覆盖件冲压工艺设计实例
关于汽车覆盖件冲压工艺与实例分析
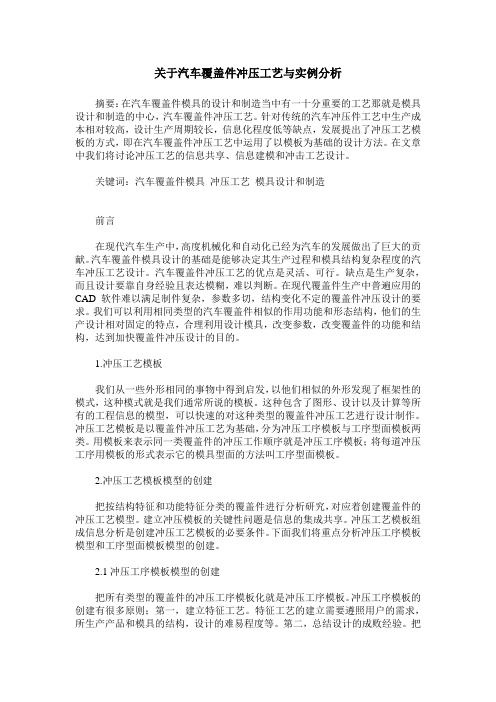
关于汽车覆盖件冲压工艺与实例分析摘要:在汽车覆盖件模具的设计和制造当中有一十分重要的工艺那就是模具设计和制造的中心,汽车覆盖件冲压工艺。
针对传统的汽车冲压件工艺中生产成本相对较高,设计生产周期较长,信息化程度低等缺点,发展提出了冲压工艺模板的方式,即在汽车覆盖件冲压工艺中运用了以模板为基础的设计方法。
在文章中我们将讨论冲压工艺的信息共享、信息建模和冲击工艺设计。
关键词:汽车覆盖件模具冲压工艺模具设计和制造前言在现代汽车生产中,高度机械化和自动化已经为汽车的发展做出了巨大的贡献。
汽车覆盖件模具设计的基础是能够决定其生产过程和模具结构复杂程度的汽车冲压工艺设计。
汽车覆盖件冲压工艺的优点是灵活、可行。
缺点是生产复杂,而且设计要靠自身经验且表达模糊,难以判断。
在现代覆盖件生产中普遍应用的CAD软件难以满足制件复杂,参数多切,结构变化不定的覆盖件冲压设计的要求。
我们可以利用相同类型的汽车覆盖件相似的作用功能和形态结构,他们的生产设计相对固定的特点,合理利用设计模具,改变参数,改变覆盖件的功能和结构,达到加快覆盖件冲压设计的目的。
1.冲压工艺模板我们从一些外形相同的事物中得到启发,以他们相似的外形发现了框架性的模式,这种模式就是我们通常所说的模板。
这种包含了图形、设计以及计算等所有的工程信息的模型,可以快速的对这种类型的覆盖件冲压工艺进行设计制作。
冲压工艺模板是以覆盖件冲压工艺为基础,分为冲压工序模板与工序型面模板两类。
用模板来表示同一类覆盖件的冲压工作顺序就是冲压工序模板;将每道冲压工序用模板的形式表示它的模具型面的方法叫工序型面模板。
2.冲压工艺模板模型的创建把按结构特征和功能特征分类的覆盖件进行分析研究,对应着创建覆盖件的冲压工艺模型。
建立冲压模板的关键性问题是信息的集成共享。
冲压工艺模板组成信息分析是创建冲压工艺模板的必要条件。
下面我们将重点分析冲压工序模板模型和工序型面模板模型的创建。
2.1冲压工序模板模型的创建把所有类型的覆盖件的冲压工序模板化就是冲压工序模板。
汽车车身覆盖件冲压工艺
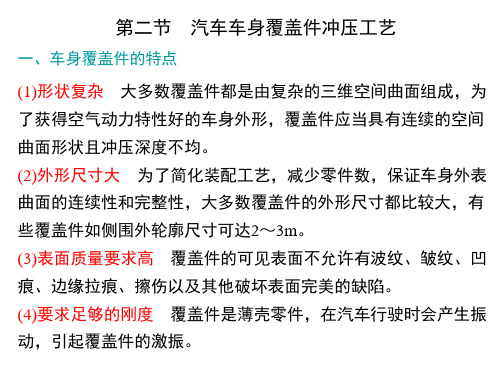
表10-13 大中型模具导向形式
2.双动拉深模的导向
(1)凸模与压料圈导向 凸模与压料圈导向的双动拉深模中,凹模与压料
圈之间一般不导向。 (2)压料圈与凹模导向
对于拉深断面形状复杂、模具型面极易产生侧向 力的双动拉深模,需采用凹模与压料圈导向方式。 (3)凸模、凹模与压料圈同时导向
目前国内外普遍采用压料圈与凸模、凹模都导向 的双动拉深模,保证运动精度。
=3~10mm,C=10~20mm e)修边线在拉深件的侧壁上,水平修边或倾 斜修边C≮12mm =4~10t,D=40~50mm
表10-9 工艺补充部分各部分的作用及尺寸
表10-9 工艺补充部分各部分的作用及尺寸
(四)压料面
(1)压料面的作用与对拉深成形的影响 压料面是指凹模上表面与压料圈下表面起压料作用的那一部
1)必须分布在工艺补充部分上,设置在修边线之外, 在修边冲孔时将它们冲掉,如图10-9所示。 2)工艺孔一般在拉深前的落料冲孔工序中完成。 3)切口或冲孔的数量、大小和形状,要根据所处位 置和变形的要求,保证各处材料变形均匀。 4)需要多个切口时,切口之间应有足够的搭边尺寸。
图10-9 工艺切口
(六)拉深筋
分表面,其位置在凹模圆角部分以外。 (2)压料面设计原则
如上所述,压料面有两种情况:一种是压料面的一部分就是 拉深件的法兰面;另一种情况是压料面全部属于工艺补充部分。
1)压料面形状应简单化,压料面最好呈水平方向。 2)压料面本身形状不能起皱。 3)压料面应降低成形深度,并且各部分深度应接近一致, 使板料不产生皱折、扭曲等现象。 4)压料面应使板料在拉深成形和修边工序中具有可靠的 定位,并考虑送料和取件的方便性,不在某一方向产生 很大的侧向力。
汽车覆盖件框前板冲压工艺设计

所 有 工 艺 补 充 面 补 齐 后 , 各补 充 面 边 线 ・ 眦 都 不 平 齐 ,用毛 坯 边 线 在z 向投 影 到 ‘ 艺 补 充 而 方 T
上 ,根据投影线剪裁边线不平齐的面 ,使得工艺补
充 面 尺寸 与 毛坯 尺 寸 大 小一 致 。建立 压 料 面 时 ,要
考虑该件属于外饰件 ,表面 质量的要求较高,所以
具 设 计 难 度 ,对 设 计 人 员 的 技 术 水 平 有 一 定 的要
求。
式中 F 一冲裁力 ( ; _ N)
L一~ 冲裁 周 边长 度 (q I ; nl ) T
卜
材 料 厚度 (11 /I 1 ); /
方 案 ③是 将拉 深 成 形 与 ? ̄ 合 成 一 道 工序 ,虽 eL o 然也 比方 案 ①少 一 道 工序 ,但是 拉 深 与 冲孔 一 起 ,
大 型 件 的大 批 量生 产 ,利 于 流水 线 生 产 。 方 案 ②采 用 复 合 模把 冲 孔 切 边 合成 一 道 工 序来 做 ,冲 孔 是 分 离 零 件 与 内 部 废 料 ,在 工 件 内 部 进 行 ,修 边 是分 离 零 件 与外 部 废料 ,在 工 件外 轮 廓进 行 ,所 以 冲孔 、修边 可以 同 时进 行 。这 样 提 高 了生
形 。③下 料 一 成形 冲 孔 一切边 一整 形 。
方案①把拉深成形、i  ̄ 、切边及整形分开 , eL p 其缺点是需要多做一套模具 ,在生产过程 中多了一 道工序 ,效率会降低 ,模具成本也增加 。但模具都 是单工序模 ,降低了模具的设计难度 ,且这种设计 通用性好 ,特别适用于小型件中、小批量的生产和
等 )的方案选定 ,更关 系到是否能 拉出合格 的零 件 。因此,冲压方 向的确定是汽车钣金件工艺设计 的 关键一步 ,可以确定拉 深件在 模具 中的 空间位 置 。零件在拉深模 中应如 图1 所示放 置,分析零件
覆盖件冲压工艺设计实例

覆盖件冲压工艺设计实例引言覆盖件是一种常见的零部件,广泛应用于汽车、家电、机械设备等领域。
冲压工艺是制造覆盖件的常用方法之一。
本文将以汽车发动机盖板的制造过程为例,介绍覆盖件冲压工艺的设计过程。
1. 覆盖件冲压工艺概述覆盖件冲压工艺是指利用冲压设备将平面板材通过模具冲压成具有特定形状的工件的加工方法。
它具有高效、精度高、成本低等优点,因此被广泛应用于工业生产中。
2. 设计要求分析汽车发动机盖板是一种对外形精度要求较高的覆盖件。
在进行冲压工艺设计之前,首先需要对其设计要求进行分析。
设计要求主要包括以下几个方面:2.1 材料选择发动机盖板通常使用钢板作为材料。
在选择材料时,需要考虑力学性能、耐腐蚀性能、强度要求等因素。
2.2 外形尺寸外形尺寸是冲压工艺设计的基础。
对发动机盖板而言,外形尺寸要满足设计要求,并且具有一定的公差要求。
2.3 表面质量要求发动机盖板的外观质量要求较高,需要保证表面光洁度、平整度以及无划痕、凹陷等缺陷。
3. 工艺流程设计在完成设计要求分析后,接下来需要确定发动机盖板的工艺流程。
工艺流程包括以下几个步骤:3.1 材料准备首先需要对钢板进行切割,将其切割成合适尺寸的方坯。
3.2 模具设计根据发动机盖板的形状和外形尺寸要求,设计合适的冲压模具。
模具设计需要考虑模具结构、导向方式、模具材料等因素。
3.3 冲裁冲裁是冲压过程的第一步,通过冲剪刀将方坯切割成与发动机盖板一样外形的小块。
3.4 冲压成形冲压成形是整个工艺的关键步骤,通过将冲裁得到的小块放入冲压机的模具中,并施加适当的压力将其冲压成发动机盖板的形状。
3.5 补强处理为了增加发动机盖板的强度和刚性,还需要进行补强处理。
可以通过冲压孔、折弯等方式进行补强。
3.6 表面处理最后,对发动机盖板的表面进行处理,通常是进行喷涂或镀锌等表面保护处理。
4. 工艺参数确定在工艺流程设计确定后,还需要确定合适的工艺参数。
工艺参数是指影响冲压工艺结果的各种参数,如冲压力、冲压速度、模具间隙等。
汽车覆盖件成开工艺及模具设计方案

3
6.1.2覆盖件的成形特点
1.成形工序多:拉深为关键工序; 2.拉深是复合成形 :常采用一次拉深; 3.拉深时变形不均匀:工艺补充、拉深筋; 4.大而稳定的压边力:双动压床; 5.高强度、高质量、抗腐蚀的钢板; 6. 覆盖件图样和主模型为依据。
4
6.1.3覆盖件的成形分类
汽车覆盖件的冲压成形分类以零件上易破裂或起皱 部位材料的主要变形方式为依据,并根据成形零件的外形 特征、变形量大小、变形特点以及对材料性能的不同要求
13
图6.1.5 拉深深度与拉深方向
14
a)
b)
c)
d)
图 6.1.6 凸模开始拉深时与拉深毛坯的接触状态示意图
15
2.修边方向的确定及修边形式 (1)修边方向的确定 所谓修边就是将拉深件修边线以外的部分切掉。 理想的修边方向: 是修边刃口的运动方向和修边表面垂直。 (2)修边形式
修边形式可分为垂直修边、水平修边和倾斜修边三种,
③当拉深件的法兰面为复杂曲面形状时,还可以在法 兰面上标注上凸、凹模和压料圈型面按工艺模型仿制、配 研的技术要求。
29
6.2.3 拉深、修边和翻边工序间的关系
覆盖件成形各工序间不是相互独立而是相互关联的, 在确定覆盖件冲压方向和加工艺补充部分时,还要考虑修 边、翻边时工序件的定位和各工序件的其它相互关系等问 题。
致局部大的胀形变形而开裂。 位置: 开裂主要发生在圆角部位,开裂部位的厚度变薄很大如
凸模与坯料的接触面积过小、拉深阻力过大等都有可能导致 材料局部胀形变形过大而开裂 。
防裂措施: 为了防止开裂,应从覆盖件的结构、成形工艺以及模具设 计多方面采取相应的措施。
8
(1) 覆盖件的结构上,可采取的措施有: 各圆角半径最好大一些、曲面形状在拉深方向的实际深度 应浅一些、各处深度均匀一些、形状尽量简单且变化尽量平缓 一些等。 (2)拉深工艺方面,可采取的主要措施有: 拉深方向尽量使凸模与坯料的接触面积大、合理的压料面 形状和压边力使压料面各部位阻力均匀适度、降低拉延深度、 开工艺孔和工艺切口等 (如图6.1.3)。 (3)模具设计上 可采取设计合理的拉深筋、采用较大的模具圆角、使凸模 与凹模间隙合理等措施。
汽车覆盖件冲压工艺优化设计实例
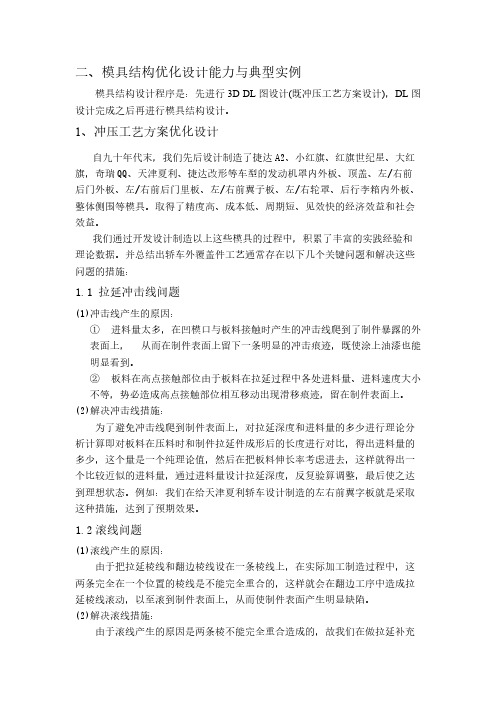
二、模具结构优化设计能力与典型实例模具结构设计程序是:先进行3D DL图设计(既冲压工艺方案设计),DL图设计完成之后再进行模具结构设计。
1、冲压工艺方案优化设计自九十年代末,我们先后设计制造了捷达A2、小红旗、红旗世纪星、大红旗,奇瑞QQ、天津夏利、捷达改形等车型的发动机罩内外板、顶盖、左/右前后门外板、左/右前后门里板、左/右前翼子板、左/右轮罩、后行李箱内外板、整体侧围等模具。
取得了精度高、成本低、周期短、见效快的经济效益和社会效益。
我们通过开发设计制造以上这些模具的过程中,积累了丰富的实践经验和理论数据。
并总结出轿车外覆盖件工艺通常存在以下几个关键问题和解决这些问题的措施:1.1 拉延冲击线问题(1)冲击线产生的原因:①进料量太多,在凹模口与板料接触时产生的冲击线爬到了制件暴露的外表面上,从而在制件表面上留下一条明显的冲击痕迹,既使涂上油漆也能明显看到。
②板料在高点接触部位由于板料在拉延过程中各处进料量、进料速度大小不等,势必造成高点接触部位相互移动出现滑移痕迹,留在制件表面上。
(2)解决冲击线措施:为了避免冲击线爬到制件表面上,对拉延深度和进料量的多少进行理论分析计算即对板料在压料时和制件拉延件成形后的长度进行对比,得出进料量的多少,这个量是一个纯理论值,然后在把板料伸长率考虑进去,这样就得出一个比较近似的进料量,通过进料量设计拉延深度,反复验算调整,最后使之达到理想状态。
例如:我们在给天津夏利轿车设计制造的左右前翼字板就是采取这种措施,达到了预期效果。
1.2滚线问题(1)滚线产生的原因:由于把拉延棱线和翻边棱线设在一条棱线上,在实际加工制造过程中,这两条完全在一个位置的棱线是不能完全重合的,这样就会在翻边工序中造成拉延棱线滚动,以至滚到制件表面上,从而使制件表面产生明显缺陷。
(2)解决滚线措施:由于滚线产生的原因是两条棱不能完全重合造成的,故我们在做拉延补充设计时,采取轮廓过拉延,即拉延件的轮廓线不一定是产品的翻边线(主要取决于是否是覆盖件以及翻边处的园角半径R的大小)。
汽车覆盖件冲压成形工艺性方案
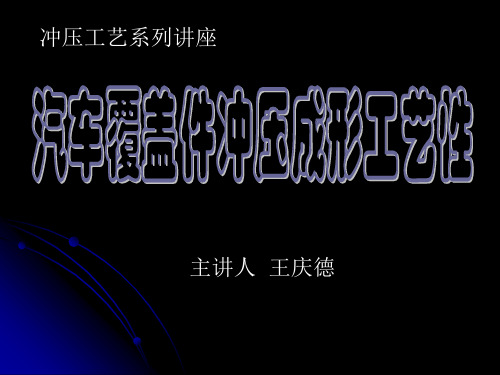
冲压技术 覆盖件 工艺性
10
14、关于设计基准问题:拉延件的设计基准 主要是要考虑比较大的面的法向作为拉延 方向,以该面作为设计基准来保证基本拉 延边都具有5~15度的拔模角。
冲压技术 覆盖件 工艺性
11
冲压方向问题
此件属深拉延
件,这里的高 度发生突变, 多面交汇点一 定要做大的球 面处理以防拉 裂。
冲压技术 覆盖件 工艺性
37
皱折状态的分类
按引起起皱的外力分类
当外力在板料平面内引起的压应力使板厚方向达到失稳极限时便产
生了失稳起皱,皱纹的走向与压应力垂直。
引起压应力的外力大致可以分为四种情况:即压缩力、剪切力、不均
匀拉伸力、板料平面内弯曲力。
压应力引起的失稳起皱
拉延时法兰变形区的起皱,曲面零件成形时悬空部分的起皱即属此类
冲压技术 覆盖件 工艺性
31
4、样车阶段
验证零件的冲压可行性、分析零件尺寸精
度的影响因素;
及时发现、解决新出现的冲压问题; 分析冲压件对焊接、装配、涂装的影响,
提出解决方案;
分析冲压件的刚度、强度对物流的影响; 验证前期SE提出的问题,以便经验反馈;
冲压技术 覆盖件 工艺性
32
汽车覆盖件冲压成形常见的质量问题
断裂 皱折 曲面\形状精度不良
冲压技术 覆盖件 工艺性
33
断裂状态的分类
按断裂的性质分
因为材料的强度不够而产生的断裂,大多都发生在传力区,称为强度断
裂(或α断裂).
因为材料的塑性不足而产生的断裂,大多都发生在变形区,称为塑性断
裂(或β断裂).
按断裂发生的区域分
冲压技术 覆盖件 工艺性
第2章汽车覆盖件冲压工艺设计
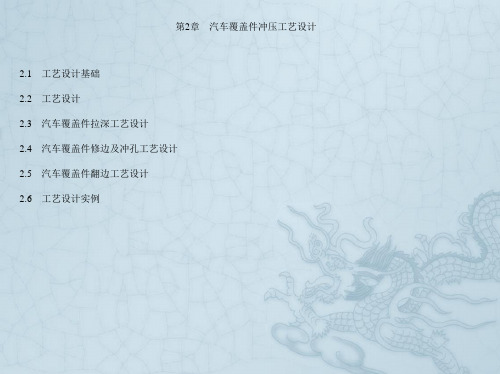
2.3 汽车覆盖件拉深工艺设计
6)当覆盖件的底部有反成形形状时,压料面必须高于反成形形状的最高点(图2-11)。 7)不在某一方向产生很大的侧向力。
2.3.4 工艺补充部分的设计
图2-11 底部有反成形形状时的压料面
2.3 汽车覆盖件拉深工艺设计 工艺补充是指为了顺利拉深成形出合格的制件,在冲压件的基础上添加的那部分材料。由于这部分材料是 成形需要而不是零件需要,故在拉深成形后的修边工序中要将工艺补充部分切除掉。工艺补充是拉深件设 计的主要内容,不仅对拉深成形起着重要影响,而且对后面的修边、整形、翻边等工序的方案设计也有影 响。 1.工艺补充的作用与对拉深成形的影响
2.2 工艺设计
当月产量大于10000件(货车)或30000件(轿车),且小于100000件时,属于大批量生产。其特点是生产处于长 期稳定状态,工件形状改变的可能性小;工艺难易程度为困难。工艺方案要为流水线生产提供保证,每道 工序都要使用冲模,拉深、修边冲孔和翻边模同时安装在一条冲压线上。至于工序间的流转,20世纪50年 代基本是人工送料和取件,工业化国家实现机械化和自动化,60年代以后开始进入全自动化时期。多工位 压力机的出现,更加提高了生产效率和工件质量。
2.3 汽车覆盖件拉深工艺设计
2.3.1 拉深工艺特点 与简单零件相比,汽车覆盖件的拉深工艺特点有: 1)简单零件(形状对称、深度均匀)可用拉深系数研究拉深次数和工序尺寸;汽车覆盖件大多由复杂的空间曲 面组成,成形时坯料各部分的变形状态差别很大,而且甚为复杂,各处应力也很不均匀。 2)通常,简单零件的压边面积比其余部分面积大,只要压边力调节合适,便能防止起皱。
2.3 汽车覆盖件拉深工艺设计 拉深成形过程中的材料流动和塑性变形就越难控制。
图2-14 工艺补充简化拉深件结构形状的实例
- 1、下载文档前请自行甄别文档内容的完整性,平台不提供额外的编辑、内容补充、找答案等附加服务。
- 2、"仅部分预览"的文档,不可在线预览部分如存在完整性等问题,可反馈申请退款(可完整预览的文档不适用该条件!)。
- 3、如文档侵犯您的权益,请联系客服反馈,我们会尽快为您处理(人工客服工作时间:9:00-18:30)。
覆盖件冲压工艺设计1.工艺设计前的准备工作 (3)2.零件的前碰撞梁工艺分析和设计 (4)2.1. 零件工艺分析 (4)2.2. 1/4拉延件工艺分析与设计 (5)2.2.1. 确定零件的冲压方向 (5)2.2.2. 零件的压料面和分模线 (6)2.2.3. 拉延件合理的工艺补充 (8)2.2.4. 拉延筋的正确合理设计 (17)2.3. 2/3,3/3修边+冲孔工艺设计 (19)2.3.1. 修边工艺分析和设计 (19)2.3.2. 废料刀设计 (20)2.3.3. 修边工艺造型 (24)3.零件前风窗下横梁上板工艺分析和设计 (27)3.1. 1/4拉延件工艺分析与设计 (28)3.1.1. 拉延冲压方向和工序内容 (28)3.1.2. 压料面和分模线 (29)3.1.3. 创建工艺补充造型 (32)3.2. 2/4修边工艺分析与设计 (36)3.2.1. 修边冲压方向和工序内容 (36)3.2.2. 修边工艺造型 (38)3.3. 3/4翻边翻孔工序工艺设计 (39)3.3.1. 翻边冲压方向和工序内容 (39)3.3.2. 翻边模各项参数 (40)3.3.3. 翻边工艺造型 (43)3.4. 4/4冲孔和侧冲孔工序工艺设计 (44)3.4.1. 冲孔冲压方向和工艺内容 (44)4.零件仪表台板安装梁工艺分析和设计 (47)4.1. 1/4工序拉延件工艺分析与设计 (48)4.1.1. 拉延冲压方向和工序内容 (48)4.1.2. 压料面和分模线 (49)4.1.3. 创建工艺补充造型 (52)4.2. 2/4工序修边+冲孔工艺分析与设计 (56)4.2.1. 修边冲压方向和工序内容 (56)4.2.2. 废料刀设计 (57)4.2.3. 修边工艺造型 (57)4.3. 3/4侧修边+侧冲孔+翻孔工序工艺设计 (58)4.3.1. 侧修边冲压方向和工序内容 (58)4.4. 4/4翻边工序工艺设计 (59)4.4.1. 翻边冲压方向和冲压内容 (59)4.4.2. 创建工艺造型 (61)5.零件行李箱外板上件工艺分析和设计 (63)5.1. OP05落料工序工艺分析与设计 (64)5.2. OP10拉延工序工艺分析与设计 (65)5.2.1. 拉延冲压方向和工序内容 (65)5.2.2. 压料面和分模线 (66)5.2.3. 创建工艺造型 (69)5.3. OP20修边+侧修边+侧冲孔工序工艺分析与设计 (72)5.3.1. 修边冲压方向和工序内容 (72)5.3.2. 废料刀设计 (73)5.4. OP30侧翻边+侧冲孔工序工艺分析与设计 (74)5.4.1. 冲压方向和工序内容 (74)5.5. OP40侧翻边+翻边工序工艺分析与设计 (75)5.5.1. 冲压方向和工序内容 (75)6.识图 (78)1. 工艺设计前的准备工作在拿到冲压件进行工艺设计前,必须查阅有关资料,以便明确产品的具体要求、现有的条件等,为设计合理而可行的冲压工艺做好必要的准备。
这些资料主要有:1.零件图或产品图,可以参考的模型。
2.冲压件的公差。
3.类似零件的成型性及作业性的有关资料、曾出现的各种质量问题及解决方法。
4.关于产品所用钢材的有关资料,如材料的各项性能参数值,表面质量等。
5.各种摸具设计的标准和模具零件的规格。
6.现有压力机的参数和附属装置、生产率等方面的资料。
7.产量和要求的时间。
通过对零件图和拉深件图的研究,应该了解该零件所应具有的功能、所要求的单个零件的强度,表面质量以及相关零件之间所要求的相关精度。
并明确下列事项:1.零件轮廓、法兰、侧壁及底部是否有形状急剧变化的部分、负角的部位等,以及其他成形困难的形状。
2.该零件和有关零件的焊接面、装配面、镶嵌面有什么要求。
3.孔的精度(直径、位置)、孔和孔的间距的要求,这些孔的位置在何处(平面部分、倾斜部分、侧壁部分)。
4.各个凸缘精度允许达到什么程度(包括长度、凸缘面的位置、回弹)。
5.焊接、装配的基准面和孔在何处。
6.零件冲压成形需要解决的重点问题有哪些。
7.材料的利用率如何。
在进行工艺设计之前,必须对零件进行合理全面的工艺分析。
根据零件本身原始信息(包含产品的材质,料厚,产品形状),冲压件的公差和车身装配位置,客户和本工厂的压力机参数和生产方式(自动线,手工线),冲压件的生产批量大小以及客户提出的模具设计的技术要求来进行冲压件的工艺分析。
2. 零件的前碰撞梁工艺分析和设计2.1. 零件工艺分析下面我们以东风项目中前碰撞梁为例图2.1零件名称:前碰撞梁材料:BUSD料厚:2.0mm图2.1为零件的产品数模,根据零件的数模和提供的基本信息,以及客户的技术要求我们来进行零件的前碰撞梁的工艺分析,并确定通过几道冲压工序来获得我们的零件。
冲压零件不论复杂或简单我们可以概括为它都是通过两类模具来获得的:1成形类模具(包括拉延模,成形模,整形模,翻边模,侧翻和侧整模),2修边类模具(包括修边模,落料模,冲孔模,侧修和侧冲孔模具),成形类模具是通过不同的成形方式来完成我们的产品形状,修边类模具则是切除零件在成形后的废料以达到产品的尺寸精度。
如图2.1所示,首先我们根据零件数模可以确定该零件拉深的成形难度不是太高,形状不是很复杂,产品在车身状态不存在负角,唯一需要考虑的或者说零件成形的唯一风险性就是产品反弹,如图2.1示梁类件是典型易反弹的形状,所以我们在成形类模具中必须考虑产品的反弹量,零件所有形状可以通过一次拉延全部完成。
如图2.1所示,我们可以由零件数模了解零件一共有8个孔位,6个在产品平面的区域,2个在产品侧壁区域,产品轮廓线比较规则可以在拉延的冲压方向下保证垂直修边。
所以我们在了解产品的装配关系和孔的精度,公差后,我们可以把零件的全部工序确定下来。
零件工序确定如下:1,拉延2,修边+冲孔3,冲孔+侧冲孔。
2.2. 1/4拉延件工艺分析与设计零件成形的确定其实就是确定拉延工序,是编制覆盖件冲压工艺首先要考虑的问题,使之不但能够方便于拉延,而且拉延后还要能够方便于修边,又要为翻边创造有利条件,因此,拉延件确定下来以后覆盖件冲压工艺也就基本上确定了。
确定拉延工序,我们必须考虑以下几个重点:2.2.1. 确定零件的冲压方向确定冲压方向是确定拉延件首先要遇到的问题,它不但决定能否拉延出满意的拉延件来,而且影响到工艺补充部分的多少和压料面形状。
有些形状复杂的拉延件往往会由于冲压方向确定不当,而拉延不出满意的拉延件来,只好改变冲压方向,这样就需要修改拉延模,同时还必须相应地修改拉延以后的冲模,回造成很大的成本损失,所以冲压方向必须慎重考虑确定之。
确定冲压方向必须考虑以下几个重点:a)保证凸模能够顺利进入凹模,尽量避免负角b)凸模开始拉延时与拉延的毛坯的接触状态,接触面积要大,尽量靠近中间,接触地方要多,要分散c)压料面各部分进料阻力要均匀依以上原则,图2.1所示零件的冲压方向我们就可以确定下来如图2.2。
图2.2图1.2示Z轴坐标方向为该零件的冲压方向,该冲压方向与零件顶面垂直,不存在负角,凸模开始拉延时与毛坯的接触状态面积大并且都在零件的中间部分有利于拉延,同时后工序修边冲孔都可以保证垂直修边和冲孔,所以拉延和后工序修边、冲孔都可使用该冲压方向。
2.2.2. 零件的压料面和分模线压料面是工艺补充部分的一部分,指凹模圆角半径以外的那一部分。
压料圈将拉延毛坯压紧在凹模压料面上,凸模对拉延毛坯拉延,不但要使压料面上的材料不皱,更重要的是保证拉入凹模的材料不皱又不裂,分模线是凸模和压边圈的分界线,通常是指压料面和凸模面延伸所产生的那条线。
基本上压料面和分模线的形状和好坏很大部分决定冲压件的拉延状态好坏。
压料面一般有两种情况:●压料面就是覆盖件本身的凸缘部分。
●压料面是工艺补充补充成的。
确定压料面的形状我们必须考虑下面的问题:●尽量降低拉延深度。
●凸模对拉延毛坯一定要有拉延状态产生压料面的展开长度必须比凸模展开长度短,压料面所形成的夹角必须比凸模的夹角要大。
●压料面形状尽量简单化,尽量采用水平压料面。
●压料面应使成形深度小且各部分深度接近一致。
●压料面应使毛坯在拉深成形和修边工序中有可靠定位,并考虑送料和取件方便。
●当覆盖件底部有反成形时,压料面必须高于反成形形状的最高点。
●不要在某一方向产生很大的侧向力。
接下对上图2.1所示零件进行压料面和分模线的创建。
根据零件数模我们可以有两种方法创建零件的压料面:1压料面就直接使用覆盖件本身的凸缘部分,2压料面由工艺补充够成即自己创建。
对两种方法分别进行分析,首先如果直接使用覆盖件的凸缘为压料面,我们可以节省毛坯材料提高材料利用率,但从工艺上考虑则会给零件带来起皱的现象,并且不利于克制和避免零件的反弹,前面就有提到过梁类件是零件中典型的易反弹件,所以直接使用零件凸缘为压料面不可行的,只能根据以上我们提到过的创建压料面的原则通过工艺补充自己创建压料面。
通过综合以上原因和条件,前碰撞梁零件的压料面我们创建如下图2.3所示图2.3当压料面确定下来后,接下来就要确定拉延件的分模线。
分模线的作用就是分开了凸模和压料圈两个工作部件,从成形角度来说就是分开了实际拉延的压料部分和拉延成形部分,通常分模线的轮廓形状结合压料面的型面形状在很大程度上就决定了零件拉延的初始状态好坏和最终零件是否起皱、开裂、反弹、刚性不足等缺陷,所以分模线也是对拉延件的成形起决定性作用的。
创建分模线时我们需注意以下几点:●分模线轮廓形状尽量不要发生急剧的变化,●分模线创建时要结合压料面的形状,●分模线创建时要结合产品零件的修边轮廓准确计算尺寸保证工艺补充合适,保证修边的余量,●分模线创建时要考虑到零件接近分模线位置的形状是否变化剧烈,是否易产生开裂和起皱等缺陷,应如何适当的改变分模线的形状来避免,来优化零件的拉延状态。
依据以上几点,前碰撞梁零件的分模线我们确定如下图2.4:图2.42.2.3. 拉延件合理的工艺补充工艺补充是指为了顺利拉深成形出合格的制件、在冲压件的基础上添加的那部分材料。
由于这部分材料是成形需要而不是零件需要,故在拉深成形后的修边工序要将工艺补充部分切除掉。
工艺补充是拉深件设计的主要内容,不仅对拉深成形起着重要影响,而且对后面的修边、整形、翻边等工序的方案也有影响。
工艺补充部分有两大类:一类是零件内部的工艺补充,即填补内部孔洞,这部分工艺补充不增加材料消耗,而且在冲内孔后,这部分材料仍可适当利用;另一类工艺补充是在零件沿轮廓边缘展开的基础上添加上去的,它包括拉深部分的补充和压料面两部分。
由于这种工艺补充是在零件的外部增加上去的,称为外工艺补充,它是为了选择合理的冲压方向、创造良好的拉深成形条件而增加,它增加了零件的材料消耗。