第九章_烧结
第九章 材料的烧结
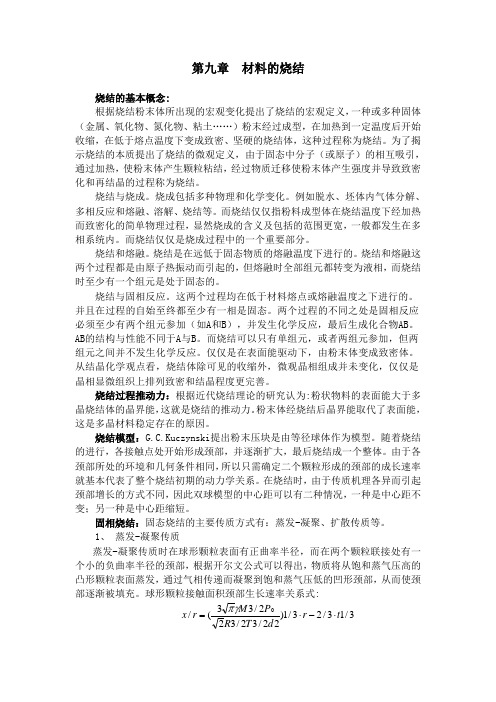
第九章 材料的烧结烧结的基本概念:根据烧结粉末体所出现的宏观变化提出了烧结的宏观定义,一种或多种固体(金属、氧化物、氮化物、粘土……)粉末经过成型,在加热到一定温度后开始收缩,在低于熔点温度下变成致密、坚硬的烧结体,这种过程称为烧结。
为了揭示烧结的本质提出了烧结的微观定义,由于固态中分子(或原子)的相互吸引,通过加热,使粉末体产生颗粒粘结,经过物质迁移使粉末体产生强度并导致致密化和再结晶的过程称为烧结。
烧结与烧成。
烧成包括多种物理和化学变化。
例如脱水、坯体内气体分解、多相反应和熔融、溶解、烧结等。
而烧结仅仅指粉料成型体在烧结温度下经加热而致密化的简单物理过程,显然烧成的含义及包括的范围更宽,一般都发生在多相系统内。
而烧结仅仅是烧成过程中的一个重要部分。
烧结和熔融。
烧结是在远低于固态物质的熔融温度下进行的。
烧结和熔融这两个过程都是由原子热振动而引起的,但熔融时全部组元都转变为液相,而烧结时至少有一个组元是处于固态的。
烧结与固相反应。
这两个过程均在低于材料熔点或熔融温度之下进行的。
并且在过程的自始至终都至少有一相是固态。
两个过程的不同之处是固相反应必须至少有两个组元参加(如A 和B ),并发生化学反应,最后生成化合物AB 。
AB 的结构与性能不同于A 与B 。
而烧结可以只有单组元,或者两组元参加,但两组元之间并不发生化学反应。
仅仅是在表面能驱动下,由粉末体变成致密体。
从结晶化学观点看,烧结体除可见的收缩外,微观晶相组成并未变化,仅仅是晶相显微组织上排列致密和结晶程度更完善。
烧结过程推动力:根据近代烧结理论的研究认为:粉状物料的表面能大于多晶烧结体的晶界能,这就是烧结的推动力。
粉末体经烧结后晶界能取代了表面能,这是多晶材料稳定存在的原因。
烧结模型:G.C.Kuczynski 提出粉末压块是由等径球体作为模型。
随着烧结的进行,各接触点处开始形成颈部,并逐渐扩大,最后烧结成一个整体。
由于各颈部所处的环境和几何条件相同,所以只需确定二个颗粒形成的颈部的成长速率就基本代表了整个烧结初期的动力学关系。
材料科学基础---第九章--烧结

一、烧结定义
1、烧结的物理过程: 颗粒间接触面积
扩大;颗粒聚集;颗粒 中心距逼近,逐渐形成 晶界;气孔形状变化; 体积缩小;从连通的气 孔变成各自独立的气孔 并逐渐缩小,以致最后 大部分甚至全部气孔从 晶体中排除。
2、烧结的定义:
❖据烧结粉末体所出现的宏观变化
一种或多种固体粉末经过成型,在加热到一定温度 后开始收缩,在低于熔点温度下变成致密、坚硬的烧结 体,这种过程称为烧结。
烧结:仅指粉料经加热而致密化的简单物理过 程
2. 烧结和熔融
烧结是在远低于固态物质的熔融温度下进行的
金属粉末
TS(0.3~0.4)TM
盐类 硅酸盐
TS 0.57TM
TS(0.8~0.9)TM
3. 烧结与固相反应
相同点:均在低于材料熔点或熔融温度下进行, 并且过程中都至少有一相是固态
不同点:固相反应至少有两组分参加,并且发生化 学反应,最后生化合物AB,烧结可以是单组分或 双组分参加,两组分间不发生化学反应。烧结使 材料更加致密,但微观晶相并未发生变化
r x r
P0 Tn
T
P0
x r
❖4. 蒸发-凝聚传质的特点
烧结时颈部区域扩大,球的形状改变为椭 圆,气孔形状改变,但球与球之间的中心距不 变,坯体不收缩,坯体密度不变。
二、扩散传质(模型:颈部应力模型)
❖ 1.传质机理:空位浓度差△C
下面通过计算不同部位空位浓度 说明扩散传质机理:
❖3. 球形颗粒接触面积颈部生长速率:
1
x r
3
3
M 2 P0
33
2R2T 2d2
3
2
r 3
1
材料科学基础--第九章-烧结

中心距L缩短 坯体收缩
适用: 蒸发-凝聚传质
扩散传质
球体-平板模型
扩散传质
烧结会引起体积的收缩和致密度增加,常用线收缩率或密度值来评
价烧结的程度。对模型(B),烧结收缩是因颈部长大,两球心距离 缩短所引起的。故可用球心距离的缩短率 L 来表示线收缩率(L0烧结前两球心距离,L-烧结后缩短值): L0
烧结后期:传质继续进行,粒子长大,气孔变成孤立闭气孔,密 度达到95%以上,制品强度提高。
(二)烧结推动力
能量差(具体表现为:压力差、空位浓度差、溶解度差)
1、能量差 粉状物料的表面能大于多晶烧结体的晶界能,即能量差是烧结的 推动力,但较小。烧结不能自发进行,必须对粉料加以高温,才 能促使粉末体转变为烧结体
2、颈部空位浓度分析
1)无应力区(晶体内部)的空位浓度:
c0
n0 N
exp
EV kT
2)应力区的空位浓度:
受压应力时,形成体积为Ω空位所做的附加功为:
En
受张应力时,形成体积为Ω空位所做的附加功为:
Et
所以,在接触点或颈部区域形成一个空位所做的功为:
3)温度的影响
T↑,D*=D0exp(-Q/RT)↑↑, x/r、△L/L↑↑。
温度升高,加快烧结。温度在烧 结中往往起决定性作用。
在扩散为主的烧结中,除体积扩
散外,质点还可以沿表面、界面或
位错等处进行多种途径的扩散。库
津斯基综合各种烧结过程,得出烧
结动力学典型方程为:
( x)n r
F(T ) rm
多相反应和熔融、溶解、烧结等,其包括范围较宽。 烧结:仅是粉料经加热而致密化的简单过程,是烧成过程的一个
第九章烧结

• • • • 相关定义 烧结推动力、种类、传质方式及机理 晶粒生长和二次再结晶的方式、推动力 影响烧结的因素
烧结体的显微结构 晶体 晶界 玻璃体 气孔
化学组成 材料组成 矿物组成 晶体的尺寸及分布 气孔的尺寸及分布 晶界的体积分数 玻璃相的数量及分布 原料的颗粒级配 成型方法 温度制度 烧成制度 压力制度 气氛
F x AD BC F AB CD
AD BC 2 sin 2
( 很小, sin 同理
)
AB CD x
F x
Fx
作用在垂直于ABCD元上的力
F 2[ Fx sin F sin ] 2 2
据数学原理
㏑(1+X)≈X (9---4)
∴
又因 x MP0 P dRT
Δ Ρ :颈部与颗粒表面的饱和蒸汽压差
据朗格缪尔公式 U P M m 2RT
Um:凝聚速率 α :调节系数 Δ Ρ :凹面与平面之间蒸汽压
1 2
(9—5)
当 凝聚速率等于颈部体积增加时
U m A dV d dt
dt
5D V L 3 3 kT V L
5 6 5 2 5 r t
9—21
讨论; ① 表面扩散不宜采用增加保温时间来达到坯体致密化的 目的 ② 起始粒度小,有利于密度的提高 ③升高温度会加快烧结
(2)中期: 结构特征:以晶界、晶格扩散为主,颗粒开始粘结,气孔逐步变为 圆柱状且相互连通,晶粒正常长大,收缩大(80—90%)
9.3.2 流动传质
1、粘性流动 (1)定义:在液相烧结时,由于高温下粘性液体出现牛顿型流 动而产生的传质称为粘性流动传质 (2)特征:定向物质迁移量与作用力(如表面张力)大小成正 比,服从粘性流动关系 F S x F 式中: S ---剪切应力 -----流动速度梯度 x F
第九章 烧结.
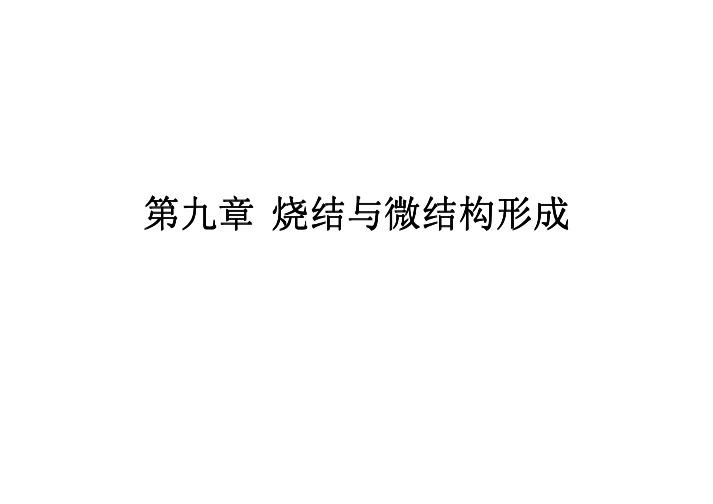
其中:Cv0为平面下的空穴浓度;Ω 为空穴体积;k为波尔兹曼常数;T为绝对温度; K为曲率。 C γ ΩK Cv − Cv 0 = ∆Cv = − v 0 SV 当 γ SV ΩK << kT
kT
9.2.2.4 弯曲表面上的蒸汽压 由于弯曲表面上的蒸汽压与表面的化学位有平衡关系,凸面的蒸汽压比平面 高,而凹面蒸汽压较低。考虑将一定数量的原子从气相中移至弯曲表面,使表面之 下的空穴浓度发生变化所带来的自由能变化,弯曲表面上的蒸汽压可用下式表示: γ SV ΩK
9.2.2.3 弯曲表面下的空穴密度 施加在凸表面下的原子上的压缩应 力会把空穴挤出,因此空穴密度比平面 低。反之,凹面下的空穴密度比平面低。 空位密度差别产生扩散流,空位从凹面向凸面迁移,原子从凸面向凹面扩散。 主曲率半径分别为a1和a2的曲面下的空穴浓度为:
γ ΩK Cv = Cvo exp − SV kT
9.2.4 烧结机制
物质转移——从化学势高的区域迁移到化学势低的区域。 从化学势高的区域迁移到化学势低的区域。 六种传质方式: 1 表面扩散传质 2 晶格扩散传质(表面层) 3 气相传质—蒸发/凝聚传质 4 晶界扩散传质 5 晶格扩散传质(晶界) 6 塑性流动
(1)六种方式都导致颈部生长,增加陶瓷强度 (2)1,2,3三种传质不会增加陶瓷的致密度 (3)4,5两种机制是多晶陶瓷烧结致密化的途径 (4)机制6在金属粉末烧结中更为普遍,提高致密度
Ψ = (180 N c − 360) / N c
如左图所示(两面角为120°): N<6,气孔具有“凸边”,气孔表面能 的减少量会大于晶界能的增加量 N>6,气孔具有“凹边”气孔表面能的 减少量会小于晶界能的增加量
三维情况下,二面角与气孔配位数对应关系图
第九章 烧 结
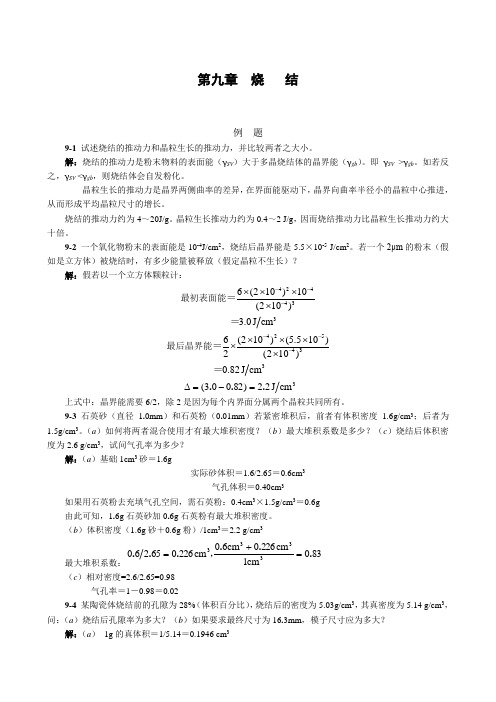
第九章 烧 结例 题9-1 试述烧结的推动力和晶粒生长的推动力,并比较两者之大小。
解:烧结的推动力是粉末物料的表面能(γSV )大于多晶烧结体的晶界能(γgb )。
即γSV >γgb 。
如若反之,γSV <γgb ,则烧结体会自发粉化。
晶粒生长的推动力是晶界两侧曲率的差异,在界面能驱动下,晶界向曲率半径小的晶粒中心推进,从而形成平均晶粒尺寸的增长。
烧结的推动力约为4~20J/g 。
晶粒生长推动力约为0.4~2 J/g ,因而烧结推动力比晶粒生长推动力约大十倍。
9-2 一个氧化物粉末的表面能是10-4J/cm 2,烧结后晶界能是5.5×10-5 J/cm 2。
若一个2μm 的粉末(假如是立方体)被烧结时,有多少能量被释放(假定晶粒不生长)?解:假若以一个立方体颗粒计:4244336(210)10(210)3.0J cm ---⨯⨯⨯⨯最初表面能==4254336(210)(5.510)2(210)0.82J cm ---⨯⨯⨯⨯⨯最后晶界能==3cm J 22)82003(...=-=∆上式中:晶界能需要6/2,除2是因为每个内界面分属两个晶粒共同所有。
9-3 石英砂(直径1.0mm )和石英粉(0.01mm )若紧密堆积后,前者有体积密度1.6g/cm 3;后者为1.5g/cm 3。
(a )如何将两者混合使用才有最大堆积密度?(b )最大堆积系数是多少?(c )烧结后体积密度为2.6 g/cm 3,试问气孔率为多少?解:(a )基础1cm 3砂=1.6g实际砂体积=1.6/2.65=0.6cm 3气孔体积=0.40cm 3如果用石英粉去充填气孔空间,需石英粉:0.4cm 3×1.5g/cm 3=0.6g 由此可知,1.6g 石英砂加0.6g 石英粉有最大堆积密度。
(b )体积密度(1.6g 砂+0.6g 粉)/1cm 3=2.2 g/cm 3最大堆积系数:830cm 1cm 2260cm 60cm 2260652603333......=+=,(c )相对密度=2.6/2.65=0.98气孔率=1-0.98=0.029-4 某陶瓷体烧结前的孔隙为28%(体积百分比),烧结后的密度为5.03g/cm 3,其真密度为5.14 g/cm 3,问:(a )烧结后孔隙率为多大?(b )如果要求最终尺寸为16.3mm ,模子尺寸应为多大?解:(a ) 1g 的真体积=1/5.14=0.1946 cm 31g 的烧后体积=1/5.03=0.1988 cm 3最终孔隙率=(0.1988-0.1946)/0.1988=2%(b )真体积=0.72V 0(烧结前体积)=0.98V L (烧后体积))mm(1181081316720980· 720980303300模子尺寸.......=⨯====L L L L L L L V V此题亦可用其它方法解,但用1g 最方便,可直接比较体积变化。
《烧结理论与工艺》第九章 烧结原料及其特性
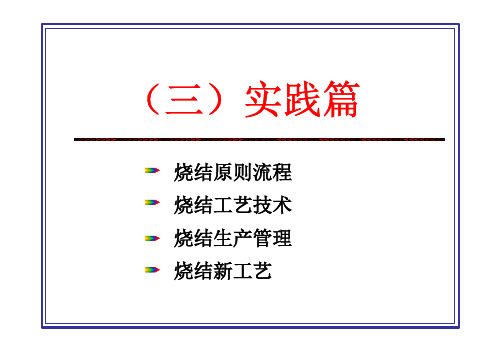
铁矿、褐铁矿。
我国主要铁矿石生产地区铁矿石产量 单位:万吨
山东
地区
2005
2006(E)
2.86% 湖北
其他
河北 辽宁 内蒙古
15227 9005 2998
24852 10137 4026
10.91% 安徽 1.75% 四川 2.41% 5.27%
河北 43.39%
山西
2103
2767
北京
北京
1834
1682
2.95%
四川
1692
2877
安徽
1099
1328
山西
山东 湖北
1077 864
1645 1002
5.09%
内蒙古 7.23% 辽宁
18.14%
全球铁矿石资源储量及基础储量
2005年世界主要铁矿石生产国产量及进出口量
矿 石 种 类
冶金工业对锰矿石的质量要求
锰矿资源概况
截至1996年底,我国陆地已查明锰矿区213处, 保有锰矿石储量5.66亿t,其中A+B+C级占40 %,为2.27亿t。如按矿石平均含锰21%计算,保有 锰金属储量1.19亿t,其中A+B+C级0.48亿t。
世界锰矿储量为6.8亿t(锰金属量,下同)、储量基础5 0亿t。其中南非居首位,储量基础40亿t;往下依次是 乌克兰,5.2亿t;加蓬,1.5亿t;澳大利亚,0.72 亿t;巴西,0.56亿t;格鲁吉亚,0.49亿t;印度, 0.36亿t。如以中国的A+B+C级储量和国外的储量 基础相比,中国居于格鲁吉亚之后,印度之前,大约排在 第6位。
《无机材料科学基础》第9章烧结

烧结和熔融 烧结是在远低于熔融温度下进行的,至少有一组元处于固 熔融则所有组元转变为液相 烧结和熔融的关系: 金属粉末:Ts≈(0.3---0.4)TM 盐 类:Ts≈0.57 TM 硅 酸 盐:Ts≈(0.8---0.9)TM
态
3、烧结与固相反应
固相反应:至少有两个组份参加,产物不同于任一反应物 烧结:可单或多组分,不发生化学反应,表面能推动下实现致密化的过程
3、烧结程度表征
(1)、气孔率 (2)烧结体密度 (4)强度 (5)晶粒尺寸 (7)坯体收缩率 (8)相对密度
(3)电阻 (6)吸水率
9.1.2与烧结有关的一些概念 1、烧结与烧成 烧结:仅指粉料经加热而致密化的物理过程 烧成:包括粉料在加热过程中发生的一切物理和化学变 化 例如:气体排除、相变、熔融;氧化、分解、固相 反应等
r r 将代入 Fx , , Fρ ,考虑 sin θ ≈ θ 2 2
,得
r F = γ ⋅θ 2 (ρ − x) A = AB∗ BC = ρ ∗ xθ
γ ∗θ (ρ − x) 1 1 =γ − σ = F A= 2 x ρ xρθ γ Qx >> ρ,∴σ ≈ − ρ
空位浓度差导致的晶格扩散是颗粒中心逼近的原因
3、扩散传质途径
4、扩散分期 、 (1)初期:表面扩散显著,空隙表面光滑和气孔球形化,坯 体收缩小(1%) 由9—16知颈部与晶体内浓度差 ∆ 2 C = [C 0 ]σΩ σ=γ
∆C = [C 0 ]γΩ
ρ
代入得
9—17 每秒从每厘米周长上扩散离开颈部的空位扩散流量 9—18 J = 4 DV ∆C DV:空位扩散系数,如D*自扩散系数, DV=
F x = γ AD = γ BC Fρ = γ AB = γ CD
- 1、下载文档前请自行甄别文档内容的完整性,平台不提供额外的编辑、内容补充、找答案等附加服务。
- 2、"仅部分预览"的文档,不可在线预览部分如存在完整性等问题,可反馈申请退款(可完整预览的文档不适用该条件!)。
- 3、如文档侵犯您的权益,请联系客服反馈,我们会尽快为您处理(人工客服工作时间:9:00-18:30)。
3.气相传质 由于颗粒表面各处的曲率不同,按开尔文公式
可知,各处相应的蒸气压大小也不同。故质点容 易从高能阶的凸处(如表面)蒸发,然后通过气 相传递到低能阶的凹处(如颈部)凝结,使颗粒 的接触面增大,颗粒和空隙形状改变而使成型体 变成具有一定几何形状和性能的烧结体。这一过 程也称蒸发-冷凝。
4.溶解—沉淀 在有液相参与的烧结中,若液相能润湿和溶解
固相烧结 液相烧结
烧结温度下基本上无液相出 现的烧结,如高纯氧化物之 间的烧结过程。
有液相参与下的烧结,如多组 分物系在烧结温度下常有液相 出现。
近年来,在研制特种结构材料和功能材料的同时,产 生了一些新型烧结方法。如热压烧结,放电等离子体 烧结,微波烧结等。
图1 热压炉
图2 放电等离子体烧结炉(SPS)
晶粒长大的推动力是晶界过剩的 自由能,即晶界两侧物质的自由 焓之差是使界面向曲率中心移动
的驱动力。
小晶粒生长为大晶粒.使界面面积减小,界面 自由能降低,晶粒尺寸由1μm变化到lcm,相 应的能量变化为0.1-5Cal/g。
自由焓
△G *
△G
位置
(a)
(b)
图12 晶界结构及原子位能图
50 3
4
10 6
晶粒直径(mm)
时间(分)
图10 在400℃NaCl晶体,置于470℃再结晶的情况
推动力
初次再结晶过程的推动力 是基质塑性变形所增加的
能量。
一般储存在变形基质中的能量约为0.5~1Cal/g的数量 级,虽然数值较熔融热小得多(熔融热是此值的1000倍 甚至更多倍),但却足够提供晶界移动和晶粒长大所需 的能量。
三、烧结机理
(一) 颗粒的粘附作用 (二) 物质的传递
(一) 颗粒的粘附作用
例子:
把两根新拉制的玻璃纤维相互叠放在一 起,然后沿纤维长度方向轻轻地相互拉过, 即可发现其运动是粘滞的,两根玻璃纤维会 互相粘附一段时间,直到玻璃纤维弯曲时才 被拉开,这说明两根玻璃纤维在接触处产生 了粘附作用。
由此可见,粘附是固体表面的普遍性质,它起因于固 体表面力。当两个表面靠近到表面力场作用范围时.即 发生键合而粘附。粘附力的大小直接取决于物质的表面 能和接触面积,故粉状物料间的粘附作用特别显著。
如果固体在高温下有较高蒸气压,则可以通 过气相导致物质从凸表面向凹表面处传递。此 外若以固体表面的空位浓度C或固体溶解度L分 别代替式2中的蒸气压P,则对于空位浓度和溶 解度也都有类似于式 2的关系,并能推动物质 的扩散传递。
可见,作为烧结动力的表面张力可以通 过流动、扩散和液相或气相传递等方式 推动物质的迁移。
c'c0
c
3
exp
1
c0
c0
一般烧结温度下,
于是
c 3 1
c0 kT
c
3 k T
c0
从式可见,在一定温度下空位浓度差是与表面 张力成比例的,因此由扩散机理进行的烧结过 程,其推动力也是表面张力。
由于空位扩散既可以沿颗粒表面或界面进行, 也可能通过颗粒内部进行,并在颗粒表面或颗 粒间界上消失。为了区别,通常分别称为表面 扩散,界面扩散和体积扩散。有时在晶体内部 缺陷处也可能出现空位,这时则可以通过质点 向缺陷处扩散,而该空位迁移到界面上消失, 此称为从缺陷开始的扩散。
S
x
式中,τ是极限剪切力。
2. 扩散传质
扩散传质是指质点(或空位)借助于浓度梯度 推动而迁移的传质过程。如图7和图8所示,烧
结初期由于粘附作用使粒子间的接触界面逐渐
扩大并形成具有负曲率的接触区。在颈部由于
曲面特性所引起的毛细孔引力△ρ≈γ/ρ。
对于一个不受应力的晶体,其空位浓度Co 是取决于温度T和形成空位所需的能量△Gf
拉力(kg/cm3) (g/cm2)
密 度
温度(°C)
图5 烧结温度对烧结体性质的影响 l一比电导 2一拉力 3一密度
结果与讨论:
1.随烧结温度的升高,比电导和抗拉强度增加。
2.曲线表明,在颗粒空隙被填充之前(即气孔率显著 下降以前),颗粒接触处就已产生某种键合,使得电 子可以沿着键合的地方传递,故比电导和抗拉强度 增大。
图11 烧结温度对AlN晶粒尺寸的影响
二、晶粒长大
概念
在烧结中、后期,细小晶粒逐渐 长大,而一些晶粒的长大过程也 是另一部分晶粒的缩小或消失过 程,其结果是平均晶粒尺寸增加
这一过程并不依赖于初次再结晶过程;晶粒 长大不是小晶粒的相互粘接,而是晶界移动 的结果。其含义的核心是晶粒平均尺寸增加。
推动力
1.流动传质 这是指在表面张力作用下通过变形、流动引起 的物质迁移。属于这类机理的有粘性流动和塑性 流动。
粘性流动传质 :
若存在着某种外力场,如表面张力作用时, 则质点(或空位)就会优先沿此表面张力作用的方 向移动,并呈现相应的定向物质流,其迁移量是 与表面张力大小成比例的,并服从如下粘性流动 的关系:
水膜的例子,见图8 因此,粘附作用是烧结初始阶段,导致粉体颗粒间产 生键合、靠拢和重排,并开始形成接触区的一个原因。
(a)
(b)
图8被水膜包裹的两固体球的粘附
(二) 物质的传递
在烧结过程中物质传递的途径是多样的,相应 的机理也各不相同。但如上所述,它们都是以表 面张力作为动力的。 有流动传质 、扩散传质 、 气相传质 、溶解—沉淀传质。
图6 粉状成型体的烧结过程示意图
6/1
12/2
a)烧结前
b)烧结后
图7 铁粉烧结的SEM照片
(a)固相烧结(Al2O3)和(b)液相烧结样品 (98W-1Ni-1F2(wt%))的显微结构
坯体中颗粒重排,接触处
烧结初期
产生键合,空隙变形、缩
烧
小(即大气孔消失),固-
结
气总表面积没有变化。
过
程 的
一、初次再结晶
概念
初次再结晶是指从塑性变形的、具 有应变的基质中,生长出新的无应
变晶粒的成核和长大过程。
初次再结晶常发生在金属中,无机非金属材料特别 是—些软性材料NaCl、CaF2等,由于较易发生塑性 变形,所以也会发生初次再结晶过程。另外,由于无 机非金属材料烧结前都要破碎研磨成粉料,这时颗粒 内常有残余应变,烧结时也会出现初次再结晶现象。
图13 烧结后期晶粒长大示意图
晶粒正常长大时,如果晶界受到第二相杂质的 阻碍,其移动可能出现三种情况:
1.晶界能量较小,晶界移动被杂质或气孔 所阻挡,晶粒正常长大停止。
2.晶界具有一定的能量,晶界带动杂质或气孔继 续移动,这时气孔利用晶界的快速通道 排除,坯体不断致密。
3.晶界能量大,晶界越过杂质或气孔,把气孔 包裹在晶粒内部。由于气孔脱离晶昂界,再不能 利用晶界这样的快速通道而排除,使烧结停止, 致密度不再增加。这时将出现二次再结晶现象。
烧结是一个自发的不可逆过程,系统表面 能降低是推动烧结进行的基本动力。
表面张力能使凹、凸表面处的蒸气压P分别低于和高
于平面表面处的蒸气压Po,并可以用开尔文本公式
表达: 对于球形表面
ln P 2M (1)
P0 dRTr
对于非球形表面
ln P M ( 1 1 )(2)
P0 dRT r1 r2
表面凹凸不平的固体颗粒,其凸处呈正压,凹处呈负 压,故存在着使物质自凸处向凹处迁移。
时可能取决于另一种机理。
图9 不同烧结机理的传质途径
第三节 再结晶和晶粒长大
在烧结中,坯体多数是晶态粉状材料压制而成,随 烧结进行,坯体颗粒间发生再结晶和晶粒长大,使坯体 强度提高。所以在烧结进程中,高温下还同时进行着两 个过程,再结晶和晶粒长大。尤其是在烧结后期,这两 个和烧结并行的高温动力学过程是绝不对不能忽视的, 它直接影响着烧结体的显微结构(如晶粒大小,气孔分 布)和强度等性质。
图3 气压烧结炉(GPS)
图4 微波烧结炉
三、烧结温度和熔点的关系
泰曼指出,纯物质的烧结温度Ts与其溶点Tm有如 下近似关系:
金属粉末Ts≈(0.3—0.4)Tm 无机盐类Ts≈0.57Tm
硅酸盐类Ts≈(0.8—0.9)Tm 实验表明,物料开始烧结温度常与其质点开始明 显迁移的温度一致。
第二节 烧结过程及机理
固相,由于小颗粒的表面能较大其溶解度 也就比大颗粒的大。其间存在类似于式3的关系:
ln c 2 SLM c0 RTr
这种通过液相传质的机理称溶解—沉淀机理。
结果与讨论
烧结的机理是复杂和多样的,但都 是以表面张力为动力的。应该指出, 对于不同物料和烧结条件,这些过 程并不是并重的,往往是某一种或 几种机理起主导作用。当条件改变
图14 由于晶粒长大使气孔扩大示意图
造成二 次再结 晶的原 因主要 是原始 物料粒 度不均 匀及烧 结温度
偏高
其次是
产
成型压
生
力不均
原
匀及局
因
部有不
均匀的
液相等
但是,并不是在任何情况下二次再结晶过程 都是有害的。 在现代新材料的开发中常利用二次再结过程 来生产一些特种材料。如铁氧体硬磁材料 BaFel2019的烧结中,控制大晶粒为二次再结晶 的晶核,利用二次再结晶形成择优取向,使 磁磷畴取向一致,从而得到高磁导率的硬磁 材料。
一、烧结过程
首先从烧结体的宏观性质随温度的变化上来认识烧结过 程。
(一)烧结温度对烧结体性质的影响
图5是新鲜的电解铜粉(用氢还原的),经高压成 型后,在氢气气氛中于不同温度下烧结2小时然 后测其宏观性质:密度、比电导、抗拉强度,并 对温度作图,以考察温度对烧结进程的影响。
比电导(Ω-1·cm-3)
三、二次再结晶
概念
二次再结晶是坯体中少数大晶粒尺 寸的异常增加,其结果是个别晶粒 的尺寸增加,这是区别于正常的晶 粒长大的。