锻造对金属组织、性能的影响与锻件缺陷
浅谈锻造对金属组织和性能的影响
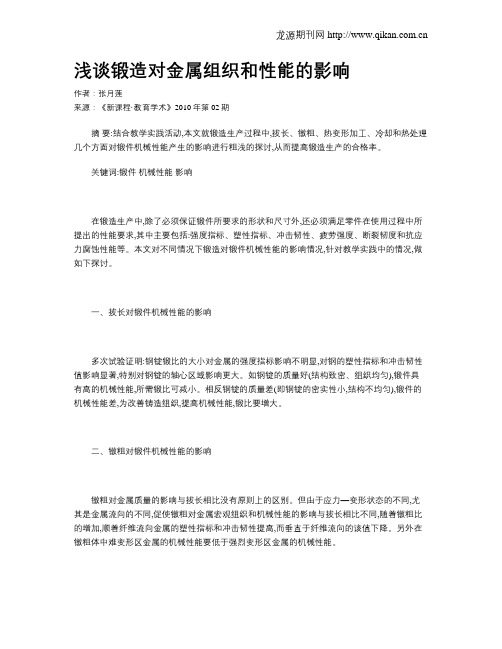
浅谈锻造对金属组织和性能的影响作者:张月莲来源:《新课程·教育学术》2010年第02期摘要:结合教学实践活动,本文就锻造生产过程中,拔长、镦粗、热变形加工、冷却和热处理几个方面对锻件机械性能产生的影响进行粗浅的探讨,从而提高锻造生产的合格率。
关键词:锻件机械性能影响在锻造生产中,除了必须保证锻件所要求的形状和尺寸外,还必须满足零件在使用过程中所提出的性能要求,其中主要包括:强度指标、塑性指标、冲击韧性、疲劳强度、断裂韧度和抗应力腐蚀性能等。
本文对不同情况下锻造对锻件机械性能的影响情况,针对教学实践中的情况,做如下探讨。
一、拔长对锻件机械性能的影响多次试验证明:钢锭锻比的大小对金属的强度指标影响不明显,对钢的塑性指标和冲击韧性值影响显著,特别对钢锭的轴心区域影响更大。
如钢锭的质量好(结构致密、组织均匀),锻件具有高的机械性能,所需锻比可减小。
相反钢锭的质量差(即钢锭的密实性小,结构不均匀),锻件的机械性能差,为改善铸造组织,提高机械性能,锻比要增大。
二、镦粗对锻件机械性能的影响镦粗对金属质量的影响与拔长相比没有原则上的区别。
但由于应力—变形状态的不同,尤其是金属流向的不同,促使镦粗对金属宏观组织和机械性能的影响与拔长相比不同,随着镦粗比的增加,顺着纤维流向金属的塑性指标和冲击韧性提高,而垂直于纤维流向的该值下降。
另外在镦粗体中难变形区金属的机械性能要低于强烈变形区金属的机械性能。
三、热变形加工对锻件机械性能的影响锻造用的原材料是铸锭,铸造组织的缺陷主要是:内部晶粒粗大且不均匀,组织疏松并有气泡、缩孔和微裂,化学成分偏析及非金属杂质分布不均匀等。
热变形加工能大大地改善铸造组织,使粗大柱状晶粒经塑性变形和再结晶后变成新的等轴细晶粒组织;疏松、空隙、微裂等缺陷在三向压应力状态下得到了压实或焊合;高熔点化合物被打碎并顺着金属变形方向呈碎粒状或链状分布,晶间低熔点杂质沿变形方向呈带状分布。
其结果使金属的塑性增加,机械性能得到提高。
锻件缺陷的主要特征及产生的原因

1锻造概述1.1锻造利用冲击力或静压力使加热后的坯料在锻压设备上、下砧之间产生塑性变形,以获得所需尺寸、形状和质量的锻件加工方法称为锻造。
常用的锻造方法为自由锻、模锻、胎模锻。
1.2自由锻利用冲击力或静压力使经过加热的金属在锻压设备的上、下砧间向四周自由流动产生塑性变形,获得所需锻件的加工方法称为自由锻。
自由锻分为手工锻造和机器锻造两种。
手工锻造只能生产小型锻件,机器锻造是自由锻。
1.3锻造特点1.3.1自由锻造所用工具和设备简单,通用性好,成本低。
同铸造毛坯相比,自由锻消除了缩孔、缩松、气孔等缺陷,使毛坯具有更高的力学性能。
锻件形状简单,操作灵活。
1.3.2锻件和铸件相比锻件的优点1.3.2.1金属经过锻造加工后能改善其组织结构和力学性能。
铸造组织经过锻造方法热加工变形后由于金属的变形和再结晶,使原来的粗大枝晶和柱状晶粒变为晶粒较细、大小均匀的等轴再结晶组织,使钢锭内原有的偏析、疏松、气孔、夹渣等压实和焊合,其组织变得更加紧密,提高了金属的塑性和力学性能。
1.3.2.2铸件的力学性能低于同材质的锻件力学性能。
此外,锻造加工能保证金属纤维组织的连续性,使锻件的纤维组织与锻件外形保持一致,金属流线完整,可保证零件具有良好的力学性能与长的使用寿命采用精密模锻、冷挤压、温挤压等工艺生产的锻件,都是铸件所无法比拟的。
1.3.2.3锻件是金属被施加压力,通过塑性变形塑造要求的形状或合适的压缩力的物件。
这种力量典型的通过使用铁锤或压力来实现。
铸件过程建造了精致的颗粒结构,并改进了金属的物理属性。
在零部件的现实使用中,一个正确的设计能使颗粒流在主压力的方向。
铸件是用各种铸造方法获得的金属成型物件,即把冶炼好的液态金属,用浇注、压射、吸入或其它浇铸方法注入预先准备好的铸型中,冷却后经落砂、清理和后处理等,所得到的具有一定形状,尺寸和性能的物件。
因此,它在重型机器及重要零件的制造上有特别重要的意义。
1.4应用领域自由锻造是靠人工操作来控制锻件的形状和尺寸的,所以锻件精度低,加工余量大,劳动强度大,生产率也不高,因此它主要应用于单件、小批量生产。
锻件的常见缺陷及原因分析
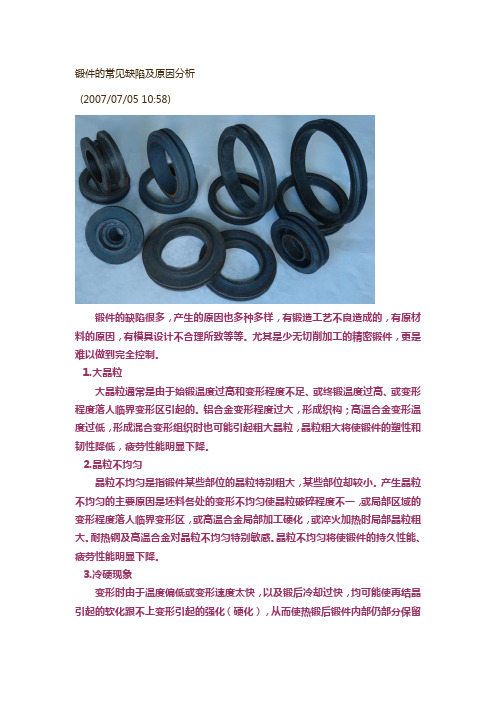
锻件的常见缺陷及原因分析(2007/07/05 10:58)锻件的缺陷很多,产生的原因也多种多样,有锻造工艺不良造成的,有原材料的原因,有模具设计不合理所致等等。
尤其是少无切削加工的精密锻件,更是难以做到完全控制。
1.大晶粒大晶粒通常是由于始锻温度过高和变形程度不足、或终锻温度过高、或变形程度落人临界变形区引起的。
铝合金变形程度过大,形成织构;高温合金变形温度过低,形成混合变形组织时也可能引起粗大晶粒,晶粒粗大将使锻件的塑性和韧性降低,疲劳性能明显下降。
2.晶粒不均匀晶粒不均匀是指锻件某些部位的晶粒特别粗大,某些部位却较小。
产生晶粒不均匀的主要原因是坯料各处的变形不均匀使晶粒破碎程度不一,或局部区域的变形程度落人临界变形区,或高温合金局部加工硬化,或淬火加热时局部晶粒粗大。
耐热钢及高温合金对晶粒不均匀特别敏感。
晶粒不均匀将使锻件的持久性能、疲劳性能明显下降。
3.冷硬现象变形时由于温度偏低或变形速度太快,以及锻后冷却过快,均可能使再结晶引起的软化跟不上变形引起的强化(硬化),从而使热锻后锻件内部仍部分保留冷变形组织。
这种组织的存在提高了锻件的强度和硬度,但降低了塑性和韧性。
严重的冷硬现象可能引起锻裂。
4.裂纹裂纹通常是锻造时存在较大的拉应力、切应力或附加拉应力引起的。
裂纹发生的部位通常是在坯料应力最大、厚度最薄的部位。
如果坯料表面和内部有微裂纹、或坯料内存在组织缺陷,或热加工温度不当使材料塑性降低,或变形速度过快、变形程度过大,超过材料允许的塑性指针等,则在镦粗、拔长、冲孔、扩孔、弯曲和挤压等工序中都可能产生裂纹。
5.龟裂龟裂是在锻件表面呈现较浅的龟状裂纹。
在锻件成形中受拉应力的表面(例如,未充满的凸出部分或受弯曲的部分)最容易产生这种缺陷。
引起龟裂的内因可能是多方面的:①原材料合Cu、Sn等易熔元素过多。
②高温长时间加热时,钢料表面有铜析出、表面晶粒粗大、脱碳、或经过多次加热的表面。
③燃料含硫量过高,有硫渗人钢料表面。
锻造常见缺陷有哪些,你都知道吗?

锻造用的原材料为铸锭、轧材、挤材及锻坯。
而轧材、挤材及锻坯分别是铸锭经轧制、挤压及锻造加工成的半成品。
一般情况下,铸锭的内部缺陷或表面缺陷的出现有时是不可避免的。
再加上在锻造过程中锻造工艺的不当,最终导致锻件中含有缺陷。
以下简单介绍一些锻件中常见的缺陷。
由于原材料的缺陷造成的锻件缺陷通常有:表面裂纹表面裂纹多发生在轧制棒材和锻制棒材上,一般呈直线形状,和轧制或锻造的主变形方向一致。
造成这种缺陷的原因很多,例如钢锭内的皮下气泡在轧制时一面沿变形方向伸长,一面暴露到表面上和向内部深处发展。
又如在轧制时,坯料的表面如被划伤,冷却时将造成应力集中,从而可能沿划痕开裂等等。
这种裂纹若在锻造前不去掉,锻造时便可能扩展引起锻件裂纹。
折叠折叠形成的原因是当金属坯料在轧制过程中,由于轧辊上的型槽定径不正确,或因型槽磨损面产生的毛刺在轧制时被卷入,形成和材料表面成一定倾角的折缝。
对钢材,折缝内有氧化铁夹杂,四周有脱碳。
折叠若在锻造前不去掉,可能引起锻件折叠或开裂。
结疤结疤是在轧材表面局部区域的一层可剥落的薄膜。
结疤的形成是由于浇铸时钢液飞溅而凝结在钢锭表面,轧制时被压成薄膜,贴附在轧材的表面,即为结疤。
锻后锻件经酸洗清理,薄膜将会剥落而成为锻件表面缺陷。
层状断口层状断口的特征是其断口或断面与折断了的石板、树皮很相似。
层状断口多发生在合金钢(铬镍钢、铬镍钨钢等),碳钢中也有发现。
这种缺陷的产生是由于钢中存在的非金属夹杂物、枝晶偏析以及气孔疏松等缺陷,在锻、轧过程中沿轧制方向被拉长,使钢材呈片层状。
如果杂质过多,锻造就有分层破裂的危险。
层状断口越严重,钢的塑性、韧性越差,尤其是横向力学性能很低,所以钢材如具有明显的层片状缺陷是不合格的。
亮线(亮区)亮线是在纵向断口上呈现结晶发亮的有反射能力的细条线,多数贯穿整个断口,大多数产生在轴心部分。
亮线主要是由于合金偏析造成的。
轻微的亮线对力学性能影响不大,严重的亮线将明显降低材料的塑性和韧性。
锻件缺陷

锻件缺陷(forging defects)锻造过程中锻件上产生的外在的和内在的质量不合要求的各种毛病。
锻件缺陷主要有:残留铸造组织,折叠,流线不顺,涡流,穿流,穿肋,裂纹,钛合金α脆化层和锻件过烧等。
残留铸造组织钢锻件有残留铸造组织时,横向低倍组织的心部呈暗灰色,无金属光泽,有网状结构,纵向无明显流线;高倍组织中的树枝晶完整,主干支干互成90。
高温合金的残留铸造组织,在低倍组织中为柱状晶,枝干未破碎;高倍组织中的晶粒极为粗大,局部有破碎的细小品粒。
钛合金低倍组织为粗大晶粒块状分布;高倍组织为粗大的魏氏组织。
铝合金横向低倍组织中的残留铸造组织为粗大的等轴晶,流线不明显,有时伴有疏松针孔;高倍组织中有网状组织、骨骼状组织和显微疏松。
残留铸造组织产生的原因是,铸锭加工成棒材或锻件的变形量小。
高温合金、铝合金及钛合金因反复锻造变形量不足或未采用多向锻造、两端面附近死区内的变形量小而引起的。
防止残留铸造组织要增大锻造比和反复镦拔,加强对原材料的检验,发现有铸造组织就要在成形工艺中增加补充变形量。
折叠表面形状和裂纹相似,多发生在锻件的内圆角和尖角处。
在横截面上高倍观察,折叠处两面有氧化、脱碳等特征;低倍组织上看出围绕折叠处纤维有一定的歪扭。
锻件上折叠的出现是由于自由锻拔长时,送进量过小和压下量过大,或砧块圆角半径太小;模锻时模槽凸圆角半径过小,制坯模槽、预锻模槽和终锻模槽配合不当,金属分配不合适,终锻时变形不均匀等原因造成金属回流而产生的。
根据上述产生的原因而采取相应的措施可以防止产生折叠。
流线不顺、涡流、穿流和穿肋这类缺陷多在锻件的H形、U形和L形部位的组织上出现。
坯料尺寸、形状不合适,锻造操作不当,模具设计时圆角半径选择不合理都会出现上述缺陷。
锻造变形时金属回流,工字形截面锻件,凸模圆角半径小金属不能沿肋壁连续填充模槽时都会产生涡流。
当肋已充满还有多余金属由圆角处直接流向毛边槽时,即形成穿流。
若锻造过程中打击过重、金属流动激烈、穿流处金属的变形程度和应力超过材料的许可强度时,便会产生穿流裂纹。
锻件的缺陷包括表面缺陷和内部缺陷

锻件的缺陷包括表面缺陷和内部缺陷锻件的缺陷包括表面缺陷和内部缺陷。
有的锻件缺陷会影响后续工序的加工质量,有的则严重影响锻件的性能,降低所制成品件的使用寿命,甚至危及安全。
因此,为提高锻件质量,避免锻件缺陷的产生,应采取相应的工艺锻件的缺陷包括表面缺陷和内部缺陷。
有的锻件缺陷会影响后续工序的加工质量,有的则严重影响锻件的性能,降低所制成品件的使用寿命,甚至危及安全。
因此,为提高锻件质量,避免锻件缺陷的产生,应采取相应的工艺对策,同时还应加强生产全过程的质量控制。
本章概要介绍三方面的问题:锻造对金属组织、性能的影响与锻件缺陷;锻件质量检验的内容和方法;锻件质量分析的一般过程。
(一)锻造对金属组织和性能的影响锻造生产中,除了必须保证锻件所要求的形状和尺寸外,还必须满足零件在使用过程中所提出的性能要求,其中主要包括:强度指针、塑性指针、冲击韧度、疲劳强度、断裂韧度和抗应力腐蚀性能等,对高温工作的零件,还有高温瞬时拉伸性能、持久性能、抗蠕变性能和热疲劳性能等。
锻造用的原材料是铸锭、轧材、挤材和锻坯。
而轧材、挤材和锻坯分别是铸锭经轧制、挤压及锻造加工后形成的半成品。
锻造生产中,采用合理的工艺和工艺参数,可以通过下列几方面来改善原材料的组织和性能:1)打碎柱状晶,改善宏观偏析,把铸态组织变为锻态组织,并在合适的温度和应力条件下,焊合内部孔隙,提高材料的致密度;2)铸锭经过锻造形成纤维组织,进一步通过轧制、挤压、模锻,使锻件得到合理的纤维方向分布;3)控制晶粒的大小和均匀度;4)改善第二相(例如:莱氏体钢中的合金碳化物)的分布;5)使组织得到形变强化或形变——相变强化等。
由于上述组织的改善,使锻件的塑性、冲击韧度、疲劳强度及持久性能等也随之得到了提高,然后通过零件的最后热处理就能得到零件所要求的硬度、强度和塑性等良好的综合性能。
但是,如果原材料的质量不良或所采用的锻造工艺不合理,则可能产生锻件缺陷,包括表面缺陷、内部缺陷或性能不合格等。
锻件的常见缺陷及原因分析
锻件的常见缺陷及原因分析(2007/07/05 10:58)锻件的缺陷很多,产生的原因也多种多样,有锻造工艺不良造成的,有原材料的原因,有模具设计不合理所致等等。
尤其是少无切削加工的精密锻件,更是难以做到完全控制。
1.大晶粒大晶粒通常是由于始锻温度过高和变形程度不足、或终锻温度过高、或变形程度落人临界变形区引起的。
铝合金变形程度过大,形成织构;高温合金变形温度过低,形成混合变形组织时也可能引起粗大晶粒,晶粒粗大将使锻件的塑性和韧性降低,疲劳性能明显下降。
2.晶粒不均匀晶粒不均匀是指锻件某些部位的晶粒特别粗大,某些部位却较小。
产生晶粒不均匀的主要原因是坯料各处的变形不均匀使晶粒破碎程度不一,或局部区域的变形程度落人临界变形区,或高温合金局部加工硬化,或淬火加热时局部晶粒粗大。
耐热钢及高温合金对晶粒不均匀特别敏感。
晶粒不均匀将使锻件的持久性能、疲劳性能明显下降。
3.冷硬现象变形时由于温度偏低或变形速度太快,以及锻后冷却过快,均可能使再结晶引起的软化跟不上变形引起的强化(硬化),从而使热锻后锻件内部仍部分保留冷变形组织。
这种组织的存在提高了锻件的强度和硬度,但降低了塑性和韧性。
严重的冷硬现象可能引起锻裂。
4.裂纹裂纹通常是锻造时存在较大的拉应力、切应力或附加拉应力引起的。
裂纹发生的部位通常是在坯料应力最大、厚度最薄的部位。
如果坯料表面和内部有微裂纹、或坯料内存在组织缺陷,或热加工温度不当使材料塑性降低,或变形速度过快、变形程度过大,超过材料允许的塑性指针等,则在镦粗、拔长、冲孔、扩孔、弯曲和挤压等工序中都可能产生裂纹。
5.龟裂龟裂是在锻件表面呈现较浅的龟状裂纹。
在锻件成形中受拉应力的表面(例如,未充满的凸出部分或受弯曲的部分)最容易产生这种缺陷。
引起龟裂的内因可能是多方面的:①原材料合Cu、Sn等易熔元素过多。
②高温长时间加热时,钢料表面有铜析出、表面晶粒粗大、脱碳、或经过多次加热的表面。
③燃料含硫量过高,有硫渗人钢料表面。
锻造的作用特点和注意事项
锻造的作用特点和注意事项锻造是一种利用锻压机械对金属坯料施加压力,使其产生塑性变形以取得具有必然机械性能、必然形状和尺寸锻件的加工方式,锻压(锻造与冲压)的两大组成部份之一。
通过锻造能排除金属在冶炼进程中产生的铸态疏松等缺点,优化微观组织结构,同时由于保留了完整的金属流线,锻件的机械性能一样优于一样材料的铸件。
相关机械中负载高、工作条件严峻的重要零件,除形状较简单的可用轧制的板材、型材或焊接件外,多采纳锻件。
锻造的作用利用金属的塑性对金属坯料施加外力,使其产生塑性变形、改变尺寸、形状及改善性能,用以制造机械零件、工件、工具或毛坯的成形加工方式确实是。
下面给大伙儿介绍锻造的作用1.细化晶粒:金属是由晶粒组成的,晶粒间靠晶界连结,晶界越多,金属结合的就越牢固。
金属经过锻造,粗大的铸造晶粒变为较细小的锻造晶粒,增加了晶界数量,金属的强度、硬度提高,也改善了金属的机械性能。
2.改变夹杂形态:金属内部的夹杂被视为裂纹源,影响了金属的机械性能和使用寿命。
通过锻造,能使颗粒状的夹杂变成条状或线状,减小内应力,减小其对金属机械性能的影响。
3.锻合内部缺陷:锻造能将金属内部的疏松压实,气孔锻合,提高金属的强度、硬度和韧性,延长金属的使用寿命。
4.消除偏析:钢锭的偏析使其各部性能不同,严重影响了金属的使用性能,通过锻造能将偏析部分或全部消除,减少偏析的区域,降低偏析对金属机械性能的影响。
5.改变金属纤维方向:锻造能使金属的纤维方向沿锻件形状分布,提高金属的强度、硬度和韧性。
锻造的种类和特点当温度超过300-400℃(钢的蓝脆区),达到700-800℃时,变形阻力将急剧减小,变形能也取得专门大改善。
依照在不同的温度区域进行的锻造,针对锻件质量和锻造工艺要求的不同,可分为冷锻、温锻、热锻三个成型温度区域。
本来这种温度区域的划分并无严格的界限,一样地讲,在有再结晶的温度区域的锻造叫热锻,不加热在室温下的锻造叫冷锻。
在低温锻造时,锻件的尺寸转变很小。
金属常见加工工艺缺陷的特征、原因、影响及措施
度下,金属再结晶退火加热温度过高或时间过长所致。晶粒粗大或粗细不均会导致在变形量较 大的部位产生裂纹,且裂纹多沿粗细混晶交界区择优分布。
三.由于材料成分、性能不合格
1.成分不合格 冷冲用钢板的化学成份应严格控,特别是碳、硫、磷元素极为重要。碳元素在钢中形成渗
2.带状组织 钢中带状组织是由铁素体和珠光体相间分布组成。它是由于碳、磷、硫晶间偏析,在热压
力加工中使之沿着金属变形方向被拉长,呈带状分布的夹杂物。 由于带状组织的取向平行于钢材轧制方向,而铁素体和珠光体的强度及塑性差异悬殊,因
此,冷冲时当钢件的变形方向与钢板带状组织相垂直,容易产生拉裂和撕裂。由于钢板带状组 织引起的冲裂,裂纹平行于钢板轧制方向,裂纹粗大,显微观察时裂纹多沿珠光体边缘分布、 取向平行于带状组织。
3.鳞片状毛刺
以较低或中等切削速度切削塑性金属时,加工表面往往会出现鳞片状毛刺,尤其对圆孔采 用拉削方法更易出现,若拉削出口毛刺没有去除,则将成为使用中应力集中的根源。
4.“R”加工过小
零件拐角半径小,尤其是横截面形状发生急骤的变化,会在局部发生应力集中而产生微裂 纹并扩展成疲劳裂纹,导致疲劳断裂。
3.涡流
金属在锻造过程中由于剧烈的热变形使金属组织发生晶粒结晶重新定向排列,形成结晶织 构和金属中的非金属夹杂物、树枝晶偏析、第二相质点等沿热加工方向形变延伸呈带状分布, 形成了锻件的纤维状组织即锻造流线。
产生的原因主要是表面氮浓度富集,化合物虽连续粗大网络状分布。在磨削时倾向于脱落 的氮化层的显微结构特点是沿奥氏体晶界存在稠密的网状氮化物,它的存在使晶格畸变加剧, 在位错与晶界处三向应力增大,在磨削力、热应力及组织应力的作用下,粗大的氮化物网络边 界区切口效应敏感性增大,造成综合应力叠加,当这种应力超过渗层的强度极限时,即产生脆 性破裂与剥落。当晶界强度大于晶内强度时,则裂纹沿晶扩展产生脆裂及剥落;当晶界强度等 于晶内强度时,则裂纹的扩展呈穿晶脆裂及剥落。
热锻件常见缺陷及防止方法
热锻件常见缺陷及防止方法发布时间:2022-06-20T08:48:50.332Z 来源:《福光技术》2022年13期作者:乔石[导读] 当我们思考所有用金属制造一个部件的方法时,锻造是重要部件获得高质量和性能的最好方法。
中国第一重型机械股份公司黑龙江省齐齐哈尔市 161042摘要:锻造成形技术广泛应用于航空航天、汽车、钢铁、装备制造、兵器、能源、造船等国民经济的各个重要领域。
锻造生产具有显著的优越性,它不但能获得金属零件的形状,而且能改善金属的内部组织,提高金属的力学性能和物理性能。
一般对于承力大的重要机械零件,大多需用锻造方法制造,锻件质量的优劣直接影响着零件的性能及使用寿命。
然而,锻造过程异常复杂,锻件质量与原材料质量、锻造工艺及锻后热处理工艺密切相关,为此,本文就坯料加热、锻造过程的不当处理可能导致的锻件缺陷进行了分析研究,并提出了具体的解决方案,对工程实践中锻件产品质量的保证与控制具有重要指导。
关键词:热锻件;常见缺陷;防止方法1.锻造工艺表面缺陷分析当我们思考所有用金属制造一个部件的方法时,锻造是重要部件获得高质量和性能的最好方法。
用锻件有时候比用其他件(如铸件,粉末金属件,焊接件)花费多些,但是如果设计者已持续体验到锻件产品的高可靠性的话,那么这些花费是值得的。
用商业的说法就是他“投入多也得到了更多”。
然而,有时候锻造工艺不正确致锻件使用中失效,顾客不仅对锻件供应商不满而且也对其选择锻造作为生产工艺感到怀疑。
当一种产品失效时,不仅失去了顾客对选择锻造作为下一个主要部件的制造方法的信心,也产生了对产品责任的忧虑。
有时候缺陷来源于初始材料但更多地是来自锻造工艺本身。
伴随着每种缺陷的描述给出了该种缺陷可能的解决方法。
在一些情况下,会有超过一种的起因。
对每种材料或锻造工艺都讨论了其选择,见表1。
表1表面缺陷、成因和解决方法2.锻造过程常见的缺陷、原因分析和防止方法2.1锻件充填不满金属没有完全充满模具型腔,造成锻件棱角、筋条等细小部位缺肉,使锻件轮廓不清。
- 1、下载文档前请自行甄别文档内容的完整性,平台不提供额外的编辑、内容补充、找答案等附加服务。
- 2、"仅部分预览"的文档,不可在线预览部分如存在完整性等问题,可反馈申请退款(可完整预览的文档不适用该条件!)。
- 3、如文档侵犯您的权益,请联系客服反馈,我们会尽快为您处理(人工客服工作时间:9:00-18:30)。
锻造对金属组织、性能的影响与锻件缺陷
锻件的缺陷包括表面缺陷和内部缺陷。
有的锻件缺陷会影响后续工序的加工质量,有的则严重影响锻件的性能,降低所制成品件的使用寿命,甚至危及安全。
因此,为提高锻件质量,避免锻件缺陷的产生,应采取相应的工艺对策,同时还应加强生产全过程的质量控制。
本章概要介绍三方面的问题:锻造对金属组织、性能的影响与锻件缺陷;锻件质量检验的内容和方法;锻件质量分析的一般过程。
(一)锻造对金属组织和性能的影响
锻造生产中,除了必须保证锻件所要求的形状和尺寸外,还必须满足零件在使用过程中所提出的性能要求,其中主要包括:强度指针、塑性指针、冲击韧度、疲劳强度、断裂韧度和抗应力腐蚀性能等,对高温工作的零件,还有高温瞬时拉伸性能、持久性能、抗蠕变性能和热疲劳性能等。
锻造用的原材料是铸锭、轧材、挤材和锻坯。
而轧材、挤材和锻坯分别是铸锭经轧制、挤压及锻造加工后形成的半成品。
锻造生产中,采用合理的工艺和工艺参数,可以通过下列几方面来改善原材料的组织和性能:
1)打碎柱状晶,改善宏观偏析,把铸态组织变为锻态组织,并在合适的温度和应力条件下,焊合内部孔隙,提高材料的致密度;
2)铸锭经过锻造形成纤维组织,进一步通过轧制、挤压、模锻,使锻件得到合理的纤维方向分布;
3)控制晶粒的大小和均匀度;
4)改善第二相(例如:莱氏体钢中的合金碳化物)的分布;
5)使组织得到形变强化或形变——相变强化等。
由于上述组织的改善,使锻件的塑性、冲击韧度、疲劳强度及持久性能等也随之得到了提高,然后通过零件的最后热处理就能得到零件所要求的硬度、强度和塑性等良好的综合性能。
但是,如果原材料的质量不良或所采用的锻造工艺不合理,则可能产生锻件缺陷,包括表面缺陷、内部缺陷或性能不合格等。
(二)原材料对锻件质量的影响
原材料的良好质量是保证锻件质量的先决条件,如原材料存在缺陷,将影响锻件的成形过程及锻件的最终质量。
如原材料的化学元素超出规定的范围或杂质元素含量过高,对锻件的成形和质量都会带来较大的影响,例如:S、B、Cu、Sn等元素易形成低熔点相,使锻件易出现热脆。
为了获得本质细晶粒钢,钢中残余铝含量需控制在一定范围内,例如Al酸0.02%~0.04%(质量分数)。
含量过少,起不到控制晶粒长大的作用,常易使锻件的本质晶粒度不合格;含铝量过多,压力加工时在形成纤维组织的条件下易形成木纹状断口、撕痕状断口等。
又如,在1Cr18Ni9Ti奥氏体不锈钢中,Ti、Si、Al、Mo的含量越多,则铁素体相越多,锻造时愈易形成带状裂纹,并使零件带有磁性。
如原材料内存在缩管残余、皮下起泡、严重碳化物偏析、粗大的非金属夹杂物(夹渣)等缺陷,锻造时易使锻件产生裂纹。
原材料内的树枝状晶、严重疏松、非金属夹杂物、白点、氧化膜、偏析带及异金属混人等缺陷,易引起锻件性能下降。
原材料的表面裂纹、折叠、结疤、粗晶环等易造成锻件的表面裂纹。
(三)锻造工艺过程对锻件质量的影响
锻造工艺过程一般由以下工序组成,即下料、加热、成形、锻后冷却、酸洗及锻后热处理。
锻造过程中如果工艺不当将可能产生一系列的锻件缺陷。
加热工艺包括装炉温度、加热温度、加热速度、保温时间、炉气成分等。
如果加热不当,例如加热温度过高和加热时间过长,将会引起脱碳、过热、过烧等缺陷。
对于断面尺寸大及导热性差、塑性低的坯料,若加热速度太快,保温时间太短,往往使温度分布不均匀,引起热应力,并使坯料发生开裂。
锻造成形工艺包括变形方式、变形程度、变形温度、变形速度、应力状态、工模具的情兄和润滑条件等,如果成形工艺不当,将可能引起粗大晶粒、晶粒不均、各种裂纹、折叠。
寒流、涡流、铸态组织残留等。
锻后冷却过程中,如果工艺不当可能引起冷却裂纹、白点、网状碳化物等。
(四)锻件组织对最终热处理后的组织和性能的影响
奥氏体和铁素体耐热不锈钢、高温合金、铝合金、镁合金等在加热和冷却过程中,没有同素异构转变的材料,以及一些铜合金和钛合金等,在锻造过程中产生的组织缺陷用热处理的办法不能改善。
在加热和冷却过程中有同素异构转变的材料,如结构钢和马氏体不锈钢等,由于锻造工艺不当引起的某些组织缺陷或原材料遗留的某些缺陷,对热处理后的锻件质量有很大影响。
现举例说明如下:
1)有些锻件的组织缺陷,在锻后热处理时可以得到改善,锻件最终热处理后仍可获得满意的组织和性能。
例如,在一般过热的结构钢锻件中的粗晶和魏氏组织,过共析钢和轴承钢由于冷却不当引起的轻微的网状碳化物等。
2)有些锻件的组织缺陷,用正常的热处理较难消除,需用高温正火、反复正火、低温分解、高温扩散退火等措施才能得到改善。
例如,低倍粗晶、9Cr18不锈钢的孪晶碳化物等。
3)有些锻件的组织缺陷,用一般热处理工艺不能消除,结果使最终热处理后的锻件性能下降,甚至不合格。
例如,严重的石状断口和棱面断口、过烧、不锈钢中的铁素体带、莱氏体高合金工具钢中的碳化物网和带等。
4)有些锻件的组织缺陷,在最终热处理时将会进一步发展,甚至引起开裂。
例如,合金结构钢锻件中的粗晶组织,如果锻后热处理时未得到改善,在碳、氮共渗和淬火后常引起马氏体针粗大和性能不合格;高速钢中的粗大带状碳化物,淬火时常引起开裂。
锻造过程中常见的缺陷及其产生原因在锻造过中常见的缺陷中将具体介绍。
应当指出,各种成形方法中的常见缺陷和各类材料锻件的主要缺陷都是有其规律的。
不同成形方法,由于其受力情况不同,应力应变特点不一样,因而可能产生的主要缺陷也是不一样的。
例如,坯料镦粗时的主要缺陷是侧表面产生纵向或45°方向的裂纹,锭料镦粗后上、下端常残留铸态组织等;矩形截面坯料拔长时的主要缺陷是表面的横向裂纹和角裂,内部的对角线裂纹和横向裂纹;开式模锻时的主要缺陷则是充不满、折叠和错移等。
各主要成形工序中常见的缺陷将在各主要成形工序中常见的缺陷与对策中详细介绍。
不同种类的材料,由于其成分、组织不同,在加热、锻造和冷却过程中,其组织变化和力学行为也不同,因而锻造工艺不当时,可能产生的缺陷也有其特殊
性。
例如,莱氏体高合金工具钢锻件的缺陷主要是碳化物颗粒粗大、分布不均匀和裂纹,高温合金锻件的缺陷主要是粗晶和裂纹;奥氏体不锈钢锻件的缺陷主要是晶间贫铬,抗晶间腐蚀能力下降,铁素体带状组织和裂纹等;铝合金锻件的缺陷主要是粗晶、折叠、涡流、穿流等。
各类材料锻件常见的缺陷将在各类金属材料锻件常见的缺陷与对策中详细介绍。
大型锻件的锻造和液态模锻涉及到较多的冶金问题,将在大型锻件常见的缺陷和对策和液态模锻件常见的缺陷与对策中介绍。