间歇精馏过程优化问题
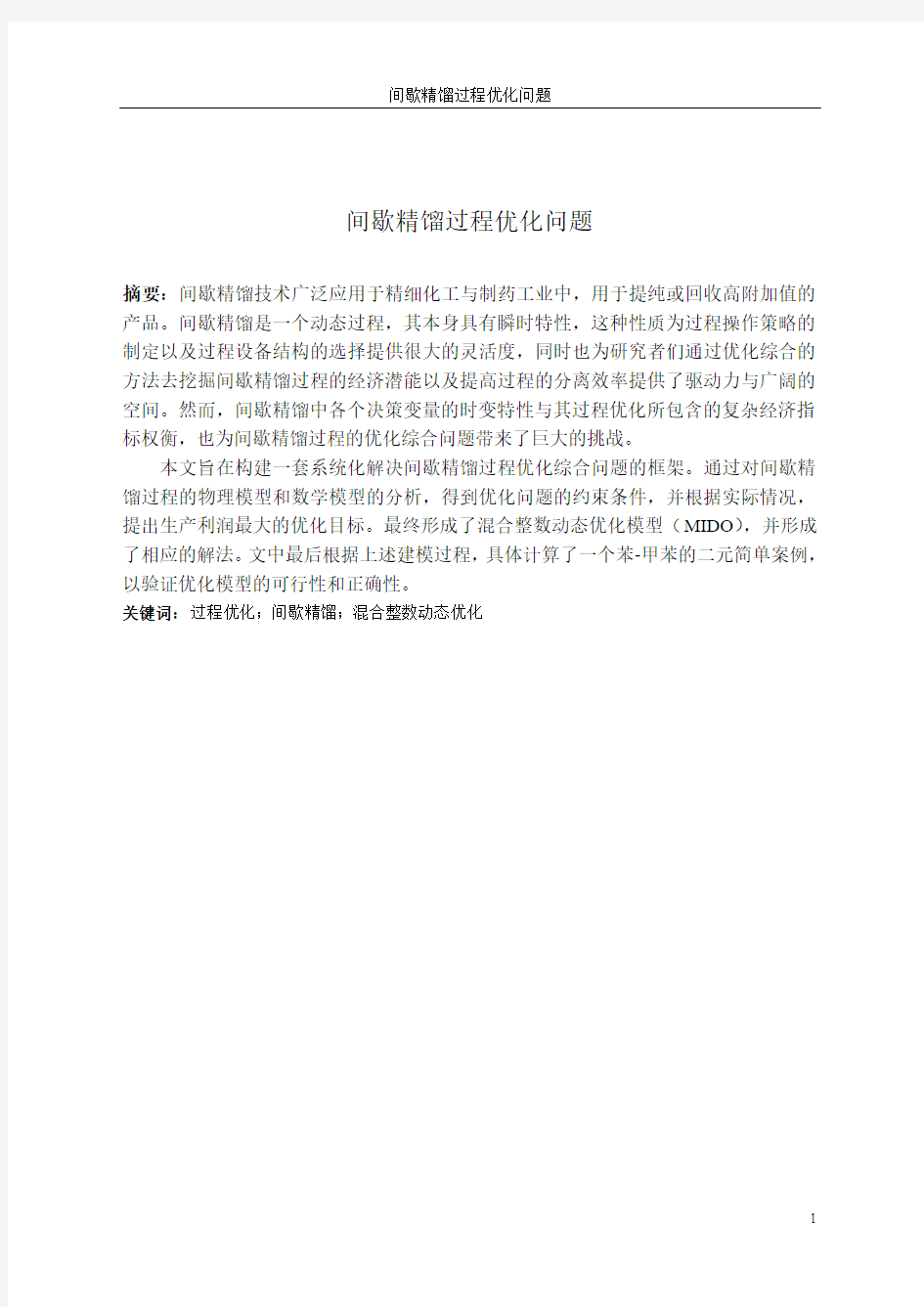
- 1、下载文档前请自行甄别文档内容的完整性,平台不提供额外的编辑、内容补充、找答案等附加服务。
- 2、"仅部分预览"的文档,不可在线预览部分如存在完整性等问题,可反馈申请退款(可完整预览的文档不适用该条件!)。
- 3、如文档侵犯您的权益,请联系客服反馈,我们会尽快为您处理(人工客服工作时间:9:00-18:30)。
间歇精馏过程优化问题
摘要:间歇精馏技术广泛应用于精细化工与制药工业中,用于提纯或回收高附加值的产品。间歇精馏是一个动态过程,其本身具有瞬时特性,这种性质为过程操作策略的制定以及过程设备结构的选择提供很大的灵活度,同时也为研究者们通过优化综合的方法去挖掘间歇精馏过程的经济潜能以及提高过程的分离效率提供了驱动力与广阔的空间。然而,间歇精馏中各个决策变量的时变特性与其过程优化所包含的复杂经济指标权衡,也为间歇精馏过程的优化综合问题带来了巨大的挑战。
本文旨在构建一套系统化解决间歇精馏过程优化综合问题的框架。通过对间歇精馏过程的物理模型和数学模型的分析,得到优化问题的约束条件,并根据实际情况,提出生产利润最大的优化目标。最终形成了混合整数动态优化模型(MIDO),并形成了相应的解法。文中最后根据上述建模过程,具体计算了一个苯-甲苯的二元简单案例,以验证优化模型的可行性和正确性。
关键词:过程优化;间歇精馏;混合整数动态优化
1 引言
间歇精溜,或许是世界上最古老的用于液体混合物分离的单元操作,几个世纪以来直至今天,间歇精馏仍然大量应用于精细化学品及特殊化学品的生产当中,间歇精馏是间歇生产过程中使用最为广泛的分离技术[1]。间歇精馏主要适用于小批量、多组分、高浓度物系的分离,能够实现单塔分离多组分物系,并获得较高纯度的各组分产品。并且允许进料组分浓度在很大范围内变化,还可以适用于不同分离要求的物料。其相对于连续精馏来讲,设备简单、灵活性高、适应力强、适用于工况多变、一塔多用的场合,因此在小批量、多元物系的分离过程中得到了广泛的应用[2]。
从目前来看,全世界由间歇精馏过程得到的化工产品的种类和价值所占的比重还是很大的,尤其是在精细化工方面。目前我国的精细化率在30%以上,精细化工产品具有品种多、更新换代快、产量小、商品性强、产品质量要求高、设备投资小、附加值高等特点,其中有很大一部分都是釆用间歇精馏的生产方式得到的[3-5]。同时精细化工包含的范围很广,包括医药、农药、合成染料、有机颜料、涂料、香料与香精、化妆品等40多个行业和门类。这也使得间歇精馏的技术水平成为了精细化工发展的关键因素。
目前我国大部分企业仍采用传统的间歇精馏技术,即设备采用只具有精馏段的常规间歇精馏塔,运行策略为恒定回流比变塔顶组成或恒定塔顶组成变回流比的常规操作。然而,已有文献表明,传统的间歇精馏技术并不是最为经济有效的生产方式,最佳的间歇精馏运行方案是根据待处理的物料状态选择最适宜的间歇精馏塔结构,并采用优化的回流比操作策略,同时权衡设备投资及公用工程费用,以利润最大化为目标而得到的。未经优化综合的常规生产模式也致使我国精细化工行业存在投资成本高、生产能力小、能源消耗严重以及产品质量差等问题,进而导致产品利润下降以及环境污染等现象的发生。要解决以上问题,依靠计算机辅助设计、模拟,提高精细化工过程的模型化、控制和优化技术水平是一个关键,其中一个重要的方面便在于间歇精馏过程的优化综合。
基于上述社会和研究现状,本文将对间歇精馏过程的优化综合问题展开系统化的研究。通过文献阅读和已有基本化工学科和工程优化学科的基本知识,以间歇精馏系统为对象,以操作时间最短、产品产量最大、过程利润最大为优化目标函数,约束条件为已有的化工间歇精馏计算模型和物性函数模型。通过对优化问题求解,获得最佳设备参数等,由此实现间歇精馏过程的优化综合。最后,本文将列举一个简单的案例来具体阐述这个优化问题,并进行求解,来验证方法的可行性和有效性。
2 间歇精馏塔的物理模型
2.1间歇精馏塔概述
间歇精馏是指间歇投料、间歇出料或连续出料的各种精馏过程,是间歇生产过程中一种十分重要的分离技术,常常被用来作为中间产品和最终产品分离和提纯的手段。间歇精馏的流程如图2-1所示。
间歇精馏与连续精馏原理基本一致,都是利用混合物中各组分挥发能力的不同,通过液相和气相的回流,使气、液两相逆向多级接触,在热能驱动和相平衡关系的约束下,使得易挥发组分(轻组分)不断从液相向气相中转移,而难挥发组分(重组分)由气相向液相中转移,从而达到使混合物得到不断分离纯化的目的。间歇精馏的操作方式与简单蒸馏相类似,即每批次物料一次性加入釜中,然后进行加热精馏。随着釜液被加热汽化,蒸汽在塔内逐级上升至塔顶被冷凝器冷凝,其凝液一部分返回塔内作为回流,另一部分作为塔顶产品采出。塔釜釜液量及组成随塔顶馏出液不断采出而减少和变化。当釜液组成达到设计目标时,则停止精馏,排出釜底残余液,完成一个生产周期。
图2-1常规精馏塔示意图
间歇精馏是一个典型的动态过程,通过有效的时空间安排,可单塔分离多组分混合物,而且设备简单,能多体系共用。工艺通用性强和操作策略灵活的优点,使间歇精馏在化学工业中具有很大的应用价值和市场前景,其内在规律的研究也引起了越来越多的关注与重视。对于间歇精馏过程的研究已有一百多年的历史,纵观研究内容主要包括:间歇精馏过程的模拟计算,间歇精馏过程操作策略的优化,间歇精馏过程的塔型设计以及同时考虑塔型设计与操作策略的过程优化综合。
2.2 间歇精馏过程的物理模型
为了深入探寻间歇精馏过程,掌握其内部规律,并准确预测间歇精馏塔的运行状态,就必须将实际间歇精馏过程抽象成为物理模型,然后运用数学手段对模型进行求解分析。
间歇精馏的建模始于著名的简单Rayleigh 蒸馏模型,但是模型中有诸多假设,模型的准确性有时并不令人满意。之后随着电子计算机的高速发展,人们开始思考引入更多的限定方程:能量平衡、塔板持液、塔板水力学以及严格的物性方程等,来使间歇精馏过程的模型更为精确。然而在许多建模过程中,由于描述间歇精馏复杂模型的是刚性代数-微分方程组,且方程及变量个数随着塔板及组分数的增加而成倍增加,导致求解耗时巨大,甚至会出现不收敛的情况,致使求解困难。因此,人们在不同的设计阶段及不同场景中,开始关注并考虑间歇精馏过程数学模型的大小及复杂度、计算机的计算能力以及是否有可行的数学方法及求解策略。总而言之,就是需要权衡对真实间歇精馏运行场景预测的准确性与求解数学模型所需要的计算代价,从而去选择适当复杂度的模型去满足当前的模拟要求。根据模型的简化程度主要可以分为简捷模型、简单模型以及严格模型[2]。
2.2.1 Rayleigh 模型
Rayleigh 模型,是Rayleigh 于1902年基于单平衡级的间歇蒸馏而建立的,是最简单的间歇精馏过程。其操作流程如图2-2所示。待处理的液体混合物原料被加入至釜内,通过加热器加热,釜内液体开始汽化,气相由釜上方排出,经冷凝器冷凝作为产品采出,过程中没有凝液作为液相回流打回釜中。对于任意时刻,釜液上方的气体都与残留于釜内的液体成相平衡关系。随着精馏的进行,釜液量不断减少,而两相组成也不断变化,易挥发组分在釜液中不断下降,釜液温度随之升高。当釜液中易挥发组分降至规定要求时,则停止精馏。
假设釜中初始二元液相混合物的原料处理量为B 0,液相组成为x B0,则任意时刻釜中残余的液体量B 1及其组成x B1可以通过Rayleigh 模型方程进行计算
1
01
ln B B x B
B
x B dx B y x =-⎰
(2-1)
式中,y 表示任意时刻与釜液液相组成x B 成相平衡关系的气相组成。 任意时刻的馏出液量可以通过下式2-2计算:
01D H B B =-
(2-2)
气液相平衡关系则一般假设组分间相对挥发度α在一定的操作温度范围内,近似为常数,瞬时平衡气相组成y 可以通过式2-3进行计算:
()11B
B x y x αα=
+- (2-3)