超精密自由曲面轮廓测量方法综述
复杂曲面测量技术的研究综述

复杂曲面测量技术的研究综述复杂曲面测量技术的研究综述!石照耀谢华锟!费业泰摘要将复杂曲面测量划分为三种模式,论述了各模式的演变及其主要测量方法;概述复杂曲面测量所涉及的数据获取、曲面重构、测头半径补偿以及误差评定等关键技术的研究现状。
关键词:复杂曲面测量坐标测量曲面重构误差评定一、复杂曲面测量的三种模式近十年来,伴随反求工程的兴起,复杂曲面测量技术研究的目的不只是为了评定曲面的质量而且为了获取曲面的几何形状信息。
曲面———曲线———点集———测点集的分解次序是实现复杂曲面测量的基本思想。
基于对曲面测量的各种方式的分析,整体上可将复杂曲面测量划分为下述三种模式:!:通过测量曲面上的一些特征线,根据对被测特征线的评定去反映曲面的质量。
":通过测量分布在曲面上的一系列点,去获取被测曲面的轮廓误差,从而评定曲面的质量。
#:通过测量分布在曲面上的一系列点,提取曲面原始形状信息,重构被测曲面,实现被测曲面的数字化。
模式!是将复杂曲面的测量简化为复杂曲线或平面曲线甚至直线的测量。
如果被测特征线选择为复杂曲面的母线或该曲面上的工作迹线,那么这种测量模式能将复杂曲面的设计、加工与使用统一起来,因此,模式!主要适用于规则复杂曲面的测量,特别是回转类复杂曲面的测量。
通过测量螺旋面的螺旋线和轴向截形去控制螺旋面的质量就是一个典型实例。
对模式!的研究已形成两种技术思想,一种以几何学为基础,另一种基于刚体运动学。
前者的基本思想是仅仅将被测对象当作几何体,借助坐标法、展成法等方法去测量复杂曲面上的特征线。
后者的基本思想是将被测对象作为一个刚性的功能元件或传动元件与另一个标准元件作啮合运动,通过测量啮合运动误差来反求曲面上的特征线误差。
我国在齿轮测量方面的突破,经过完善与推广,现已形成!模式下的运动几何测量法。
与!模式相关的测试技术得到了较快发展,各种!"!式的专用测量机、齿轮测量中心、多维测量中心以及坐标测量机已成为生产实际中的主要检测手段。
自由曲面光学技术概述

3
1、经典研抛法
铣磨成型
即经过铣磨,将毛坯加工成需要的形状。 该形状需要提前做一计算,得到 最 大 去 除量形状,从而减轻后续过程任务量, 程任务量。该过程需要用到铣磨机,属 于下面要提到的粗磨的铣削加工,又称 范成法加工。
研磨
即用研磨剂,研磨光学元件表面以减少 成形过程中产产生的下表面损伤。这一 过程根据添加研磨剂尺寸不同,分为粗 磨 和 精 磨 。 精磨过程中还需要使用冷却 液,起到冷却、润滑、清洗和化学反应 等作用。精磨后的光学元件由于有凹凸 层的存在而形成不透明的表面,这也是 抛光的必要性所在。
优缺点
传统的轨迹成形法加工自由曲面,共同的特点是加工效率高,但一般难于加工高精度的自 由曲面,其根本原因在于加工所依据的轨迹的准确性差,轨迹转移精度不高,而且模具或 机构等的轨迹单一,只能加工一种尺寸一种形状的非球面,且可加工的材质有限,通用性 差, 通常只用于中低精度非球面零件的批量生产。 由于该方法已经比较成熟,并且很传统,目前,国外对这方面研究的报道很少。国内主要 是中科院长春光机所和长春理工大学在做这方面的研究工作。
1972年
发展历程 1980年
摩尔公司首先开发出了用3个坐标控制的 M―18AG非球面加工机床,这种机床可加工 直径356mm的各种非球面的金属反射镜。 英国RankPneumo公司向市场推出了利用激 光反馈控制的两轴联动加工机床,该机床可 加工直径为350mm的非球面金属反射镜,加 工工件形状精度达0.25-0.5μ m,表面粗糙度 Ra在0.01-O.025μ m之间。随后又推出了 ASG2500、ASG2500T、Nanoform300等 机床
3、CNC磨削、研磨和抛光技术
优缺点
其加工过程大致可以概述为计算机控制的精密机床先将工 件表面磨削成一个最接近自由曲面的球面,在不改变工件 面形精度的前提下,通过研磨加工去除偏离量,最后通过 抛光的方法达到曲面的表面质量要求, 左 图即为CNC磨削、 研磨和抛光流程图。此加工过程的特点是阶段多、周期长, 起始球面的选择对偏离量及工艺的制定起着决定性作用; 适合加工高精度、大及超大口径的光学元件;对碳化钨、 光学玻璃等脆硬材料有明显的优势。 不过,这种方法也有很多不足之处,如果要加工不同的自 由曲面零件,由于工件表面的光洁度和成形精度都需要通 过磨削、研磨和抛光来改善,就需要大量的研磨盘,提高 了成本,同时也增加了维护的难度;还有就是抛光过程中 不可避免的会产生一些形状误差,自由曲面的不对称度越 大,误差也就越大。
自由曲面光学元件的设计加工及面形测量之综合制造系统

合制造平台 ,主要的技术创新点如下 :
1 自由曲面 光学 设计 考虑 较为 复 杂 , ) 因为光 学面 的坐 标 系统 不断 改变 , 学表 面 用复 杂的 自由曲面 , 光 所以 光线 追迹 及优化 比较费时 , 差的分析 和制定也 有一定 的困难 , 公
如倾 角、光学面位置的变化 、曲面面形误差的评定。项目 组创新地采用了边缘光线扩展度守恒的原理 , 开发了一套
精 度 自曲 曲面 光学关 键元 件的成功 制造 , 只依赖 数控机床 不单 的精 度 ,更 有赖 于先 进光学 设计 、 加工 工艺 、 自由曲面 测量技 术的综 合考虑 , 以及复 杂的数据 演算 和大量 实验数据 验证 ,才
得以提 升 自曲面光 学的加 工精 度及检测 质量 。 现有 的 国内外设
产 品开 发周 期 。 目组成 功开 发 出拥有 自主 知识 产权 的数 项 字化 综合制 造 系统 ,填补 了我 国在 自由曲面光学 制造 技术 上的 空 白 ,使我 国的 自由曲面 光学 在光 电通 讯产 品 、 天 航 及 国防 中的应 用 可达 世界先 进 水平 。 光学 自由曲面是 指无法 用球 面或 非球面 系数 来表示 的 曲面 , 中 包括 任意 非传 统 、非 对称 的 曲面 、微结 构阵 列 其 和 参 数 向量表 示 的任何 形状 的 曲面 。 与传 统 的光学 制造 比 较 ,自由曲面 光学 的面 形精 度要 求高 ,制 造 工艺技 术及 其 面形 的检测 技术 极为 复杂 ,涉及 繁复 的数据 处理和 大量 实
面光 学与光 电通讯 产 品及汽车 照 明的研 发 。 自由 曲面光 学设 在 计、 多轴超 精密 自由 曲面加 工 、 刀具轨 迹生 成 、 工艺 流程 仿真 及 工艺优化 、 自由 曲面 的 面形测 量 与光学性 能评 定等方 面 , 项 目组 作 了大量 的研 发工 作( 附录 论文 列表 )通过 大量 的算 参考 ,
调查报告:曲面检测

关于复杂曲面检测调研一、曲面测量的常用方式方法近十年来,随着航空、航天事业的飞速发展,对传动部件的性能要求越来越高,而传动部件无论是齿轮还是叶片,都是依靠复杂曲面来完成运动和动力的传输,而对复杂曲面的进行精度检验离不开对曲面的测量。
复杂曲面测量技术历来是几何量计量检测技术中的一项重要研究课题。
传统的研究内容主要注重于被测曲面质量指标的获取与评判,即曲面测量的主要目的是为了获取曲面的质量信息。
近几十年来,随着逆向工程工程(Reverse Engineering以下简称RE)的兴起,复杂曲面测量技术的研究增加了新的内容,曲面测量的目的不只是为了评定曲面质量,而且要求获取曲面的几何形状信息。
虽然曲面的测量目的各异方法众多,但曲面→曲线→点集→测点集的分解次序始终是实现复杂曲面测量的基本思路。
复杂曲面的测量与RE中的表面数据采集具有很多的共同目标,所以RE的测量手段具有很强的借鉴意义,目前采用的RE 测量方法主要有三种,分别为接触式测量法、非接触式测量法和逐层扫描法。
其中逐层扫描法是主要针对工件内部结构的检测方法。
1.接触式测量法:RE 传统上使用三坐标测量机法,又称探针扫描,它主要应用于由基本的几何形体构成的实体的数字化过程,适用于测量实体外部的几何形状。
采用该方法可以达到很高的测量精度(±0.5um),但测量速度很慢,并易于损伤探头或划伤被测实体表面,而且价格较高,对使用环境也有一定要求。
采用这种方法会使测量周期大大延长。
一般来说,CMM 有两种不同的测量方式:点对点测量(Point to Point Method)、截面扫描(Section Scanning Method)。
2.非接触式测量法:非接触式数据采集方法有光学测量、激光三角形法、超声波测量、电磁测量等方式。
根据测量原理的不同,以激光作为基本光源,分为光点、单线条、多光条等结构模式,采用光电敏感元件在另一位置接收激光的反射能量,将其投射到被测物体表面,通过被测物体基平面、象点、象距等之间的关系计算物体的信息,依据光点或光条在物体上成象的偏移,非接触式数据采集方法可探测到被测机械测头难以测量到的部位,能够真实反映被测物体表面的外形。
自由曲面超精密加工技术疑难点
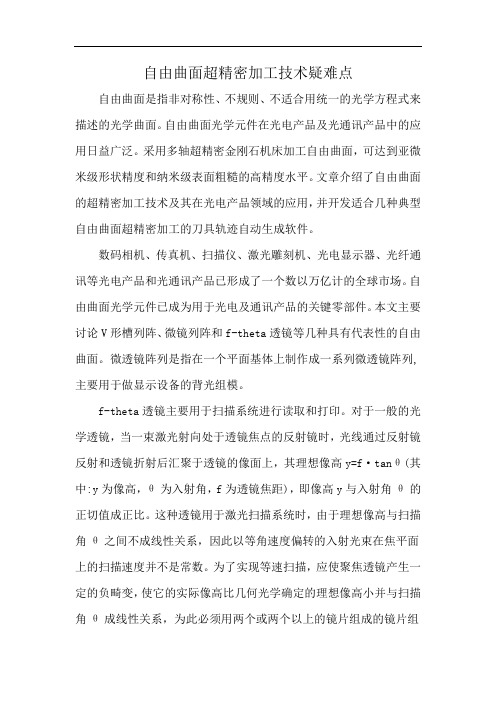
自由曲面超精密加工技术疑难点自由曲面是指非对称性、不规则、不适合用统一的光学方程式来描述的光学曲面。
自由曲面光学元件在光电产品及光通讯产品中的应用日益广泛。
采用多轴超精密金刚石机床加工自由曲面,可达到亚微米级形状精度和纳米级表面粗糙的高精度水平。
文章介绍了自由曲面的超精密加工技术及其在光电产品领域的应用,并开发适合几种典型自由曲面超精密加工的刀具轨迹自动生成软件。
数码相机、传真机、扫描仪、激光雕刻机、光电显示器、光纤通讯等光电产品和光通讯产品已形成了一个数以万亿计的全球市场。
自由曲面光学元件已成为用于光电及通讯产品的关键零部件。
本文主要讨论V形槽列阵、微镜列阵和f-theta透镜等几种具有代表性的自由曲面。
微透镜阵列是指在一个平面基体上制作成一系列微透镜阵列,主要用于做显示设备的背光组模。
f-theta透镜主要用于扫描系统进行读取和打印。
对于一般的光学透镜,当一束激光射向处于透镜焦点的反射镜时,光线通过反射镜反射和透镜折射后汇聚于透镜的像面上,其理想像高y=f·tanθ(其中:y为像高,θ为入射角,f为透镜焦距),即像高y与入射角θ的正切值成正比。
这种透镜用于激光扫描系统时,由于理想像高与扫描角θ之间不成线性关系,因此以等角速度偏转的入射光束在焦平面上的扫描速度并不是常数。
为了实现等速扫描,应使聚焦透镜产生一定的负畸变,使它的实际像高比几何光学确定的理想像高小并与扫描角θ成线性关系,为此必须用两个或两个以上的镜片组成的镜片组来取代单个镜片。
所谓f-theta镜,就是经过严格的设计,使像高与扫描角满足关系式y=f·θ的镜头,因此f-theta镜又称线性镜头。
自由曲面超精密加工技术自由曲面光学元件的设计和制造与传统光学元件有很大的差别。
传统的球面和非球面光学透镜有回转对称轴,用传统的2轴超精密车床就可以加工。
传统的加工设备和加工技术很难满足高精度光电产品中复杂自由曲面的加工要求。
精密零件表面粗糙度的测量方法综述

精密零件表面粗糙度的测量方法综述摘要:精密零件的表面粗糙度是表征工件表面质量的主要指标,也是工程实际中应用最广泛的,因此准确测量工件表面粗糙度是评价工件表面质量优劣的有效方法。
本文按接触式和非接触式测量方法分类介绍了表面粗糙度的测量方法及其最新研究进展。
关键词:表面粗糙度;测量;精密制造0 引言表面粗糙度,其英文缩写为SR,即surface roughness,是指加工表面上具有较小间距和微小峰谷不平度,是评定加工后的材料表面由峰、谷和间距等构成的微观几何形状误差的物理量。
表面粗糙度是衡量表面质量的主要依据。
关系到零件与机器的使用性能和寿命,尤其对在高温,高速和高压条件下工作的机械零件影响更大。
因此,在零件加工、使用中必须对表面粗糙度予以控制,提高零件生产时的表面质量,保证产品质量。
所以表面粗糙度的测量方法的研究至关重要。
随着对加工零件表面质量的要求越来越高,零件表面粗糙度的精确测量显得尤其的重要。
表面粗糙度测量按测量方式可以分为接触式和非接触式两种。
1 接触式测量接触式测量就是测量装置的探测部分直接接触被测表面,能够直观地反映被测表面的信息,但是这类方法不适合于那些易磨损刚性强度高的表面。
主要有比较法、印模法、针描法等测量方法。
1.1 比较法[1,2]比较法是车间现场常用的最简便易行的方法,是将被测表面与表面粗糙度比较样块进行比较,用肉眼判断或借助于放大镜、比较显微镜放大后进行比较;也可用手摸、指甲划动的感觉来判断被测表面的粗糙度。
比较法一般只用于粗糙度参数值较大时的近似评定。
一般说来Ra > 2.5 μm的加工表面可直接目测与比较样块进行比较。
当目测不易判别时,可用手指甲以适当速度分别沿比较样块和被测表面划过,凭主观触觉进行判断。
根据经验,当表面微观不平度间距在0.1 mm 左右时,手指的移动速度以25 mm/s 为宜。
当Ra 值在0.4~2.5 μm 范围时可采用5~10 倍放大镜进行观察比较。
自由曲面光学技术..

优缺点
传统的轨迹成形法加工自由曲面,共同的特点是加工效率高,但一般难于加工高精度的自 由曲面,其根本原因在于加工所依据的轨迹的准确性差,轨迹转移精度不高,而且模具或 机构等的轨迹单一,只能加工一种尺寸一种形状的非球面,且可加工的材质有限,通用性 差, 通常只用于中低精度非球面零件的批量生产。 由于该方法已经比较成熟,并且很传统,目前,国外对这方面研究的报道很少。国内主要 是中科院长春光机所和长春理工大学在做这方面的研究工作。
1972年
发展历程 1980年
摩尔公司首先开发出了用3个坐标控制的 M―18AG非球面加工机床,这种机床可加工 直径356mm的各种非球面的金属反射镜。 英国RankPneumo公司向市场推出了利用激 光反馈控制的两轴联动加工机床,该机床可 加工直径为350mm的非球面金属反射镜,加 工工件形状精度达0.25-0.5μ m,表面粗糙度 Ra在0.01-O.025μ m之间。随后又推出了 ASG2500、ASG2500T、Nanoform300等 机床
代表当今员高水平的超精密金刚石车床是美 国劳伦斯.利弗莫尔(LLNL)实验室研制成功的 LODTM,它可加工直径达2100mm,重达 4500kg的工件其加工精度可达0.25μ m,表 面粗糙度RaO.0076μ m,该机床可加工平面、 球面及非球面,主要用于加工激光核聚变工 程所需的零件、红外线装置用的零件和大型 天体反射镜等。
抛光
可以分为初抛光和精抛光等两个过程。 光学零件的抛光是获得光学表面的工序。 其目的首先是去除精磨的破坏层,达到 规定的表面疵病要求,其次是精修面形, 达到要求的光圈,形成透镜规则的表面 。
2、轨迹成型法
类别
轨迹成形法主要包括使用成形工具的轨迹成形法、使用仿形靠模的轨迹成形法和使用机 构轨迹的成型法等几种。
计算全息补偿检测自由曲面的高精度位姿测量

第 31 卷第 11 期2023 年 6 月Vol.31 No.11Jun. 2023光学精密工程Optics and Precision Engineering计算全息补偿检测自由曲面的高精度位姿测量李雯研1,2,程强1,2,曾雪锋1,2*,李福坤1,2,薛栋林1,2*,张学军1,2(1.中国科学院长春光学精密机械与物理研究所,吉林长春 130033;2.中国科学院大学,北京100049)摘要:为实现自由曲面的定位与位姿高精度测量,提出了“光学-机械”基准定位法,建立了位姿测量模型,并对该方法的定位误差和基准选择展开研究。
根据三坐标测量机与计算全息提出了“光学-机械”基准定位法。
然后,采用球形安装的回射器(Sphere Mounted Retroreflector ,SMR)、猫眼、基准球作为基准,基于波像差理论与视差效应分别建立了3种基准的位姿测量模型,得到了位置误差与基准区域波前像差的函数关系,并对3种位姿测量模型进行对比。
最后,对3种基准位姿测量方法进行仿真及实验验证,实测结果与模型的残差结果均小于0.05λ,相对误差均小于2.43%,验证了模型的准确性。
实验结果表明,当检测距离为1 000 mm时,猫眼法的轴向定位误差为24 μm;基准球法的轴向定位误差为50 μm;SMR靶球法的轴向定位误差为16 μm,X,Y方向的定位误差为1 μm,滚转角定位误差为3.26″。
SMR靶球法的定位误差最小、检测动态范围最大且检测光学元件的自由度最多,更适用于自由曲面的高精度位姿检测。
关键词:光学检测;光学面形位姿测量;“光学-机械”基准定位法;计算全息;定位误差中图分类号:O439 文献标识码:A doi:10.37188/OPE.20233111.1581High-precise posture measurement for measuring freeform surface with computer generated hologram compensationLI Wenyan1,2,CHENG Qiang1,2,ZENG Xuefeng1,2*,LI Fukun1,2,XUE Donglin1,2*,ZHANG Xuejun1,2(1.Changchun Institute of Optics, Fine Mechanics and Physics, Chinese Academy of Sciences,Changchun 130033, China;2.University of Chinese Academy of Sciences, Beijing 100049, China)* Corresponding author, E-mail:zengxf@ciomp. ac. cn;xuedl@ciomp. ac. cn Abstract: To realize the high-precision position measurement of freeform surfaces, this paper proposes an optic-mechanical reference positioning method that employs a position measurement model. First, an opti⁃cal-mechanical reference positioning method based on a coordinate measuring machine and computer-gener⁃ated holography is proposed. Then, using a spherical mounted retroreflector (SMR) target ball, cat eye,and reference ball as the benchmarks,three benchmark position measurement models are established on the basis of wave aberration theory and parallax effect. The functional relationship between the position er⁃ror and the wavefront aberration in the reference area is obtained, and the three position measurement mod⁃文章编号1004-924X(2023)11-1581-12收稿日期:2023-01-11;修订日期:2023-02-14.基金项目:吉林省卓越创新团队(No.20210509067RQ);国家自然科学基金资助项目(No.61975201,No.62075218,No.12003034);国家重大科研仪器研制项目(No.62127901);中科院青促会项目(No.2020224,(No.2022213)第 31 卷光学精密工程els are compared and analyzed. Finally, the three benchmark position measurement methods are simulated and validated via experiments. The residual difference between the measurement results and the model is below 0.05λ, and the relative error is below 2.43%, confirming the accuracy of the model. The experi⁃mental results indicate that the axial positioning error of the cat-eye method is 24 μm when the measure⁃ment distance is 1 000 mm. The axial positioning error of the reference-ball method is 50 μm. The SMR target ball positioning error is 16 μm in the axial direction, 1 μm in the X and Y directions, and 3.26″ in clocking.The SMR target ball method has the minimum positioning error,maximum measurement dy⁃namic range, and maximum degree of freedom in detecting optical elements; therefore, it is more suitable for high-precision pose measurement of freeform surfaces.Key words: optical testing;optical surface posture measurement;computer generated holography;optic-mechanical reference positioning method; positioning error1 引言计算全息(Computer Generated Hologram,CGH)补偿检测具有高精度、非接触测量等优点,可实现非球面、自由曲面等光学面形补偿检测[1-2]。
- 1、下载文档前请自行甄别文档内容的完整性,平台不提供额外的编辑、内容补充、找答案等附加服务。
- 2、"仅部分预览"的文档,不可在线预览部分如存在完整性等问题,可反馈申请退款(可完整预览的文档不适用该条件!)。
- 3、如文档侵犯您的权益,请联系客服反馈,我们会尽快为您处理(人工客服工作时间:9:00-18:30)。
超精密自由曲面轮廓测量方法综述自由曲面广泛应用于汽车、航空航天以及各类模具制造等领域,有着平面、球面等无法比拟的优势。
随着超精密制造技术的发展,自由曲面零件的精度得到大幅度提升,但超精密加工极易受到外界环境的干扰,对加工环境和加工稳定性有很高的要求,而对于复杂结构纳米加工表面的自由曲面,更是难以一次达到加工精度的要求,所以要对加工表面采取多次“成型测量——补偿”的生产过程,最终获得满足精度要求的零件。
纳米级精度测量是自由曲面加工中面形评价和修正的基础,但是超精密加工后表面轮廓测量难、测量成本高、表面表征理论不完善,急需有效的测量方法来检验评价。
目前,对于自由曲面轮廓的测量方法主要分为离线测量和原位测量两种方式。
离线测量是借助已商业化生产的测量机器,如三坐标测量机(CMM),各类轮廓仪等,这种方法不仅能够测量已知轮廓,而且能够测量未知的复杂自由曲面轮廓,具有高精度和良好的重复性,缺点是评价结果极易受到测头的精度的影响,并且重复装卡零件会带来较大的归位误差。
而原位测量是在被加工件加工完成时进行测量,对其误差进行整体补偿修正,也叫在位测量或在机测量,避免了反复装卡带来的误差,是一种高效集成化测量方法,特别适合于面形精度要求高的自由曲面超精密制造中。
一、离线测量1.基于三坐标机类CMM有其机器坐标系,而自由曲面的零件自身具有设计坐标系,要利用CMM上对超精密自由曲面零件轮廓检测,目前研究的重点主要在于将CMM的测量坐标系与设计坐标系进行匹配、对定位方法的研究、求解变换矩阵的参数和建立误差评定模型等。
何改云等人1提出了一种求解最优化问题找到变换矩阵的参数值从而将测点从测量坐标系下变换到设计坐标系的方法,并用“S”形试件的自由曲面对提出的误差评定方法进行了验证,扩展不确定度为3.8μm(k=2);对于具有复合自由曲面特征的零件,通常都是由多个自由曲面片组成,表面情况复杂,何雪明等人2采用降阶思想,将复合自由曲面先分解为多个自由曲面片,进行合理的边界划分和自由曲面片间测量次序规划,然后对每个自由曲面片应用双参数向自适应测量法,使测点可随被测曲面自身曲率变化特性而疏密分布,实现了CMM自动测量复合自由曲面,对具有自由曲面特征的叶片等零件进行实际测量,结果表明测量精度可达μm级,相对于均匀跨距扫描方式精度提高了一个数量级;仇谷烽3等人以最小二乘法为基础,建立了能够根据测量结果精确分析出两个坐标系统之间的偏离量的数据处理模型,结果表明,该模型可精确地恢复1cm以下的偏心和0.1°以下的旋转量,从而为进行高精度的面形误差分析提供了工具分析。
2.微纳米坐标测量机在三坐标机的基础上,针对于微纳米级制造零件,各大生产商开始对微纳米测量机进行研究,并且有了很大的进展。
德国SIOS公司根据阿贝原则,以激光干涉仪作为位移传感器,研制了高精度的定位测量系统纳米定位测量机(NMM),可提供范围为25 mm×25 mm×5 mm,分辨力达0.1nm的三维尺寸定位和测量,测量不确定度优于10 nm。
此外,NMM 可以通过机械连接件安装不同功能的表面检测测头和工具4;IBS精密工程公司研制的Isara400采用三面镜激光干涉仪,测量范围增加到400 mm×400 mm×100 mm,一维测量不确定度为50 nm(k=2),分辨力为l nm5;Zygo公司独有的SureScanTM抗震专利技术,开发了多款基于3D 相干扫描干涉法、移相干涉法的表面轮廓仪,主要有ZeGage、ZYGO-ZeGage_Plus、NewView系列、ZYGO-Nexview、ZYGO-Nomad产品,其系统都配置了ZYGO综合测量软件包MetroPro,可以提供三维和两维表面特性、实时显示以及应用处理选项,RMS 重复性可达0.005nm,光学横向分辨率最小0.34μm(100x 物镜),样品可俯仰倾斜±4°,测量口径达147×100mm×100mm甚至更大;Taylor Hobson 公司设计开发的用于测量表面粗糙度的Talysurf 系列仪器产品,解决了大角度的非球面镜片测量的难题,同时也打破了以往探针尖端到达工件部位有限的束缚。
如Talysurf PGI 1250 轮廓仪,分辨率可达0.8nm,可测量倾斜角±45°、角度分辨率0.001°。
二、原位测量现有原位测量方法大致可以分为点扫描和整场测量两种方式6。
点扫描方式是将测量系统构建于超精密加工系统之上,由加工运动系统产生测量系统与工件之间的相对位移,从而实现加工表面的高精度测量,但是点扫描方式的效率较低,不能很好地满足高效加工的需求,于是出现了以干涉测量方法为主的整场测量方式。
1.点扫描测量方式点扫描式原位测量系统被大量应用于超精密磨削加工中,实现被加工表面或砂轮轮廓的原位测量,以有效控制磨削过程和提高精度。
点扫描测量方式根据是否需要已知被测面形,得到被测点三维坐标或者被测面和理想面之间的偏差值集。
F.J. Chen7等人在具有线电解砂轮修整的磨削装备中安装激光原位测量系统,并加入补偿磨削循环,实现了177 nm (PV)和1.7 nm (Ra)精度的加工非球面镜的能力;将量程小、精度高的传感器集成在原位测量系统中,可实现大范围、高精度自由曲面零件轮廓的测量——比如原子力显微镜(AFM)可以达到原子量级的分辨率,并且不受复杂曲面的限制,但是扫描范围只有几十个μm面积;赵健8开发了自感应AFM 测头,并使用双平台拓展扫描范围,将研究测头与大范围纳米定位平台结合,在实现纳米级分辨力的基础上,使测量范围达到25 mm × 25 mm × 5 mm ;Gao W等人9将AFM 悬臂端与分辨率为0.5 nm 的线性编码器一起组成测量系统,能实现口径50mm双正弦工件(X 和Y 向周期150μm,矢高1μm)100nm的高精度原位测量;浙江大学的Wu-le Zhu等人10则将隧道扫描显微镜(STM)应用到原位测量系统中,实现复杂结构自由曲面如复眼复杂结构特征、结构偏角过大的高精度测量,分辨率达3.5nm(40 x 细分电路),并且可以测量倾斜度达45°的表面,不过扫描面积只有140μm *90μm;中国计量科学研究院(NIM)与清华大学11合作开发的大范围纳米几何结构测量,系统的水平运动机构由大范围气浮工作台和小范围纳米位移台(分辨力0.2 nm)组成,测量范围可达50 mm × 50 mm × 6 μm 。
程云勇等人12发明了一种基于线激光传感器的四轴测量系统及测量方法,研究了传感器激光平面法向量和激光主光轴光束方向标定方法,进行了电控旋转台的轴向标定技术研究,并对多视角测量得到的点云数据进行了拼合,得到了完整的航空叶片三维数据,解决了针对形状复杂且具有自由曲面的零件非接触数字化测量效率低下、精度不高、成本高昂等问题;张效栋等人13对螺旋反射镜进行原位测量,测量系统分辨率优于10nm,在此基础上,可实现Ra为10.7nm,加工误差小于1μm的复杂光学元件的超精密制造;李坡14在其学位论文介绍了基于超精密机床聚焦式激光原位测量系统,利用聚焦误差信号(FES)检测原理的激光测量方法,针对超精密车床的加工和运动的特点,设计了有效的加工与测量路径,实现了坐标信息和误差信息一一对应的采集,能够保证测量工件表面点的法向量与测头的夹角小于10°的测量,对超精密车削加工得到的口径20mm双正弦曲面面形误差最小0.6μm;魏桂爽等人15提出了一种基于超精密机床的光学自由曲面原位测量方法,采用气浮式传感器减少表面接触带来的测量误差,并用螺旋线方式进行加工及测量路径的设计,实验结果表明,所加工的双正弦自由曲面的面形误差在±0.5μm范围内。
2.整场测量方式自由曲面光学元件的干涉检测法常见的有数字莫尔移相干涉法和环形子孔径拼接法。
沈华16提出了基于多重倾斜波面的光学自由曲面非零位干涉测量方法、虚拟莫尔条纹旋转匹配法及调整流程,解决了高精度自由曲面被测件空间姿态的精确匹配问题,得出了测量过程中在无任何外部基准的情况下被测件与其理想测量位置的匹配误差在X、Y、Z方向达到5μm以内,在旋转方向上达到0.4°以内的结论,从而使姿态误差引入的波面误差控制在λ/20(PV值)以内,梯度变化达到±7°的自由曲面面形的测量精度优于λ/10(PV值);李绍辉等人17提出了基于虚拟参考面得到参考相位分布的方法,避免了光栅条纹反射视觉测量方法中对参考平面测量的需求,提高了测量速度的同时降低了测量的复杂性,有利于系统的集成化,对超精密加工平面镜和组合台阶的表面形貌进行测量结果显示测量精度达到50μm左右;而后他们18又提出了基于迭代的光栅相位偏折测量方法,建立相位偏折与零件表面梯度的对应关系,采用结合区域波前重构与路径积分的三维重建算法,可实现对150mm×150mm×20mm的超精密加工平面镜精度为40μm 的测量。
针对高曲率及大倾角样品的形状测量,常应用数据拼接技术,如子孔径拼接干涉测量技术,通过拼接多角度测量结果来获取样品完整面形,但是受机械扫描范围和样品安装方式限制,拼接方法对外表面面形测量能力仍然有限,不能实现半球或者近半球的超高曲率样品和超高曲率内表面面形的完整测量等问题,周宇豪等人19-20提出了一套自由曲面子孔径拼接干涉检测(FSSI)技术与系统及基于系统模型的多孔径同步逆向优化重构(MSROR)算法,能够对任意形状的子孔径进行拼接检测,且无需重叠区域,甚至在一定精度范围内允许区域数据缺失。
实验验证了浅度抛物面(偏离顶点球9μm)顶点球曲率半径的测量,测量精度达0.016%;非球面(偏离顶点球50μm)环形子孔径拼接实验结果相比于ZYGO verifier子孔径扫描干涉仪检测结果更精确,而口径为30mm的双圆锥面扇形子孔径拼接实验结果与轮廓仪相比,检测精度十分相近,证明了FSSI系统对于光学非常规子孔径拼接自由曲面的检测的有效性与精确性;居冰峰等人21提出了一种基于自动跟踪与彩色共焦测量原理的自由曲面光学元件形貌测量系统及方法,采用探头自动跟踪的测量方法来拟合轮廓形貌,能有效解决现有测量方法中探头不动带来的无法测量PV值较大的问题,测量精度和分辨率都达到纳米级,测量表面倾斜角度最大为±21°,不过测量量程只有10mm;而针对超高曲率表面面形刘辰光22提出来一种基于中介层散射原理的高曲率及大倾角表面共焦测量理论和仪器方法,可获得极端加工状态下的工艺参数,在数值孔径NA=0.75 下对光滑倾斜曲面的探测能力达到88.4°,曲面可探测角度超过传统反射成像方法理论极限的82%,在国际上率先研制高曲率及大倾角表面形状量值溯源科学仪器。