
埋地管道防腐层检测技术培训教材

埋地钢质管线防腐层检测系统及其应用2009年2月一、埋地管道腐蚀评价与防腐层检测技术1.1、管道腐蚀与防腐层检测金属材料发生腐蚀是一个自发的、不可避免的渐变过程。
管体腐蚀的发生将严重降低管道的剩余强度、承受能力和可靠性、缩短使用寿命,增大运行风险;大大地增加维修费用、缩短维修和更换周期,威胁整个输送系统的安全。
管道在整个服役期间的事故发生率一般遵循浴盆曲线。
在投产初期,管道诸多方面的不足逐一暴露出来,因此事故率较高。
随着运行时间的延续,各方面不断完善,事故率逐步下降至较低的水平,该阶段称之为投产初期,通常为半年到两年。
在其后的一个阶段,事故一直平稳地保持在低水平上,称之为事故平稳期,通常为20-30年。
之后,事故呈上升态势。
我国早期的管道有的已经运行了二三十年,管道已经陆续进入老龄期;而近年大批新建管道正处于幼年期,这两个阶段都是事故高发阶段。
因而管道行业面临的安全形势十分严峻。
对老管道的腐蚀与防护状况评价工作迫在眉睫,在有效检测评价的基础上采取合理的维护措施,保证管道的安全具有重大的经济效益和社会意义。
埋地钢质管道的腐蚀与防护一直是行业的工作重点,管道腐蚀的影响因素众多,作用机理复杂,而且各个影响因素之间又存在着相互影响和制约的关系。
对埋地钢质管道腐蚀与防护状况的检测及评价,涉及多种检测方法、多种检测技术和设备,需要从事这项工程的单位具有很强的技术能力、多方面的技术人员及设备、业主单位也要花费较大的经济投入。
此外,受当前技术发展水平的限制,诸如管体剩余壁厚的检测等项目还要进行开挖检测,除了费用很高之外,势必会对管道造成一定的不良影响。
从当前国内外应用的腐蚀检测评价标准上分析,埋地管道腐蚀检测是以防腐层检测作为工程实施的切入点。
防腐层(又称防护层)是防止和减缓埋地钢质管道腐蚀的重要手段,管体的腐蚀往往是因为该处的防腐层失效,使管体不能受到有效地保护导致的。
尽管防腐层破损点处的管体不一定发生腐蚀,但是可以说,发生管体腐蚀处的防腐层一定失效。
腐蚀直接评价的概念

腐蚀直接评价的概念
腐蚀直接评价是一种衡量材料腐蚀程度的方法。
腐蚀是指,在特定条件下,金属或其他材料表面发生的自然或人为引起的氧化、腐烂、脱落等现象。
在评价腐蚀程度时,通常可以采用多种方法,如计算腐蚀速率、测量腐蚀深度等。
而腐蚀直接评价是一种比较直观的方法,它通过观察材料表面的变化来评价材料腐蚀的情况。
腐蚀直接评价方法包括两种主要方式:视觉评价和触摸评价。
视觉评价是指通过直接观察材料表面的变化来评价腐蚀的程度,例如颜色、光泽、细节等。
触摸评价是指通过触摸材料表面的变化来评价腐蚀的程度,例如表面的平滑度、粗糙度、硬度等。
腐蚀直接评价具有直观、简单易行、快速等优点,因此在工业生产和科学研究中得到了广泛应用。
例如,在汽车生产中,通过视觉和触摸评价来检测车辆表面是否存在腐蚀,并及时采取相应的措施。
在机械制造领域,通过腐蚀直接评价来检测零部件表面的腐蚀情况,以保证零部件的可靠性和耐腐蚀性。
但是,腐蚀直接评价也存在一些局限性。
首先,它只能提供表面腐蚀的信息,对于内部腐蚀难以发现。
其次,由于人眼的主观差异和视力限制,不同人对同一样品的评价结果可能存在差异。
此外,腐蚀直接
评价需要考虑环境因素等多种因素,因此在应用中需要根据具体情况加以分析,不能简单地凭一己之见做出评价。
综上所述,腐蚀直接评价是一种有效的评价材料腐蚀程度的方法,具备直观、简单易行、快速等特点。
但它也存在一些局限性,需要在实际应用中加以注意。
在评价过程中,应根据具体情况综合考虑多种因素,提高评价的准确性和可靠性。