2021全位置管道自动焊接设备的研究
施工机具设备配置

施工机具设备配置第一节施工机械总体安排情况一、配置原则优选精良、先进的设备,并合理匹配,形成综合生产能力;设备能力大于进度指标要求的能力;同类设备尽可能采用同厂家同型号设备,以方便配件供应和维修;就近调配机械设备。
二、调配计划施工机械设备由我单位设备物资部门进行统一调配,以满足本合同段工程需要。
拟投入本合同工程的主要施工机械见下表。
开槽机PCR-30 1 凯联-美国辛姆莱2021年——养护13吨双钢轮压路机STR130C-8C1三一重工2021年119激振力(kn):169/119道路双钢轮液压振动压路机LTC208 1洛阳路通2021年74激振力(kn):160×2/90×2道路全液压单钢轮压路机XS123 1 徐工2021年93激振力280/190kN道路全液压单钢轮压路机XG626H 1 厦工2021年154激振力(高/低)480/375kN道路施工设备具体见附表五试验和检测仪器设备见附表六第二节施工机械性能先进、保证本工程措施一、施工机械性能先进除以上通用市政工程机械外,本工程为保证热力管道焊接质量,引入专门的先进管道焊机进行管道连接。
(一)HW-ZD-201 磁吸式全位置智能焊机满足各种工况的GMAE/FCAW-GS焊接工艺。
碳钢、不锈钢、合金钢、低温钢等(不可磁力吸附的材质应另配小车轨道)采用高清5寸彩色触摸界面,可实现焊接参数实时编辑输入,储存和调用。
实现360° 24个焊接分区参数预设,自动调用。
焊缝质量满足AUT/RT等探伤检测。
技术参数型号HW-ZD-201工作电压额定电压DC12-35V 典型DC24 额定功率:<100W电流控制范围大于等于80A小于500A电压控制范围16-35V焊接速度0-800mm/min,无线调速适用管径≥Φ168mm适用壁厚5-100mm外形尺寸(L*W*H)焊接小车275mm*172mm*220mm(二)YX-G168 轨道式全位置智能焊机(单炬)G168单炬外焊机是结合控制技术和焊接工艺技术的自动焊设备。
全位置药芯焊丝自保护焊厚壁钢管焊接试验

第1 5卷
第 4期
北京 石油化 工学 院学报
J u n lo ej g I siu eo o r a fB in n tt t f i
Peto c e ia c no o r — h m c lTe h l gy
Vo .1 NO 4 I 5 .
摘
要 为 了 解决 长输 管 道 安 装 工 程 中全 位 置 自动 化 焊 接 问 题 , 用 自行 研 制 的 全 位 置 焊 采
接 机 器 人 B P 3 采 用 自保 护 药 芯 焊 丝 对 管 径 为 4i 厚 为 6 T 的输 水 钢 管 进 行 了打 底 、 充 和 盖 I T一 , n壁 0ml l 填
8 N1 1 高熔 敷率 自保 护 药 芯焊 丝 , 丝 直径 q 焊 l 2
mm, 试验 焊 接 设 备 采 用 MP S一5 0平 特 性 焊 0 接 电源 , 速送丝 配恒压 源系统 , 等 北京石 油化工 学 院全 位 置 焊 接 机 器 人 B P 一33 , 前 预 IT _ l] 焊 。 热, 焊后 分 时降温 , 接 环境 温 度 为 3 焊 5℃ 。管 外壁 采用 向上焊 ; 内壁采用 向下 焊 。 管
位置实 时调 节焊接速 度 、 电弧电压 、 电弧长 度和 焊接 速度 等参 数 , 不断 摆动 电弧 和调 整焊 枪 并
笔者 采用采用 自行研 制 的全位置 焊接机 器
人, 对全 位 置药 芯 焊丝 自保 护 焊进 行 了试 验研
角度 , 以防 止全 位置 焊 接过程 中熔 滴下 淌 和未
中 圈 法 分类 号 T 4 . G4 4 2
长距 离 、 口径 管道 现场 焊 接 速度 一 直是 大 备 受关 注的 问题 。手工 焊接 向 自动 化焊接 发展 是 提高焊 接速度 的必 由之路 。 由于 自保护 药芯 焊 丝具有 熔敷速 度快 , 于实现 自动 化等特 点 , 易 成 为继 焊 条 、 实心 焊丝 之后 广 泛 应用 的 又一 类 焊 接材料口 。 自保 护焊丝 是在焊 接过程 中不 需 ] 要 外加保 护气或 焊剂 的一 类焊 丝 。其 突 出的特 点 是在 施 焊过 程 中具 有较 强 的抗 风 能力 , 别 特 适 合 于远 离 中心城 市 、 通运 输 困难 的野 外 安 交 装工 程 。 目前 , 国内大 型 管道 现 场 安装 工 程 的焊 接 主要 采 用 焊 条 电弧 焊 、 工 T G 焊 和 半 自动 手 I
X65钢管焊接工艺分析及质量控制

Electric Welding Machine·100·第51卷 第3期2021年3月Electric Welding MachineVol.51 No.3Mar. 2021本文参考文献引用格式:孙强,段英新,苏衍福,等. X65钢管焊接工艺分析及质量控制[J]. 电焊机,2021,51(3):100-102.X65钢管焊接工艺分析及质量控制0 前言 X65钢管海洋工程应用极为广泛,管道焊接技术不断发展、更新,但气体保护焊及手工焊仍然有不可替代的地位。
在海洋服役环境中对X65钢管要求更为苛刻,严格保证焊接质量的同时还要具备一定抗腐蚀能力。
下面将介绍对于X65钢管,相同管径壁厚及焊接标准下,通过对E81T1-NI1M、E8018-C3 H4R 二种牌号焊材试件进行检测,分析其焊接性并提出焊接质量控制要点。
1 焊接方法及焊接材料的选择 本工艺采用宝钢生产X65级别钢管,其化学成分和力学性能的实测结果见表1、表2。
考虑到生产效率、焊缝质量和设备的应用实际情况等因素,故选择手工焊条和药芯焊丝对钢管分别进行焊接。
X65作为低碳钢应选用与母材相匹配的焊接材料,为形成具有良好低温韧性的返修焊接接头,选用低氢型焊条及药芯焊丝,扩散氢含量<5 mL/100 g。
本研究选取以下2种牌号焊材:E81T1-NI1M (AWS A5.29)、E8018-C3 H4R (AWS A5.5)。
焊材金属的化学成分见表1。
焊接前采用密封包装状态,便于焊工收稿日期:2020-10-09作者简介:孙 强(1985—),男,学士,工程师,主要从事焊接设备及工艺的研究。
E-mail:****************。
操作施焊。
2 焊接工艺试验 试验管尺寸为φ610 mm×厚20.6 mm,采用30°坡口,组对坡口如图1所示。
焊件组对避免出现错边,焊前使用砂轮打磨清理坡口边缘15 mm 范围内的铁锈等杂质,直至露出金属光泽。
管道横焊的焊接方法
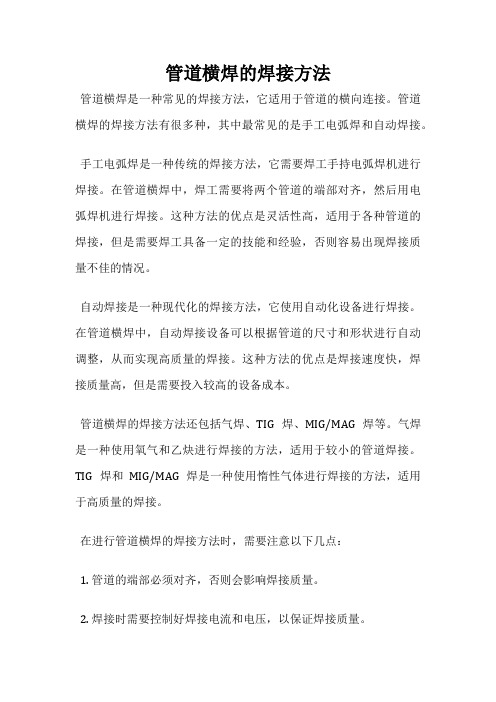
管道横焊的焊接方法
管道横焊是一种常见的焊接方法,它适用于管道的横向连接。
管道横焊的焊接方法有很多种,其中最常见的是手工电弧焊和自动焊接。
手工电弧焊是一种传统的焊接方法,它需要焊工手持电弧焊机进行焊接。
在管道横焊中,焊工需要将两个管道的端部对齐,然后用电弧焊机进行焊接。
这种方法的优点是灵活性高,适用于各种管道的焊接,但是需要焊工具备一定的技能和经验,否则容易出现焊接质量不佳的情况。
自动焊接是一种现代化的焊接方法,它使用自动化设备进行焊接。
在管道横焊中,自动焊接设备可以根据管道的尺寸和形状进行自动调整,从而实现高质量的焊接。
这种方法的优点是焊接速度快,焊接质量高,但是需要投入较高的设备成本。
管道横焊的焊接方法还包括气焊、TIG焊、MIG/MAG焊等。
气焊是一种使用氧气和乙炔进行焊接的方法,适用于较小的管道焊接。
TIG焊和MIG/MAG焊是一种使用惰性气体进行焊接的方法,适用于高质量的焊接。
在进行管道横焊的焊接方法时,需要注意以下几点:
1. 管道的端部必须对齐,否则会影响焊接质量。
2. 焊接时需要控制好焊接电流和电压,以保证焊接质量。
3. 焊接时需要注意安全,避免发生火灾和爆炸等事故。
管道横焊是一种常见的焊接方法,它适用于管道的横向连接。
在选择焊接方法时,需要根据管道的尺寸、形状和要求等因素进行选择,以保证焊接质量。
同时,在进行焊接时需要注意安全,避免发生事故。
电焊机(月刊)2020年第1~12期总目次

专题讨论:激光加工激光选区熔化成型SS316L不锈钢粉末演变机理路超,肖梦智,屈岳等(7-1)大型厚壁构件窄间隙激光焊接研究现状孙清洁,李军兆,刘一搏(7-9)焊接参数对不等厚钛合金角接结构激光诱导电弧焊接成形的影响吕晓辉,徐信坤,高健等(7-18)纯钛TA2薄板电弧辅助激光焊高速焊接过程的电弧和熔池特征行为研究周洋,孔谅,王敏等(7-24)光丝耦合及工艺参数对激光填丝熔覆层成形特征的影响玗伏文如,苏国兴,石等(7-30)基于激光直接沉积技术的增减材复合制造核用304L不锈钢接头性能研究赵建光,侯娟,熊孝经(7-39)模具磨损表面激光熔覆修复层的数值模拟技术刘立君,刘大宇,崔元彪等(7-46)核电用304不锈钢扫描激光微连接工艺研究梁晓梅,黄瑞生,刘金湘等(7-53)304不锈钢激光-MIG复合焊焊接电流对接头组织性能的影响宋世达,杨子威,钱美霞等(7-59)汽车车身激光焊接技术发展与应用韩立军(7-64)水下激光加工技术在核电维修领域的应用现状及发展王伟,王泽明,魏连峰等(7-74)27SiMn液压支架立柱的激光熔覆多道搭接工艺研究曹青,蔡志海,杜学芸等(7-80)稀土镁合金GW103K光纤激光焊接工艺研究及优化曹海涛,张鹏,杜云慧等(7-85)不同回火温度对不等厚钢板B340LA/B1500HS 激光焊接头组织性能的影响肖康,刘鹏,闫丰刚等(7-91)不锈钢车体激光叠焊电磁超声检测技术应用研究田勐,张勇,王丽萍等(7-96)核燃料防屑板的激光增材制造技术研究张丽英,秦国鹏(7-104)不锈钢轨道客车侧墙激光焊接与电阻点焊数值模拟对比研究王春生,王文权,王洪潇等(7-109)1060铝合金激光焊晶粒生长情况及其对接头力学性能的影响高启涵,金成(7-114)基于西门子PLC的激光焊接装备控制系统设计时云,赵凯,侍倩等(7-122)热丝激光熔覆技术在垃圾处理行业的应用方裕存,余宁,李振伟(7-127)大型复杂构件的无模型工业机器人自动编程系统侯润石,蒋启祥,王胜华等(7-134)Inconel690/321不锈钢异种金属焊接接头组织与性能研究黄卫东,伍建文,芦丽莉等(7-141)50卷400期“纪念专刊”开创我国焊接行业的新局面宋天虎(9-1)穴月刊雪2020年第1~12期总目次Co对多元碳化物复合熔覆层高温性能的影响龙伟民,刘大双,傅玉灿等(9-11)异种金属焊接接头微观组织演化及高温失效机理综述李克俭,李晓刚,张宇等(9-17)静止轴肩搅拌摩擦焊研究进展及展望褚强,郝思洁,Devang Sejani等(9-44)油气管道环焊缝焊接技术现状及发展趋势隋永莉(9-53)铝/钢旋转摩擦焊接头微观组织与腐蚀性能不均匀性研究李鹏,马超群,李艳光等(9-60)中厚板高效焊接技术的研究进展玗石,王文楷(9-69)层状双金属复合材料激光穿透焊工艺及质量控制研究与展望张小凡,张建勋(9-79)Q345R钢纵向磁场辅助K-TIG焊接接头组织和性能研究石永华,宁强,崔延鑫(9-87)海洋工程用焊接材料的研究现状及发展趋势邸新杰,巴凌志,利成宁(9-92)先进材料焊接现状及进展李亚江(9-103)水下湿法焊接研究进展叶建雄,彭显玲,李兵(9-111)异质材料连接研究进展钟素娟,张丽霞,龙伟民等(9-118)压力容器用国产化高端钢材和焊材焊接性研究概况房务农,蒋军(9-134)现代铁道车辆结构伤损形式与再制造修复技术周希孺,吴圣川,郭峰等(9-147)双相不锈钢堆焊层金属的空化腐蚀行为及影响因素研究进展王子睿,包晔峰(9-161)浅谈焊接科学与工程的创新创造王文先,闫志峰,董鹏等(9-170)镍钛形状记忆合金/钛合金异种材料焊接研究进展陈玉华,邓怀波,许明方等(9-177)逆变式电弧焊机的发展与展望王振民,江东航,吴健文等(9-186)核级主设备焊接技术探讨及展望罗英,郑浩,邱天等(9-194)电磁制造技术在航空航天领域的应用尹立孟,张丽萍,苏子龙等(9-202)影响钢结构焊接技术进步的几个重要因素戴为志(9-207)焊接工艺智能设计研究进展魏艳红,张玉莲(9-213)铝合金高能束焊接及其复合焊接的研究现状韩永全,孙振邦,杜茂华等(9-221)农机部件表面耐磨涂层的国内外研究现状武胜金,王星星,施进发等(9-232)焊接工程领域建模和数值模拟的不确定性问题杨建国,王赛,郑文健等(9-239)ZL114A电弧熔丝增材制造、热处理工艺及组织与性能研究郑涛,施瀚超,乔燕琦等(9-245)电弧增材再制造技术研究进展朱胜,杜文博(9-251)激光同轴送粉增材制造工艺调控研究孙军浩,庞小通,朱彦彦等(9-256)经济型含Nb X70管线钢双丝埋弧焊试验研究黄治军,邓照军,崔雷等(9-262)采用BNi82CrSiB钎料钎焊1Cr12Ni3MoVN不锈钢的接头组织及性能裴冲,吴欣,程耀永等(9-268)基于冶金反应的埋弧焊熔滴过渡形态表征孙咸(9-273)镍基钎料钎焊DD5单晶合金的接头组织和高温持久性能李思思,毛唯,陈波等(9-286)船舶高效焊接装备的研究———以江苏科技大学为例黎文航,于瑞,陈书锦等(9-291)重点关注大型金属构件增材制造技术在航空航天制造中的应用及其发展趋势朱忠良,赵凯,郭立杰等(1-1)6061铝合金与可伐合金钎焊接头残余应力分析张阳阳,胡子翔,王梅等(1-15)高强钢冷裂纹启裂位置判据与焊缝强度匹配的关系孙咸(1-21)激光离焦量对金属漆去除机理的影响玗朱映瑞,朱明,石等(1-29)电弧熔敷用高熵合金粉芯丝材熔敷层的摩擦磨损行为彭勇,雷卫宁,张扬等(1-34)碳纳米管/铝基复合材料阳极氧化与耐腐蚀性能申世军,钱小明,陈登海等(1-42)工业纯钛TA2双钨极氩弧焊焊接接头腐蚀性能研究周洋,孔谅,王敏等(1-47)Q345NQR2耐候钢薄板CMT焊接变形分析刘文杰,邢彦锋(1-51)铝合金与钢搅拌摩擦铆焊技术研究现状孙靖,陈艳,王旭琴等(1-57)基于结构光的角焊缝空间位置检测系统马泽润,蔡艳,孔谅等(2-1)CO2气体保护焊熔滴过渡与飞溅的关系孙咸(2-6)晶体管式电阻点焊电源及其复合模式控制研究钟磊,黄增好,杨凯等(2-14)钎焊中Au80Sn20共晶钎料与Ni/Au镀层的界面反应胡子翔,张阳阳,王梅等(2-19)基于集磁器的电磁脉冲点焊设计及实验吴铁洲,熊厚博,邓方雄(2-25)Cu核微焊点界面显微组织及拉伸力学性能研究江山,姚宗湘,左存果等(2-30)汽轮机12Cr/30Cr2Ni4MoV异质焊接转子接头组织与韧性研究吴海峰,李勃,熊建坤等(2-35)改善Sn-Bi系无铅钎料力学性能的研究进展闫丽静,黄永强,纪海涛等(2-41)超高速激光熔覆技术研究现状及其发展方向吴影,刘艳,陈文静等(3-1)核电CV厚板窄间隙摆动自动焊接工艺参数研究陈鹏,刘一搏,王亚峰等(3-11)超大尺寸3D打印成型钛合金叶片性能组织分析高骥天,李清松,张波等(3-18)全位置手工焊接线能量在线检测技术研究陈志远,傅强,朱雅琼等(3-25)逆变焊机的强迫风冷散热设计张守会,杨克柱,张光先等(3-28)增材制造TiAl合金的研究现状及展望王林,沈忱,张弛等(4-1)基于工程应用的HR3C奥氏体耐热钢焊接材料选用原则探讨孙咸(4-13)搅拌摩擦孔道加工技术发展及应用展望冯杏梅(4-24)304不锈钢激光K-TIG复合焊接电弧特性的研究李京洋,李伟,焦向东等(4-30)基于相关性对搅拌摩擦焊接头特征值的确定许飞,臧伟锋,张海英(4-36)车身铝板电阻点焊技术发展趋势与分析钟丽慧,韩立军,郭院波(6-1)不锈钢冷堆工艺对SA-508Gr.3Cl.1钢裂纹敏感性的影响分析张亚斌,罗英,杨敏等(6-10)电站锅炉奥氏体耐热钢管接头中的σ相孙咸(6-16)搅拌摩擦焊焊后高温振荡热处理组织及机理分析董丰波,封小松,罗传红等(6-26)6005A-5083铝合金焊接接头的微观组织与力学性能研究潘柏清,丁浩,刘雄等(6-30)半导体激光熔覆成形过程的特征行为检测与分析朱明,王博,颜步云等(8-1)基于铁研试验的耐热钢接头再热裂纹倾向探讨孙咸(8-7)焊接顺序对AH36船用高强钢焊接残余应力及其释放的影响研究沈言,李萌萌,张本顺等(8-15)KTIG焊接单面焊双面成型工艺及其在海洋工程装备制造领域的应用肖明颖,王琪晨,陈增铎等(8-22)B元素对Cr-Ni-Mo-Mn系药芯焊丝堆焊金属组织结构的影响裘荣鹏(8-27)Nb和N对Fe-Cr13-C堆焊层金属耐磨性能的影响冒志伟,杨可,李嘉琪等(8-31)基于视觉与重力传感的焊缝空间姿态检测技术研究与发展张天一,朱志明,郭吉昌等(11-1)LNG用低温高锰钢及其焊接技术发展郭伟,蔡艳,华学明(11-7)激光熔覆制备铝硅梯度材料孙泽阳,华鹏,李枘等(11-12)钎料对真空钎焊YG8/DC53接头微观组织的影响原靖,王娟,李亚江(11-16)690镍基合金焊条熔敷金属性能研究谷雨,张俊宝,黄逸峰等(12-1)基于熔池振荡的GTAW熔透实时传感与控制顾玉芬,席保龙,李春凯等(12-5)采用Ni中间层的5052铝合金/DP600车用钢电阻点焊研究李佳,陈地群,冉启洪等(12-9)ZL102铝合金搅拌摩擦焊焊缝成形及组织性能研究温雨,金玉花(12-14)电阻钎焊过程的动态电阻特征分析张昌青,荣琛,秦卓(12-18)焊接设备基于DSP的无桥PFC变换器研究朱才青,曹彪,钟磊等(1-63)智能焊接云管理系统开发及应用刘金龙,柳振国,李江等(2-45)基于单面焊双面成形的大型拼板焊接专机设计孟令涛(2-49)基于LabVIEW的双脉冲MIG焊系统研究炤李宜,陈克选,陈彦强等(3-32)水下螺柱焊枪的研制与应用薛延华,杜永鹏,朱小俊等(3-37)商用车国六后处理器机器人焊接生产线特点研究叶坤(3-41)基于DeviceNet总线的双钨极堆焊系统设计及工艺性验证袁亮文,刘万存,高永光等(4-41)基于ARM控制的脉冲MIG焊机研究炤李玉荣,陈克选,李宜等(4-47)钢管柱全位置自动焊接装置研究及应用邓宗生,张贝(4-52)基于准PR控制直流电焊机的研究黄小凡,林玉婷(4-57)一种基于数据统计的电阻点焊飞溅快速识别方法路向琨,徐昊,翟宝亮等(5-98)电阻点焊动态信号实时监测及焊接质量预测文静,贾洪德(5-102)水工钢结构双面坡口机器人焊接工艺蔡云秀,李斗,李飞(5-107)储罐倒装埋弧自动横焊机的改进研发刘恒毅(5-111)双丝双弧焊在中厚板焊接的应用罗强,甘跃,刘春明(5-114)长筒薄壁件纵缝焊接专机设计孟令涛(6-117)装载机油箱角焊缝焊接电弧跟踪技术的实践与应用张洪波,罗传孝(6-122)长距离无线传能系统最大效率点分析与验证黄小凡,李康文,戴睿鹏等(6-127)卡车车桥双机器人协调焊接模拟平台的设计与实现高党寻,姚启明,肖磊等(8-35)一种基于图像识别系统的焊瘤清理设备郭吉萍,吴鸣,胡锦扬等(8-39)基于dsPIC30F4011的CO2气保焊机设计李朋朋,杨志东,陈书锦等(10-78)双电源Plasma-MIG焊接系统的设计与实现王学远,杨学勤,成群林等(10-85)自由组装式焊接工位的创新设计与制作朵丛,黄新然,胡海莲(10-88)松下焊接机器人在组合件中的应用缪辉,王福林,钟俊林(10-92)横向磁脉冲MAG焊电弧旋转机理研究孙志星,路林,包正义等(10-97)基于多库支撑的轨道车辆车体焊接工艺智能系统的设计与实现于岩,王陆钊,侯震冬等(12-22)数据采集系统在焊接领域中的应用现状张磊,王博健,于静伟等(12-26)纳米晶铁心抗偏磁能力对逆变焊机的影响金晶,张双建,陈佳俊等(12-32)工业机器人焊接路径规划研究与应用徐达,陶长城(12-37)管道筒体对接环缝全自动焊接设备设计与应用周明远,李英伟,杨永家(12-43)焊接工艺复合阻隔镀层对钒合金与不锈钢电子束焊接头组织与性能的影响王亚荣,余洋,雷华东(1-67)ND钢高频焊管的应用可行性研究丛相州,彭杏娜,彭先宽等(1-71)A3钢薄板激光对接焊工艺研究杜洋,赵凯,时云等(1-75)7N01铝合金板材对接MIG焊接位置适应性研究范军,韩光旭,戴晓超等(1-79)6061-T6铝合金激光-MIG复合焊广域环境下疲劳性能研究毛镇东,韩晓辉,庞西南等(1-83)液压支架结构件常见缺欠国内外标准对比解析李福永,杨高,白海明(1-88)7075铝合金不同冷却介质条件下搅拌摩擦焊接头的组织与性能汪虎,韦叶,王巍等(1-92)400km/h高速列车轴箱体有限元仿真戴晓超,张英波,王泽飞等(1-97)返修工艺对6005-T6铝合金型材搅拌摩擦焊接头性能的影响徐海涛,李静,褚雪峰等(1-102)快捷货车转向架用Q345E钢板焊接接头疲劳性能研究魏世同,姜海昌,陆善平(1-105)牵引电机鼠笼式转子断条失效分析赵东超,谢贵生(1-109)铝合金导电管焊接缺陷及解决措施李博强,贾昕宇,谭茜茜等(1-114)GMAW工艺参数对倾斜位置的穿孔塞焊焊缝成形的影响研究修延飞,都婧婧,朱跃德等(1-117)镀铝锌板与不锈钢板电弧钎焊工艺研究张昕,巩金明,李霞等(1-121)铝合金熔丝增材制造表面平整度研究张弛,沈忱,李芳等(2-53)AZ31B镁合金的几种激光焊接特性研究方栩强(2-58)К65管道自动焊工艺研究及应用周文波,寇宝庆,苗广君(2-64)动车组车轴激光增材再制造工艺评定及分析侯有忠,李世亮,齐先胜等(2-69)山地管道焊接质量控制难点及应对措施王学军,刘铠(2-76)焊接工艺对高强度贝氏体钢激光-电弧复合焊接头组织和性能的影响毛镇东,韩晓辉,谢韶等(2-79)半牵引梁U型拐角焊缝连续自动焊接方法张继林,高德佳,胡文浩等(2-87)国内锚链、矿用链闪光对焊用电极铜合金现状孙爱俊,李学浩,朱仁萍(2-92)耐磨管件磨损数值仿真及优化方案杜占江,彭杏娜,丛相州等(2-96)Inconel600热电偶套管焊接的组织和性能研究杨子威,余进,洪浩源等(2-99)焊接温度对铜合金T型接头断裂失效影响分析曾美扬,李儒彬,汤芳等(2-103)Mn-N双相不锈钢堆焊熔覆层耐点蚀性能研究锜许伟康,包晔峰,谢秉等(3-49)特种焊接技术在核电汽轮机部件修复及再制造方面的应用陈兴东,郭洋,黄滔(3-53)装配式建筑用耐候钢的焊接热模拟潘进,信瑞山,安会龙等(3-60)12Cr2Mo1R钢制加氢反应器焊接裂纹原因分析及解决措施徐传华(3-65)7075铝合金不同冷却介质条件下搅拌摩擦焊接头的组织与性能汪虎,韦叶,王巍等(3-70)新型奥氏体耐热钢HR3C焊接工艺及接头性能研究进展张骏(3-75)超声相控阵技术在高速动车组转向架焊缝检测中的应用王丽萍,田勐,蔡瑞明等(3-80)双钨极不锈钢与低合金钢异种金属焊缝组织性能方迪生,高永光,刘万存等(3-86)钛板与不锈钢网片滚焊工艺优化研究于康,孙亚非,谢屹(3-92)能量密度对A7N01铝合金激光清洗表面形貌的影响陈辉刚,陈婧雯,陈辉(3-97)基于六西格玛方法的高温合金焊接工艺改进技术研究李扬,丁顺玉,许猛等(3-102)FPSO单点集成激光扫描数据与模型比对检验技术孙小磊(3-110)激光增材修复TC6钛合金工艺性能研究范朝,程宗辉,张志强等(3-115)卢塞尔体育场项目质量控制及关键工艺研究杜冰冰,王笛,阙子雄等(3-120)激光的加入对激光-MIG复合焊熔滴过渡的影响研究王秋影,邱培现,陈辉(3-126)J型坡口焊缝MAG焊工艺性研究梁姝博,董明(3-131)不同焊接位置铝合金接头的气孔敏感性分析张宗来,兰玲,陆雷俊等(3-133)实心焊丝堆焊奥氏体不锈钢堆焊工艺与性能史顺望,向锦,张磊等(3-137)水平固定复合管双金属环焊缝焊接工艺和应用研究穆学杰,孙宁松,曲海涛等(4-61)8mm厚TC4钛合金TIG、MIG焊接工艺及性能对比研究牟刚,华学明,徐小波等(4-70)基于大数据驱动的焊接接头力学性能预测张昭,白小溪,李健宇(4-75)基于双向流固耦合的铁路客车水箱冲击分析戴忠晨,闫海宁,刘建军等(4-79)铝合金焊接接头的设计特点吕同辉(4-85)电流对等离子堆焊WC p/Ni60复合层组织与性能的影响郭洋,陈兴东,黄岚等(4-89)Super304H奥氏体不锈钢晶间腐蚀敏感性研究陈浩,蒋奕锋,左敦桂等(4-95)电站锅炉低温再热器蛇形管冷弯断裂成因分析程东岳,金硕,孙旭东等(4-100)6082-T6铝合金等离子-CMT复合热源焊接特性研究赵函,辛志彬,杨志斌(4-103)不同热输入Q450NQR1钢焊接过热区组织、硬度和冲击韧性的研究黄显峰,赵娇玉,黄君辉等(4-107)A7N01S-T5铝合金激光-MIG复合焊接头低温韧性研究佘鹏,孙维光,马传平(4-110)基于有限元数值模拟的激光包覆焊焊接变形预测与控制孙强,方荣超,樊宇等(4-116)基于ANSYS的高硅铝合金平板对接激光焊数值模拟王鹏陆,何庆国(4-123)中部槽双面双弧打底焊工艺研究张彩霞(4-127)X70钢管自保护药芯焊丝全位置自动焊接接头组织与力学性能研究黄龙鹏(5-1)SAC0307/Cu电磁脉冲焊接接头的组织和性能研究苏子龙,徐永庚,高雷等(5-10)不同热处理对TC4/Ti60电子束焊接头微观组织及力学性能的影响喆王世清,邢博,赵启等(5-16)重熔焊对TC4钛合金接头气孔及力学性能的影响杨斯达,刘立安,赵舵等(5-21)SQ460FRW抗震耐蚀耐火钢气保焊焊接技术王垒,刘中华,张伟等(5-27)250km/h动车组头车底架有限元分析与优化设计何晓蕾,刘晨辉,宋巍等(5-31)低碳钢油管铜钎焊接头疲劳断裂分析孔德群,杨利,周建等(5-37)添加Mo-Ti-Zr填充层的钼镧钇合金电子束焊接特性分析蔡立辉,于斌,王廷等(5-41)基于随机森林的点蚀电位预测邢易,李树枝(5-45)301L不锈钢激光填丝焊接头腐蚀性能研究曹春鹏,吕卫群,单清群等(5-50)超厚爆炸复合板覆层裂纹分析韩玉改,刘宝剑,孙靖东等(5-54)锅炉水冷壁横向裂纹开裂原因分析董志红,蒙殿武,沈全宏等(5-57)汽车用双相钢板焊点组织性能的仿真优化袁成逸,李根,朱伟等(5-62)ENiCrMo-3等级镍基合金单层带极电渣堆焊工艺研究张兆林(5-67)BS960E高强钢激光-电弧复合高速焊接接头组织及性能研究李斌,朱勇辉,邓林等(5-72)自动切割及焊接技术在放射性阀门更换上的开发及应用郭召生,李杰,刘瑜(5-77)Q620钢药芯焊丝气体保护焊接头组织与性能的研究邢珂,李博文(5-84)不同打磨状态对6005A-T6铝合金MIG焊接头组织及力学性能的影响陈刚辉,张向钧,路伟(5-89)14Cr1MoR钢焊接工艺性研究及其在石油化工装置中的应用陈昌军,林立,王文涛(5-94)反应堆压力容器用低合金钢回火焊道工艺试验研究金亮,匡艳军,黄腾飞等(6-39)焊接热输入对25Cr35NiNb+微合金炉管焊接接头性能的影响任明皓,刘春娇,连晓明等(6-44)基于帧间匹配去噪的角接焊缝识别谢盛,魏昕,梁梓铭(6-48)某20CrNiMo部件等离子堆焊镍基硬质合金工艺研究陈兴东,郭洋,黄岚等(6-54)国际标准(ISO9606-1)焊工考试项目制定解析邵辉(6-60)某高温合金测压导管焊缝漏率超标分析史春山,郭大治(6-65)921A钢水下激光填丝焊接工艺研究瑄杜士,朱加雷,唐若晖等(6-69)重载车用BS960E高强贝氏体钢MAG焊接工艺研究江勇,冯仁锦,张成竹等(6-73)层间温度对核电用18MND5钢焊接接头冲击韧性影响的研究刘铁刚,吴义党,王德富等(6-79)铆接力对铝/钢自冲铆接头几何特性的影响李建军,侯平均,贺玉刚森等(6-84)S271低合金钢堆焊镍基合金稀释率影响因素研究黄卫东,柏忠炼,叶义海等(6-88)基于精益手法的石油钻机生产方案试点刘国荣,颜勇清,黄强等(6-93)电阻点焊熔核检测标准对比及分析王大臣,刘晓琴,逯连文等(6-96)直流双脉冲MIG焊对5A06铝合金焊缝组织和性能的影响黄浩,周洪刚,耿洋茉等(6-100)核岛钢衬里埋弧焊接头组织和性能研究黄清辉,项杰波(6-105)移动式压力容器罐体牵引支座肋板开裂修复黄道涛,鲁鹏,钟林志等(6-110)LNG储罐9%Ni钢立缝全自动焊技术韦宝成,杨尚玉,郭鹰(6-113)基于时间序列深度学习的超窄间隙焊接质量预测方法张爱华,魏浩,马晶等(8-43)焊接变形对核电厂控制棒驱动机构切割更换的影响及分析谭文良,朱德才,李全星等(8-48)钛合金高速列车转向架侧梁组成焊接工艺才鹤,李维哲,王泽飞等(8-52)焊剂带约束电弧超窄间隙横焊焊缝成形橦董敏,朱亮,韩潇等(8-57)B1800HS/DP1180电阻点焊接头组织研究凌华,孙浩,郭亚洲等(8-62)核电厂管道封闭式自熔焊的工艺研究吕旭伟,朱德才,谭文良等(8-67)大型结构模块现场拼装焊接变形控制刘非(8-71)6063-T5厚板搅拌摩擦焊接头层状撕裂缺陷研究邓清洪,游菲,吴勇(8-78)海洋平台TKY节点6GR位置焊接技术历超,孙志广,张彬等(8-83)低表面能修饰工艺对涂层接触角的影响研究刘楠,张相宁,杨桂英等(8-86)交流MIG焊接的电流换向维弧研究侯润石,吴勇健(8-91)非直线型厚壁大直径椭圆截面筒体对接环缝自动焊应用黄军(8-96)钛/钢异种金属激光焊接接头微观组织及数值模拟研究杨胜,李军兆,刘一搏等(8-101)提高中型驱动后桥壳焊接接头疲劳寿命的方法胡义华,柳明,黄志超等(8-106)LNG储罐9%Ni钢立缝SMAW焊接质量安全健康隐患韦宝成,杨尚玉,孙昕辉(8-110)工程机械液压缸焊接性能研究杨明轩,李跃华,刘丹(8-118)钛换热管与管板焊接接头电化学腐蚀性能研究崔巍,高磊,王东丽等(8-124)铜铝异种材料搅拌摩擦焊接头组织和力学性能分析徐萌,李文晓,徐晓霞等(10-1)小型承重立柱桁架结构设计及其焊接性能分析张苹,张潇然,张元彬(10-7)6061-T6铝合金电弧喷涂Ni-Al涂层结合强度性能研究王吉孝,王黎,马李等(10-14)大厚度沉淀硬化不锈钢双面焊接接头组织及性能演变张国军,陈凤,张贵一等(10-18)工艺参数对Mg-3Zn-0.5Y合金搅拌摩擦焊接接头组织与性能的影响吕建刚,陈曦,张磊(10-22)热处理对电弧增材制造316L不锈钢组织和性能的影响徐亮,杨可,王秋雨等(10-29)窄坡口等离子-MIG复合焊及焊接温度场的数值模拟田仁勇,吴向阳,张志毅等(10-35)厚板铝合金激光填碎丝焊接工艺研究胡广胜,单清群,曹春鹏(10-40)焊后热处理对P92钢焊接接头显微组织和力学性能的影响丁光柱,郭未昀,孙松涛等(10-44)单、双道焊缝熔合区的一次补焊对Q345E钢的焊接接头性能的影响李昌范,郝永魁,古典等(10-50)白车身四层板点焊工艺试验研究徐世龙,朱加雷,王伟峰等(10-57)国产镍基合金带极电渣堆焊在三相分离器制造中的应用研究王树涛,厚喜荣,马冬和等(10-61)SMA490BW耐候钢深熔焊工艺及接头的组织和性能吴向阳,田仁勇,张志毅等(10-65)Incoloy825Ω环对接的焊接工艺研究崔巍,高磊,张莹莹等(10-70)核电厂阀芯WCB钢钴基耐磨堆焊工艺研究徐宝坪,晋嘉昱,朱家泽(10-74)基于固有应变法的焊接残余应力数值模拟集成插件设计董昊,王博士,沐卫东等(11-23)管道环焊缝缺陷漏磁检测仿真模拟毛瑞麒,马梦想,饶连涛等(11-28)K465镍基铸造高温合金钎焊及其在修复中的应用李思思,静永娟,程耀永等(11-37)激光熔覆制备Al-70Si组织及性能研究王云龙,华鹏,李枘等(11-43)S355J2W+N耐候钢板根部大熔深MAG对接焊工艺及接头的组织和性能郭超超,丁成钢,杨大龙(11-50)焊接变形的三维扫描测量及热弹塑性有限元分析张腾,陈斌,许丹等(11-55)CRDM管座贯穿件密封焊工艺改进研究陈俊锋(11-58)U20Mn钢轨钢线性摩擦焊接头组织与力学性能研究郑霄,谭克利,戴虹(11-64)弯扭菱形箱型桁架制作工艺研究与应用程登,张发荣,李正等(11-71)双相不锈钢法兰侧焊缝热影响区裂纹和腐蚀问题分析郑倩倩(11-79)凝汽器管子管板封口焊问题分析及焊接工艺改进张斌(11-83)高酸性气田冶金复合汇管焊接制造技术周鑫(11-88)CPR1000主管道焊缝缺陷问题分析张进,吴伟帮,董义令(11-93)N800CF低碳贝氏体钢及其焊接接头腐蚀行为研究张志毅,汪认,崔云龙等(11-98)核电站控制棒导向筒组件半方管电子束焊缝熔深问题分析及改进运用汪为庆(11-104)核能行业焊评标准NB/T20002.3与NB/T 20450.3的比较分析和技术路线统一研究王宇欣,马迎兵,高宇等(11-109)基于KUKA弧焊机器人的燃料组件上管座焊接工作站钟建伟,盛国福,余国严等(11-115)马氏体不锈钢堆焊镍基合金工艺开发江国焱,何冰,刘远彬等(12-48)6082-T6铝合金填料搅拌摩擦焊工艺张欣盟,何广忠,王贝贝等(12-54)。
乌克兰国家科学院巴顿焊接研究所
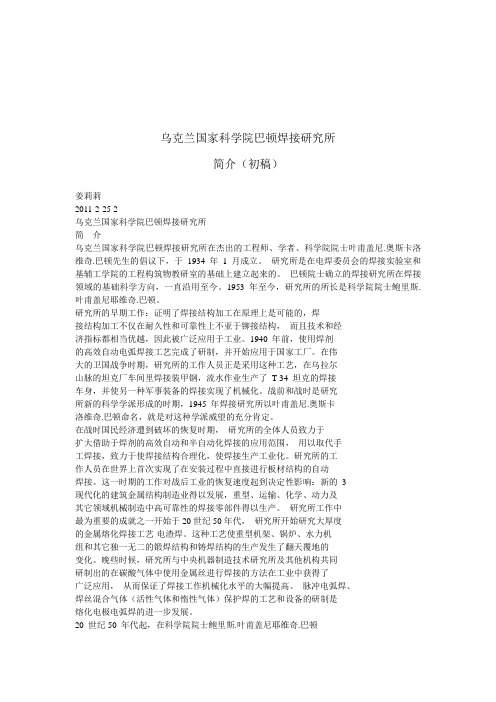
乌克兰国家科学院巴顿焊接研究所简介(初稿)姜莉莉2011-2-25 2乌克兰国家科学院巴顿焊接研究所简介乌克兰国家科学院巴顿焊接研究所在杰出的工程师、学者、科学院院士叶甫盖尼.奥斯卡洛维奇.巴顿先生的倡议下,于1934 年 1 月成立。
研究所是在电焊委员会的焊接实验室和基辅工学院的工程构筑物教研室的基础上建立起来的。
巴顿院士确立的焊接研究所在焊接领域的基础科学方向,一直沿用至今。
1953 年至今,研究所的所长是科学院院士鲍里斯.叶甫盖尼耶维奇.巴顿。
研究所的早期工作:证明了焊接结构加工在原理上是可能的,焊接结构加工不仅在耐久性和可靠性上不亚于铆接结构,而且技术和经济指标都相当优越,因此被广泛应用于工业。
1940 年前,使用焊剂的高效自动电弧焊接工艺完成了研制,并开始应用于国家工厂。
在伟大的卫国战争时期,研究所的工作人员正是采用这种工艺,在乌拉尔山脉的坦克厂车间里焊接装甲钢,流水作业生产了T-34 坦克的焊接车身,并使另一种军事装备的焊接实现了机械化。
战前和战时是研究所新的科学学派形成的时期,1945 年焊接研究所以叶甫盖尼.奥斯卡洛维奇.巴顿命名,就是对这种学派威望的充分肯定。
在战时国民经济遭到破坏的恢复时期,研究所的全体人员致力于扩大借助于焊剂的高效自动和半自动化焊接的应用范围,用以取代手工焊接,致力于使焊接结构合理化,使焊接生产工业化。
研究所的工作人员在世界上首次实现了在安装过程中直接进行板材结构的自动焊接。
这一时期的工作对战后工业的恢复速度起到决定性影响:新的3现代化的建筑金属结构制造业得以发展,重型、运输、化学、动力及其它领域机械制造中高可靠性的焊接零部件得以生产。
研究所工作中最为重要的成就之一开始于20世纪50年代,研究所开始研究大厚度的金属熔化焊接工艺-电渣焊。
这种工艺使重型机架、锅炉、水力机组和其它独一无二的锻焊结构和铸焊结构的生产发生了翻天覆地的变化。
晚些时候,研究所与中央机器制造技术研究所及其他机构共同研制出的在碳酸气体中使用金属丝进行焊接的方法在工业中获得了广泛应用,从而保证了焊接工作机械化水平的大幅提高。
海底管道铺设用全位置自动外焊机行走机构设计
套通 过 夹 紧环 与连杆 连接 。活塞杆 通过 弹 簧座
固装 在底 板 上 , 紧 力 由安 装 在 活 塞杆 上 的弹 锁
簧提 供 , 弹簧 座末 端安 装有 调整 螺母 , 以调 节 可
弹簧 的预紧力 。该 机构 采用 的弹簧 预紧 和偏 心
2 6
北 京石 油化工 学 院学报
21 0 0年 第 1 9卷
机构 配合 , 保证 驱动 齿轮 副 的 中心距 不 变 , 不 且
第 3 期
梅
梅等 .海 底管 道铺 设用 全 位置 自动 外焊 机行 走机 构设 计
2 5
承受 径 向 力 。 目前 主 要 的 锁 紧 机 构 有 如 下
几种 :
轮 结 构 , 仅 能解 决 由于磨 损 引 起 的焊 机 锁 不 不 死 问题 , 可 以实现 焊机 的快速 装 卡 , 辅 助操 还 使
缘 配合 承担 焊机 的重 量 , 驱 动焊机 运 行 。 并
固定夹紧轮 自动锁紧夹紧轮 轨道 驱 动齿 轮 固定夹 紧轮
使 压 紧轮 在滑 道 内左右 移 动 。4个 滚 轮 固定 安
装 在 焊 机 4个 角 上 与 轨道 外 缘 配合 , 两个 压 紧 轮 安 装 在 焊 机 中 间与 轨 道 两侧 的 内 楔 形 面 配 合 , 转 轨 道 两侧 丝 杆 使 两个 压 紧 轮 同 时 与轨 旋 道 配合 面压 紧 , 即可将 焊 机锁 紧在 轨道 上 , 调整 两 丝杆 还可 以调 节 焊 机 与 轨道 的相 对 位 置 E 。 3 ] 锁 紧力 由拧 紧丝 杆 的力提 供 , 有锁 紧 可靠 , 具 结 构 简单 , 寸小 等优 点 。但 是 安 装 过 程 中两 个 尺 压 紧轮需 要 协调 压紧 , 操作 过程 稍显 复杂 , 有 没 摩擦 补偿 功 能 。另外 锁 紧机构 和驱 动机 构 的配
焊接机器人
2021/1/27
精品课程
7
4.5.2 点焊机器人
第四章
金属连接成形设备及自动化
点焊机器人约占国内焊接机器人总数的45%左右,最常用的是直角坐标 式(2~4个自由度)和全关节式(5~6个自由度)点焊机器人。全关节式 机器人既有落地式安装,也有悬挂式安装,在驱动型式方面多采用直流或 交流伺服电机驱动。
③.焊接柔性自动生产线 为了适应现代产品更新换型快,生产的批量少、品种多 的特点,可按准时制造(Just-in-time manufacture,缩写为JIT)或无库存的生产 管理方式也可以说按订单生产,这时采用机器人柔性自动生产线是比较合适的。所 谓柔性自动生产线,即利用机器人可以储备多套程序,只要更换工件的夹具并调出相 应的程序就可以焊接另一种工件,因此在生产线上设置识别传感器,一旦新的工件 被识别,机器人的初始状态进入当前程序的执行。
2021/1/27
精品课程
5
4.5.1 概述
第四章
金属连接成形设备及自动化
图4-81 全关节型机器人
2021/1/27
精品课程
6
4.5.1 概述
第四章
金属连接成形设备及自动化
控制器是机器人的神经中枢,它由计算机硬件、软件和一些专用电
路构成。软件包括控制器系统软件、机器人专用语言、机器人运动学及动 力学软件、机器人自诊断及自保护功能软件等。控制器负责处理机器人工 作过程中的全部信息和控制其全部动作。
2021/1/27
精品课程
15
4.5.2 点焊机器人
第四章
金属连接成形设备及自动化
一体式焊钳的种类和选择 一体式焊钳有C型和X型两种,如图4-85所示为 常用的基本结构形式。
焊接时,根据工件形状,材料、工艺参数及焊点的位置来选用焊钳的形式, 电极直径、电极间的压紧力、两电极的最大开口度和焊钳的最大喉深等,一般来 说,垂直及近于垂直的焊点位选C型焊钳;水平及近于水平的焊点位选X型焊钳。
10-关于CRC全自动焊接质量缺陷成因的分析
关于CRC全自动焊接质量缺陷成因的分析摘要在国内外的管道施工实际中CRC全自动焊接工艺已经广泛的应用于长输管线的焊接施工中。
CRC 自动焊技术采用熔化极气体保护焊方法,借助于机械和电气原理使焊接过程实现全自动化和程序化操作。
CRC自动焊技术具有焊接效率高、劳动强度低、焊接过程受人为因素影响小等特点,在地势平坦、大口径、厚壁管道建设中优势明显。
在长输管线的安装过程中,CRC全自动气体保护焊接在施工速度越来越快的情况下,质量问题就成为了阻碍CRC全自动气体保护焊接的主要因素,如何做好自动焊质量的控制工作,要充分的分析质量缺陷问题产生的成因。
关键词CRC全自动气体保护焊接质量缺陷中亚C线质量成因分析1.焊接中出现的常见的气孔缺陷在中亚C线管道建设施工项目中,CRC全自动气体保护焊接取得了骄人的战绩和极高的质量合格率,这样所有参战员工的辛勤的努力是分不开的。
在CRC全自动气体保护焊接焊接实际中,容易出现的质量缺陷有一下几点。
1.1 焊接气孔出现的成因在CRC全自动气体保护焊接中容易出现气孔缺陷。
气孔在各种管道焊接工艺中相当常见,在在CRC全自动气体保护焊接中气孔的形成是由于溶解在金属中的气体货反应气态产物的析出所产生的气泡被凝固金属所包围而形成的。
其中各种气体在熔池金属中被氧化所形成的一氧化碳在此起到了主导的作用。
还有经常是因一中气体的析出所形成的气泡中气体气体也扩散进去,以加速它长大,从而形成多气孔。
1.2 CRC全自动气体保护焊接所使用的保护气体类型在CRC全自动气体保护焊接过程中,CRC全自动气体保护焊接设备主要有内对口器和内焊机组合系统,P260热焊机,和P600外焊机组成。
他实现了内部打根焊接到外焊填盖的全自动焊接。
其中CRC全自动气保焊采用1、根焊采用75%Ar+25%CO2的混合气体作保护,全部焊接在管子内部完成,自动化程度高,焊接速度快。
焊缝成形好,错边量小于3.5mm时,根焊质量不受影响。
海洋油气管道的焊接装备及技术研究
的西气东输二线工程 ,采用最高级别 的管线钢就是 X8 0最大
管 径 中1 1 m (8i 。 9m 4 n 2 1
求 高 , 现场施工风的影响较大 , 受 影响焊接质量 。我国在上世 纪9 O年代 , 功地 将 sT表 面张力焊运用 到国内的某管道工 成 r I r
高、 适应 性强等优点 , 但是 在追求 高效焊 接 的管 道施工 中 , 此 种焊 接工艺已经被逐渐淘汰 ,只在管 道维抢修和管道 连头时
应用 。
6. O 6mm( 4 ) 9 >2 ” 通常 采用 直缝 焊接钢 管 ( O 。钢 管 的制 U E) 造, 应按照美 国石油学会 的 A I pe5 P Se L的规范。规范 中包 含 的钢管钢级有 X 2 X 2 X 6 X 0X 0和 X8 4 、5 、 5、 6 、7 0等。目前 , 在美 国 、 国 、 国等工 业发达 国家 , 7 、 0级别 的高钢级管 材 德 韩 X 0X8 已经被 普遍 应用于海洋油气管道建设 中。我 国 目前正在建 设
( ) 自动焊。 自动焊根焊 主要是 C ! 2半 半 O 气体保护半 自动 焊, 属于下 向焊方法。 具有典型代表的是美 国林肯公 司 s T表 T 面张力焊 。 1 是一种 以表面张力溶 滴为过渡力 的熔化极 C : sT r O 气体保护 电弧焊 。s T表面张力焊非常适合管道 的根 焊 , T 具有 焊接速度快 、 背面成型好等优点。 S T对管 口的组对质量要 但 T
生 产 的 F E T L P ( WSA . 9 6 1 ) L E WE D5 + A 51 1 0 0 。 — E
焊接工艺及焊接设备 的应用 ,不仅提高 了管道施工 的经济效
益, 而且代表 了海洋油气管道建设 的科技水平 。
- 1、下载文档前请自行甄别文档内容的完整性,平台不提供额外的编辑、内容补充、找答案等附加服务。
- 2、"仅部分预览"的文档,不可在线预览部分如存在完整性等问题,可反馈申请退款(可完整预览的文档不适用该条件!)。
- 3、如文档侵犯您的权益,请联系客服反馈,我们会尽快为您处理(人工客服工作时间:9:00-18:30)。
Safety is the goal, prevention is the means, and achieving or realizing the goal of safety is the basic connotation of safety prevention.
(安全管理)
单位:___________________
姓名:___________________
日期:___________________
2021全位置管道自动焊接设备的
研究
2021全位置管道自动焊接设备的研究导语:做好准备和保护,以应付攻击或者避免受害,从而使被保护对象处于没有危险、不受侵害、不出现事故的安全状态。
显而易见,安全是目的,防范是手段,通过防范的手段达到或实现安全的目的,就是安全防范的基本内涵。
随着我国高科技产品的不断更新,全自动化设备受到人们的青睐。
日常生活中管道输送成为重要事项。
管道输送安全性能较高,同时能有效改善社会环境破坏问题。
因此管道在建设过程中焊接工艺起着重要组成部分,焊接技术直接影响着管道的使用寿命。
本文将对管道自动焊接设备进行研究。
我国管道在焊接过程中仍普遍出现手工焊接现象,直接影响管道使用的整体性能。
手工焊接需要较长工期,同时需要投入大量成本。
管道使用手工焊接直接影响管道的使用效率,而自动焊接不但能减少焊接工期,同时也对管道使用提供有效保护。
1.全位置管道自动焊接技术现状
1.1.自动焊接技术发展现状
全位置焊接主要将管道进行固定,运用机械与电气方法,使焊接设备有效带动焊枪进行焊缝环绕工作,实现全位置管道自动焊接技术。
目前我国全位置管道焊接工作存在一定难度,从而不能有效运用在管
道焊接工作中,其主要原因是由于直径厚壁压力管道难以到达环缝组装达到一致的精准度,因此需要全位置焊接设备自动调整焊枪位置,将坡口尺寸偏差进行自动调节。
焊接工作容易产生弧光、灰尘、振动等现象,因此自动调节跟踪无法达到理想要求。
美国已经成功研制出自动焊接设备,大量应用于石油天然气管道的建设中。
管道主要作用是将水流进行传输工作,因此有效控制管道缝隙衔接尤为重要,如出现偏差将产生严重影响,我国管道多数建设在地下,如出现破损将加大施工难度,需要工人长时间排查工作,因此管道焊接工作尤为重要。
焊接技术自动调节方面,我国相关部门研制出自动自动焊接工艺,并且建立在大量焊接工艺初期试验中,并且实际数据与试验数据存在一定数差现象。
这种现象不但降低管道自动焊接效果,同时加大管道焊接施工难度,为工作人员带来大量的工作难度。
其次我国自动焊接技术多数采用摆钟式原理,需要左右摆动进行交替工作,这种现象将提升数据偏差数值。
1.2.新研制管道自动焊接设备特点
针对我国管道自动焊接存在的问题,相关部门进行研究,研制出新型自动焊接设备,主要对管道环形位置进行细致检测,同时减少焊
枪存在的偏差问题,有效进行管道焊接工作。
近年来随着高科技技术的成熟,以及相关部门对焊接工艺的重视,自动技术已成为一种先进的焊接技术,并且成功运用在管道焊接工作中。
自适应焊接技术是一种高科技技术含量较高的焊接工艺,此技术配有高科技的传感器与电子检测线路,在管道焊接过程中能有效控制焊缝出现误差现象的发生,同时实施自动导航与跟踪系统。
管道焊接工作前期只需要将工艺参数进行预先设定,自动焊接设备将自动完成管道焊接工作,不但能减少大量人工作业,同时能有效提升管道使用寿命。
2.自动焊接设备的构成
2.1.自动焊接设备的重要组成部分
自动焊接设备的组建比较繁琐,零件之间需要紧密配合才能更好的完成焊接工作。
使用自动焊接的初期要保证其电源的稳定性,其输出功率与焊接设备进行结合,通过电源输出功率有效带动自动焊接设备的使用,并装有与主控器相接的接口。
自动焊接在设计过程中需要配备专业的自动调速系统,焊接工作属于细致工作,尤其体现在焊缝焊接中,对焊接面积较大的施工应采用快速焊接工艺,针对细小的工作能选用较慢的自动焊接技术,自动焊接调速系统能有效改善管道焊接的整体工艺,确保管道正常使用的同时降低成本开支。
焊接工艺的机械化与自动化是近代焊接技术的一项重要发展,它不仅能提升焊接生产效益同时也能保障焊接质量,而且大大的改善了生产劳动条件。
以往手工电焊是引燃电弧,送进焊条以维持一定的电弧长度,焊接工作中向前移动电弧,如采用机器完成焊接工作,则成为自动焊接。
自动焊接分为明弧与埋弧两种形式,焊接工作中如采用明弧焊接工艺,其生产效益将提升两倍左右,而使用埋弧工艺其生产效益将达到5-10倍。
埋弧主要是利用焊剂层下的电弧,通过加热并融化焊丝、焊剂与母材,而进行焊接工作的一种工艺手法,电弧在焊剂层下进行燃烧,自动焊机头将焊丝自动送入电弧区,确保使用电弧的长度,电弧通过焊机的有效控制,均匀向前移动,从而完成自动焊接作业。
2.2.自动焊接工艺的优点
自动焊接主要优点体现为生产效益高,自动焊接工艺在焊接工作中将使用较大电流,因此电弧整体穿透力较强,将管道缝隙进行有效融合,降低在使用过程中出现裂缝现象,由于埋弧焊的热量较为集中,并且焊接速度较快,因此生产效益与手工焊相比提升幅度较大。
自动焊接工艺能有效控制焊接工艺流程,通过自动化进行焊枪调整,保证其稳定性。
在自动焊接过程中焊剂的保护尤为重要,应防止空气对熔
池金属造成的侵害,埋弧焊焊缝金属质量较高,性能稳定,并且外表成形美观。
使用自动焊接工艺能有效降低材料与电能消耗,是由于电弧在焊剂层下燃烧,将热量散失较少,同时能有效较少电能的消耗,同时中薄板焊接时可以不开坡口,焊丝金属不存在飞溅损失,没有焊条头所以能节省大量焊接金属材料。
以往手工焊接工艺制作过程中,存在人工控制焊接过程的不准确、不稳定导致焊缝成形不好的现象,容易在焊接部位产生气孔、裂纹、未融合现象的发生。
自动焊接工艺在制造过程中,由于电弧燃烧程度稳定,连结处成份均匀,焊缝成型好的优点,因此被广泛的使用在焊接工作中。
自动焊接技术不但能提升生产质量,同时能大幅度的减少焊接工作量。
在我国全为管道建设中应充分利用自动焊接技术,确保管道使用寿命,为社会带来经济效益。
为了有效提升焊接工艺的生产质量,在工作中应全面使用自动系统,减轻工人的劳动强度。
XX设计有限公司
Your Name Design Co., Ltd.。