第四章 刀具磨损及磨钝标准--(机械制造技术A)
机械制造技术基础简答题

1.何为刀具的工作角度?刀具角度变化的根本原因是什么?车刀安装位置和进给运动对刀具工作角度有何影响?以切削过程中实际的基面,切削平面和正交平面为参考系所确定的刀具角度称为刀具的工作角度,又称实际角度。
角度变化的根本原因是基面,切削平面和正交平面位置的改变.横向进给运动:进给量f增大,前角增大,后角减小。
轴向进给运动:进给量f增大,前角增大,后角减小。
刀具安装高低:车削外圆时,刀尖高于工件轴线,工作前角增大,工作后角减小;刀尖低于工作轴线,工作角度的变化则正好相反。
2.何为积屑瘤?影响因素有哪些?对切削过程的影响?避免产生和减小积屑瘤的措施?以中低切削速度切削一般钢料或其他塑性金属时,常常在刀具前刀面靠近刀尖处黏附着一块硬度很高的金属楔状物,称为积屑瘤。
切削温度,刀-屑接触面间的压力,前刀面粗糙度,粘结强度。
使刀具实际前角增大,切削力降低;影响刀具耐用度;使切入深度增大;使工件表面粗糙度值增大.避开产生积屑瘤的中速区,采用较低或较高的切削速度;采用润滑性能好的切削液,减小摩擦;增大刀具前角,减小刀—屑接触压力;采用适当的热处理方法提高工件硬度,减小加工硬件倾向。
3.切屑的类型?影响切屑变形的主要因素?带状切削,挤裂切削,单元切屑,崩碎切屑.工件材料:工件材料强度愈高,切屑变形愈小,工件材料塑形愈大,切屑变形就愈大。
前角:前角愈大,切屑变形愈小。
切削速度:在无积屑瘤的切削速度范围内,切削速度愈高,切屑变形就愈小;在积屑瘤增长阶段,实际前角增大,变形随切削速度增加而减小,在积屑瘤消退阶段,实际前角减小,变形随之增大.4.切削力的来源?切削层金属,切屑和工件表面层金属的弹性,塑性变形所产生的变形抗力。
(2)刀具与切屑,工件表面间的摩擦阻力.5.切削热的来源?影响切削温度的因素?切削热来源于:切削层金属发生弹性变形和塑性变形所产生的热和切屑与前刀面,工件与主后刀面间的摩擦热。
1)切削用量:Vc,f,ap增加,切削功率增大,切削热增多,温度升高,其中。
第四章-刀具磨损及磨钝标准(机械制造技术A)
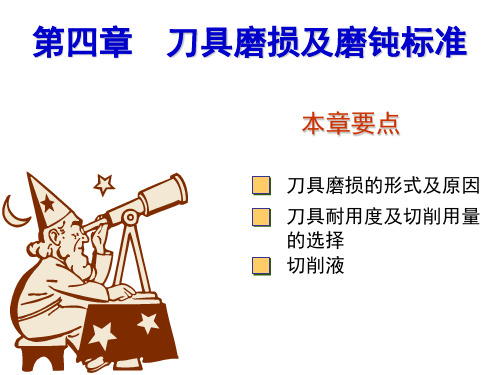
2.后刀面的磨损:
刀尖
B区
VBmax
待加工表面有上道工序产生的加工硬化或毛坯 表面硬层的影响
N区
C区
⑴ 后刀面磨损的特征
① C区:在靠近刀尖的位置。 特征:此部位切削过程中承受较大的切削力和较 高的切削温度,强度和散热条件差,所以磨损较 大。其磨损量用VC表示。
② N区:在靠近工件待加工表面的位置。 特征:由于加工表面的加工硬化或毛坯表面硬层 的影响,会在此部位造成较大的磨损且形成磨损 缺口。其磨损量用VN表示;
在高温高压下,刀具材料中的元素扩散到切屑 和工件材料中,工件材料中的铁元素又扩散到刀具 表层,从而改变了刀具表层的化学成分,使其硬度 和强度下降,磨损加剧。
⑵ 发生场合:
元素的耐热性差,则原子的稳定性差,易发生 扩散磨损;元素的耐热性好,则原子的稳定性好, 不易发生扩散磨损。
4)氧化磨损
Co3O4,CoO,WO3,TiO2
发生场合:工具钢刀具磨损的主要原因。
不同切削温度对磨损的影响:
温度对磨损的影响
1—粘结磨损 2—磨粒磨损 3—扩散磨损 4—相变磨损 5—氧化磨损
4.1 刀具磨损的形式及原因 刀具的磨损过程
D
C B
A
后刀面磨损量
刀具磨损的典初型期曲磨线损
正常磨损
剧烈磨损
1.初期磨损 图中AB段 • 特点:磨损较快 • 机理:
1.前刀面磨损
(1)前刀面磨损的特征 ①磨损后在前刀面上形成了一个月牙洼 ②月牙洼和刀刃之间有一个窄边; ③随着磨损的加剧,月牙洼不断扩展,该
窄边越来越窄,最后导致刀刃崩刃。
⑵ 发生前刀面磨损的场合: 用较高的切削速度和较大的切削厚度切削
塑性材料时产生前刀面磨损。
机械制造技术基础(第三版)课后习题答案

机械制造技术基础(第三版)课后习题答案第二章2-1。
金属切削过程有何特征?用什么参数来表示?答:2-2。
切削过程的三个变形区各有什么特点?它们之间有什么关联?答:第一变形区:变形量最大。
第二变形区:切屑形成后与前刀面之间存在压力,所以沿前刀面流出时有很大摩擦,所以切屑底层又一次塑性变形.第三变形区:已加工表面与后刀面的接触区域.这三个变形区汇集在切削刃附近,应力比较集中,而且复杂,金属的被切削层在此处于工件基体分离,变成切屑,一小部分留在加工表面上。
2—3.分析积屑瘤产生的原因及其对加工的影响,生产中最有效地控制它的手段是什么? 答:在中低速切削塑性金属材料时,刀—屑接触表面由于强烈的挤压和摩擦而成为新鲜表面,两接触表面的金属原子产生强大的吸引力,使少量切屑金属粘结在前刀面上,产生了冷焊,并加工硬化,形成瘤核。
瘤核逐渐长大成为积屑瘤,且周期性地成长与脱落。
积屑瘤粘结在前刀面上,减少了刀具的磨损;积屑瘤使刀具的实际工作前角大,有利于减小切削力;积屑瘤伸出刀刃之外,使切削厚度增加,降低了工件的加工精度;积屑瘤使工件已加工表面变得较为粗糙。
由此可见:积屑瘤对粗加工有利,生产中应加以利用;而对精加工不利,应以避免。
消除措施:采用高速切削或低速切削,避免中低速切削;增大刀具前角,降低切削力;采用切削液。
2—4切屑与前刀面之间的摩擦与一般刚体之间的滑动摩擦有无区别?若有区别,而这何处不同?答:切屑形成后与前刀面之间存在压力,所以流出时有很大的摩擦,因为使切屑底层又一次产生塑性变形,而且切屑与前刀面之间接触的是新鲜表面,化学性质很活跃。
而刚体之间的滑动摩擦只是接触表面之间的摩擦,并没有塑性变形和化学反应2—5车刀的角度是如何定义的?标注角度与工作角度有何不同?答:分别是前角、后角、主偏角、副偏角、刃倾角(P17)。
工作角度是以切削过程中实际的切削平面、基面和正交平面为参考平面确定的刀具角度。
2-6金属切削过程为什么会产生切削力?答:因为刀具切入工具爱你,是被加工材料发生变形并成为切屑,所以(1)要克服被加工材料弹性变形的抗力,(2)要克服被加工材料塑性变形的抗力,(3)要克服切屑与前刀面的摩擦力和后刀面与过度表面和以加工表面之间的摩擦力。
机械制造技术基础考试复习

六点定位原理:采用六个按一定规则布置的支承点,并保持与工件定位基准面的接触,限制工件的六个自由度,使工件位置完全确定的方法。
1.过定位:也叫重复定位,指工件的某个自由度同时被一个以上的定位支撑点重复限制。
2.加工精度:零件加工后的实际几何参数和理想几何参数符合程度。
加工误差:零件加工后的实际参数和理想几何参数的偏离程度。
3.原始误差:由机床,刀具,夹具,和工件组成的工艺系统的误差。
4.误差敏感方向:过切削刃上的一点并且垂直于加工表面的方向。
5.主轴回转误差:指主轴瞬间的实际回转轴线相对其平均回转轴线的变动量。
6.表面质量:通过加工方法的控制,使零件获得不受损伤甚至有所增强的表面状态。
包括表面的几何形状特征和表面的物理力学性能状态。
7.工艺过程:在生产过程中凡是改变生产对象的形状、尺寸、位置和性质等使其成为成品或半成品的过程。
8.工艺规程:人们把合理工艺过程的有关内容写成工艺文件的形式,用以指导生产这些工艺文件即为工艺规程。
9.工序:一个工序是一个或一组工人在一台机床(或一个工作地),对同一工件(或同时对几个)所连续完成的工艺过程.10.工步:在加工表面不变,加工刀具不变,切削用量不变的条件下所连续完成的那部分工序。
11.定位:使工件在机床或夹具中占有准确的位置.12.夹紧:在工件夹紧后用外力将其固定,使其在加工过程中保持定位位置不变的操作。
13.装夹:就是定位和夹紧过程的总和。
14.基准:零件上用来确定点线面位置是作为参考的其他点线面。
15.设计基准:在零件图上,确定点线面位置的基准。
16.工艺基准:在加工和装配中使用的基准。
包括定位基准、度量基准、装配基准。
一、简答题1.什么是误差复映,减少复映的措施有哪些?误差复映:指工件加工后仍然具有类似毛坯误差的现象(形状误差、尺寸误差、位置误差)措施:多次走刀;提高工艺系统的刚度.2.什么是磨削烧伤?影响磨削烧伤的因素有哪些?磨削烧伤:当被磨工件的表面层的温度达到相变温度以上时,表面金属发生金相组织的变化,使表面层金属强度硬度降低,并伴随有残余应力的产生,甚至出现微观裂纹的现象.影响因素:合理选择磨削用量;工件材料;正确选择砂轮;改善冷却条件。
机械制造技术基础-目录

第1章㊀机械制造技术概论1………………………………………………………㊀㊀1.1㊀制造与制造系统1………………………………………………………1.1.1㊀制造与制造技术1………………………………………………1.1.2㊀制造系统1………………………………………………………1.1.3㊀制造业的地位2…………………………………………………1.2㊀先进的生产模式3………………………………………………………1.2.1㊀计算机集成制造系统3…………………………………………1.2.2㊀并行工程8………………………………………………………1.2.3㊀精益生产11……………………………………………………1.2.4㊀虚拟制造13……………………………………………………1.2.5㊀敏捷制造16……………………………………………………思考与练习16…………………………………………………………………第2章㊀机械制造工艺方法与机床17……………………………………………㊀㊀2.1㊀毛坯制造方法17…………………………………………………………2.1.1㊀铸㊀造17………………………………………………………2.1.2㊀锻压成形21……………………………………………………2.1.3㊀焊㊀接25………………………………………………………2.1.4㊀毛坯成形方法比较30…………………………………………2.1.5㊀先进毛坯成形技术31…………………………………………2.2㊀材料热处理及表面处理技术32…………………………………………2.2.1㊀材料整体热处理32……………………………………………2.2.2㊀表面处理技术33………………………………………………2.3㊀零件加工制造34…………………………………………………………2.3.1㊀传统切削加工方法35…………………………………………2.3.2㊀特种加工方法41………………………………………………2.4㊀金属切削机床基础48……………………………………………………2.4.1㊀概㊀述48………………………………………………………2.4.2㊀金属切削机床的主要部件54…………………………………思考与练习71…………………………………………………………………第3章㊀机床夹具原理72…………………………………………………………㊀㊀3.1㊀机床夹具概述72…………………………………………………………3.2㊀工件在夹具中的定位75…………………………………………………3.2.1㊀基准的概念75…………………………………………………3.2.2㊀工件定位的基本原理77………………………………………2㊀机械制造技术基础㊀3.2.3㊀定位方式及定位元件81………………………………………3.3㊀工件在夹具中的夹紧92…………………………………………………3.3.1㊀加紧装置的组成及其设计要求92……………………………3.3.2㊀夹紧力的确定93………………………………………………3.3.3㊀夹紧机构设计96………………………………………………3.3.4㊀夹紧动力源装置103……………………………………………3.4㊀各类机床夹具105………………………………………………………3.4.1㊀车床夹具105……………………………………………………3.4.2㊀铣床夹具108……………………………………………………3.4.3㊀钻床夹具113……………………………………………………3.4.4㊀数控机床夹具118………………………………………………3.5㊀机床专用夹具设计步骤和方法120……………………………………3.5.1㊀设计机床专用夹具的基本要求120……………………………3.5.2㊀专用夹具的设计步骤121………………………………………思考与练习124…………………………………………………………………第4章㊀切削过程及其控制127……………………………………………………㊀㊀4.1㊀金属切削刀具基础127…………………………………………………4.1.1㊀切削加工的基本概念127………………………………………4.1.2㊀刀具角度129……………………………………………………4.1.3㊀刀具材料134……………………………………………………4.2㊀金属切削过程中的变形138……………………………………………4.2.1㊀切屑的形成过程138……………………………………………4.2.2㊀切削变形程度141………………………………………………4.2.3㊀前刀面上的摩擦142……………………………………………4.2.4㊀积屑瘤的形成及其对切削过程的影响143……………………4.2.5㊀影响切屑变形的因素144………………………………………4.3㊀切屑的类型及控制145…………………………………………………4.3.1㊀切屑的类型145…………………………………………………4.3.2㊀切屑类型控制146………………………………………………4.4㊀切削力147………………………………………………………………4.4.1㊀切削力与切削功率148…………………………………………4.4.2㊀切削力经验计算公式149………………………………………4.4.3㊀影响切削力的因素151…………………………………………4.5㊀切削热和切削温度153…………………………………………………4.5.1㊀切削热的产生与传导153………………………………………4.5.2㊀切削温度的测量154……………………………………………4.5.3㊀影响切削温度的主要因素155…………………………………4.6㊀刀具磨损㊁刀具寿命和切削用量的选择157……………………………㊀目录3㊀4.6.1㊀刀具磨损形态和磨损机制157…………………………………4.6.2㊀刀具磨损过程及磨钝标准158…………………………………4.6.3㊀刀具寿命159……………………………………………………4.6.4㊀刀具的破损及刀具状态监控161………………………………4.6.5㊀切削用量的选择162……………………………………………4.7㊀刀具几何参数的选择167………………………………………………4.7.1㊀前角γo 的选择167……………………………………………4.7.2㊀后角αo 的选择167……………………………………………4.7.3㊀主偏角K r ㊁副偏角Kᶄr 的选择168……………………………4.7.4㊀刃倾角λs 的选择169…………………………………………4.8㊀磨削原理169……………………………………………………………4.8.1㊀砂轮的特性和选择169…………………………………………4.8.2㊀磨削过程172……………………………………………………4.8.3㊀磨削力173………………………………………………………4.8.4㊀磨削温度174……………………………………………………思考与练习175…………………………………………………………………第5章㊀机械加工质量176…………………………………………………………㊀㊀5.1㊀机械加工质量概述176…………………………………………………5.1.1㊀加工精度的基本概念176………………………………………5.1.2㊀获得规定加工精度的方法176…………………………………5.2㊀影响机械加工精度的因素177…………………………………………5.2.1㊀加工误差177……………………………………………………5.2.2㊀工艺系统几何误差对加工精度的影响178……………………5.2.3㊀工艺系统力效应对加工精度的影响182………………………5.2.4㊀工艺系统热变形对加工精度的影响187………………………5.3㊀加工误差的综合分析189………………………………………………5.3.1㊀加工误差的性质与分析方法189………………………………5.3.2㊀分布曲线法190…………………………………………………5.3.3㊀点图法193………………………………………………………5.4㊀机械加工表面质量195…………………………………………………5.4.1㊀概㊀述195………………………………………………………5.4.2㊀零件表面质量对零件使用性能的影响196……………………5.4.3㊀影响机械加工表面粗糙度的工艺因素198……………………5.4.4㊀影响加工表面变质层的因素200………………………………5.5㊀提高机械加工质量的方法203…………………………………………5.5.1㊀提高机械加工精度的主要途径203……………………………5.5.2㊀提高机械加工表面质量的工艺途径208………………………5.6㊀机械加工过程中的振动及其控制212…………………………………4㊀机械制造技术基础㊀5.6.1㊀概㊀述212………………………………………………………5.6.2㊀强迫振动及其控制措施212……………………………………5.6.3㊀自激振动及其抑制措施214……………………………………思考与练习221…………………………………………………………………第6章㊀机械加工工艺过程设计223………………………………………………㊀㊀6.1㊀机械加工工艺规程概述223……………………………………………6.2㊀制订工艺规程的技术准备227…………………………………………6.2.1㊀零件图的分析227………………………………………………6.2.2㊀毛坯的选择229…………………………………………………6.3㊀定位基准及其选择230…………………………………………………6.3.1㊀工件的装夹方法230……………………………………………6.3.2㊀基准及其分类231………………………………………………6.3.3㊀粗基准的选择234………………………………………………6.3.4㊀精基准的选择238………………………………………………6.4㊀工艺路线的拟定246……………………………………………………6.4.1㊀加工方法的选择246……………………………………………6.4.2㊀工序顺序的安排252……………………………………………6.4.3㊀工序的分散与集中255…………………………………………6.5㊀加工余量及工序尺寸㊁公差的制订255…………………………………6.5.1㊀加工余量的含义255……………………………………………6.5.2㊀加工余量的确定257……………………………………………6.5.3㊀工序尺寸及其公差的确定259…………………………………6.6㊀工艺尺寸链259…………………………………………………………6.6.1㊀尺寸链的定义及组成259………………………………………6.6.2㊀尺寸链的计算方法261…………………………………………6.6.3㊀工艺尺寸链的应用263…………………………………………6.7㊀时间定额和提高生产效率的工艺措施266……………………………6.7.1㊀时间定额的组成266……………………………………………6.7.2㊀提高劳动生产率的工艺措施267………………………………6.8㊀工艺工程经济分析271…………………………………………………6.9㊀数控加工工艺设计273…………………………………………………6.9.1㊀数控加工工艺设计概述273……………………………………6.9.2㊀数控加工的工艺分析和工艺设计274…………………………思考与练习280…………………………………………………………………第7章㊀机器的装配工艺282………………………………………………………㊀㊀7.1㊀概㊀述282………………………………………………………………7.1.1㊀机器装配的基本概念282………………………………………7.1.2㊀机器装配的主要内容283………………………………………㊀目录5㊀………………………………7.1.3㊀装配精度与零件精度的关系284…………………………………………………………7.2㊀装配尺寸链286……………………………………7.2.1㊀装配尺寸链的基本概念286…………………………………………7.2.2㊀装配尺寸链的建立286……………………………………7.2.3㊀装配尺寸链的计算方法288…………………………………………7.3㊀保证装配精度的工艺方法289…………………………………………………7.3.1㊀互换装配法289………………………………………………………7.3.2㊀选配法292………………………………………………………7.3.3㊀修配法294………………………………………………………7.3.4㊀调整法296………………………………………………7.4㊀装配工艺规程的制订298…………………………………………7.4.1㊀装配工艺规程概述298…………………………7.4.2㊀装配工艺规程制订的方法和步骤298………………………………………7.5㊀装配自动化及先进装配技术305…………………………………………………………………思考与练习307……………………………………………………第8章㊀先进机械制造技术309………………………………………………………………㊀㊀8.1㊀概㊀述309…………………………………………………8.2㊀高速切削加工技术310…………………………………8.2.1㊀高速切削加工技术的定义310………………………………8.2.2㊀高速切削加工技术的优越性311…………………………………8.2.3㊀高速切削加工的关键技术311………………………………………8.2.4㊀高速切削加工的应用315 8.3㊀精密与超精密加工技术316…………………………………………………………………………………8.3.1㊀精密与超精密加工概述316……………………………………………8.3.2㊀超精密切削加工3198.3.3㊀超精密磨削加工320…………………………………………………………………………………………8.3.4㊀精密研磨与抛光320 8.4㊀纳米级加工技术330…………………………………………………………………………………8.4.1㊀纳米级加工的物理实质和特点330……………………………………8.4.2㊀扫描隧道显微加工技术332 8.5㊀快速原型制造技术336…………………………………………………………………………………………8.5.1㊀快速原型制造的概念336…………………………………………8.5.2㊀快速原型成形原理336……………………………………8.5.3㊀快速原型主要成形工艺338…………………………………………………………………思考与练习341…………………………………………………………………………参考文献342。
机械制造技术基础 考试复习资料
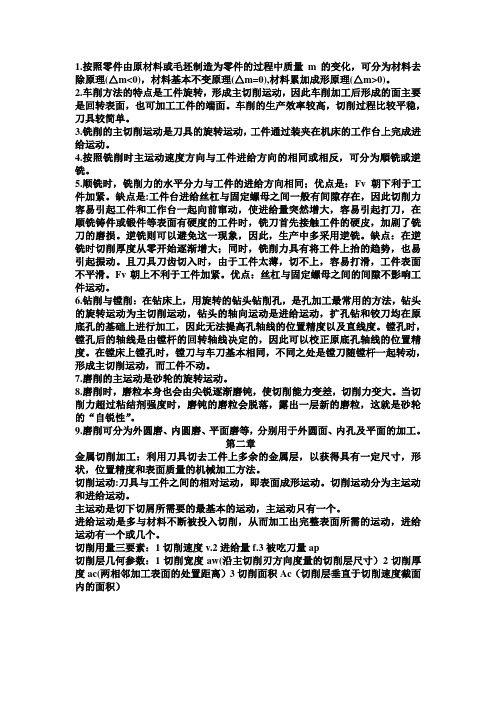
1.按照零件由原材料或毛坯制造为零件的过程中质量m的变化,可分为材料去除原理(△m<0),材料基本不变原理(△m=0),材料累加成形原理(△m>0)。
2.车削方法的特点是工件旋转,形成主切削运动,因此车削加工后形成的面主要是回转表面,也可加工工件的端面。
车削的生产效率较高,切削过程比较平稳,刀具较简单。
3.铣削的主切削运动是刀具的旋转运动,工件通过装夹在机床的工作台上完成进给运动。
4.按照铣削时主运动速度方向与工件进给方向的相同或相反,可分为順铣或逆铣。
5.顺铣时,铣削力的水平分力与工件的进给方向相同;优点是:Fv朝下利于工件加紧。
缺点是:工件台进给丝杠与固定螺母之间一般有间隙存在,因此切削力容易引起工件和工作台一起向前窜动,使进给量突然增大,容易引起打刀,在顺铣铸件或锻件等表面有硬度的工件时,铣刀首先接触工件的硬皮,加剧了铣刀的磨损。
逆铣则可以避免这一现象,因此,生产中多采用逆铣。
缺点:在逆铣时切削厚度从零开始逐渐增大;同时,铣削力具有将工件上抬的趋势,也易引起振动。
且刀具刀齿切入时,由于工件太薄,切不上,容易打滑,工件表面不平滑。
Fv朝上不利于工件加紧。
优点:丝杠与固定螺母之间的间隙不影响工件运动。
6.钻削与镗削:在钻床上,用旋转的钻头钻削孔,是孔加工最常用的方法,钻头的旋转运动为主切削运动,钻头的轴向运动是进给运动,扩孔钻和铰刀均在原底孔的基础上进行加工,因此无法提高孔轴线的位置精度以及直线度。
镗孔时,镗孔后的轴线是由镗杆的回转轴线决定的,因此可以校正原底孔轴线的位置精度。
在镗床上镗孔时,镗刀与车刀基本相同,不同之处是镗刀随镗杆一起转动,形成主切削运动,而工件不动。
7.磨削的主运动是砂轮的旋转运动。
8.磨削时,磨粒本身也会由尖锐逐渐磨钝,使切削能力变差,切削力变大。
当切削力超过粘结剂强度时,磨钝的磨粒会脱落,露出一层新的磨粒,这就是砂轮的“自锐性”。
9.磨削可分为外圆磨、内圆磨、平面磨等,分别用于外圆面、内孔及平面的加工。
机械制造技术基础复习资料(1)
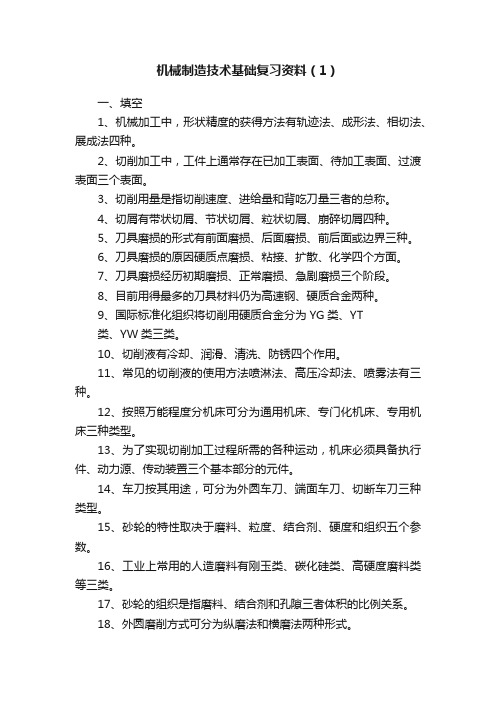
机械制造技术基础复习资料(1)一、填空1、机械加工中,形状精度的获得方法有轨迹法、成形法、相切法、展成法四种。
2、切削加工中,工件上通常存在已加工表面、待加工表面、过渡表面三个表面。
3、切削用量是指切削速度、进给量和背吃刀量三者的总称。
4、切屑有带状切屑、节状切屑、粒状切屑、崩碎切屑四种。
5、刀具磨损的形式有前面磨损、后面磨损、前后面或边界三种。
6、刀具磨损的原因硬质点磨损、粘接、扩散、化学四个方面。
7、刀具磨损经历初期磨损、正常磨损、急剧磨损三个阶段。
8、目前用得最多的刀具材料仍为高速钢、硬质合金两种。
9、国际标准化组织将切削用硬质合金分为YG类、YT类、YW类三类。
10、切削液有冷却、润滑、清洗、防锈四个作用。
11、常见的切削液的使用方法喷淋法、高压冷却法、喷雾法有三种。
12、按照万能程度分机床可分为通用机床、专门化机床、专用机床三种类型。
13、为了实现切削加工过程所需的各种运动,机床必须具备执行件、动力源、传动装置三个基本部分的元件。
14、车刀按其用途,可分为外圆车刀、端面车刀、切断车刀三种类型。
15、砂轮的特性取决于磨料、粒度、结合剂、硬度和组织五个参数。
16、工业上常用的人造磨料有刚玉类、碳化硅类、高硬度磨料类等三类。
17、砂轮的组织是指磨料、结合剂和孔隙三者体积的比例关系。
18、外圆磨削方式可分为纵磨法和横磨法两种形式。
19、无心外圆磨削有贯穿磨法和切入磨法两种磨削方式。
20、齿轮加工按其加工原理可分为成形法和展成法两类。
21、齿轮精加工常用剃齿、珩齿和磨齿三种方法。
22、圆周铣削有逆铣和顺铣两种方式。
23、在孔加工中,钻孔和扩孔统称为钻削。
24、刨床类机床主要有牛头刨床、龙门刨床和插床三种类型。
25、配合选择常用的方法有类比法、计算法和实验法三种。
26、加工精度包括尺寸精度、形状精度、位置精度三个方面。
27、加工表面质量是指表面粗糙度、波度、及表面层的物理机械性能。
28、表面层冷作硬化程度,从冷硬层深度h、表面层的显微硬度及硬化程度N表示。
机械制造技术基础答案

(一)判断题1.车床的主运动是工件的旋转运动,进给运动是刀具的移动。
(√)2.钻床的主运动是钻头的旋转运动,进给运动是钻头的轴向移动。
(√)3.铣床的主运动是刀具的旋转运动,进给运动是工件的移动。
(√)4.牛头刨床刨斜面时,主运动是刨刀的往复直线运动,进给运动是工件的斜向间歇移动。
(X )5.龙门刨床刨水平面时,主运动是刨刀的往复直线运动,进给运动是工件的横向间隙移动。
(X )6.车床的主运动和进给运动是由两台电动机分别带动的。
(X )7.立铣的主运动和进给运动是由一台电动机带动的。
(X )8.牛头刨床的切削速度是指切削行程的平均速度。
(X)9.车槽时的背吃刀量(切削深度)等于所切槽的宽度。
(√)10.刀具前角是前刀面与基面的夹角,在正交平面中测量。
(√)11.刀具后角是主后刀面与基面的夹角,在正交平面中测量。
(X )12.刀具主偏角是主切削平面与假定工作平面间的夹角(即主切削刃在基面的投影与进给方向的夹角。
(√)13.工艺系统刚度较差时(如车削细长轴),刀具应选用较大的主偏角。
(√)14.在切削用量中,对切削力影响最大的是前角和后角。
(X )15.CA6140型机床是最大工件回转直径为140mm的卧式车床。
(X )16.X5020立式升降台铣床的工作台面宽度为200mm。
(√)17.在加工质量方面,铣削和刨削一般同级,但对于尺寸较大的平面,由于刨削无明显的接刀痕,故刨削优于铣削。
(√)18.磨削过程实际上是许多磨粒对工件表面进行切削、刻划和滑擦(摩擦抛光)的综合作用过程。
(√)19.磨具的组织标注出磨具中磨料、结合剂和气孔三者之间不同体积的比例关系。
(√)20.磨具的硬度是指组成磨具的磨料的硬度。
(X)21.光磨可提高工件的形状精度和位置精度。
(X)(二)单选题(请将正确选项的序号填入题后的括号内)1.通过切削刃选定点的基面是:①垂直于假定主运动方向的平面√;②与切削速度相平行的平面;③与过渡表面相切的表面。
- 1、下载文档前请自行甄别文档内容的完整性,平台不提供额外的编辑、内容补充、找答案等附加服务。
- 2、"仅部分预览"的文档,不可在线预览部分如存在完整性等问题,可反馈申请退款(可完整预览的文档不适用该条件!)。
- 3、如文档侵犯您的权益,请联系客服反馈,我们会尽快为您处理(人工客服工作时间:9:00-18:30)。
又:tm
Lw d w L dw w T m 1000 v f a p 1000 A f a p
将上式代入式(4-14),对T求导,并令其为0,可得到 最大生产率刀具寿命为:
1 m Top tc m
磨钝标准的定义:刀具后刀面磨损带中间的平均 磨损量VB允许达到的最大磨损尺寸。(P54表4-1) 精加工刀具,以沿工件径向的刀具磨损尺寸作 为刀具的磨钝标准,称为刀具的径向磨损量NB。
图2-21 刀具磨钝标准 (纵向剖面)
4.2 刀具耐用度及切削量的选择
刀具耐用度概念
◆ 刀具由刃磨后用于切削开始至磨损量达到磨钝标准为 止的总切削时间。(两次刃磨之间的总切削时间。)
⑴ 磨损过程:
在高温高压下,刀具材料中的元素扩散到切屑 和工件材料中,工件材料中的铁元素又扩散到刀具 表层,从而改变了刀具表层的化学成分,使其硬度 和强度下降,磨损加剧。
⑵ 发生场合:
元素的耐热性差,则原子的稳定性差,易发生 扩散磨损;元素的耐热性好,则原子的稳定性好, 不易发生扩散磨损。
4)氧化磨损
破损信号
图3-29 声发射钻头破损检测装置系统图
flash
3.3 刀具耐用度的选择
一是根据单件工时最短的观点来确定耐 用度,这种耐用度称为最大生产率耐用度; 二是根据工序成本最低的观点来确定的耐用 度,称为经济耐用度。 在一般情况下均采用经济耐用度,当任 务紧迫或生产中出现不平衡环节时,则采用 最大生产率耐用度。
Thank you for your listening!
3.5
切削液的选择
3.5.1 切削液的作用 (1)冷却作用 (2)润滑作用 (3)清洗作用 (4)防锈作用 3.5.2 切削液的选用 (1)根据刀具材料 (2)根据工件材 料 (3)根据加工性质
返回本章目录
3.5.3 切削液的使用方法 (1)浇注法 (2)高压冷却法
2.后刀面的磨损:
⑴ 后刀面磨损的特征
B区
刀尖
VBmax
N区
C区
待加工表面有上道工序产生的加工硬化或毛坯 表面硬层的影响
N区
⑴ 后刀面磨损的特征
后刀面临近切削刃处因磨损而产生沟痕,由于切削中各 个部位的切削条件不同,沿切削刃的磨损是不均匀的:
① C区:在靠近刀尖的位置。 特征:此部位切削过程中承受较大的切削力和较 高的切削温度,强度和散热条件差,所以磨损较 大。其磨损量用VC表示。 ② N区:在靠近工件待加工表面的位置。 特征:由于加工表面的加工硬化或毛坯表面硬层 的影响,会在此部位造成较大的磨损且形成磨损 缺口。其磨损量用VN表示; ③ B区:在参与切削的切削刃中部区域。 特征:磨损比较均匀,其平均磨损量用VB表示。
4.2 刀具耐用度及切削量的选择
最大生产率寿命
使工序时间最短的刀具寿命。以车削为例,工序时间:
tm to t m t a tc分别为工序时间、基本时间、辅助 时间和换刀时间;T 为刀具寿命。令f,ap为常数,有:
v T m A
n —— 指数, 2.5 ~ 5; p —— 指数, 1.2 ~ 1.8 ; q —— 指数, 0.6 ~ 0.8 ;
可见v 的影响最显著;f 次之;ap 影响最小 。所以根据刀具耐用度选择切 削用量时,应首先选择较大的切削深度,然后选择较大的进给量,最后在刀 具耐用度和机床功率允许的条件下选取适当的切削速度。
•
1.机械擦伤磨损 如图5—1所示,车刀在切除工件上金属层使之转变成切屑,并形成加工表 面过程中,在有压力接触的前刀面与切屑之间、后刀面与工件表面之间的相对运 动中,当工件和切屑k的硬质点(如碳化物和积屑瘤碎片等)流经刀具表面时,就像 砂轮亡的磨粒一样,在前后刀面上划出间痕或擦掉一些刀具材料,使刀具磨 第144页损,这种机械擦伤磨损又称磨粒磨损。 2.热效应磨损 热效应磨损是由于车刀切削工件时产生的切削温度引起的物理、化学综合作 用造成的刀具磨损。下面举例说明。 [例5-1] 高速钢车刀切削时,当切削温度超过相变温度(550~650℃)时,刀 具表面金相组织发生变化,使马氏体组织转变为托氏体或索氏体组织,则硬度下 降,而使刀具产生相变磨损。 [例5-2] 硬质合金车刀切削时,当切削温度超过850~950℃时,刀—屑之间、 刀—工件之间的分子活动能量加大,使两摩擦面间的化学元素相互扩散到对方去。 如刀具中的碳、钨、钴、钛(C、W、Co、Ti)等元素向工件、切屑中扩散,而工 件和切屑中的铁(Fe)元素则向刀具中扩散,这就改变了硬质合金的表层组织,使 其硬度和强度下降,使刀具产生扩散磨损。 前者是刀具的正常磨损,后者使刀具产生急剧磨损。其磨损结果,将使刀具 的几何形状被改变,切削性能丧失。而更严重的是还将造成以下加工质量问题。 ①造成零件直径尺寸不准确。如图5—2所示,车削外圆和内孔时由于刀尖 磨损,刀尖位置后退,使工件直径发生变化。如图5—2(a)的d变为d',图5—2(L) 的蛔变为D',所示,造成零件加工尺寸不准确而影响精度。 ②零件的表面粗糙度增大。由于刀具磨损,改变了刀刃和刃口的质量,使粗 糙的刀刃轮廓原封不动地复印在加工表面上。而圆钝的刃口挤压摩擦加工表面, 造成工件表面粗糙不光的程度增大。
切削速度对刀具磨损强度的影响
返回本章目录
4.1 刀具磨损的形式及原因 刀具的磨损过程
后刀面磨损量
初期磨损
正常磨损
剧烈磨损
D C B
时间
A
刀具磨损的典型曲线
1.初期磨损 图中AB段 • 特点:磨损较快 • 机理: ⑴新刃磨的刀具表面粗糙不平,接触应力大; ⑵新刀表面有脱碳层、氧化层等表面缺陷。 2.正常磨损 图中BC段 • 特点:磨损量随切削时间缓慢均匀增大,切削过程稳 定 • 该磨损阶段是刀具的有效工作时间。 3.剧烈磨损 图中CD段 • 特点:刀具材料切削性能急剧下降,磨损迅速。 • 机理: 刀具变钝,摩擦过大,切削力与切削温度迅速增长。
Top
刀具费用 ta C m 刀具耐用度
图3-28 经济寿命 (3-19)
Ct 1 m Top tc Cm m
3.5.4 刀具磨损、破损检测与监控
常规方法
规定刀具切削时间,离线检测
切削力与切削功率检测方法
通过切削力(切削功率)变化幅值,判断刀具的磨损程 度;当切削力突然增大或突然下降很大幅值时,则表明 刀具发生了破损 通过实验确定刀具磨损与破损的“阈值”
⑵ 产生后刀面磨损的场合 ① 用较低的切削速度和较小的切削厚度切削塑性 材料; ②切削脆性材料。 (3)影响: 切削力↑, 切削温度↑, 产生振动,降低加工质量
⑶前刀面和后刀面同时磨损
4.1 刀具磨损的形式及原因 刀具磨损原因
1)磨料磨损(硬质点磨损) ⑴ 定义:切屑或工件表面的微小硬质点 与刀具表面的相对运动中,在刀具表面划出 沟痕的磨损称为磨料磨损。
1.前刀面磨损
(1)前刀面磨损的特征 ①磨损后在前刀面上形成了一个月牙洼 ②月牙洼和刀刃之间有一个窄边; ③随着磨损的加剧,月牙洼不断扩展,该 窄边越来越窄,最后导致刀刃崩刃。 ⑵ 发生前刀面磨损的场合: 用较高的切削速度和较大的切削厚度切削 塑性材料时产生前刀面磨损。 (3)影响: 削弱刀刃强度,降低加工质量
后刀面磨损量VB
刀具磨损曲线
4.2 刀具耐用度及切削量的选择
刀具耐用度标准
综合生产效率和生产成本所确定的刀具耐用度。 刀具的磨钝标准是固定的,而刀具的耐用度则是可 以变化的,在切削加工中,可以通过改变加工条件提 高刀具的耐用度,也就是说,延长刀具达到磨钝标准 的时间。
1) 最大生产率耐用度:保证单件工时最短、生产
(3)喷雾冷却法
返回本章目录
至第四章
VBmax
a)
b)
刀具磨损形态
3.5.1 刀具磨损
◆ 非正常磨损 破损(裂纹、崩刃、破碎等),卷刃(刀刃塑性变形)
刀具磨损过程 3个阶段(图3-26)
后刀面磨损量VB
初期磨损 正常磨损 急剧磨损
切削时间
图3-26 刀具磨损过程
磨钝标准 常取后刀面最大允许磨损量VB
返回本章目录
4.1 刀具磨损的形式及原因
刀具磨损的形式
图4-1 车刀典型磨损形式示意图
• 刀具耐用度标准:综合生产效率和生产成本所确 定的刀具耐用度。 刀具磨钝是确定的,刀具的耐用度是可以变化的, 在切削加工中,可以通过改变加工条件提高刀具 的耐用度,也就是说,延长刀具达到磨钝标准的 时间。 • 最大生产率耐用度:保证单件工时最短、生产率 最高的耐用度; • 经济耐用度:保证加工成本最低、经济效益最好 的耐用度。
⑴ 磨损过程: 空气中的氧与刀具硬质合金中的钴和碳化钨等 发生氧化作用,产生疏松脆弱的氧化物。切削时这 些氧化物被切屑和工件带走,形成刀具的氧化磨损。 ⑵ 发生场合: 硬质合金中的碳化钛含量较低时,则氧化较快, 易发生氧化磨损。
5)相变磨损
切削温度超过相变温度时,刀具金相组织发生变 化,使表层的硬度下降造成刀具的相变磨损。 发生场合:工具钢刀具磨损的主要原因。
率最高的耐用度;
2) 经济耐用度:保证加工成本最低、经济效益最好
的耐用度。 在一般情况下均采用经济耐用度,当任务紧迫或生产 中出现不平衡环节时,则采用最大生产率耐用度。
4.3 切削液
切削液的作用 (1)冷却作用 (3)清洗作用 (2)润滑作用 (4)防锈作用
切削液的种类
(1)水溶液 (2)乳化液 (3)切削油
4.3 切削液
添加剂
◆ 油性添加剂 ◆ 极压添加剂 ◆ 表面活性剂
切削液的选用
◆ ◆ ◆ ◆ 按工件材料选用 按加工要求选用 按刀具材料选用 按加工方法选用
Thank you for your listening!
作业:
1、刀具耐用度的定义? 2、刀具磨损的原因及磨钝标准的定义? 3、切削用量三要素对切削力的影响与对刀具 耐用度的影响有什么不同?