硫化锌精矿加压氧浸工艺的酸平衡分析
高铁硫化镍精矿富氧加压酸浸工艺研究

高铁硫化镍精矿富氧加压酸浸工艺研究以高铁硫化镍精矿为原料,采用富氧加压工艺浸出铜、镍。
研究液固比、硫酸浓度、氧压、温度与时间等条件对加压浸出过程的影响。
结果表明:对于粒度为-270目占95%以上,平均粒度为17.25μm的精矿,在L:S=3:1,硫酸浓度50g/L,氧气压力1.2MPa,反应温度150℃,反应时间2h的条件下,镍、铜、钴的浸出率分别为:98.70%、80.30%、98%,Fe的浸出率控制在6%以下。
标签:硫化镍精矿富氧加压浸出我国某处高铁硫化镍矿主要包含镍黄铁矿、镍滑石、镍磁黄铁矿、黄铜矿等成分。
其常规湿法冶金工艺中存在着反应速度慢,浸出时间长等不足,因此过程强化必不可少。
目前加压氧化浸出为重要方法之一。
本文采用加压氧化浸出法对高铁硫化镍矿进行镍、铜的直接浸出,研究不同因素对镍、铜浸出率的影响规律,为得到铜镍浸出率高,而铁离子浓度和酸度都低的浸出液提供技术指导。
1 原料试验所用的硫化镍精矿化学分析结果如表1。
由表1的分析结果可见,该精矿中S、Fe、Ni是主要元素,是典型的高铁硫化镍矿,同时该精矿中有价元素钴和铜的含量也较高,也具有综合回收的价值。
为了了解硫化镍精矿中各种有价金属的赋存形式,对该矿进行了XRD分析,分析结果如图1,表明矿石中的镍主要以镍黄铁矿形态存在,少量镍还以镍滑石和镍绿泥石形态存在,铁还以磁黄铁矿和硫化铁矿形态存在,铜以黄铜矿形态存在,MgO和SiO2以滑石和镍绿泥石矿物形态存在。
2 试验原理硫化镍精矿在富氧条件下加压酸浸时,镍、铜以离子形式进入溶液。
通过控制酸度、温度等使铁大部分留在浸出渣中。
硫在浸出时的行为比较复杂,在酸性介质中,S2-被氧化为S0的标准电位(-0.48V)比Fe2+被氧化为Fe3+的标准电位(+0.771V) 低得多,从热力学分析,氧对S2-的氧化能力比Fe2+的氧化能力强得多,使矿物中硫一部分以单质形态进入渣中;另外,还有一部分硫被最终氧化为硫酸根SO42-进入溶液。
氧压浸出
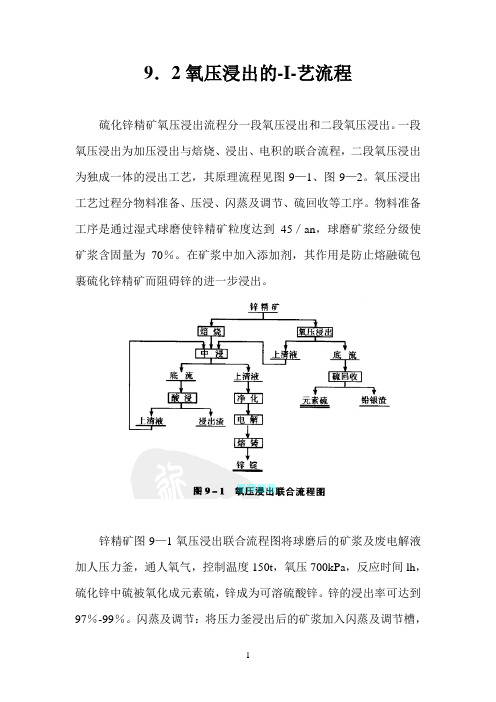
9.2氧压浸出的-I-艺流程硫化锌精矿氧压浸出流程分一段氧压浸出和二段氧压浸出。
一段氧压浸出为加压浸出与焙烧、浸出、电积的联合流程,二段氧压浸出为独成一体的浸出工艺,其原理流程见图9—1、图9—2。
氧压浸出工艺过程分物料准备、压浸、闪蒸及调节、硫回收等工序。
物料准备工序是通过湿式球磨使锌精矿粒度达到45/an,球磨矿浆经分级使矿浆含固量为70%。
在矿浆中加入添加剂,其作用是防止熔融硫包裹硫化锌精矿而阻碍锌的进一步浸出。
锌精矿图9—1氧压浸出联合流程图将球磨后的矿浆及废电解液加人压力釜,通人氧气,控制温度150t,氧压700kPa,反应时间lh,硫化锌中硫被氧化成元素硫,锌成为可溶硫酸锌。
锌的浸出率可达到97%-99%。
闪蒸及调节:将压力釜浸出后的矿浆加入闪蒸及调节槽,力釜中生成的元素硫是熔融状态,矿浆进入闪蒸槽后,控制温度120~C,保持熔融状态的硫。
从闪蒸槽中可回收蒸汽供生产使用,矿浆再进人调节槽冷却,控制温度100~C,使元素硫成固态冷凝。
调节槽冷却后的矿浆送人浓密机浓缩,浓缩上清液送往净化、电积、熔铸生产电锌,浓密机底流送硫回收工序。
硫回收工艺是将浓密机底流进行浮选回收硫精矿,浮选尾矿经水洗后送渣场堆存。
含硫精矿送人粗硫池熔融,再通过加热过滤,从未浸出的硫化物中分离出熔融元素硫,然后将熔融硫送人精硫池产出含硫大于99%的元素硫。
加热过滤所产的过滤渣含有的稀有金属和贵重金属待回收。
9.3氧压浸出装置氧压浸出高压釜是由碳钢作外壳,用铅及耐酸砖做内衬。
高压釜内用隔板隔成4—6个室,每个室内配有机械搅拌槽(图9—3)。
球磨后的矿浆经分级使矿浆含固量为70%,加入浸出添加剂后,泵人高压釜第l室。
浸出添加剂能使熔融硫呈疏散球状,防止熔融硫包裹硫化锌精矿而阻碍浸出时锌的进一步浸出。
废电解液分别泵人高压釜第1室、第2室,同时向釜内通人浓度98%以上的氧气,控制反应温度150~C,氧分压0.7MPa,釜压1.1MPa,反应时间1-1.5h,进行连续浸出,使硫化锌中硫被氧化成元素硫,锌成为可溶硫酸锌。
硫化锌精矿与锌浸出渣协同助浸机理及行为
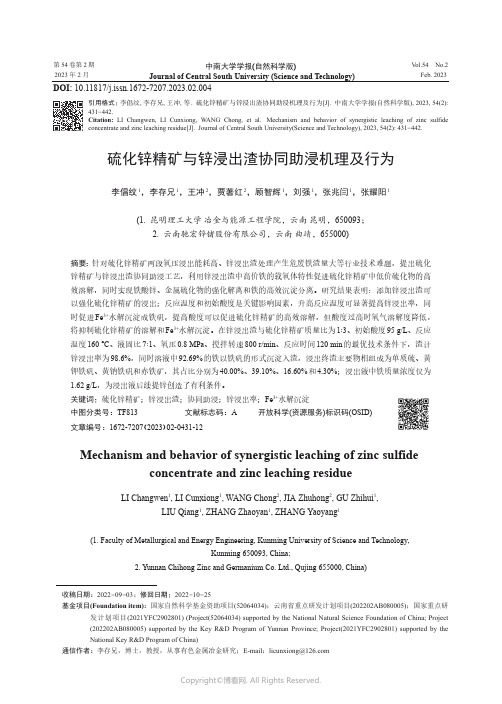
第 54 卷第 2 期2023 年 2 月中南大学学报(自然科学版)Journal of Central South University (Science and Technology)V ol.54 No.2Feb. 2023硫化锌精矿与锌浸出渣协同助浸机理及行为李倡纹1,李存兄1,王冲2,贾著红2,顾智辉1,刘强1,张兆闫1,张耀阳1(1. 昆明理工大学 冶金与能源工程学院,云南 昆明,650093;2. 云南驰宏锌锗股份有限公司,云南 曲靖,655000)摘要:针对硫化锌精矿两段氧压浸出能耗高、锌浸出渣处理产生危废铁渣量大等行业技术难题,提出硫化锌精矿与锌浸出渣协同助浸工艺,利用锌浸出渣中高价铁的载氧体特性促进硫化锌精矿中低价硫化物的高效溶解,同时实现铁酸锌、金属硫化物的强化解离和铁的高效沉淀分离。
研究结果表明:添加锌浸出渣可以强化硫化锌精矿的浸出;反应温度和初始酸度是关键影响因素,升高反应温度可显著提高锌浸出率,同时促进Fe 3+水解沉淀成铁矾,提高酸度可以促进硫化锌精矿的高效溶解,但酸度过高时氧气溶解度降低,将抑制硫化锌精矿的溶解和Fe 3+水解沉淀。
在锌浸出渣与硫化锌精矿质量比为1꞉3、初始酸度95 g/L 、反应温度160 ℃、液固比7꞉1、氧压0.8 MPa 、搅拌转速800 r/min 、反应时间120 min 的最优技术条件下,渣计锌浸出率为98.6%,同时溶液中92.69%的铁以铁矾的形式沉淀入渣,浸出终渣主要物相组成为单质硫、黄钾铁矾、黄钠铁矾和赤铁矿,其占比分别为40.00%、39.10%、16.60%和4.30%;浸出液中铁质量浓度仅为1.62 g/L ,为浸出液后续提锌创造了有利条件。
关键词:硫化锌精矿;锌浸出渣;协同助浸;锌浸出率;Fe 3+水解沉淀中图分类号:TF813 文献标志码:A 开放科学(资源服务)标识码(OSID)文章编号:1672-7207(2023)02-0431-12Mechanism and behavior of synergistic leaching of zinc sulfideconcentrate and zinc leaching residueLI Changwen 1, LI Cunxiong 1, WANG Chong 2, JIA Zhuhong 2, GU Zhihui 1,LIU Qiang 1, ZHANG Zhaoyan 1, ZHANG Yaoyang 1(1. Faculty of Metallurgical and Energy Engineering, Kunming University of Science and Technology,Kunming 650093, China;2. Yunnan Chihong Zinc and Germanium Co. Ltd., Qujing 655000, China)收稿日期: 2022 −09 −03; 修回日期: 2022 −10 −25基金项目(Foundation item):国家自然科学基金资助项目(52064034);云南省重点研发计划项目(202202AB080005);国家重点研发计划项目(2021YFC2902801) (Project(52064034) supported by the National Natural Science Foundation of China; Project (202202AB080005) supported by the Key R&D Program of Yunnan Province; Project(2021YFC2902801) supported by the National Key R&D Program of China)通信作者:李存兄,博士,教授,从事有色金属冶金研究;E-mail :******************DOI: 10.11817/j.issn.1672-7207.2023.02.004引用格式: 李倡纹, 李存兄, 王冲, 等. 硫化锌精矿与锌浸出渣协同助浸机理及行为[J]. 中南大学学报(自然科学版), 2023, 54(2): 431−442.Citation: LI Changwen, LI Cunxiong, WANG Chong, et al. Mechanism and behavior of synergistic leaching of zinc sulfide concentrate and zinc leaching residue[J]. Journal of Central South University(Science and Technology), 2023, 54(2): 431−442.第 54 卷中南大学学报(自然科学版)Abstract:In view of the industrial technical problems such as high energy consumption of two-stage oxygen pressure leaching of zinc sulfide concentrate and large amount of hazardous waste iron slag from zinc leaching slag treatment, a synergistic leaching process of zinc sulfide concentrate and zinc leaching slag was proposed. The oxygen carrier properties of medium and high valent iron promote the efficient dissolution of low-valent sulfides in zinc sulfide concentrates, and the dissociation of zinc ferrite and metal sulfides and the efficient precipitation and separation of iron were enhanced. The results show that adding zinc leaching residue can strengthen the leaching of zinc sulfide concentrate. The reaction temperature and initial acidity are the key influencing factors.Increasing the reaction temperature can significantly improve the zinc leaching rate and promote the hydrolysis and precipitation of Fe3+into alum. Increasing the acidity can promote the efficient dissolution of zinc sulfide concentrate. However, when the acidity is too high, the oxygen solubility decreases, which will inhibit the dissolution of zinc sulfide concentrate and the hydrolysis and precipitation of Fe3+. The optimal technology is that the mass ratio of zinc leaching residue to zinc sulfide concentrate is 1:3, the initial acidity is 95 g/L, the reaction temperature is 160 ℃, the liquid-solid ratio is 7:1, the oxygen pressure is 0.8 MPa, the stirring speed is 800 r/min, and the reaction time is 120 min. Under the conditions, the leaching rate of zinc from the slag is 98.60%, and92.69% of the iron in leachate is precipitated into the slag in the form of jarosite. The main phase composition ofthe final leaching slag is elemental sulfur, jarosite, jarosite, hematite, whose proportions are 40.00%, 39.10%,16.60% and 4.30%, respectively. The iron concentration in the leaching solution is only 1.62 g/L, which createsfavorable conditions for the subsequent extraction of zinc from the leaching solution.Key words: zinc sulphide concentrate; zinc leaching residue; synergistic leaching; zinc leaching rate; Fe3+ hydrolysis precipitation金属锌被称为“现代工业的保护剂”,是消费量仅次于铝和铜的第三大有色金属[1−2]。
硫化锌精矿加压浸出时H2S的生成及影响

有色金属(冶炼部分)2007年5期硫化锌精矿加压浸出时h2s的生成及影响谢克强\杨显万\王吉坤2(1. I明理工大学材料与冶金工程学院,昆明650093;2.云南冶金集团总公司,昆明650031)摘要:分析了硫化锌精矿加压浸出过程中H2S的生成,并结合试验中所发现的现象阐明了 H2S生成对钛质加压釜体的腐蚀作用,提出了腐蚀机理,在此基础上提出了钛质加压釜安全操作的原则。
关键词:硫化锌精矿;加压浸出;加压釜;H2S;腐蚀机理;钛中图分类号:TF813 文献标识码:A 文章编号:1007 —7545(2007)05 —0005 —03The Formation and Effect of H2S in Pressure Leaching Process of Zinc Sulphide ConcentrateXIE Ke-qiang!, YANG Xian-wan1, WANG Ji-kun2(1. Faculty of Materials and Metallurgical Engineering, Kunming University of Science and Technology,Kunming 650093, Chinaj 2. Yunnan Metallurgical General Company, Kunming 650031, China)Abstract:The formation of H2S in the oxygen pressure leaching process is analyzed, the chemical attack of H2S on titanium—base autoclave is observed and the corrosion mechanism is proposed, and the safe working rules are also recommended.Keywords: Zinc sulphide concentrate; Pressure leaching; Autoclave; H2S; Corrosion mechanism;Titanium 随着加压浸出技术在有色冶金中的应用,加压釜的设计与安全操作至关重要。
在压力场下高硅氧化锌矿酸浸实验研究

摘要锌矿主要分为硫化锌矿和氧化锌矿两类,由于硫化锌矿日益枯竭,氧化锌矿的开发逐渐受到重视,但是由于氧化锌矿通常含硅较高,直接酸浸容易产生可溶性硅,致使矿浆液固分离困难。
因此,如何控制可溶性硅的浸出是高硅氧化锌矿酸浸工艺研究的关键所在。
本文以云南兰坪高硅氧化锌矿为研究对象,在压力场下进行了加压酸浸的试验研究,分析了矿物粒度、起始酸度、反应温度、釜内压力、浸出时间、液固比这六个因素对锌浸出率、二氧化硅浸出率和过滤速率的影响。
条件试验研究得出最佳工艺条件为:矿物粒度-0.105mm占85%以上,起始酸度90.16g·L-1,釜内压力1.2MPa,浸出时间90min,反应温度120℃,液固比3:1。
根据以上最佳条件,进行综合性试验,研究得出:锌浸出率可达98%以上,SiO2浸出率低于 1.02%,矿浆过滤速率大于941L·m-2·h-1。
此时pH=2,硅酸处于最稳定的状态,矿浆具有良好的过滤性能。
由于采用加压酸浸工艺,有效的避免了高硅氧化锌矿中可溶硅的大量溶出,极大地改善了矿浆的过滤性能,为高硅氧化锌矿的处理开辟了新途径。
关键词:高硅氧化锌矿;加压酸浸;锌浸出率;SiO2浸出率;矿浆过滤性能AbstractZinc sulfide and zinc oxide are two main mineral forms existing in zinc ores. Theprocessing of zinc oxide is becoming more attractive due to the depletion of zinc sulfide ores. Usually, zinc oxide ores contain much SiO2and in the process of direct sulfuric leaching, may dissolve in leaching solution and cause ore pulp difficult for solid liquid separation. Therefore, the research on sulfuric acid leaching of high silica zinc oxide orefocuses on how to control leaching percent of SiO2.Experiments on acid leaching at pressure is studied according to the mineralogical analyses of high silicon zinc oxide ore from Lanping, Yunnan province.The influence of six factors on leaching rate of Zn and SiO2and filtration rate is studied, including initial acidity, leaching temperature, oxygen pressure, leaching time, particle size , and the ratio of liquid to solid.the best technology conditions was obtained by condition experiments, which are particle size is -150mush above 85%,sulfuric acid is 90.16 g·L-1, oxygen pressure is 1.2MPa, leaching time is 90min,reacting temperature is 120℃, liquid solid ratio is 3:1.It can be conclude that under the best technology conditions the leaching percent of zinc and SiO2are above 98% and below 1.02% separately, filtration rate is over 941L·m-2·h-1, at this point, the silicon acid is in the most stable state and the leaching slurry is in good filtration property.As a result of pressure acid leaching process, it is effective to avoid a large number of soluble silicon in high silicon oxide zinc, and greatly improve the filtering property of the leaching slurry. It open up a new treatment way for high silicon zinc oxide ore.Keywords: high silicon zinc oxide ore; pressure acid leaching, leaching percent of Zn; leaching percent of SiO2; filtration property of slurry.前言锌是一种仅次于铝和铜的重要金属资源,其用途极其广泛,是人类生活中不可或缺的重要物质,在国民经济中占有很重要的地位。
硫化锌精矿常压富氧直接浸出行为

硫化锌精矿常压富氧直接浸出行为
徐志峰;江庆政;王成彦
【期刊名称】《中国有色金属学报(英文版)》
【年(卷),期】2013(000)012
【摘要】通过矿物学分析研究了锌富含型富含型富含浸出条件下锌浓缩物中的主要金属硫化物的浸出行为。
结果表明,除黄铁矿外,硫化物明显溶解。
基于元素硫和浸出残留物中的残留硫化物之间的关系,假设散丝,硫代吡啶,科洛勒州和伽罗兰纳米溶解,遵循间接氧化反应,其中酸性溶解首先进行,然后释放的H2S转移矿物表面进入散装溶液,进一步氧化成元素硫。
界面化学反应进一步被认为是浸出这些硫化物的控制步骤。
假设直接电化学氧化反应有助于Pyrhotite的溶解,其通过通过元素硫层的扩散来控制。
%借助工艺含有物学分析对常压富氧直接浸出条件下料精料中间含化物的浸出行为研究。
结果说明,除除外,其他其他化矿均会明显溶解。
基于对浸出渣中单质与反应残余硫出渣中单关键词,为之,闪锌矿,黄,铜蓝,方铅矿的溶出可能遵循接氧式,生成的h2s脱离脱离溶,生成的h2s脱离脱离溶,生成素脱离溶进而并迁移至本体中央化成单位质。
对于对于铁矿的溶出,直接电气化学介绍可起起作用,其其程程可受产硫硫硫。
【总页数】8页(P3780-3787)
【作者】徐志峰;江庆政;王成彦
【作者单位】江西理工大学冶金与化学工程学院,赣州341000;江西理工大学冶金与化学工程学院,赣州341000;北京矿冶研究总院,北京 100160
【正文语种】中文
因版权原因,仅展示原文概要,查看原文内容请购买。
硫化铜精矿加压氧化酸浸试验研究
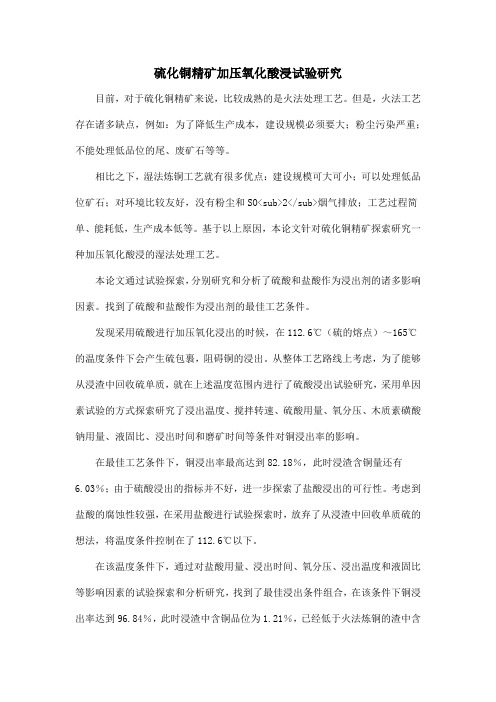
硫化铜精矿加压氧化酸浸试验研究目前,对于硫化铜精矿来说,比较成熟的是火法处理工艺。
但是,火法工艺存在诸多缺点,例如:为了降低生产成本,建设规模必须要大;粉尘污染严重;不能处理低品位的尾、废矿石等等。
相比之下,湿法炼铜工艺就有很多优点:建设规模可大可小;可以处理低品位矿石;对环境比较友好,没有粉尘和SO<sub>2</sub>烟气排放;工艺过程简单、能耗低,生产成本低等。
基于以上原因,本论文针对硫化铜精矿探索研究一种加压氧化酸浸的湿法处理工艺。
本论文通过试验探索,分别研究和分析了硫酸和盐酸作为浸出剂的诸多影响因素。
找到了硫酸和盐酸作为浸出剂的最佳工艺条件。
发现采用硫酸进行加压氧化浸出的时候,在112.6℃(硫的熔点)~165℃的温度条件下会产生硫包裹,阻碍铜的浸出。
从整体工艺路线上考虑,为了能够从浸渣中回收硫单质,就在上述温度范围内进行了硫酸浸出试验研究,采用单因素试验的方式探索研究了浸出温度、搅拌转速、硫酸用量、氧分压、木质素磺酸钠用量、液固比、浸出时间和磨矿时间等条件对铜浸出率的影响。
在最佳工艺条件下,铜浸出率最高达到82.18%,此时浸渣含铜量还有6.03%;由于硫酸浸出的指标并不好,进一步探索了盐酸浸出的可行性。
考虑到盐酸的腐蚀性较强,在采用盐酸进行试验探索时,放弃了从浸渣中回收单质硫的想法,将温度条件控制在了112.6℃以下。
在该温度条件下,通过对盐酸用量、浸出时间、氧分压、浸出温度和液固比等影响因素的试验探索和分析研究,找到了最佳浸出条件组合,在该条件下铜浸出率达到96.84%,此时浸渣中含铜品位为1.21%,已经低于火法炼铜的渣中含铜量。
文章对两种浸出剂的试验探索结果进行了综合分析,发现了一些有价值结论。
并对比研究了硫酸浸出和盐酸浸出的条件与结果,认为采用盐酸对硫化铜精矿进行加压氧化浸出有明显的优势,同时,经过工艺成本估算分析,可以认为采用盐酸对硫化铜精矿进行加压氧化浸出的工艺方案是完全可行的。
锌冶炼酸浸渣硫化焙烧工艺研究

锌冶炼酸浸渣硫化焙烧工艺研究摘要:以黄铁矿为硫化剂,锌冶炼过程中的酸浸渣为处理对象,采用硫化焙烧新工艺对锌浸渣进行处理,考察了硫化焙烧温度、反应时间以及黄铁矿添加量对锌浸渣硫化率的影响。
研究结果表明在硫化温度为900℃、硫化时间60min和黄铁矿添加量为30%时,锌的硫化率可达91%以上。
关键词:锌浸渣;硫化焙烧;黄铁矿;硫化率1.前言硫化锌精矿中锌常与含铁硫化矿物夹杂共生,铁在硫化矿石中主要以铁闪锌矿(mZnS•nFeS)或硫铁矿(FeS2,FeS,CuFeS2)的形态存在[1]。
在锌精矿氧化焙烧过程,锌、铁分别被氧化为氧化锌(ZnO)和三氧化二铁(Fe2O3),当温度过高,ZnO和Fe2O3极易发生固溶现象,铁酸锌(mZnO•nFe2O3)会不可避免的生成[2, 3]。
铁酸锌具有典型的尖晶石结构,性质极其稳定,难以溶解于稀硫酸溶液。
因此在酸性浸出工序,很大一部分的锌以铁酸锌的形式残留于浸出渣中,导致锌回收率不足80%[4]。
因此浸出渣中的这部分锌需要采取合适的技术对其进行资源回收。
目前,针对冶炼工艺中铁酸锌生成的普遍性,国内外学者对含铁酸锌物料资源化展开了大量的研究,开发了一系列的锌、铁及其他有价金属回收技术。
按照分离工艺的不同,大致可分为火法处理、湿法处理、火法-湿法联合处理及选冶联合处理四大类。
但因铁酸锌稳定的尖晶石结构,常规的上述方法难以将铁锌分离,从而导致锌铁资源流失。
现有的含铁酸锌物料资源化技术,由于存在各种问题而无法大规模推广。
传统火法技术能耗高、设备损耗大、铁资源难以回收。
而湿法技术中酸性浸出存在后续沉铁工序复杂,沉铁渣难以资源化等难题,碱性浸出存在锌溶出率不高,设备损耗大等难题。
因此,将含铁酸锌物料作为二次资源回收其中的锌铁对充分利用资源、延缓矿物资源的枯竭和保护环境具有重大意义,迫切需要一种同时实现锌铁资源化的新技术。
硫化焙烧目前广泛应用于低品位的氧化矿的处理,但是该方法也为火法铅锌冶炼废渣资源化提供了一个新的思路。
- 1、下载文档前请自行甄别文档内容的完整性,平台不提供额外的编辑、内容补充、找答案等附加服务。
- 2、"仅部分预览"的文档,不可在线预览部分如存在完整性等问题,可反馈申请退款(可完整预览的文档不适用该条件!)。
- 3、如文档侵犯您的权益,请联系客服反馈,我们会尽快为您处理(人工客服工作时间:9:00-18:30)。
5 酸 平 衡 措 施
加压 氧浸 过程 中 的产 酸反 应 主 要是 精 矿 硫化 物
中的硫被 直 接氧化 成硫 酸盐 中的硫 。 加压 氧 浸 过 程 中 的耗 酸 反 应 主 要 是 精 矿 中 的
3 原料 中的耗酸元素
浸 出过程 消耗 的硫 酸通 中的游 离 酸 及 外加 硫 酸 , 矿 中 的金 属 组分 分 精
+2 2 H0
中。
() 4
国内已投产或正在建设 的锌加压氧浸工厂有 : 云南
冶 金 集 团 的 系列 小 规模 氧 压 浸 出 工 厂 、 霞 冶 炼 厂 丹 10k/ 0 ta电锌 氧 压 浸 出工 厂 、 部 矿 业 10k/ 西 0 ta电 锌氧 压浸 出工 厂 、 伦 贝尔 驰 宏 矿 业 有 限 公 司 20 呼 0
含铁 高 的浸 出液 。从 含铁 高 的浸 出液 中沉 铁 的方 法 主要有 黄钾 铁矾 法 、 铁 矿法 、 铁 矿 法等 l 。加 压 针 赤 6 1 浸 出液一般 采用 针铁 矿法 沉铁 l 。 针 铁矿 沉铁 反应式 :
2 e +3 2 F H 0+0 5 2 .0 — 2 e H+4 ( 1 F 00 H 1)
因此 , 湿法 炼 锌 过 程 的耗 酸 量 取 决 于 浸 出物 料
中的铅 、 、 的含 量 以及 铁 在浸 出液 中 的含 量 和溶 钙 钡 液 除铁方 法 。
在对 浸 出 液进 行 针 铁 矿 沉 铁 时 , 择 锌 焙 砂 为 选
4 浸 出液沉 铁 过程 中的耗 酸分 析
通过设 定 加 压 氧 浸 的工 艺 条 件 , 以控 制 浸 出 可
F S 的氧化程 度 取 决 于 浸 出 条件 , 强 氧化 气 e: 在
氛及高 温下 , 氧化 生成硫 酸盐 。 被
2 e 2+7 5 +H2 FS . 02 0一 F 2 S 43 。 ( O ) +H2 O4 S
系统溶 液 中的金 属 平 衡 、 积 平 衡 和 渣 平 衡 。而 与 体 其他 湿 法 炼 锌工 艺 不 同的是 , 压 氧浸 工 艺 的产 酸 加 及耗 酸机 理 有 其 自身 的一 些 特 点 。 因此 , 必要 对 有 锌加 压 氧 浸 工 艺 的酸 平 衡 进行 分 析 , 以指 导 工 艺路
[ j K R B bn M oisIM Matr.rncnrlnz cpesr 3 ua , JC ln , sesIo o t i rs e l oi n u
lahpoesJ .OM,9 9 5 (2 :3—2 . ec rcs[] J 19 , 1 1 )2 5 [ ] 利选民 . 法 炼锌 中酸 的平 衡 [ ] 有 色 金 属 ( 4 湿 J. 冶炼 部 分 ) ,
硫 化锌 精矿 加压 氧浸 工艺 是将 硫 化锌 精 矿在 硫 酸溶 液 中直 接加 压氧化 成硫 酸 锌溶 液 的湿 法 炼锌 工 艺, 与常规 湿法 炼锌 工艺 相 比 , 压氧 浸 工艺 具 有流 加 程短 、 原料 适应 性强 、 环保 、 综合 回收 效果 好 等 特点 。 20 09年 9月 , 国内第 一座 10k/ 0 ta锌加 压 氧 浸 车 间
合 的加 压氧浸 系统 , 一般 采 用锌 焙砂 作 为 中和剂 , 可
[ ] 李有 刚, 1 李波 . 锌氧压浸出工艺现状及技术进展 [ ] J .中国有 色 冶金 ,0 0 3 ( )2 2 1 ,9 3 :6—2 . 9 [ ] 仝一 器 . 氧压 浸 出工艺 的应 用及 推 广 [ ] 矿 冶 ,0 1 2 2 锌 J. 2 1 ,0
为 两类 : 类 与硫 酸 反 应 生 成 不 溶 盐 , 铅 、 、 一 如 钙 钡
铅 、 、 等组 分 形 成 了不 溶 性 硫 酸 盐 , 钙 钡 以及 后 续 工 段加 入 的石灰 石 中和剂形 成 了石膏 渣 。
因此 , 主要应从 控制加 压氧 浸 的工艺条 件 以及选
等; 另一 类与 硫 酸 反 应 生 成 可 溶 性 盐 , 如锌 、 、 、 铁 铜 镉 、 、 等。 镍 钴
锌在 从浸 出到 电积 的湿 法炼 锌 全 过程 中理 论 上
择合适 的中和剂这两方 面人手 , 对酸平衡 进行调节 。
5 1 控 制浸 出工 艺条件 . 在强氧 化气 氛 及 高 温 下 , e , 氧 化 生 成 硫 酸 FS 被
是不 耗酸 的 。铁 的耗 酸 情 况 , 随浸 出液 除铁 方 法 的 不 同而不 同 J 4。对 于铜 、 、 、 等组 分 , 镉 镍 钴 由于采 用 锌 粉 置换 的净 化 方法 , 与转 换 它 们 的当 量金 属 锌 参
() 3
通常, 在锌 精 矿 中有 足 够 可 溶 于 酸 的 铁 来 满 足 浸 出需 要 。 此 外 , u e 2中的铜 也被 浸 出 : C FS
CuFe 2+O2+2H2 O4— CuS04+Fe O4+ 2S S S S u
产达 标 _ , 1 引起 了行业 内的广泛 关 注 , 国内锌 冶 炼 J 为 工业 的清洁生 产 、 术升 级 提供 了一个 方 向。 目前 , 技
M 代表 z 、b c n P 、 u和 F 。在 浸 出过 程 中 , e 随着 酸 度 的降低 , 成 了水 合铁 氧 化物 及矾 渣 , 形 由水解 反
应从 溶液 中除 去铁 , 同时 , 又生成 一些硫 酸 : F 2 S 4 3 x +3 H O_ +F 2 3 XH O+ e ( O ) +( ) 2 _ eO ・ 2
中和掉 浸 出过程产 生 的酸 、 护 系统 的动态 酸平衡 。 维
参 考文 献 : 、
在沉 铁 过 程 中 , H 值 控 制 在 3~3 5之 间 , D . 因 此, 需要 加 入 中和剂 中 和沉 铁 反 应 产 生 的酸 。沉 铁
反 应采 用 的 中和 剂 一 般 为 锌 焙 砂 ( n 、 氧 化 锌 Z O)次 烟尘 或石 灰石 ( a 。如 果 是 与 常规 沸 腾 焙 烧 相 结 C O)
在丹 霞 冶 炼 厂 建成 投 产 , 在 较 短 时 间 内实 现 了达 并
Z S e( O ) 一 n +F 2 S 43
Z S 4 FS 4 。 () n O +2 e O +S 2
2 e O +H 8 4 .0 — 。( O ) +H 0 F S 4 2 0 +0 5 2 F 2S 43 2
3 8
湖 南有 色金属
HUNAN NONFE RROUS M E TAL S
第2 8卷第 2期
21 0 2年 4月
硫化锌精矿加压氧浸工艺的酸平衡分析
仝一枯 , 陈龙义
( 沙有 色冶金设计研究院有限公司 , 南 长沙 4 0 1 ) 长 湖 10 1
摘 要: 硫化锌精矿加压氧浸工艺的酸平衡除了与精矿中耗酸组分有关外 , 与浸 出条件 以及中和 还
k/ 铅锌 冶炼 厂等 l ta 。 与所有 的湿 法 炼 锌 工 艺 一 样 , 压 氧 浸 工 艺 的 加 酸平衡 直 接影 响锌冶 炼 系统 的“ 三大 平衡 ” 问题 ——
浸 出过程 中 ,b P S在 高酸 下 形成 P S 进 入 渣 bO ,
2 加压氧浸过程 中的产酸机理
3 2O HS4 () 9
第 2期
仝一 菇 , : 等 硫化 锌精 矿加 压氧 浸 工艺 的酸平衡 分 析
2 3 F 3( O )- H O e S 42 ( 0 1)
3 9
3 e( O ) F 2 S 4 3+ 1 H 0 — 42 ( H) +5 2 0 O 6 HS4
中和反 应产 生 了石膏渣 , 是耗 酸反 应 。
( 4):4—9 9 7.
以得 到含 铁较 高 的 中和 渣 。如果 是 新 建 的独 立 加 压
氧 浸系 统 , 由于锌 焙砂 的来 源 问题 , 般采 用 石 灰 石 一 作 为 中和剂 。 以锌 焙砂 为 中和剂 时 , 中和反 应为 :
Z O+H S 4 n 0 +H 0 n 2 O —— z S 4 2 ( 2 1)
剂 的选择有关 。控制浸出条件和选择合适的沉铁 中和剂有助于维护整个生产系统的动态酸平衡 。
关 键 词 : 压 氧 浸 ; 法炼 锌 ; 平衡 ; 加 湿 酸 除铁 ; 中和 剂 中 图分 类号 : F 0 . 1 T 832 文献标识码 : A 文章 编 号 :0 3 50 2 1 )2 0 8 2 10 —5 4 (0 20 —0 3 —0
6 结
语
硫化 锌精 矿 的加 压 氧 浸 过 程 是 一 个 产 酸 过 程 ,
产 酸量取 决 于浸 出工艺 条件 。在对 浸 出 液进 行 沉铁
时 , 以搭配 使用锌 焙砂 和 石灰 石 为 中和 剂 , 根据 可 并 实 际情 况 调 整 和 选 择石 灰 石 中和 剂 的最 佳 比例 , 以
积 工段 是有 利 的。
液 中的铁 含量 在 06—18gL 以尽 量 减 少 后 续 除 . . / , 铁工 段 的负 荷 _ 。但 如 果 精 矿 中铅 和银 的含 量 较 5 J 高 , 值得 在浸 出过 程 中限制 铁 的沉 淀 , 就 以便 从 浸 出 渣分 离高 品位 的铅银 产 品 , 样 的话 , 会得 到一 个 这 就
线选 择 和实 际生产操 作 。
() 5
2 e2 .0 +4 2 F S +7 5 2 H 0— 。0 +4 2 0 ( ) F 2 3 H S 4 6
而在弱 氧化气 氛 、 温及 高 酸下 , 氧 化生 成 元 低 被 素硫 [ : ]
Fe S2+ 0. 502+ H2 SO4— — Fe S04+ H2 +2S 0 u
中和剂 , 会对 整个 生产 系统 带来 酸 耗 ; 不 而选 择 石 灰
石 为 中和剂 , 会 从 系 统 中 带走 硫 酸 。 如 果 浸 出 液 则