熔模铸造工艺卡
低压工艺卡

低压铸造工艺卡片
铝液温度
690-710℃
产品名称
TL5033
铸件毛重(Kg):9±0.2
机台型号:
铝液密度
≥2.60g/cm3
毛坯编号
ET44S
Sr含量:
见熔铝炉工艺指导书
冷却控制
工艺参数
压力控制
冷却时间
开始时间(S)
开通时间(S)
压力(bar)
控制项目
压力(mbar)
充型速率(mbar/S)
50±10
下模轮盘
280±10
40±10
4.5—6
模具烤模时间
45±10
下模大环
/
/
/
模具温度
轮盘
/
冷却风道基本位置图
轮缘
/
易出缺陷
1)轮辋易疏松
控制重点
1)严格按工艺参数进行
2)外观不能有碰伤、拉模、涂料脱落现象
编制
审核
批准
日期
分流锥风
160±20
80±20
4.5—6
升液
185
0.45
上模轮盘内环
80±20
170±20
4.5—6
充型Biblioteka 3400.06上模轮盘外环
130±20
70±20
4.5—6
420
0.06
增压
420
0.07
上模轮辐
/
/
/
750
0.72
保压
750
160±15
下模冒口
120±20
130±20
4.5—6
自然冷却时间
工艺卡片模板100例
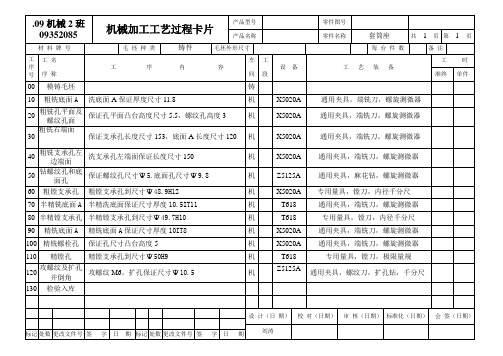
.09机械2班09352085 机械加工工艺过程卡片产品型号零件图号产品名称零件名称套筒座共 1 页第 1 页材料牌号毛坯种类铸件毛坯外形尺寸每台件数备注工序号工名序称工序内容车间工段设备工艺装备工时准终单件00 模铸毛坯铸10 粗铣底面A洗底面A保证厚度尺寸11.8 机X5020A 通用夹具,端铣刀,螺旋测微器20 粗铣孔平面及螺纹孔面保证孔平面凸台高度尺寸5.5,螺纹孔高度3 机X5020A 通用夹具,端铣刀,螺旋测微器30 粗铣右端面保证支承孔长度尺寸153,底面A长度尺寸120 机X5020A 通用夹具,端铣刀,螺旋测微器40 粗铣支承孔左边端面洗支承孔左端面保证长度尺寸150 机X5020A 通用夹具,端铣刀,螺旋测微器50 钻螺纹孔和底面孔保证螺纹孔尺寸ψ5.底面孔尺寸ψ9.8 机Z5125A 通用夹具,麻花钻,螺旋测微器60 粗镗支承孔粗镗支承孔到尺寸ψ48.9H12机X5020A 专用量具,镗刀,内径千分尺70 半精铣底面A半精洗底面保证尺寸厚度10.5IT11机T618 通用夹具,端铣刀,螺旋测微器80 半精镗支承孔半精镗支承孔到尺寸ψ49.7H10机T618专用量具,镗刀,内径千分尺90 精铣底面A精铣底面A保证尺寸厚度10IT8机X5020A 通用夹具,端铣刀,螺旋测微器100 精铣螺栓孔保证孔尺寸凸台高度5 机X5020A 通用夹具,端铣刀,螺旋测微器110 精镗孔精镗支承孔到尺寸ψ50H9机T618 专用量具,镗刀,极限量规120 攻螺纹及扩孔并倒角攻螺纹M6,扩孔保证尺寸ψ10.5机Z5125A通用夹具,螺纹刀,扩孔钻,千分尺130 检验入库设计(日期)校对(日期)审核(日期)标准化(日期)会签(日期)材料牌号毛坯种类毛坯外形尺寸每毛坯件数每台件数备注工序号工名序称工序内容车间工段设备工艺装备工时准终单件设计(日期)校对(日期)审核(日期)标准化(日期)会签(日期)材料牌号毛坯种类毛坯外形尺寸每毛坯件数每台件数备注工序号工名序称工序内容车间工段设备工艺装备工时准终单件设计(日期)校对(日期)审核(日期)标准化(日期)会签(日期)。
熔模铸造工艺资料
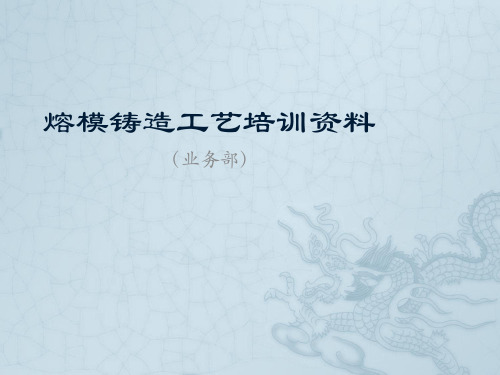
4、月产量:根据经验确定射蜡班产×3班×11个工位×30天×产品单重 5、面层:根据产品结构,及产品要求确定,一般复杂产品存在细的孔槽、产品单重大
以及产品表面质量要求较高时需加厚1-2层面层。 6、加厚层:根据产品最大尺寸及重量确定,一般最大尺寸超过150mm,重量超过2kg,
熔模铸造工艺培训资料
(业务部)
报价
报价
1、单重:客户提供单重或立体图的,若为毛坯单重可直接使用,若为加工单重则必须 加上加工量的重量,如没有提供则需根据图纸自己绘图计算。
2、合格率:主要考虑产品壁厚、结构、材质的影响,一般壁厚越小、结构越复杂、特 殊材质(高铬、高镍、铜合金、高温合金等)合格率低。
熔模铸件的尺寸精度高,表面粗糙度细。熔模铸件的尺寸精度可达到CT5~7级,表面粗糙度可 达到Ra(1.6~12.5)μm,因此可以减少铸件的切削加工量,甚至可以无须切削加工。
可以铸造薄壁铸件以及重量很小的铸件。最小壁厚可达0.5mm,重量可以小到几克。 可以铸造花纹精细的图案、文字、带有细槽和弯曲细孔的铸件。最小孔径可以小到0.5mm。 可以制造形状复杂的铸件。熔模铸件的外形和内腔形状几乎不受限制。 可以制造各种合金的铸件。如铝合金、镁合金、铜合金、不锈钢、镍铬合金、钴合金等。对于
制壳车间加快型壳表面的空气流动,从而增加型壳的干燥速度、减少干燥时间。但面层干燥速度不 可过快,干燥不可过度,防止出现龟裂。一般面层使用微风和不用吹风。 (3)环境湿度是影响型壳干燥的又一重要因素 在温度基本稳定的情况下,湿度大的车间,型壳水 分蒸发速度慢。当相对湿度大于80%时,型壳的干燥时间将大大加长。因而,制壳车间必须有除湿 机,严格控制车间的湿度。 面层涂挂区环境要求:温度25±2℃,干燥区环境要求:温度25±2℃,具体干燥时间应根据模壳实 际干燥情况而定。 型壳干燥程度的测量方法有:重量法、显色法、电阻法等。重量法因型壳外部砂粒容易脱落而不准 确;显色法是在涂料中加入显色剂,型壳干燥前后的颜色有明显区别,很容易根据颜色来判断型壳 是否干燥;电阻法的原理是利用型壳中水的高导电性,型壳的电阻和其含水量有关,当失水率达 70%以上时电阻值急剧增大,可以认为型壳的电阻增大到超过某一临界值时,型壳已干燥。 目前主要是靠经验,用手摸来感觉模壳是否干燥透或用小棒捅看是否有其强度
熔模铸造工艺流程
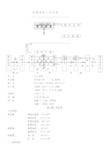
熔 模 铸 造 工 艺 流 程模料主要性能:灰 分 ≤0.025%铁含量 灰分的10% ≤0.0025% 熔 点 83℃-88℃(环球法)60℃±1℃ 针入度 100GM (25℃)3.5-5.0DMM450GM (25℃)14.0-18.0DMM收缩率 0.9%-1.1% 比 重 0.94-0.99g/cm 3 颜 色 新蜡——兰色、深黄色 旧蜡——绿色、棕色蜡(模)料处理工艺参数:除水桶 搅拌时温度 110-120℃ 搅拌时间 8-12小时 静置时温度 100-110℃ 静置时间 6-8小时 静置桶 静置温度 70-85℃ 静置时间 8-12小时 保温箱 温 度 48-52℃ 时 间 8-24小时 二、操作程序1、从脱蜡釜泄出的旧蜡用泵或手工送到除水桶中,先在105-110℃下置6-8小时沉淀,将水分泄掉。
2、蜡料在110-120℃下搅拌8-12小时,去除水份。
3、将脱完水的蜡料送到70-85℃的静置桶中保温静置桶中保温静置8-12小时。
4、也可将少量新蜡加入静置桶中,静置后清洁的蜡料用手工灌到保温箱蜡缸中,保温温度48-52℃,保温时间8-24小时后用于制蜡模。
5、或把静置桶中的回收蜡料输入到气动蜡模压注机的蜡桶中,保温后压制浇道。
三、操用要点1、严格按回收工艺进行蜡料处理。
2、除水桶、静置桶均应及时排水、排污。
3、往蜡缸灌蜡时,蜡应慢没缸壁流入,防止蜡液中进入空气的灰尘。
4、蜡缸灌满后应及时盖住,避免灰尘等杂物落入。
5、经常检查每一个桶温,防止温度过高现象发生。
6、作业场地要保持清洁。
7、防止蜡液飞溅。
8、严禁焰火,慎防火灾。
压制蜡(熔)模一、工艺参数室温20-24℃压射蜡温50-55℃压射压力0.2-0.5Mpa 保压时间10-20S冷却水温度15±3℃二、操作程序1、从保温槽中取出蜡缸,装在双工位液压蜡模压注机上,使用前应去除蜡料中空气及硬蜡。
2、将模具放在压注机工作台面上定位,检查模具所有芯子位置是否正确,模具注蜡口与压注机射蜡嘴是否对正。
精密铸造工艺-熔模铸造
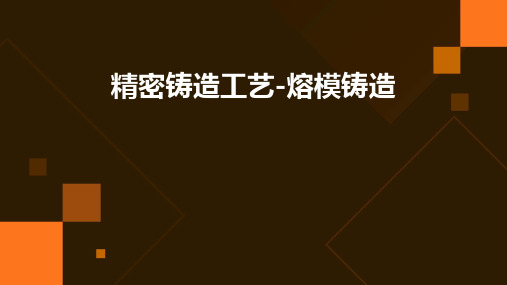
一定的强度
在搬运和组装过程中不易损坏。
易于脱壳
在铸件冷却后能够顺利脱去壳型,不 损伤铸件表面。
合金选择与性能要求
符合产品使用要求
良好的铸造性能
根据产品的使用环境和性能要求选择合适 的合金种类和牌号。
合金应具有较低的熔点和良好的流动性, 以便于充型和补缩。
安全操作规程及培训要求
制定安全操作规程
明确各工序的安全操作要求和注 意事项,确保操作人员严格遵守
。
应急预案与演练
对新员工和转岗员工进行安全培 训,提高员工的安全意识和操作
技能。
安全培训与教育
对涉及特种作业的员工,如电工 、焊工等,必须持证上岗,确保 操作安全。
特种作业人员持证上岗
制定针对熔模铸造过程中可能出现 的紧急情况的应急预案,并定期进 行演练,提高员工的应急处置能力。
加强人才培养
加强人才培养和引进,培养一支高素质、专业化的熔模铸造技术人才队伍,推动行业的技 术进步和可持续发展。例如,建立完善的人才培养和激励机制,吸引和留住优秀人才。
感谢您的观看
THANKS
蜡料选择与性能要求
低熔点和高流动性
确保蜡料在注射时能够充分填充模具,形成 精确的蜡模。
易于脱模
与模具材料之间有良好的分离性,降低脱模 难度。
稳定性好
在存放和使用过程中不易变质或产生缺陷。
对环境友好
无毒无害,符合环保要求。
壳型材料及其性能要求
高耐火度
能够承受高温金属液的冲刷而不破裂 或变形。
良好的透气性
较高的力学性能
良好的耐蚀性和耐磨性
合金应具有足够的强度、硬度和韧性等力 学性能,以满足产品的使用要求。
压铸工艺卡(800T)

数量
备注
配制比例 1:120
增压预热模数/模 慢速压力/bar 慢速流量/% 压射时间/s 开模时间/s 铝液温度/℃ 顶针前延时/s 顶针后延时/s 料柄厚度/mm
5±2 140±10
80±5 8±1 6±1 680±30 1±1 25±5 25±5
更改标记
处数 更改文件号 签名
日期
批准
版本号:A-0 ;
XX有限公司
新旧料比 7:3
铸件 (KG)
2.53
浇注 系统 (KG)
压力铸造工艺卡片
每模 腔数
1
每模重量 (KG)
编制 会签 审核
产品名称 产品图号 材料牌号
设备
工艺 装备
表单编号:
ADC12 设备名称 DCC800 压室直径 工艺装备名称
镶
图号
嵌
件
名称 涂 料
名称
牌号 9/bar
工 艺 规
锤头至模具行程 /mm
二快位置/mm
范 增压位置/mm
一快开度/%
二快开度/%
增压开度/%
重点自检内容:
15±5 130±5 110±5 620±5 400±5 450±5 60±5 60±5 40±5
客户代码 物料编码 工序号
设备编号
ф100 工艺装备编号
铸造工艺(附图)
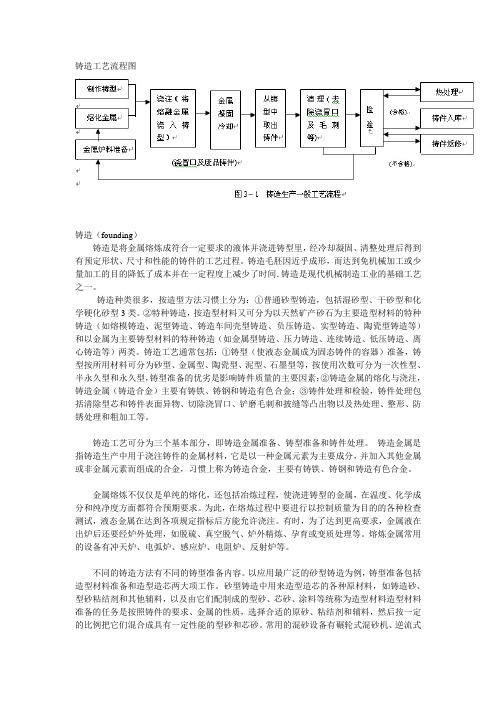
铸造工艺流程图铸造(founding)铸造是将金属熔炼成符合一定要求的液体并浇进铸型里,经冷却凝固、清整处理后得到有预定形状、尺寸和性能的铸件的工艺过程。
铸造毛胚因近乎成形,而达到免机械加工或少量加工的目的降低了成本并在一定程度上减少了时间.铸造是现代机械制造工业的基础工艺之一。
铸造种类很多,按造型方法习惯上分为:①普通砂型铸造,包括湿砂型、干砂型和化学硬化砂型3类。
②特种铸造,按造型材料又可分为以天然矿产砂石为主要造型材料的特种铸造(如熔模铸造、泥型铸造、铸造车间壳型铸造、负压铸造、实型铸造、陶瓷型铸造等)和以金属为主要铸型材料的特种铸造(如金属型铸造、压力铸造、连续铸造、低压铸造、离心铸造等)两类。
铸造工艺通常包括:①铸型(使液态金属成为固态铸件的容器)准备,铸型按所用材料可分为砂型、金属型、陶瓷型、泥型、石墨型等,按使用次数可分为一次性型、半永久型和永久型,铸型准备的优劣是影响铸件质量的主要因素;②铸造金属的熔化与浇注,铸造金属(铸造合金)主要有铸铁、铸钢和铸造有色合金;③铸件处理和检验,铸件处理包括清除型芯和铸件表面异物、切除浇冒口、铲磨毛刺和披缝等凸出物以及热处理、整形、防锈处理和粗加工等。
铸造工艺可分为三个基本部分,即铸造金属准备、铸型准备和铸件处理。
铸造金属是指铸造生产中用于浇注铸件的金属材料,它是以一种金属元素为主要成分,并加入其他金属或非金属元素而组成的合金,习惯上称为铸造合金,主要有铸铁、铸钢和铸造有色合金。
金属熔炼不仅仅是单纯的熔化,还包括冶炼过程,使浇进铸型的金属,在温度、化学成分和纯净度方面都符合预期要求。
为此,在熔炼过程中要进行以控制质量为目的的各种检查测试,液态金属在达到各项规定指标后方能允许浇注。
有时,为了达到更高要求,金属液在出炉后还要经炉外处理,如脱硫、真空脱气、炉外精炼、孕育或变质处理等。
熔炼金属常用的设备有冲天炉、电弧炉、感应炉、电阻炉、反射炉等。
不同的铸造方法有不同的铸型准备内容。
压铸工艺卡范例

客户 产品名称
后壳体
零(部)件号 文件版本号
材料 牌号
铸件毛重பைடு நூலகம்(kg)
7.8
模穴数 (pcs)
1
试模日期
设备
料管直径(mm)
¢110 每模周期(s)
工
1 机器检查、铝锭预热/溶解 2 架模、模具预热(模温机) 3 参数调整 4 吹气/喷涂 5 给料、压射
序
内
容
6
开模、顶出、取件、去浇口、自检
参数模具每调整一次需对相关项目进行检测取样送检品质部及时将检验情况反馈给现场压铸工程师配合生产直至质量达标目标良率96机器检查铝锭预热溶解架模模具预热模温机进入二次循环首检前15模产品强制报废吹气喷涂1射料最大位置7锤头追踪2增压开始位置选择8压射时间s3二快开始位置选择9射料慢速4一快开始位置选择10冷却时间s5储能压力bar11触发压力bar6铝液温度630650注
生产,直至质量达标(目标良率≥96%)
1
100 顶针前进速度 80% 顶针前进延时 4s
铸
80
顶针后退速度
80% 顶针后退延时 25s
件 质
稀释倍数
送料设备
喷涂设备 喷涂时间
量
外观质量 符合制程检验标准
内在质量 符合探伤标准
离型 剂 离型剂
编制:
ELP-Z
1:90
质
量
离型剂压送机
气枪
>15S
审核:
符合制程检验标准 批准:
符合探伤标准
45%
8、压射时间(s)
13
530mm
65%
9、射料慢速
60%
480mm
45%
10、冷却时间(s)