毕业设计外文文献格式
毕业论文(设计)外文文献翻译及原文
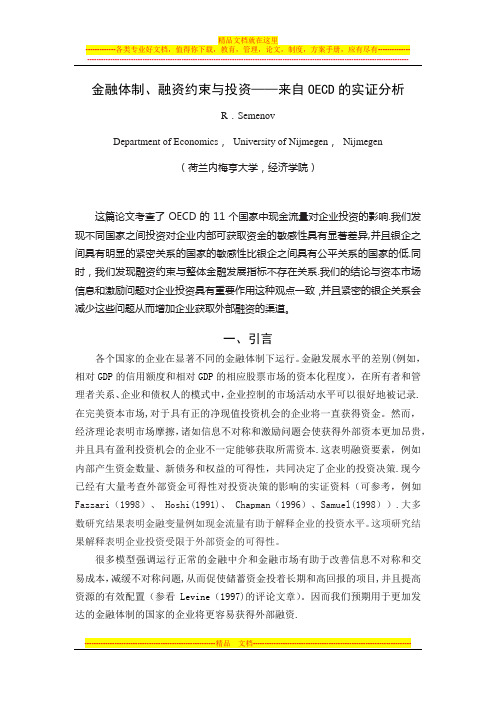
金融体制、融资约束与投资——来自OECD的实证分析R.SemenovDepartment of Economics,University of Nijmegen,Nijmegen(荷兰内梅亨大学,经济学院)这篇论文考查了OECD的11个国家中现金流量对企业投资的影响.我们发现不同国家之间投资对企业内部可获取资金的敏感性具有显著差异,并且银企之间具有明显的紧密关系的国家的敏感性比银企之间具有公平关系的国家的低.同时,我们发现融资约束与整体金融发展指标不存在关系.我们的结论与资本市场信息和激励问题对企业投资具有重要作用这种观点一致,并且紧密的银企关系会减少这些问题从而增加企业获取外部融资的渠道。
一、引言各个国家的企业在显著不同的金融体制下运行。
金融发展水平的差别(例如,相对GDP的信用额度和相对GDP的相应股票市场的资本化程度),在所有者和管理者关系、企业和债权人的模式中,企业控制的市场活动水平可以很好地被记录.在完美资本市场,对于具有正的净现值投资机会的企业将一直获得资金。
然而,经济理论表明市场摩擦,诸如信息不对称和激励问题会使获得外部资本更加昂贵,并且具有盈利投资机会的企业不一定能够获取所需资本.这表明融资要素,例如内部产生资金数量、新债务和权益的可得性,共同决定了企业的投资决策.现今已经有大量考查外部资金可得性对投资决策的影响的实证资料(可参考,例如Fazzari(1998)、 Hoshi(1991)、 Chapman(1996)、Samuel(1998)).大多数研究结果表明金融变量例如现金流量有助于解释企业的投资水平。
这项研究结果解释表明企业投资受限于外部资金的可得性。
很多模型强调运行正常的金融中介和金融市场有助于改善信息不对称和交易成本,减缓不对称问题,从而促使储蓄资金投着长期和高回报的项目,并且提高资源的有效配置(参看Levine(1997)的评论文章)。
因而我们预期用于更加发达的金融体制的国家的企业将更容易获得外部融资.几位学者已经指出建立企业和金融中介机构可进一步缓解金融市场摩擦。
中英文论文参考文献标准格式 超详细
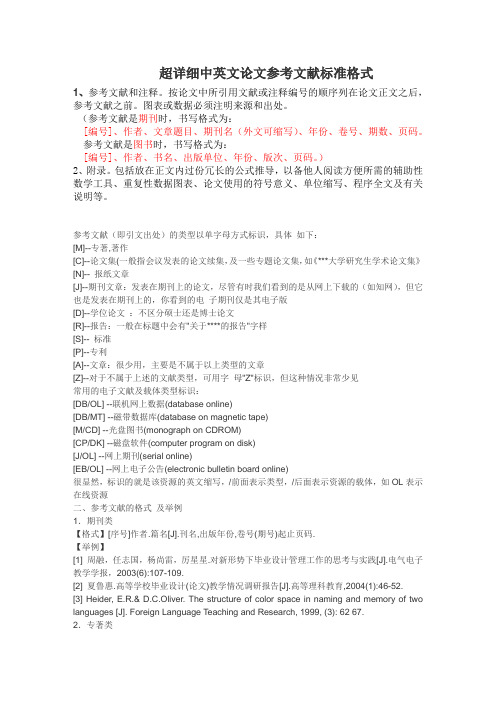
超详细中英文论文参考文献标准格式1、参考文献和注释。
按论文中所引用文献或注释编号的顺序列在论文正文之后,参考文献之前。
图表或数据必须注明来源和出处。
(参考文献是期刊时,书写格式为:[编号]、作者、文章题目、期刊名(外文可缩写)、年份、卷号、期数、页码。
参考文献是图书时,书写格式为:[编号]、作者、书名、出版单位、年份、版次、页码。
)2、附录。
包括放在正文内过份冗长的公式推导,以备他人阅读方便所需的辅助性数学工具、重复性数据图表、论文使用的符号意义、单位缩写、程序全文及有关说明等。
参考文献(即引文出处)的类型以单字母方式标识,具体如下:[M]--专著,著作[C]--论文集(一般指会议发表的论文续集,及一些专题论文集,如《***大学研究生学术论文集》[N]-- 报纸文章[J]--期刊文章:发表在期刊上的论文,尽管有时我们看到的是从网上下载的(如知网),但它也是发表在期刊上的,你看到的电子期刊仅是其电子版[D]--学位论文:不区分硕士还是博士论文[R]--报告:一般在标题中会有"关于****的报告"字样[S]-- 标准[P]--专利[A]--文章:很少用,主要是不属于以上类型的文章[Z]--对于不属于上述的文献类型,可用字母"Z"标识,但这种情况非常少见常用的电子文献及载体类型标识:[DB/OL] --联机网上数据(database online)[DB/MT] --磁带数据库(database on magnetic tape)[M/CD] --光盘图书(monograph on CDROM)[CP/DK] --磁盘软件(computer program on disk)[J/OL] --网上期刊(serial online)[EB/OL] --网上电子公告(electronic bulletin board online)很显然,标识的就是该资源的英文缩写,/前面表示类型,/后面表示资源的载体,如OL表示在线资源二、参考文献的格式及举例1.期刊类【格式】[序号]作者.篇名[J].刊名,出版年份,卷号(期号)起止页码.【举例】[1] 周融,任志国,杨尚雷,厉星星.对新形势下毕业设计管理工作的思考与实践[J].电气电子教学学报,2003(6):107-109.[2] 夏鲁惠.高等学校毕业设计(论文)教学情况调研报告[J].高等理科教育,2004(1):46-52.[3] Heider, E.R.& D.C.Oliver. The structure of color space in naming and memory of two languages [J]. Foreign Language Teaching and Research, 1999, (3): 62 67.2.专著类【格式】[序号]作者.书名[M].出版地:出版社,出版年份:起止页码.【举例】[4] 刘国钧,王连成.图书馆史研究[M].北京:高等教育出版社,1979:15-18,31.[5] Gill, R. Mastering English Literature [M]. London: Macmillan, 1985: 42-45.3.报纸类【格式】[序号]作者.篇名[N].报纸名,出版日期(版次).【举例】[6] 李大伦.经济全球化的重要性[N]. 光明日报,1998-12-27(3).[7] French, W. Between Silences: A Voice from China[N]. Atlantic Weekly, 1987-8-15(33). 4.论文集【格式】[序号]作者.篇名[C].出版地:出版者,出版年份:起始页码.【举例】[8] 伍蠡甫.西方文论选[C]. 上海:上海译文出版社,1979:12-17.[9] Spivak,G. "Can the Subaltern Speak?"[A]. In C.Nelson & L. Grossberg(eds.). Victory in Limbo: Imigism [C]. Urbana: University of Illinois Press, 1988, pp.271-313.[10] Almarza, G.G. Student foreign language teacher's knowledge growth [A]. In D.Freeman and J.C.Richards (eds.). Teacher Learning in Language Teaching [C]. New York: Cambridge University Press. 1996. pp.50-78.5.学位论文【格式】[序号]作者.篇名[D].出版地:保存者,出版年份:起始页码.【举例】[11] 张筑生.微分半动力系统的不变集[D].北京:北京大学数学系数学研究所, 1983:1-7. 6.研究报告【格式】[序号]作者. 篇名[R].出版地:出版者,出版年份:起始页码.【举例】[12] 冯西桥.核反应堆压力管道与压力容器的LBB分析[R].北京:清华大学核能技术设计研究院, 1997:9-10.7.专利【格式】[序号]专利所有者.题名[P].国别:专利号,发布日期.【举例】[13] 姜锡洲.一种温热外敷药制备方案[P].中国专利:881056073, 1989 07 26.8.标准【格式】[序号]标准编号,标准名称[S].【举例】[14] GB/T 16159-1996, 汉语拼音正词法基本规则[S].9.条例【格式】[序号]颁布单位.条例名称.发布日期【举例】[15] 中华人民共和国科学技术委员会.科学技术期刊管理办法[Z].1991-06-0510.电子文献【格式】[序号]主要责任者.电子文献题名.电子文献出处[电子文献及载体类型标识].或可获得地址,发表或更新日期/引用日期.【举例】[16] 王明亮.关于中国学术期刊标准化数据库系统工程的进展[EB/OL].http:///pub/wml.txt/980810 2.html, 1998 08 16/1998 10 04.[17] 万锦.中国大学学报论文文摘(1983 1993).英文版[DB/CD]. 北京: 中国大百科全书出版社, 1996.11.各种未定义类型的文献【格式】[序号] 主要责任者.文献题名[Z].出版地:出版者, 出版年.特别说明:凡出现在"参考文献"项中的标点符号都失去了其原有意义,且其中所有标点必须是半角,如果你的输入法中有半角/全解转换,则换到半角状态就可以了,如果你的输入法中没有这一转换功能,直接关闭中文输入法,在英文输入状态下输入即可.其实,很多输入法(如目前比较流行的搜狐输入法)都提供了四种组合:(1)中文标点+ 全角:这时输入的标点是这样的,:【1】-(而这时,我没有找到哪个键可以输入/ 符号)也就是说,这些符号是一定不能出现在"参考文献"中的;(2)中文标点+半角:这时输入的标点是这样的,:【1】-(这时,我还是没有找到哪个键可以输入/ 符号)也就是说,这些符号也不能出现在"参考文献"中的;上面列出的符号,中间没有任何的空格,你能看出它们有什么区别吗?我看只是-的宽度有一点点不同,其它都一样(3)英文标点+全角:这时输入的标点是这样的,.:[1]-/(4)英文标点+半角:这时输入的标点是这样的,.:[1]-/从这两项可以明显的看出,半角和全角其实最大的差别是所占的宽度不一样,这一点对于数字来说最为明显,而英文标点明显要比中文标点细小很多(也许因为英文中,标点的功能没有中文那么复杂,就是说英文中标点符号的能力没有中文那么强大)所以,很多人在写"参考文献" 时,总是觉得用英文标点+半角很不清楚,间距也太小,其实这点完全不用担心如果你觉得真的太小不好看,就用英文标点+全角吧而在[1] 之后,一般也都有一个空格更为详细的内容,大家可以从附件中下载国家标准《文后参考文献著录规则GB/T 7714-2005》查看,不过,很长很烦,拿出点耐心看吧对于英文参考文献,还应注意以下两点:①作者姓名采用"姓在前名在后"原则,具体格式是:姓,名字的首字母. 如:Malcolm Richard Cowley 应为:Cowley, M.R.,如果有两位作者,第一位作者方式不变,&之后第二位作者名字的首字母放在前面,姓放在后面,如:Frank Norris 与Irving Gordon应为:Norris, F. &I.Gordon.②书名、报刊名使用斜体字,如:Mastering English Literature,English Weekly.三、注释注释是对论文正文中某一特定内容的进一步解释或补充说明注释应置于本页页脚,前面用圈码①、②、③等标识。
本科毕业设计外文翻译需要注意的问题

外文翻译需要注意的问题,
1 外文文献的出处不要翻译成中文,且写在中文译文的右上角(不是放在页眉处);会议要求:名称、地点、年份、卷(期),等
2 作者姓名以及作者的工作单位也不用必须翻译;
3 abstract翻译成“摘要”,不要翻译成“文章摘要”等其他词语;
4 Key words翻译成“关键词”
5 introduction 翻译成“引言”(不是导言)
6 各节的标号I、II等可以直接使用,不要再翻译成“第一部分”“第二部分”,等。
7 注意排版格式,都是单排版,行距1.25,字号小4号,等(按照格式要求)
8 里面的图可以拷贝粘贴,但要将图标、横纵指标的英文标注翻译成中文
9里面的公式、表不可以拷贝粘贴,要自己重新录入、重新画表格
大家翻译时,可以将太长的句子用两句或多句描述。
本科毕业设计(论文)外文翻译基本规范
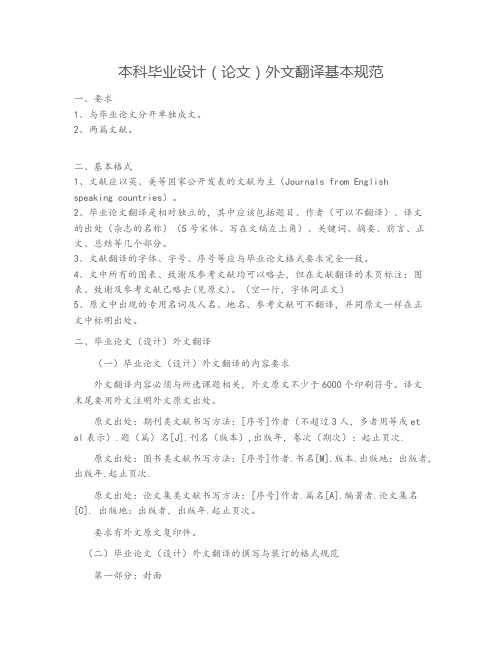
本科毕业设计(论文)外文翻译基本规范一、要求1、与毕业论文分开单独成文。
2、两篇文献。
二、基本格式1、文献应以英、美等国家公开发表的文献为主(Journals from English speaking countries)。
2、毕业论文翻译是相对独立的,其中应该包括题目、作者(可以不翻译)、译文的出处(杂志的名称)(5号宋体、写在文稿左上角)、关键词、摘要、前言、正文、总结等几个部分。
3、文献翻译的字体、字号、序号等应与毕业论文格式要求完全一致。
4、文中所有的图表、致谢及参考文献均可以略去,但在文献翻译的末页标注:图表、致谢及参考文献已略去(见原文)。
(空一行,字体同正文)5、原文中出现的专用名词及人名、地名、参考文献可不翻译,并同原文一样在正文中标明出处。
二、毕业论文(设计)外文翻译(一)毕业论文(设计)外文翻译的内容要求外文翻译内容必须与所选课题相关,外文原文不少于6000个印刷符号。
译文末尾要用外文注明外文原文出处。
原文出处:期刊类文献书写方法:[序号]作者(不超过3人,多者用等或et al表示).题(篇)名[J].刊名(版本),出版年,卷次(期次):起止页次.原文出处:图书类文献书写方法:[序号]作者.书名[M].版本.出版地:出版者,出版年.起止页次.原文出处:论文集类文献书写方法:[序号]作者.篇名[A].编著者.论文集名[C]. 出版地:出版者,出版年.起止页次。
要求有外文原文复印件。
(二)毕业论文(设计)外文翻译的撰写与装订的格式规范第一部分:封面1.封面格式:见“毕业论文(设计)外文翻译封面”。
普通A4纸打印即可。
第二部分:外文翻译主题1.标题一级标题,三号字,宋体,顶格,加粗二级标题,四号字,宋体,顶格,加粗三级标题,小四号字,宋体,顶格,加粗2.正文小四号字,宋体。
第三部分:版面要求论文开本大小:210mm×297mm(A4纸)版芯要求:左边距:25mm,右边距:25mm,上边距:30mm,下边距:25mm,页眉边距:23mm,页脚边距:18mm字符间距:标准行距:1.25倍页眉页角:页眉的奇数页书写—浙江师范大学学士学位论文外文翻译。
毕业设计外文文献格式

本科毕业论文外文文献及译文Current situation of energy consumption and measures taken for energy saving in the iron and steel industry in China文献来源:期刊发表日期:2009.5.17学院:资源与冶金学院专业:冶金工程班级:冶金121姓名:孔博文学号:1206300131指导教师:梁铎强翻译日期:2016.6.23外文文献:Current situation of energy consumption and measures taken for energy saving in the iron and steel industry in China abstractA survey of the key issues associated with the development in the Chinese iron and steel industry and current situations of energy consumption are described in this paper. The apparent production of crude steel in China expanded to 418.78 million tonnes in 2006, which was about 34% share of the world steel production. The iron and steel industry in China is still one of the major high energy consumption and high pollution industries, which accounts for the consumption of about 15.2% of the national total energy, and generation of 14% of the national total waste water and waste gas and 6% of the total solid waste materials. The average energy consumption per unit of steel is about 20% higher than that of other advanced countries due to its low energy utilization efficiency. However, the energy efficiency of the iron and steel industry in China has made significant improvement in the past few years and significant energy savings will be achieved in the future by optimizing end-use energy utilization. Finally, some measures for the industry in terms of the economic policy of China’s 11th five-year plan are also presented.1.IntroductionThe steel industry has for long played an important role in the development of China’s economy. Over the past decades, China’s steel industry has grown rapidly, overtaken Japan, and become the world’s largest steel producer in 1996. In 2006, China’s production of crude steel amounted to 418.78 million tonnes (Mt) [1] and, continued to remain first in rank. The share of output of crude steel of about 335.17 Mt of the key producers accounted for 80% of the aggregate national production and 83.61 Mt of local producers for 20% [2]. In this paper, these key producers are the main subjects of our study.Despite these achievements, China remains a steel producer whose energy efficiency is the lowest among the major steel-producing countries, although the overall technical level of its industry has been greatly improved in line with the developments in science and technology. One typical example is the rapid adop-tion of continuous casting technology. The share of continuous casting output has increased from about 30% of all steel produced in 1992 to 95.8% in 2004. In the meantime, many large firms replaced aging blast furnaces, open-hearth furnaces, and ingot casters with large-scale, modern blast furnaces, and casting and rolling facilities. Iron making may take place either through the blast furnace process or by direct reduction and the subsequent transformation of iron into steel may be carried out either in an oxygen-blown converter or in an electric arc furnace.With improvement of the overall technical level in the steel industry, the production of iron and steel has greatly expanded in the past decade, as shown in Fig. 1 [1–4]. The apparent production of crude steel in China grew from 95 million tonnes in 1995 to 418.78 million tonnes in 2006, which is about 4.5 times that in 1995 and more than three times that in 2000 [3]. As a result, China’s share of world steel production leaped from 13% in 1995 to 34% in 2006. This growth is expected to be sustained over the next few years due to the continued growth in domestic demand.As is well known, the iron and steel industry is the industry with the largest energy consumption in the world. Having become the world’s largest steel producer since 1996 China’s steel industry has grown rapidly following huge growth in domestic demand. This increase is consistent with the trend in the increase in its energy consumption.Iron and steel production consumes large quantities of energy, especially in developing countries and countries with economies in transition where outdated and inefficient technologies are often still used. Steel production in developing countries has grown at an average annual rate of 6.6% in recent years [5] and is expected to continue to grow at similar levels due to the current low per capita steel consumption levels in these countries. In industrialized countries, steel consumption averages over 425 kg/capita, whereas even key steel-producing developing countries have extremely low average per capita consumption levels of 80 kg/capita (in 1995).Fig. 1. Crude steel production of China and share of the world from 1995 to 2006.Most of China’s steel industry developed through a system of state-owned ‘enterprises’, in which an entire community was devoted to the production of steel. As a result, the data collected relating to the energy consumed to produce steel in China also contain energy used at the enterprise level for a variety of other functional departments, both directly and indirectly related to the production of steel. In addition, part of China’s steel is produced by small steel mills that do not report energy consumption data to government statistical sources. It is important to differentiate these data so that the consumption values of China’s energy can be fairly evaluated, especially when we compare the energy consumption and energy intensity of the Chinese steel industry to those of other countries or to particular ‘best practice’examples. We note that even with these adjustments, it is possible that the data still include inaccuracies due to the issues of statistical reports.The objective of this paper is to present a survey of some of the key issues associated withthe development in the Chinese steel industry, and describes the status of its energy consumption. The differences in steel consumption in major processes and China’s role in the scene of the international steel industry are analyzed, and the outlook and the measures to be instituted for China’s iron and steel industry are also presented in the paper. It is important for the world to better understand China’s energy consumption and the use of raw materials and for China to better understand the approaches that have been developed or are being developed in other countries for more efficient use of energy and raw materials. The authors hope this paper contributes to the improved under-standing of these aspects of the industry.2.Energy consumption structure of the iron and steel industry in ChinaIt is well known that electricity production in China mainly depends on coal, and coal is also the most important fuel used in China’s iron and steel industry. In 2004, the energy consumption mix of the Chinese steel industry consisted of 69.90% coal, 26.40% electricity, 3.2% fuel oil, and 0.5% natural gas, as shown in Fig. 2 [4]. Coal is not only the most widely used fuel but is also as necessary as raw material in the iron and steel industry as most of the rest is electricity. Such a fuel structure raises the energy consumption per unit of production and is unlikely to change greatly in the near future.Fig. 2. Energy consumption mix of the steel industry of China in 2004.3. Energy consumption situation in the steel industryThe key iron and steel producers in China play an important role in its manufacture of steel and in the consumption of energy. In 2003, China’s 10 largest steel firms produced more than a third of China’s steel output, with the top four firms producing more than 20% [6]. This implies that many advanced technologies have earlier existed in China’s steel industry, but the current industry’s concentration limits the application of these technologies lowering energy efficiency in general [7]. Therefore, the iron and steel industry remains one of the highest energy consumersand pollu-tion producers accounting for about 15.2% of the national total energy consumption, 14% of the national total waste water and waste gas, and 6% of the total solid waste materials generated.Fig. 3 shows the variations in energy consumption of the key enterprises in China from 1995 to 2006 [3,8–10]. The total energy consumption of the iron and steel industry rose rapidly along with rising steel production in the past decades. In the year 2004, the total steel production of China was 274.7 Mt, rising by 107.7% compared to 2000 and by 184.2% compared to 1995 [10]. The total energy consumption of the key enterprises in China soared from 96.30 Mtce in 2000 to 197.79 Mtce in 2006, which was over twice that for 2000. However, the rising trend in energy consumption weakened in 2006, when it was 8.8% lower than that of the year before.With the application of many new technologies and equipment, the index of energy consumption per tonne of steel decreased remarkably in the past decades. The overall energy consumption for China’s large and medium producers in 2005 was 741 kgce per tonne of steel, which was 20.3% lower than that in 2000 of 930 kgce per tonne. In 2006, the overall energy consumption per tonne of steel continued to decrease to 645 kgce per tonne of steel. The comparable energy consumption also took on a decreasing trend.Fig. 3. Variation of energy consumption of the key enterprises in China from 1995 to 2006.Fig. 4. Fresh water consumption per tonne of steel from 2000 to 2005.The variations in fresh water consumption per tonne of steel from 2000 to 2006 are shown in Fig. 4 [3,10]. The total quantity of fresh water used per tonne of steel in 2006 was 6.56 m3, which is 14.9% lower than that in 2005. Other data comparing energy saving, water saving, and environmental protection between 2000 and 2005 are presented in Table 1 [10]. It can be seen that the energy efficiency of China’s iron and steel industry has made significant improvement in the past few years.4.Energy consumption situation of several main processes in the steel industryFig. 5 shows the variations in energy consumption of several major processes in the steel industry from 1995 to 2005 [3,10]. The energy consumption of the blast furnace, electric furnace and steel rolling processes has decreased remarkably since 1995, and the corresponding values for the coking, sintering, and converter furnaces have also shown minor decreases. In contrast to the years before 2001, the current energy consumption of the blast furnace process presents an increasing trend that is attributed to cost increases since 2001 in raw materials for iron making, such as coke and coal.Fig. 5. Variation of energy consumption of several main processes in the steel industry in1995–2005.Among several major processes, the energy consumption of the iron making process is markedly higher than that of other processes. Taking the example of 2004 as shown in Fig. 6, the total energy consumption of the iron making system accounted for about 70% of the total process energy consumption, including 39% for the blast furnace, 11.9% for coking, 3.51% for balling and 5.55% for sin-tering. The remaining processes accounted for a small part of about 30%, which is comprised of 12.5% for power, 7.77% for rolling steel, 17.5% for the electric furnace, and 2.22% for the converter furnace. This means that the iron making system is a key part of any energy conservation effort in the steel industry.parisons of energy consumption of the steel industry in China with international levelsEnergy consumption per tonne of steel in China is higher than that of most advanced countries. One of the reasons for this is that the energy utilization efficiency in China is low. The average energy consumption per unit of steel is about 20% higher than that of other advanced countries. Compared with Japan, for example, energy consumption for China’s large and medium firms in 2004 was 705 kgce per tonne of steel, 7.5% higher than that in Japan, which was 656 kgce per tonne. However, the energy consumption level of the small production units in Chinawas as high as 1045 kgce per tonne of steel.Fig. 6. Energy consumption structure of several main processes in the steel industry in 2004.Z.C. Guo, Z.X. Fu / Energy 35 (2010) 4356–4360The general energy efficiency of China’s steel industry is still relatively low. One of the important reasons is the existence of these small units. Table 2 shows that there is a vast difference in energy consumption between the advanced and small plants [8]. Only a few large-scale steel-makers have attained or have even exceeded the international levels. Since the output of these advanced plants cannot achieve market dominance, the average energy consumption level of China’s iron and steel industry is still embarrassing.The second reason is the existence of small-scale and decen-tralized industry in China. There are 18 plants with production capacities exceeding 5 Mt of crude steel, which accounted for 46.36% of the total national crude steel production in 2005. In Japan, the crude steel production of four largest plants accounted for 73.22% of the total national crude steel production in 2004, three of which accounted for 61.09%. Except for a few of the large-scale steel plants, China’s steel industry lags behind in technology, equipment, energy saving, environmental protection, etc. The third reason is that the low recovery and recycling efficiency of the secondary energy resources results in higher energy consumption.6.Measures and policy recommendations for the iron and steel industries of China6.1. To expand coke dry quenching technologyTraditionally, the sensible heat of hot coke, pushed from the coking chamber at the temperature of 950–1050 C, is almost equal to 35%–40% of the total amount of heat consumed in the coking process. Adopting coke dry quenching technology can enable recovery of about 80% of the sensible heat from hot coke. Besides, during dry quenching 1 tonne of hot coke can generate 0.45–0.60 tonne of steam at a pressure of about 3.9 MPa. The coke dry quenching process belongs to a technology that is energy saving, environmentally protective, and pollution-free. By using coke dry quenching, it is estimated that the rotary drum strength (M40) of coke increases by 3%–8% and the coke strength after CO2 reaction by 3%–4%. In addition, the quantity of weak binding coal input can be increased by 10% saving about 0.38 tonne of water for every tonne of coke.At the end of 2005, the proportion of coke dry quenching technology usage in China’s iron and steel industry was less than 30%. At the end of 2007, with the spread of this technology rein-forced by an independent innovation in the past two years, the proportion of usage rose to 45%. Now 34 sets of the coke dry quenching unit are under construction and the output share of coke of about 101.58 Mt produced by the coke dry quenching technology accounts for one-third of the total national production.6.2. To expand top gas pressure recovery turbine (TRT) technologyPower can be generated with the energy of pressure from the top of a blast furnace using a turbine generator group. Theoretically,the power generated from TRT equipment is equal to the power energy consumed when the coal gas pressure at the top of the blast furnace is 80 kPa. Economic returns may be obtained when the pressure of the coal gas reaches 100 kPa and even higher economic returns can be achieved, especially, if the coal gas pressure is greater than 120 kPa. In steel production by the blast furnace route, increasing the pressure at the top of the blast furnace is advanta-geous as it leads to recovery of energy resources. The amount of power generated increases by 30% if dry dust is removed at the coal gas purification stage and theturbine capacity by about 3% if the temperature of coal gas is raised by 10 C. If TRT equipment is adopted, it is estimated that 30% of energy can be recovered from the air blast for the furnace and the energy consumption in the steel making processes reduced by l l kgce/t.At the end of 2007, the blast furnaces of capacity greater than 2000 m3 in China that were equipped with TRT technology numbered 49. In future, the use of TRT technology large-scale blast furnaces in China will be widespread and vigorous.6.3. To expand the technology of pulverized coal injection for the blast furnaceUse of pulverized coal injection for blast furnaces is an impor-tant innovation for optimizing steel making systems using the blast furnace route. In addition, it is a powerful incentive to prompt the iron–steel industry to progress in many aspects such as optimizing energy structure, energy saving, reducing consumption of mate-rials, cost reduction, etc. Replacing coke by coal can ease the problem of coking coal shortage caused by energy saving measures. Besides, it can reduce environmental pollution from the coking process while also producing considerable economic returns resulting from the price difference between coal and coke.In 2007, the average quantity of pulverized coal injection employed for the blast furnace route by China’s large and medium producers was 137 kg per tonne of iron, which in 2000 was 118 kg per tonne of iron. The average quantity of injection has exceeded 200 kg per tonne of iron in some large-scale blast furnaces of China. The 4350 m3 capacity blast furnace in Bao-steel is an example. It is estimated that in 2010 the average pulverized coal injection quantity realized in China’s blast furnaces iron will be 160 kg per tonne.6.4. To eliminate low-level equipment and introduce and develop new technologyOver the past few years, the government of China made a strong effort to eliminate low-level equipment. The energy consumption of China’s small iron and steel units was 1.5 times higher than that of the large and medium producers. When China implemented its 11th five-year plan’s policy of energy saving and reducing discharge of pollutants the steel industry was restructured, its equipment capacities enhanced, and pace of modernization accelerated all ofwhich produced an enormous effect.In 2007, the number of blast furnaces with a capacity of 2000 m3 in China was 63, 17 more than that in 2005, and production capacity increased by 35%. The number of converters with a capacity of 100 tonnes was 98 in 2007, eight more than that in 2005, and production capacity increased by 8%. In 2007, the overall energy consumption, the fresh water consumption, the total emission of SO2, the total soot emission, and the total mill dust emission per tonne of steel declined by about 8%, 24%, 4.5%, 3% and 4.5%, respectively, when compared with that in 2005.In addition, China’s iron and steel industries introduced and developed actively new technologies, such as COREX and C300 melted-deoxidize technology.6.5. To create the recycling economy chain within the iron–steel industryIt is believed that three recycling economy chains could be developed in the iron–steel production process aiming at zero emission. First is recycling flue gas, which means that not only coal or coke but also flue gas will be recycled from blast furnaces, converters, or coke ovens to realize zero flue gas emission. The second is recycling industrial waste water, which means that the consumption of fresh water will be minimized and industrial waste water will be recycled using some treating equipment. The third is recycling solid waste materials. It is a comprehensive reuse process for some raw materials such as iron ores left over from the production process.China’s traditional development pattern such as large invest-ment, regardless of serious pollution and lower value-added products resulted in China’s location at the low end of the value chain of the worldwide industrial structure. It is the most impor-tant reason for China’s high consumption of energy. Compared with developed countries, China’s use of poorer quality equipment and ineffective use of process energy led to lower energy utilization efficiency.7.ProspectsWith the improvement of the overall technical level in the steel industry, the production of iron and steel has greatly expanded in the past decade. However, the iron and steel industry is still one of the major high energy consumption and high polluting industries in China. Although the energy efficiency of the iron and steel industry in China has made significant improvement in the past few years, the average energy consumption per unit of steel is about 20% higher than that of other advanced countries owing to low energy utilization efficiency, the existence of somesmall-scale and decentralized industries and low recovery and recycling efficiency of the secondary energy resources. During 2006–2010, the period of China’s 11th five-year plan, based on existing policies, measures and standards, China will promulgate and implement some new policies with more ambitious objectives of sustainable develop-ment and restructuring in the steel industry. One objective of this plan is to build a society committed to energy conservation and a pollution-free environment and to develop the recycling economy chain in the iron and steel industry. Successful implementation of current sustainable development policies and measures will result in considerable energy saving.According to this plan, China’s energy consumption per GDP in ‘China’s 11th five-year plan’will decrease by 20%, the water consumption per unit of industrial added value will decrease by 30% and the total emission of main pollutants will decrease by 10%. Some major tasks will be undertaken for some high energy consumption industries such as the iron and steel industry, nonferrous metal industry, coal industry, power sector, and chemical industry. Therefore, a new industrial path leading to the use of technology-intensive products, optimal economic efficien-cies, lower resource consumption, and less environmental pollu-tion should be forged. There will be significant energy savings by optimizing end-use energy utilization.References[1]Xie QH. The operational aspects of iron and steel industry of China in 2006 and the prospects in 2007. China Steel 2007;2:6–11 (in Chinese).[2]/cyfz/hxfx/t20070126_113627.htm[3]/economic/txt/2007-02/22/content_7852832.htm[4]Wang K, Wang C, Lu XD, Chen JN. Scenario analysis on CO2 emissions reduction potential in China’s iron and steel industry. Energy Policy 2007;35: 2320–35.[5]The Editorial Board of China steel yearbook China steel yearbook. Beijing: China Statistical Publishing House; 2004.[6]Heane A, Heste S, Gurney A, Fairhead L, Beare S, Me´lanie S, et al. New energy technologies: measuring potential impacts in APEC. APEC Energy Working Group, Report no. APEC#205–RE–01.1. Published by ABARE as Research Report 05.1, Canberra. /apec/publications/free_downloads/2005.Medialib Download.v1.html?url=/et c/medialib/apec_media_library/ downloads/workinggroups/ewg/pubs/2005.Par.0001.File.v1.1. [7]Weng YQ. Current status and prospect of energy saving and environment protection of Chinese steel industry. China Metallurgy 2003;11:1–6 (in Chinese).[8]/Info_Show.aspx?Mess_Id¼1659[9]Wang WX. Iron and steel enterprises’process energy consumption and energy saving potential. Metallurgy Management 2005;6:32–4 (in Chinese).[10]Cai JJ, He JH, Lu ZW, Li GT, Wang WX, Kong LH. Analysis of energy saving and energy consumption in Chinese steel industry for last 20 years and next 5 years. Iron and Steel 2002;37:68–73 (in Chinese).中文译文:我国钢铁工业能源消耗现状及节能对策摘要本文介绍了我国钢铁工业发展中的关键问题和能源消耗现状。
毕业设计参考文献格式

毕业设计参考文献格式篇一:毕业论文参考文献规范格式一、参考文献的类型参考文献(即引文出处)的类型以单字母方式标识,具体如下:M——专著C——论文集 N——报纸文章J——期刊文章D——学位论文 R——报告对于不属于上述的文献类型,采用字母―Z‖标识。
对于英文参考文献,还应注意以下两点:①作者姓名采用―姓在前名在后‖原则,具体格式是:姓,名字的首字母. 如: Malcolm Richard Cowley 应为:Cowley, M.R.,如果有两位作者,第一位作者方式不变,&之后第二位作者名字的首字母放在前面,姓放在后面,如:Frank Norris 与Irving Gordon应为:Norris, F. &I.Gordon.;②书名、报刊名使用斜体字,如:Mastering English Literature,English Weekly。
二、参考文献的格式及举例1.期刊类【格式】[序号]作者.篇名[J].刊名,出版年份,卷号(期号):起止页码.【举例】[1] 王海粟.浅议会计信息披露模式[J].财政研究,20XX,21:56-58.[2] 夏鲁惠.高等学校毕业论文教学情况调研报告[J].高等理科教育,20XX:46-52.[3] Heider, E.R.& D.C.Oliver. The structure of color space in naming and memory of two languages [J]. Foreign Language Teaching and Research, 1999, : 62 –67.2.专著类【格式】[序号]作者.书名[M].出版地:出版社,出版年份:起止页码.【举例】[4] 葛家澍,林志军.现代西方财务会计理论[M].厦门:厦门大学出版社,20XX:42.[5] Gill, R. Mastering English Literature [M]. London: Macmillan, 1985: 42-45.3.报纸类【格式】[序号]作者.篇名[N].报纸名,出版日期(版次).【举例】[6] 李大伦.经济全球化的重要性[N]. 光明日报,1998-12-27.[7] French, W. Between Silences: A Voice from China[N]. Atlantic Weekly, 1987-8-15.4.论文集【格式】[序号]作者.篇名[C].出版地:出版者,出版年份:起始页码.【举例】[8] 伍蠡甫.西方文论选[C]. 上海:上海译文出版社,1979:12-17.[9] Spivak,G. ―Can the Subaltern Speak?‖[A]. InC.Nelson & L.Grossberg. Victory in Limbo: Imigism [C]. Urbana: University of Illinois Press, 1988, pp.271-313.[10] Almarza, G.G. Student foreign language teacher’s knowledge growth [A]. In D.Freeman and J.C.Richards . Teacher Learning in Language Teaching [C]. New York: Cambridge University Press. 1996. pp.50-78.5.学位论文【格式】[序号]作者.篇名[D].出版地:保存者,出版年份:起始页码.【举例】[11] 张筑生.微分半动力系统的不变集[D].北京:北京大学数学系数学研究所, 1983:1-7.6.研究报告【格式】[序号]作者.篇名[R].出版地:出版者,出版年份:起始页码.【举例】[12] 冯西桥.核反应堆压力管道与压力容器的LBB分析[R].北京:清华大学核能技术设计研究院, 1997:9-10.7.条例【格式】[序号]颁布单位.条例名称.发布日期【举例】[15] 中华人民共和国科学技术委员会.科学技术期刊管理办法[Z].1991—06—058.译著【格式】[序号]原著作者. 书名[M].译者,译.出版地:出版社,出版年份:起止页码.三、注释注释是对论文正文中某一特定内容的进一步解释或补充说明。
(英语)毕业设计(论文)内容及格式要求

广东岭南职业技术学院毕业设计(论文)内容及格式要求各二级学院:为了统一规范毕业论文的撰写、编辑、装订,便于论文处理、储存、检索、利用、交流、传播,特对毕业论文的格式提出如下统一要求:一、毕业论文内容要求毕业论文应用汉语撰写(外语相关专业除外),文科专业毕业论文字数一般3000字以上,理工科毕业设计字数5000字以上。
毕业论文(设计)内容应层次分明,数据可靠,文字简练,分析透彻,推理严谨,立论正确。
论文内容一般应由四个主要部分组成,依次为:(一)卷首部分(封面和封底、题目、中文摘要、关键词、目录),(二)主体部分(绪论(前言)、正文、结论或建议、尾注、参考文献表),(三)附录,(四)结尾。
各部分的具体要求如下:(一)卷首部分包括内容如下:1.封面和封底:由教务部统一制定(A3),学生自行打印装订,封面栏目要求打印。
2.题目:应在25字以内,能简明、具体、确切地表达毕业论文(设计)的特定内容。
3.中文摘要:在300字以内。
摘要是对毕业论文内容不加注释和评论的简述。
它应使人不阅读毕业论文全文即可获得全文的主要信息和结论,是一篇完整的短文,可以独立使用。
论文摘要应说明研究工作的目的、方法、成果和结论。
要突出本文的新见解和研究工作的创新点。
4.关键词:论文关键词一般3至8个,应采用能覆盖论文主要内容的通用标准词条(参照相应的技术术语标准),按词条的外延层次从大到上排列,并以显著的字符另起一行,排在摘要左下方。
5.目录:由论文的章节以及附录、参考文献等序号、题名和页码组成。
6. 段落编码 .编码按三级编写,理工科(1……、1.1……、1.1.1……),文科类(一......、(一)......、1.....、(1).......)要求层次清晰。
(二)主体部分主体部分包括:绪论(概述)、正文、结论或建议、尾注、参考文献表。
1.绪论(概述):是该研究内容所涉及的研究领域研究进展的综述。
主要说明研究工作的目的、涉及范围、相关领域的前人研究成果、研究设想、研究方法和实际的概述、理论意义和实际价值。
毕业设计论文外文文献翻译
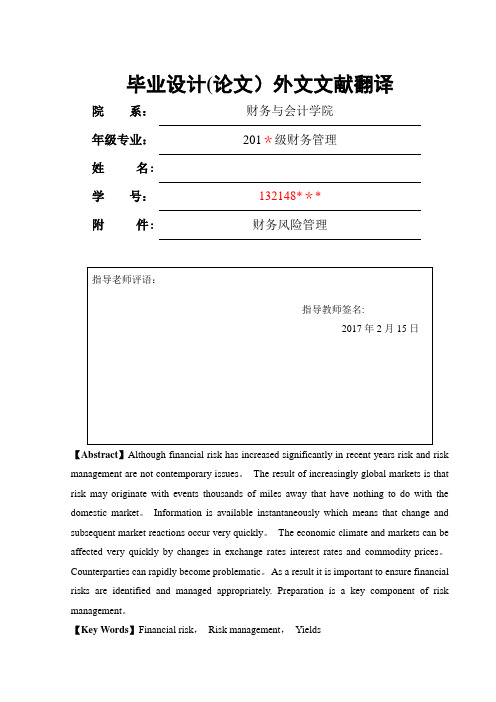
毕业设计(论文)外文文献翻译院系:财务与会计学院年级专业:201*级财务管理姓名:学号:132148***附件: 财务风险管理【Abstract】Although financial risk has increased significantly in recent years risk and risk management are not contemporary issues。
The result of increasingly global markets is that risk may originate with events thousands of miles away that have nothing to do with the domestic market。
Information is available instantaneously which means that change and subsequent market reactions occur very quickly。
The economic climate and markets can be affected very quickly by changes in exchange rates interest rates and commodity prices。
Counterparties can rapidly become problematic。
As a result it is important to ensure financial risks are identified and managed appropriately. Preparation is a key component of risk management。
【Key Words】Financial risk,Risk management,YieldsI. Financial risks arising1.1What Is Risk1.1.1The concept of riskRisk provides the basis for opportunity. The terms risk and exposure have subtle differences in their meaning. Risk refers to the probability of loss while exposure is the possibility of loss although they are often used interchangeably。
- 1、下载文档前请自行甄别文档内容的完整性,平台不提供额外的编辑、内容补充、找答案等附加服务。
- 2、"仅部分预览"的文档,不可在线预览部分如存在完整性等问题,可反馈申请退款(可完整预览的文档不适用该条件!)。
- 3、如文档侵犯您的权益,请联系客服反馈,我们会尽快为您处理(人工客服工作时间:9:00-18:30)。
附件3:
(本科毕业论文)文献、资料题目:
院(部)
专
班
姓名:张三
学号:2001888888
指导教师:张九光
翻译日期:2005.6.30
山东建筑大学毕业设计(或毕业论文,二选一)外文文献及译文
,the National Institute of Standards and Technology (NIST) has been working to develop a new encryption standard to keep government information secure .The organization is in the final stages of an open process of selecting one or more algorithms ,or data-scrambling formulas ,for the new Advanced Encryption Standard (AES) and plans to make adecision by late summer or early fall .The standard is slated to go into effect next year .
AES is intended to be a stronger ,more efficient successor to Triple Data Encryption Standard (3DES),which replaced the aging DES ,which was cracked in less than three days in July 1998.
“Until we have the AES ,3DES will still offer protection for years to come .So there is no need to immediately switch over ,”says Edward Roback , acting chief of the computer security division at NIST and chairman of the AES selection committee .“What AES will offer is a more efficient algorithm .It will be a federal standard ,but it will be widely implemented in the IT community .”
According to Roback ,efficiency of the proposed algorithms is measured by how fast they can encrypt and decrypt information ,how fast they can present an encryption key and how much information they can encrypt .
The AES review committee is also looking at how much space the algorithm takes up on a chip and how much memory it requires .Roback says the selection of a more efficient AES will also result in cost savings and better use of resources .
“DES was designed for hardware implementations ,and we are now living in a world of much more efficient software ,and we have learned an awful lot about the design of algorithms ,”says Roback .“When you start multiplying this with the billions of impl ementations done daily ,the saving on overhead on the networks will be enormous .”
……
山东建筑大学毕业设计(或毕业论文,二选一)外文文献及译文
- 2 -
以确保政府的信息安全。
该组织目前正处于为新的先进加密标准(
AES )选择一个或几个算法或数据打乱公式的开放过程的最后阶段,并计划在夏末或秋初作出决定。
此标准内定明年实施。
AES 预定为比三层数据加密标准(3DES)更强、更高效的后续标准,3DES 替代了老化的DES 加密标准,DES 在1998年7月在不到三天的时间内就被破译了。
NIST 计算机安全部的代理主管兼AES 选择委员会主席Edward Roback 说:“在我们拥有AES 之前,3DES 还将在今后几年提供保护。
所以没有必要马上转换。
AES 所提供的是一种更有效的算法。
它将是一项联邦标准,但它将在IT 界广泛实施。
”
据Roback 称,提议中的算法的效率是通过对信息加密和解密有多快、给出加密密钥有多快以及能对多少信息加密等几个方面进行测量的。
AES 评价委员会也要看算法占据芯片上多少空间和需要多少内存。
Roback 说,选择一个更高效的AES 也会带来成本的节省和资源的更好利用。
Roback 说:“DES 是为硬件实现而设计的,而我们现在处于软件更高效的世界,我们对算法的设计有极多的了解。
当我们开始大规模使用此算法,每天实现几十亿次的加密时,(算法带来的)网络开销的节省将是巨大的。
”
……。