机械加工质量技术方案的优化
机械制造行业中的产品质量问题与提升措施

机械制造行业中的产品质量问题与提升措施一、引言机械制造行业作为制造业的重要组成部分,在经济发展中起着举足轻重的作用。
然而,随着市场竞争的加剧和消费者对产品质量要求的提高,机械制造行业面临着产品质量问题。
本文将探讨机械制造行业中存在的产品质量问题,并提出一些可行的提升措施。
二、机械制造行业中存在的产品质量问题1. 设计不合理导致的质量问题在机械制造过程中,设计环节是至关重要的。
一些企业在设计阶段没有充分考虑产品使用环境和用户需求,导致制品功能不全、易损坏或无法维修等问题。
此外,设计上的缺陷也可能导致使用不便或安全隐患。
2. 加工工艺不当引发的质量问题加工工艺是决定产品质量的关键之一。
一些企业为了降低成本,采用低质量原材料或粗糙加工技术,导致产品强度低下、易磨损或容易出现故障等。
此外,生产过程中可能存在操作不规范、设备老化等问题,也会影响产品质量。
3. 材料选择不当带来的质量问题机械制造行业涉及到多种材料的选择。
若选择不当,可能导致产品使用寿命缩短、易腐蚀或易燃等问题。
一些企业追求短期利益,使用劣质材料或夹带有害物质的材料,给用户带来安全隐患。
4. 售后服务不完善造成的质量问题售后服务是衡量企业综合实力和产品品质的重要指标。
一些企业在售后服务方面存在问题,无法及时解决用户遇到的故障或提供技术支持,给消费者造成了困扰和损失。
三、提升机械制造行业产品质量的措施1. 强化设计能力与标准化管理加强设计环节,在设计之初就要考虑产品使用环境和用户需求,进行全面而合理地分析评估,并制定科学合理的设计方案。
建立完善的设计标准和规范,并严格执行,在确保产品功能和性能的基础上提高设计可靠性和稳定性。
2. 优化生产工艺与质量控制加强对生产工艺的研究和创新,采用先进、精确的加工设备和技术,提高产品的加工精度和外观质量。
建立严格的过程控制体系,实施全面质量管理,确保每个环节都符合标准要求,并进行全面检测和测试。
3. 选择优质材料与供应商加强对材料的选择与使用管理,选择优质可靠的供应商,并建立长期稳定的合作关系。
机械制造工艺改进方案
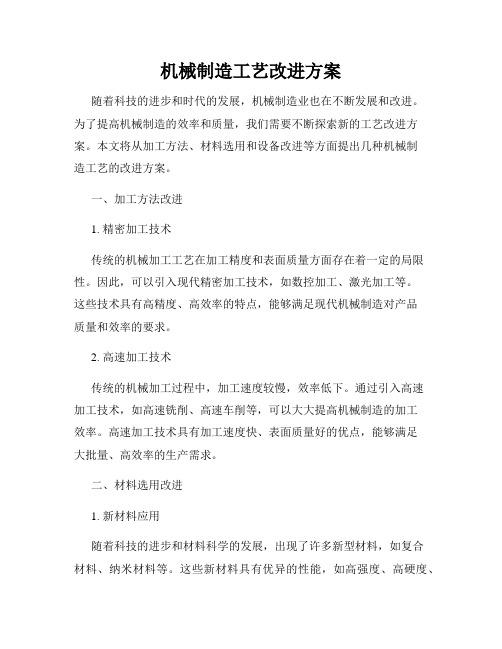
机械制造工艺改进方案随着科技的进步和时代的发展,机械制造业也在不断发展和改进。
为了提高机械制造的效率和质量,我们需要不断探索新的工艺改进方案。
本文将从加工方法、材料选用和设备改进等方面提出几种机械制造工艺的改进方案。
一、加工方法改进1. 精密加工技术传统的机械加工工艺在加工精度和表面质量方面存在着一定的局限性。
因此,可以引入现代精密加工技术,如数控加工、激光加工等。
这些技术具有高精度、高效率的特点,能够满足现代机械制造对产品质量和效率的要求。
2. 高速加工技术传统的机械加工过程中,加工速度较慢,效率低下。
通过引入高速加工技术,如高速铣削、高速车削等,可以大大提高机械制造的加工效率。
高速加工技术具有加工速度快、表面质量好的优点,能够满足大批量、高效率的生产需求。
二、材料选用改进1. 新材料应用随着科技的进步和材料科学的发展,出现了许多新型材料,如复合材料、纳米材料等。
这些新材料具有优异的性能,如高强度、高硬度、耐磨损等,能够满足特殊工况下的要求。
因此,在机械制造过程中,可以适当引入新材料的应用,以提高产品的性能和品质。
2. 绿色环保材料随着全球环保意识的不断提高,绿色环保材料的应用也越来越受到重视。
在机械制造中选择绿色环保材料可以降低对环境的污染,减少资源的消耗,提高产品的可持续性。
因此,我们可以在材料选用上考虑绿色环保材料,如可降解材料、再生材料等。
三、设备改进1. 自动化设备传统的机械制造过程中,往往需要大量的人工操作,效率低下。
而引入自动化设备可以替代人工操作,提高生产效率和产品质量,减少人力成本。
自动化设备具有高效率、高精度等优点,能够适应现代机械制造的发展需求。
2. 智能化设备随着人工智能技术的发展,智能化设备在很多领域得到了应用。
在机械制造中,可以引入智能化设备,如智能机器人、智能生产线等。
这些设备能够自动完成工艺过程,具有高度的灵活性和智能化的特点,能够提高生产效率和产品质量。
综上所述,机械制造工艺的改进方案主要包括加工方法的改进、材料选用的改进以及设备的改进。
机械加工改善方案(一)

机械加工改善方案(一)机械加工改善方案资料介绍本方案旨在通过改善机械加工流程和设备,提高生产效率和产品质量。
通过引入先进的技术和优化操作流程,可以显著改善机械加工的效果。
方案内容1. 优化工艺流程•分析现有工艺流程,找出可能存在的瓶颈和改进点•研究最佳的工艺流程,并进行试验验证•制定新的工艺流程并进行培训,确保操作人员能够熟练掌握2. 引入先进设备•评估现有机械设备的性能和功能,确定是否需要更新或升级•寻找符合生产需求的先进设备,并进行采购和安装•培训操作人员掌握新设备的使用和维护方法3. 优化刀具选择和切削参数•建立刀具管理系统,定期检查刀具状态并及时更换或维修•通过实验和数据分析,确定合适的刀具选择和切削参数,以提高加工效果和延长刀具寿命4. 自动化和智能化改造•增加自动化生产线,减少人工操作,并提高生产效率和产品质量•探索智能化改造的可能性,如引入机器人和人工智能技术,以进一步提升机械加工的水平和效益5. 质量控制和连续改进•建立完善的质量控制体系,确保产品质量稳定可靠•通过持续改进,不断优化机械加工过程,提高生产效率和产品质量结论通过本方案的实施,我们将能够显著改善机械加工过程,提高生产效率和产品质量。
通过优化工艺流程、引入先进设备、优化刀具选择和切削参数、自动化和智能化改造,以及加强质量控制和连续改进,我们可以实现机械加工的整体升级和提升。
6. 培训和技术支持•为操作人员提供必要的培训,包括新工艺流程、新设备的使用和维护方法以及质量控制知识。
•提供定期的技术支持和咨询服务,解答工艺和设备方面的问题,确保顺利实施和运行。
7. 资源节约和环保措施•评估并优化能源利用,采取节能措施,降低生产成本。
•优化废料处理方案,确保符合环保要求,减少对环境的影响。
8. 安全管理•建立完善的安全管理制度,明确责任和操作规范。
•定期进行安全培训,提高员工的安全意识和应急响应能力。
9. 绩效评估和数据分析•设立明确的绩效指标,对机械加工流程进行评估,进行监控和数据分析。
机械工程加工质量控制措施

机械工程加工质量控制措施摘要:近年来,随着我国工业的发展和进步,各行各业对机械工程的需求越来越大。
但在实际的机械工程加工中,不可避免地会出现一些误差,影响加工质量和水平。
对机械工程来说,合理控制和提高加工质量是非常重要的,对各行业的发展起着重要的作用。
从企业角度来说,对于机械产品质量的最终要求是很严格的,但是,难免在对机械产品加工的过程中出现各种问题,是我们有待于解决的,因此,我们要想办法控制对机械产品加工质量并严格管理其过程。
对于新设备要加强研究,在机械工程设备安装过程中做好管理优化,提升项目工程质量和效率,提高经济效益和安全性。
本文对机械工程加工的质量控制进行了分析,并提出了相应的质量控制措施,具有十分重要的现实意义。
关键词:机械工程;加工质量;控制导言当今社会,生产技术不断提高,人类社会的机械化也得到广泛普及,促进了机械制造企业的发展,对产品质量也提出了更高的要求,这直接影响到机械制造企业的经营和发展。
影响机械制造企业产品质量的因素很多。
企业应该从多方面努力,为提高产品质量做出贡献。
现代企业要想在竞争激烈的市场环境中生存并取得更好的发展,就必须提高自身的机械制造水平。
要做到这一点,最重要的是优化企业现有的加工质量。
加工质量的关键在于加工精度,因此加工精度是一个值得关注的问题。
研究工程机械设备高效利用新方法,建设高质量工程。
让企业成长。
科学管理,运用好工程机械设备。
取得良好的经济效益。
1机械加工过程中质量控制的问题1.1机械的精度机械的精度决定着机械制造业、产品的质量以及加工后的产品是否符合标准。
主要决定因素是各部分的协调和加工材料的使用。
在这个过程中,为了保证产品的精度,这并不是唯一的方法,因为这样会导致生产效率的下降。
但如果不注意精度,机器零件也会损坏,仍然难以保证机器的生产能达标。
1.2机械加工变形问题在机械制造过程中,切削和磨削技术是主要的技术,而这两种技术的使用,实际上是对零件的极大损耗。
机械加工质量控制

机械加工质量控制标题:机械加工质量控制引言概述:机械加工质量控制是一个关键的环节,直接影响到产品的质量和性能。
通过合理的质量控制措施,可以提高机械加工的精度和效率,降低产品的缺陷率和不合格率。
本文将从五个方面介绍机械加工质量控制的重要性和具体措施。
一、材料选择1.1 选择合适的材料:根据产品的要求和使用环境,选择适合的材料。
考虑材料的强度、硬度、耐磨性等特性,以确保产品的使用寿命和性能。
1.2 检查材料质量:对进货的材料进行严格的质量检查,包括外观、尺寸、化学成分等方面。
确保材料的质量符合标准要求,避免因材料质量问题导致的加工缺陷。
1.3 控制材料变形:在机械加工过程中,材料的变形会直接影响产品的尺寸精度和形状。
通过合理的加工工艺和工装设计,控制材料的变形,保证加工精度。
二、加工工艺控制2.1 设计合理的加工工艺:根据产品的要求和材料的特性,设计合理的加工工艺流程。
考虑加工顺序、切削参数、刀具选择等因素,以确保加工的精度和效率。
2.2 严格的加工过程控制:在加工过程中,严格执行加工工艺要求,控制各个环节的加工参数。
包括切削速度、进给量、刀具磨损等方面的控制,以保证加工的一致性和稳定性。
2.3 定期检查和维护设备:定期对加工设备进行检查和维护,确保设备的正常运行。
包括设备的润滑、刀具的更换、机床的校准等方面,以保证加工的稳定性和精度。
三、质量检验与控制3.1 制定合理的检验标准:根据产品的要求和行业标准,制定合理的质量检验标准。
包括尺寸精度、表面质量、材料成分等方面的要求,以确保产品的质量符合要求。
3.2 使用合适的检测设备:选择适合的检测设备和方法,对产品进行全面的质量检测。
包括三坐标测量机、硬度计、显微镜等设备的使用,以保证检测的准确性和可靠性。
3.3 建立完善的质量控制体系:建立完善的质量控制体系,包括质量记录、异常处理、追溯体系等方面。
通过对质量数据的分析和整理,及时发现和解决质量问题,提高产品的质量稳定性。
探讨数控机械加工效率优化措施

探讨数控机械加工效率优化措施1. 引言1.1 研究背景数控机械加工是现代制造业中不可或缺的重要技术手段,具有高效、精准和稳定的加工特点。
随着科技的发展和市场需求的不断变化,对数控机械加工效率提出了更高的要求,因此如何优化数控机械加工效率成为了当前研究的热点之一。
在过去的研究中,很多学者都从不同角度对数控机械加工效率进行了探讨,但随着制造业的转型升级和技术的不断创新,对数控机械加工效率优化的研究依然具有重要的现实意义。
有必要系统总结和分析数控机械加工效率的优化措施,为进一步提高数控机械加工效率提供理论和实践上的支持。
本文将从数控机械加工的基本原理出发,深入探讨影响数控机械加工效率的因素,并针对这些因素提出相应的优化措施。
我们将详细介绍优化加工工艺流程的方法和优化刀具选择和切削参数的技术,以期为提高数控机械加工效率提供有效的参考。
通过本文的研究,我们可以更好地了解数控机械加工效率优化的重要性,并为未来的相关研究提供参考和启示。
1.2 研究意义探讨数控机械加工效率优化的重要性在于提高生产效率,降低生产成本,增加企业竞争力。
随着工业生产的不断发展,数控机械加工已成为现代制造业的重要环节,其效率直接影响到产品质量和生产周期。
通过优化加工流程和选择合适的刀具和切削参数,可以有效提高数控机械加工的效率,减少加工时间和材料浪费。
优化措施还能够提高加工精度和表面质量,增加产品的市场竞争力。
数控机械加工效率优化研究不仅对企业生产具有重要意义,还能促进制造业的发展和升级。
通过优化加工流程和刀具选择,可以降低能源消耗和环境污染,推动工业绿色化发展。
优化措施也可以提高加工人员的技术水平和工作环境,促进员工培训和技术创新。
深入探讨数控机械加工效率优化措施的意义重大,对于提高产业发展水平,推动制造业转型升级具有重要的现实意义。
2. 正文2.1 数控机械加工的基本原理数控机床是一种根据预先编好的加工程序来控制刀具和工件相对位置、速度、转速和进给量等加工工艺参数的机器。
机械加工质量技术控制[方案]
![机械加工质量技术控制[方案]](https://img.taocdn.com/s3/m/5b6b9735492fb4daa58da0116c175f0e7cd11916.png)
机械加工质量技术控制摘要:本文介绍了机械加工精度的概念及内容,分析了机械加工产生误差的原因,最后提出提高机械加工精度的工艺措施。
关键词:机械加工精度;几何误差;定位误差;工艺1机械加工精度的概念及内容机械加工精度是指零件加工后的实际几何参数(尺寸、形状和位置)与理想几何参数相符合的程度。
它们之间的差异称为加工误差。
加工误差的大小反映了加工精度的高低。
误差越大加工精度越低,误差越小加工精度越高。
加工精度包括三个方面内容:尺寸精度指加工后零件的实际尺寸与零件尺寸的公差带中心的相符合程度;形状精度指加工后的零件表面的实际几何形状与理想的几何形状的相符合程度;位置精度指加工后零件有关表面之间的实际位置与理想。
在相同中的各种因对准确和完足产品的工加工方法,的生产条件下所加工出来的一批零件,由于加工素的影响,其尺寸、形状和表面相互位置不会绝全一致,总是存在一定的加工误差。
同时,从满作要求的公差范围的前提下,要采取合理的经济以提高机械加工的生产率和经济性。
2机械加工产生误差主要原因2.1机床的几何误差加工中刀具相对于工件的成形运动一般都是通过机床完成的,因此,工件的加工精度在很大程度上取决于机床的精度。
机床制造误差对工件加工精度影响较大的有:主轴回转误差、导轨误差和传动链误差。
机床的磨损将使机床工作精度下降。
(1)主轴回转误差,机床主轴是装夹工件或刀具的基准,并将运动和动力传给工件或刀具,主轴回转误差将直接影响被加工工件的精度。
(2)导轨误差,导轨是机床上确定各机床部件相对位置关系的基准,也是机床运动的基准。
除了导轨本身的制造误差外,导轨的不均匀磨损和安装质量,也使造成导轨误差的重要因素。
导轨磨损是机床精度下降的主要原因之一。
(3)传动链误差,传动链误差是指传动链始末两端传动元件间相对运动的误差。
一般用传动链末端元件的转角误差来衡量。
2.2 刀具的几何误差刀具误差对加工精度的影响随刀具种类的不同而不同。
采用定尺寸刀具成形刀具展成刀具加工时,刀具的制造误差会直接影响工件的加工精度;而对一般刀具,其制造误差对工件加工精度无直接影响。
机械制造行业中零部件质量问题的原因及改进方案
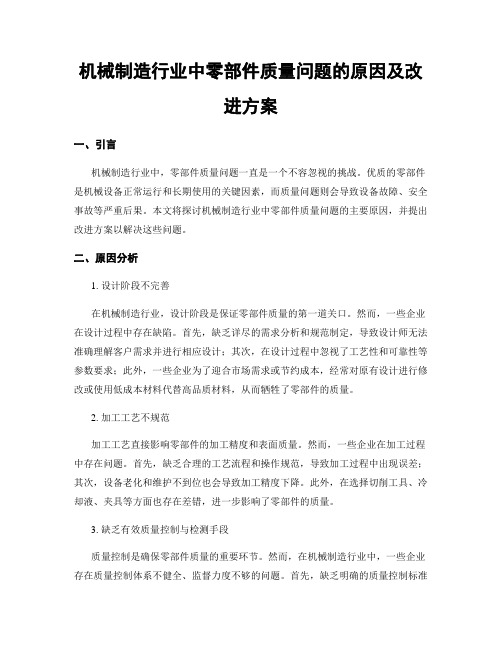
机械制造行业中零部件质量问题的原因及改进方案一、引言机械制造行业中,零部件质量问题一直是一个不容忽视的挑战。
优质的零部件是机械设备正常运行和长期使用的关键因素,而质量问题则会导致设备故障、安全事故等严重后果。
本文将探讨机械制造行业中零部件质量问题的主要原因,并提出改进方案以解决这些问题。
二、原因分析1. 设计阶段不完善在机械制造行业,设计阶段是保证零部件质量的第一道关口。
然而,一些企业在设计过程中存在缺陷。
首先,缺乏详尽的需求分析和规范制定,导致设计师无法准确理解客户需求并进行相应设计;其次,在设计过程中忽视了工艺性和可靠性等参数要求;此外,一些企业为了迎合市场需求或节约成本,经常对原有设计进行修改或使用低成本材料代替高品质材料,从而牺牲了零部件的质量。
2. 加工工艺不规范加工工艺直接影响零部件的加工精度和表面质量。
然而,一些企业在加工过程中存在问题。
首先,缺乏合理的工艺流程和操作规范,导致加工过程中出现误差;其次,设备老化和维护不到位也会导致加工精度下降。
此外,在选择切削工具、冷却液、夹具等方面也存在差错,进一步影响了零部件的质量。
3. 缺乏有效质量控制与检测手段质量控制是确保零部件质量的重要环节。
然而,在机械制造行业中,一些企业存在质量控制体系不健全、监督力度不够的问题。
首先,缺乏明确的质量控制标准和流程,导致生产过程中无法及时发现和纠正问题;其次,在零部件检测方面,缺乏高效准确的测试设备和技术手段限制了对零部件质量进行全面监管。
三、改进方案1. 加大设计阶段的投入为了提高零部件质量,并避免后期出现问题需要重新投入大量时间和成本进行修复,企业应该加大设计阶段的投入。
首先,完善需求分析和规范制定,确保设计师准确理解客户需求并制定合理的设计方案;其次,在设计过程中加强工艺和可靠性分析,注重材料选择等关键环节;此外,提高设计师的专业能力和技术水平也是必要的步骤。
2. 规范加工工艺为了确保零部件的加工精度和表面质量,企业应该规范加工工艺。
- 1、下载文档前请自行甄别文档内容的完整性,平台不提供额外的编辑、内容补充、找答案等附加服务。
- 2、"仅部分预览"的文档,不可在线预览部分如存在完整性等问题,可反馈申请退款(可完整预览的文档不适用该条件!)。
- 3、如文档侵犯您的权益,请联系客服反馈,我们会尽快为您处理(人工客服工作时间:9:00-18:30)。
机械加工质量技术方案的优化
作者:张志刚
来源:《科技创新与应用》2013年第27期
摘要:机械加工企业的发展,离不开其机械加工生产环节、管理环节的应用,这是保证机械加工质量稳定提升的一个重要条件。
文章就机械加工的相关精度概念展开一系列的分析,根据影响机械加工质量相关问题的产生因素展开剖析,保障其机械加工质量体系的健全。
关键词:机械加工精度;定位误差;存在问题
前言
在实际生活中,影响机械加工环节的因素是比较多的,比较常见的是机械加工厂的内部环境,这会直接影响机械加工质量环节的稳定运行,这就需要针对这些问题,展开机械加工管理制度、机械加工规范制度的优化,以实现机械加工环节综合效益的提升。
1 关于机械加工精度及其误差环节的分析
1.1 在机械加工环节中,由于相关因素的影响,其机械加工精度是难以得到有效控制,一般来说,所谓的机械加工精度,就是零件加工过后的几何参数和理想几何参数的符合状况,他们之间的差异越小,其加工误差也就越小,也就实现了其加工精度的提升。
反之,如果不能对其技工误差的有效控制,就会导致其加工精度的降低。
尺寸精度环节对于加工精度的影响是非常大的,该环节主要是理想尺寸和现实尺寸之间的区别。
形状精度环节是影响机械加工环节的重要因素,通过对这一环节的优化,可以保证日常工作的稳定开展。
所谓的形状精度就是加工后的零件形状和零件理想形状之间的吻合度。
所谓的位置精度,就是零件加工前后的其理想位置和实际位置之间的协调。
产品的有效生产,离不开其产品加工模式的应用,这可以实现其零件质量的综合效益的提升,从而满足现实工作的需要。
通过对其加工要素的分析,可以导致影响机械加工质量的因素是很多的,比如其表面形状、尺寸问题等,由于这些环节的差错,就容易产生加工误差。
需要针对这些误差,展开分析,保障其日常工作的生产率及其质量的提升。
由于其刀具的影响,也会导致机械加工精度的变化,这些活动都是在机床上运行的,受到机床精度的影响,工件的加工精度或多或少的发生相关变化。
工件加工精度的影响因素是比较多的,比如机床制造误差环节,比如传动链的误差环节、导轨误差环节、主轴回转误差环节等,都一定程度影响工件的精确程度。
由于长时间的工作应用,正是由于上述环节的影响,其机床工作精度会发生相关的变化。
导轨误差的出现,离不开其机床部位的各个位置关系的联系,这是机床稳定运行的一个判断条件。
由于其导轨自身制作误差的影响,就容易产生其安装过程中的各个质量问题,比如不均匀磨损的问题,导致其导轨误差的加大。
通过对导轨磨损环节的优化,可以保证其机床精度的提升。
所谓的传动链误差,就是传动链的始末两个方向元件运动的相关误差。
1.2 刀具误差也是影响加工精度的重要环节,设计基准的差异,也会导致工件的精度的变化,我们把这些基准称之为设计基准,在日常工作过程中,通过对工序图的应用,实现其加工表面加工尺寸的规划,这就是工序基准。
在机床工件加工过程中,要通过对工件的几何要素的应用,实现其定位基准环节的优化,这需要保证其设计基准和定位基准的相对吻合性,如果不能保证该环节,就会出现基准不重合误差的现象,这是不利于加工工件的自身精度的提升,上述环节的稳定运行,离不开其定位副制造误差的有效控制。
通过对夹具定位元件的有效应用,以符合工程运行的标准,实现其尺寸的有效控制,限制其在正确的公差范围内。
受到其定位副制造环节的应用,就容易出现其定位副间的配合间隙,该环节和其最大位置变动量有着密切的关系,我们称它是定位副制造部准确误差。
通过对工艺系统的工件刚度环节的优化,可以实现其切削力的有效应用,以符合工件加工精度的需要。
下文将对刀具刚度展开分析,一般来说,由于其外圆车刀的影响,其加工表面的法线方向具备较高的刚度,在此过程中,选择对其变形因素的忽略。
由于其镗直径的影响,导致其较差的刀杆刚度。
其刀杆发生相关的受力变形,就会导致其加工精度的变化。
机床部件刚度的变化,也会影响其工件的精度,机床设备的稳定运行,离不开其内部各个零件,目前来说,还没有完善的方法实现其机床部件刚度的有效计算,实验方法是确定机床部件刚度的一个重要模式。
加载曲线和卸载曲线不重合,卸载曲线滞后于加载曲线。
两曲线间所包容的面积就是在加载和卸载循环中所损耗的能量,它消耗于摩擦力所做的功和接触变形功;第一次卸载后,变形恢复不到第一次加载的起点,这说明有残余变形存在,经多次加载卸载后,加载曲线起点才和卸载曲线终点重合,残余变形才逐渐减小到零。
1.3 由于工艺系统的热变形环节的影响,加工精度会发展相关的变化,在大件加工过程中,由于受到其工艺系统热变形环节的影响,容易出现一系列的加工误差,这不利于工件误差的有效控制,并且由于热源作用的影响,其温度会发生相关的变化,其热量呈分散性的扩散。
在机械加工的每一工序中,总要对工艺系统进行这样或那样的调整工作。
由于调整不可能绝对地准确,因而产生调整误差。
2 加工精度工艺方案的优化
为了实现其加工精度工艺方案的优化,要实现其原始误差的有效控制。
通过对加工零件的机床几何精度的有效控制,促进其工具自身精度的提升、夹具精度的提升,从而实现其工艺系统的热变形环节、系统受力环节的控制,避免其过大的误差的产生,实现其刀具磨损的降低。
针对由相关因素导致的变形误差,可以进行其测量误差的减少,实现其原始误差的控制。
为了保证其加工精度的有效应用,要针对其各个原始误差展开研究,实现其相关模式的解决方案的应用。
对于精密零件的加工应尽可能提高所使用精密机床的几何精度、刚度和控制加工热变形;对具有成形表面的零件加工,则主要是如何减少成形刀具形状误差和刀具的安装误差。
误差补偿法。
对工艺系统的一些原始误差,可采取误差补偿的方法以控制其对零件加工误差的影
响。
误差补偿法:该方法是人为地造出一种新的原始误差,从而补偿或抵消原来工艺系统中固有的原始误差,达到减少加工误差,提高加工精度的目的。
通过对误差抵消法的应用,可以满足日常加工原始误差的控制。
在工作过程中,通过对原始误差的有效分化,也可以促进零件的加工精度的提升。
一般来说,为了促进其零件表面精度的有效提升,要积极展开相关试切加工环节的优化,实现其原始误差的有效均化,以满足现实工作的需要。
分化原始误差法:根据误差反映规律,将毛坯或工序的工件尺寸经测量按大小分为n组,每组工件的尺寸范围就缩减为原来的1n。
然后按各组的误差范围分别调整刀具相对工件的准确位置,使各组工件的尺寸分散范围中心基本一致,以使整批工件的尺寸分散范围大大缩小。
在均化原始误差的过程中,需要实现其加工环节的优化,以降低其加工表面的相关误差,这也需要实现其均化原理的优化,保证其相关工具检查方案的优化,以实现其差异环节的优化,保证其有效修正及其基准优化环节的应用,实现其原始误差的有效转移。
转移原始误差至非敏感方向。
各种原始误差反映到零件加工误差上的程度与其是否在误差敏感方向上有直接关系。
若在加工过程中设法使其转移到加工误差的非敏感方向,则可大大提高加工精度。
转移原始误差至其他对加工精度无影响的方面。
3 结束语
为了保障机械加工质量的提升,需要针对其机械加工质量技术方案展开优化,以实现日常加工工件的自身误差的有效控制,以满足现实工作的需要。