高铁硫化锌精矿加压浸出工艺
氧压浸出[详细讲解]
![氧压浸出[详细讲解]](https://img.taocdn.com/s3/m/306e7913eef9aef8941ea76e58fafab069dc443f.png)
9.2氧压浸出的-I-艺流程硫化锌精矿氧压浸出流程分一段氧压浸出和二段氧压浸出。
一段氧压浸出为加压浸出与焙烧、浸出、电积的联合流程,二段氧压浸出为独成一体的浸出工艺,其原理流程见图9—1、图9—2。
氧压浸出工艺过程分物料准备、压浸、闪蒸及调节、硫回收等工序。
物料准备工序是通过湿式球磨使锌精矿粒度达到45/an,球磨矿浆经分级使矿浆含固量为70%。
在矿浆中加入添加剂,其作用是防止熔融硫包裹硫化锌精矿而阻碍锌的进一步浸出。
锌精矿图9—1氧压浸出联合流程图将球磨后的矿浆及废电解液加人压力釜,通人氧气,控制温度150t,氧压700kPa,反应时间lh,硫化锌中硫被氧化成元素硫,锌成为可溶硫酸锌。
锌的浸出率可达到97%-99%。
闪蒸及调节:将压力釜浸出后的矿浆加入闪蒸及调节槽,力釜中生成的元素硫是熔融状态,矿浆进入闪蒸槽后,控制温度120~C,保持熔融状态的硫。
从闪蒸槽中可回收蒸汽供生产使用,矿浆再进人调节槽冷却,控制温度100~C,使元素硫成固态冷凝。
调节槽冷却后的矿浆送人浓密机浓缩,浓缩上清液送往净化、电积、熔铸生产电锌,浓密机底流送硫回收工序。
硫回收工艺是将浓密机底流进行浮选回收硫精矿,浮选尾矿经水洗后送渣场堆存。
含硫精矿送人粗硫池熔融,再通过加热过滤,从未浸出的硫化物中分离出熔融元素硫,然后将熔融硫送人精硫池产出含硫大于99%的元素硫。
加热过滤所产的过滤渣含有的稀有金属和贵重金属待回收。
9.3氧压浸出装置氧压浸出高压釜是由碳钢作外壳,用铅及耐酸砖做内衬。
高压釜内用隔板隔成4—6个室,每个室内配有机械搅拌槽(图9—3)。
球磨后的矿浆经分级使矿浆含固量为70%,加入浸出添加剂后,泵人高压釜第l室。
浸出添加剂能使熔融硫呈疏散球状,防止熔融硫包裹硫化锌精矿而阻碍浸出时锌的进一步浸出。
废电解液分别泵人高压釜第1室、第2室,同时向釜内通人浓度98%以上的氧气,控制反应温度150~C,氧分压0.7MPa,釜压1.1MPa,反应时间1-1.5h,进行连续浸出,使硫化锌中硫被氧化成元素硫,锌成为可溶硫酸锌。
硫化锌精矿加压浸出元素硫的形成机理及硫回收工艺的研究

硫化锌精矿加压浸出元素硫的形成机理及硫回收工艺的研究
硫化锌精矿加压浸出元素硫的形成机理及硫回收工艺的研究是一项重要的研究内容,它主要是用于研究如何从硫化锌精矿中进行硫的回收。
首先要明确的是,硫化锌精矿中的硫是一种天然的元素,它是通过地壳中的火山活动和热液作用而形成的,随着时间的推移,它被地壳中的其他元素所包围,成为一个组合物,形成硫化锌精矿。
由于硫化锌精矿中的硫元素是非常稳定的,因此要想从硫化锌精矿中回收硫,就必须采用加压浸出工艺。
加压浸出工艺是将硫化锌精矿通过高压和高温条件下放入特定溶液中,使硫元素从矿石中解离,并被溶液所吸收,达到回收硫元素的目的。
加压浸出工艺中,主要有三个关键因素:压力、温度和溶剂。
硫化锌精矿中的硫元素解离的难易程度,主要取决于这三者的配比,当它们的比例达到一定的标准时,硫元素就能够被有效地解离出来。
硫的解离一般都会产生大量的气体和液体,因此,在加压浸出过程中,必须采用一定的控制方法,避免产生大
量的废气和废液。
此外,为了保证浸出效果,还需要添加一定的辅助试剂,以增强加压浸出工艺中的作用。
在硫回收工艺中,主要采用的是“蒸馏法”,即将溶液中的硫元素以蒸气的形式蒸发出来,再通过冷凝的方式回收硫元素,最后通过冷却来回收冷凝液体中的硫元素。
总之,硫化锌精矿加压浸出元素硫的形成机理及硫回收工艺的研究,是一项重要的研究内容,它主要是用于研究如何从硫化锌精矿中进行硫的回收。
要实现这一目标,除了需要做好加压浸出工艺及蒸馏法的研究外,还需要考虑到溶液中硫元素解离的机理,以及硫元素回收时的效率问题等。
硫化锌精矿的加压酸浸(一)
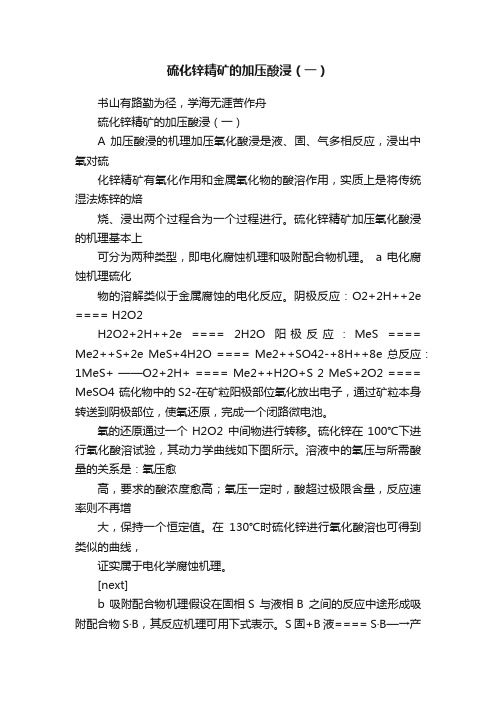
硫化锌精矿的加压酸浸(一)书山有路勤为径,学海无涯苦作舟硫化锌精矿的加压酸浸(一)A 加压酸浸的机理加压氧化酸浸是液、固、气多相反应,浸出中氧对硫化锌精矿有氧化作用和金属氧化物的酸溶作用,实质上是将传统湿法炼锌的焙烧、浸出两个过程合为一个过程进行。
硫化锌精矿加压氧化酸浸的机理基本上可分为两种类型,即电化腐蚀机理和吸附配合物机理。
a 电化腐蚀机理硫化物的溶解类似于金属腐蚀的电化反应。
阴极反应:O2+2H++2e ==== H2O2H2O2+2H++2e ==== 2H2O 阳极反应:MeS ==== Me2++S+2e MeS+4H2O ==== Me2++SO42-+8H++8e 总反应:1MeS+ ——O2+2H+ ==== Me2++H2O+S 2 MeS+2O2 ==== MeSO4 硫化物中的S2-在矿粒阳极部位氧化放出电子,通过矿粒本身转送到阴极部位,使氧还原,完成一个闭路微电池。
氧的还原通过一个H2O2 中间物进行转移。
硫化锌在100℃下进行氧化酸溶试验,其动力学曲线如下图所示。
溶液中的氧压与所需酸量的关系是:氧压愈高,要求的酸浓度愈高;氧压一定时,酸超过极限含量,反应速率则不再增大,保持一个恒定值。
在130℃时硫化锌进行氧化酸溶也可得到类似的曲线,证实属于电化学腐蚀机理。
[next]b 吸附配合物机理假设在固相S 与液相B 之间的反应中途形成吸附配合物S·B,其反应机理可用下式表示。
S 固+B 液==== S·B—→产物吸附配合物的形成是过程的最缓慢阶段,为过程速率的控制步骤。
过程的反应动力学可以推导如下:设Q 为形成吸附配合物过程中参与反应的部分,1 - Q = 没有参与反应的游离部分设形成配合物的速率ξ1为ξ1= K1(1-Q)[B]n 设配合物分解(成组分)的速率ξ2为ξ2= K2Q 设配合物分解(成产物)的速率ξ3为ξ3= K3Q 式中,K1,K2,K3 均为速率常数。
硫化锌精矿的加压酸浸(一)

书山有路勤为径,学海无涯苦作舟硫化锌精矿的加压酸浸(一)A 加压酸浸的机理加压氧化酸浸是液、固、气多相反应,浸出中氧对硫化锌精矿有氧化作用和金属氧化物的酸溶作用,实质上是将传统湿法炼锌的焙烧、浸出两个过程合为一个过程进行。
硫化锌精矿加压氧化酸浸的机理基本上可分为两种类型,即电化腐蚀机理和吸附配合物机理。
a 电化腐蚀机理硫化物的溶解类似于金属腐蚀的电化反应。
阴极反应:O2+2H++2e ==== H2O2H2O2+2H++2e ==== 2H2O 阳极反应:MeS ==== Me2++S+2e MeS+4H2O ==== Me2++SO42-+8H++8e 总反应:1MeS+ ——O2+2H+ ==== Me2++H2O+S 2 MeS+2O2 ==== MeSO4 硫化物中的S2-在矿粒阳极部位氧化放出电子,通过矿粒本身转送到阴极部位,使氧还原,完成一个闭路微电池。
氧的还原通过一个H2O2 中间物进行转移。
硫化锌在100℃下进行氧化酸溶试验,其动力学曲线如下图所示。
溶液中的氧压与所需酸量的关系是:氧压愈高,要求的酸浓度愈高;氧压一定时,酸超过极限含量,反应速率则不再增大,保持一个恒定值。
在130℃时硫化锌进行氧化酸溶也可得到类似的曲线,证实属于电化学腐蚀机理。
[next]b 吸附配合物机理假设在固相S 与液相B 之间的反应中途形成吸附配合物S·B,其反应机理可用下式表示。
S 固+B 液==== S·B—→产物吸附配合物的形成是过程的最缓慢阶段,为过程速率的控制步骤。
过程的反应动力学可以推导如下:设Q 为形成吸附配合物过程中参与反应的部分,1 - Q = 没有参与反应的游离部分设形成配合物的速率ξ1为ξ1= K1(1-Q)[B]n 设配合物分解(成组分)的速率ξ2为ξ2= K2Q 设配合物分解(成产物)的速率ξ3为ξ3= K3Q 式中,K1,K2,K3 均为速率常数。
当n=1 反应。
高铁硫化锌精矿催化氧化直接酸浸新工艺的开发及产业化(一)

计, 国外 有 加拿 大 、 德 国、 南菲 、 韩国、 哈 萨克斯 坦 等 ;
国 内也 有 1 - 2 家 处 于起步 阶段 。
Hale Waihona Puke 剂, 即木质 素 磺 酸盐 , 由原 轻 工业 部劳 保所 提 供 , 为 木材 和稻 草造 纸厂 的副产物 , 是 一种 大 网络分 子 , 可 在 颗 粒 群 中架 起 “ 立交 桥 ” 。早 在 1 9 8 2 年 的锌 精 矿
0 . 9 x 4 . 8 m, 总体积 4 . 2 4 I n , 四室 , 依放热过 程设计
其 中一 室 大 , 装 置 2台搅 拌机 , 有 别 于 国外 。此 外 ,
【 作者简介] 夏光祥( 1 9 3 4 一) , 男, 山东人 , 研 究员 , 长期从事湿法 冶
金研究工作 。 [ 收稿 日期】 2 0 1 2 — 0 7 — 1 9
合 同 中指 定 的云南 澜沧 铅矿 的浮 选锌精 矿 成份
1 9 9 9 年3 月, 云 南冶 金集 团 总公 司与 我所 洽谈 合
作, 就《 高铁 硫化 锌精 矿直 接酸 浸新 工艺 开发及 产业 化》 与 云南 省 院 省 校 科 技 办 签 定 协 议 , 项 目编 号 为 Y K 9 9 0 1 1 。此后 课 题 组 便 开 始 了 一 系列 工 作 , 包 括 探 索实验 ( 1 9 9 9年 9 月) 、 系 列 催 化 氧 化 酸 浸 实 验 ( 2 0 0 0 年3 月) 、 扩大实验( 2 0 0 0 年7 月) 、 1 . 5 t / d 半 工 业 主体设 备 稳 定 运 转 一个 月 的试 验 ( 2 0 0 2 年 2月 ) , 最 终 完 成半 工 业试 验 报 告及 3 O t , d 规 模 的 可行 性 研
锌精矿常压浸出与加压浸出工艺比较

了加压与常压浸出试验。试验条件见表2,在该条件 下得到的锌精矿浸出率见表3It]。 在常压浸出的间断试验中,精矿粒径在23¨m 以下时24 h能获得95%的浸出率。从表3可以看 出.精矿的粒度对浸出率影响较大。对比试验可得 出结论:加压浸出要求锌精矿经球磨后90%的粒度 达到44
pLm,1
4技术经济指标
图2
IIBMS锌厂二段氧压浸出工艺流程图
(2)搅拌桨在釜下密封,需要定期更换、清洗、补
漏,需要备个大槽子放空溶液。 (3)釜敞开,溶液温度要保持90℃,热损失较大, 不能回收利用。
硫,总硫回收率达88%。得到的铅银渣品位高(送铅 冶炼系统),可综合同收稀散金属。常压浸出锌的浸 出率在98%左右,回收率97%.产出的硫渣含硫
氢气 ——
氧气
(1)加压浸出对原料的C1、F含量有严格要求, 因为高压釜的内衬为耐磨板,易被cl一、F一破坏。 (2)因为元素硫在134。C粘度最低,在高压釜和 管道内容易结疤,影响生产。 (3)闪蒸槽的解压阀阀杆磨损较快,即使用最 耐磨的K台金,也仅用一个星期就需要修补。 5.2常压浸出 (1)浸出效率低,需要22—24 h才能达到加压2 h的浸出率。
30.6%,S 53.7%,该公司用粒径不同的锌精矿分别做
锌精矿
图1科科拉常压浸出工艺流程图 氧压程出工艺以加拿大HBMS矿业公司锌厂
为例,其工艺包括精矿球磨、调浆、一段低酸压浸、
浓密、上清液除钙除铁、常规净化、电解、熔铸工序。 一段低酸浸出矿浆浓密后底流经二段高酸浸出,再 浓密,浓密上清液进一段浸出,底流经洗涤过滤等 工序,整个生产过程是连续的,流程图如图2所示。
::::
士苎童鱼兰垒
目茎垒量
锌精矿常压浸出与加压浸出工艺比较
硫化锌精矿加压氧浸回收有价金属的工艺
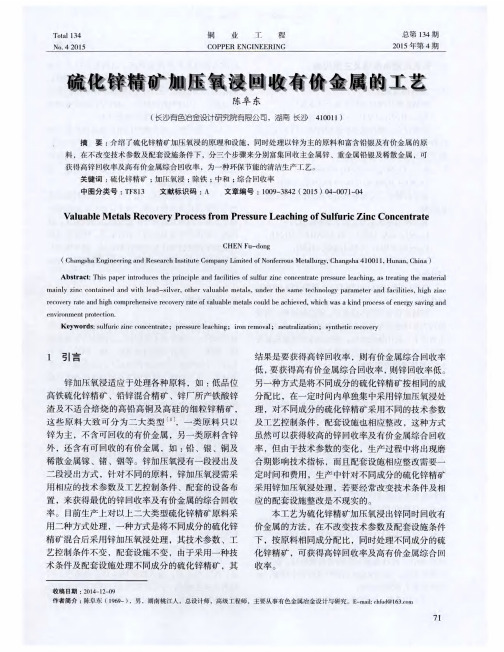
反应器将只含锌的硫化锌精矿中锌浸出 ,利用反应
器 同时除铁 ,得到 一种 铁渣 ,将 铁及 脉石成 分 与主
金属锌分离 ,铁渣堆存 。三步骤将浸出溶液中的稀 散金属利用中和剂富集到中和渣 中,中和渣送稀散 金属 回收,浸出溶液中锌送后续工序 回收锌。三个
+ 5 H2 S O 4
P b S O 4 + 3 F e 2 ( S O 4 ) 3 + 1 2 H 2 O_ P b F e 6 ( S O 4 ) 4 ( 0 H) 1 2
+ 6 H2 S O 4
3 工艺方案
不 同成分 的硫 化锌 精 矿需 回收 的有用 成分 主要
锌精 矿在 氧 压浸 出过 程 中 ,铁会 被溶 解 ,而铁 的行 为 可 以通 过 浸 出液 的酸度加 以控制 ,在 高温 高
压条件下 , 采用低酸浸出,能形成水合铁氧化物及 矾渣 ,由水解反应从溶液 中除去铁 。
2 . 2 氧压 浸 出主要 设施
有三部分 : 一部分为主金属锌 ,二部分为含重金属 铅 、银 等 ,三部 分 为稀 散 金属镓 、锗 、铟等 。本 工 艺分三个步骤来分别富集 回收以上有价金属 ,一步 骤利用一个反应器 ,将含锌及有价金属的硫化锌精 矿 中大部分锌及稀散金属浸出到溶液中,而得到一
的反 应是 以下二 个反 应之 和 :
Z n S+F e 2 ( S O 4 ) 3 Z n S O 4 + 2 F e S O 4 +S
2 F e S O 4 +H2 S O 4 + 1 / 2 O 2 F e 2 ( S 0 4 ) 3 +H 2 O
通常锌精矿含有足够可溶于酸的铁以满足浸出 的需要 。
高铁硫化锌精矿加压浸出技术应用
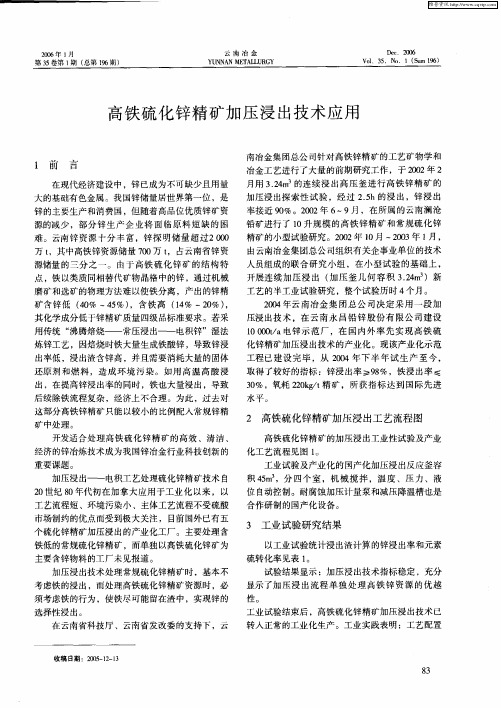
开发适合处理高铁硫化锌精矿的高效 、清洁 、 经济的锌冶炼技术成为我代经济建设 中,锌已成为不可缺少且用量 大的基础有色金属。我国锌储量居世界第一位 ,是 锌的主要生产和消费国,但随着高品位优质锌矿资 源的减少 ,部分锌生产企业 将面临原料短 缺的困
难 。云南 锌 资 源 十分 丰 富 ,锌探 明 储 量 超 过 200 0
铅矿进行 了 1 0升规模 的高铁锌精矿和常规硫化锌 精矿的小型试验研究。20 年 l 月 ~ 03 1 , 02 0 20 年 月
2O 年 1 06 月
云 南 冶 金
YUN NAN M肼 AL _ -URGY I
De c.2 0 O6
第 3 卷第 1 ( 5 期 总第 1 期 ) 9 6
V 1 5 o 1(u 9 ) o.3 .N . S m 16
合理 ,工艺流程顺畅 ,技术指标稳定 ,压力釜运行
安全可靠 ,自动控制系统灵敏 ,彻底摆脱了传统湿
其化学成分低于锌精矿质量 四级品标准要求 。若采 用传 统 “ 腾焙烧 —— 常压 浸 出— — 电积锌 ”湿 法 沸
炼锌 工艺 ,因焙 烧 时铁 大 量生成 铁 酸锌 ,导致 锌浸
出率低,浸 出渣含锌高,并且需要消耗大量 的固体
还原剂和燃料 ,造成环 境污染。如用 高温高酸浸 出,在提高锌浸出率的同时 , 铁也大量浸出,导致 后续除铁流程复杂 ,经济上不合理。为此 ,过去对
重要课 题 。
- 1、下载文档前请自行甄别文档内容的完整性,平台不提供额外的编辑、内容补充、找答案等附加服务。
- 2、"仅部分预览"的文档,不可在线预览部分如存在完整性等问题,可反馈申请退款(可完整预览的文档不适用该条件!)。
- 3、如文档侵犯您的权益,请联系客服反馈,我们会尽快为您处理(人工客服工作时间:9:00-18:30)。
高铁硫化锌精矿加压浸出新工艺瞿仁静王晓曼鲁艳梅(云南省冶金研究设计院,云南昆明650031)摘要:高铁硫化锌精矿加压浸出冶炼工艺与传统工艺不同,锌精矿焙烧过程发生的氧化反应和锌焙砂浸出过程发生的酸溶反应合并在一起进行,主体设备为高压釜。
该技术较传统工艺节能30%,锌浸出率≥95%,铁浸出率≤30%,浸出指标好,有广阔的发展前景。
本文介绍了这种工艺的原理、流程、特点以及该新兴工艺在工业上的具体应用。
关键词:高铁硫化锌精矿;加压浸出;节能;环保;锌浸出率;铁浸出率。
New Process of Pressure Leaching on High-ironZinc-sulphide ConcentrateQu Renjing Wang Xiaoman Lu Yanmei(Yunnan Metallurgical Research and Design Institute, Kunming, Yunnan 650031, China) ABSTRACT:Different with the traditional process, pressure leaching on high-iron zinc-sulphide concentrate combines the oxidation reaction occurs zinc concentrate roasting process and the acid-soluble reaction occurs zinc calcine leaching process together, and the main equipment is autoclave. The process saves 30% energy compared with traditional technology, and with the high rate of zinc leaching processes. Zinc leaching rate is greater than or equal to 95%, iron leaching rate is less than or equal to 30%, leaching index was better, and has broad prospects for development. The principles, processes, characteristics and the industrial applications of this new technology were described.KEYWORDS:high-iron zinc sulphide concentrate;pressure leaching;energy saving;environmental protection;zinc leaching rate;iron leaching rate1 前言在现代经济建设中,锌已成为不可缺少且用量大的基础有色金属。
我国锌储量居世界第一位,云南锌资源十分丰富,锌探明储量超过2000万t,其中高铁锌资源储量700万t,占云南锌资源储量的三分之一。
高铁硫化锌精矿中,铁以类质同相替代矿物晶格中的锌,通过机械磨矿和选矿的物理方法难以使铁分离,产出的锌精矿含锌低(40~45%),含铁高(14~20%),其化学成分低于铁精矿质量四级品标准要求。
采用传统湿法炼锌工艺,焙烧时铁大量生成铁酸锌,锌浸出率低,浸出渣含锌高。
采用高温高酸浸出,虽提高锌浸出率,但铁大量浸出,导致后续除铁流程复杂,经济上不合理。
为此,开发适合处理高铁硫化锌精矿的高效、清洁、经济的锌冶炼技术成为我国锌冶金行业科技创新的重要课题。
国内对氧化锌精矿加压浸出技术进行了一系列研究,上世纪80年代末,北京矿冶研究总院、株洲冶炼厂和加拿大舍利特研究中心合作进行锌精矿氧压浸出试验研究,取得一定的研究成果,由于各方面原因,没有实现工业化应用。
1993年10月,北京矿冶研究总院经过多年的研究,率先将高冰镍加压浸出技术在新疆阜康冶炼厂实现工业化生产,为国内加压浸出技术的发展积累了经验。
2001年起,云南冶金集团总公司进行了高铁硫化锌精矿加压浸出技术新工艺的小型及半工业试验研究,取得了预期的技术经济指标,为该项目的产业化奠定了基础。
2002年6~9月,云南冶金集团总公司在云南澜沧铅矿进行了10升规模的高铁锌精矿和常规硫化锌精矿的小型试验研究。
2002年l0月~2003年1月,在小型试验的基础上,开展连续加压浸出(加压釜几何容积3.24m3)新工艺的半工业试验研究。
2004年,云南冶金集团总公司采用一段加压浸出技术,在云南永昌铅锌股份有限公司建设10000t/a电锌示范厂。
2007年6月,在澜沧铅矿采用两段加压浸出工艺建设20000t/a电锌示范厂。
2009年,该工艺应用于云南建水光慈有限公司100000t/a电锌示范厂和云南驰宏呼伦贝尔140000t/a电锌示范厂的建设中,进一步完善了加压浸出处理高铁硫化锌精矿工艺。
该工艺以流程短、环境污染小、主体工艺流程不受硫酸市场制约的优点受到极大关注。
加压处理高铁硫化锌精矿,必须考虑铁的行为,使铁尽可能留在渣中,实现锌的选择性浸出。
2 工艺简介高铁硫化锌精矿氧压浸出,是在温度为140~150℃,氧分压0.8~1.3Mpa的条件下,将高铁硫化锌精矿直接浸出的工艺。
在锌浸出过程中,矿物晶格中的铁也部分浸出,并作为氧的传递载体加速锌的浸出,在浸出结束后,铁大部分以铁矾形态沉淀留在渣中,从而实现锌的选择性浸出。
高铁硫化锌精矿中的铁可作为催化剂,达到趋利避害的目的,解决了其他炼锌工艺受到铁杂质干扰的难题,是一种新兴的环保型工艺。
高铁硫化锌精矿氧压浸出工艺根据基础条件的不同,分为两种工艺路线:一段加压浸出和两段加压浸出。
对于已有焙烧—浸出—电解锌生产厂,可采用一段加压浸出工艺进行技术改造,扩大产量;对于新建的处理高铁硫化锌精矿厂,采用两段加压浸出工艺。
采用氧压浸出工艺处理高铁硫化锌精矿,锌浸出率≥95%,铁浸出率≤30%,氧耗220kg/t精矿,硫以元素硫形态产出,所获指标达到国际先进水平。
3 工艺原理、流程氧压浸出的实质是将锌精矿焙烧过程发生的氧化反应和锌焙砂浸出过程发生的酸溶反应合并在一起进行。
为了加速反应的进行,在锌精矿焙烧过程中,采用提高温度的办法来增大反应速度常数。
而在氧压浸出时,除了适当提高反应温度至140~150℃外,则主要是采用具有较高的氧分压。
由于所用氧浓度增大,在质量作用定律支配下,锌精矿的氧化反应速度也大大地提高了。
加压浸出以铁闪锌矿[Zn·nFe]S为主的高铁锌精矿时,其中的硫化锌按(1)式反应,锌以硫酸锌的形态浸出进入溶液。
由于铁以类质同相替代闪锌矿晶格中的锌,形成部分FeS,在高温加压浸出时按反应(2)生成硫酸亚铁FeSO4,然后进一步按反应(3)氧化为硫酸铁Fe2(SO4)3,硫酸铁与铁闪锌矿中的硫化锌矿物按反应(4)进行生成硫酸锌和硫酸亚铁,硫酸亚铁又按反应(3)再生为硫酸铁。
因此,铁闪锌矿中的铁经加压浸出后形成的三价铁是氧的传递载体,是锌浸出的催化剂,加速锌的浸出。
ZnS+H2SO4+0.5O2=ZnS04+S+ H2O (1)FeS+H2SO4+0.5O2=FeSO4+S+H2O (2)2FeSO4+H2SO4+0.5O2=Fe2(S04)3+H2O (3)Fe2(SO4)3+ZnS=2FeSO4+ZnSO4+S (4)反应(2)在直接加压浸出锌的同时,不断提供硫酸亚铁。
反应(4)使浸出过程中形成的硫酸亚铁间接浸出硫化锌,并通过反应(3)使直接浸出和间接浸出产生的硫酸亚铁氧化为硫酸铁,实现间接浸出剂硫酸铁的再生,使间接浸出贯穿整个浸出过程。
现介绍两段加压浸出工艺流程。
第一段加压浸出采用低酸浸出(约50%的锌被浸出),然后进行第二段高酸加压浸出,第二段的浸出液返回第一段。
第一段加压低酸浸出产出的浸出液(锌120~130g/L、含铁2~3.5g/L、含酸3~5g/L),经氧化水解除铁,除铁后液直接进入溶液净化工序;第二段加压浸出处理第一段加压浸出的浸出渣,使渣含锌降至2%以下,其浸出液返回到第一段高压釜;第二段浸出渣经过浮选,产出元素硫精矿;银富集在铅银渣中另行处理,弃渣堆存。
4 设备传统锌冶金采用流态化焙烧炉、浸出槽、净化槽、电解槽等设备,需要建设配套的焙烧车间和制酸厂,锌浸出率低。
空气污染严重。
加压浸出高铁硫化锌精矿工艺采用高压釜、矿浆加热器、闪蒸槽、加压泵、高压釜控制仪表等,无需建设配套的焙烧车间和制酸厂,在环保和经济方面都有很强的竞争力。
机械设备优先选用节能产品,大功率的风机、水泵采用变频调速装置。
槽子加盖,蒸汽管道保温,减少热损失。
整个生产工艺过程采用现场总线技术PROIBUS的DCS系统控制。
锌熔铸采用耗能较低的新型低频感应电炉。
5 工艺优势高铁硫化锌精矿加压浸出工艺具有如下优势:(1)工艺流程简洁。
该工艺将传统湿法炼锌工艺的焙烧、收尘、制酸、浸出、渣处理工序合并为一段加压浸出或两段加压浸出,工艺流程简化,环节减少。
(2)趋利避害。
前已述及高铁硫化锌精矿中的铁在该工艺中起到催化作用,加速了锌的浸出,化害为利,实现了锌的选择性浸出,使铁的浸出得到有效控制,降低沉矾除铁系统的投资。
(3)环境友好,易实现清洁生产。
工艺为全湿法流程,精矿中的硫以元素硫形式从渣中回收,省去了传统工艺中焙烧脱硫、烟气的收集、冷却系统及制酸工序,避免了SO2的污染。
(4)伴生金属回收利用程度高。
铅、银等伴生金属在加压浸出过程中进入浸出渣,通过浮选浸出渣,将大量元素硫及硫化物浮选后,铅、银等富集在浮选尾矿中,相对于精矿的富集比约5倍,有利于下一步回收利用。
(5)工艺灵活。
规模可大可小,特别适合交通欠发达地区实现硫化锌精矿的冶炼,降低运输成本,提高企业综合效益。
可以单独建设加压浸出的全湿法炼锌厂;也可以与传统湿法炼锌工艺相互衔接,进行扩产改造。
(6)基建投资省。
省去了传统工艺的工序,其基建投资仅为传统工艺的60~70%。
6 应用实例2002年6~9月,在云南澜沧铅矿进行了10升规模的高铁锌精矿和常规硫化锌精矿的小型试验研究。
2002年l0月~2003年1月,由云南冶金集团总公司组织有关企事业单位的技术人员组成的联合研究小组,在小型试验的基础上,开展连续加压浸出(加压釜几何容积3.24m3)新工艺的半工业试验研究,整个试验历时4个月。
2004年云南冶金集团总公司采用一段加压浸出技术,在云南永昌铅锌股份有限公司建设10000t/a电锌示范厂,在国内外率先实现高铁硫化锌精矿加压浸出技术的产业化。