发动机叶尖间隙影像测量系统的设计
航空发动机叶片测量夹具重构设计

开发研究航空发动机叶片测量夹具重构设计智绪旺(中国航发南方工业有限公司,湖南株洲412002)摘要:航空发动机叶片的复杂曲面测量需要专用特性夹具,夹具的设计应更加多元化、智能化。
提出利用计算机辅助软件技术基于TRIZ理论完成叶片测量夹具的重构设计思想,在构设软件系统模型后对主要功能模块进行介绍,并利用软件系统完成叶片测量夹具的重构设计。
关键词:航空发动机叶片;夹具;重构1CAI软件系统设计关键技术1.1软件开发架构本文所建软件系统体系架构自下而上分别为数据层、业务层、应用层。
数据层可与数据库联通交互,实现数据实时访问;业务层接客户侧指令启动逻辑操作,完成数据库操作;应用层主要提供应用信息以及方法服务,制定应用程序访问路径,可在该层渲染业务层的数据库操作结果。
1.2软件系统单元软件系统划分信息单元、问题解答单元、辅助功能单元。
其中,信息单元可提供航空发动机叶片参数指标、测量夹具信息,全维度解析待设计对象。
问题解答单元涵盖多个模块,用于解决技术冲突、技术效应,化解物理设计冲突。
辅助功能单元可强化软件系统功能,配置知识数据库及系统智能辅助模块。
1.3软件数据库本文对航空发动机叶片测量夹具的重构设计,意图利用创新性设计软件来提升重构设计效率,软件系统需要强大的卿库支撑,其中包括^业领域知识、先进设计理念等内容,因此数据容量惊人,为提升数据利用率,需要提升用户提取调用数据的效率。
TRIZ理论下,数据库的建立和应用更加直观便捷。
在数据库设计中,先行明确各类属性及对应属性的数据类型,加强属性表间关联。
选择使用SQL Server关系型数据库作为本文数据库系统,使用C#编程语言面向对象进行开发,可保护封装数据。
2CAI创新设计系统模型及主要功能模块2.1系统模型本文的系统模型如图1所示。
2.2系统主要功能模块(1)冲突模块。
用户登录系统后,需要点击技术冲突界面确定矛盾冲突数据,完成技术冲突的程式化描述,如出现储加系统组件(定位元件)的(适用性)参数将导致另一系统组件(测量夹具)的复杂化”语句描述,相关技术冲突参数作者简介:智绪旺(1988-),男,山东荷泽人,助理工程艸,研究方向:航空发动机用零件模具、夹具、测具等设计及工艺生产过程。
航空发动机叶尖间隙测量技术

航空发动机叶尖间隙测量技术
张娜;黄春峰
【期刊名称】《航空制造技术》
【年(卷),期】2010(000)013
【摘要】@@ 虽然可用计算机模型来预测压气机和涡轮的叶尖间隙,但这种预测必须由试验数据来验证和细调.所以,在一台航空发动机的研制过程中,叶尖间隙是一个基本的测量参数,同时也是发动机在运转过程中主动叶尖间隙控制、健康管理和故障诊断的一个重要组成部分.
【总页数】5页(P41-45)
【作者】张娜;黄春峰
【作者单位】中国燃气涡轮研究院;中国燃气涡轮研究院
【正文语种】中文
【相关文献】
1.航空发动机叶尖间隙数学模型的建立与验证 [J], 陈研;吕天波;张生;张镭
2.航空发动机转子叶尖间隙及同心度变化规律研究 [J], 张龙;韩鹏卓;刘忠奎;周笑阳
3.叶尖间隙对航空发动机性能的影响和测量技术 [J], 陈炳贻
4.航空发动机叶尖间隙影像测量技术研究 [J], 郑臣;朱目成
5.基于叶尖间隙的航空发动机转子运动特征提取技术 [J], 李杰;郭光辉;魏之平;熊兵
因版权原因,仅展示原文概要,查看原文内容请购买。
航空发动机叶片的无损检测毕业设计说明书
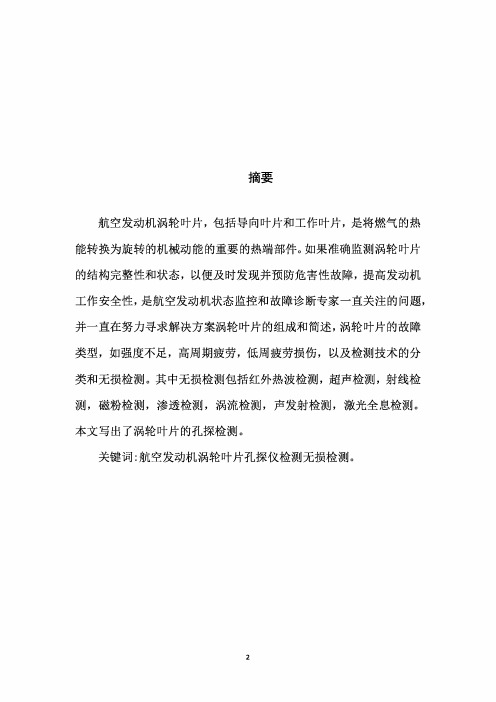
摘要航空发动机涡轮叶片,包括导向叶片和工作叶片,是将燃气的热能转换为旋转的机械动能的重要的热端部件。
如果准确监测涡轮叶片的结构完整性和状态,以便及时发现并预防危害性故障,提高发动机工作安全性,是航空发动机状态监控和故障诊断专家一直关注的问题,并一直在努力寻求解决方案涡轮叶片的组成和简述,涡轮叶片的故障类型,如强度不足,高周期疲劳,低周疲劳损伤,以及检测技术的分类和无损检测。
其中无损检测包括红外热波检测,超声检测,射线检测,磁粉检测,渗透检测,涡流检测,声发射检测,激光全息检测。
本文写出了涡轮叶片的孔探检测。
关键词:航空发动机涡轮叶片孔探仪检测无损检测。
目录摘要 (2)绪论 (1)第一章涡轮叶片的简述 (2)1.1涡轮的工作叶片 (2)1.2导向叶片 (2)第二章故障类型 (3)2.1强度不足及其故障模式 (3)2.2高周期疲劳损伤及其故障模式 (3)2.3低周疲劳损伤及故阵模式 (3)2.4涡轮叶片的常见故障及概率 (3)2.5注意事项 (5)第三章机上孔探检测 (6)3.1涡轮叶片的机上孔探检查 (6)3.2涡轮叶片的不同部位孔探检查 (6)3.3孔探技术的发展和实际应用的需求 (7)3.4修理车间检测前的清洗预处理 (7)3.5叶片完整性检查 (8)3.6探孔注意事项 (8)第四章涡轮叶片孔探案例分析 (9)4.1高压涡轮叶片断裂 (9)4.2典型案例分析 (10)4.3叶片断裂的原因 (11)4.4叶片修理与孔探检测 (13)4.5总结 (14)参考资料 (15)致谢 (16)航空发动机涡轮叶片无损检测技术绪论航空发动机涡轮叶片,包括导向叶片和工作叶片,是将燃气的热能转换为旋转的机械动能的重要的热端部件。
基于提高推重比和单位推力的需要,涡轮前燃气温度日益提高,目前国外新型的航空燃气涡轮发动机涡轮前的温度已达到1700K以上。
涡轮叶片在高压腐蚀性燃气的神击下高速旋转,除承受巨大的拉应力外,还承受频率、幅值变化都很大的交变拉应力和扭转应力,此外还存在高温氧化、热腐蚀和磨损问题。
涡轮转子H形叶片叶尖间隙测量

涡轮转子H形叶片叶尖间隙测量 陈洪敏;韩伟;熊兵;郭光辉 【摘 要】叶尖间隙是燃气轮机中的一个重要性能参数和安全监测参数。现代燃气轮机中采用H形凹腔冷却涡轮叶片,该叶片具有单叶片双间隙的特点。利用电容式叶尖间隙测量系统,通过改进算法,实现了H形叶片的叶尖间隙测量,并成功应用于H形叶片涡轮级性能试验。试验录取了三种不同设计间隙下的实际叶尖间隙变化数据,分析了叶尖间隙与涡轮性能之间的关系,并对试验中的转子异常运动进行了成功监测。%Tip clearance is an important parameter of performance and safety monitor in gas turbine. The H-form blade which is characterized with two tips has been used in modern gas turbines. Software that can calculate tip clearance of H-form blade was developed based on hardware of the capacitance tip clearance measure system, and had a good impression in a turbine experiment. Tip clearance data of three different designs were collected in experiments. The relationship between turbine performance and tip clearance was analyzed, and an abnormal state of turbine was monitored successfully in the experiment.
- 1、下载文档前请自行甄别文档内容的完整性,平台不提供额外的编辑、内容补充、找答案等附加服务。
- 2、"仅部分预览"的文档,不可在线预览部分如存在完整性等问题,可反馈申请退款(可完整预览的文档不适用该条件!)。
- 3、如文档侵犯您的权益,请联系客服反馈,我们会尽快为您处理(人工客服工作时间:9:00-18:30)。
第33卷第4期2012年7月应 用 光 学Journal of Applied OpticsVol.33No.4Jul.2012收稿日期:2011-09-15; 修回日期:2011-11-10基金项目:四川省科技支撑计划项目(2012GZ0022)作者简介:范小虎(1988-),男,湖北黄冈人,硕士研究生,主要从事光电成像与检测技术研究.E-mail:potianxing2007@163.com文章编号:1002-2082(2012)04-0743-04发动机叶尖间隙影像测量系统的设计范小虎,朱目成,聂诗良(西南科技大学制造过程测试技术教育部重点实验室,四川绵阳621010)摘 要:发动机转子叶片叶尖到开半机匣内壁径向距离是衡量发动机质量是否合格的一个重要指标,其值的大小对发动机的高效安全运行至关重要。
利用立体视觉原理、自动聚焦技术和边缘检测算法,设计了一套发动机装配过程中叶尖间隙静态测量装置。
该测量装置实现了对发动机叶尖间隙的非接触测量,且操作简单,测量精度高。
实验结果表明该套装置测量精度达到20μm。
关键词:叶尖间隙;立体视觉;自动聚焦;Canny中图分类号:TN207;TH432.1 文献标志码:A doi:10.5768/JAO201233.0403002Image measuring system of engine tip clearanceFAN Xiao-hu,ZHU Mu-cheng,NIE Shi-liang(Key Laboratory of Testing Technology for Manufacturing Process,Ministry of Education,Southwest University of Science and Technology,Mianyang 621010,China)Abstract:The gap from the engine rotor blade tip to the open half machine magazine is an im-portant parameter that inspects whether the engine is qualified.And its value is of prime im-portance to the engine on high efficient and safe operation.Based on stereo vision principle,automatic focus technology,edge detection algorithm,this paper designed a blade tip clearancemeasurement device used in the process of engine assembling.This device realized the non-con-tact measurement to aero-engine rip clearance with simple operation and high-accuracy meas-urement.Experiment result shows that the device accuracy can reach to 20μm.Key words:tip clearance;stereoscopic vision;auto-focusing;Canny引言研究表明[1]发动机叶尖间隙值越小,压气机工作效率就越高,所需的耗油量就越少。
但叶尖间隙设计过小,或转子叶片安装过程中偏离预定位置。
发动机工作时,会造成叶片与机匣内壁的摩擦与碰撞,影响发动机的寿命。
目前国内外对发动机的叶尖间隙的动态测量研究比较多,但对其在装配过程中的叶尖间隙的静态测量还比较少。
国内大多还采用塞尺法测量,在欧美国家采取的测量方法[2]有激光法、光纤法等。
而采用图像方式测量,则很少。
在国内清华大学提出的辐射成像测量法[1]还处在研究阶段。
本文提出了叶尖间隙光学影像测量方法,并展开可行性的实验研究。
1 叶尖间隙影像测量系统的原理发动机叶尖间隙影像测量系统[3-4]如图1所示。
其工作原理:当工控机发出开始工作命令,照应用光学 2012,33(4) 范小虎,等:发动机叶尖间隙影像测量系统的设计明系统将均匀、柔和的光照射在被测物体上,CCD摄像机开始对被测物体成像,图像采集卡采集图像信号,并送给上位机。
上位机通过调用自动聚焦算法、边缘检测等算法,对图像进行分析与处理。
根据分析的结果,发出控制命令给运动控制卡,运动控制卡根据控制命令,调整摄像机的位置并校正焦距。
对焦完成后,找出二维图像和三维图形间的函数关系,然后建立发动机叶尖间隙的数学模型,并精确计算出其值的大小。
图1 系统原理图Fig.1 System schematic diagram2 成像系统硬件组成本设计中的成像装置采用LED环形可调光源,XC-75/75CE相机,其CCD尺寸为6.45mm×4.84mm,有效像素为768×494,可知一个CCD像元的尺寸为6.45/768=8.34μm,并配以20倍变焦镜头VS-16TC-XL,使图像分辨率更高。
设计中采用微视V510图像采集卡,具有CPI接口,10bit A/D采样精度,最大采集分辨率:768×576。
则CPI总线一秒传输数据为768×494×25×10/8Mb=11.3Mb。
运动控制卡采用雷赛三轴DMC1380并配以XYZ轴滑台,可控制3个电机转动。
2.1 成像原理立体视觉原理[5]是基于针孔相机光心与成像点连线的反向延长线必经过发光光点这一事实,如有两条这样的反向延长线,则空间中的一点,就可以被唯一确定。
如图2所示,p为空间中的一实点,P1′和P2′分别为相机c1与c2上的成像点。
o1和o2分别为相机c1与c2的光心。
P′为o1与P1′反向延长线上的一点,从图2中可看出P′明显不是实际的实点P,而是在o1P1′和o2P2′两射线的交点上,因此可以利用双目视觉原理定位空间物体表面的一点。
图2 双目视觉工作原理图Fig.2 Operating principle of binocular vision CCD摄像机成的是二维的图像,实测间隙是三维的物理模型,因此要准确测量发动机的叶尖间隙就必须建立二维图像与三维图像关系。
若M=[X,Y,Z]T为空间物体表面中的一点,M1=[u1,v1]T和M2=[u2,v2]T是N的两个像点。
M1=[u1,v1,1]T和M2=[u2,v2,1]T分别是M1和M2的齐次坐标,M=[X,Y,Z,1]T是M的齐次坐标。
两摄像机标定后获得投影矩阵P1和P2。
根据针孔相机模型[6]可推出关于X、Y、Z的4个线性方程[6]:u1p131-p111u1p132-p112u1p133-p113v1p131-p121u1p132-p122u1p133-p123u2p231-p211u1p232-p212u1p233-p213v2p231-p221u1p232-p222u1p233-p22熿燀燄燅3XY熿燀燄燅Z=p114-u1p134p124-u1p134p234-u2p234p244-v2p23熿燀燄燅4(1)(1)式中每个方程都表示一个平面,前两个方程联立为摄像机C1的一条视线空间直线方程,后两个方程为摄像机C2的一条视线空间直线方程。
若两条视线相交,则(1)式中只有3个独立方程,可以得到唯一解;若视线不相交,则上式变为超定方程组,则需用最小二乘法解出点M。
3 软件算法研究设计中的所有软件程序都在VC++6.0环境中完成,主要包括图像预处理程序、自动聚焦程序、边缘检测程序和、测量计算程序等。
3.1 自动聚焦算法相机标定[7-8]后,本设计采用二叉搜索法和爬山坡法[9-10]相结合,相比传统的自动聚焦效果更好。
其聚焦过程分为三部分:粗对焦、细对焦和监控模式。
粗对焦找到焦点大致范围;细对焦进行微调。
一次对焦已经完成,启动视频监控模式,为了判断是否需要重新对焦,用一个函数[10]FC来评估对焦量。
·447·应用光学 2012,33(4) 范小虎,等:发动机叶尖间隙影像测量系统的设计FC=|Ft(0)-Ft(n)|/Ft(0)(2)(2)式中,Ft(i)是进入监控模式后第i帧图像的对焦量,Ft(n)是最近n帧图像对焦量的平均值。
T1和T2为两个预设的阈值,并且T1>T2。
如果T2<FC<T1,说明图像只是稍有偏焦,只需重新进行细对焦;如果FC>T1,就需再次进行粗对焦。
3.2 Canny边缘检测算法应用较多的边缘检测算子[11-12]有Laplacian、Prewitt、Sobel、Canny等。
根据不同的应用场合选择不同的边缘检测算子对图像进行处理。
本系统要求所采取的算法必须准确定位图像边缘,且具有高信噪比。
Canny的目标是找到一个最优的边缘检测算法,最优边缘检测的含义是:1)最优检测,信噪比高;2)最优定位准则;3)检测点与边缘点一一对应。
图3是一副未经边缘检测算子处理的发动机叶片图像,运用Canny算子对其进行处理得到图4。
3.3 叶尖间隙测量算法利用Canny算子可生成两幅二维离散的边缘图像。
根据(2)式,被测物体表面上的点都能被两幅离散图像中对应的点唯一表示出来。
取被测模型一截面,平移后得到图5,图5显示的是截面中的一个转子叶片。
当摄像机在近距离小视场范围内成像,可认为图5中的两边界曲线中的一小段近似为直线段。
对每个小线段进行拟合可求出其数学表达式,如(3)式。
已知发动机的机匣内壁截面为圆形,直径大小为R。
图5 叶尖间隙示意图Fig.5 Schematic of tip clearancefi(x,y)=kix+bix2+y2=R烅烄烆2(3)式中:fi(x,y)=kix+bi为曲线段LAB拟合直线段。
Ci(x,y)为圆O上的动点。
Ai与Bi为曲线LAB上的动点。
从而可知圆上动点Ci到动直线段LAB最小距离公式,如(4)式:d=min|kix-y+bi|1+k2槡{}i(i=1,2,3,n)(4)根据上述理论,对某型发动机模型的叶尖间隙进行仿真实验得出结果,如表1所示。
用影像法测量发动机转子不同级上不同叶片,从表1可知该方法测量结果精确到μm级。
影像测量值与实际值之差的绝对值小于20μm,其差值比较小,保证了影像测量结果的准确性。
表1 叶尖间隙测量结果(单位:μm)Table 1 Tip clearance measurement results实际值影像测量误差实际值影像测量误差300 292-8 380 374-6320 330 10 400 386-14340 352 12 420 426 6360 368 8 440 454 14·547·应用光学 2012,33(4) 范小虎,等:发动机叶尖间隙影像测量系统的设计5 结论在实验条件下,研究了影像测量系统的测量原理,并建立了相关数学模型。