进、排气门座粉末冶金生产过程中混料工艺的研究
粉末混合工艺
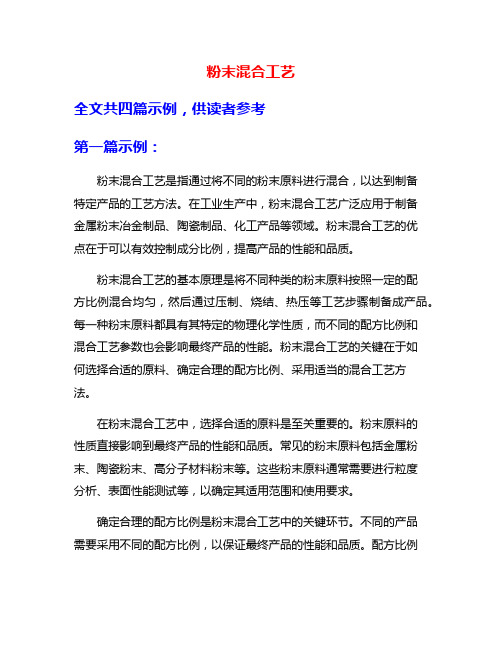
粉末混合工艺全文共四篇示例,供读者参考第一篇示例:粉末混合工艺是指通过将不同的粉末原料进行混合,以达到制备特定产品的工艺方法。
在工业生产中,粉末混合工艺广泛应用于制备金属粉末冶金制品、陶瓷制品、化工产品等领域。
粉末混合工艺的优点在于可以有效控制成分比例,提高产品的性能和品质。
粉末混合工艺的基本原理是将不同种类的粉末原料按照一定的配方比例混合均匀,然后通过压制、烧结、热压等工艺步骤制备成产品。
每一种粉末原料都具有其特定的物理化学性质,而不同的配方比例和混合工艺参数也会影响最终产品的性能。
粉末混合工艺的关键在于如何选择合适的原料、确定合理的配方比例、采用适当的混合工艺方法。
在粉末混合工艺中,选择合适的原料是至关重要的。
粉末原料的性质直接影响到最终产品的性能和品质。
常见的粉末原料包括金属粉末、陶瓷粉末、高分子材料粉末等。
这些粉末原料通常需要进行粒度分析、表面性能测试等,以确定其适用范围和使用要求。
确定合理的配方比例是粉末混合工艺中的关键环节。
不同的产品需要采用不同的配方比例,以保证最终产品的性能和品质。
配方比例经常通过试验和实践来确定,通常需要考虑到原料的化学成分、物理性质、烧结性能等因素。
混合工艺方法的选择也对最终产品的性能有重要影响。
常见的混合工艺方法包括机械混合、溶液混合、气液混合等。
机械混合是最常用的混合工艺方法,通过搅拌、研磨等机械力作用将粉末原料混合均匀。
溶液混合则是将粉末原料溶解在溶剂中,再进行混合。
气液混合则是将气体和液体一起混合,常用于颗粒状粉末原料的混合。
粉末混合工艺是一种重要的工艺方法,广泛应用于工业生产中。
通过选择合适的原料、确定合理的配方比例、采用适当的混合工艺方法,可以制备出高性能、高品质的产品。
粉末混合工艺的发展也为工业生产提供了更多的可能性,促进了产品的创新和升级。
希望随着科技的不断进步,粉末混合工艺能够得到更大的发展和应用。
第二篇示例:粉末混合工艺是工业生产中常用的一种工艺方法,它主要用于将不同性质的粉末原料混合在一起,以制备出符合特定要求的混合物。
粉末冶金的生产过程
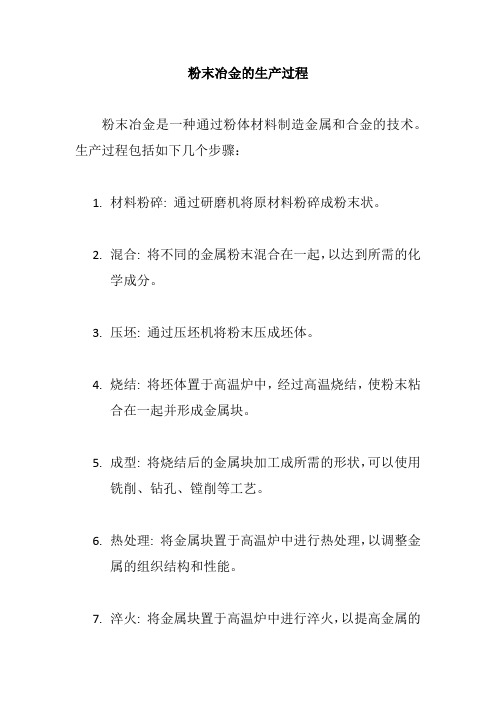
粉末冶金的生产过程
粉末冶金是一种通过粉体材料制造金属和合金的技术。
生产过程包括如下几个步骤:
1.材料粉碎: 通过研磨机将原材料粉碎成粉末状。
2.混合: 将不同的金属粉末混合在一起,以达到所需的化
学成分。
3.压坯: 通过压坯机将粉末压成坯体。
4.烧结: 将坯体置于高温炉中,经过高温烧结,使粉末粘
合在一起并形成金属块。
5.成型: 将烧结后的金属块加工成所需的形状,可以使用
铣削、钻孔、镗削等工艺。
6.热处理: 将金属块置于高温炉中进行热处理,以调整金
属的组织结构和性能。
7.淬火: 将金属块置于高温炉中进行淬火,以提高金属的
硬度和耐磨性。
8.深火: 将金属块置于高温炉中进行深火,以提高金属的
韧性。
9.清理: 将金属块清理干净,以确保其表面干净无杂质。
10.检测: 对金属块进行检测,以确保其质量符合标准。
粉末冶金TiAl基合金排气门的研制

件进 一 步轻 量 化和 优 化 。同时 , 术 状况 的耐久 性 技
2 元素 粉 末 冶 金 法 的 基 本 过 程 和 特 点
元 素 粉 末 冶金 法 制 备 TA 合金 排 气 门大致 经 i1
提高; 固定 工况 降低 油耗 1 综 合节 能大 于 5%; %, 明 显 降低 噪声 和排放 污染 。。近年 来 , 发低 成本 高 开 质 量生 产 TA 基台 金排 气门 的技术 成 为研 究热点 iI 由 于 A 基 合金 冷 、热加 工 与成 型性 能较差 , n l
产, 可以降 低成 本 , 足大批 量 生产 的要 求 。但 由于 满 从单 元 素粉 末 到最 后 的成 品 , 容易 产 生 杂质 元 素污 染和 氧化 夹 杂现 象 , 对材 料 的 延伸 性产 生不 利 的影
响 , 以必须 尽量 避免 夹杂和 氧化 问题 。 所
明, 汽车发 动机 装配 TA 基台 金排 气门 可使 弹簧力 il 和惯 性力 明显 降低 ; 臂力 降低 2 摇 5%, 门杆力 降 气 低4 5%; 凸轮 轴 驱动 扭 矩至 少 降 低 3 %; 以对 摇 0 可 臂 和 凸轮轴 设 计轻 量 化 , 使整 个气 门传 动机 构 的零
好, 而且 , 质量 只有 钢质 气 门 的一 半 。试验 结果 表 其
相 应 的材 料 。这 种方 法 的主 要优 点 是成 本低 , 于 易
进、排气门座粉末冶金生产过程中混料工艺的研究
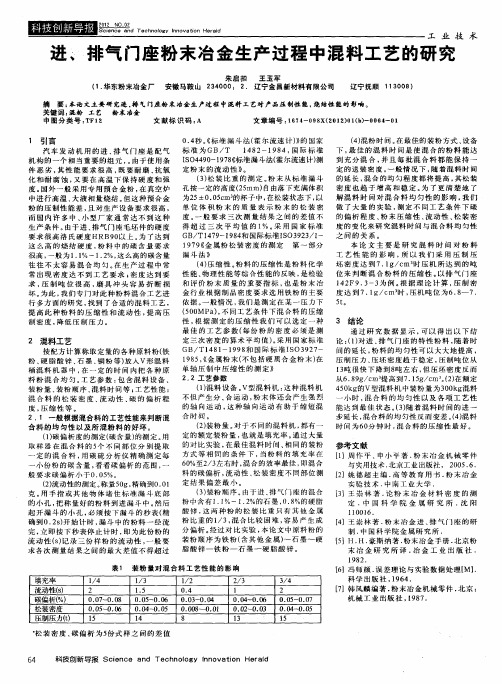
0 4 。 标 准 漏 斗 法 ( 尔流 速 计 ) 国家 .秒 《 霍 的 标 准 为 GB/ 1 8 —1 8 国 际 标 准 T 2 4, 4 9 I 0 4 0 9 8 标 准 漏 斗法 ( S 4 9 -l 7 Ⅸ 霍尔 流速 计) 测 定粉末的流动性 》 ( ) 装 比 重 的 测 定 。 末 从 标 准 漏 斗 3松 粉 孔按 一 定 的 高度 ( 5 2 mm) 由落 下充 满 体积 自 为2 土0 0 c 的 杯 子 中, 松装 状态 下 , 5 . 5 m。 在 以 单 位 体 积 粉 末 的 质 量 表 示 粉 末 的 松 装 密 度 。 般 要 求 三 次 测 量 结 果 之 间 的 差 值 不 一 得 超 过 三 次 平 均 值 的 1 。 用 国 家 标 准 % 采 G / 4 9 9 4 国 际标 准 I O3 2 / 一 B T1 7 -l 8 和 s 93 l 1 7 金 属粉 松 装 密 度 的 测 定 第一 部分 9Ⅸ 9 漏斗法》 ( ) 缩 性 。 料 的 压 缩 性 是 粉 料 化 学 4压 粉 性 能 、 理 性 能 等 综 合 性 能 的 反 映 , 检验 物 是 和 评 价 粉 末 质 量 的 重 要 指 标 , 是 粉 末 冶 也 金 行 业根 据 制 品 密 度 要 求选 用 铁 粉 的 主要 依据 。 般 情 况 , 们 是 测 定 在 某 一 压 力 下 一 我 (0 MP )不 同工 艺 条 件下 混 合料 的 压缩 50 , 性 , 据 测 定 的 压 缩 性 我 们 可 以 选 定 一 种 根 最 佳 的 工 艺 参 数 ( 份 粉 的 密 度 必 须 是 测 每 定 三 次 密 度 的 算 术 平 均 值 ) 采 用 国 家标 准 。 GB/T1 1 9 8 国 际 标 准 I 48 —1 9 和 S03 7 92 — 1 8 ,金 属 粉 末 ( 包 括 硬 质 合 金 粉 末 ) 9 5《 不 在 单 轴 压制 中 压 缩 性 的 测 定 2 2工 艺参 数 . () 料 设 备 。 1混 V型 混 料 机 : 种 混 料 机 这 不但 产 生 分 、 运 动 , 末 体 还 会 产 生 强 烈 合 粉 的轴 向 运 动 , 种 轴 向运 动 有 助 于 缩 短 混 这 合时 间。 () 粉 量 。 2装 对于 不 同的 混 料 机 , 有一 都 定的 额 定 装 粉 量 , 就 是 填 充 率 。 也 通过 大量 的对 比实 验 , 最 佳 混 料 时 间 、 同 的 装粉 在 相 方式 等 相 同 的 条 件 下 , 粉 料 的 填 充 率 在 当 6 %至 2 3 右 时 , 合 的效 率 最佳 , 0 /左 混 即混 合 料 的 碳 偏 析 , 动 性 、 装 密 度 不 同 部 位 测 流 松 定结 果 偏 差 最 小 。 ( ) 粉 顺 序 由 于进 、 气 门 座 的 混合 3装 排 粉 中 含有 1 1 . %~1 2 . %的石 墨 , . %的硬 脂 08 酸 锌 , 西 种 粉 的 松 装 比 重 只 有 其 他 金属 这 粉 比重的1 /3, 合 比较 困 难 , 易 产 生 成 混 容 分 偏 析 。 过 对 比 实 验 , 论 文 中 原料 粉 的 经 本 装粉顺序 为铁粉( 含其 他 金 属 ) 石 墨~ 硬 一 脂 酸 锌一 铁 粉 一 石 墨一 硬 脂 酸 锌 。
粉末冶金工艺简介及问题点展示课件
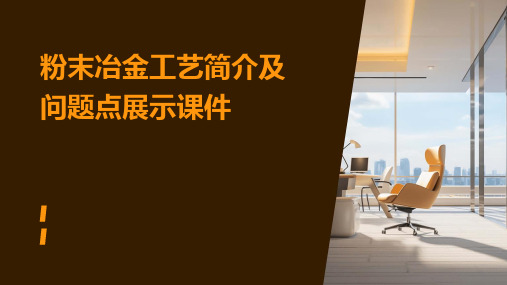
可制造复杂结构零件
粉末冶金工艺能够制造具有复杂内部 结构和精细特征的零件,满足高精度 和高性能的需求。
该工艺通过压制和烧结等步骤,能够 实现零件的复杂形状和精细特征的成 型,避免了传统加工方法的限制。
材料的组合与优化
粉末冶金工艺能够实现多种材料 的组合和优化,以获得最佳的性
能和功能。
通过将不同的金属粉末、非金属 粉末和其他添加剂混合,可以制 造出具有优异性能的复合材料和
压制过程中密度分布不均
密度不均的原因
在压制过程中,由于粉末的流动性、 模具的设计和压制工艺等因素,可能 会导致密度分布不均。
对产品质量的影响
密度分布不均会导致烧结后产品的性 能不均,如硬度和强度等。这可能会 影响产品的使用寿命和可靠性。
烧结过程中收缩率不一致
收缩率不一致的原因
在烧结过程中,由于温度场的不均匀、冷却速度不一致等因素,可能会导致收 缩率不一致。
通过优化原材料和工艺参数,产品性能和尺 寸精度得到显著提升。
能耗与污染明显降低
工艺流程的优化和先进设备的采用使得能源 消耗和环境污染明显降低。
生产效率大幅提高
自动化设备的引入使得生产效率大幅提升, 减少了人工成本。
成本有效控制
通过优化原材料、能源和人力成本,产品成 本得到有效控制。
THANKS FOR WATCHING
改进前的问题分析
01
02
03
04
产品质量不稳定
由于原材料和工艺参数的波动 ,导致产品性能和尺寸精度不
稳定。
生产效率低下
传统工艺流程长,且依赖大量 手工操作,导致生产效率低下
。
高能耗与高污染
由于设备陈旧和工艺落后,导 致能源消耗大且环境污染严重
气门配研
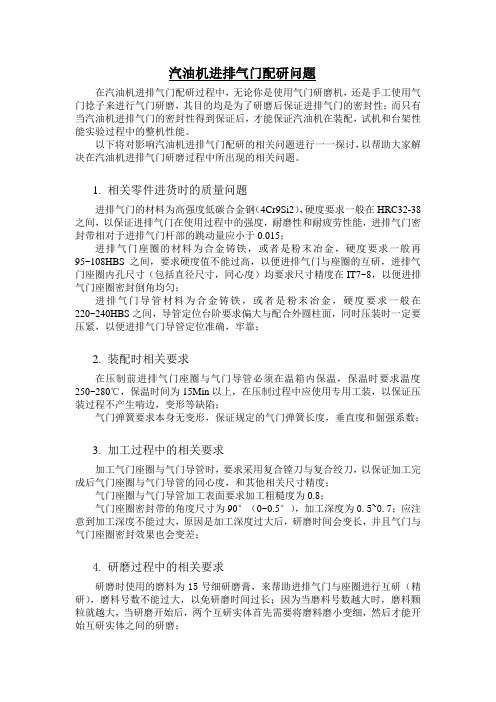
汽油机进排气门配研问题在汽油机进排气门配研过程中,无论你是使用气门研磨机,还是手工使用气门捻子来进行气门研磨,其目的均是为了研磨后保证进排气门的密封性;而只有当汽油机进排气门的密封性得到保证后,才能保证汽油机在装配,试机和台架性能实验过程中的整机性能。
以下将对影响汽油机进排气门配研的相关问题进行一一探讨,以帮助大家解决在汽油机进排气门研磨过程中所出现的相关问题。
1.相关零件进货时的质量问题进排气门的材料为高强度低碳合金钢(4Cr9Si2),硬度要求一般在HRC32-38之间,以保证进排气门在使用过程中的强度,耐磨性和耐疲劳性能,进排气门密封带相对于进排气门杆部的跳动量应小于0.015;进排气门座圈的材料为合金铸铁,或者是粉末冶金,硬度要求一般再95~108HBS之间,要求硬度值不能过高,以便进排气门与座圈的互研,进排气门座圈内孔尺寸(包括直径尺寸,同心度)均要求尺寸精度在IT7~8,以便进排气门座圈密封倒角均匀;进排气门导管材料为合金铸铁,或者是粉末冶金,硬度要求一般在220~240HBS之间,导管定位台阶要求偏大与配合外圆柱面,同时压装时一定要压紧,以便进排气门导管定位准确,牢靠;2.装配时相关要求在压制前进排气门座圈与气门导管必须在温箱内保温,保温时要求温度250~280℃,保温时间为15Min以上,在压制过程中应使用专用工装,以保证压装过程不产生啃边,变形等缺陷;气门弹簧要求本身无变形,保证规定的气门弹簧长度,垂直度和倔强系数;3.加工过程中的相关要求加工气门座圈与气门导管时,要求采用复合镗刀与复合绞刀,以保证加工完成后气门座圈与气门导管的同心度,和其他相关尺寸精度;气门座圈与气门导管加工表面要求加工粗糙度为0.8;气门座圈密封带的角度尺寸为90°(0~0.5°),加工深度为0.5~0.7;应注意到加工深度不能过大,原因是加工深度过大后,研磨时间会变长,并且气门与气门座圈密封效果也会变差;4.研磨过程中的相关要求研磨时使用的磨料为15号细研磨膏,来帮助进排气门与座圈进行互研(精研),磨料号数不能过大,以免研磨时间过长;因为当磨料号数越大时,磨料颗粒就越大,当研磨开始后,两个互研实体首先需要将磨料磨小变细,然后才能开始互研实体之间的研磨;研磨时应使用专用气门捻子来研磨气门;应保证气门捻子与气门头部之间的吸力,并且特别注意不要将研磨砂掉到气门头部,防止气门捻子过早报废;应注意到气门捻子在带动气门进行研磨时,它的研磨动作可以分为两种动作,一种是气门冲击气门座圈的动作,该动作有助于将磨料磨细,另一种动作是气门相对于气门座圈的旋转运动,该运动将使气门与气门座圈进行充分研磨;研磨过程中,气门捻子对气门的压力不宜过大,以免在研磨未完成前将磨料提前从气门座圈研磨带上挤出,造成气门与座圈研磨不充分;气门研磨的时间一般为15~20Min,不过一般应根据气门与气门座圈在研磨过程中的实际情况来决定;气门研磨过程分析:清洁进排气门,气门座圈和气门导管后,将研磨膏均匀的抹在气门密封带表面,要求涂抹时均匀,不宜过多,以防止研磨膏流入气门导管;研磨前,将气门捻子与气门调到合适的研磨力度和位置,以帮助研磨的顺利进行;研磨过程中,磨料被逐渐的压碎,形成一层细泥状,在气门与气门座圈中上下移动,当听到气门与气门座圈之间清脆的撞击声时,这时可以看到气门座圈上有一条很亮的环形亮带,等到该亮带在气门座圈上形成一条完整的,并且约有0.2~0.4mm之间宽时研磨完成。
新型粉末冶金气门座致密化过程论文
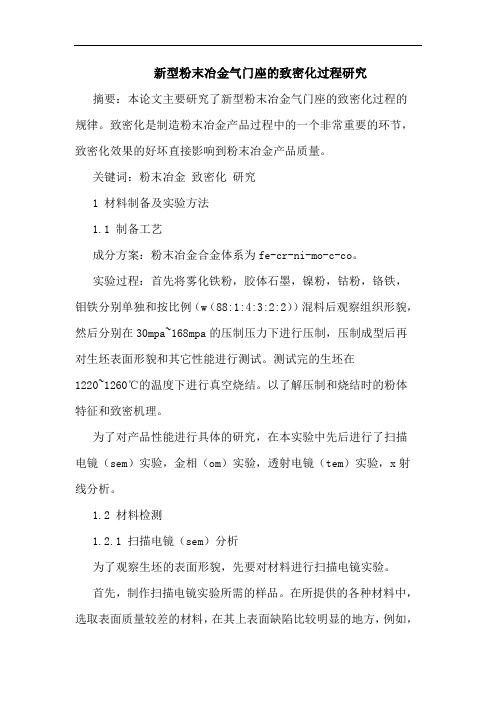
新型粉末冶金气门座的致密化过程研究摘要:本论文主要研究了新型粉末冶金气门座的致密化过程的规律。
致密化是制造粉末冶金产品过程中的一个非常重要的环节,致密化效果的好坏直接影响到粉末冶金产品质量。
关键词:粉末冶金致密化研究1 材料制备及实验方法1.1 制备工艺成分方案:粉末冶金合金体系为fe-cr-ni-mo-c-co。
实验过程:首先将雾化铁粉,胶体石墨,镍粉,钴粉,铬铁,钼铁分别单独和按比例(w(88:1:4:3:2:2))混料后观察组织形貌,然后分别在30mpa~168mpa的压制压力下进行压制,压制成型后再对生坯表面形貌和其它性能进行测试。
测试完的生坯在1220~1260℃的温度下进行真空烧结。
以了解压制和烧结时的粉体特征和致密机理。
为了对产品性能进行具体的研究,在本实验中先后进行了扫描电镜(sem)实验,金相(om)实验,透射电镜(tem)实验,x射线分析。
1.2 材料检测1.2.1 扫描电镜(sem)分析为了观察生坯的表面形貌,先要对材料进行扫描电镜实验。
首先,制作扫描电镜实验所需的样品。
在所提供的各种材料中,选取表面质量较差的材料,在其上表面缺陷比较明显的地方,例如,边部裂纹所在的地方,横纹明显的地方,或夹杂聚集的地方等,剪切下长和宽大约为1cm的样品,并且在表面缺陷不明显的地方,利用同样的方法采集实验样品,以作为比较之用。
制样结束后,将样品放入kyky-2800型扫描电子显微镜下观察。
为了了解形成表面缺陷的原因,在做完金相实验之后,用金相实验样品再做一次扫描电镜,以了解样品内部成分,找到产生缺陷的原因。
通过这两次扫描电镜实验,不仅了解了样品的宏观形貌特征,而且也知道了缺陷附近的组成成分,这为分析表面缺陷成因奠定了坚实的基础,具体的分析在后面的结果分析中加以讨论。
在kyky-2800扫描电镜上进行显微组织观察和能谱分析,电压15v,观察倍数4个:500,1500,3000,5000。
1.2.2 金相(om)实验在做金相实验时,首先是金相试样的制备。
粉末冶金配方及工艺技术
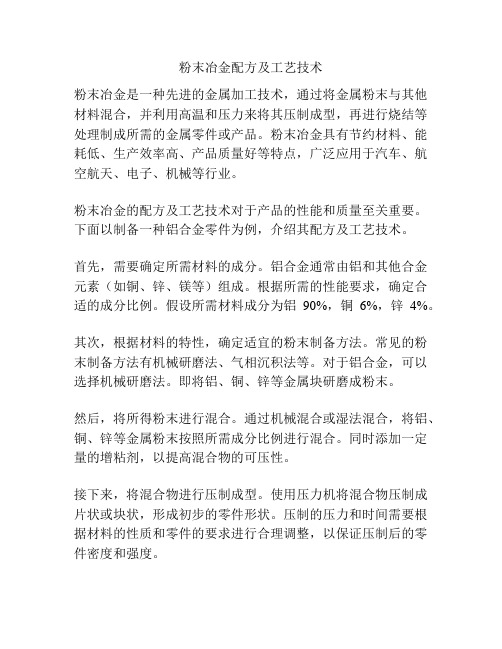
粉末冶金配方及工艺技术粉末冶金是一种先进的金属加工技术,通过将金属粉末与其他材料混合,并利用高温和压力来将其压制成型,再进行烧结等处理制成所需的金属零件或产品。
粉末冶金具有节约材料、能耗低、生产效率高、产品质量好等特点,广泛应用于汽车、航空航天、电子、机械等行业。
粉末冶金的配方及工艺技术对于产品的性能和质量至关重要。
下面以制备一种铝合金零件为例,介绍其配方及工艺技术。
首先,需要确定所需材料的成分。
铝合金通常由铝和其他合金元素(如铜、锌、镁等)组成。
根据所需的性能要求,确定合适的成分比例。
假设所需材料成分为铝90%,铜6%,锌4%。
其次,根据材料的特性,确定适宜的粉末制备方法。
常见的粉末制备方法有机械研磨法、气相沉积法等。
对于铝合金,可以选择机械研磨法。
即将铝、铜、锌等金属块研磨成粉末。
然后,将所得粉末进行混合。
通过机械混合或湿法混合,将铝、铜、锌等金属粉末按照所需成分比例进行混合。
同时添加一定量的增粘剂,以提高混合物的可压性。
接下来,将混合物进行压制成型。
使用压力机将混合物压制成片状或块状,形成初步的零件形状。
压制的压力和时间需要根据材料的性质和零件的要求进行合理调整,以保证压制后的零件密度和强度。
最后,对压制成型的零件进行烧结处理。
将零件置于特定的烧结炉中,在一定时间内进行高温加热处理。
在烧结过程中,金属粉末之间发生扩散,形成固相焊接,使零件的密度和强度得到提高。
在工艺过程中,还需要注意一些关键的技术要点。
首先,粉末的制备质量直接影响了最终零件的性能。
为了提高粉末的均匀性和细度,可以采用球磨法进行研磨,同时控制研磨时间和研磨介质的选择。
其次,压制过程中要注意控制压力和时间,避免压制过度或不足,以保证零件的密度和形状。
最后,在烧结过程中,温度、时间和气氛的控制都非常重要,以确保零件达到预期的物理和化学性能。
综上所述,粉末冶金配方及工艺技术对于产品的性能和质量具有重要的影响。
通过合理确定材料成分、选择适宜的粉末制备方法和控制关键工艺参数,可以生产出具有优异性能的粉末冶金产品。
- 1、下载文档前请自行甄别文档内容的完整性,平台不提供额外的编辑、内容补充、找答案等附加服务。
- 2、"仅部分预览"的文档,不可在线预览部分如存在完整性等问题,可反馈申请退款(可完整预览的文档不适用该条件!)。
- 3、如文档侵犯您的权益,请联系客服反馈,我们会尽快为您处理(人工客服工作时间:9:00-18:30)。
进、排气门座粉末冶金生产过程中混料工艺的研究摘要:本论文主要研究进、排气门座粉末冶金生产过程中混料工艺对产品压制性能,烧结性能的影响。
关键词:混粉工艺粉末冶金
1 引言
汽车发动机用的进、排气门座是配气机构的一个相当重要的组元,。
由于使用条件恶劣,其性能要求很高,既要耐磨、抗氧化和耐腐蚀,又要在高温下保持硬度和强度。
国外一般采用专用预合金粉,在真空炉中进行高温、大液相量烧结。
但这种预合金粉的压制性能差,且对生产设备要求很高,而国内许多中、小型厂家通常达不到这种生产条件。
由于进、排气门座毛坯件的硬度要求很高洛氏硬度HRB90以上。
为了达到这么高的烧结硬度,粉料中的碳含量要求很高,一般为1.1%~1.2%,这么高的碳含量往往不太容易混合均匀。
在生产过程中常常出现密度达不到工艺要求;密度达到要求,压制吨位很高,磨具冲头容易折断损坏。
为此,我们专门对此种粉料混合工艺进行多方面的研究,找到了合适的混料工艺,提高此种粉料的压缩性和流动性,提高压制密度,降低压制压力。
2 混料工艺
按配方计算称取定量的各种原料粉(铁粉、硬脂酸锌、石墨、铜
粉等)放入V形混料桶混料机器中,在一定的时间内把各种原料粉混合均匀。
工艺参数:包含混料设备、装粉量、装粉顺序、混料时间等;工艺性能:混合料的松装密度、流动性、碳的偏析程度,压缩性等。
2.1 一般根据混合料的工艺性能来判断混合料的均匀性以及所混粉料的好坏。
(1)碳偏析度的测定(碳含量)的测定。
用取样器在混合料的5个不同部位分别提取一定的混合料,用碳硫分析仪精确测定每一小份粉的碳含量,看看碳偏析的范围,一般要求碳偏析小于0.05%。
(2)流动性的测定。
称量50g,精确到0.01克。
用手指或其他物体堵住标准漏斗底部的小孔,把称量好的粉料到进漏斗中。
然后起开漏斗的小孔,必须按下漏斗的秒表(精确到0.2s)开始计时,漏斗中的粉料一经流完,立即按下秒表停止计时,即为此份粉的流动性(s)记录三份样粉的流动性,一般要求各次测量结果之间的最大差值不得超过0.4秒。
《标准漏斗法(霍尔流速计)》的国家标准为GB/T 1482-1984,国际标准ISO4490-1978《标准漏斗法(霍尔流速计)测定粉末的流动性》。
(3)松装比重的测定。
粉末从标准漏斗孔按一定的高度(25mm)自由落下充满体积为25±0.05cm3的杯子中,在松装状态下,以单位体积粉末的质量表示粉末的松装密度。
一般要求三次测量结果之间的差值不得超过三次平均值的1%。
采用国家标准GB/T1479-1984和国际标准ISO3923/1-1979《金属粉松装密度的测定第一部分漏斗法》
(4)压缩性。
粉料的压缩性是粉料化学性能、物理性能等综合性能的反映,是检验和评价粉末质量的重要指标,也是粉末冶金行业根据制品密度要求选用铁粉的主要依据。
一般情况,我们是测定在某一压力下(500MPa),不同工艺条件下混合料的压缩性,根据测定的压缩性我们可以选定一种最佳的工艺参数(每份粉的密度必须是测定三次密度的算术平均值)。
采用国家标准GB/T1481-1998和国际标准ISO3927-1985,《金属粉末(不包括硬质合金粉末)在单轴压制中压缩性的测定》
2.2 工艺参数
(1)混料设备。
V型混料机:这种混料机不但产生分、合运动,粉末体还会产生强烈的轴向运动,这种轴向运动有助于缩短混合时间。
(2)装粉量。
对于不同的混料机,都有一定的额定装粉量,也就是填充率。
通过大量的对比实验,在最佳混料时间、相同的装粉方式等相同的条件下,当粉料的填充率在60%至2/3左右时,混合的效率最佳,即混合料的碳偏析,流动性、松装密度不同部位测定结果偏差最小。
(3)装粉顺序。
由于进、排气门座的混合粉中含有1.1%~1.2%的石墨,0.8%的硬脂酸锌,这两种粉的松装比重只有其他金属粉比重的1/3,混合比较困难,容易产生成分偏析。
经过对比实验,本论文中原料粉的装粉顺序为铁粉(含其他金属)—石墨—硬脂酸锌—铁粉—石墨—硬脂酸锌。
(4)混粉时间。
在最佳的装粉方式、设备下,最佳的混料时间是使混合的粉料能达到充分混合,并且每批混合料都能保持一定的送装密度。
一般情况下,随着混料时间的延长,混合的均匀程度都将提高,其松装密度也趋于增高和稳定。
为了更清楚地了解混料时间对混合料均匀性的影响,我们做了大量的实验,测定不同工艺条件下碳的偏析程度、粉末压缩性、流动性、松装密度的变化来研究混料时间与混合料均匀性之间的关系。
本论文主要是研究混料时间对粉料工艺性能的影响,所以我们采用压制压坯密度达到7.1g/cm3时压机所达到的吨位来判断混合粉料的压缩性。
以排气门座142F9.3-3为例。
根据理论计算,压制密度达到7.1g/cm3时,压机吨位为6.8—7.5t。
3 结论
通过研究数据显示,可以得出以下结论:(1)对进、排气门座的特性粉料,随着时间的延长,粉料的均匀性可以大大地提高,压制压力、压坯密度趋于稳定,压制吨位从13吨很快下降到8吨左右,但压坯密度反而
从6.89g/cm3提高到7.15g/cm3。
(2)在额定450kg的V型混料机中装粉量为300kg混料一小时,混合料的均匀性以及各项工艺性能达到最佳状态。
(3)随着混料时间的进一步延长,混合料的均匀性反而变差。
(4)混料时间为60分钟时,混合料的压缩性最好。
参考文献
[1]周作平、申小平著.粉末冶金机械零件与实用技术.北京工业出版社, 2005.6.
[2]姚德超主编.高等教育用书.粉末冶金实验技术.中南工业大学.
[3]王崇林著.论粉末冶金材料密度的测定.中国科学院金属研究所.沈阳110016.
[4]王崇林著.粉末冶金进、排气门座的研制.中国科学院金属研究所.
[5]H.H.豪斯纳著.粉末冶金手册.北京粉末冶金研究所译.冶金工业出版社.1982.
[6]冯师颜.误差理论与实验数据处理[M].科学出版社,1964.
[7]韩风麟编著.粉末冶金机械零件.北京:机械工业出版社,1987.。