航空铝合金加工时的变形控制
铝合金薄壁件加工中变形的因素分析与控制方法

铝合金薄壁件加工中变形的因素分析与控制方法作者:乔楠楠来源:《知识文库》2017年第10期一般认为,在壳体件、套筒件、环形件、盘形件、轴类件中,当零件壁厚与内径曲率半径(或轮廓尺寸)相比小于1:20时,称作为薄壁零件。
这一类零件的共同特点是受力形式复杂,刚度低,加工时极易引起误差变形或工件颤振,从而降低工件的加工精度。
薄壁零件因其制造难度极大,而成为国际上公认的复杂制造工艺问题。
一、薄壁件加工变形因素分析薄壁件由于刚度低,去除材料率大,在加工过程中容易产生变形,对装夹工艺要求高,使加工质量难以保证。
薄壁类零件在加工中引起变形的因素有很多,归纳总结有以下几个方面:1、工件材料的影响铝合金作为薄壁件最理想的结构材料,与其他金属材料相比,具有切削加工性好的特点。
但由于铝合金导热系数高、弹性模量小、屈强比大、极易产生回弹现象,大型薄壁件尤为显著。
因此,在相同载荷情况下,铝合金工件产生的变形要比钢铁材料的变形大,同时铝合金材料具有硬度小、塑性大和化学反应性高等性质,在其加工中极易产积屑瘤,从而影响工件的表面质量和尺寸精度。
2、毛坯初始残余应力的影响薄壁件加工中的变形与毛坯内部的初始残余应力有直接的关系,同时由于切削热和切削力的影响,使工件和刀具相接触处的材料产生不能回弹的塑性变形。
这种永久性的变形一旦受到力的作用就会产生残余应力,而在加工过程中,一旦破坏了毛坯的残余应力,工件内部为达到新的平衡状态而使应力重新分布,从而造成了工件的变形。
3、装夹方式的影响在加工中夹具对工件的夹、压而引起的变形直接影响着工件的表面精度,同时如果由于夹紧力的作用点选择不当而产生的附加应力,也将影响工件的加工精度。
其次,由于夹紧力与切削力产生的耦合效应,也将引起工件残余应力的重新分布,造成工件变形。
4、切削力和切削热的影响切削力是影响薄壁件变形的一个重要因素。
切削力会导致工件的回弹变形,产生不平度,当切削力达到工件材料的弹性极限会导致工件的挤压变形。
3A21—F铝合金板材在数控加工中防止变形的工艺措施
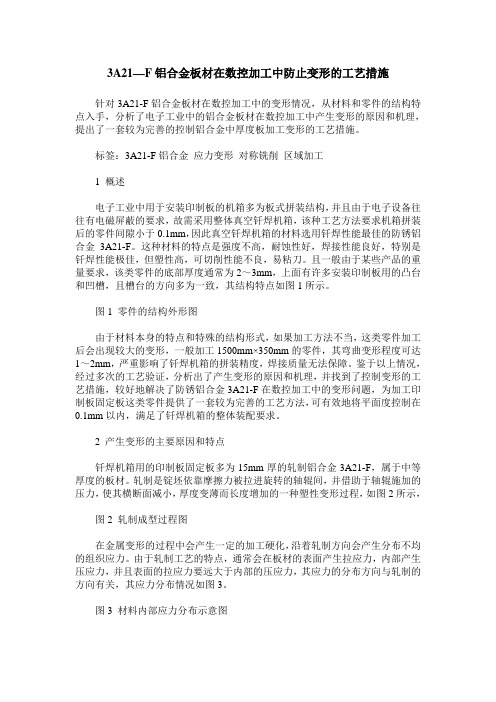
3A21—F铝合金板材在数控加工中防止变形的工艺措施针对3A21-F铝合金板材在数控加工中的变形情况,从材料和零件的结构特点入手,分析了电子工业中的铝合金板材在数控加工中产生变形的原因和机理,提出了一套较为完善的控制铝合金中厚度板加工变形的工艺措施。
标签:3A21-F铝合金应力变形对称铣削区域加工1 概述电子工业中用于安装印制板的机箱多为板式拼装结构,并且由于电子设备往往有电磁屏蔽的要求,故需采用整体真空钎焊机箱,该种工艺方法要求机箱拼装后的零件间隙小于0.1mm,因此真空钎焊机箱的材料选用钎焊性能最佳的防锈铝合金3A21-F。
这种材料的特点是强度不高,耐蚀性好,焊接性能良好,特别是钎焊性能极佳,但塑性高,可切削性能不良,易粘刀。
且一般由于某些产品的重量要求,该类零件的底部厚度通常为2~3mm,上面有许多安装印制板用的凸台和凹槽,且槽台的方向多为一致,其结构特点如图1所示。
图1 零件的结构外形图由于材料本身的特点和特殊的结构形式,如果加工方法不当,这类零件加工后会出现较大的变形,一般加工1500mm×350mm的零件,其弯曲变形程度可达1~2mm,严重影响了钎焊机箱的拼装精度,焊接质量无法保障。
鉴于以上情况,经过多次的工艺验证,分析出了产生变形的原因和机理,并找到了控制变形的工艺措施,较好地解决了防锈铝合金3A21-F在数控加工中的变形问题,为加工印制板固定板这类零件提供了一套较为完善的工艺方法,可有效地将平面度控制在0.1mm以内,满足了钎焊机箱的整体装配要求。
2 产生变形的主要原因和特点钎焊机箱用的印制板固定板多为15mm厚的轧制铝合金3A21-F,属于中等厚度的板材。
轧制是锭坯依靠摩擦力被拉进旋转的轴辊间,并借助于轴辊施加的压力,使其横断面减小,厚度变薄而长度增加的一种塑性变形过程,如图2所示,图2 轧制成型过程图在金属变形的过程中会产生一定的加工硬化,沿着轧制方向会产生分布不均的组织应力。
常用航空用铝合金热处理规范解读
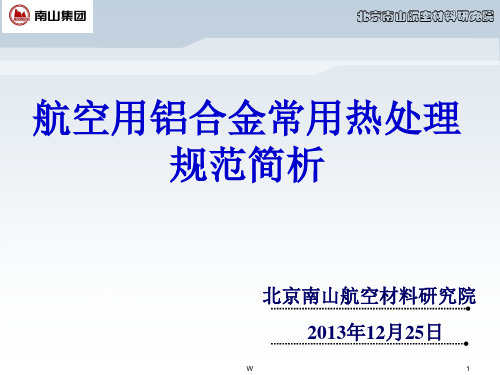
O2---材料在形变处理后所处的状态,这种处理是为了提高材料的成 形性能,以便进行超塑性加工(SPF);
O3---均匀化处理后的状态。
W
2
北京南山航空材料研究院
H态: 加工硬化状态。适用于通过加工硬化提高强度的产品,产品在加 工硬化后可经过(也可不经过)使强度有所降低的附加热处理。 (对于船用合金,如5083、5383、5456、5059等合金,常用的热 处理状态有H321及H116状态)。
7150型材 7055 厚板 2090板 6061压光板
T6151 T7751 T77511 T7751 T83 T651
19.1~38.1 6.35~76.2 / 9.53~31.75厚(~2790mm宽) / /
W
5
北京南山航空材料研究院
Issoire (Alcan) 产品
合金牌号 2024 2024 HF Clad 2024A 2027 2195 2297 2098 7010 7040 7449 7050 7150 7075 7475 6056 6061
适用于固溶处理、淬火或从高温成型过程冷却后,按规定量进行拉伸 的挤压棒材、型材或管材以及拉制管材。这些产品在拉伸后不再进行 矫直。挤压棒材、型材或管材的永久变形量是1~3%;拉制管材的永久 变形量为1.5%~3%。
适用于固溶处理、淬火或从高温成型过程冷却后,按规定量进行拉伸 的挤压棒材、型材或管材以及拉制管材。这些产品在拉伸后可略微矫 直以使产品达到公差要求。挤压棒材、型材或管材的永久变形量是 1~3%;拉制管材的永久变形量为1.5%~3%。
T37---固溶处理后,为增加产品强度而进行断面减缩率约 7%的冷加工,然后进行自然时效处理。
航空结构件纵梁工艺设计与变形控制分析

航空结构件纵梁工艺设计与变形控制分析摘要] 随着航空制造技术的快速发展以及对飞机性能要求的不断提高,飞行器设计趋于整体化和轻量化。
整体结构件的使用对航空制造企业提出更高的要求,其中加工变形是瓶颈问题之一。
研究影响航空结构件加工变形的因素及减小或抑制零件加工变形的工艺方法,对结构件加工技术具有重要的意义和价值。
本文以A220项目纵梁零件为研究目标,通过理论分析、实践验证相结合的方法,对大型结构件的工艺设计与铣削加工变形控制进行了分析和阐述,突破了高速、强力切削下变形控制的技术瓶颈。
关键词:民用飞机内应力整体结构件变形控制1 零件介绍1)结构设计情况。
纵梁零件属细长梁,为PCCN1类型(关键件),外廓尺寸2788mm×142mm×179mm,重约13.022kg,去除率达95.83%,整体零件结构设计不对称,正面为双侧缘条,槽口带立筋,槽深85至94mm,背面为单侧缘条,结构开敞无立筋。
2)尺寸公差情况。
理论外形面(OML面)以及局部装配面外形轮廓公差为0.25mm,其余外形轮廓公差为0.76mm。
腹板厚度为5-6mm,端头处最薄处仅2mm,公差±0.17mm。
缘条厚度6-8mm,端头最薄处仅2.4mm,公差±0.24mm。
3)原材料情况。
原材料使用进口航空硬铝合金,牌号状态7040-T7451,材料规范BAMS 516-021,规格选用最大允许7.75英寸(200mm),定额尺寸为2900mm×210mm。
4)零件在装配厂进行组装后,交付国外总装线进行中中与中后机身对接。
5)为保证装配精度,在装配工装上设置了检查器,要求间隙6±1mm。
2.1 变形原因分析1)毛坯初始残余应力是产生加工变形主要原因。
高强度航空铝合金厚板经过各种工艺处理过程,虽然最终进行了预拉伸和人工时效处理,但是仍然存在大量残余应力,它们在板材内部达到“M”型静态平衡。
在加工过程中,随着材料不断被去除,初始残余应力的释放使工件内部力矩平衡状态产生破坏,工件通过应力重新分布和变形达到新的平衡状态。
铝合金薄壁件加工变形控制技术研究

铝合金薄壁件加工 变形控制技术发展 趋势和展望
铝合金薄壁件加工变形控制技术需要高精度和高稳定性的设备,导致制造成本较高。
铝合金薄壁件加工变形控制技术需要精确的工艺参数和操作技巧,对工人的技能水平要求较高。
铝合金薄壁件加工变形控制技术需要长时间的加工过程,导致生产效率较低。
铝合金薄壁件加工变形控制技术需要严格的质量检测和控制,对检测设备的精度和可靠性要求 较高。
技术方案和实施过程应用案例:介绍铝合金薄壁件加工变形控制技术在具体产品中的应用案例,如航空航天、汽 车、电子等领域,说明该技术的应用价值和广泛性。
提高了铝合金薄壁 件加工精度和表面 质量
减少了加工过程中 的材料浪费和废品 率
提高了生产效率和 加工周期,降低了 生产成本
为企业带来了显著 的经济效益和社会 效益
铝合金薄壁件加工 变形控制技术
进给量:优化进给量可以提 高加工精度和减小变形
切削速度:选择合适的切削 速度以减小加工变形
切削深度:合理选择切削深度, 避免过大的切削力导致工件变 形
刀具薄壁件装 夹方式对加工变 形的影响
优化装夹方式的 方法和原理
铝合金薄壁件加工 变形控制实验研究
铝合金薄壁件:材料为5A06铝合金,壁厚为1mm
实验设备:数控加工中心、切削液、夹具等
实验环境:温度20±5℃,湿度50±10%
实验步骤:加工前对铝合金薄壁件进行热处理和表面处理,采用合适的切削参数进行加工, 观察并记录加工变形情况
实验材料:铝 合金薄壁件
实验设备:加 工机床、测量
加大研发投入,持 续探索更有效的加 工变形控制技术。
加强产学研合作, 推动铝合金薄壁件 加工变形控制技术 的创新发展。
建立完善的加工变 形控制技术标准体 系,提升行业整体 水平。
铝蜂窝板成型变形控制-概述说明以及解释

铝蜂窝板成型变形控制-概述说明以及解释1.引言1.1 概述概述铝蜂窝板作为一种新型复合材料,在现代工业中得到广泛应用。
它具有轻质、高强度、隔热、隔音等诸多优点,因此在航空航天、汽车、建筑等领域中得到了广泛应用。
本文将深入研究铝蜂窝板的成型变形控制方法。
铝蜂窝板成型过程中,必然会出现一定的变形现象,这些变形可能会影响产品的质量和性能。
因此,掌握和控制铝蜂窝板的成型变形,对于提高产品的精度和稳定性至关重要。
通过分析铝蜂窝板的应用领域、成型过程和成型变形的控制方法,本文旨在为工程师和研究人员提供一种全面的了解铝蜂窝板成型变形控制的途径。
希望通过本文的研究和总结,能够为相关行业的生产和研发提供有价值的参考和指导。
文章结构本文共分为引言、正文和结论三个部分。
引言部分将对文章进行概述,并阐明文章的目的和结构。
正文部分将详细介绍铝蜂窝板的应用领域、成型过程以及成型变形的控制方法。
结论部分将对全文进行总结,并探讨该研究的意义和未来展望。
目的本文的目的是探讨和研究铝蜂窝板的成型变形控制方法。
通过深入分析铝蜂窝板的应用领域和成型过程,了解铝蜂窝板在不同领域中的成型变形特点和影响因素。
在此基础上,探索和介绍一些常用的铝蜂窝板成型变形控制方法,以帮助工程师和研究人员更好地掌握和应用这些方法,提高产品的质量和稳定性。
通过本文的研究和总结,期望能够提供有价值的参考和指导,为相关行业的生产和研发提供技术支持。
同时,也为进一步深入研究和探索铝蜂窝板的成型变形控制打下基础,为该领域的发展和创新做出贡献。
1.2文章结构1.2 文章结构本文将按照以下结构组织:第一部分为引言,旨在概述本文的主题和目的。
引言部分将包括以下主要内容:1.1 概述:给出铝蜂窝板成型变形控制的背景和重要性,说明为什么该主题值得研究和讨论。
1.2 文章结构:简要介绍本文的结构和各个章节的内容,以便读者能够对整篇文章有一个整体的认识。
1.3 目的:明确本文的目标和研究重点,解释我们将要探讨和验证的假设或论点。
铝合金零件加工变形的解决方法
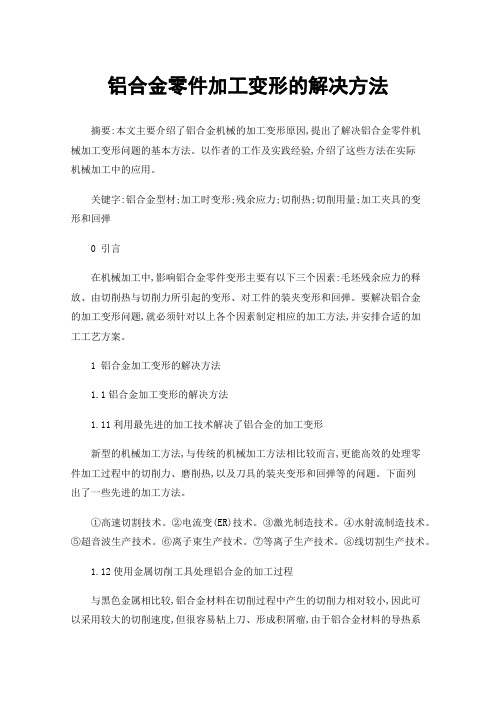
铝合金零件加工变形的解决方法摘要:本文主要介绍了铝合金机械的加工变形原因,提出了解决铝合金零件机械加工变形问题的基本方法。
以作者的工作及实践经验,介绍了这些方法在实际机械加工中的应用。
关键字:铝合金型材;加工时变形;残余应力;切削热;切削用量;加工夹具的变形和回弹0 引言在机械加工中,影响铝合金零件变形主要有以下三个因素:毛坯残余应力的释放、由切削热与切削力所引起的变形、对工件的装夹变形和回弹。
要解决铝合金的加工变形问题,就必须针对以上各个因素制定相应的加工方法,并安排合适的加工工艺方案。
1 铝合金加工变形的解决方法1.1铝合金加工变形的解决方法1.11利用最先进的加工技术解决了铝合金的加工变形新型的机械加工方法,与传统的机械加工方法相比较而言,更能高效的处理零件加工过程中的切削力、磨削热,以及刀具的装夹变形和回弹等的问题。
下面列出了一些先进的加工方法。
①高速切割技术。
②电流变(ER)技术。
③激光制造技术。
④水射流制造技术。
⑤超音波生产技术。
⑥离子束生产技术。
⑦等离子生产技术。
⑧线切割生产技术。
1.12使用金属切削工具处理铝合金的加工过程与黑色金属相比较,铝合金材料在切削过程中产生的切削力相对较小,因此可以采用较大的切削速度,但很容易粘上刀、形成积屑瘤,由于铝合金材料的导热系数较高,在切削时由切屑和零件导出的热量都较多,且切削区温度也较低,所以虽然刀具耐用度较高,但由于零件本身的温升也相对较快,很容易引起变形的产生。
因此,通过选用合适的刀具材料,在原刀具材料的基础上选用合适的刀具角度,并提高刀具表面的粗糙度的要求,对降低切削力和切削热十分有效。
1.13利用热处理解决相合金的加工变形解决铝合金型材加工应力问题的热处理方式,一般为去内部应力退火、再结品退火、均匀性退火及时效。
1.14利用冷处理解决铝合金的加工变形解决铝合金加热变形问题的冷处理技术,只要有振动时效和人工冷校形。
由于冷处理工艺节能、制造周期复、制造代价小,所以在制造流程中使用最广泛。
大型薄壁铝合金壳体数控加工变形模拟分析与控制(下)
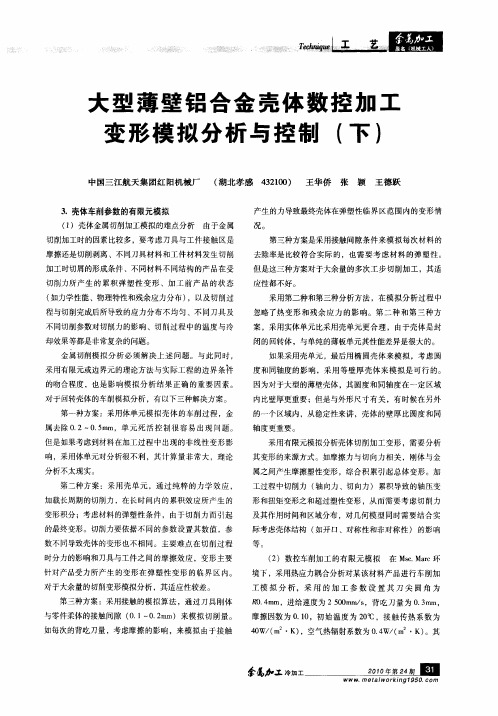
的最终变形 。切削力要依据不 同的参 数设置其 数值 ,参 数不同导致壳体的变形也不相 同。主要 难点在切 削过 程 时分力的影响和刀具 与工件之 间的摩擦效应 ,变形 主要 针对产 品受力所产生 的变形在 弹塑性 变形 的临界 区内。
( )数控车削加 工的有 限元模拟 2
在 M cMa s. r c环
境下,采用热应力耦合分析对某该材料产品进行车削加
工模 拟 分 析 ,采 用 的 加 工 参 数 设 置 其 刀 尖 圆 角 为
/ .m t 4 m,进给速度为 25 0 m s O 0 m / ,背吃刀量为 0 3 m, .m
对 于大余量的切削变形模拟分 析 , 其适应性较差。
第三种方案 :采用接触的模拟算法 ,通 过刀具刚体 与零件柔体的接触 间隙 ( . ~0 2 m)来模拟切 削量 。 0 1 .r a 如每次的背吃刀量 ,考虑摩擦 的影响 ,来模拟 由于接触
切削力所产 生 的累积 弹塑 性变 形 、加 工前 产 品的状 态
张
颖
王德跃
产生的力导致最终壳体在弹塑性临界 区范 围内的变形情
况。
第三种方案是采用接触间隙条件来模拟 每次材料的
去除率是 比较符合实 际的 ,也需 要考 虑材料 的弹塑性 。
但是这三种方案对于大余量的多次工步切 削加工 , 适 其
余应力 , 控制变形的作用 明显 。③切削加工 过程 中的工
序余量分配和工序组合 。由于加工过程 中存在加 工余 量 小 ,而所有的面均需要进行加工 ,各特征加工余量分 配 本身存在较大差异 ,从而对 导致 变形 的因素变得 复杂 ;
忽略了热变 形和残 余应 力 的影 响。第二 种 和第 三种方
- 1、下载文档前请自行甄别文档内容的完整性,平台不提供额外的编辑、内容补充、找答案等附加服务。
- 2、"仅部分预览"的文档,不可在线预览部分如存在完整性等问题,可反馈申请退款(可完整预览的文档不适用该条件!)。
- 3、如文档侵犯您的权益,请联系客服反馈,我们会尽快为您处理(人工客服工作时间:9:00-18:30)。
航空铝合金加工时的变形控制
作者:陈守伟
来源:《中国新技术新产品》2012年第17期
摘要:随着目前飞机制造业的大力发展,对于航空铝合金的加工工艺要求也越来越高,而航空铝合金在加工时的变形问题也成为了航空制造加工过程中出现的重要问题之一。
为了解决这一问题,我国从国外引入了先进的高速切削设备,并开始自主研究高速切削加工技术。
根据大量地研究表明,选择合理的加工参数、控制切削中的残余应力和对加工零件恰当使用可以大大地提高航空铝合金高速切削的质量。
关键词:航空铝合金加工技术;高速切削;控制
中图分类号:TU512.4 文
1 目前对航空铝合金加工技术的需求
铝合金整体构件都具有其壁薄、体积大、刚度差和易变性的特点,这就导致了其在加工时加工周期长、切削加工余量大和加工精度难控制的缺点。
而目前大型商用客机由于性能要求的提高,对于飞机的整体腹板、整体梁和长缘条等部分的制造加工要求也越来越高。
这就要求拥有更细致和更可靠的控制铝合金加工变形技术。
1.1 航空铝合金的加工要求
航空铝合金较之其他金属,具备很好的可切削性。
但是航空铝合金在加工过程中的要求却远远高于汽车等其他制造业。
这些要求主要反映在航空制造加工业对质量加工效率、零件精度和航空构件加工的形位误差控制上。
这些都导致了高效的铣削加工一直备受关注。
1.2 大型航空铝合金整体结构的缺陷
利用大型航空铝合金制造的航空整体结构一般包括客机的整体框、整体壁板、梁缘条和整体肋等。
这些构件在制造加工中往往会出现刚性差的特性,加上切削振动、切削力和切削热的作用则会容易导致零件变形。
这样一来,整体结构的加工精度和加工表面的质量均会降低。
1.3 高速切削技术
高速切削技术是一种金属加工领域的新工艺,它将切削工艺和高速加工技术进行了良好的结合,在目前航空整体结构件的加工上得到了广泛的应用。
目前国外的高速切削技术已经得到了国防部、政府和有关企业的支持。
波音公司在加工目前最大的航空整体构件之一的C-17铝合金机翼框架时候就使用了高速切割技术,仅仅耗时100h,4吨重的毛培切削完成。
我国在前
几年还以传统的制造业为主,航空制造加工工业的技术水平相对较低,加工时使用的仍是产同的铝合金切削工艺。
这种切削工艺导致了我国航空制造加工业的落后。
尤其是对于一些大尺寸零件和薄壁、型面复杂、复杂结构的难加工零件,如果采用这种加工方式,工艺路线复杂和加工周期长,周期要求难以得到满足。
在这种情况下,只有通过高效高速的切削,才能够有效地提高加工效率。
2 对造成航空铝合金加工时变形因素的简要分析
飞机的整体结构件加工容易变形主要是由于构件刚度差以及加工时的切削力、切削振动和切削热所导致。
引起这些问题的根本原因还是由于目前的航空整体构件加工仍缺乏系统的理论分析和研究。
理论的缺乏直接导致加工参数的选取十分保守,从而影响到了高速加工中心性能的发挥。
以下我们将简要就航空铝合金加工中的加工参数不合理、切削力的副作用和“让刀”现象进行分析。
2.1 加工参数的不合理
目前的航空构件制造业在材料加工过程中,由于对于力学、机械制造和切削加工等多种不同科学领域的涉及,导致了加工理论研究难度的加大,很难进行系统性的控制加工变形理论研究和切削加工时变形的理论分析。
在这种情况下,航空构件的加工只能采取试切的态度,对于加工参数的选择就会十分保守。
高速加工中心无法进行最有效的加工,很容易引起切削颤振,切削颤振会直接导致构件的薄壁部位变形。
2.2 切削力的副作用
据物理学理论分析,在金属材料的加工过程中,在切削力的作用下,零件的加工表面会产生残余应力,这种残余应力会导致零件的变形。
在通常情况下,航空大型构件的材料加工是采用大悬伸刀具,强大的切削力度会导致产生更为突出的残余应力,这样极容易出现航空铝合金在加工中的变形现象。
2.3 “让刀”现象
“让刀”在加工工艺中主要是指在一次加工行程结束后,工件或工具回到一开始的位置并相互离开一定距离。
这里的“让刀”现象指的是在航空构件制造的材料加工中,由于铝合金的屈强比大和弹性模量小,在加工切削时很有可能会产生回弹,从而对被加工的零件产生一定的形状误差。
这种现象在大型薄壁构件的切削中尤为明显。
航空构件的大型薄壁位置本身就比较多,所以“让刀”现象也成为了造成铝合金材料变形的主要原因之一。
3 解决铝合金加工时变形问题的策略
上文已大致分析了加工参数、切削力和“让刀”现象对航空铝合金构件加工的不利影响,现在我们将对这些问题的解决提出一些有效的解决策略:
3.1 选择合理的加工参数
合理的加工参数是保障切削质量的关键。
在航空铝合金加工过程中即使拥有再先进的机床和道具,如果没有良好的加工技术,切削时依然很难避免引起其它问题。
所以,在航空铝合金材料的实际加工中,选择适当的加工参数尤为重要。
合理的工作参数的选择要求编程人员能够依据不同的加工方法和加工要求来正确编写数控加工程序,并以此来达到最大的切削效率和加工目标。
3.2 对残余应力的控制
由上文所述,残余应力在航空铝合金材料的切削中所导致的影响是不可忽视的。
在解决此问题时,我们首先可以考虑材料本身,良好的取材可以从一定程度上减少零件受到残余应力的影响。
在切削时,还可以尽量通过对称的方式去除材料,这样可以合理地释放材料加工时产生的残余应力。
同时,还可以合理安排切削时零件的定位和材料的切除顺序,这也是减小残余应力的有效方法。
结合第一点,在加工过程中,如果能够选择合理的加工参数,使得零件能够局部保持高刚度,即可充分发挥出高速切削的优势。
这样一来,在高速切削时,所产生的热量会一部分被带走,这样就可以减少铝合金材料在加工中的热变形。
3.3 对加工零件的恰当使用
在对航空铝合金的加工过程中,如果能够选择中心环切的道具路径,即可使得零件在整个加工过程中都能够保持局部的高刚度。
同时也要注意夹具的选择,减小材料加工过程中的底面变形可以采用真空夹具装夹;而在进行飞机蒙皮的铣削加工等大型薄壁加工时,一般选择柔性多点的组合式支撑装置来完成装夹。
3.4 对航空铝合金加工中的变形进行预测
值得一提的是,目前我们已经提出来一种航空构件加工全过程的物理仿真方法,它基于接力计算模型,可以提前预测出航空构件在切削加工中的变形行为。
通过这种接力计算机系统可以对铝合金加工工艺的信息和有限元仿真计算信息进行转化,利用有限元模型来模拟航空构件的切削全过程。
在整个模拟过程中,前文所提到的切削力副作用和残余应力等都会被考虑。
利用这种接力计算系统对航空铝合金加工过程中的变形情况进行预测,从而起到良好地防范作用。
结语
在目前对于航空构件加工形位误差控制的高度要求下,航空制造加工产业对于铝合金加工时产生变形控制的需求也越来越高,高速切削工艺备受关注。
虽然我国目前已经引进了先进的加工设备,但是由于国外对于航空铝合金加工的先进技术的封锁,我国无法引进先进的切削工艺,这导致了先进设备的功能难以得到完全应用。
为此,国内的航空制造加工企业已经开始将生产和研究相结合,从高校和研究院所引入大量人才,对构件的制造加工进行了自主地研究,通过企业的自身条件再进行创新,从而掌握真正高效的航空铝合金加工变形的控制技术。
参考文献
[1]航空制造工程手册总编委员会.航空制造工程手册[M].北京:航空工业出版社.1995,(06).
[2]王兰志,张怀存.高速切削技术[J].航天制造技术.2008,(05).。