数控铣削加工零件毛坯的工艺性分析要点
62数控铣床加工工艺分析

62数控铣床加⼯⼯艺分析6.2数控铣床加⼯⼯艺分析6.2.1数控铣床加⼯零件的⼯艺性分析在选择并决定数控铣床加⼯零件及其加⼯内容后,应对零件的数控铣床加⼯⼯艺性进⾏全⾯、认真、仔细的分析。
主要内容包括产品的零件图样分析、零件结构⼯艺性分析与零件⽑坯的⼯艺性分析等内容。
1.零件图⼯艺分析⾸先应熟悉零件在产品中的作⽤、位置、装配关系和⼯作条件,搞清楚各项技术要求对零件装配质量和使⽤性能的影响,找出主要的和关键的技术要求,然后对零件图样进⾏分析。
针对数控铣削加⼯的特点,下⾯列举出⼀些经常遇到的⼯艺性问题作为对零件图进⾏⼯艺性分析的要点来加以分析与考虑。
(1)图样尺⼨的标注⽅法是否⽅便编程?构成⼯件轮廓图形的各种⼏何元素的条件是否充要?各⼏何元素的相互关系(如相切、相交、垂直和平⾏等)是否明确?有⽆引起⽭盾的多余尺⼨或影响⼯序安排的封闭尺⼨?等等。
(2)零件尺⼨所要求的加⼯精度、尺⼨公差是否都可以得到保证?不要以为数控机床加⼯精度⾼⽽放弃这种分析。
特别要注意过薄的腹板与缘板的厚度公差,“铣⼯怕铣薄”,数控铣削也是⼀样,因为加⼯时产⽣的切削拉⼒及薄板的弹性退让,极易产⽣切削⾯的振动,使薄板厚度尺⼨公差难以保证,其表⾯粗糙度也将恶化或变坏。
根据实践经验,当⾯积较⼤的薄板厚度⼩于3mm时就应充分重视这⼀问题。
(3)内槽及缘板之间的内转接圆弧是否过⼩?(4)零件铣削⾯的槽底圆⾓或腹板与缘板相交处的圆⾓半径r是否太⼤?(5)零件图中各加⼯⾯的凹圆弧(R与r)是否过于零乱,是否可以统⼀?因为在数控铣床上多换⼀次⼑要增加不少新问题,如增加铣⼑规格、计划停车次数和对⼑次数等,不但给编程带来许多⿇烦,增加⽣产准备时间⽽降低⽣产效率,⽽且也会因频繁换⼑增加了⼯件加⼯⾯上的接⼑阶差⽽降低了表⾯质量。
所以,在⼀个零件上的这种凹圆弧半径在数值上的⼀致性问题对数控铣削的⼯艺性显得相当重要。
⼀般来说,即使不能寻求完全统⼀,也要⼒求将数值相近的圆弧半径分组靠拢,达到局部统⼀,以尽量减少铣⼑规格与换⼑次数。
第六章 数控铣削加工工艺
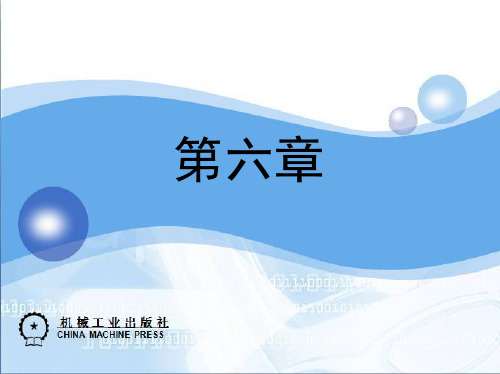
图6-33 几种常用的成形铣刀
第一节 数控铣削加工工艺的制订
2.铣刀的选择 (1)面铣刀主要参数的选择 标准可转位面铣刀直径为ϕ1 6~ϕ630mm,应根据侧吃刀量ae,选择适当的铣刀直径, 尽量包容工件整个加工宽度,以提高加工精度和效率,减 小相邻两次进给之间的接刀痕迹和保证铣刀的寿命。
图6-34 面铣刀几何角度的标注
第六章
第一节 数控铣削加工工艺的制订
一、零件的工艺性分析 1.零件的结构工艺性分析 1)检查零件的加工要求,如加工尺寸公差、几何公差及表 面粗糙度在现有的加工条件下是否可以得到保证,是否还 有更经济的加工方法或方案。 2)分析零件的形状、结构及尺寸的特点,确定零件上是否 有妨碍刀具运动的部位,是否有会产生加工干涉或加工不 到的区域,零件的最大形状尺寸是否超过机床的最大行程, 零件的刚性随着加工的进行是否有太大的变化等。
第一节 数控铣削加工工艺的制订
3)在零件上是否存在对刀具形状及尺寸有限制的部位和尺 寸要求,如过渡圆角、倒角、槽宽等,这些尺寸是否过于 凌乱,是否可以统一。 4)保证基准统一原则。 5)分析零件的变形情况。 2.零件毛坯的工艺性分析 1)毛坯应有充分、稳定的加工余量。 2)分析毛坯的余量大小及均匀性。 3)分析毛坯的装夹适应性。
第一节 数控铣削加工工艺的制订
图6-3 通用可调气动台虎钳 a)通用可调气动台虎钳 b) 、c)更换调整件 1、2—可更换调整件 3—活动钳口 4—粗调螺杆 5—活塞杆
6—杠杆 7—活塞
第一节 数控铣削加工工艺的制订
图6- 4 通用可调夹具系统 1—基础件 2—立式液压缸 3—卧式液压缸 4、5—销
第一节 数控铣削加工工艺的制订
图6-8 用鼓形铣刀分层铣削变斜角
数控编程中的工艺处理

数控编程中的工艺处理数控机床是根据编制的程序进行的,加工中的全部工序、工步,每道工序的切削用量、走刀路线、加工余量和所用刀具的尺寸、类型都需要预先确定好并编入程序中。
这就涉及工艺处理问题。
1、数控加工工艺的特点与内容1)数控加工工艺的特点(1)工序内容详细:数控加工工序卡中卡片中应包括具体的工步内容和工艺参数等信息,在编制数控加工程序时,每个动作、每个参数都应体现。
(2)工序内容简单:在支配数控加工时,一般应首先考虑使用一般机床加工困难、使用数控加工能明显提高效率和质量的简单零件,零件的工艺相应简单。
(3)工序集中:高档数控机床可以在一次或多次装夹中对零件进行多种加工,并完成由粗加工到精加工的过程,工序特别集中。
2)数控加工工艺的主要内容(1)数控加工零件或加工内容的选择(2)数控加工工艺性分析(3)数控加工工艺路线的设计(4)数控加工工序的具体设计,包括工步内容、对刀点、走刀路径、切削用量确定等2、数控加工零件或加工内容的选择两种状况:有毛坯和零件图样,选择合适的数控机床;有数控机床,选择合适零件。
考虑因素主要有:毛坯材料、类型;零件轮廓简单程度、尺寸大小;加工内容及精度、零件批量……3、数控加工工艺性分析1)采纳统一几何类型和尺寸2)内槽圆角半径不应过小3)槽底圆角半径不应过大4、数控加工工艺性路线的设计主要包括:机床选择、加工方法、装夹、加工阶段划分、工序支配等。
工序指一个零件在同一台机床上所完成的那部分工艺内容。
工步指零件在加工表面和加工刀具不变的状况下,所连续完成的那部分工艺内容。
工步的划分及加工挨次的支配主要考虑:加工精度和效率。
5、数控加工工序具体设计1. 零件装夹与夹具设计数控机床的夹具与传统夹具结构的差别:夹详细+定位+夹紧;不需要导向和对刀功能,夹具比较简洁。
数控夹具选用的主要原则:1)基准重合,以削减定位误差2)统一基准,削减重复定位次数,削减重复定位误差3)夹紧要牢靠;夹紧点分布要合理,夹紧力大小要适中且稳定,削减夹紧变形4)夹具结构应力求简洁,加工部位要放开5)数控夹具装卸应便利。
典型铣削零件加工的工艺分析及编程

典型铣削零件加工的工艺分析及编程1. 引言铣削是一种常见的机械加工方法,广泛应用于零件加工领域。
在铣削加工中,我们通常需要进行工艺分析和编程,以保证零件加工的准确性和效率。
本文将针对典型铣削零件的加工过程进行工艺分析,并介绍如何进行编程。
2. 零件加工的工艺分析在进行铣削零件加工之前,我们首先需要对零件的形状、尺寸、加工材料进行分析,以确定合适的工艺路线和加工参数。
2.1 零件形状分析零件的形状对于确定铣削工艺有重要影响。
常见的零件形状包括平面零件、曲面零件、孔型零件等。
不同形状的零件需要采用不同的加工策略和工艺路线。
2.2 尺寸分析零件的尺寸要求对于决定加工工艺参数也非常重要。
尺寸分析包括零件的最大尺寸、最小尺寸、公差要求等。
根据不同的尺寸要求,我们可以选择合适的刀具和机床进行加工。
2.3 加工材料分析加工材料的硬度、韧性、热传导性等性质也会对加工工艺产生影响。
选择合适的切削速度、进给量和切削深度可以提高加工质量和效率。
3. 零件加工的编程在确定了合适的工艺路线和加工参数之后,我们需要进行编程,将加工过程转化为机床可以理解和执行的指令。
3.1 编程语言介绍目前,常用的铣削加工编程语言包括G代码和M代码。
G代码用于定义运动轨迹和加工方式,M代码用于定义辅助功能和机床控制。
3.2 编程步骤编程的步骤包括创建编程文件、选择刀具和工艺路线、编写加工指令、设定初始位置等。
在编程过程中,需要考虑刀具半径补偿、切削参数调整和刀具路径优化等问题。
3.3 编程实例以下是一个简单的铣削编程实例:1. G90 G54 G17 G40 ;刀具半径编程方式选择,选择工作坐标系,选择平面2. M3 S1000 ;主轴启动,设置主轴转速3. G0 X0 Y0 Z20 ;快速定位到初始位置4. G1 Z-5 ;快速下刀到指定深度5. G2 X50 Y0 I25 J0 F200 ;顺时针沿圆弧加工6. G1 X100 ;快速移动到指定位置7. G1 Z-10 F100 ;沿Z轴下刀到指定深度8. G1 X50 ;移动到指定位置9. G1 Z-20 ;下刀到指定深度10. G2 X0 Y0 I-25 J0 ;逆时针沿圆弧加工11. G0 Z20 ;快速抬刀12. M5 ;主轴停止13. M30 ;程序结束4. 总结本文针对典型铣削零件的加工过程进行了工艺分析,并介绍了编程的相关知识。
模块五 典型零件数控铣削加工工艺分析.

图5-5 槽底平面圆弧对铣削工艺的影响
(4)保证基准统一原则 有些零件需要多次装夹才能完成加工时,如图5-6所示,由于数控铣削不 能采用“试切法”来接刀,会因为零件的重新安装而接不好刀。为避免两 次装夹误差,最好采用统一基准定位,因此零件上应有合适的孔作为定位 基准孔,如果零件上没有基准孔,可专门设置工艺孔作为定为基准(如在 毛坯上增加工艺凸耳设基准孔)。如实在无法制出基准孔,也要用经过精 加工的面作为统一基准。
一、零件图的工艺分析
数控铣削零件图纸工艺分析包括分析零件图纸技术要求、检查零件图的完 整性和正确性、零件的结构工艺性分析和零件毛坯的工艺性分析。 (一)分析零件图技术要求 分析铣削零件图技术要求时,主要考虑如下方面: (1)各加工表面的尺寸精度要求; (2)各加工表面的几何形状精度要求; (3)各加工表面之间的相互位置精度要求; (4)各加工表面粗糙度要求以及表面质量方面的其他要求; (5)热处理要求及其他要求。
图5-10 3轴联动行切法加工曲面的切削点轨迹
(二)划分加工阶段
1.加工阶段的划分 (1)粗加工阶段—主要任务是切除各表面上的大部分余量,其目的是提 高生产率。 (2)半精加工阶段—其任务是使主要表面达到一定的精度,留有一定的 精加工余量,为主要表面的精加工(精铣或精磨)做好准备,并完成一些 次要表面加工,如扩孔、攻螺纹、铣键槽等。 (3)精加工阶段—保证各主要表面达到图纸规定的尺寸精度和表面粗糙 度要求,其主要目标是如何保证加工质量。 (4)光整加工阶段—任务是对零件上精度和表面粗糙度要求很高的表面, 需要进行光整加工。其目的是提高尺寸精度、减小表面粗糙度。
模块五 典型零件数控铣削加工工艺分析
项目一
“法兰盘”零件加工工艺的编
制
【工作任务】
数控铣削加工工艺分析

浙江工业职业技术学院精品课程
(4)螺纹的加工
①
直径在M5mm~M20mm之间的螺纹,通常采用攻 螺纹的方法加工。
②
直径在M6mm以下的螺纹,在数控机床上完成底孔加 工后, 通过其他手段来完成攻螺纹。
直径在M25mm以上的螺纹,可采用镗刀片镗削加工 或采用圆弧插补(G02或G03)指令来完成。
③
浙江工业职业技术学院精品课程
式中,当被加工零件的曲面在ab段内是凸的时候 取“+”号,是凹的时候取“-”号。
浙江工业职业技术学院精品课程
3.3 工艺设计
1)工序的划分
2)加工余量的选择
3)进给路线的确定
浙江工业职业技术学院精品课程
1) 工 序 的 划 分 的 方 法
(1)按先面后孔的原则划分工序
(2)按所用刀具划分工序
(3)按粗、精加工划分工序
合理选择铣削方式,以提高零件的加工质量。
浙江工业职业技术学院精品课程
合理选取刀具的起刀点、切入和切出点及刀具的切入
和切出方式,保证刀具切入和切出的平稳性。 隙的带入而影响孔的位置精度;
位置精度要求高的孔系零件的加工应避免机床反向间
复杂曲面零件的加工应根据零件的实际形状、精度要
求、加工效率等多种因素来确定是行切还是环切,是 等距切削还是等高切削的加工路线等。
半精加和精加时,应在保证加工质量的前提下,兼顾 切削效率、经济性和加工成本。 具体数值应根据机床说明书、切削用量手册,刀具切 削参数,并结合实际经验而定。
浙江工业职业技术学院精品课程
1) 切 削 深 度 ap
切削深度的选取 主要由加工余量和表面质量的要 求决定的。原则上尽可能切削深度 选大些,可以减少走刀次数,但也 不能太大,否则会造成由于切削力 过大而造成“闷车”或蹦刃现象。
数控铣削加工工艺分析

数控铣削加工工艺分析一、加工工艺1.工艺流程:2.加工特点:(1)高精度:数控铣削加工可以实现高精度的加工,可以满足对零件精度要求较高的应用领域;(2)加工复杂零件:数控铣削加工可以通过合理设置刀具路径和切削参数来加工复杂形状的零件,具有很大的灵活性和可塑性;(3)高效率:数控铣削加工可以实现多种刀具的自动换刀,减少了换刀时间,并且可以通过自动化程度高的设备进行连续加工,提高了生产效率;(5)适应性强:数控铣削加工适用于各种材料的加工,如金属材料、非金属材料和复合材料等。
二、优点1.精度高:数控铣削加工可以实现高精度的加工,满足对尺寸和形状要求严格的零件加工需求;2.加工效率高:数控铣削加工由于采用自动化设备和自动换刀系统,可以减少换刀和人工操作时间,提高了生产效率;3.工艺灵活性好:数控铣削加工可以通过编写不同的加工程序,实现对不同形状和尺寸的零件加工,具有很大的灵活性;4.加工质量好:数控铣削加工减少了人为因素对加工质量的影响,提高了加工质量的稳定性和一致性。
三、应用领域1.机械制造业:数控铣削加工广泛应用于机械制造业,如汽车制造、航空航天、模具制造等,用于加工复杂形状的零件;2.电子工业:数控铣削加工可用于加工电子设备的外壳和零件,提高电子产品的精度和稳定性;3.医疗器械制造业:数控铣削加工可用于制造各种形状复杂的医疗器械,如假肢、人工关节等;4.能源行业:数控铣削加工可用于加工燃气轮机等能源设备的零部件;5.其他行业:数控铣削加工还可应用于船舶制造、冶金设备制造、精密仪器制造等行业。
综上所述,数控铣削加工工艺是一种高精度、高效率的加工方法,具有工艺灵活性和加工质量好的优点。
它在各种行业中有着广泛的应用,对于加工精度要求高、形状复杂的零件是一种不可或缺的加工手段。
数控铣削加工的工艺分析
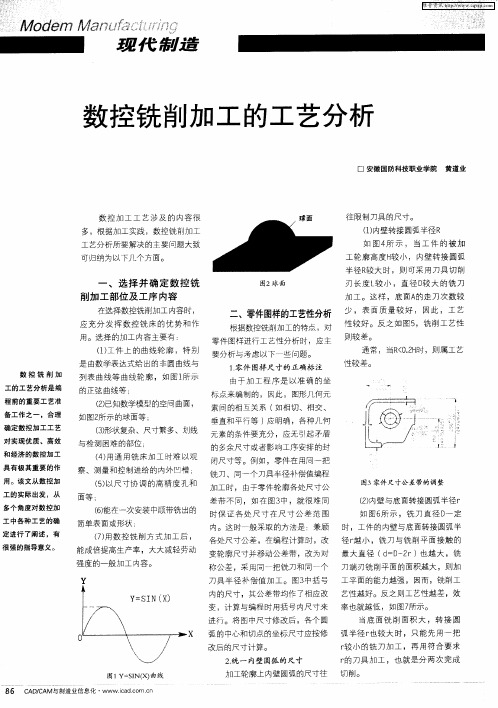
很强的指导意义。
能成倍提高 生产 率 ,大大减轻 劳动 强度 的一般加工 内容 。
Y
刀具 半径补 偿值加 工。 图3 中括号 工平面 的能 力越强 ,因而 ,铣 削工
Y s NL j : I X
内的尺寸 ,其公差带均作 了相应改 艺性越好。反之则工艺性越差 ,效
所 变 ,计算与编程时用括号 内尺寸来 率 也 就越 低 ,如 图 7 示 。
加工 。这 样 ,底 面A 的走 刀次数较
在选择 数控铣削加工内容 时,
应 充分 发 挥数 控 铣床 的优 势和 作
二、零件图 样的工艺性分析 少 ,表 面质 量较 好 ,因此 ,工艺
,铣削 工艺性 根据数控铣削加工的特点 ,对 性较 好。反 之如 图5 用。选择 的加工内容主要有 : 则较差。 零件图样进行工艺性分析时 ,应主 通 常 ,当 RO2 时 ,则 属 工 艺 < .H () 1工件 上 的曲线轮 廓 ,特 别 要分 析 与考 虑 以 下一 些 问题 。 是 由数学表达式给 出的非圆曲线 与 性较 差。 1零 件 图样 尺 寸 的 正 确 标 注 .
闭尺寸等。例如 ,零件在用同一把 铣刀、同一个刀具半径补偿值 编程
加工时 ,由于零件轮 廓各处尺 寸公
1 l_t 一
l
测 量和控 制进给 的内外 凹槽 ; () 5以尺 寸协调 的高 精 ̄ T @ Ln
用。该文从数控加
工的实际出发 ,从
图3零 件 尺 寸 公 差 带 的 调 整
多 ,根据加 工实践 ,数控铣  ̄3 I Jl ll j
工 艺分析所要解决 的主要 问题大致 可归纳为以下几个方面。
工轮 廓高度 H 小 ,内壁转接 圆弧 较
- 1、下载文档前请自行甄别文档内容的完整性,平台不提供额外的编辑、内容补充、找答案等附加服务。
- 2、"仅部分预览"的文档,不可在线预览部分如存在完整性等问题,可反馈申请退款(可完整预览的文档不适用该条件!)。
- 3、如文档侵犯您的权益,请联系客服反馈,我们会尽快为您处理(人工客服工作时间:9:00-18:30)。
数控铣削加工零件毛坯的工艺性分析要点
数控铣削加工零件毛坯的工艺性分析要点
”
在对零件图进行工艺性分析后,还应结合数控铣削的特点,对所用毛坯(常为板料、铸件自由锻及模锻件)进行工艺性分析,否则,如果毛坯不适合数控铣削,加工将很难进行下去;甚至会造成前功尽弃的后果。
这方面的教训在实际工作中也是不少见的,应引起充分重视。
根据经验,下列几方面应作为毛坯工艺性分析的要点:
①毛坯的加工余量是否充分,批量生产时的毛坏余量是否稳定。
毛坯主要指锻、铸件,因模锻时的欠压量与允许的错模量会造成余量多少不等,铸造时也会因沙型误差、收缩量及金属液体的流动性差不能充满型腔等造成余量不等。
此外,锻、铸后,毛坯的翘曲与扭曲变形量的不同也会造成加工余量不充分、不稳定。
在通用铣削工艺中,对上述情况常常采用划线时串位借料的方法来解决。
但是在采用数控铣削时,—次定位将决定工件的“命运”,加工过程的自动化很难照顾到何处余量不足的问题。
因此,除板料外,不管是锻件、铸件还是型材,只要准备采用数控铣削加工,其加工面均应有较充分的余量。
经验表明,数控铣削中最难保证的是加工面与非加工面之间的尺寸,这一点应该引起特别重视。
在这种情况下,如果已确定或准备采用数控铣削,就应事先对毛坯的设计进行必要更改或在设计时就加以充分考虑,即在零件图纸注明的非加工面处也增加适当余量。
②分析毛坯在安装定位方面的适应性。
主要是考虑毛坯在加工时的安装定位方面的可靠性与方便性,以便充分发挥数控铣削在一次安装中加工出许多待加工面。
主要是考虑要不要另外增加装夹余量或工艺凸台来定位与夹紧,什么地方可以制出工艺孔或要不要另外准备工艺凸耳来特制工艺孔。
值得注意的是,对某些看上去很难定位安装的或缺少定位基准孔与定位面的工件,只要在毛坯上想想办法,就迎刃而解了。
如图c所示工件,加工上下腹板与内外轮廓时因缺少定位安装面造成装夹困准,但只要在上下两筋上分别增加两个工艺台就可以较好地解决该工件的装夹困难问题。
再如图d所示,该工件缺少定位用的基准孔,用其他方法很难保工件定位精度,如果在图示位置增加两个工艺凸耳,在凸耳上制出走位基准孔,这一问题就能得到圆满的解决。
对于增加的工艺凸台或凸耳,可以在它们完成定位安裴使命后通过补加工去掉。
图c 图d
③分析毛坯的余量大小及均匀性。
主要是考虑在加工时要不要分层切削,分几层切削,也要分析加工中与加工后的变形程度,考虑是否应采取预防性措施与补救措施。
如对于热轧中、厚铝板,经淬火时效后很容易在加
工中与加工后变形,最好采用经预拉伸处理后的淬火板坯。