冲压件设计
冲压件模具设计常用公式

冲压件模具设计常用公式1. 材料和工艺参数计算公式1.1 冲击力的计算公式冲击力是冲压件模具设计中重要的参考指标之一,它可以用于确定模具的强度和稳定性。
冲击力的计算公式如下:F = K × A × T × σ其中,F表示冲击力,K表示冲击系数,A表示冲压件的有效面积,T表示冲压时间,σ表示材料的抗拉强度。
1.2 冲床力的计算公式冲床力是指冲床在冲压过程中对工件所产生的压力。
冲床力的计算公式如下:P = F / A其中,P表示冲床力,F表示冲击力,A表示冲压件的有效面积。
1.3 冲压时间的计算公式冲压时间是指冲床一次冲压周期所需的时间。
冲压时间的计算公式如下:T = (L / V) + t其中,T表示冲压时间,L表示冲压件的长度,V表示冲床的下行速度,t表示冲程停留时间。
1.4 最大冲床力的计算公式最大冲床力是指冲床所能承受的最大压力。
最大冲床力的计算公式如下:P_max = K × A × σ其中,P_max表示最大冲床力,K表示冲击系数,A表示冲压件的有效面积,σ表示材料的抗拉强度。
2. 模具结构设计公式2.1 模具剪切强度的计算公式模具剪切强度是指模具在剪切过程中所能承受的最大剪切力。
模具剪切强度的计算公式如下:P_shear = F / A_shear其中,P_shear表示模具剪切强度,F表示冲击力,A_shear表示模具剪切面积。
2.2 模具挤压强度的计算公式模具挤压强度是指模具在挤压过程中所能承受的最大挤压力。
模具挤压强度的计算公式如下:P_extrusion = F / A_extrusion其中,P_extrusion表示模具挤压强度,F表示冲击力,A_extrusion表示模具挤压面积。
2.3 模具弯曲强度的计算公式模具弯曲强度是指模具在弯曲过程中所能承受的最大弯曲力。
模具弯曲强度的计算公式如下:P_bending = F / A_bending其中,P_bending表示模具弯曲强度,F表示冲击力,A_bending表示模具弯曲面积。
冲压件模具设计常用公式

冲压件模具设计常用公式1. 冲裁力计算公式冲裁力是模具在冲裁过程中对工件施加的力的大小,可以使用以下公式进行计算:$$ P = K \\cdot T \\cdot L \\cdot S $$其中: - P 是冲裁力〔单位:N〕 - K 是系数〔根据材料和冲裁方式进行选择〕 - T 是材料的厚度〔单位:mm〕 - L 是冲裁长度〔单位:mm〕 - S 是材料强度的保险系数2. 冲孔力计算公式冲孔是冲压件模具中常见的一个工序,为了计算冲孔力,可以使用以下公式:$$ F = K \\cdot T \\cdot L \\cdot S $$其中: - F 是冲孔力〔单位:N〕 - K 是系数〔根据材料和冲孔方式进行选择〕 - T 是材料的厚度〔单位:mm〕 - L 是冲孔孔径〔单位:mm〕 - S 是材料强度的保险系数3. 模具开孔面积计算公式在冲压件模具设计中,开孔面积对模具的设计和选择起着重要的作用。
开孔面积可以通过以下公式计算:$$ A = L \\cdot W $$其中: - A 是开孔面积〔单位:mm²〕 - L 是模具的长度〔单位:mm〕 - W 是模具的宽度〔单位:mm〕4. 模具强度计算公式模具强度的计算是冲压件模具设计中的关键步骤之一。
可以使用以下公式计算模具的强度:$$ P_t = P \\cdot S_f $$其中: - P_t 是模具的强度〔单位:N〕 - P 是冲裁力或冲孔力〔单位:N〕 - S_f 是平安系数5. 模具寿命计算公式模具寿命的计算是冲压件模具设计过程中需要关注的一个重要指标。
可以使用以下公式计算模具寿命:$$ N_m = \\frac{S_m}{f \\cdot V_c} $$其中: - N_m 是模具的使用寿命〔单位:次〕 - S_m 是模具材料的疲劳强度〔单位:MPa〕 - f 是载荷系数 - V_c 是模具的速度〔单位:m/s〕6. 模具热应力计算公式模具在使用过程中会受到热应力的影响,为了进行热应力的计算,可以使用以下公式:$$ \\sigma = \\frac{Q}{A} $$其中: - σ 是热应力〔单位:MPa〕 - Q 是热量〔单位:J〕 - A 是模具横截面积〔单位:mm²〕7. 模具变形计算公式模具在使用过程中会发生一定的变形,为了进行变形的计算,可以使用以下公式:$$ \\delta = \\frac{{F \\cdot L}}{{E \\cdot A}} $$其中: - δ 是变形量〔单位:mm〕- F 是施加在模具上的力〔单位:N〕 - L 是模具的长度〔单位:mm〕 - E 是弹性模量〔单位:MPa〕 - A 是模具的截面积〔单位:mm²〕总结在冲压件模具设计过程中,常用的公式可以帮助工程师快速准确地进行相关计算,从而确保模具的性能和可靠性。
冲压件模具设计的常用公式

冲压件模具设计的常用公式
一、材料力学公式
1.应力公式:σ=F/A,其中σ为应力,F为受力,A为受力面积。
2.应力应变关系公式:σ=E×ε,其中E为杨氏模量,ε为应变。
3.屈服强度公式:σs=F/A0,其中σs为屈服强度,F为屈服点所受力,A0为初始横截面积。
二、材料成形公式
1. 塑性变形公式:ε = ln (h0 / hn) ,其中ε为塑性变形,h0为初始厚度,hn为最终厚度。
2.变形力公式:F=S×σs,其中F为变形力,S为变形面积,σs为屈服强度。
3.针对特定形状的材料成形公式,如直冲材料成形公式、弯曲材料成形公式等。
三、模具设计公式
1.强度计算公式:F=σ×A,其中F为受力,σ为应力,A为受力面积。
2. 弯曲应力公式:σ = M / (W × yc),其中σ为弯曲应力,M为弯矩,W为截面模量,yc为弯曲轴心距离。
四、装配公式
1.装配公差公式:A=A1+A2+A3,其中A为总公差,A1为尺寸公差,
A2为形位公差,A3为相对公差。
五、切削力公式
1. 切削功率公式:P = F × V × kc,其中P为切削功率,F为切
削力,V为切削速度,kc为切削功率系数。
以上是冲压件模具设计中的常用公式,通过这些公式的运用,可以对
冲压件进行力学、成形、模具设计、装配以及切削力等方面的优化和设计。
当然,具体的设计中还需要根据实际情况和不同材料的特性来选择合适的
公式。
冲压件设计

冲压(Stamping)冲压是在常温下利用压力机并依靠模具对金属材料剪切,使之变形获得所需形状的工艺。
压力机属于锻压机的一类,冷冲压的压力机有机械压力机和液压压力机,常用的是机械压力机(冲床)。
冲压工艺(Stamping Process)(1)落料Cutting落料:从材料上沿着封闭轮廓分离出工件初胚的工艺。
(2)冲孔Punching冲孔:从工件上沿着封闭轮廓分离出废料,获得所需要的带孔零件的工序。
(3)压凸/压筋Embossing压凸/压筋:用凸模挤入工件的一面,迫使材料流入对面凹坑以形成凸起的一种冲压工序。
用途:a)增强产品强度b)代替其他子件(4)弯曲Bending弯曲:弯曲是把板材加工成具有一定的角度和形状的零件成形方法,材料在模具的作用下产生弯曲变形。
(5)卷边和翻边Revolving and Hemming卷边:对板、圆筒或圆形容器或圆形容器的端部进行圆形卷边的加工。
翻边:翻边是沿外形曲线周围将材料翻成侧立短边的一种冲压工序。
(6)冲沉孔Chamfering冲沉孔:可借助模具在零件孔侧压出锥形沉孔或圆柱形沉孔,一般用于装配沉头螺丝或去除毛刺。
(7)翻孔Turns Hole翻孔:沿内圆孔周围将材料翻成侧立凸缘的冲压工序,一般用于薄片攻螺纹孔。
(8)切舌与切开/冲桥位Part Cutting & Bridge Forming切舌:将材料沿轮廓局部而不是完全分离的一种冲压工序。
被局部分离的材料,具有工件所要求的一定位置,不再位于分离前所处的平面上。
切开/冲桥位:将材料沿敞开轮廓局部而不是完全分离的一种冲压工序。
被切开而分离的材料位于或基本位于分离前所处的平面。
(9)拍披锋Deburring拍披锋:利用模具清除剪切带来的锋利毛刺。
(10)拉深Deep Draw拉深:把平直毛料或工序件变为空心件,或者把空心件进一步改变形状和尺寸的一种冲压工序。
拉深时空心件主要依靠位于凸模底部以外的材料流入凹模而形成的。
冲压件模具设计常用公式

冲压件模具设计常用公式一、前言冲压件模具设计是冲压加工实现自动化、高效生产的关键环节,冲压件模具设计的好坏直接影响冲压品质和生产效益。
因此,在冲压件模具设计过程中,必须掌握一些常用公式,以便在实践中更加精准地解决模具设计中的各种问题。
本文将围绕冲压件模具设计常用公式进行阐述,以期为读者提供一些实用、有效的模具设计知识和技巧。
二、冲压件模具设计常用公式分类1. 材料折弯空间S材料折弯空间S是指冲压时材料在弯曲过程中被拉长的长度,用于计算按照弯缘角度和弯曲半径计算成品长度。
公式如下:S=K*L*(180°-2α)/π 式中,L是材料长度,α是折弯角度,K 是常数,其值根据材料厚度和折弯角度而定。
2. 冲压件毛坯重量M冲压件毛坯重量M是指冲压件在未经加工之前的重量,用于计算材料消耗。
公式如下:M=ρ*L*w*t 式中,ρ是材料密度,L是边长,w是厚度,t 是数量。
3. 模具壁厚t模具壁厚t是指冲压件模具中金属材料的厚度,包括上、下、左、右四个方向的壁厚,一般与压力有关。
可按照最小切削层厚度取值,公式如下:t=K*H/24 式中,K是常数,一般为6~10,H是加工硬度。
4. 补料长度L补料长度L是指冲压件模具中需要加上的余量,保证成品尺寸精度和质量,公式如下:L=αt/K 式中,α是成品弯缘角度,t是壁厚,K是常数,一般为4~6。
5. 小孔冲孔孔距P小孔冲孔孔距P是指在被加工材料上,两相邻的小孔冲或冲孔之间的距离,用于计算模具孔距间距。
公式如下:P=p*t 式中,p是小孔冲孔孔距系数,t是壁厚。
6. 冲模的直径D冲模的直径D是指用以冲剪及压穿时所用的模具直径大小,用于计算冲模的耐用程度。
公式如下:D=0.7√t 式中,t是最薄材料厚度。
7. 冲孔直径d冲孔直径d是指冲剪和冲孔过程中冲头的直径大小,直接影响冲穿质量和模具的使用寿命。
公式如下:d=0.9√H 式中,H是加工硬度。
三、总结本文从材料折弯空间S、冲压件毛坯重量M、模具壁厚t、补料长度L、小孔冲孔孔距P、冲模的直径D和冲孔直径d等七个方面介绍了冲压件模具设计常用公式,并为读者提供了详细的公式计算方法和实用技巧。
冲压件设计要点

冲压件设计要点冲压件是冲压工艺中常用的一种零件加工方式,其特点是高效快速、成本低廉,广泛应用于汽车、电子、家电等行业。
在进行冲压件设计时,需要注意以下几个要点。
1. 材料选择:冲压件的材料选择直接影响到产品的质量和性能。
一般情况下,冲压件常用的材料有冷轧板、热轧板、不锈钢、铝合金等。
在选择材料时,要考虑到产品的实际使用环境、强度要求、耐腐蚀性等因素,确保材料的可靠性和经济性。
2. 孔洞设计:冲压件常常需要在板材上开设孔洞,用于连接、安装或通风等用途。
在进行孔洞设计时,需要考虑到孔洞的尺寸、位置和形状,确保其与其他零件的配合精度,并提供足够的强度和刚度。
3. 弯曲设计:冲压件常常需要进行弯曲加工,用于形成特定的形状或角度。
在进行弯曲设计时,需要考虑到板材的强度、弯曲角度、弯曲半径等因素,确保弯曲后的产品符合设计要求,并避免出现开裂或变形等问题。
4. 表面处理:冲压件的表面处理对于提高产品的质量和外观非常重要。
常用的表面处理方式包括镀锌、喷涂、电泳等。
在进行表面处理时,需要考虑到产品的使用环境和要求,选择合适的表面处理方式,并确保其与产品材料的相容性。
5. 模具设计:冲压件的模具设计是冲压工艺中的关键环节。
在进行模具设计时,需要考虑到产品的形状、尺寸和加工要求,确保模具的精度和稳定性。
同时,也要考虑到模具的制造成本和寿命,选择合适的材料和加工工艺。
6. 工艺规程:冲压件的加工过程需要制定详细的工艺规程,包括材料切割、冲孔、弯曲、表面处理等各个环节。
在制定工艺规程时,需要考虑到产品的加工难度、工艺稳定性和成本效益,确保产品的质量和交货期。
7. 检验要求:冲压件的质量检验是确保产品质量的重要环节。
在制定检验要求时,需要考虑到产品的尺寸精度、表面质量、材料性能等因素,选择合适的检验方法和标准,确保产品符合设计要求和客户需求。
8. 工装设计:冲压件的加工需要使用适当的工装和夹具。
在进行工装设计时,需要考虑到产品的形状、尺寸和加工要求,选择合适的工装类型和结构,确保产品的加工精度和稳定性。
冲压件工艺过程设计的内容及步骤
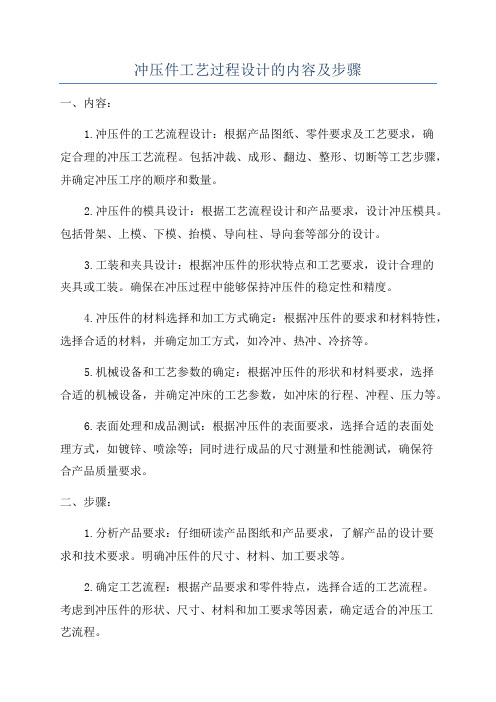
冲压件工艺过程设计的内容及步骤一、内容:1.冲压件的工艺流程设计:根据产品图纸、零件要求及工艺要求,确定合理的冲压工艺流程。
包括冲裁、成形、翻边、整形、切断等工艺步骤,并确定冲压工序的顺序和数量。
2.冲压件的模具设计:根据工艺流程设计和产品要求,设计冲压模具。
包括骨架、上模、下模、抬模、导向柱、导向套等部分的设计。
3.工装和夹具设计:根据冲压件的形状特点和工艺要求,设计合理的夹具或工装。
确保在冲压过程中能够保持冲压件的稳定性和精度。
4.冲压件的材料选择和加工方式确定:根据冲压件的要求和材料特性,选择合适的材料,并确定加工方式,如冷冲、热冲、冷挤等。
5.机械设备和工艺参数的确定:根据冲压件的形状和材料要求,选择合适的机械设备,并确定冲床的工艺参数,如冲床的行程、冲程、压力等。
6.表面处理和成品测试:根据冲压件的表面要求,选择合适的表面处理方式,如镀锌、喷涂等;同时进行成品的尺寸测量和性能测试,确保符合产品质量要求。
二、步骤:1.分析产品要求:仔细研读产品图纸和产品要求,了解产品的设计要求和技术要求。
明确冲压件的尺寸、材料、加工要求等。
2.确定工艺流程:根据产品要求和零件特点,选择合适的工艺流程。
考虑到冲压件的形状、尺寸、材料和加工要求等因素,确定适合的冲压工艺流程。
3.设计模具和工装:根据工艺流程设计和产品要求,设计合理的冲压模具和工装。
包括骨架、上模、下模、抬模、导向柱、导向套等部分的设计,并确保模具和工装的合理性和可行性。
4.选择材料和加工方式:根据冲压件的要求和材料特性,选择合适的材料,考虑材料的强度、硬度、韧性等性能要求。
同时,根据冲压件的形状和材料要求,确定适合的加工方式。
5.确定机械设备和工艺参数:根据冲压件的形状和材料要求,选择合适的机械设备,确定冲床的工艺参数。
包括冲床的行程、冲程、压力等参数。
6.表面处理和成品测试:根据冲压件的表面要求,选择合适的表面处理方式,如镀锌、喷涂等。
同时进行成品的尺寸测量和性能测试,确保冲压件符合产品质量要求。
冲压件模具设计的常用公式

冲压件模具设计的常用公式1. 强度和刚度计算公式1.1 拉伸强度计算冲压件在工作过程中会受到拉伸力的作用,因此计算冲压件的拉伸强度是非常重要的。
拉伸强度的计算公式如下:F = σ × A其中,F表示拉伸力,σ表示材料的抗拉强度,A表示冲压件的截面积。
1.2 刚度计算刚度是指冲压件在受力下的变形程度,计算冲压件的刚度可以确定其在工作过程中是否会发生过度变形。
刚度的计算公式如下:K = (E × A) / L其中,K表示刚度,E表示材料的弹性模量,A表示冲压件的截面积,L表示冲压件的长度。
2. 冲压参数计算公式2.1 冲头压力计算冲头压力是冲压件在冲床上受到的压力,计算冲头压力可以确定冲床的最小压力要求。
冲头压力的计算公式如下:P = F / A其中,P表示冲头压力,F表示冲压件的拉伸力,A表示冲头的截面积。
2.2 厚度计算冲压件的厚度是冲压件的重要参数之一,计算冲压件的厚度可以确定其制备过程中所需的原材料量。
厚度的计算公式如下:t = V / (A × L)其中,t表示冲压件的厚度,V表示冲压件的体积,A表示冲压件的截面积,L表示冲压件的长度。
3. 离型力计算公式冲压件在离型过程中需要克服一定的摩擦力,计算离型力是确定冲压模具设计是否合理的重要指标。
离型力的计算公式如下:F = μ × N其中,F表示离型力,μ表示冲压件和模具之间的摩擦系数,N表示冲压件的法线力。
4. 寿命计算公式冲压模具在工作过程中会受到疲劳载荷的影响,因此计算冲压模具的寿命可以指导模具的选材和使用。
寿命的计算公式如下:N = (S / K) × (F / σf)^b其中,N表示模具寿命的预测次数,S表示冲压次数,K表示对应于S次冲压的磨损系数,F表示冲压力,σf表示冲压件的疲劳强度,b表示指数。
结论以上是冲压件模具设计过程中常用的计算公式。
这些公式可以帮助工程师在设计冲压模具时进行强度、刚度、参数和寿命等方面的计算,以确保模具的设计合理和稳定性。
- 1、下载文档前请自行甄别文档内容的完整性,平台不提供额外的编辑、内容补充、找答案等附加服务。
- 2、"仅部分预览"的文档,不可在线预览部分如存在完整性等问题,可反馈申请退款(可完整预览的文档不适用该条件!)。
- 3、如文档侵犯您的权益,请联系客服反馈,我们会尽快为您处理(人工客服工作时间:9:00-18:30)。
《冲压工艺与模具设计》
目录
一.任务书--------------------------------------------2
二.冲压件工艺性分析----------------------------------3
三.冲压工艺方案的确定--------------------------------3
四.模具结构形式确定----------------------------------3
五.主要设计计算--------------------------------------4
六.模具总体设计--------------------------------------7
七.模具主要零件设计----------------------------------8
一、任务书
1、冲压件及要求
1.材料:08钢
2.厚度:1.5mm
3.精度:IT14
4.批量:大批量
2、主要内容
1.对所给零件进行工艺性分析并确定合理的冲压工艺方案;
2.确定模具的总体设计方案;
3.进行有关工艺与设计计算;
4.设计、选用模具零部件,绘制模具总装草图;
5.绘制模具总装图和主要工作零件的零件图;
6.编写设计说明书。
3、设计工作量
1.模具装配图1张;
2.模具工作零件的零件图3~4张;
3.设计计算说明书1份。
二、冲压件工艺性分析
该冲压件材料为08钢,具有良好的冲压性能,适合冲裁。
该冲压件结构相对简单,最小孔径为8mm,孔与孔之间的距离为65mm,孔与边缘之间的最小距离为6mm,所有尺寸均满足冲压工艺的要求,适合冲裁。
所有尺寸公差取IT14,满足普通冲裁的经济精度要求。
综上所述,该冲压件的冲压工艺性好,适合冲压加工。
三、冲压工艺方案的确定
该工件包括落料、冲孔两个基本工序,可有以下三种工艺方案:
方案一:先落料,后冲孔。
采用单工序模生产。
方案二:落料—冲孔复合冲压。
采用复合模生产。
方案三:冲孔—落料级进冲压。
采用级进模生产。
方案一的模具结构简单,但需要两道工序两套模具,成本高而生产效率低,难以满足大批量生产要求。
方案二的冲压件精度及生产效率都较高,但模具比较复杂,制造难度大,而且难以实现自动化。
方案三的生产效率高,操作方便,易于实现自动化,冲压件精度也能满足要求。
所以经过比较,采用方案三最为合适。
四、模具结构形式确定
(1)模具类型的选择根据上述方案,选择级进模。
(2)凹模结构形式采用整体式凹模。
(3)定位方式的选择利用导料板导料和侧刃定距。
(4)卸料,出件方式的选择采用弹性卸料和下出件方式。
(5)导向方式的选择选择中间导柱的滑动导向方式。
五、主要设计计算
(1)排样设计由于该工件为冲裁件,且外形和孔形结构都比较简单,因此可直接进行排样设计。
根据工件的结构,选用有废料的单直排,由表3-3查得搭边值为2mm,侧搭边值为2.5mm,则条料宽度为
图2设计的排样图
(侧刃定距时,条料宽度的计算公式为,这里
L=65mm+15mm+10mm=90mm;a是侧搭边值;n是侧刃数量,这里取1;b与材料和厚度有关,查表3-6得1.5mm)
进距为S=15mm+15mm+2mm=32mm
此工件只需落料和冲孔两道工序,因此在排样时,第一工位利用侧刃冲去等于进距的料边进行定位,第二工位冲孔,第三工位落料。
设计的排样图,如图所示。
(2)冲压力的计算该工件在冲压过程中需要的冲压工艺力有冲一个∅8mm孔及一个∅12mm孔需要的冲孔力,侧刃冲料边需要的力,落外形需要的落料力,卸料力以及推件力。
冲裁力为
式中,L是两个孔的总周长,侧边的冲切长度与外形轮廓长度之和,经计算约为305.3mm,材料厚度为1.5mm,08钢的抗剪强度取260到340MPa,=300MPa。
由式(3-7)和式(3-8)并查表3-8可得卸料板和推件力为
卸卸
=4X0.055X178.6kN=39.292kN
推推
式中,n=h/t=6mm/1.5mm=4,h是凹模刃口高度,由表3-27查得,t是材料厚度。
由于选用的是弹性卸料和下出件方式,因此总的冲压力为
总推卸
可选择公称压力为250kN的开式曲柄压力机J23-25,由表1-7查得其主要技术参数如下。
公称压力:250kN。
最大装模高度:230mm。
装模高度调节量:50mm。
工作台垫板尺寸:700mmX400mm。
模柄孔尺寸:∅40mm。
(3)压力中心的确定压力中心即冲裁力的作用点,计算压力中心的目的是在模具设计时保证模具的压力中心与模柄的中心线重合。
压力中心可按下述步骤进行计算。
1)按比例绘制出各凸模刃口形状,侧刃需要按照切去的料边绘制,如图3所示的凸模1,2,3,4。
2)建立坐标系xOy。
3)按照3.3.2节介绍的方法首先分别求出每一形状的压力中心位置。
这里各圆形凸模的压力中心位于其圆心,根据图3中的几何关系,得到它们在坐标系xOy中的坐标分别为(32,65)和(32,0)。
对于侧刃冲去的料边(凸模1),可首先建立图3所示坐标系,得到其压力中心的坐标为(0.72,0.03),再转换到xOy坐标系中为
(64.72,81.28)。
对于外形,可首先分别建立和xOy 坐标系,求出R15mm和
R10mm的重心坐标(0,9.08)和(0,-6.67),再按照3.3.2节中介绍的单凸
模冲裁复杂工件的压力中心的求解方法求出外形在xOy坐标系中的压力中心坐标(0,36.14)。
4)按照求多凸模压力中心的求解方法得到模具的压力中心的位置
(17.50,43.23)。
(4)工作零件刃口尺寸计算因工作零件的形状相对较简单,适宜采用线切割机床分别加工凸模及凹模。
由于零件无任何质量要求,模具间歇选用表
3-20中iii类间歇,即单边间歇 c=(7%~10%) t (t为材料厚度),则=0.105mm,。
凸,凹模刃口尺寸见下表。
表 1 凸,凹模刃口尺寸(单位:mm)
六、模具总体设计
(1)凹模设计凹模采用整体式结构,考虑到凹模固定时需要加工螺孔、销孔,并尽量做到压力中心与模块中心的偏移量在允许范围内(不超过凹模各边
长的1/6),这里选用标准凹模板:矩形凹模板。
由表3-26得板料厚度的影响的系数 K=0.28
零件外形最大尺寸b=90mm
凹模厚度 H =Kb=0.28x90=25.2mm,取H=25mm
凹模壁厚 c=(1.5~2)H=37.8~50.4mm,取c=45mm
凹模宽度 B ==14.785+2x45=104.785mm,取B=160mm
凹模长度 L= =65+9.73+14.785+2x45=179.515mm,取L=200mm
选用标准凹模板:矩形凹模板 200x160x25 JB/T 7643.1-2008.
(2)其他零件设计凹模设计完成后,即可以选择模架,固定板,垫板,导柱,导套等。
模架:中间导柱模架 200x160x190-I GB/T 23565.3-2009
上模座:中间导柱上模座 200x160x40 GB/T 23566.3-2009
下模座:中间导柱下模座 200x160x50 GB/T 23562.3-2009
导柱:滑动导向导柱 A 28x190 GB/T 2861.1-2008
滑动导向导柱 A 32x190 GB/T 2861.1-2008
导套:滑动导向导套 A 28x100x38 GB/T 2861.3-2008
滑动导向导套 A 32x100x38 GB/T 2861.3-2008 固定板:矩形固定板 200x160x16 JB/T 7643.2-2008
垫板:矩形垫板 200x160x8 JB/T 7643.3-2008
侧刃:侧刃 IA 32.2x12x56 JB/T 7648.1-2008
侧刃挡块:A 型侧刃挡块 20x8 JB/T 7648.2-2008
导料板:导料板 160x50x8 JB/T 7648.5-2008
内六角圆柱头螺钉:螺钉 GB/T 70.1-2008 M8x50
内六角圆柱头螺钉:螺钉 GB/T 70.1-2008 M8x60
内六角圆柱头螺钉:螺钉 GB/T 70.1-2008 M8x70
内六角螺钉:螺钉 GB/T 70.2-2008 M4x10
销:销 GB/T 119.2-2000 6x35
销:销 GB/T 119.2-2000 8x60
销:销 GB/T 119.2-2000 8x80
查表3-36得卸料板的厚度是16mm,则卸料板尺寸:200x160x16.
卸料螺钉:圆柱头内六角卸料螺钉 M8x45 JB/T 7650.6-2008
根据初选设备J23-25模柄孔的尺寸,查JB/T 7646.1-2008得:
压入式模柄A 40x110 JB/T 7646.1-2008
模具总装配图,(见CAD文件)
七、模具主要零件设计(图见CAD文件)
(1)落料凸模落料凸模如图所示,材料选用Cr12。
(2)冲孔凸模由于是圆形,采用台阶式,如图所示,材料选用Cr12。
(3)凹模凹模如图所示,材料选用Cr12。
(4)垫板垫板如图所示,材料选用45钢。
(5)固定板固定板如图所示,材料选用45钢。