钢管超声波自动探伤控制装置的研制与应用
浅谈超声波检测在钢轨探伤中的应用

浅谈超声波检测在钢轨探伤中的应用发布时间:2022-01-20T07:48:47.121Z 来源:《防护工程》2021年30期作者:杨昊楠[导读] 伤损产生后发展速度快,易造成钢轨折断等重大事故,严重影响铁路运输安全。
因此钢轨探伤检测工作,是保证铁路安全运营的基础工作之一。
呼和浩特铁路局集团公司包头工务段探伤车间内蒙古包头 014040摘要:随着我国经济水平腾飞,铁路发展也逐渐进入新篇章,为国民的出行带来便捷。
作者针对小型钢轨探伤仪在铁路线路维修检测中的应用进行了研究,浅谈了对超声波钢轨探伤技术,及其在铁路线路维修检测中的应用和重要性的一些认识。
关键词:钢轨探伤仪;超声波探伤;钢轨伤损随着我国铁路列车运行不断发展,运营里程不断延伸,运营速度不断提高,线路无缝化技术的大范围应用,钢轨伤损也随之增加。
列车在加速、制动和通过钢轨接头、焊缝、岔区、曲线等地段时,会加重对钢轨的冲击、挤压、摩擦、和弯曲作用;列车不断提速和轴重的增加,特别是在我国北方地区,冬季气温低,昼夜温差大,钢轨内部拉应力大,更是加快了钢轨伤损的发展速度。
在这些应力的作用下,钢轨非常容易产生疲劳性伤损。
伤损产生后发展速度快,易造成钢轨折断等重大事故,严重影响铁路运输安全。
因此钢轨探伤检测工作,是保证铁路安全运营的基础工作之一。
作为一名钢轨探伤工就要熟悉了解钢轨探伤仪器原理结构并熟练使用,全面掌握探伤的基础知识,把所学到的知识与实际情况相结合。
才能做到及时地发现并准确的判断钢轨伤损。
做到在钢轨探伤中不漏检,不误检。
一、钢轨无损检测:超声波探伤在目前钢轨探伤中普遍使用超声波探伤(UT)、涡流探伤(ET)、射线探伤(RT)、磁粉探伤(MT)、渗透探伤(PT)五种方法。
其中,超声波探伤是一种很重要的方法,有不可取代的优势。
超声波本质是一种机械波,靠振动在弹性介质内传播,振动频率一般高于20k赫兹(Hz)。
被检对象材质的不同,其工作频率也不同。
在进行无损检测时,超声波的工作频率为0.2~25MHz,最常用的频段为0.5~10MHz。
高频焊接钢管焊缝的超声波自动检测工艺
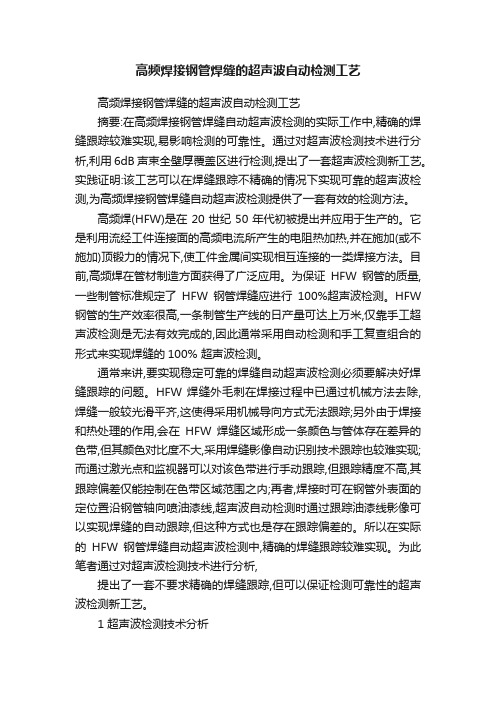
高频焊接钢管焊缝的超声波自动检测工艺高频焊接钢管焊缝的超声波自动检测工艺摘要:在高频焊接钢管焊缝自动超声波检测的实际工作中,精确的焊缝跟踪较难实现,易影响检测的可靠性。
通过对超声波检测技术进行分析,利用6dB声束全壁厚覆盖区进行检测,提出了一套超声波检测新工艺。
实践证明:该工艺可以在焊缝跟踪不精确的情况下实现可靠的超声波检测,为高频焊接钢管焊缝自动超声波检测提供了一套有效的检测方法。
高频焊(HFW)是在20世纪50年代初被提出并应用于生产的。
它是利用流经工件连接面的高频电流所产生的电阻热加热,并在施加(或不施加)顶锻力的情况下,使工件金属间实现相互连接的一类焊接方法。
目前,高频焊在管材制造方面获得了广泛应用。
为保证HFW钢管的质量,一些制管标准规定了HFW钢管焊缝应进行100%超声波检测。
HFW 钢管的生产效率很高,一条制管生产线的日产量可达上万米,仅靠手工超声波检测是无法有效完成的,因此通常采用自动检测和手工复查组合的形式来实现焊缝的100% 超声波检测。
通常来讲,要实现稳定可靠的焊缝自动超声波检测必须要解决好焊缝跟踪的问题。
HFW 焊缝外毛刺在焊接过程中已通过机械方法去除,焊缝一般较光滑平齐,这使得采用机械导向方式无法跟踪;另外由于焊接和热处理的作用,会在HFW焊缝区域形成一条颜色与管体存在差异的色带,但其颜色对比度不大,采用焊缝影像自动识别技术跟踪也较难实现;而通过激光点和监视器可以对该色带进行手动跟踪,但跟踪精度不高,其跟踪偏差仅能控制在色带区域范围之内;再者,焊接时可在钢管外表面的定位置沿钢管轴向喷油漆线,超声波自动检测时通过跟踪油漆线影像可以实现焊缝的自动跟踪,但这种方式也是存在跟踪偏差的。
所以在实际的HFW钢管焊缝自动超声波检测中,精确的焊缝跟踪较难实现。
为此笔者通过对超声波检测技术进行分析,提出了一套不要求精确的焊缝跟踪,但可以保证检测可靠性的超声波检测新工艺。
1 超声波检测技术分析1.1 超声波在钢板试块中的传播分析为了方便研究,先就超声波在钢板试块中的传播情况进行分析。
超声波探伤技术在钢轨探伤领域的应用及其局限性

超声波探伤技术在钢轨探伤领域的应用及其局限性摘要:超声波技术是无损检测技术的关键手段之一,广泛应用于高速列车钢轨焊缝的检测。
钢轨铝热焊超声波探伤采用超声波原理。
探头将声频发送到钢轨内部,当声波遇到钢轨内部组织或缺陷时,接收来自声波反射面的回波,通过对雷达回波的分析,得到了被检钢轨焊缝的损坏情况。
关键词:超声技术;钢轨探伤;应用前言:频率>20kHz的机械波是超声波。
超声波具有专一性、集中性、瞬时速度高等特点。
在不同的媒质界面中,超声波的大部分动能会被表面反射。
超声波具有很强的穿透特性,基本上可以在所有物体中传播。
钢轨焊接质量的好坏直接关系到铁路货运的安全、焊接方法不当造成的焊接缺陷等,需要及时采用无损检测技术进行检验,超声波检测是一种合理的检验方法。
近年来,超声相控阵无损检测技术在工业生产领域得到了很好的应用。
可用于钢轨焊缝检测,提高检测效率。
超声波相控阵光束聚焦具有强大的动能,在基本的超声波检测中可以防止泄漏,使用超声波探伤仪进行钢轨铝热焊探伤时,钢轨中的缺陷会相互影响,产生传输波,进而检测出缺陷,一般采用纵斜波探头进行无损检测,传输的数据信号更容易被探头接受。
一、探伤的原理及常用探伤方法1.1探伤的基本原理(1)单脉冲反射器检测基本原理。
超声波发射到两种不同材料的边界条件,产生反射面,同一探头可用作发送和接收。
(2)单脉冲投影判断的缺点。
根据单脉冲波或通过工件产生的动能转换,单脉冲投影将发送和接收放置在被检零件两侧的探头,以确保探头与样品之间的良好声耦合。
(3)共振法的基本原理。
当被测工件的厚度为超声波半波长的非负整数时,会引起共振,使用相邻共振差来测量工件的厚度。
1.2常用探伤方法现阶段钢轨铝热焊探伤设备主要是数据焊接通用探伤仪。
该设备是一款全智能设备,显示屏大,功能齐全,重量轻。
适用于公共工程系统的钢轨焊接和轨道列车传动轴的探伤。
关键是对接头焊缝进行年检和再诊断,可以区分焊接损伤状态,对已经发生的损伤进行探伤,可以准确定位和定量分析。
超声波检测在铁路铁轨探伤中的应用研究
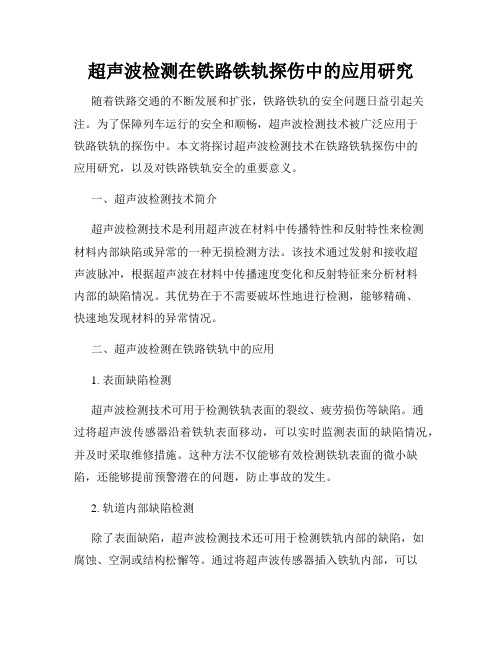
超声波检测在铁路铁轨探伤中的应用研究随着铁路交通的不断发展和扩张,铁路铁轨的安全问题日益引起关注。
为了保障列车运行的安全和顺畅,超声波检测技术被广泛应用于铁路铁轨的探伤中。
本文将探讨超声波检测技术在铁路铁轨探伤中的应用研究,以及对铁路铁轨安全的重要意义。
一、超声波检测技术简介超声波检测技术是利用超声波在材料中传播特性和反射特性来检测材料内部缺陷或异常的一种无损检测方法。
该技术通过发射和接收超声波脉冲,根据超声波在材料中传播速度变化和反射特征来分析材料内部的缺陷情况。
其优势在于不需要破坏性地进行检测,能够精确、快速地发现材料的异常情况。
二、超声波检测在铁路铁轨中的应用1. 表面缺陷检测超声波检测技术可用于检测铁轨表面的裂纹、疲劳损伤等缺陷。
通过将超声波传感器沿着铁轨表面移动,可以实时监测表面的缺陷情况,并及时采取维修措施。
这种方法不仅能够有效检测铁轨表面的微小缺陷,还能够提前预警潜在的问题,防止事故的发生。
2. 轨道内部缺陷检测除了表面缺陷,超声波检测技术还可用于检测铁轨内部的缺陷,如腐蚀、空洞或结构松懈等。
通过将超声波传感器插入铁轨内部,可以检测轨道内部的异常情况,并及时修复或更换受损部分,确保铁轨的完整性和稳定性。
3. 轨距测量超声波检测技术还可用于测量铁路轨道的轨距。
通过发射超声波脉冲并接收其反射信号,根据信号的时间差来计算轨距的大小。
这种方法能够快速、准确地测量轨距,并及时调整轨道的位置,确保列车行驶的平稳性和安全性。
三、超声波检测技术的优势和意义超声波检测技术具有以下几个优势和意义:1. 无损检测:超声波检测技术无需破坏性地进行,能够准确、有效地发现铁路铁轨的异常情况,同时不会对铁轨的正常使用造成干扰。
2. 高精度:超声波检测技术能够对铁路铁轨进行精确的缺陷检测,能够发现微小的问题,防止问题进一步扩大。
3. 实时监测:超声波检测技术能够实时监测铁路铁轨的情况,可以及时采取维修或更换措施,确保铁路运营的安全和顺畅。
超声波检测技术在钢铁冶炼中的应用研究

超声波检测技术在钢铁冶炼中的应用研究随着钢铁产业的发展,冶炼工艺和设备不断更新迭代。
其中,超声波检测技术在钢铁冶炼中的应用,成为了当前研究的焦点之一。
本文将着重介绍超声波检测技术在钢铁冶炼中的应用及其研究进展。
一、超声波检测技术在钢铁冶炼中的应用超声波检测技术是指利用超声波对材料进行无损检测的技术,该技术在钢铁冶炼中有广泛应用。
主要分为以下几个方面。
(一)连铸过程中的应用钢铁连铸工艺中,温度和流动状态是关键的控制参数,超声波检测技术可以用于实时检测铸坯物流状态、气泡大小和数量等,帮助操作人员及时调整工艺参数,保证铸坯质量。
(二)熔铁预测采用超声波检测技术,可以通过测量炉前料层和炉后气泡来预测炉内熔铁温度,提高铁水出铁质量和效率。
(三)铁水净化过程中的应用在铁水净化过程中,超声波检测技术可以识别气泡、杂质和其他不良因素,促进铁水净化,并提高铁水质量。
同时,它还可以检测喷洒的液体流动情况,以确定铁水在净化过程中是否均匀。
二、超声波检测技术在钢铁冶炼中的研究进展随着钢铁产业的不断发展,人们对超声波检测技术在钢铁冶炼中的应用不断深入研究。
下面介绍一下近期的研究进展。
(一)超声波相控阵成像技术超声波相控阵成像技术是一种高精度的无损检测技术,可用于测量材料的几何参数、皮层厚度、裂纹等缺陷。
在钢铁冶炼中,应用超声波相控阵成像技术,可以直观地观察炉内铁水流动状态、气泡情况等,为操作人员提供重要参考。
(二)多参数超声波探头开发针对钢铁冶炼中多种不同的材料和工艺参数,研究人员正在开发多参数超声波探头,以适应更多的应用场景。
例如,针对炉前料层测量,可以开发具有高分辨率和抗干扰能力的超声波探头。
(三)基于神经网络的缺陷检测模型随着人工智能技术的不断发展,研究人员开始将神经网络算法应用于超声波检测中。
根据不同的检测场景,采用不同的神经网络结构,在钢铁冶炼中实现高精度的缺陷检测。
三、结语总之,超声波检测技术在钢铁冶炼中具有重要的应用价值,可以提高钢铁生产的效率和产品质量,降低生产成本。
无缝钢管超声波探伤检验方法
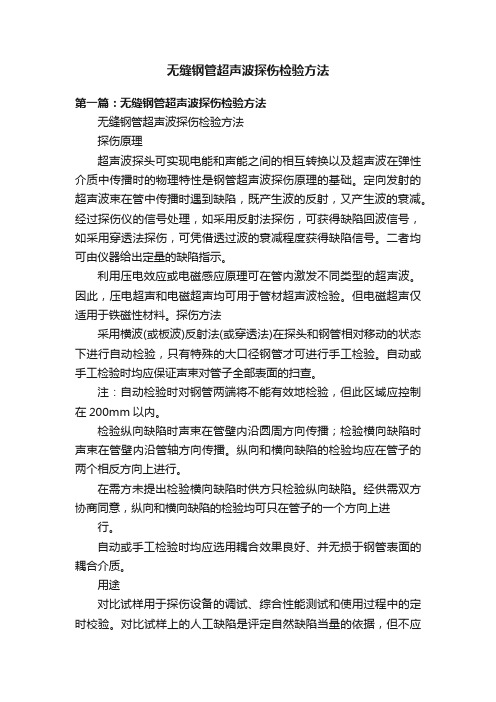
无缝钢管超声波探伤检验方法第一篇:无缝钢管超声波探伤检验方法无缝钢管超声波探伤检验方法探伤原理超声波探头可实现电能和声能之间的相互转换以及超声波在弹性介质中传播时的物理特性是钢管超声波探伤原理的基础。
定向发射的超声波束在管中传播时遇到缺陷,既产生波的反射,又产生波的衰减。
经过探伤仪的信号处理,如采用反射法探伤,可获得缺陷回波信号,如采用穿透法探伤,可凭借透过波的衰减程度获得缺陷信号。
二者均可由仪器给出定量的缺陷指示。
利用压电效应或电磁感应原理可在管内激发不同类型的超声波。
因此,压电超声和电磁超声均可用于管材超声波检验。
但电磁超声仅适用于铁磁性材料。
探伤方法采用横波(或板波)反射法(或穿透法)在探头和钢管相对移动的状态下进行自动检验,只有特殊的大口径钢管才可进行手工检验。
自动或手工检验时均应保证声束对管子全部表面的扫查。
注:自动检验时对钢管两端将不能有效地检验,但此区域应控制在200mm以内。
检验纵向缺陷时声束在管壁内沿圆周方向传播;检验横向缺陷时声束在管壁内沿管轴方向传播。
纵向和横向缺陷的检验均应在管子的两个相反方向上进行。
在需方未提出检验横向缺陷时供方只检验纵向缺陷。
经供需双方协商同意,纵向和横向缺陷的检验均可只在管子的一个方向上进行。
自动或手工检验时均应选用耦合效果良好、并无损于钢管表面的耦合介质。
用途对比试样用于探伤设备的调试、综合性能测试和使用过程中的定时校验。
对比试样上的人工缺陷是评定自然缺陷当量的依据,但不应理解为被检出的自然缺陷与人工缺陷的信号幅度相等时二者的尺寸必然相等。
材料制作对比试样用钢管与被检验钢管应具有相同的名义尺寸并具有相似的化学成分、表面状况、热处理状态和声学性能。
制作对比试样用钢管上不得有影响探伤设备综合性能测试的自然缺陷。
长度对比试样的长度应满足探伤方法和探伤设备的要求。
人工缺陷形状检验纵向缺陷和横向缺陷所用的人工缺陷应分别为平行于管轴的纵向槽口和垂直于管轴的横向槽口,其断面形状均可为矩形或V形(见图1和图2)。
超声相控阵的钢轨探伤装置研究

超声相控阵的钢轨探伤装置研究摘要:我国铁路正在向高速、重载的方向发展。
超期服役的钢轨数量很大,线路上的钢轨在承担繁重的运输任务中,不可避免要产生各种损伤。
因此,进行钢轨内部的探伤可以及时发现各种钢轨伤损,保证线路质量,确保铁路运输安全。
关键词:探伤,超声相控阵,检测工艺1.概述当前国内外钢轨超声波探伤主要有两种方式:一种是高速钢轨探伤车,另一种是手推式超声波探伤仪。
然而这两种钢轨探伤方式都是采用多通道即多个检测方向上单探头进行探伤,因而结构笨重复杂,多方向单探头虽可实现多声束同时探伤,但角度调节不灵活,无法进行实时扫描,对钢轨内部不能详细检查,同时单探头探伤声束不能精细可调,因而检测可靠性差。
基于以上现状,研发超声相控阵的钢轨探伤装置,能够满足现场探伤需求,同时建立向导式的检测工艺流程,降低人为因素对检测结果的影响。
1.总体设计方案(一)应用技术1. 超声相控阵波束控制技术超声波相控阵是指按照一定的规则和时序激发一组探头晶片,通过调整激发晶片的序列、数量、时间来控制波束的形状、轴线偏转角度及焦点位置等参数的超声波电子扫查方式。
超声波相控阵探头由按照一定序列排列的多个晶片组成,仪器通过调节单个晶片激发时间控制超声波声束形状、轴线偏转角和焦点位置等参数,它有2个不同以往超声波探头的特点,多晶片阵列和电子控制超声场特性。
超声相控阵检测技术是一种特殊的超声检测技术,它利用精密复杂的相控阵和功能强大的软件来控制超声波声束,使其覆盖被检测材料,并生成修正的材料内部结构图像。
相控阵检测技术不仅可探查缺陷,而且在检测压力容器、管路的腐蚀和绘制腐蚀图等方面也有其独特的应用。
超声相控阵波束控制技术,通过控制系统分别调整各个阵元发射信号的参数,使得各阵元发出的超声子波束在空间干涉叠加增强,形成阵列发射声束的指向性及聚焦偏转等效果,以适应钢轨探伤的要求。
1.钢轨探伤检测工艺流程向导化技术钢轨探伤主要检查钢轨中的材质缺陷和制作缺陷,如夹杂、疏松、气孔、白点和各种表面裂纹等。
超声波相控阵技术在管道检测中的应用研究
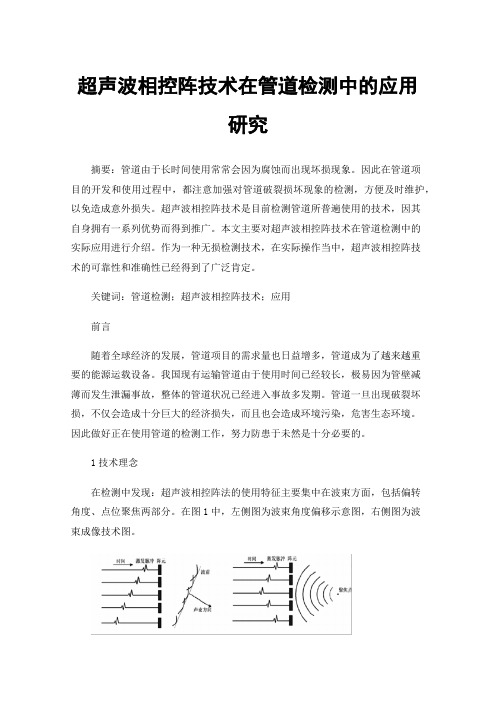
超声波相控阵技术在管道检测中的应用研究摘要:管道由于长时间使用常常会因为腐蚀而出现坏损现象。
因此在管道项目的开发和使用过程中,都注意加强对管道破裂损坏现象的检测,方便及时维护,以免造成意外损失。
超声波相控阵技术是目前检测管道所普遍使用的技术,因其自身拥有一系列优势而得到推广。
本文主要对超声波相控阵技术在管道检测中的实际应用进行介绍。
作为一种无损检测技术,在实际操作当中,超声波相控阵技术的可靠性和准确性已经得到了广泛肯定。
关键词:管道检测;超声波相控阵技术;应用前言随着全球经济的发展,管道项目的需求量也日益增多,管道成为了越来越重要的能源运载设备。
我国现有运输管道由于使用时间已经较长,极易因为管壁减薄而发生泄漏事故,整体的管道状况已经进入事故多发期。
管道一旦出现破裂坏损,不仅会造成十分巨大的经济损失,而且也会造成环境污染,危害生态环境。
因此做好正在使用管道的检测工作,努力防患于未然是十分必要的。
1技术理念在检测中发现:超声波相控阵法的使用特征主要集中在波束方面,包括偏转角度、点位聚焦两部分。
在图1中,左侧图为波束角度偏移示意图,右侧图为波束成像技术图。
图 1 波束角度偏移、聚焦成像示意图2在特种设备性能测定中超声2.1探头选用2.1.1晶片阵列晶片阵列含有多种类型,如图2所示。
现阶段在特种设备性能检测工作中,使用频数较高的晶片阵列类型为线性。
在必要检测时,使用的双线性类型,顺应装置的收发检测需求。
图 2 各类阵列示意图2.1.2频率频率值大小对于检测结果具有直接影响,在频率值较高时,检测结果的灵敏性、影像清晰度相对较高,更有利于检测分析。
然而,频率参数较高时,相对应的衰减性能较高,对检测形成了不利作用。
一般情况下,如果特种设备在检测时,以碳钢焊缝为检测方向,适用的检测频率区间为[2.5,5]MHz。
针对焊缝壁较为轻薄的情况,在检测时频率选择7.5MHz。
对于不锈钢材质的焊缝,在检测时探头可选频率区间为[1,2.5]MHz。