铸造充型过程数值模拟特征分数步长法
铸造过程的模拟仿真技术及在发动机零部件设计上的应用

热应力数值模拟
铸锻材料与工艺研究所
铸件凝固过程中的热应力数值模拟涉及凝固 过程复杂的传热分析、随温度和组织变化的力学 模型、铸件和铸型之间的相互作用和热裂的发生 等。
铸件热应力模拟可以预测铸件凝固过程中应 力和变形的动态变化,在此基础上进行热裂的预 测,并对铸件残余应力和残余变形进行分析,为 铸件尺寸精度控制提供依据。
化技术可以有效地发现铸件可能产生缺陷的位置
和种类,从而指导工艺人员采取恰当的工艺措施 加以避免。
ห้องสมุดไป่ตู้
发动机工程研究院
铸造过程的模拟仿真技术
铸锻材料与工艺研究所
通过数值模拟的应用,可以分析铸件中存在
的各种缺陷的产生原因,进而采取相应工艺措施 来消除缺陷,实现工艺优化,同时可以节省大量 的人力、物力和财力,缩短产品从设计到应用的 周期,增强产品的市场竞争能力。
发动机工程研究院
铸锻材料与工艺研究所
数值模拟: 在计算机上实现的一个特定的计算,通
过数值计算和图像显示,履行一个虚拟的物 理实验—数值试验。
发动机工程研究院
有限元法
铸锻材料与工艺研究所
发动机工程研究院
有限元法
铸锻材料与工艺研究所
有限元法(FEM-finite element method)
横浇道
压铸压射速度----压室内冲头推动金属 液时的移动速度。
慢压射速度----通常包括冲头越过浇料 口这段行程。一般为0.1~0.5m/s。
快压射速度----确定内浇道截面积、内 浇口速度,然后根据压室直径得到。
直浇道
内浇道
发动机工程研究院
铸锻材料与工艺研究所
铸件充型过程(流场)数值模拟
排溢系统----熔融金属在填充型腔过程中,排除型 腔内的气体、涂料余烬以及流动金属前沿的冷金 属的通道和处所。
压铸镁合金罩盖充型过程的数值模拟

压铸镁合金罩盖充型过程的数值模拟写一篇3000字的中文文章,以“压铸镁合金罩盖充型过程的数值模拟”为标题,要求:近年来,压铸镁合金零件成为汽车行业和航空航天行业中应用越来越广泛的新型材料,而纳米材料对此又有着重要的影响。
为了研究压铸镁合金罩盖充型过程的精确度,本文以压铸镁合金罩盖充型的传热现象为核心,将数值模拟方法应用于该充型过程,遵循以下步骤进行研究:(1)实验装置及试件的制备。
这一步骤的目的是确定实验装置的结构和材料及试件的要求,包括实验变量的设计、制备件的材料种类及尺寸大小等。
(2)建立数学模型。
在这一步骤中,我们将根据实验装置及试件的材料特性建立压铸镁合金罩盖充型过程的数学模型,包括模拟充型温度场、流场及温度分布的影响等。
(3)数值模拟,采用计算流体力学(CFD)技术,首先通过建立相应的预处理程序进行网格生成,然后使用求解器对建立的数学模型进行求解,以获得所需的物理量在空间上的分布状况以及其它结果。
(4)仿真结果分析。
从仿真结果中可得到充型过程中温度场、流场及温度分布等重要参数的分析,从而探究影响充型精度的因素,以便为压铸镁合金罩盖充型的加工过程的更好的控制提供重要的理论依据。
本文首先介绍了压铸镁合金罩盖充型过程的数学模型及实验装置的制备,然后,通过CFD技术对该数学模型进行数值模拟,最后对仿真结果进行分析,从而探究影响充型精度的因素。
结果表明,压铸镁合金罩盖充型过程受多种因素影响,如型芯形状、工艺参数、模具设计等;另外,使用纳米粉末加工时,由于其特殊的性质,温度场和流场影响也更为明显,对充型精度的影响更大,因此要提高充型精度,必须合理控制相关参数,采用有效的工艺设计和定制的模具,并结合本文的研究结果,运用数值模拟进行多次实验验证,以期达到最佳的充型效果。
综上所述,通过数值模拟研究压铸镁合金罩盖充型过程,对于更好地了解该充型过程的物理机理,提高充型精度,优化充型工艺具有重要意义。
未来的研究工作应该着重于实验与数值模拟的结合,并不断改进压铸镁合金罩盖充型过程的数学模型,以实现充型性能的优化。
钢质圆盘类工件挤压铸造成形过程数值模拟

钢质圆盘类工件挤压铸造成形过程数值模拟
钢质圆盘类工件挤压铸造是一种重要的金属成形加工方法,其成形过程受多种因素影响,需要通过数值模拟来优化工艺参数和改善成形质量。
本文将采用有限元数值模拟方法,对钢质圆盘类工件挤压铸造成形过程进行模拟。
该数值模拟方法可以较为准确地预测材料的流动情况、变形和应力分布。
首先,我们需要建立有限元模型。
钢质圆盘类工件的几何形状复杂,需要通过计算机辅助设计软件进行三维建模,并将模型导入有限元分析软件中,进一步生成数值模型。
然后,在数值模型中设置物理参数、材料模型、初始条件和边界条件等。
其次,进行数值模拟。
数值模拟过程中,需要使用合适的数值求解方法,对材料流动、变形和应力分布等物理过程进行模拟。
同时,需要根据实际工艺参数进行仿真计算,如挤压速度、温度、压力等。
通过迭代计算过程,可以得到每个时间步长的应变、应力和变形分布情况。
最后,分析和优化结果。
数值模拟得到的应变、应力和变形分布结果可以用于分析成形过程中的缺陷和质量问题,并在此基础上调整工艺参数,提高产品质量。
同时,也可以通过数值模拟来评估不同的工艺参数对于产品质量的影响,以实现成本优化的目的。
综上所述,钢质圆盘类工件挤压铸造成形过程的数值模拟是一种有效的方法,它可以较为准确地预测材料流动、变形和应力分布等物理过程,对于优化工艺参数和提高成形质量具有重要意义。
数值模拟在曲轴铸件工艺优化中的应用

数值模拟在曲轴铸件工艺优化中的应用
曲轴铸件工艺是一种常用的机械零件制造工艺,其重要的技术要求是材料的分散性和质量的可控性。
为了保证其质量,在曲轴铸件生产过程中,曲轴铸件的工艺参数需要经常进行调节和优化,以获得最优的曲轴铸件产品性能。
数值模拟是一种能够对工艺参数在任意给定情况下的变化及其影响进行计算的现代工程技术,它的特点是精确且速度快,具有自适应的优势。
此外,它还可以模拟复杂场景,恢复曲轴铸件工艺参数和优化的实际概况。
在曲轴铸件工艺优化中,数值模拟的应用(建立一个三维的曲轴模型)能有效帮助我们更客观地理解曲轴的制造过程,从而协助我们优化各类工艺参数,提供更恰当的工艺设计,给出更符合实际的结果。
数值模拟也可以帮助我们理解浇筑及冷却过程,从而帮助我们优化工艺,提高制造质量。
此外,还可以利用数值模拟对变形和强度进行分析,以提高曲轴铸件的可靠性和耐用性。
这一过程可以建立一个三维的曲轴力学模型,帮助企业更加客观地评估各个参数的影响,设计更佳的力学性能过程。
总的来说,数值模拟可以很好地用来帮助企业优化曲轴铸件的工艺,提高曲轴铸件的品质,延长使用寿命。
它的可视化技术可以模拟更复杂的场景,建立可靠的理论模型,从而有效帮助企业降低成本,提高生产效率。
凝固过程数值模拟隐式算法时间步长优化模型研究

FOUNDRY
变化曲线如图 5 所示, 缩孔缩松的预测结果与实际缺 陷情况吻合, 如图 6 所示。用 3 08h 即完成总单元数 为一千多万的温度场计算, 说明自动优化时间步长模 型可以充分地发挥分数步长法计算速度快的优势。
Vol 53 No 9
图 5 计算时间步长 Fig 5 Time step of simulation
存在临界时间步长的限制, 使大型铸件的模拟速度很 低, 计算花费的时间太长, 影响了软件的商品化与普 及化进程。
基于隐式算法, 列选主元高 斯消去法 1 、交替 方向隐式迭代法 2 、分数步长法 3 、以及分区计 算 4 被用来求解温度场, 大大提高了温度场的计算 效率。采用隐式差分法, 由于求解方法稳定, 对时间 步长无限制, 这就带来了一个具体问题, 隐式差分法 的时间步长如何确定。作者基于隐式分数步长法, 建 立了自动优化计算时间步长的模型, 实现了合理的调
( 2) 用均匀时间步长方案和自动优化时间步长模 型方案对铸件进行了温度场的模拟计算, 对计算结果 进行了比较, 验证了模型的可靠性。并与实际情况比 较了缺陷的位置与大小, 验证了模型的正确性。
参考文献: 1 林首位, 徐宏, 侯华, 龚荣良. 铸件三维温度场数值模拟隐式
图 6 轧钢机架的缩孔缩松预测结果 Fig 6 Shrinkage prediction of the mill housing 差分法研究 J . 铸造 2002, ( 6) : 358~ 361 2 刘伟涛, 曾大新, 苏俊义. 用 交替方向隐 式迭代法 计算铸件 凝 固过程的温度场 J . 西安交通大学学报. 2000, ( 7) : 68~ 72 3 吴亮, 熊守美, 柳百成. 应用 分数步长法 进行压铸 过程温度 场 数值模拟研究 J . 铸造. 1998, ( 11) : 15~ 19 4 Xiong Shoumei, Li Yongqiang, Peng Jingsong. Zone partit ioning computation t echnique during solidification simulation of sand casting process J . Int J Cast Metal Res. , 2002, 15, ( 4) : 385 ~ 388 5 Upadhya G, Paul A J. Comprehensive casting analysis model using a geometry- based technique followed by fully coupled, 3-D fluid flow, heat t ransfer and solidification kinetics calculations J . AFS Transact ions, 1992, 100: 25~ 33
球墨铸铁曲轴多维振动铸造充型过程的数值模拟
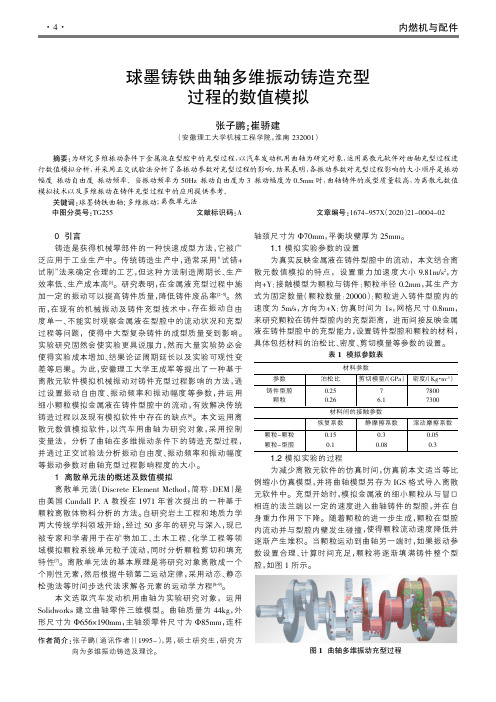
图1曲轴多维振动充型过程Internal Combustion Engine&Parts1.3不同振动参数对曲轴充型能力的影响研究不同振动参数对铸件充型能力的影响,采用控制变量法,分析该因素对颗粒在型腔中充型距离的影响程度,从而间接表征该因素对金属液充型能力的影响。
本文将选择在相同浇注速度和相同模拟总步数的条件下,分析颗粒在型腔中的充型距离,从而进一步用来判断金属液在型腔中充型能力的大小。
1.3.1振动自由度的影响振动自由度的类型有单自由度(X、Y、Z),两自由度(XY、XZ、YZ)和三自由度(XYZ)三种。
本文选取f=50Hz,A=0.5mm来研究振动自由度对曲轴充型过程的影响,结果如表2所示。
当振动自由度DOF=3时,颗粒充型距离取得最大值,说明颗粒充型距离随振动自由度的增加而增加。
自由度充型距离/mm最远位置型腔内的颗粒数X Y Z XY XZ YZ XYZ3003613003614014014467621274710表2不同振动自由度下颗粒的充型距离1.3.2振动频率的影响由表2可知,当自由度DOF=3时,充型距离取得最大值,故本实验取DOF=3,A=0.5mm来研究振动频率对曲轴充型能力的影响,结果如表3所示。
当振动频率f=50Hz 时,颗粒充型距离取得最大值。
若进一步增加振动频率,金属液产生紊流的可能性增大,反而会使得金属液的充型能力降低。
振动频率/Hz充型距离/mm最远位置型腔内的颗粒数10 20 30 40 50 60235300361426446401325963832表3不同振动频率下颗粒的充型距离1.3.3振动幅度的影响由表3可知,当DOF=3、f=50Hz时充型距离取得最大值,故本次实验取DOF=3、f=50Hz来研究振动幅度对曲轴充型能力的影响。
由表4可知,当振动幅度A=0.5mm时,颗粒充型距离达到最大值。
表4不同振动幅度下颗粒的充型距离振幅/mm充型距离/mm最远位置型腔内的颗粒数0.1 0.2 0.3 0.5 0.6 0.7235361426491466466-16838211.4模拟实验研究的结果为减少实验次数,提高实验数据的可信度,本文采用正交试验法来确定振动自由度、振动频率、振动幅度等因素对铸件充型能力的影响程度,令B为振动自由度;令C 为振动频率;令D为振动幅度,实验方案采用L9(34)的正交试验表,如表5所示,采用正交试验得出最佳的实验方案为B3C3D1,各参数对颗粒充型距离影响大小的顺序依次为振动频率、振动自由度、振动幅度。
熔铸AZS材料的铸造充型及凝固过程数值模拟

浇 注温度对铸 件 凝 固的影响 , 认 为较 为合 适 的浇 注温度在 1 8 1 0 左右 。 关 键词 : 熔铸 A Z S ; 充型 ; 凝固; 数 值模 拟
中图分类号 : T Q 1 7 5 文献标识码 : A 文章编 号 : 1 0 0 1— 1 9 3 5 ( 2 0 1 5 ) 0 5— 0 3 4 4— 0 5
的质量 。计算技术 的飞速发展为耐火砖熔铸成型过
程研 究提 供 了新 的研 究 手 段 。 。采 用 计 算 机 对 锆 刚玉熔 体 的充 型凝 固过程 进行 数值 仿 真分 析 , 可 以直
观地 观测 到其 充 型凝 固过 程 , 定量分析充型 、 传 热 凝 固规 律及 各 种 因 素 的 影 响 规 律 , 从 而 预 测 分 析 熔 铸
l 数 学及 物 理模 型 的建 立
1 . 1 数学 模型
由于充型 凝 固过程 的温度 场情 况 比较 复 杂 , 为 了
简 化模 型 , 进 行下列 假设 J : ( 1 )浇铸 的 A Z S 3 3熔 体 和 砂 型 的初 始 温 度 场均
匀 一致 ;
国 家科 技支 撑 计 划 课 题 资 助 项 目 ( 2 0 1 3 B AE 0 3 B 0 1 常庆 明 : 男, 1 9 6 4年 生 , 博士 , 教授 。
D O I : 1 0 . 3 9 6 9 / j . i s s n . 1 0 0 1 —1 9 3 5 . 2 0 1 5 . 0 5 . 0 0 6
熔铸锆刚玉 ( A Z S) 制 品 广 泛 应 用 于 玻 璃 制
备¨ 、 钢铁 冶 金行 业 , 是 一 种 非 常重 要 的 耐火 材
E- ma i l : q mc h a n g @ 1 6 3, t o n i
《挤压铸造过程数值模拟及工艺优化》范文

《挤压铸造过程数值模拟及工艺优化》篇一一、引言挤压铸造是一种重要的金属铸造工艺,广泛应用于各种工程领域。
为了更精确地掌握和控制挤压铸造过程,提升产品的质量、降低成本、优化工艺参数,进行数值模拟及工艺优化至关重要。
本文将对挤压铸造过程进行数值模拟,并通过分析模拟结果来探讨其工艺优化。
二、挤压铸造过程数值模拟1. 模型建立在挤压铸造过程中,模型建立是数值模拟的基础。
通过CAD 软件建立铸件、模具及挤压装置的三维模型,并导入有限元分析软件中。
在模型中考虑材料的物理性能、热传导性能、流变特性等关键因素。
2. 材料选择与参数设置根据所使用的合金材料和实际生产要求,设置合适的材料参数。
这些参数包括材料密度、比热容、热导率等,对于流动性和热物理性质的不同阶段要详细描述。
此外,挤压铸造过程中压力、温度等关键工艺参数也需根据实际进行设置。
3. 数值模拟过程利用有限元分析软件对挤压铸造过程进行数值模拟。
这一过程包括模具填充、冷却凝固、压力释放等关键阶段。
通过数值模拟可以观察材料在各个阶段的流动状态、温度分布以及应力变化等。
三、工艺优化探讨1. 填充过程优化通过数值模拟结果,可以观察到铸件在填充过程中的流动状态。
针对流动不均匀或出现涡流等问题,可以通过调整模具设计、改变浇注速度和压力等措施进行优化。
同时,合理的填充顺序和速度控制也是提高产品质量的关键因素。
2. 冷却凝固过程优化冷却凝固是决定铸件质量的重要环节。
通过数值模拟分析,可以找出温度梯度较大的区域和潜在的热应力集中点。
根据这些信息,可以调整冷却速率和模具温度分布,以改善铸件的凝固过程和力学性能。
3. 工艺参数优化工艺参数的优化包括压力、温度、时间等关键因素的调整。
通过数值模拟分析,可以确定最佳的工艺参数组合,以提高产品质量、降低成本和减少生产周期。
同时,根据生产需求和市场反馈,可以不断调整和优化这些参数,以适应市场的变化。
四、实际生产中的效果与应用通过在生产实践中应用数值模拟的结果和工艺优化的方法,可以实现更好的产品设计和制造。
- 1、下载文档前请自行甄别文档内容的完整性,平台不提供额外的编辑、内容补充、找答案等附加服务。
- 2、"仅部分预览"的文档,不可在线预览部分如存在完整性等问题,可反馈申请退款(可完整预览的文档不适用该条件!)。
- 3、如文档侵犯您的权益,请联系客服反馈,我们会尽快为您处理(人工客服工作时间:9:00-18:30)。
Charecteristics Fractional Step Method for Melt FlowSimulation in Casting Process1Lu Tongchao, Ge LiangSchool of Mathematics and System Sciences, Shandong University Jinan (250100)E-mail:lutc@AbstractA computational model on the melt flow simulation in casting process is partial differential equations which include the continuous equation and the momentum equation . We use the fractional step method to deal with the momentum equation. The compution is divided into two steps. In the first step, we use the characteristics finite difference method to compute the intermediate value. In the second step, we gain the possion equation of the pressure with help of the continuous equation; the equation is solved with the iterative method. The convergence and the stability of the equation are analyzed in this paper. Keywords: the fractional step method; method of characteristics; convergence; iterative1IntroductionThe substance of casting process is to pour the liquid metal into the mold cavity and make it cool and freeze. The filling of liquid metal is the first phase of the form of casting. A lot of defects such as cold cut, impurity or gas entrapment and the mould erosion are formed in mould filling. So it is important for gaining the high grade casting to know the process of mould filling. But owing to the complexity of the mould filling, people only had to gain the experiental rule by a lot of experiments for the mould filling. Now along with the development of computer, the melt flow simulation in casting process makes great progress[4].In simulation of the mould filling the fluid flow phenomena are governed by a set of non-linear equations. We could use the numerical methods such as finite element or finite difference to solve the Navier-Stokes equation, and gain the flowing role of liquid. In earlier studies, Chorin(1968) and Teman(1969)[6 ] had brought forward the projection method independently. In 1972 Patankar and Spalding [13 ]brought forward the simple method. And then the simplec method had also been brought forward, and Raithby[11 ] gave the simplex method, Sheng [12 ]gave the simplet method.In this article A computational model on the melt flow simulation in casting process is partial differential equations which include the continuous equation and the momentum equation . We use the fractional step method to deal with the momentum equation. The compution is divided into two steps. In the first step, we use the characteristics finite difference method to compute the intermediate value. In the second step, we gain the possion equation of the pressure with help of the continuous equation; the equation is solved with the iterative method. The convergence and the stability of the equation are analyzed in this paper.2Mathematical modelsIn simulation of the mould filling the fluid flow phenomena are governed by mass and momentum conservation equations that can be described as follows [10 ](a) The momentum equations for the liquid phase are as follows:1 Support by Research Fund for Doctoral of High Education by China State Educationg Ministry(20030422049)1x u p V u g u tx μρρ∂∂∂∂=−⋅−++Δr " (2.1)1y v p V v g v t y μρρ∂∂=−⋅−++Δ∂∂r " (2.2)where ,()x y ,∈Ω(0]t J T ∈=,V ui vj =+r r ris the velocity vector, is the pressure, p x g and y g are the body accelerationcomponents, ρ is the average density and μ is the viscosity. (b) The continuity equation for the liquid region is()0V tρρ∂+⋅=∂r " (2.3)[()]()l s l lf V f V tρρρ−∂0+⋅+⋅=∂r r "" (2.4)where sf ,lf are solid and liquid fractions respectively, and ss l l ff ρρρ+=,. Inthis article the molten metal could be seen as the incompressible liquid. And also assume that themolten metal would not solidity before the end of the mold filling. Then the equation could be simplified as 1s l f f +=0u vV x y∂∂⋅=+=∂∂r " (2.5)(c)The velocity boundary conditions for the liquid region areThe wall boundary and the free surface boundary are included in the velocity boundary conditions. In the situation of wall boundary, the velocity in the vertical orientation to the wall is equal to zero. The velocity in the free surface boundary is demand to meet the continuity equation.0u v V x y∂∂⋅=+=∂∂r" Series of iris images, includin3 fractional step characteristics finite difference schemeDivide the domain , the steps in x-direction and y-direction are Ωx Δ,, nodey Δi x i x =Δ,. We will consider a time step j y j =Δy T Nt Δ= and approximate the solution at times, where 。