§第五章-缩口和胀形
材料成型工艺教学大纲
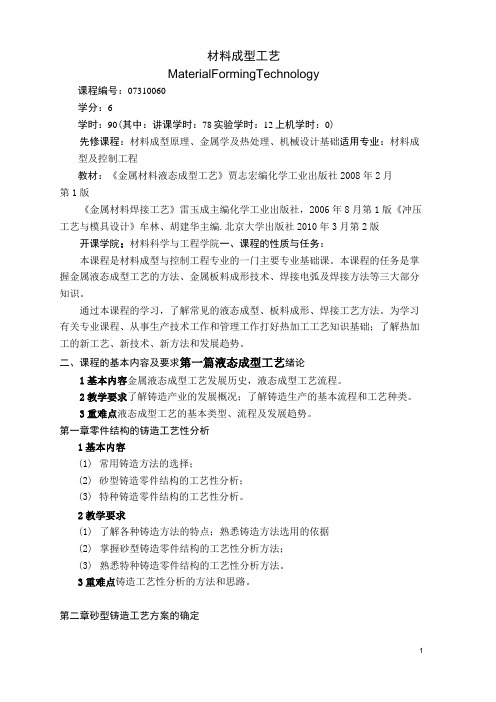
材料成型工艺MaterialFormingTechnology课程编号:07310060学分:6学时:90(其中:讲课学时:78实验学时:12上机学时:0)先修课程:材料成型原理、金属学及热处理、机械设计基础适用专业:材料成型及控制工程教材:《金属材料液态成型工艺》贾志宏编化学工业出版社2008年2月第1版《金属材料焊接工艺》雷玉成主编化学工业出版社,2006年8月第1版《冲压工艺与模具设计》牟林、胡建华主编.北京大学出版社2010年3月第2版开课学院:材料科学与工程学院一、课程的性质与任务:本课程是材料成型与控制工程专业的一门主要专业基础课。
本课程的任务是掌握金属液态成型工艺的方法、金属板料成形技术、焊接电弧及焊接方法等三大部分知识。
通过本课程的学习,了解常见的液态成型、板料成形、焊接工艺方法。
为学习有关专业课程、从事生产技术工作和管理工作打好热加工工艺知识基础;了解热加工的新工艺、新技术、新方法和发展趋势。
二、课程的基本内容及要求第一篇液态成型工艺绪论1基本内容金属液态成型工艺发展历史,液态成型工艺流程。
2教学要求了解铸造产业的发展概况;了解铸造生产的基本流程和工艺种类。
3重难点液态成型工艺的基本类型、流程及发展趋势。
第一章零件结构的铸造工艺性分析1基本内容(1)常用铸造方法的选择;(2)砂型铸造零件结构的工艺性分析;(3)特种铸造零件结构的工艺性分析。
2教学要求(1)了解各种铸造方法的特点;熟悉铸造方法选用的依据(2)掌握砂型铸造零件结构的工艺性分析方法;(3)熟悉特种铸造零件结构的工艺性分析方法。
3重难点铸造工艺性分析的方法和思路。
第二章砂型铸造工艺方案的确定1基本内容(1)工艺设计内容及流程;(2)砂型铸造工艺方案确定的基本原理;2教学要求(1)熟悉铸造工艺设计的依据、内容及流程;(2)掌握砂型铸造工艺方案制定的原理及方法。
3重难点(1)生产纲领、生产条件对工艺方案制定的影响;(2)分型面及浇注位置的确定。
冲压成形模具设计课件-缩口、旋压、校形

① 模具结构 ② 工作原理 ③ 适用地方 a 软材料 b 薄材料 c 工件表面不允许有压痕 ④ 如何提高校平效果?
工件反叠 (3)齿形校平模 ① 模具结构
2021年9月28日星期二
学习情境4:其它冲压成形模具设计
第五节 校
② 工作原理 ③ 适用地方 a 硬材料 b 平面度误差较小 ④ 齿形的类型 A尖齿 a 齿形及尺寸 b 优点 c 缺点 B平齿
一、给定任务 设计如图所示零件的冲压模具
2021年9月28日星期二
学习情境4:其它冲压成形模具设计
第三节 缩 口
缩口:
将管坯或预先拉深好的圆筒形 件通过缩口模将其口部直径缩小的 一种成形方法。
一、缩口变形特点及变形程度
1.缩口的变形过程(三维、二维) 2.缩口的变形特点 (1)缩口变形区的应力与应变状 态
2021年9月28日星期二
学习情境4:其它冲压成形模具设计
第五节 校
二、平板零件的校平
1.校平方式 (1)模具校平 (2)手工校平 (3)专门设备校平 2.模具校平 (1)校平模具的种类 ① 光面校平模 ② 齿形校平模 (2)光面校平模
形
2021年9月28日星期二
学习组成 (2)工作原理(三维动画、二维动画) ① 坯料的定位 ② 滑块下行时各零件如何动作? ③ 滑块回程时各零件如何动作? (3)零件间的配合关系分析 ① 凹模与固定板 ② 支撑凸模与凹模 (4)部分零件性能分析
2021年9月28日星期二
学习情境4:其它冲压成形模具设计
学习情境4:其它冲压成形模具设计
第三节 缩 口
① 材料的塑性 ② 材料厚度 ③ 支承方式
二、缩口工艺计算
1.缩口次数 若工件的缩口系数m小于允许的缩口系数时,则需进行
冲压过程技术标准
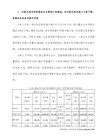
冲压工艺培训教材魏龙2004-5第一章绪论冷冲压是一种先进的金属加工方法,它是建立在金属塑性变形的基础上,利用模具和冲压设备对板料金属进行加工,以获得所需要的零件形状和尺寸。
冲压工艺应用范围十分广泛,在国民经济各个部门中,几乎都有冲压加工产品,如汽车、飞机、拖拉机、电机、电器、仪表、铁道、邮电、化工以及轻工日用产品中均占有相当大的比重。
冷冲压和切削加工比较,具有生产率高、加工成本低、材料利用率高、产品尺寸精度稳定、操作简单、容易实现机械化和自动化等一系列优点,特别适合大批量生产。
一、冲压工序的分类冷冲压工艺按其变形性质可分为分离工序和成形工序两大类。
分离工序又可分为落料、冲孔和切边等,如表1-1所示。
成形工序可分为弯曲、拉深、翻孔、翻边、胀形、扩口、缩口和旋压等,如表1-2所示。
根据产品零件的形状、尺寸精度和其他技术要求,可分别采用各种工序对板料毛坯进行加工,以获得满意的零件。
表1-1分离工序工序名称简图特点及应用范围第二章冲裁冲裁是利用模具使板料产生分离的冲压工序,包括落料、冲孔、切口、剖切、修边等。
用它可以制作零件或为弯曲、拉深、成形等工序准备毛坯。
一、落料从板料上冲下所需形状的零件(或毛坯)叫落料。
如图2-1所示。
图2-1落料图2-2冲孔二、冲孔在工件上冲出所需形状的孔(冲去的为废料)叫冲孔。
如图2-2所示。
三、冲裁的过程冲裁既是分离工序,工件受力时必然从弹、塑性变形开始,以断裂告终。
当凸模下降接触板料,板料即受到凸、凹模压力而产生弹性变形,板料产生弯曲,即从模具表面上翘起(图2-3-1)。
随着凸模下压,模具刃口压入材料,内应力状态满足塑性条件时,产生塑性变形(图2-3-2)。
塑性变形从刃口开始,随着刃口的深入,变形区向板料的深度方向发展、扩大,直到在板料的整个厚度方向上产生塑性变形,板料的一部分相对于另一部分移动。
当切刃附近材料各层中达到极限应变与应力值时,便产生微裂(图2-3-3),裂纹产生后,沿最大剪应变速度方向发展,直至上、下裂纹会合,板料就完全分离。
翻边的预冲孔如何计算(ppt)

F pA
胀形单位面积压力p可用下式计算:
p
1.1
5zx
2t dmax
式中
zx ――胀形变形区实际应力,近似估算时取 zx≈ b(材料的抗拉强度)
第五章 其它成形工艺与模具设计
第三节 翻边
翻边: 在模具的作用下,将坯料的孔边缘或外边缘冲制成竖立边
的成形方法。
一、内孔翻边
1.圆孔翻边 (1)圆孔翻边的变形特点与变形程度
圆孔翻边凸模的形状和主要尺寸 凸、凹模单边间隙Z/2=(0.75~0.85)t
第五章 其它成形工艺与模具设计
第三节 翻边
一、内孔翻边(续)
2.非圆孔翻边
变形区分类
非圆孔翻边系数 K
(一般指小圆弧部分的翻边系数)可
f
小于圆孔翻边系数K
Kf (0.8~ 50.9)5 K
非圆孔的极限翻边系数,可根据各圆弧段的圆心角a大小, 查表5.3.2
1.胀形方法 刚性模具胀形 软模胀形 轴向压缩和高压液体联合作用的胀形
第五章 其它成形工艺与模具设计
第二节 胀形
三、空心坯料的胀形
2.胀形的变形程度 常用胀形系数K表示 K dmax D
K和坯料伸长率的关系为 dmaxDK1
D
第五章 其它成形工艺与模具设计
第二节 胀形
三、空心坯料的胀形
3.胀形的坯料尺寸计算
重点:
胀形、翻边工序的变形特点、工艺计算和模具结构特点。
难点:
翻边工序的变形特点、工艺计算。
第五章 其它成形工艺与模具设计
本章目录
第一节 概述 第二节 胀形 第三节 翻边 第四节 缩口 第五节 旋压 第六节 校形
第五章 其它成形工艺与模具设计
冲压知识

• 冷冲压是塑性加工的基本方法之一,它主 要用于加工板料零件,所以有时也叫板料 冲压。冲压加工的应用范围十分广泛,不 仅可以加工金属板料,而且也可以加工非 金属材料。冲压加工时,板料在模具的作 用下,与其内部产生使之变形的内力。当 内力的作用达到一定的数值时,板料毛坯 或毛坯的某个部分便会产生与内力的作用 性质相对应的变形,从而获得一定的形状、 尺寸和性能的零件。
V形弯曲过程
• 在弯曲的开始阶段,毛坯 自由弯曲。凸模下压,毛 坯的直边与凹模工作表面 靠拢。凸模继续下压,板 料与凸模三点接触,此后 弯曲区继续缩小,半成形 弯曲件的两边,被凸模向 外撑开,逐步贴向凹模工 作表面。在行程终了时, 凸模与凹模对弯曲件进行 校正,使弯曲件的圆角、 直边与凸模全部贴近。
注意事项
(1)毛坯放置在模具上必须保证有正确可靠的定位。当工 件上有孔并且允许其作为定位孔时,应尽量利用工件上的 孔定位。若工件上无孔但允许在毛坯上冲制工艺孔时,可 以考虑在毛坯上设计出定位工艺孔。当工件上不允许有工 艺孔时,应考虑用定位板对毛坯外形定位,同时应设置压 料装置压紧毛坯以防止弯曲过程中毛坯的偏移。 (2)当采用多道工序弯曲时,各工序尽可能采用同一定位 基准。 (3)设计模具结构应注意放入和取出工件的操作要安全、 迅速和方便。 (4)对于容易磨损的部分如凸模,凹模的结构设计要便于 拆卸。
降低冲裁力的方法
1阶梯式凸模 (H=0.5~1t) 2斜刃的形式 斜角5°~8°
卸料力、推料力和顶料力
• 卸料力:卸下包在凸模上材料所需要的力 叫做卸料力。
• 推料力:顺着冲裁方向推出卡在凹模里的 料所需要的力叫做推料力。 • 顶料力:逆着冲裁方向顶出卡在凹模里料 所需要的力叫顶料力。
刃口尺寸计算
冲压工艺学6-胀形与翻边

图5-7 两道工序完成的凸形
(2)圆柱形空心毛坯的胀形 1)胀形方式 a.橡皮(或聚氨酯)凸模 胀形 该胀形方式如图5-8 所示。由于聚氨酯橡胶优 良的物理机械性能,用它 作工作介质的胀形得到愈 来愈广泛的应用。
图5-8 橡皮凸模胀形
b.分块式凸模胀形 如图5-9所示,采用刚性凸模, 凸模必须作成分块式,以便出模时由楔状心块 将其分开。
(3)影响胀形成形极限的因素 1)材料性能 加工硬化指数n值对胀形成形极限 影响极大。 n值大,加工硬化能力强,可促使 应变分布趋于均匀化,同时还能提高材料的局 部强度,故成形极限也大。 2)变形均匀程度 胀形破裂发生在板料厚度减薄 最大部位。变形均匀,板料厚度减薄均匀能获 得较大的胀形变形程度。
图5-9 分块式凸模胀形
c.液压胀形 如图510所示,用液体作 为凸模的胀形方式 称做液压胀形。 d.石蜡胀形 除采用 橡皮和液体等软模 来成形外,还可采用 石蜡作为传力介质 进行胀形。
a)直接倾注液体法 b)充液橡皮囊法 图5-10 液压胀形
2)圆柱形空心毛坯胀形的成形极限 生产中用 胀形系数K表示圆柱形空心毛坯胀形的变形程 度。用最大胀形系数Kmax表示其破裂成形极 限。 胀形系数: K=dmax/d 在胀形时对毛坯轴向加压的话,胀形成形 极限可以增大。对毛坯变形区局部加热会显 著增大胀形变形程度。
图5-17 非圆形孔翻边
图5-18 非圆形孔翻边的实例
(3) 内孔翻边的工艺计算 1)圆孔翻边的毛坯计算 a.预制孔径计算 翻边时材料主要是切向伸长, 厚度变薄,径向变形不大,可根据弯曲件中性层 长度不变原则来求预制孔径。
t d 0 D1 (r ) 2h1 d1 2(h 0.43r 0.72t ) 2
胀形 翻边 缩口(二)
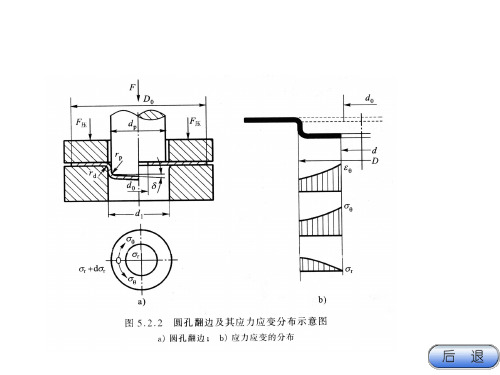
5.3.2缩口变形程度 缩口变形程度
缩口变形程度用缩口系数K来表示,其表达式: 缩口变形程度用缩口系数 来表示,其表达式: 来表示
d K= D
式中:d—缩口后的直径 式中: 缩口后的直径 D—为缩口前的直径 为缩口前的直径
5.3.3缩口模具结构设计举例 缩口模具结构设计举例
刚制气瓶缩口模,成形材料为1 刚制气瓶缩口模,成形材料为1mm的08钢(如 的08钢 图5.3.3) 33
2.冲压设备规格的选择 冲压设备规格的选择 1)公称压力 1)公称压力 一般情况下, 一般情况下,设备的公称压力应大于或等于成 形总工艺力的1.3倍。 形总工艺力的1.3倍 1.3 2)滑块行程 2)滑块行程 在拉深、弯曲工序中工件的高度较大时, 在拉深、弯曲工序中工件的高度较大时,为便 于取件,滑块行程应大于或等于工件高度的2.5 2.5倍 于取件,滑块行程应大于或等于工件高度的2.5倍。 3)闭合高度 闭合高度 模具的闭合高度必须适合于压力机闭合高度范围 的要求,它们之间的关系一般为: 的要求,它们之间的关系一般为:
D = d p + 4dH − 3.44d × r = 542 + 23.8×16− 3.44× 23.8× 2.25mm≈ 65mm
2
2) 计算拉深次数 因为 ; t / D = 2.3%
d ' 凸 54 = = 0.83 D 65
m总 =
d 23.8 = = 0.366 D 65
初定 r1 ≈ ( 4 ~ 5)t 《冲压手册》中查表可得极限拉深 从 冲压手册》 系数 [m1 ] = 0.44, [m2 ] = 0.75 又由 所以
特点:生产率高,操作比较安全,用于大批量的, 特点:生产率高,操作比较安全,用于大批量的,采用其他工序 加工困难的精度要求不太高的小型工件的生产。 加工困难的精度要求不太高的小型工件的生产。
缩口

工作过程1 缩口工艺性分析
【知识与技能准备】
一、缩口简述
1、定义:
将圆筒件或管件坯料,通过缩口模具将其口部缩小的一种成型工序。
2、应用:
子弹壳、炮弹壳、钢制气缸等;
车车架立管、自行车坐垫鞍管等。
3、对细长的管状类零件,有时用缩口代替拉深可取得更好的效果:
用拉深和冲底孔成形的制件,工序5道工序:
用管状毛坯缩口工序,只需3道工序:
二、缩口成形的变形特点
图5.3.2 缩口成形的变形特点
1、变形区主要两向应力作用,其中切向压应力最大,使直径缩小、厚度和高
度增加;
2、由于受切向应力较大,容易产生切向失稳和起皱;
3、属压缩类变形,常见的压缩变形形式如下:
【项目实施】气瓶缩口工艺性分析
气瓶为带底的筒形件,可采用拉深工艺制成圆筒形件,在进行缩口成形。
工艺过程:拉深制成圆筒形件----->缩口成瓶形。
零件名称:气瓶
生产批量:中批量
材 料:08钢 材料1mm。