热熔钻孔/攻丝技术原理及其应用
热熔器的原理

热熔器的原理热熔器是一种利用高温将固体物质熔化的装置。
它主要由加热元件、熔化腔室和控制系统等组成,能够将固体物质快速熔化成流动状物质,用于各种加工和制造过程。
热熔器的工作原理可以简单描述为:通过加热元件向熔化腔室提供热能,使腔室的温度升高到熔点以上,从而将固态物质熔化成流动态。
具体来说,热熔器的工作原理可以分为以下几个步骤:首先,将需要熔化的固体物质放入熔化腔室中。
可以根据需要调整腔室的容量,以适应不同尺寸和重量的物质。
然后,通过加热元件向熔化腔室供应热能。
热熔器常用的加热元件有加热电线、加热棒或加热板等。
加热元件可以通过电能、燃气或其他能源提供所需的热量。
加热元件与熔化腔室之间通常有热介质(如空气、油或水等)进行传热或热量传导。
随着加热元件向熔化腔室供热,腔室的温度逐渐升高。
当温度达到熔点时,固态物质开始熔化成流动状物质。
此时,可以通过控制系统监测和调整腔室的温度,以保持在理想的熔化温度范围内。
一旦固态物质完全熔化成流动状物质,熔化腔室中的物质可以通过熔化腔室下方的出口进行排放或供应到生产线或其他加工设备中。
在这个过程中,请注意熔化腔室的密封性,以避免热能损失或流动态物质外泄。
热熔器的工作涉及到许多因素,如加热元件的功率、熔化腔室的设计、传热介质的选择以及控制系统的精度等。
合理地设计这些参数可以提高热熔器的熔化效率和加工质量。
总结起来,热熔器的工作原理是通过加热元件向熔化腔室供应热能,使固态物质熔化成流动态物质。
通过控制系统调整熔化腔室的温度,可以实现精确的控制。
热熔器广泛应用于各种加工和制造过程中,提高了生产效率和产品质量。
钻孔工作原理

钻孔工作原理
钻孔工作原理是指利用钻头对地面或其他硬质物体进行的穿孔加工。
钻孔是一种常用的金属加工方法,其原理基于旋转和切削力。
首先,钻孔需要使用一个旋转的工具,也就是钻头。
钻头多为金属材料制成,具有尖锐的尖端,通常有螺旋状的沟槽。
当钻头以一定的速度旋转时,沟槽会形成切削面,将工件上的材料削除。
这种削除过程需要施加一定的切削力。
切削力是通过将钻头与工件之间施加压力来产生的。
这个力会导致钻头将材料从工件上削除或剥离下来。
钻孔的深度和孔径可以通过调整钻头的大小和加工时间来控制。
较大的钻头可以用于加工大孔径,而较小的钻头则适用于加工小孔径。
钻孔的材料通常为金属,因为金属具有硬度较高的特性,可以保证钻孔的质量和精度。
然而,钻孔也可以用于非金属材料,如木材、塑料和石材等。
总的来说,钻孔的工作原理是通过旋转的钻头和施加的切削力,将工件上的材料削除,实现穿孔加工的目的。
通过控制钻头的尺寸和深度,可以满足不同加工要求。
热熔机工作原理

热熔机工作原理
热熔机是一种用来融化和熔接塑料的设备,其工作原理是利用热量将固态的塑料材料加热到熔融状态,然后将熔融的塑料材料注入模具中,待冷却后形成所需的塑料制品。
热熔机主要由加热系统和压力系统两部分组成。
加热系统通常采用电加热方式,将电能转化为热能,通过加热元件将热量传递给塑料材料,使其快速升温。
常见的加热元件有加热棒和加热板,它们分别负责加热塑料材料的两个侧面或表面。
在加热的同时,热熔机还通过压力系统提供一定的压力,将热熔的塑料材料推入模具中。
压力系统通常由液压缸或气动缸组成,通过控制液体或气体的压力来调节熔融塑料的注入速度和压力大小。
压力大小的调节可以影响塑料制品的密度和强度。
在注入模具之后,热熔机会立即停止加热,让注入模具中的塑料材料自然冷却,形成所需的塑料制品。
冷却时间的长短取决于塑料材料的种类和注入模具的尺寸,通常需要几秒钟到几分钟不等。
总的来说,热熔机利用热量将塑料材料加热到熔融状态,通过压力将熔融的塑料材料注入模具中,并在适当的时间内冷却成型,实现塑料制品的加工和生产。
热熔器工作原理

热熔器工作原理
热熔器是一种热力学设备,通常用于将固体物质加热至液态态,并用于各种制程中,例如塑料加工、金属熔化和玻璃工艺等。
热熔器的工作原理可以概括为以下几个步骤:
1. 加热源:热熔器通常有一个加热源,用于提供足够的热能。
这个加热源可以是电加热器、燃气燃烧器或其他能源。
2. 加热器:热熔器内部通常有一个加热器,用于将加热源提供的热能传递给待熔化的物质。
加热器可以是电加热线圈、加热管或加热板等。
3. 热传递:当加热器加热时,热能会通过传导、对流或辐射等方式传递给待熔化的物质。
传递的热能会提高物质的温度,直到达到熔化点。
4. 熔化:一旦物质达到了熔化点,它的固态结构会开始解体,变成液体。
熔化过程中,物质分子之间的键被打破,形成自由流动的液体颗粒。
5. 控制温度:为了保持物质在液态状态,热熔器通常有一种温度控制系统,可以监测和调整加热源的热输出,以控制物质的温度在所需范围内。
值得注意的是,不同的物质有不同的熔化点和熔化过程,因此热熔器的设计和工作参数也可能会因物质的不同而有所不同。
另外,对于一些特殊的应用中,热熔器可能会有其他的特殊构造或附加的控制系统,以适应特殊要求。
电缆热熔接技术
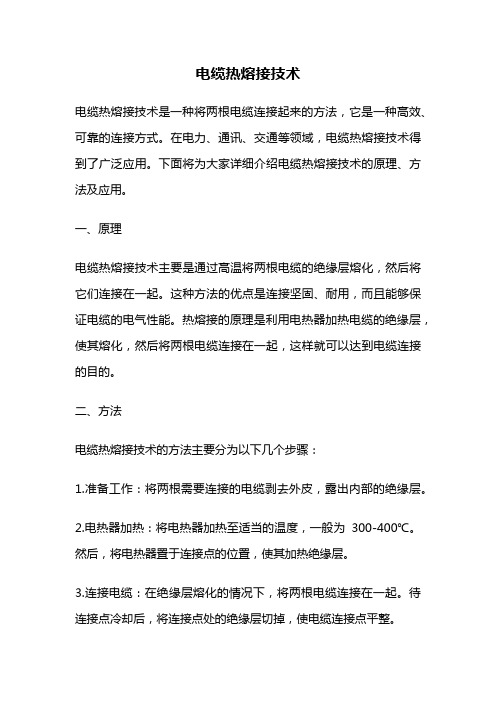
电缆热熔接技术
电缆热熔接技术是一种将两根电缆连接起来的方法,它是一种高效、可靠的连接方式。
在电力、通讯、交通等领域,电缆热熔接技术得到了广泛应用。
下面将为大家详细介绍电缆热熔接技术的原理、方法及应用。
一、原理
电缆热熔接技术主要是通过高温将两根电缆的绝缘层熔化,然后将它们连接在一起。
这种方法的优点是连接坚固、耐用,而且能够保证电缆的电气性能。
热熔接的原理是利用电热器加热电缆的绝缘层,使其熔化,然后将两根电缆连接在一起,这样就可以达到电缆连接的目的。
二、方法
电缆热熔接技术的方法主要分为以下几个步骤:
1.准备工作:将两根需要连接的电缆剥去外皮,露出内部的绝缘层。
2.电热器加热:将电热器加热至适当的温度,一般为300-400℃。
然后,将电热器置于连接点的位置,使其加热绝缘层。
3.连接电缆:在绝缘层熔化的情况下,将两根电缆连接在一起。
待连接点冷却后,将连接点处的绝缘层切掉,使电缆连接点平整。
4.检测:连接完成后,需要对连接点进行检测,以确保连接的质量。
主要检测电缆的电气性能和机械性能。
三、应用
电缆热熔接技术在电力、通讯、交通等领域得到广泛应用。
在电力系统中,电缆热熔接技术主要用于高压电缆的连接,如输电线路、变电站、发电厂等。
在通讯领域,电缆热熔接技术用于光缆的连接,如光纤通讯线路、光缆终端连接等。
在交通领域,电缆热熔接技术主要用于铁路信号、通讯、电力线路的连接。
电缆热熔接技术是一种高效、可靠的电缆连接方式。
在各个领域得到广泛应用,它能够保证电缆连接的质量,提高了电缆的可靠性和安全性。
热熔自攻螺钉连接技术

热熔自攻螺钉连接技术哎,说起热熔自攻螺钉连接技术,这可真是个让人又爱又恨的玩意儿。
爱它,因为它能快速、方便地把各种材料连接起来,恨它,因为一旦操作不当,那可真是让人头疼。
不过,今天咱们就聊聊这个技术,看看它到底是怎么一回事。
首先,咱们得明白,热熔自攻螺钉连接技术,顾名思义,就是用一种特殊的螺钉,通过加热的方式,让螺钉的尖端熔化,然后快速插入材料中,形成连接。
这种技术在建筑、家具制造等行业里特别受欢迎,因为它既省时又省力。
记得有一次,我在家里搞装修,需要把一块木板固定在墙上。
那时候,我手头正好有一盒热熔自攻螺钉,心想这下可省事了。
我拿起电钻,装上螺钉,对着木板就是一通操作。
结果,可能是因为我太心急,螺钉没完全熔化就急着往里钻,结果螺钉卡在了木板里,怎么也拔不出来。
我当时那个急啊,满头大汗,最后还是请了个老师傅来帮忙才搞定。
从那以后,我就学乖了,每次用热熔自攻螺钉之前,都会仔细检查螺钉是否完全熔化,确保操作无误。
而且,我发现,这种技术其实挺讲究技巧的。
比如,你得控制好电钻的速度,不能太快也不能太慢,太快了螺钉容易断,太慢了螺钉又熔化不充分。
还有一次,我在帮朋友组装一个书架,用的就是热熔自攻螺钉。
这次我可是小心翼翼,每一步都按照说明书来。
结果,书架组装得既结实又美观,朋友直夸我手艺好。
我心里那个得意啊,心想这热熔自攻螺钉连接技术,还真是个好东西。
不过,话说回来,虽然热熔自攻螺钉连接技术方便,但也不是万能的。
有些材料,比如金属或者特别硬的塑料,用这种技术就不太合适。
这时候,就得用其他方法,比如焊接或者用专用的螺丝和螺母。
总之,热熔自攻螺钉连接技术,就像生活中的很多工具一样,用得好,能帮大忙;用不好,也能添不少麻烦。
所以,咱们在使用的时候,一定要耐心、细心,这样才能发挥它的最大效用。
好了,关于热熔自攻螺钉连接技术,咱们今天就聊到这儿。
下次再有什么新鲜事儿,咱们再继续聊。
别忘了,不管做什么,耐心和细心总是最重要的。
攻丝机的工作原理

攻丝机的工作原理攻丝机是一种用于制作螺纹的机械设备,它基本上是一个由多个部件组成的系统。
其主要工作原理是在工件表面形成螺纹剖面,通常是圆柱形的。
下面将详细介绍攻丝机的工作原理。
攻丝机的组成部件包括主体机架、主轴、攻丝刀具、进给机构、主动力和控制系统等。
攻丝机可以分为手动攻丝机和自动攻丝机,原理基本相同,下文以自动攻丝机为例进行介绍。
当工作开始时,工件被夹持在攻丝机主体机架上,并通过进给机构调整位置和方向。
主轴受主动力驱动旋转,攻丝刀具则负责切削工件表面形成螺纹。
主轴的转速和进给速度可以通过控制系统进行调节。
这是一个重要的参数,决定了螺纹的规格和质量。
通常,高速旋转的主轴将工件与攻丝刀具之间的摩擦力转化为热量,因此需要冷却系统来防止过热。
进给机构控制攻丝刀具的位置和速度。
它通过向前或向后移动以调整刀具与工件的接触位置,同时还可以控制切削速度。
进给机构可以是机械式的,如螺杆传动系统,也可以是液压或电动驱动的。
攻丝刀具是用于切削螺纹的关键部件。
它们通常呈V型,可以根据所需的螺纹规格进行选择。
攻丝刀具通过旋转主轴与工件表面接触,并进行切削操作。
一般情况下,攻丝刀具具有多个刀片,可以根据需要进行更换。
控制系统是攻丝机的核心部分,用于控制主轴转速、进给速度和刀具位置等参数。
它可以是基本的机械式控制,也可以是更先进的数控系统。
数控系统可以根据预先输入的指令自动调整操作参数,提高生产效率和精度。
攻丝机的工作过程如下:首先,通过进给机构将攻丝刀具移动到预定位置,并与工件表面接触。
然后,主轴开始转动,使得攻丝刀具开始切削工件表面。
同时,进给机构会逐渐将攻丝刀具移动到工件上,沿着所需螺纹的方向切削。
当切削刀具完成一次切削时,进给机构将刀具移动一段固定的距离,以进行下一次切削。
这个过程不断重复,直到整个螺纹被切削完成。
整个工作过程可以通过控制系统进行监控和控制,以确保螺纹规格和质量的准确性。
总结一下,攻丝机通过旋转主轴和移动攻丝刀具来切削工件表面,形成所需的螺纹剖面。
塑料热熔焊接工艺
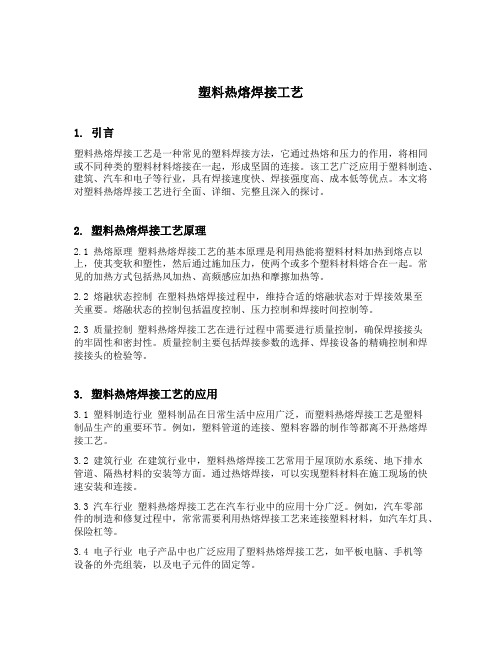
塑料热熔焊接工艺1. 引言塑料热熔焊接工艺是一种常见的塑料焊接方法,它通过热熔和压力的作用,将相同或不同种类的塑料材料熔接在一起,形成坚固的连接。
该工艺广泛应用于塑料制造、建筑、汽车和电子等行业,具有焊接速度快、焊接强度高、成本低等优点。
本文将对塑料热熔焊接工艺进行全面、详细、完整且深入的探讨。
2. 塑料热熔焊接工艺原理2.1 热熔原理塑料热熔焊接工艺的基本原理是利用热能将塑料材料加热到熔点以上,使其变软和塑性,然后通过施加压力,使两个或多个塑料材料熔合在一起。
常见的加热方式包括热风加热、高频感应加热和摩擦加热等。
2.2 熔融状态控制在塑料热熔焊接过程中,维持合适的熔融状态对于焊接效果至关重要。
熔融状态的控制包括温度控制、压力控制和焊接时间控制等。
2.3 质量控制塑料热熔焊接工艺在进行过程中需要进行质量控制,确保焊接接头的牢固性和密封性。
质量控制主要包括焊接参数的选择、焊接设备的精确控制和焊接接头的检验等。
3. 塑料热熔焊接工艺的应用3.1 塑料制造行业塑料制品在日常生活中应用广泛,而塑料热熔焊接工艺是塑料制品生产的重要环节。
例如,塑料管道的连接、塑料容器的制作等都离不开热熔焊接工艺。
3.2 建筑行业在建筑行业中,塑料热熔焊接工艺常用于屋顶防水系统、地下排水管道、隔热材料的安装等方面。
通过热熔焊接,可以实现塑料材料在施工现场的快速安装和连接。
3.3 汽车行业塑料热熔焊接工艺在汽车行业中的应用十分广泛。
例如,汽车零部件的制造和修复过程中,常常需要利用热熔焊接工艺来连接塑料材料,如汽车灯具、保险杠等。
3.4 电子行业电子产品中也广泛应用了塑料热熔焊接工艺,如平板电脑、手机等设备的外壳组装,以及电子元件的固定等。
4. 塑料热熔焊接工艺的优势和挑战4.1 优势 - 焊接速度快:塑料热熔焊接工艺可以在短时间内完成焊接过程,提高生产效率。
- 焊接强度高:通过塑料热熔焊接工艺连接的接头强度高,可以承受一定的拉力和剪力。
- 1、下载文档前请自行甄别文档内容的完整性,平台不提供额外的编辑、内容补充、找答案等附加服务。
- 2、"仅部分预览"的文档,不可在线预览部分如存在完整性等问题,可反馈申请退款(可完整预览的文档不适用该条件!)。
- 3、如文档侵犯您的权益,请联系客服反馈,我们会尽快为您处理(人工客服工作时间:9:00-18:30)。
株洲宏达模具热熔钻孔/攻丝技术原理及其应用
在机械加工中,常常需要解决薄壁型、板条型或管型工件的相互联接问题。
但是,这些联接方式及其相关技术存在一定的缺陷或不足。
a是在薄壁通孔中直接攻丝,通过螺栓(钉)实现薄壁工件的螺纹联接。
由于薄壁工件壁厚不足,螺纹牙数少,造成螺纹联接的强度、自锁性和可靠性较差。
b是在联接孔处焊(铆)接一个辅助螺母,以增加联接螺纹长度,提高联接强度。
但是,薄板焊(铆)接操作烦琐,技术要求较高,很容易烧穿板件,点焊强度也不高。
c是在联接螺栓(钉)上加装螺母。
这种方法会增加工序,降低效率,加大生产成本;此外,额外增加外部元件还会对装配操作带来不便,影响产品质量等。
以上几种联接方式还有一个共同的缺点:在联接部位钻孔切削会降低强度、浪费材料、产生切屑,不利于5s生产管理。
为了实现简便快速、经济有效的薄壁工件联接,星火公司开发出了一种无屑钻孔技术——热熔钻(Flowdrill)。
它可通过一次加工,在实现无屑钻孔的同时,利用加工部位的材料形成支承衬套。
在该衬套上可采用热熔丝锥攻制螺纹,形成强度更高的螺纹孔,避免了另外焊(铆)接联接用螺母,从而使传统的薄壁工件联接方式发生了根本变革。
1热熔钻工作原理及加工孔型
(1)热熔钻工作原理
热熔钻采用碳化钨硬质合金材料制造,其端部呈30。
60。
的锥尖形,锥面上无切削刃口。
当热熔钻在金属薄壁工件表面高速回转并被施以向下的轴向压力时,热熔钻的头部与金属材料剧烈摩擦,产生高达650~750℃的高温,使与锥顶接触的局部金属材料升温变红并迅速软化,随着轴向压力加大和进给加深,端部锥面与金属材料的接触面积增大,发热进一步增加,加工区温度继续上升而使变红区域扩大。
随着孔内原来的熔融实体材料在钻头的轴向进给和旋转作用下沿径向和轴向作热塑性流动而形成环颈和衬套,并快速加工出孔洞,而衬套的形成正是热熔钻所需要的加工效果。
同理,使用热熔丝锥可以在加工出的孔中进一步攻制螺纹,以达到增大联接长度、提高联接强度的效果。
此外,加工出的衬套还可作为轴承支撑座、分叉歧管等用途。
(2)热熔钻加工孔型
标准热熔钻可以钻削或攻螺纹的孔型包括长型、长平型、短型和短平型。
加工不同孔型时使用的热熔钻头形状也有所不同:加工长型、短型孔的热熔钻头端部是平整的;而加工长平型、短平型孔的热熔钻头端部有一定的弧度。
因此,加工出长平型、短平型孔的工件表面是平整的;而加工出长型、短型孔的工件表面则有凸台阶。
2热熔钻的特点与优势:
热熔钻孔/攻丝技术具有如下特点和优势:
(1)可使传统钻孔/攻丝时产生的切屑转化为联接薄壁工件所需的环颈(位于工件表面以上)和衬套(位于工件表面以下)结构,其总厚度可达工件原始壁厚的3倍左右。
通过改变工件结构和加工方式,提高了螺纹的成型精度、拉伸强度、联接扭矩值和稳定性。
(2)加工表面因热熔钻头部与金属材料剧烈摩擦产生高温,然后在空气中冷却而获得正火处理效果,使孔的表层硬度及防锈、耐腐蚀性能得以提高
(3)热熔钻加工速度快,循环时间短。
根据材料厚度及孔径大小的不同,加工1个孔仅需2—6秒钟,大大提高了生产效率。
(4)热熔钻实现了无屑加工,无需处理切屑等废料,简化了工序,提高了材料利用率。
(5)热熔钻头结构简单,易于制备和维护,刀具寿命较长。
热熔钻头圆柱面磨损小,锥面磨损不影响加工孔侧面的成形,无需刃磨刀具。
(6)热熔钻可在标准钻床或数控钻床上进行加工(加工功率水平1.5~3.5kW,主轴转速1000~3500);钻头夹持采用套筒夹头,刀柄采用莫氏锥柄或直圆柱柄。
无需额外增加专用设备和配件。
(7)热熔钻加工可优化、简化和改进产品结构设计和工艺路线,有利于后续装配加工。
4热熔钻的应用范围
(1)工件材料
热熔钻技术适用于加工壁厚O.5~12.5mm的多种金属材料,如低碳钢、不锈钢、钛、铝、铜、紫铜、黄铜(Zn含量低于40%)、铝合金(si含量低于0.5%)等
(2)应用领域
热熔钻可广泛应用于机械、汽车、航空航天、家用电器、自行车、金属建筑、金属家具、中央空调、照明等行业,可加工各种标准螺纹、公制螺纹和NPT螺纹。
(3)加工参数
目前已获得有效应用的热熔钻头/丝锥加工参数见表1。
表1热熔钻头/丝锥的加工参数
螺纹热熔钻直径转数马达功率加工时间攻丝转速
尺寸(mm)(r/min)(kW)(s)(r/而n)
M21.83200O.521600
M32.730000.621350
M43.72600O.721000
M54.525000.82800
M65.3/5.424001.02650
M87.322001.32500
MlO9.220001.53400
M1210,918001.73330
M1614.814002.24350
M2018.712002.75200。