吹塑薄膜自动厚度控制技术
中空吹塑机壁厚控制器的技术要求和控制原理

在中空吹塑机的系统中,有一个叫壁厚控制器的系统,它对于设备有着很重要的作用,不知道大家对它的了解有多少呢?1、壁厚控制系统的技术要求壁厚控制系统是对模芯缝隙的开合度进行控制的系统,即位置伺服系统。
在中空容器的生产过程中,为了保证制品的质量,要求被控量能够准确地跟踪设置值,同时还要求响应过程尽可能快速。
以简单的10点壁厚控制器为例,在连续挤出的模式下,从模头挤出一个型坯最短时间约5s,在5s的时间内要实现一条有限长度的函数曲线,需要将其分成10个段落,在时间轴上,每个段落只有大约0.5s的时间,按照跟踪理论,壁厚控制器的单位脉冲过渡时间应为段落时间的1/5~1/10,即0.05~0.1s,这就要求系统响应非常迅速。
而在响应如此迅速的同时,还要保证被控的位置量能够准确跟踪设置值,否则,壁厚控制将失去意义。
要达到上述两种要求的控制效果,对于重载荷系统来说,正是壁厚控制系统设计的难点。
另外,由于在型坯轮廓曲线上取l0个点来描绘曲线,点与点之间还须进行插值处理,尽量使轮廓曲线光滑。
2、壁厚控制系统的控制原理壁厚控制系统采用闭环反馈设计,其组成部分包括壁厚控制器、电液伺服阀、动作执行机构和作为信号反馈装置的电子尺。
用户在壁厚控制器的面板上设定型坯壁厚轴向变化曲线,控制器根据曲线输出大小变化的电压或者电流信号至电液伺服阀,由电吹瓶机、吹膜机、吸塑机、塑料包装机械、制袋机液伺服阀驱动执行机构控制模芯的上下移动,从而造成模芯缝隙的变化。
电子尺通过测量缝隙的大小得出相应的电压信号反馈给壁厚控制器。
这就构成了闭环的壁厚控制系统。
杭州奥仕通自动化系统有限公司成立于2011年,是一家专业提供塑料机械行业自动化系统解决方案的高科技技术企业。
公司为意大利杰佛伦(GEFRAN)和法国赛德(CELDUC)在中国大陆地区的核心代理商,主要产品有塑料机械控制器(PLC)、伺服驱动器、位移传感器、压力传感器、注射力和合模力传感器、高温熔体压力传感器、固态继电器(SSR)、温控表等。
吹塑壁厚控制原理及控方法

中空吹塑机头分类及壁厚原理储料式机头分为中心入料式和侧向入料式。
侧向入料式是应用非常广泛的一种方式。
在储料式侧向入料中空吹塑机中,机头所起的作用是融合融料,并形成型坯,融料融合的关键是机头中的流道。
目前我国一些企业研究出了双层心形包络流道,但双层心形包络流道流道长度较短,压降较大,熔料融合后周向均匀性较差。
在此基础上国内研究出了双层双螺旋流道,如图1所示。
1.中心杆;2.推料盘;3.上端盖;4.入料口;5.分流芯套;6.分流孔;7.头外筒;8.外芯;9.内芯;10.推料筒;11.固定套;12.衬套;13.下端盖;14.芯模;15.口模;16.导流套;17.键;18.储料腔;19.推杆;20.外螺旋流道;21.导流通孔;22.分流锥图1双层双螺旋流道机头图1中,外芯设有两条呈180o对称缠绕的外螺旋流道,内芯设有两条呈180o 对称缠绕的内螺旋流道,内螺旋流道与外螺旋流道呈180o对称布置,外芯和内芯上的每条螺旋流道(内螺旋流道与外螺旋流道)的缠绕角度均为360o,以使外芯和内芯的360o的外壁面上的熔料充分均匀地融合。
工作时,熔料从入料口进入机头外筒,经过分流芯套的分流孔,由外芯上的分流锥顺利完成分流,熔料向分流锥两侧流动,并经导向流道转向90o后,引流到内、外芯分流处,一部分熔料由外芯上的外螺旋流道向下螺旋流动,另一部分则通过导流通孔流入到内芯的内螺旋流道中,熔料在内、外螺旋流道内流动时,一部分熔料随着内、外螺旋流道向下流动,另一部分熔料顺着内、外芯壁向下流向储料腔,这样可以保证360o都有熔料下流,使得熔料均匀融合。
型坯壁厚的自动控制有轴向控制和径向控制两种。
对于径向控制技术,我国还处于研究阶段,相对而言,轴向控制的研究成熟一些。
本文针对200L以上的大容量中空吹塑机进行了型坯壁厚的轴向控制研究。
型坯壁厚的轴向控制采用的是闭环控制技术。
用户在壁厚控制器的触摸屏面板上设定型坯壁厚轴向变化曲线,PLC控制器根据曲线把相应的电压或者电流信号传至电液伺服阀,由电液伺服驱动伺服油缸控制中心杆的上下移动,从而改变机头口模间隙。
吹厚膜有什么技巧和方法-

吹厚膜有什么技巧和方法?
吹厚膜技巧和方法如下。
1、选用合适的原材料,吹膜的原材料通常为高密度聚乙烯HDPE,低密度聚乙烯LDPE等塑料颗粒,不同的原材料具有不同的物理和化学性质,根据产品要求进行选择。
2、调节吹膜机的温度,吹膜机的温度对膜的质量有很大的影响,根据不同的原材料进行调节,通常来说,高密度聚乙烯的吹膜温度为180℃-230℃,低密度聚乙烯的吹膜温度为160℃-200℃。
3、调节吹膜机的压力,吹膜机的压力对膜的厚度和平整度有很大的影响,一般来说,膜的厚度通过调节吹膜机的压力来控制。
4、控制冷却效果,吹膜过程中需要通过冷却来使膜迅速凝固,保证膜的平整度和透明度,通过调节冷却风扇的速度和方向来控制冷却效果。
5、控制拉伸速度,在吹膜机的出口处,通过拉伸膜来使其变薄并增加透明度,拉伸速度的大小会影响到膜的拉伸效果和厚度。
—1 —。
中空吹塑成型机生产中如何控制塑料坯壁厚-

中空吹塑成型机生产中如何掌控塑料坯壁厚?使用中空吹塑机/进行生产的产品,要求壁厚均匀。
通常0.2L以下的中空容器可以不带型坯壁厚掌控装置,其他情况应考虑使用型坯壁厚掌控装置,特别是多而杂截面的中空成型制品。
目前,通常采纳更改机头套与模芯处的模唇间隙的方法实现壁厚掌控。
依据机头套、模芯形状的不同,唇口间隙的调整方法也不同。
模芯的上下运动一般采纳液压缸驱动。
当中空吹塑机加工形状较简单的塑料中空容器时,可用开关式液压系统实现。
电液换向阀只接受通电或断电信号,使液压缸向上或向下,液压缸移动的距离(即口模的开度变化)由上、下限位螺母调定,液压缸移动的速度由流量阀的节流作用设定,电液换向阀的电信号由时间继电器掌控。
这种掌控方法简单、价廉,但壁厚变化规律简单,只有两种壁厚变化,只能用于挤吹形状简单的中空容器。
当涉及大型的且形状多而杂的制品时,型坯壁厚掌控系统须是一个位置掌控系统,其中芯棒位置掌控精度是决议型坯壁厚掌控效果的关键,要求运动平稳、位置精度高、响应快,具有良好的重复精度。
目前,中空成型型坯掌控电液位置掌控系统按使用的掌控阀不同,可分为两大类:电液比例掌控系统和电液伺服掌控系统。
壁厚掌控系统采纳闭环反馈设计,其构成包括壁厚掌控器、电液伺服阀、动作执行机构和作为信号反馈装置的电子尺。
用户在壁厚掌控器的面板上设定型坯壁厚轴向变化曲线,掌控器依据曲线输出大小变化电压或者电流信号至电液伺服阀,由电液伺服阀驱动执行机构掌控模芯的上下移动,从而更改模芯缝隙。
电子尺通过测量缝隙的大小得出相应的电压信号反馈给壁厚掌控器,这就构成了闭环的壁厚掌控系统。
25点型坯壁厚掌控器工作原理。
在储料工作期间,位移传感器2随时检测储料缸内储料位置,当储料量达到预选储料时,掌控系统发出“储料到位”信号,系统就转入“注射”工作程序。
注射型坯时,位移传感器2连续检测注射量,掌控系统将整个注射量均匀地25等分,并使其与型坯上的各等分区所需厚度相应编码,每等分区域都配备有可变电位器,依据其制品要求任意更改25只电位器的旋钮,预选开口的间隙。
吹塑机自动厚度控制系统设计

2 控制方案设计 2.1 控制系统特点
自动模头是一种较为复杂的过程控制系统, 系统控制对象 为分布在模环上的热膨胀机构内加热器, 反馈信号为薄膜横向 厚度信号。 从控制过程看,薄膜厚度变化与热膨胀机构之间控制 量变化关系较为复杂, 不同厚度薄膜以及热膨胀机构变化与控 制量之间呈非线性无规律变化, 且圆周上相邻点调整互相影响 都很大,同时热膨胀机构调整滞后性较强,不同时刻之间又互相 关联,对于这种复杂过程控制系统,很难建立其精确控制模型。 2.2 控制方式选择
4 结束语 自动厚度控制系统采用模糊-PID 控制算法控制方式,解决
单一控制存在的调节时间长、超调量大、参数难以确定、无法消 除静差、 震动及系统的动态响应性和控制精度都达不到要求等 问题。 在实际使用过程比单一控制性能有很大的提高,可以使吹 塑薄膜厚薄均匀度从 8%提高到 3~4%,调整时间缩短 20 分钟, 静态偏差及震动都有很大提高,长时间运行稳定可靠,取得了较 好的控制效果。
Abstract This paper analyse working principle and control requirement of gauge control system,explain system construction,calculation and software design by industrial computer on the basis of gauge control characteristics of automatic die head, and introduces the application of Fuzzy-PID control calculation in the system which is proved to be fast and precise control with stable system and better property than single-way control. Keywords:blown film line,automatic die head,fuzzy,PID,thickness measuring
【吹膜技术】吹膜生产中的三个关键控制要点

【吹膜技术】吹膜生产中的三个关键控制要点吹膜生产中温度对质量的影响塑化是否完全和均匀, 泡形是否稳定, 温度是主要工艺条件之一。
在生产聚乙烯吹塑薄膜时, 应根据原料的熔体指数( M I ) 和不同的产品规格, 选择不同的温度, 一般熔体指数越大, 加工时所用的温度就越低, 反则就高。
如挤出机温度低, 则塑料粘度大, 薄膜透明度差, 易出现未塑化的晶点和云雾, 薄膜易拉断, 薄膜的断裂伸长率降低。
若挤出机温度偏高, 塑料粘度降低, 流动性很大, 薄膜开口性差, 易造成生产不稳定, 但透明度提高。
继续升温, 则物料过热分解, 薄膜发黄, 有黄黑焦点。
所以温度不稳定会使泡形不正, 影响产品质量, 甚至造成次品。
对吹塑薄膜的厚度控制薄膜厚度是质检主要指标之一, 影响厚度的因素有:①机头设计型腔结构流畅, 无死角, 使物料流速一致均匀。
②模口间隙均匀, 不偏中,并能得心应手地调节, 控制出料量的均匀。
③冷却风环的吹风流量和流速也要稳定, 否则,薄膜冷却差的部分就要延伸变薄, 反则变厚, 利用风力来调节厚薄。
④机头加热装置: 机头加热分布要均匀, 以保证模口处均等的树脂流量。
否则, 温度高的部分薄膜延伸、膨胀变薄;反之变厚。
⑤主机运转正常, 保证出料量的均匀, 牵引速度也要均匀。
⑥外来气流影响, 在吹膜管冷却线下部位, 不允许出现外来风力波动引起的气流干扰, 可用塑料薄膜设帷幕。
螺杆转速对薄膜生产质量的影响杆转速增加, 塑料在机筒内停留时间短, 塑化不良, 薄膜出现塑化不完全的晶点,或是由于挤出量提高, 冷却部位不相适应, 也会使薄膜外观质量不好。
在生产中也有特殊情况出现, 螺杆转速的增加, 出料量也就增加, 而加热器温度并非继续升温, 生产仍正常, 这是剪切热所致, 但总须与牵引比相匹配, 产品质量才能稳定。
螺杆转速降低, 有利于膜管冷却。
在塑化不完全的情况下, 降低螺杆转速有利于提高产品质量, 但转速低, 塑料在机筒停留时间长, 易分解。
LDPE吹塑薄膜生产工艺的控制要点
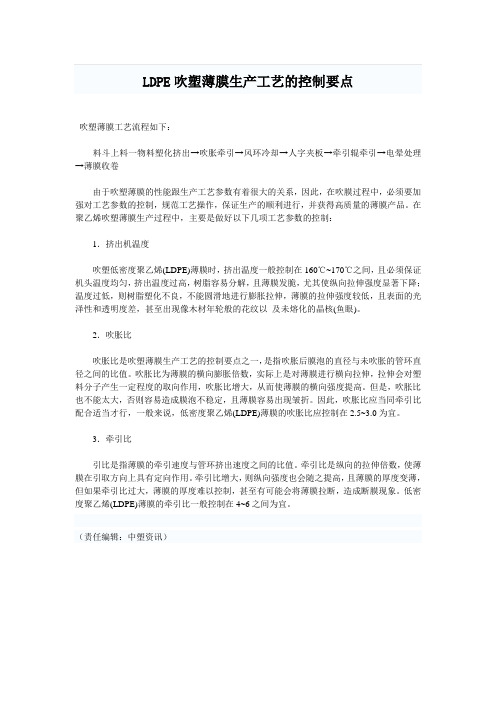
LDPE吹塑薄膜生产工艺的控制要点吹塑薄膜工艺流程如下:料斗上料一物料塑化挤出→吹胀牵引→风环冷却→人字夹板→牵引辊牵引→电晕处理→薄膜收卷由于吹塑薄膜的性能跟生产工艺参数有着很大的关系,因此,在吹膜过程中,必须要加强对工艺参数的控制,规范工艺操作,保证生产的顺利进行,并获得高质量的薄膜产品。
在聚乙烯吹塑薄膜生产过程中,主要是做好以下几项工艺参数的控制:1.挤出机温度吹塑低密度聚乙烯(LDPE)薄膜时,挤出温度一般控制在160℃~170℃之间,且必须保证机头温度均匀,挤出温度过高,树脂容易分解,且薄膜发脆,尤其使纵向拉伸强度显著下降;温度过低,则树脂塑化不良,不能圆滑地进行膨胀拉伸,薄膜的拉伸强度较低,且表面的光泽性和透明度差,甚至出现像木材年轮般的花纹以及未熔化的晶核(鱼眼)。
2.吹胀比吹胀比是吹塑薄膜生产工艺的控制要点之一,是指吹胀后膜泡的直径与未吹胀的管环直径之间的比值。
吹胀比为薄膜的横向膨胀倍数,实际上是对薄膜进行横向拉伸,拉伸会对塑料分子产生一定程度的取向作用,吹胀比增大,从而使薄膜的横向强度提高。
但是,吹胀比也不能太大,否则容易造成膜泡不稳定,且薄膜容易出现皱折。
因此,吹胀比应当同牵引比配合适当才行,一般来说,低密度聚乙烯(LDPE)薄膜的吹胀比应控制在2.5~3.0为宜。
3.牵引比引比是指薄膜的牵引速度与管环挤出速度之间的比值。
牵引比是纵向的拉伸倍数,使薄膜在引取方向上具有定向作用。
牵引比增大,则纵向强度也会随之提高,且薄膜的厚度变薄,但如果牵引比过大,薄膜的厚度难以控制,甚至有可能会将薄膜拉断,造成断膜现象。
低密度聚乙烯(LDPE)薄膜的牵引比一般控制在4~6之间为宜。
(责任编辑:中塑资讯)。
吹塑壁厚控制原理及控方法

中空吹塑机头分类及壁厚原理储料式机头分为中心入料式和侧向入料式。
侧向入料式是应用非常广泛的一种方式。
在储料式侧向入料中空吹塑机中,机头所起的作用是融合融料,并形成型坯,融料融合的关键是机头中的流道。
目前我国一些企业研究出了双层心形包络流道,但双层心形包络流道流道长度较短,压降较大,熔料融合后周向均匀性较差。
在此基础上国内研究出了双层双螺旋流道,如图1所示。
1.中心杆;2.推料盘;3.上端盖;4.入料口;5.分流芯套;6.分流孔;7。
头外筒;8.外芯;9.内芯;10。
推料筒;11。
固定套;12。
衬套;13.下端盖;14.芯模;15.口模;16.导流套;17。
键;18.储料腔;19.推杆;20.外螺旋流道;21。
导流通孔;22。
分流锥图1 双层双螺旋流道机头图1中,外芯设有两条呈180o对称缠绕的外螺旋流道,内芯设有两条呈180o 对称缠绕的内螺旋流道,内螺旋流道与外螺旋流道呈180o对称布置,外芯和内芯上的每条螺旋流道(内螺旋流道与外螺旋流道)的缠绕角度均为360o,以使外芯和内芯的360o的外壁面上的熔料充分均匀地融合。
工作时,熔料从入料口进入机头外筒,经过分流芯套的分流孔,由外芯上的分流锥顺利完成分流,熔料向分流锥两侧流动,并经导向流道转向90o后,引流到内、外芯分流处,一部分熔料由外芯上的外螺旋流道向下螺旋流动,另一部分则通过导流通孔流入到内芯的内螺旋流道中,熔料在内、外螺旋流道内流动时,一部分熔料随着内、外螺旋流道向下流动,另一部分熔料顺着内、外芯壁向下流向储料腔,这样可以保证360o都有熔料下流,使得熔料均匀融合.型坯壁厚的自动控制有轴向控制和径向控制两种。
对于径向控制技术,我国还处于研究阶段,相对而言,轴向控制的研究成熟一些.本文针对200L以上的大容量中空吹塑机进行了型坯壁厚的轴向控制研究。
型坯壁厚的轴向控制采用的是闭环控制技术。
用户在壁厚控制器的触摸屏面板上设定型坯壁厚轴向变化曲线,PLC 控制器根据曲线把相应的电压或者电流信号传至电液伺服阀,由电液伺服驱动伺服油缸控制中心杆的上下移动,从而改变机头口模间隙.同时,连接中心杆的伺服油缸活塞杆上安有传感器(磁悬浮电子尺),电子尺可感知头口模间隙的大小并反馈给PLC控制器,在PLC控制器内与标准信号进行比较,然后经伺服功率放大器传送给电液伺服阀,再通过伺服阀驱动伺服油缸,油缸带动中心杆移动,最终控制口模的开度,完成对型坯壁厚的控制.型坯壁厚控制的结构图如图2所示.本文研究的型坯壁厚控制系统是一个位置控制系统,由电液伺服系统组成。
- 1、下载文档前请自行甄别文档内容的完整性,平台不提供额外的编辑、内容补充、找答案等附加服务。
- 2、"仅部分预览"的文档,不可在线预览部分如存在完整性等问题,可反馈申请退款(可完整预览的文档不适用该条件!)。
- 3、如文档侵犯您的权益,请联系客服反馈,我们会尽快为您处理(人工客服工作时间:9:00-18:30)。
吹塑薄膜自动厚度控制技术
评论:0 条查看:605 次airring发表于2009-12-15 16:28
直到2002年,一直在寻找自动厚度控制技术的吹塑薄膜加工厂商才有了分段式机头装置、IBC基装置和几种分段式风环供选用。
现在,至少有9种自动厚度控制机头(包括两种用于高颈膜泡的机头)和多种风环面世,据称它们都能提高薄膜厚度的均匀度,但又有所区别。
美国的吹塑薄膜加工厂商在如何生产平整度更高的薄膜方面落后于欧洲同行5~8年。
几乎100%的欧洲吹塑薄膜厂商的生产线上都采用了重量控制技术,而且许多生产线上都采用了薄膜自动厚度控制技术。
”而在美国,采用重量控制的加工厂商只有30%,采用厚度控制的不到5%。
美国加工厂商大多采用国产的老式吹塑薄膜生产线,使用的是摆动机头,数量多得惊人,这限制了想进行自动厚度控制装置更新的机器的数量。
自动机头厚度控制不能与摆动式机头配套使用,分段式风环与摆动式机头配套使用不如与固定机头和摆动式牵引设备配套使用有效。
自动厚度控制技术在美国应用的另一个障碍是其膜卷销售传统上是以磅为单位,而欧洲是以面积为单位来销售的。
ISOPoly薄膜公司的车间主任
Tom Saxton解释说,“我们约有85%的用户仍旧以磅为单位来购买膜卷”。
ISOPolv两条最先进的薄膜生产线(从W&H公司购买的三层共挤装置)采用了自动机头厚度控制技术。
ISOPoly公司投资自动厚度控制技术是为了获得竞争优势,因为均匀度更高的薄膜在后续的复合和印刷中会运行得更快更好。
将自己生产的薄膜加工成袋及复合产品的厂商如Plassein国际公司等急于改用自动厚度控制技术,因为这将直接转化成更高的产率。
Plassein公司使用的单层和三层共挤高颈HDPE薄膜生产线是从Hosokawa Alpine公司购买的,生产线上配备了Plast—Control公司的风环自动厚度控制装置和重量控制技术。
HDPE膜泡的缺点是弹性大,难以控制,但Plassein公司将其厚度保持在标准设定值的±10%之内,实际厚度变化范围为±13%~15%。
这对于HDPE来说已经很严格了。
很明显,现在自动厚度控制这个字眼出现得越来越多了。
2002年,有100多台自动厚度控制装置卖到了美国——超过了以前历年之和。
但并不是所有加工厂商都愿意购买。
Reifenhauser的美国总经理John Wise说,“有一些加工厂商被迫采用自动厚度控制装置是因为他们的用户对此有要求。
”例如,用户需要更严格的厚度控制,从而保证薄膜能够在最先进的高速印刷机上运行良好。
由于每条采用自动厚度控制技术的薄膜生产线要花费25万美元,问题的关键是如何选择生产线并使其能够物超所值。
一、品种繁多的薄膜厚度自动控制装置
过去两年来,市场上的薄膜自动厚度控制装置发展迅速。
由于W&H长期拥有的分段式机头专利到期,至少还有8家机器制造商推出了分段模唇上带有加热器的自动机头。
另外,包括W&H在内的多家公司都推出了自动风环装置。
最初W&H的自动机头控制器采用压缩空气冷却膜泡周边的特定区域,而现在所有分段式机头都用加热器局部加热。
分段式风环不能改变空气体积或速度来冷却膜泡的局部区域,但是有3种风环装置是加热空气。
所有这些装置都是根据安装在膜泡中上部的摆动传感器采集到的薄膜厚度值来调整厚度。
但厚度读数受到多种因素的影响,如膜泡的颤动、来自不相关机器方向厚度变化的干扰等,而这些都是机头、风环无法校正的。
电容厚度仪可能是最常用的测厚仪,但阻透薄膜一般采用β或x射线仪测量厚度,因为它们用于EVOH和尼龙树脂时更精确。
接触式电容厚度仪不适合于有些薄膜,例如,FlexTech已转而采用非接触x射线传感器,因为接触式厚度仪会划伤甚至刺破薄膜(有一些较新的电容仪是非接触性的)。
传感器测完膜泡上某一特定点的厚度之后,自动测厚软件进行计算,后推确定出熔体通过机头或风环时的点位。
然后,软件对机头上的加热器发出指令,打开或关闭,或对风环内的气阀发出指令,打开或关闭。
这种反向定位软件必须考虑到生产线的速度和机头或牵引摆动,这是自动厚度装置设计难度最大的部分。
实际上,与没有厚度控制的同种吹塑薄膜相比,不论是机头型还是风环型的所有自动厚度控制装置都能够将厚度均匀度的基本偏差减小50%。
德国Nordenia公司的技术主任JuppWilling解释说,“这就意味着如果你有一台基本偏差为20%的老式机头,采用自动厚度控制后,偏差会降至10%。
如果你的机头质量高,基本偏差为15%,采用自动厚度控制后,偏差会降至7%。
”Nordenia 全球范围内的吹塑薄膜生产线都采用了自动厚度控制技术。
Hosokawa Aopine美国公司总裁DavidNunes说,“为了充分利用实时自动厚度控制的优势,无论是机头式还是风环式厚度控制装置都需要稳定不变的工艺,这不仅仅是正确设计机头的问题,还包括挤出机、冷却装置、风环和IBC
的设计。
”
机头质量越高,薄膜厚度控制的要求越低。
W&H公司负责市场和业务开发的营销主任Christoff Herschbach说,“设计优异的机头,优化用于一种或少数几种材料,用与不用自动厚度控制装置都能加工出厚度精度相同的薄膜”。
但是,加工厂商一般都想要灵活性大的机头,能加工各种不同材料,这就增加了厚度变化幅度,需要进行厚度控制。
Tyco公司的Wright警告说,“自动厚度控制技术也必须正确使用,否则生产出的薄膜的质量会更差。
”
1.机头模唇与风环的比较
很多加工厂商都认为,在启动和更换时,分段式机头对膜泡的稳定比风环慢得多。
机头内的加热器必须热起来,将热量传递给熔体,因此响应时间可能为2~3分钟,而冷却空气在1秒或2秒内就会对熔体产生影响。
因此,采用两种装置进行生产的加工厂商认为,频繁更换薄膜品种时风环更好。
不过,另一方面,机头内的加热器对膜泡上熔体的影响位置比风环低
150mm,因此Kiefel公司总裁Steven Engel说,分段式机头产生的厚度偏差从根本上低于风环。
Kiefel既生产分段式机头,也生产分段式风环。
风环在后面影响熔体,所以受到限制。
德国Kiefel挤出公司技术主任Joehen Hennes博士说,“熔体到达风环时,已经有点凉了,所以达不到你想要的结果”。
Alpine公司也认为,分段式机头比风环更精确,尤其是大直径风环。
Addex公司称,其IBC基自动厚度控制装置也很有效,因为它也在机头模唇处影响熔体。
在挤出厚27.5~75um的LDPE和LLDPE薄膜时,Addex保证其控制装置的精确度达到±3.5%~5.5%(3sigma)。
与分段式机头相比,分段式风环更容易改装到现有设备上,费用也低,因为采用风环时不需要对机头进行改造。
分段式风环与其它直径的机头匹配时也比较容易。
Reifenhauser首席工程师Bernd Schroeter解释说,他们的直径350mm 机头的自动机头和风环装置的初始成本几乎相等,但如果用户决定改用直径
300mm的机头,风环可以很容易地用嵌件来更改,而采用分段式机头时一般需要一个全新的机头。
Kuhne公司正在试验一种新型设计的装置,将加热器的环放在机头内模唇下方150mm处,比其他任何装置都能更快地调控熔体,并为机头嵌件留下空间以改变膜泡直径。
Kuhne相信,这是首台可以容纳可拆卸机头嵌件的机头基自动厚度控制装置。
一些供应商认为,分段式机头需要的维护比分段式风环少,分段式风环上有步进电机和不断运动的气阀。
不过,磨损不是主要问题,任何一个气阀一天的运动时间仅仅20~30秒。
据说分段式机头的能耗大于分段式风环。
估计一台W&H机头每年的能耗在8000~12000美元(具体能耗取决于利用成本)”。